Aluminum is gaining traction in injection molding, but is it truly the right choice for your needs?
Aluminum can be used for injection molds, offering benefits like excellent thermal conductivity, lightweight handling, and ease of processing. However, its lower hardness and poor corrosion resistance may limit its application in high-volume or high-precision production settings.
While aluminum presents compelling advantages in certain scenarios, it’s crucial to weigh these against its limitations. Understanding the specifics of your production requirements will help determine if aluminum is the right material choice for your molds.
Aluminum molds offer superior thermal conductivity.True
Aluminum's high thermal conductivity allows for faster cooling, improving cycle times.
What Are the Advantages of Using Aluminum in Injection Molds?
Choosing aluminum for injection molds can revolutionize your production with its unique advantages.
Aluminum molds offer superior thermal conductivity, lightweight benefits, and exceptional processability, making them ideal for efficient and versatile injection molding applications.
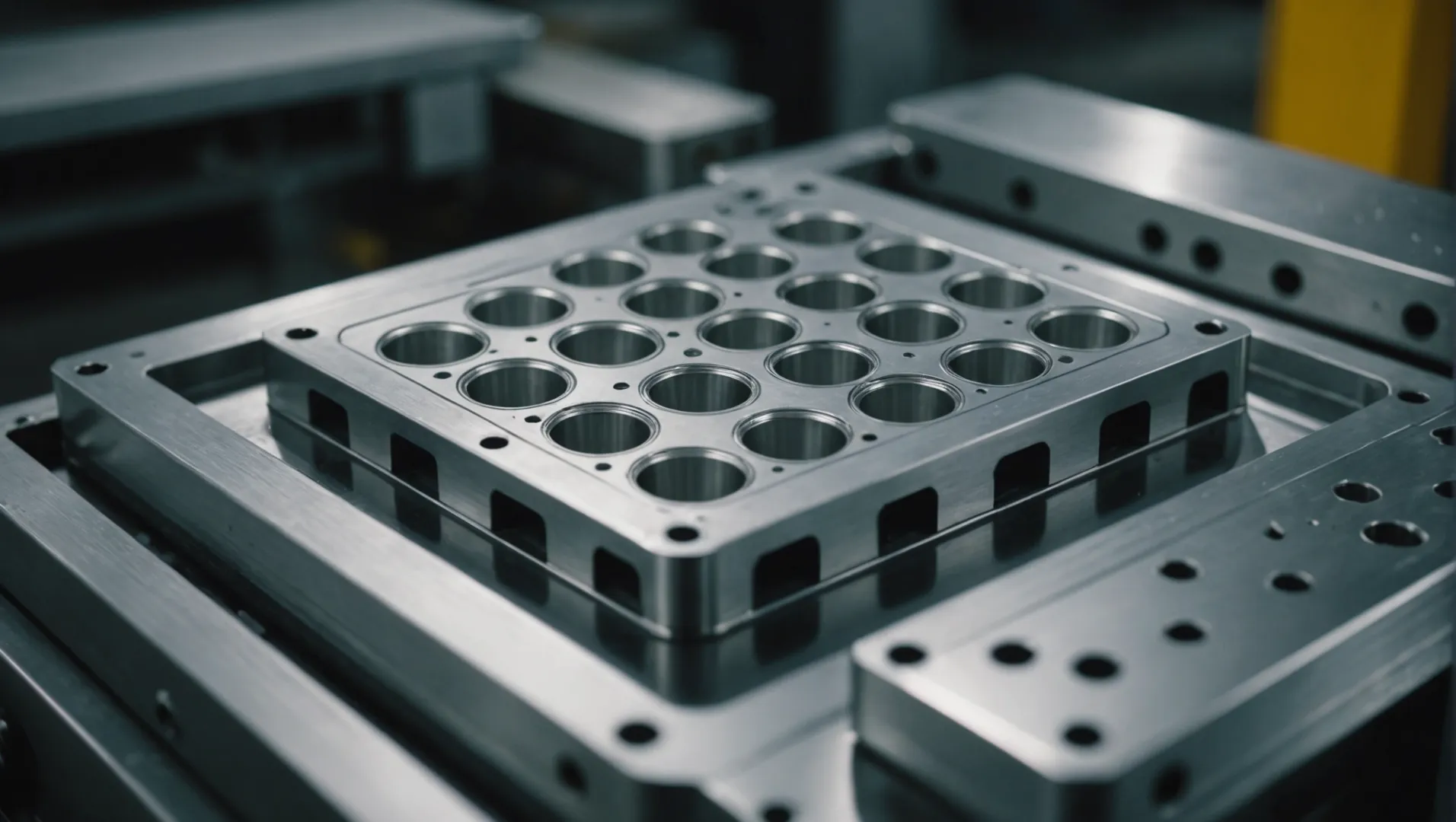
Superior Thermal Conductivity
One of the standout features of aluminum molds is their excellent thermal conductivity. This property allows aluminum to efficiently dissipate the heat generated during the injection molding process. Faster heat dissipation means shorter cooling times, leading to quicker cycle times and enhanced production efficiency.
For example, in manufacturing thin-walled products where rapid cooling is crucial, aluminum molds ensure the plastic solidifies swiftly. Additionally, for temperature-sensitive materials, aluminum’s thermal properties allow for better temperature control, ensuring stable product quality.
Lightweight Advantages
Aluminum’s low density means that molds made from this material are significantly lighter than those made from steel. This lightweight nature eases handling and installation, reducing worker fatigue and allowing for faster mold changes on production lines.
Consider a scenario where molds are frequently swapped on a production line: the lighter weight of aluminum not only speeds up this process but also reduces machine wear and tear. This advantage extends the lifespan of smaller injection molding machines by lessening their operational load.
Exceptional Processability
Aluminum is known for its outstanding processability. Its cutting performance facilitates the creation of complex mold shapes using various machining techniques. The ease of processing translates into reduced manufacturing costs and shorter lead times.
For instance, employing a CNC machining center can rapidly produce high-precision aluminum molds. Moreover, aluminum can undergo surface treatments like anodizing to enhance its wear and corrosion resistance, thus extending mold life.
Comparison with Steel
Although not the focus here, it is worth noting how these advantages position aluminum favorably against traditional steel in certain applications. For readers interested in a detailed comparison, further exploration into how aluminum compares to steel1 may provide valuable insights.
Aluminum molds reduce cooling time in injection molding.True
Aluminum's thermal conductivity allows faster heat dissipation.
Steel molds are lighter than aluminum molds.False
Aluminum is lighter due to its low density compared to steel.
How Does Aluminum Compare to Steel for Injection Molding?
Aluminum and steel are two popular choices for injection molding, but how do they truly compare in terms of performance and cost-effectiveness?
Aluminum offers advantages like superior thermal conductivity and lightweight handling, making it ideal for rapid production cycles. Steel, however, provides unmatched durability and resistance to wear, suitable for high-volume and precision applications. The choice between aluminum and steel largely depends on the specific requirements of your injection molding project.
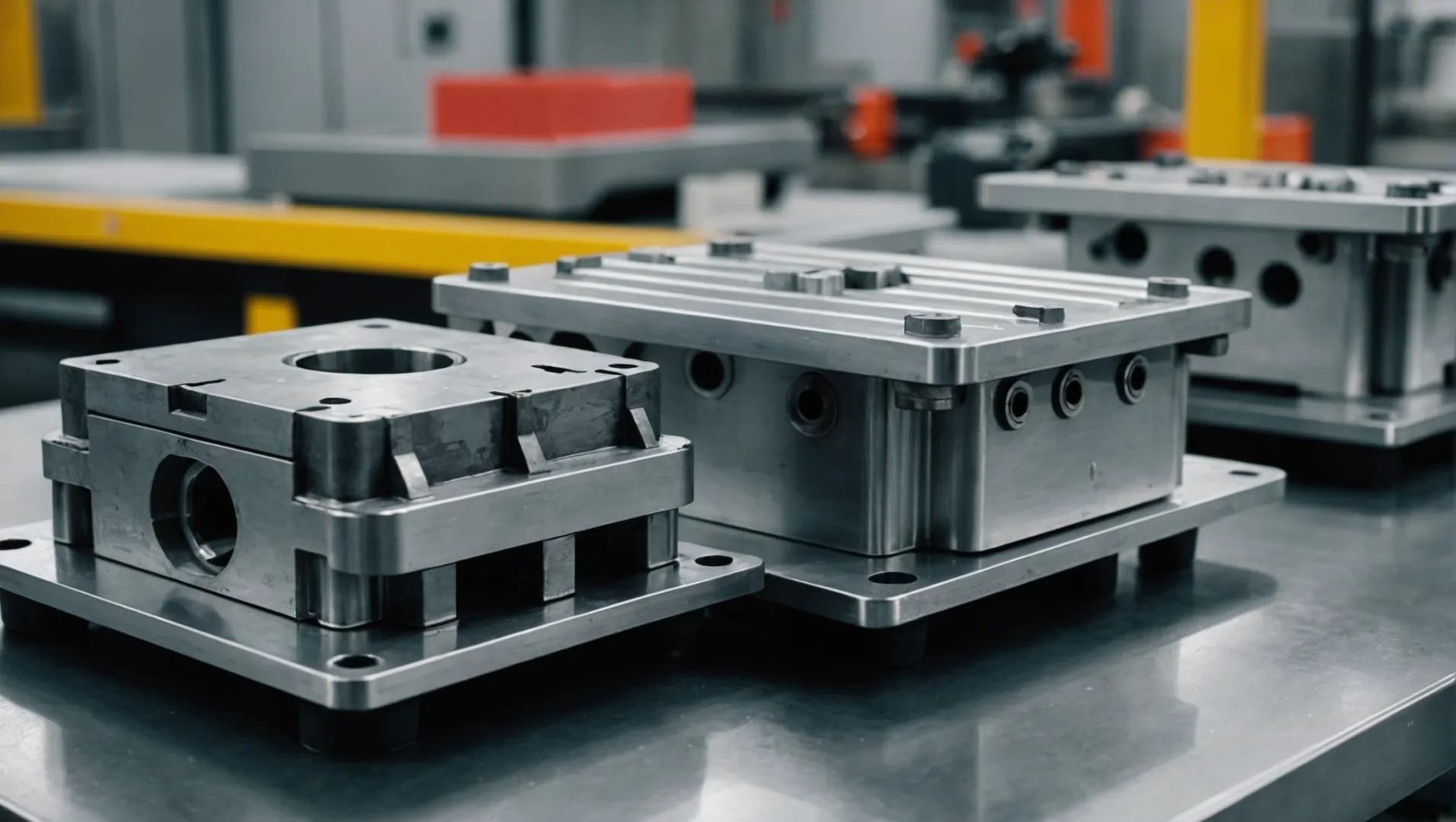
Thermal Conductivity and Cycle Time
Aluminum boasts a high thermal conductivity coefficient, significantly reducing the cooling time during the injection molding process. This results in shorter cycle times and increased production efficiency. For instance, in the production of thin-walled items, aluminum molds help in faster cooling and solidification of the plastic, which can be a critical factor in mass production.
In contrast, steel has lower thermal conductivity, which might prolong cooling times. However, this can be advantageous when uniform cooling is required to maintain dimensional stability in complex parts.
Weight and Handling
One of the most significant advantages of aluminum over steel is its lightweight nature. Aluminum molds are easier to handle, install, and change out on production lines. This can minimize downtime and labor costs. On lines where molds are frequently swapped out, aluminum’s lighter weight allows for quicker transitions.
Steel molds, being heavier, may require additional equipment for handling but offer stability during the injection process, which is crucial for precision molding.
Durability and Maintenance
Steel’s high hardness makes it resistant to wear and deformation, which is crucial for maintaining quality in high-volume production runs. Steel molds can endure higher clamping forces and pressures without deforming, making them suitable for large or deep-cavity products.
Conversely, aluminum’s lower hardness means it may wear out faster under similar conditions. However, with proper care, such as controlling injection pressure and using surface treatments like anodizing, aluminum molds can perform well in less demanding environments.
Corrosion Resistance and Environmental Suitability
Aluminum is more prone to corrosion than steel, especially when exposed to certain plastics or humid environments. This necessitates protective coatings or treatments to extend its lifespan.
Steel generally offers better corrosion resistance naturally, but when exposed to harsh chemicals or environments, it also requires protective measures.
Feature | Aluminum | Steel |
---|---|---|
Thermal Conductivity | Excellent for quick cooling | Moderate for uniform cooling |
Weight | Lightweight | Heavy |
Durability | Lower hardness | High hardness |
Corrosion Resistance | Requires coating | Generally better |
Understanding these characteristics will help you evaluate the best material2 for your injection molding needs based on production volume, precision requirements, and environmental conditions.
Aluminum molds reduce cycle times in injection molding.True
Aluminum's high thermal conductivity shortens cooling times, speeding up production.
Steel molds are lighter than aluminum molds.False
Steel is heavier than aluminum, requiring more effort to handle and install.
When Is Aluminum Not the Best Choice for Injection Molds?
Choosing the right material for your injection molds is crucial for production efficiency and product quality. When might aluminum not be the ideal choice?
Aluminum may not be suitable for injection molds requiring high durability, precision, or corrosion resistance. Its lower hardness and susceptibility to wear and corrosion can limit its use in high-volume or harsh environments.
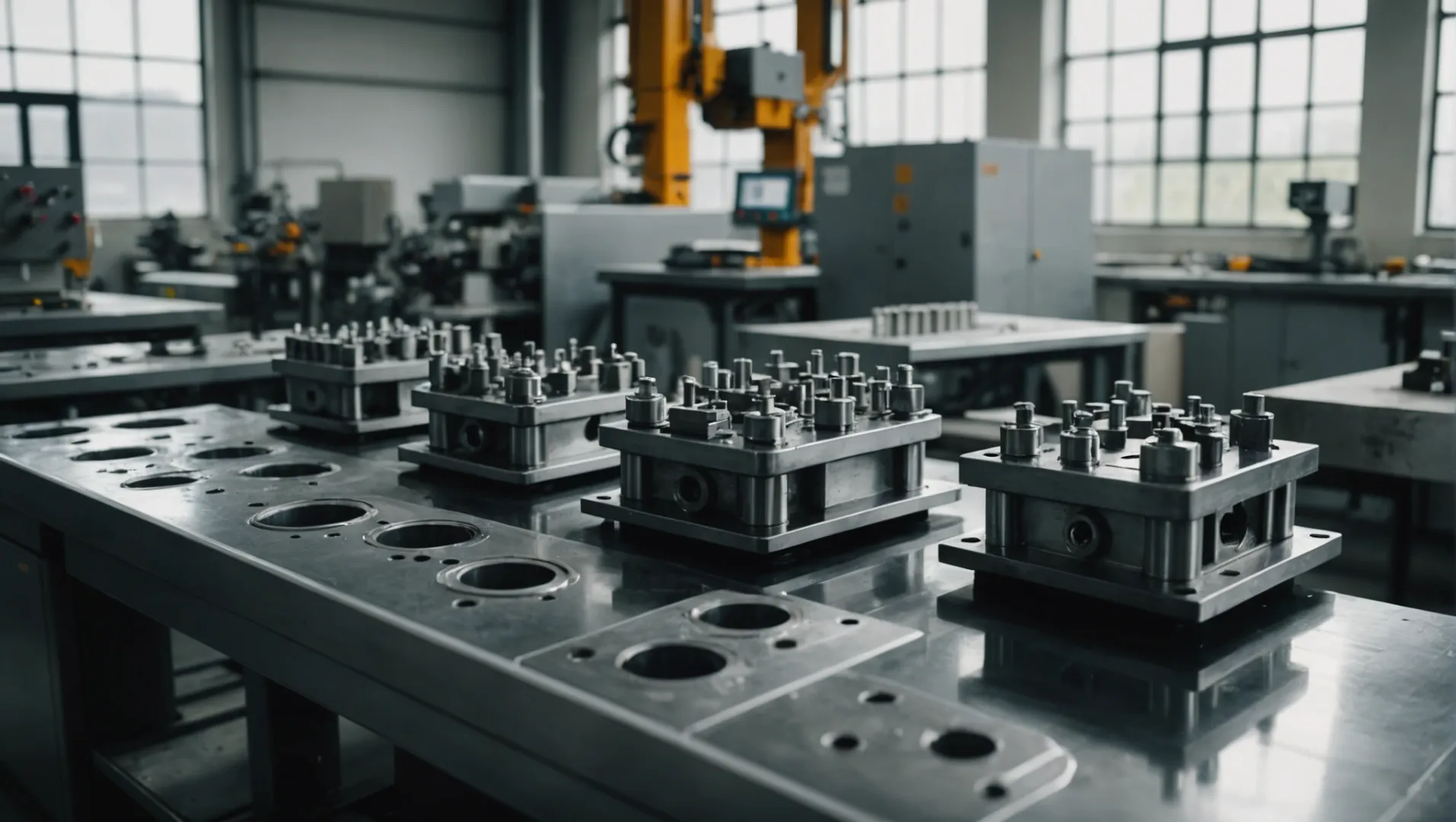
Understanding Aluminum’s Limitations in Injection Molding
Aluminum is often praised for its lightweight nature and excellent thermal conductivity, but these advantages don’t always translate into every injection molding scenario. Understanding when aluminum might fall short can help in selecting the right material for specific applications.
Low Hardness: A Double-Edged Sword
While the malleability of aluminum makes it easy to work with, it also means that it can deform under high pressure. For high-volume production3 runs where molds endure significant wear and tear, aluminum’s low hardness could lead to quicker degradation compared to harder materials like steel. This is particularly concerning in the production of large, deep-cavity products where maintaining mold integrity is critical.
Corrosion Resistance: A Potential Pitfall
Aluminum’s susceptibility to corrosion becomes a major concern in environments where it is exposed to moisture or corrosive materials. In cases where plastic materials used in the injection process are chemically aggressive, the aluminum mold may deteriorate faster than anticipated. Protective treatments, such as anodizing or coating, can mitigate this issue but add additional cost and complexity.
Cost Considerations: The Long-Term View
Although initially cheaper than steel, aluminum molds may require more frequent replacements due to their limited lifespan. This could lead to increased costs over time, particularly if production demands high durability and precision. In scenarios where molds must sustain a long service life, the investment in a more robust material may be justified.
Property | Aluminum | Steel |
---|---|---|
Thermal Conductivity | High | Medium |
Weight | Light | Heavy |
Hardness | Low | High |
Corrosion Resistance | Low | High |
Initial Cost | Lower | Higher |
Specific Use Cases Where Steel Excels
In industries where product quality cannot be compromised, such as automotive or medical device manufacturing, the precision and durability offered by steel molds often outweigh the benefits of aluminum. For precision-driven projects4, steel provides the robustness needed to maintain tight tolerances over extended production runs.
Choosing between aluminum and steel for injection molds isn’t a one-size-fits-all decision. Each project requires careful consideration of the material’s properties in relation to production needs and environmental factors.
Aluminum molds are best for high-volume production.False
Aluminum molds degrade faster in high-volume runs due to low hardness.
Steel molds offer better corrosion resistance than aluminum.True
Steel's higher corrosion resistance makes it ideal in harsh environments.
What Types of Aluminum Alloys Are Used in Injection Molding?
Choosing the right aluminum alloy for injection molding can significantly impact product quality and production efficiency.
Common aluminum alloys used in injection molding include 7075, 2024, and 6061, each offering unique benefits such as strength, corrosion resistance, and machinability. Selecting the right alloy depends on the specific requirements of the molded product and the operational conditions.
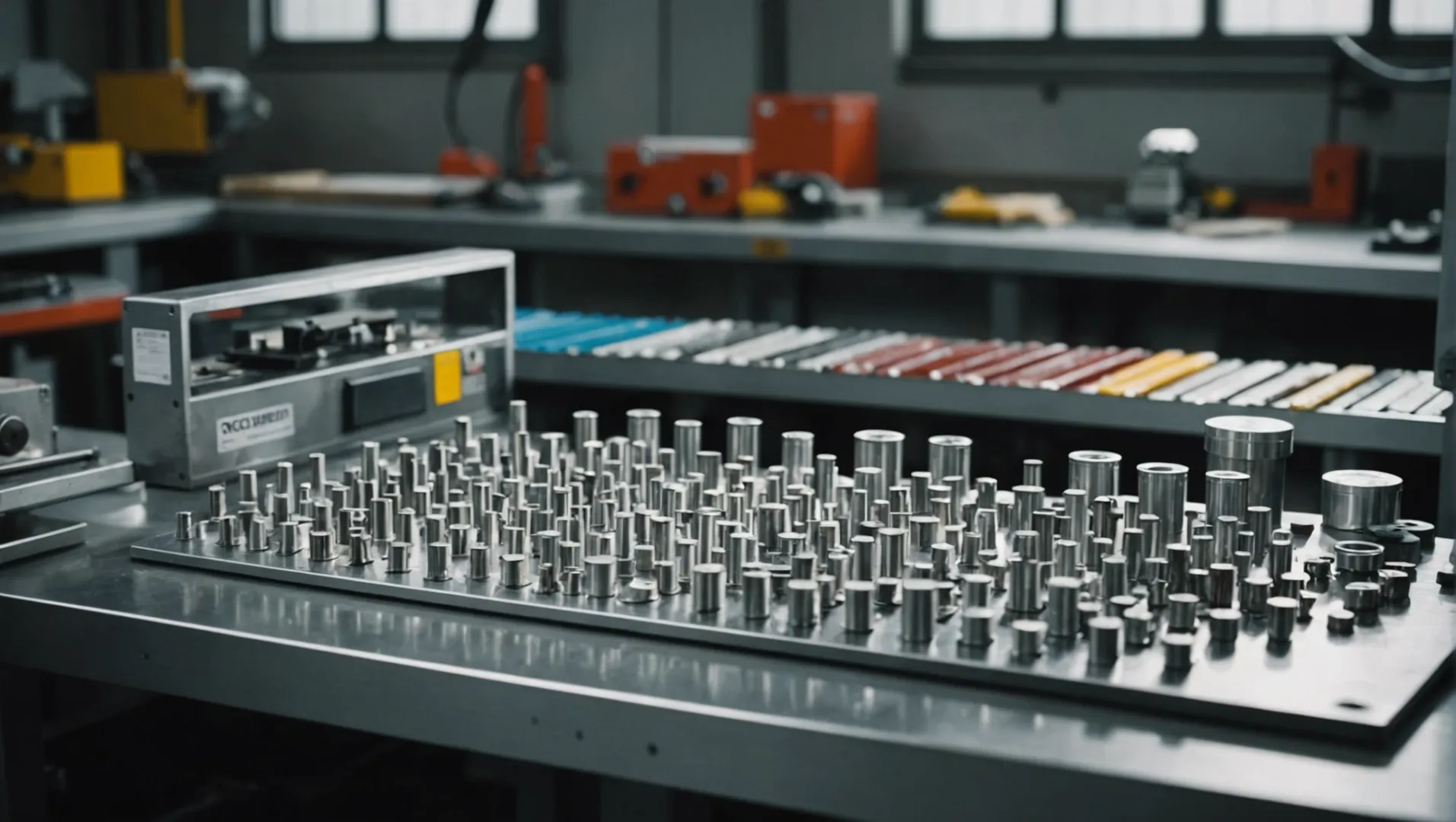
Exploring Common Aluminum Alloys for Injection Molding
The choice of aluminum alloy in injection molding plays a crucial role in the performance and durability of the mold. Each alloy offers distinct properties that cater to different needs. Below are some popular choices:
7075 Aluminum Alloy
Known for its high strength-to-weight ratio, 7075 is often used in applications requiring superior strength and stress resistance. This alloy exhibits excellent machinability5 and is favored for manufacturing complex mold shapes. However, it tends to have lower corrosion resistance compared to other alloys.
2024 Aluminum Alloy
With its impressive tensile strength, 2024 is commonly chosen for high-stress components. It is renowned for its fatigue resistance6, making it suitable for molds subjected to repeated cycles. While it provides good strength, its corrosion resistance may be less than optimal in humid environments.
6061 Aluminum Alloy
6061 stands out due to its excellent corrosion resistance7 and versatility. It balances strength and ease of machining, which makes it a popular choice for various injection molding applications. Its ability to undergo surface treatments further enhances its durability and wear resistance.
How to Choose the Right Aluminum Alloy
When selecting an aluminum alloy, consider the specific requirements of your production process:
- Strength Requirements: Evaluate whether high strength or stress resistance is essential.
- Corrosion Resistance: Determine the environmental conditions your molds will face.
- Machinability and Processing Needs: Consider the complexity of mold design and processing capabilities.
Alloy | Strength | Corrosion Resistance | Machinability | Applications |
---|---|---|---|---|
7075 | High | Moderate | Excellent | Complex molds |
2024 | Very High | Moderate | Good | High-stress components |
6061 | Moderate | High | Good | General-purpose molds |
Understanding these factors helps ensure that the chosen aluminum alloy meets both the technical demands and economic considerations of your project.
7075 aluminum alloy has excellent corrosion resistance.False
7075 has high strength but moderate corrosion resistance.
6061 aluminum alloy is versatile for injection molding.True
6061 balances strength and machinability, making it versatile.
Conclusion
In conclusion, while aluminum injection molds offer distinct advantages, careful consideration of their limitations is essential. Assess your production needs thoroughly to decide if aluminum is suitable for your project.
-
Explore detailed comparisons of aluminum and steel in injection molding.: With a much higher rate of heat dissipation than steel, aluminum molds can heat and cool much more quickly than steel molds — typically up to seven times. ↩
-
Explore detailed comparisons between aluminum and steel molds.: With a much higher rate of heat dissipation than steel, aluminum molds can heat and cool much more quickly than steel molds — typically up to seven times. ↩
-
Learn why steel outlasts aluminum in high-volume production scenarios.: According to the study, the aluminum molds cost up to 50% less to build than steel molds and produced higher-quality parts. Further, the … ↩
-
Discover why steel molds are preferred for high-precision manufacturing.: In this piece, we’ll take a side-by-side look at some benefits and disadvantages of aluminum molds and steel molds for 10 key factors. ↩
-
Discover why 7075 excels in high-strength applications.: 7075 aluminum alloy, known as aircraft aluminum, offers tremendous strength and is commonly employed in prototype tooling and production injection molds. No … ↩
-
Learn about 2024’s fatigue resistance for mold longevity.: The use of aluminum alloy can enhance the hardness and strength of the mold, while also offering significant advantages in reducing weight and improving thermal … ↩
-
Explore how 6061 withstands harsh environments effectively.: 6061 is exceptionally great at resisting corrosion from ammonium hydroxide, ammonia, and nitric acid. You can get rid of these corrosive … ↩