Injection molding is not just about filling a mold; it’s about crafting perfection amid unseen challenges.
Internal stresses in injection molded products result from uneven flow, cooling, and shrinkage during the molding process. These stresses can lead to dimensional changes, mechanical failures, and aesthetic defects, affecting product quality and performance.
While understanding the basics of internal stresses is crucial, delving deeper into their causes and effects can offer valuable insights into mitigating potential issues. Let’s explore these aspects further to improve product reliability and manufacturing efficiency.
Flow imbalance causes internal stress in injection molding.True
Flow imbalance leads to uneven velocity and pressure, causing stress.
What Are the Primary Causes of Internal Stress in Injection Molding?
Internal stress in injection molding arises from factors like flow imbalance, uneven cooling, and molecular orientation.
The primary causes of internal stress in injection molding include flow imbalance, uneven cooling, and molecular orientation, which occur due to process and design inconsistencies. These stresses can compromise the structural integrity and appearance of molded products.
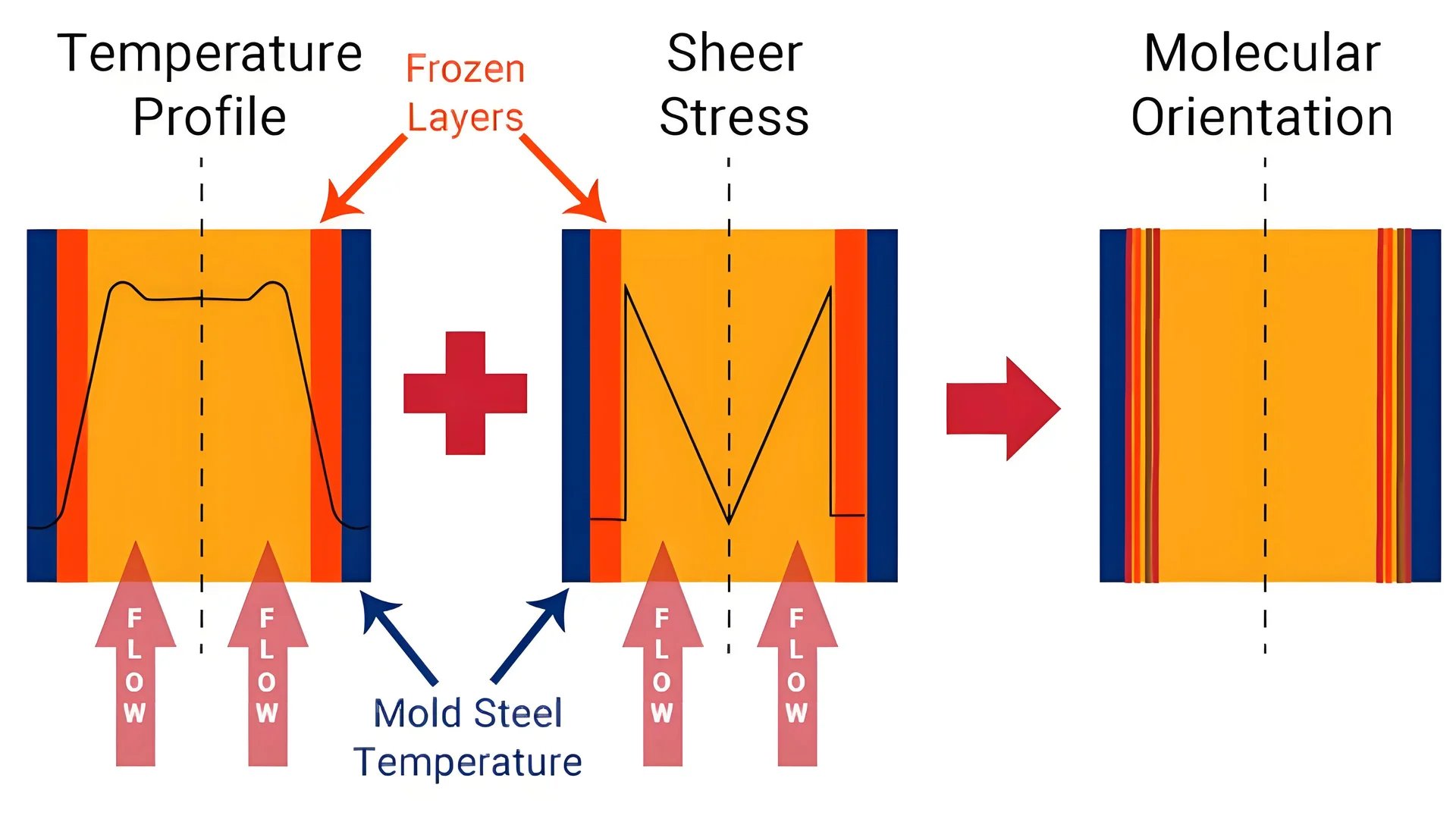
Flow Imbalance
During the injection molding process, the plastic melt does not always flow uniformly within the mold cavity. This discrepancy is mainly due to variations in flow velocity and pressure distribution. For instance, near the gate where the plastic enters, the melt flows faster compared to areas farther away. This imbalance generates shear stress within the product.
Unreasonable mold designs, such as poorly positioned gates or inadequately sized runners, exacerbate this imbalance. By refining these design elements, the stress induced by flow discrepancies can be significantly reduced.
Uneven Cooling
The cooling phase is crucial in defining the final properties of an injection molded product. If certain areas cool faster than others, thermal stress is introduced. Factors such as inconsistent mold temperature and poorly designed cooling channels contribute to this.
Uneven wall thickness also plays a role. Thicker sections cool slower than thinner ones, creating internal stress. A strategic design approach, focusing on uniform wall thickness, can mitigate this issue.
Molecular Orientation
As the plastic melt flows through the mold, its molecules align in the direction of flow. This alignment can lead to orientation stress, which is predominantly found along the flow direction and less so perpendicular to it.
Process parameters like injection speed and holding pressure directly impact molecular orientation. For example, an excessively high injection speed or holding pressure can amplify orientation stress. Adjusting these parameters helps manage the degree of molecular orientation effectively.
Comparative Analysis: Causes of Internal Stress
Cause | Description | Mitigation Strategy |
---|---|---|
Flow Imbalance | Uneven velocity and pressure distribution within mold cavity. | Optimize gate position and runner size. |
Uneven Cooling | Differential cooling rates leading to thermal stress. | Uniform mold temperature; better channel layout. |
Molecular Orientation | Alignment of molecules causing stress in flow direction. | Control injection speed and holding pressure. |
Understanding these root causes is pivotal for anyone involved in injection molding optimization1. By identifying and addressing these factors, manufacturers can enhance product quality and extend their lifecycle.
Flow imbalance causes shear stress in molded products.True
Flow imbalance creates uneven pressure, leading to shear stress.
Uniform wall thickness increases internal stress in molding.False
Uniform wall thickness reduces thermal stress, not increases it.
How Do Internal Stresses Affect the Mechanical Properties of Products?
Internal stresses in products can severely compromise their mechanical properties, influencing strength and durability.
Internal stresses can degrade the mechanical properties of products by causing dimensional changes, reducing strength, and promoting failure under stress.
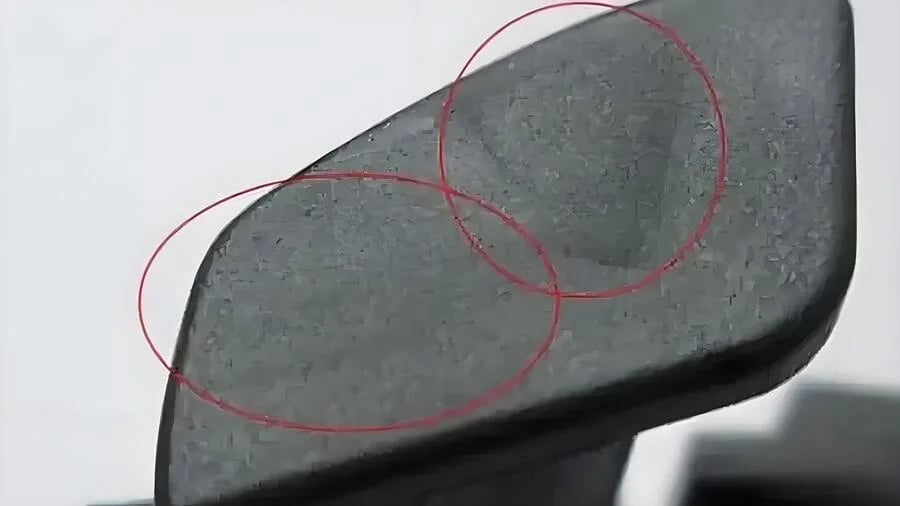
Understanding the Role of Internal Stresses
Internal stresses in injection molded products are generated due to flow imbalances, uneven cooling, and molecular orientation during the manufacturing process. These stresses can manifest in various forms, including shear stress, thermal stress, and orientation stress. Each type contributes uniquely to altering the mechanical characteristics of a product.
Dimensional Stability Challenges
Internal stresses often lead to dimensional changes post-manufacture. As these stresses relax over time, products may experience warping or shrinkage, impacting not only appearance but also functionality. For example, an incorrect fit2 in assembly operations can result from even slight dimensional deviations.
Factor | Impact on Dimensions |
---|---|
Flow Imbalance | Uneven shrinkage, warping |
Uneven Cooling | Localized expansion or contraction |
Molecular Orientation | Differential shrinkage in flow direction |
Mechanical Property Degradation
Internal stresses directly impact mechanical properties such as strength, toughness, and fatigue resistance. When these stresses are concentrated in specific areas, they can become points of weakness. Consequently, products may fail prematurely under mechanical loads, particularly if subjected to repetitive or dynamic forces.
For instance, automotive components made through injection molding must withstand significant stress over time. Internal stress concentrations can lead to cracks3 or fractures under load, compromising safety and performance.
Factors Influencing Mechanical Properties
- Material Characteristics: Different plastics exhibit varying degrees of susceptibility to internal stress. For instance, amorphous plastics may react differently compared to crystalline ones when exposed to internal stress.
- Manufacturing Parameters: The choice of injection speed, pressure settings, and cooling rates significantly influence the degree of internal stress formation. Optimizing these parameters can help mitigate adverse effects.
Mitigation Strategies
To preserve the mechanical properties of injection molded products, manufacturers can:
- Optimize Mold Design: This includes strategic placement of gates and cooling channels to promote uniform flow and cooling.
- Process Adjustments: Fine-tuning injection speed and pressure helps reduce molecular orientation stress. Implementing multi-stage injection can also alleviate flow-induced stresses.
- Post-Processing Techniques: Techniques like annealing can relax internal stresses, enhancing mechanical stability over time.
Understanding these strategies is crucial for enhancing product longevity and reliability while minimizing potential failures due to internal stresses.
Internal stresses cause product warping over time.True
Internal stresses relax, leading to dimensional changes like warping.
All plastics are equally affected by internal stresses.False
Different plastics have varying susceptibilities to internal stress.
What Appearance Defects Can Result from Internal Stress?
Internal stress in injection molded products can lead to unsightly defects that compromise both aesthetics and functionality.
Internal stress can cause various appearance defects in injection molded products, such as cracks, silver streaks, and bubbles. These issues not only mar the product’s visual appeal but may also impact its structural integrity.
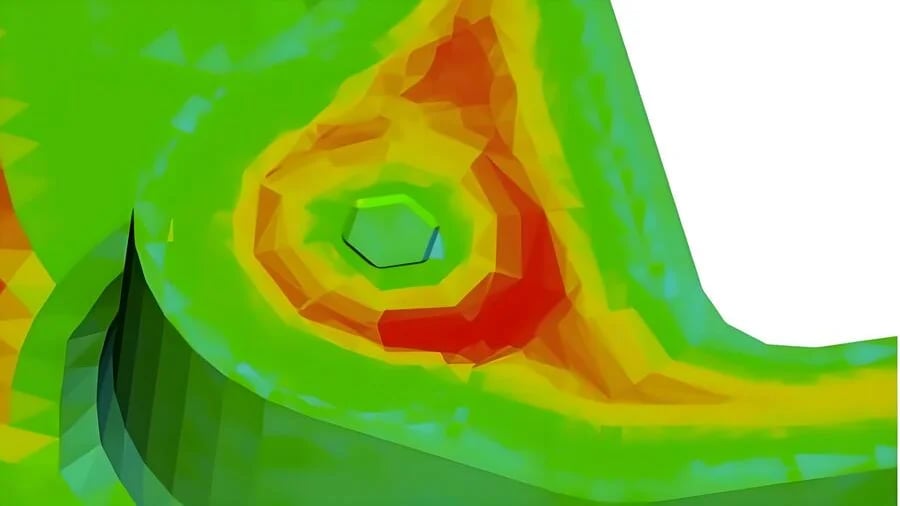
Understanding Internal Stress
Internal stress arises during the injection molding process when the plastic melt experiences uneven flow, cooling, and shrinkage. This stress manifests as defects that affect the product’s visual quality.
Common Appearance Defects
-
Cracks:
- Cracks often appear due to high internal stress concentrating in specific areas. They can occur during or after demolding.
- Factors like improper mold design or rapid cooling rates exacerbate crack formation.
-
Silver Streaks:
- These are wavy, silvery lines seen on the surface, caused by moisture or air trapped within the material during molding.
- Silver streaks are particularly noticeable in transparent products, affecting clarity and aesthetic appeal.
-
Bubbles:
- Occur when gas or air pockets form inside the product, usually due to rapid cooling or high moisture content in the plastic.
- Bubbles compromise both appearance and potentially the mechanical properties of the product.
Factors Contributing to Appearance Defects
Mold Design and Process Parameters
- Flow Imbalance: Uneven distribution of plastic melt flow can lead to defects like cracks and bubbles4.
- Cooling Rate: Inconsistent cooling causes thermal stress, contributing to defects such as warping and silver streaks.
- Molecular Orientation: High orientation levels during fast injection speeds increase the likelihood of silver streaks.
Solutions to Mitigate Appearance Defects
- Optimize mold designs by adjusting gate positions and ensuring balanced flow.
- Use multi-stage injection processes to manage molecular orientation and reduce stress.
- Implement proper cooling channel layouts to ensure uniform cooling across the product.
By addressing these factors, manufacturers can significantly reduce appearance defects in injection molded products, enhancing both aesthetic quality and performance.
Cracks in products result from rapid cooling.True
Rapid cooling causes uneven stress distribution, leading to cracks.
Silver streaks are caused by excessive heat.False
Silver streaks result from trapped moisture or air, not heat.
How Can Internal Stress Be Minimized During Injection Molding?
Minimizing internal stress in injection molding is crucial for ensuring product durability and aesthetic appeal. Effective strategies involve optimizing mold design, adjusting process parameters, and implementing post-processing techniques.
To minimize internal stress in injection molding, optimize mold design, adjust processing parameters like injection speed and pressure, and use post-processing methods such as annealing. These steps help balance flow, cooling, and molecular orientation, reducing potential defects and enhancing product quality.
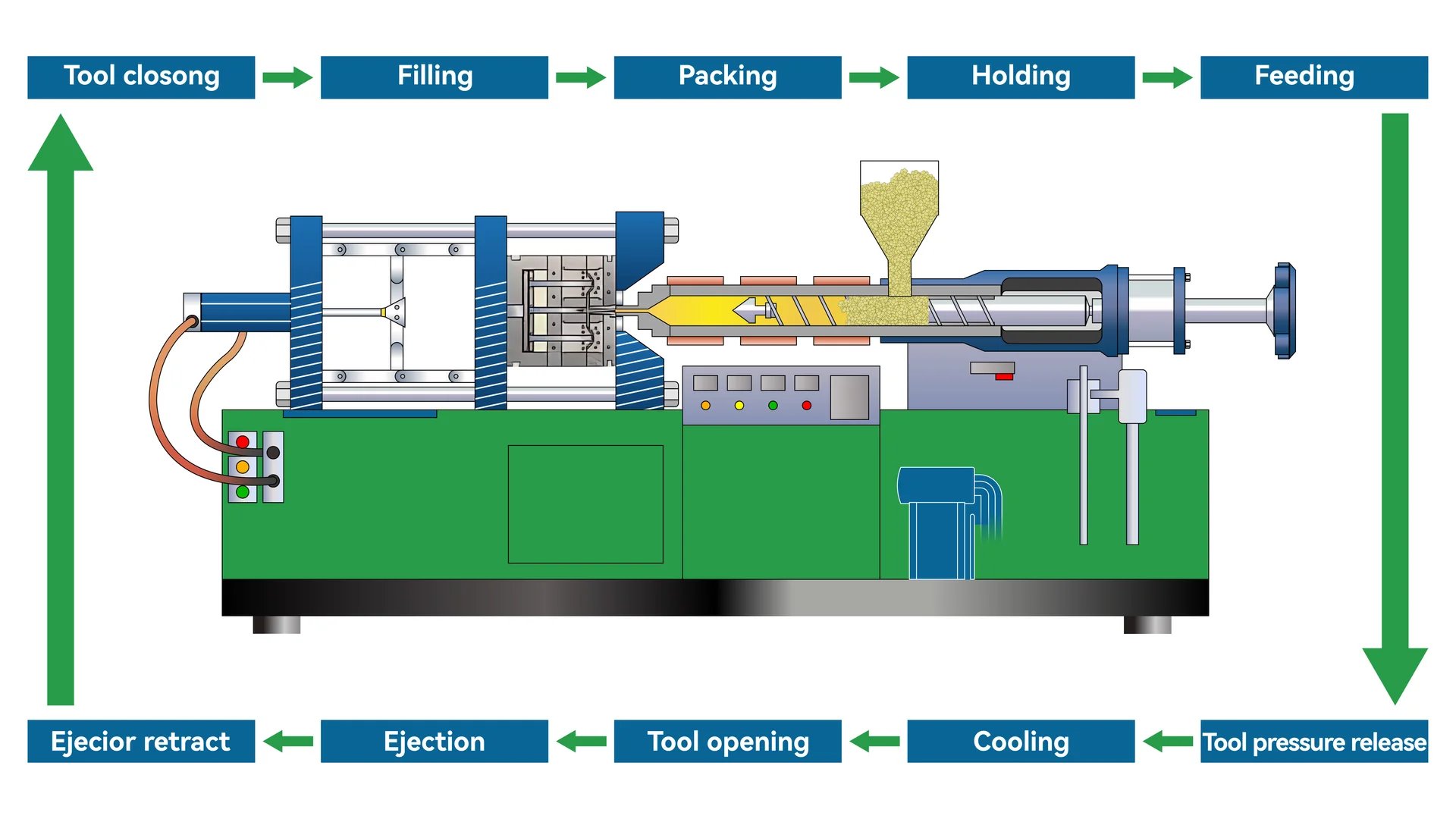
Optimize Mold Design
One of the primary ways to reduce internal stress is through careful mold design. By strategically placing gates and using multiple gate systems, manufacturers can achieve a more balanced flow of the plastic melt, which prevents shear stress accumulation. A well-thought-out design also includes optimizing runner sizes and shapes to minimize resistance, ensuring even flow across the mold.
Additionally, arranging cooling channels to facilitate uniform cooling is vital. For instance, a product with varying wall thickness can benefit from a gradual wall thickness design5, which helps maintain consistent cooling rates and minimizes thermal stress.
Adjust Injection Molding Process Parameters
Process parameters have a significant impact on the internal stress levels within an injection molded product. Reducing the injection speed and holding pressure can decrease the degree of molecular orientation, leading to less internal stress. Extending the holding time allows for reduced shrinkage rates, thereby lessening stress.
Controlling temperatures—both mold and melt—is also crucial. High melt temperatures can increase molecular orientation, so selecting appropriate temperatures based on material type is essential. Implementing a multi-stage injection process can further help manage stress by gradually adjusting speed and pressure throughout the molding cycle.
Parameter | Suggested Adjustment |
---|---|
Injection Speed | Lower to reduce orientation stress |
Holding Pressure | Lower to minimize shrinkage |
Mold Temperature | Optimize for even cooling |
Melt Temperature | Adjust based on material needs |
Post-Processing Techniques
Post-processing techniques such as annealing can significantly alleviate internal stresses in injection molded products. Annealing involves heating the product to a specific temperature, maintaining it for a set period, and then cooling it slowly. This process relaxes the molecular structure, effectively reducing stress.
For products requiring high dimensional accuracy, humidity conditioning may be applied. By placing the product in a controlled humidity environment, it absorbs moisture, which helps to adjust shrinkage and relieve stress.
These techniques collectively ensure that the final product meets quality standards and performs reliably in its intended application. Implementing such measures not only enhances durability but also extends the product’s lifespan.
Optimizing mold design reduces internal stress.True
Strategic gate placement and cooling channel design balance flow and cooling.
Higher injection speed decreases internal stress.False
Higher speed increases molecular orientation, raising internal stress.
Conclusion
By addressing internal stresses through strategic mold design and process adjustments, manufacturers can significantly enhance product quality. Embrace these strategies to minimize defects and optimize performance.
-
Explore strategies to enhance product quality through process optimization.: Best Practices To Optimize Your Injection Molding Process · 1. Regularly Monitoring and Adjusting Parameters · 2. Use of Advanced Control Systems · 3. Thorough … ↩
-
Learn how minor stress-induced changes impact assembly accuracy.: A local change of the strain during cold forming could cause a different stress state and stiffness in the product. This can enhance or lessen … ↩
-
Discover why internal stresses cause cracks under load.: (1) The existence of internal stress in the product will seriously affect the mechanical properties and performance of the product; due to the … ↩
-
Learn techniques to avoid common defects in molded products.: When conventional venting methods fail, vacuum venting can effectively solve issues related to outgassing and air entrapment in injection molds. ↩
-
Discover how gradual wall thickness design improves cooling uniformity.: Part Quality: Designing injection molded parts with wall thickness problems can result in defects like sinkholes, warping, and short shots. These problems … ↩