As I delve into the intricate world of injection molding, I often find myself reflecting on a crucial element: clamping force. It’s fascinating how something so fundamental can cause significant disruptions when it falls short.
Insufficient clamping force in injection molding machines can cause defects such as flash, dimension deviation, and surface quality problems. Adjusting system parameters, checking mold condition, optimizing process parameters, and inspecting machine hardware can help mitigate these issues.
Understanding the manifestations of insufficient clamping force is just the beginning. Join me as I explore specific adjustment methods that will equip you with the tools to enhance product quality and machine efficiency.
Insufficient clamping force causes flash in molded parts.True
Flash occurs when the mold parting surface isn't tightly sealed, allowing plastic to leak.
How Does Insufficient Clamping Force Affect Product Quality?
Insufficient clamping force during injection molding can lead to several product quality issues, impacting precision and efficiency.
Insufficient clamping force can lead to defects such as flash, dimension deviation, difficult demoulding, and surface quality issues in injection molded products. Proper adjustments and maintenance are essential to prevent these problems and ensure high-quality production.
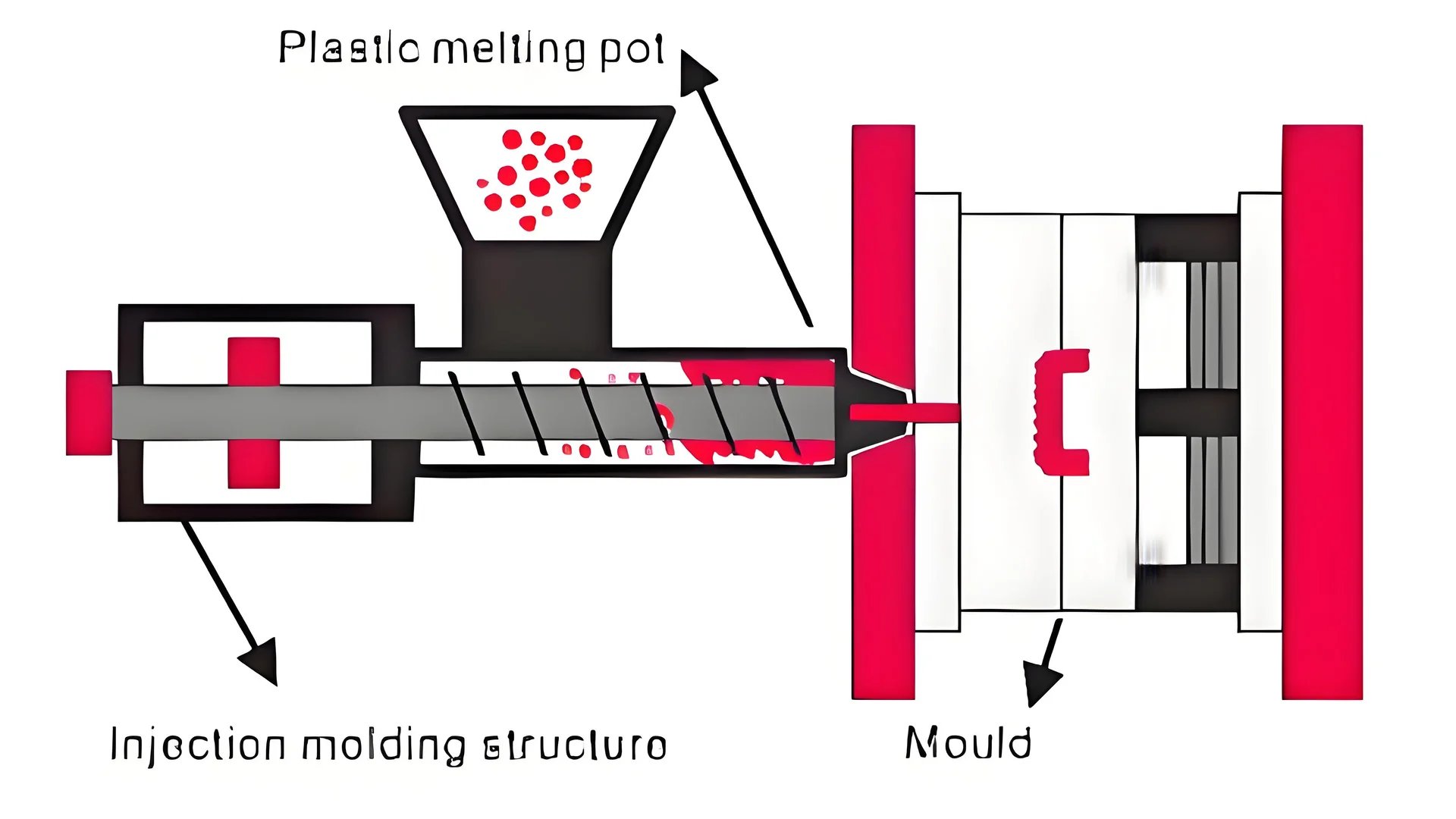
Understanding the Impact of Flash on Product Quality
One of the first visible signs of insufficient clamping force1 is the appearance of flash. Flash occurs when excess plastic leaks out of the mold cavity at the parting line due to inadequate sealing. This not only spoils the aesthetic of the product but can also hinder its functionality. For instance, flash can interfere with how components fit together or even cause issues during assembly.
Dimension Deviation and Its Consequences
When clamping force is lacking, the mold may slightly deform under injection pressure, causing deviations from the intended design specifications. This is particularly problematic for precision-engineered products where even minimal deviations can render them unusable or require costly post-processing.
Challenges in Demoulding
Another significant issue is difficult demoulding. Uneven clamping force might lead to certain areas being more tightly clamped than others, resulting in challenging release of the product from the mold. This can cause damage not only to the product but also to the mold itself, escalating repair costs and downtime.
Surface Quality Defects
Insufficient clamping force affects the stability of the mold, leading to surface defects like ripples or flow marks. These imperfections arise due to inconsistent flow patterns of the molten plastic, directly affecting the visual appeal and potentially compromising the structural integrity of the product.
Practical Steps to Mitigate Insufficient Clamping Force
Addressing these issues involves not only recognizing the signs but also implementing effective solutions. Adjusting clamping system parameters, ensuring mold cleanliness, and performing regular maintenance checks are vital steps. Regular inspections for hardware wear and ensuring proper installation can significantly enhance clamping effectiveness.
In summary, while insufficient clamping force poses significant challenges in maintaining product quality, understanding its manifestations and taking proactive measures can safeguard against defects and ensure consistent production quality.
Flash is caused by excess plastic leaking out of the mold.True
Flash occurs when insufficient clamping force allows plastic to escape.
Insufficient clamping force improves surface quality of products.False
It leads to defects like ripples, compromising visual and structural quality.
What Are the Key Steps to Adjust Clamping Force Effectively?
Adjusting clamping force is crucial in ensuring the quality of injection molded products. Without it, defects can occur.
To adjust clamping force effectively, increase clamping pressure, adjust clamping speed, ensure mold cleanliness and repair wear, optimize process parameters, and check machine hardware for defects.

Adjusting the Clamping System Parameters
The first step in adjusting clamping force involves manipulating the system’s parameters. You can increase the clamping pressure2 by gradually tweaking settings on the injection molding machine. However, this should be done cautiously to avoid damaging both the mold and the machinery. Monitoring product flash and the clamping force display value can help determine the optimal pressure.
Another parameter to consider is adjusting the clamping speed3. Reducing the speed slightly can make the process smoother and boost clamping efficiency. However, bear in mind that a slower speed may extend the cycle time, so finding the right balance is key.
Checking Mold Condition
Regular inspection and maintenance of the mold are pivotal. Begin with a thorough mold cleaning4 to ensure that no foreign substances are affecting its performance. Check for wear, particularly on the parting surfaces and guiding parts. If wear is evident, prompt repair or replacement will prevent a decrease in clamping force.
Additionally, proper mold installation adjustment5 is essential. Ensure that the mold is installed correctly with evenly tightened bolts. Tools like dial indicators can be used to verify parallelism and verticality, which are crucial for even clamping force distribution.
Optimizing Process Parameters
Fine-tuning process parameters such as injection pressure and speed can significantly affect clamping force requirements. By reducing these values6, you minimize the expansion forces on the mold, thereby decreasing the demand for excessive clamping force.
Moreover, adjusting holding time and pressure can also reduce product shrinkage, which further decreases clamping force needs.
Inspecting Machine Hardware
Finally, a detailed check of the hardware components of your injection molding machine is necessary. Inspect the clamping cylinder for leaks7, as any leakage will compromise clamping efficiency. Similarly, examine mechanical parts like elbow connecting rods and clamping nuts for wear or damage. Prompt repairs or replacements ensure that these components function optimally, maintaining stable clamping force outputs.
Increasing clamping pressure prevents product defects.True
Higher clamping pressure ensures mold stays closed, reducing defects.
Slower clamping speed always reduces cycle time.False
A slower clamping speed can increase cycle time, not reduce it.
Why Is Regular Mold Maintenance Crucial for Optimal Clamping?
Regular mold maintenance is vital for ensuring optimal clamping force, directly impacting product quality and production efficiency.
Regular mold maintenance prevents issues like flash, dimension deviation, and difficult demolding by ensuring proper clamping force. It involves cleaning, repairing wear, and adjusting installation for improved performance.

The Impact of Mold Condition on Clamping Force
In the injection molding process8, the condition of the mold is paramount to maintaining optimal clamping force. A mold that is poorly maintained can lead to a host of problems, from cosmetic defects to severe mechanical failures.
-
Cleanliness Matters: A clean mold ensures that the parting surfaces seal correctly, which is crucial for maintaining adequate clamping force. Foreign materials like dust, grease, or plastic remnants can create gaps that lead to flash, a common issue where excess material leaks out and forms burrs on the finished product.
-
Wear and Tear: Over time, molds experience wear, especially along parting surfaces and guide components. Regularly checking for wear and repairing or replacing worn parts can prevent insufficient clamping force that leads to dimensional deviations.
-
Installation Integrity: Proper installation of the mold is essential. Misalignment or improperly tightened bolts can cause uneven clamping force, leading to difficult demolding and potential damage to both the product and the mold itself.
Methods for Effective Mold Maintenance
-
Routine Cleaning: Implementing a routine cleaning schedule9 helps maintain mold integrity and performance. This includes removing any residue from previous runs and ensuring all moving parts are lubricated properly.
-
Inspection for Wear: Regular inspections should focus on identifying wear in key areas. Utilizing tools like dial indicators can help ensure that the mold’s parallelism and verticality are maintained.
-
Repair and Replacement: Addressing any signs of wear immediately can prolong the life of the mold and enhance clamping force efficiency. Mold components such as inserts or bushings should be replaced when necessary to prevent broader system failures.
-
Proper Storage: When not in use, molds should be stored properly to avoid corrosion and damage. This includes using rust inhibitors and keeping them in a controlled environment.
By prioritizing these maintenance activities, you can significantly improve the longevity and performance of your molds, leading to more efficient production cycles and higher quality products. For more comprehensive strategies on maintaining mold health, consider exploring advanced maintenance techniques10 employed by leading manufacturers.
Regular mold maintenance prevents flash formation.True
Maintenance ensures parting surfaces seal correctly, avoiding flash.
Poorly maintained molds have no effect on clamping force.False
Neglected molds can cause uneven clamping, affecting product quality.
What Role Do Process Parameters Play in Maintaining Clamping Force?
In injection molding, process parameters are crucial for ensuring the clamping force is effective and consistent.
Process parameters such as injection pressure, speed, and holding time directly influence clamping force. Properly adjusting these parameters can prevent defects like flash and improve overall product quality.

Understanding the Importance of Injection Pressure and Speed
Injection pressure and speed are primary process parameters that impact clamping force. High injection pressure can lead to excessive force on the mold, which may cause defects such as flash. By adjusting the injection pressure and speed11, manufacturers can manage the force exerted on the mold, ensuring it remains within safe limits while maintaining product quality.
Holding Time and Pressure: Key Players
Holding time and pressure are equally vital in maintaining clamping force. They influence the cooling and solidification of the plastic within the mold, affecting shrinkage and final product dimensions. Appropriate adjustment of these parameters ensures that the product maintains its intended shape and size, reducing the need for excessive clamping force.
Parameter | Effect on Clamping Force |
---|---|
Injection Pressure | Higher pressure increases mold stress, requiring more clamping force. |
Injection Speed | Faster speeds can lead to uneven flow and increased mold stress. |
Holding Time | Longer times allow for better cooling but may increase cycle time. |
Holding Pressure | Adjusting pressure helps control shrinkage and improve dimensional accuracy. |
Optimizing Through Experimentation
Fine-tuning these parameters requires experimentation and a thorough understanding of the material properties. Reducing injection pressure and speed12 without compromising product quality can significantly decrease the demand for high clamping force, enhancing both efficiency and sustainability.
The Role of Advanced Monitoring Systems
Utilizing advanced monitoring systems can aid in tracking the performance of process parameters in real-time. These systems provide valuable data that can be used to make informed decisions about parameter adjustments, ensuring optimal clamping force is maintained throughout the production process.
Process parameters are integral to maintaining clamping force within optimal ranges, ensuring product quality while enhancing machine performance.
Higher injection pressure increases mold stress.True
High pressure exerts more force on the mold, requiring increased clamping.
Longer holding time reduces cycle time in molding.False
Longer holding time allows better cooling but increases cycle time.
Conclusion
By addressing insufficient clamping force through understanding and proactive adjustments, I can significantly enhance product quality and extend machine longevity.
-
Understand how flash impacts both aesthetics and functionality of products.: The presence of flash can affect the quality and appearance of plastic parts, and may even impact their performance and lifespan. If these … ↩
-
Learn how to adjust clamping pressure safely and effectively.: Set the required clamping force first, and then set the high-pressure clamping pressure proportionally. The system pressure of the machine with different … ↩
-
Discover methods to find the optimal clamping speed.: In the jog state, set the clamping pressure to 0, slow down the clamping speed, and set the position to 0. Because the machine itself has a certain pressure … ↩
-
Find tips on maintaining mold cleanliness for better performance.: The 5 Injection Mold Cleaning Methods · Chemical cleaning · Ultrasonic immersion cleaning · Dry ice blasting · Soft plastic media blasting · Laser cleaning. ↩
-
Ensure proper mold installation for uniform clamping force.: 1. Check that the mold will cover at least 70% of the distance between the tiebars. · 2. Ensure the safety strap is in the correct position and … ↩
-
Explore how to adjust process parameters for reduced clamping force.: Steps to INJECTION MOLDING Process Optimization · 1. Tool functionality examination · 2. Short shot testing · 3. Gate seal studies · 4. Sample parts evaluation/data … ↩
-
Identify leak detection techniques for maintaining clamping efficiency.: To help identify an active leak, you can use a spray bottle filled with soapy water. Spray the soapy water onto suspected areas of the cylinder,. ↩
-
Understand how mold condition affects injection molding performance.: If the mold temperature is too high, the melt may undergo thermal decomposition, increasing the shrinkage rate in the air, causing the product … ↩
-
Learn effective cleaning schedules to maintain mold performance.: Mold-Focused Cleaning Instructions (Weekly & Quarterly Cleaning) · The Air: Clean the air you breathe using purifiers, mold candles, or foggers. ↩
-
Discover advanced methods for maintaining mold health and efficiency.: This should include cleaning the mold regularly to remove debris and buildup, lubricating the mold to help prevent wear and tear on the moving … ↩
-
Learn how these parameters influence mold stress and clamping efficiency.: If this pressure is not set high enough the mold will be forced open prematurely by injection pressure and will create flash on the related part … ↩
-
Discover how reducing these can enhance efficiency and sustainability.: Before application of injection pressure, it is important to let the material settle and molecules form cohesive bonds to reduce cavities. ↩