In the world of electronics manufacturing, innovation isn’t just a buzzword—it’s the lifeblood that keeps the industry thriving. Injection molding is at the forefront of this evolution, witnessing transformative changes driven by advanced design and technology.
Innovative design is transforming injection molded electronic equipment by integrating new materials, optimizing structural designs, and employing advanced manufacturing technologies. These changes enhance product performance, efficiency, and sustainability in complex environments.
But there’s so much more to discover! As we dive deeper into the specifics of these innovations, you’ll see how they can significantly influence your approach to product development.
3D printing reduces mold creation time in injection molding.True
3D printing accelerates mold creation by allowing rapid prototyping and iteration.
- 1. What Role Does Material Selection Play in Innovative Injection Molding?
- 2. How Are Structural Design Innovations Enhancing Electronics Manufacturing?
- 3. In What Ways Is Technology Revolutionizing Injection Molding Processes?
- 4. How Does Intelligent Manufacturing Influence Quality and Efficiency?
- 5. Conclusion
What Role Does Material Selection Play in Innovative Injection Molding?
Material selection is pivotal in innovative injection molding, directly impacting the performance, sustainability, and cost-effectiveness of electronic components.
Material selection in innovative injection molding determines the mechanical, thermal, and environmental properties of electronic components. It involves choosing high-performance plastics, eco-friendly materials, and composite materials to meet specific product requirements and enhance overall performance.

Exploring High-Performance Materials
The selection of high-performance materials is crucial for products that must endure demanding conditions. Engineering plastics like polycarbonate (PC) and polyetheretherketone (PEEK) offer superior strength, heat resistance, and insulation. For instance, using PEEK in high-end equipment1 enhances durability under high temperatures and pressures.
Embracing Eco-Friendly Materials
As sustainability becomes more pressing, the use of biodegradable and renewable materials is on the rise. Bio-based plastics such as polylactic acid (PLA) are increasingly popular, reducing reliance on petroleum-based alternatives. These materials are ideal for components like charger shells where environmental impact is a concern.
Material | Properties | Application Example |
---|---|---|
Polycarbonate | High strength, transparency | Protective covers, housings |
PEEK | High temperature resistance | High-end electronic equipment shells |
PLA | Biodegradable, renewable | Eco-friendly electronic accessories |
Developing Composite Materials
Composite materials leverage the strengths of multiple substances to create injection-molded products with unique properties. By combining plastics with fibers or metal powders, manufacturers can enhance strength and rigidity while reducing weight. For example, plastic-glass fiber composites2 are ideal for structural parts in electronic devices due to their lightweight yet robust nature.
Material Selection and Design Innovation
Innovative material selection goes hand-in-hand with design innovation. A thin-wall design can minimize material usage without compromising strength, contributing to lighter, cost-effective products. By choosing appropriate materials, designers can incorporate internal structures like reinforcing ribs to bolster stability and heat dissipation.
The role of material selection in injection molding is multifaceted, affecting not just the functional aspects but also the aesthetic and environmental implications of electronic products. By continuing to explore advanced materials and combining them with innovative design principles, manufacturers can push the boundaries of what’s possible in electronic equipment production.
PLA is a non-renewable material used in electronics.False
PLA is biodegradable and made from renewable resources.
PEEK enhances durability under high temperatures.True
PEEK offers superior heat resistance, ideal for harsh conditions.
How Are Structural Design Innovations Enhancing Electronics Manufacturing?
Structural design innovations are propelling electronics manufacturing into a new era, emphasizing efficiency and sustainability.
Structural design innovations in electronics manufacturing focus on optimizing component layouts, integrating multifunctionality, and employing lightweight materials to enhance performance, reduce costs, and meet environmental standards.

Optimizing Component Layouts
One major advancement in structural design is the optimization of component layouts. By redesigning the internal structures of electronic devices, such as adding reinforcing ribs and support columns, manufacturers can enhance the stability and durability of products. For instance, internal structure optimization3 in charger shells improves heat dissipation by incorporating heat channels, a critical factor for devices generating significant heat.
Integrating Multifunctionality
Another innovative approach is integrating multiple functions into a single injection-molded product. This not only reduces the number of components within electronic devices but also boosts integration and reliability. A prime example is combining antennas and sensors within a device’s shell, which conserves space and enhances performance. Multi-function integrated design4 streamlines manufacturing processes and offers a more robust product to consumers.
Employing Lightweight Materials
The adoption of lightweight materials is a pivotal innovation in structural design. Using engineering plastics like PEEK or bio-based materials like PLA not only reduces the weight of devices but also improves their environmental footprint. For instance, mobile phone shells benefit from thin-wall design5, which minimizes material use while maintaining strength.
Material Type | Benefits |
---|---|
Polycarbonate | High strength and heat resistance |
PEEK | Excellent mechanical strength and temperature resistance |
PLA | Eco-friendly and biodegradable |
Emphasizing Personalization
Personalization in structural design is becoming increasingly important to meet consumer demands for unique products. By employing advanced color and surface treatment innovations6, manufacturers can create aesthetically pleasing devices with distinctive textures and colors. Techniques like nano-coating enhance both appearance and wear resistance, contributing to a product’s premium feel.
These structural design innovations are redefining the landscape of electronics manufacturing, providing opportunities for improved performance, cost-efficiency, and ecological benefits. As the industry continues to evolve, these advancements will play a crucial role in shaping future developments.
Optimized layouts enhance device durability.True
Redesigning internal structures like adding ribs improves stability.
Integrating multifunctionality reduces component count.True
Combining functions into single parts conserves space and boosts reliability.
In What Ways Is Technology Revolutionizing Injection Molding Processes?
The landscape of injection molding for electronics is evolving rapidly with technological advancements leading the charge. These innovations are reshaping processes, making them more efficient and versatile.
Technology is revolutionizing injection molding by introducing 3D printing for mold creation, enhancing mold treatment techniques, and integrating intelligent manufacturing systems, thereby improving production efficiency and product quality.
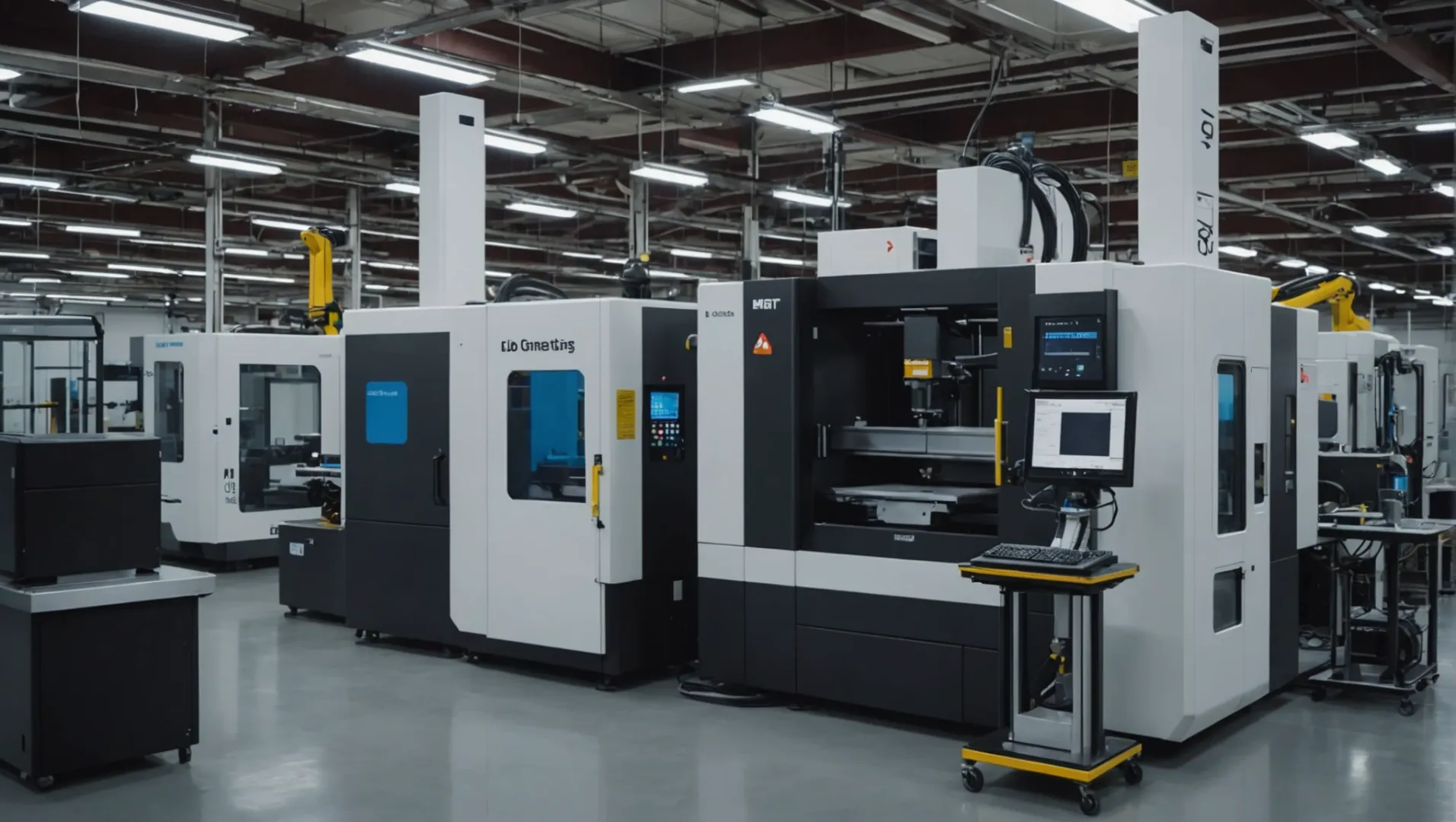
3D Printing in Mold Creation
One of the most significant advancements in injection molding is the use of 3D printing technology7 to create molds. This approach drastically reduces the time and cost involved in traditional mold manufacturing. Particularly for complex shapes, 3D printing offers a precision that traditional methods struggle to match. For instance, small electronic device components can now be quickly prototyped and tested using 3D-printed molds, facilitating rapid iteration and innovation.
Advanced Mold Treatment Techniques
Another critical development is in the realm of mold surface treatment. Techniques such as nano-coating and laser processing are being employed to enhance mold durability and efficiency. These treatments improve wear resistance and corrosion resistance, significantly extending the lifespan of molds. Furthermore, they enhance demolding performance, which boosts production efficiency and reduces waste. For example, nano coatings reduce friction between the mold and the plastic, enabling easier demolding and a smoother finish on the product.
Optimized Mold Structure
Innovations in mold design, like hot runner and flip mold technologies, are also transforming the injection molding landscape. These technologies optimize plastic flow within molds, improving the speed and uniformity of filling processes. This results in fewer defects, such as shrinkage or warping, thus enhancing overall product quality. The use of hot runners, for example, helps in minimizing material wastage and speeds up cycle times by maintaining an optimal temperature throughout the mold.
Intelligent Manufacturing Systems
The introduction of intelligent manufacturing technologies is another game-changer. Automated production lines equipped with robots handle tasks ranging from picking and placing to inspection. This not only increases production efficiency but also minimizes human error. Additionally, real-time data acquisition and monitoring systems ensure constant oversight of critical parameters such as temperature and pressure. These systems help in early detection and correction of potential issues, reducing downtime and ensuring consistent quality.
The integration of big data and AI into quality management further enhances this aspect. By analyzing vast amounts of production data, these systems predict quality issues before they arise, allowing for proactive adjustments. This results in improved product consistency and reliability.
Together, these technological advancements are not just enhancing current injection molding processes but also paving the way for future innovations that could redefine electronic equipment manufacturing altogether.
3D printing reduces mold creation time significantly.True
3D printing allows rapid prototyping, cutting down traditional mold manufacturing time.
Intelligent systems increase injection molding errors.False
Intelligent systems reduce errors by automating tasks and monitoring critical parameters.
How Does Intelligent Manufacturing Influence Quality and Efficiency?
In the era of smart manufacturing, how does technology enhance quality and efficiency in production?
Intelligent manufacturing enhances quality and efficiency by integrating automation, real-time data monitoring, and AI-driven quality management systems. This approach minimizes errors, optimizes resources, and boosts productivity in electronic equipment manufacturing.

The Role of Automation in Manufacturing Efficiency
Automation is at the heart of intelligent manufacturing, streamlining processes that were once manual and labor-intensive. By employing automated production lines and robotic systems, manufacturers can significantly reduce human error and increase consistency. For example, in injection molding operations, robots can handle tasks such as part retrieval and quality inspection, ensuring precision and reliability.
- Benefits of Automation:
- Increased Speed: Automated systems can operate continuously without fatigue, boosting production rates.
- Consistency: Uniformity is maintained across batches, enhancing overall product quality.
Real-time Data Acquisition and Monitoring
Intelligent manufacturing leverages sensors and IoT devices to collect real-time data on critical parameters such as temperature, pressure, and material flow. This data is crucial for monitoring process conditions8 and making instantaneous adjustments to maintain optimal performance.
- Impact on Quality:
- Immediate Problem Detection: Issues are identified early, reducing the risk of defective products.
- Process Optimization: Data insights enable fine-tuning of machinery for better efficiency.
AI-driven Quality Management Systems
Artificial intelligence plays a pivotal role in the quality management of injection molded products. AI systems analyze large datasets to predict potential defects, allowing proactive measures to be taken. These systems can evaluate size, shape, and surface quality to ensure standards are consistently met.
- Advantages of AI Integration:
- Predictive Maintenance: AI forecasts equipment failures before they occur, minimizing downtime.
- Enhanced Decision Making: Informed decisions are made based on predictive analytics, improving resource allocation and operational strategies.
The integration of these intelligent technologies not only refines production quality but also improves overall efficiency. This transformation allows manufacturers to meet stringent industry standards while maintaining competitive advantages in the global market.
Automation reduces human error in manufacturing.True
Automation replaces manual tasks, increasing precision and consistency.
AI systems cannot predict defects in production.False
AI analyzes data to foresee defects, enabling proactive measures.
Conclusion
Innovative design in injection molding is pivotal for advancing electronic equipment manufacturing. By embracing these trends, professionals can enhance product quality and sustainability, driving industry progress.
-
Discover how PEEK enhances durability in harsh environments.: PEEK is a highly-machinable semi-crystalline thermoplastic that has excellent heat resistance, mechanical strength, and chemical resistance. ↩
-
Explore the benefits of lightweight and strong composites.: After glass fiber reinforcement, glass fiber is a high-strength material, which also greatly improves the strength of plastics, such as: tensile strength, … ↩
-
Discover how optimized internal structures enhance product durability and efficiency.: Improves Product Performance. One of the main benefits of design optimization is its power to elevate the performance of metal parts by strategically trimming … ↩
-
Learn how integrating multiple functions streamlines manufacturing and improves reliability.: Our integrated design-build approach allows us to proactively identify and solve problems, saving the client time, money and the hassle of … ↩
-
Explore how thin-wall designs reduce material use while ensuring strength.: Thin-wall molding offers greater component design flexibility that conventional injection molding processes are incapable of, such as continuous … ↩
-
Find out how advanced treatments enhance product aesthetics and durability.: Laser surface texturing is a non-contact metal finishing technique that uses high-powered lasers to create precise patterns and textures on metal surfaces. ↩
-
Discover how 3D printing accelerates mold creation and reduces costs.: In this webinar, we’ll show you how to use stereolithography (SLA) 3D printed molds in the injection molding process to lower costs, reduce lead times, and … ↩
-
Discover how real-time monitoring optimizes manufacturing processes effectively.: MachineMetrics production monitoring software monitors OEE, machine utilization, and downtime for maximum production efficiency and deep operational insights. ↩