Ever find yourself lost in the labyrinth of plastic manufacturing choices? You’re not alone.
Injection molding excels in high-volume, intricate plastic parts, while rotational molding is ideal for large, hollow items with uniform thickness.
When I first stepped into the world of mold design, I remember feeling overwhelmed by the sheer number of options. Choosing between injection and rotational molding felt like standing at a crossroads. But here’s the thing—understanding the nuances of each can truly empower your decision-making. Injection molding, with its precision and speed, is like a well-oiled machine perfect for high-volume tasks. On the other hand, rotational molding offers a slower, yet robust alternative for larger products. It’s like comparing a sprinter to a marathon runner—each excels in its own field. By diving into their unique characteristics and applications, you can align your choice with your project’s goals. Just like when I finally cracked the code, you’ll find that sweet spot where efficiency meets creativity.
Injection molding is suitable for high-volume production.True
Injection molding allows for rapid production of numerous identical parts.
Rotational molding cannot create hollow products.False
Rotational molding is ideal for making large, hollow items with uniform walls.
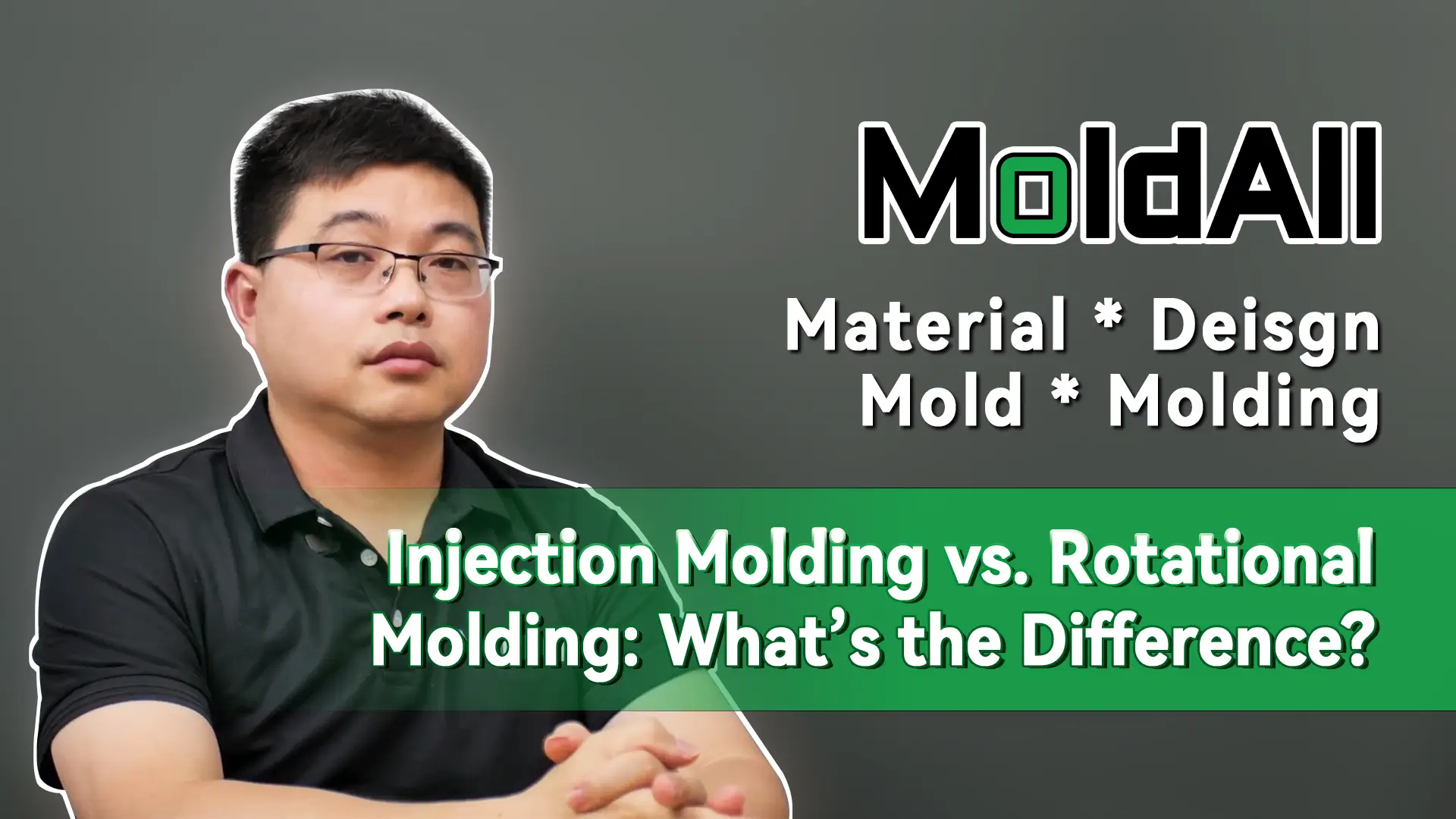
- 1. How do injection and rotational molding processes differ?
- 2. How Do Mold Design and Costs Compare Between These Methods?
- 3. What Types of Materials Are Best Suited for Each Molding Technique?
- 4. How Does Production Speed Affect Manufacturing Decisions?
- 5. Which method best suits your product needs?
- 6. Conclusion
How do injection and rotational molding processes differ?
Have you ever marveled at the intricate shapes of everyday plastic items and wondered how they’re made?
Injection molding involves injecting molten plastic into a mold using a rotating screw, while rotational molding heats and rotates a mold to form hollow shapes. Each method suits different product needs.
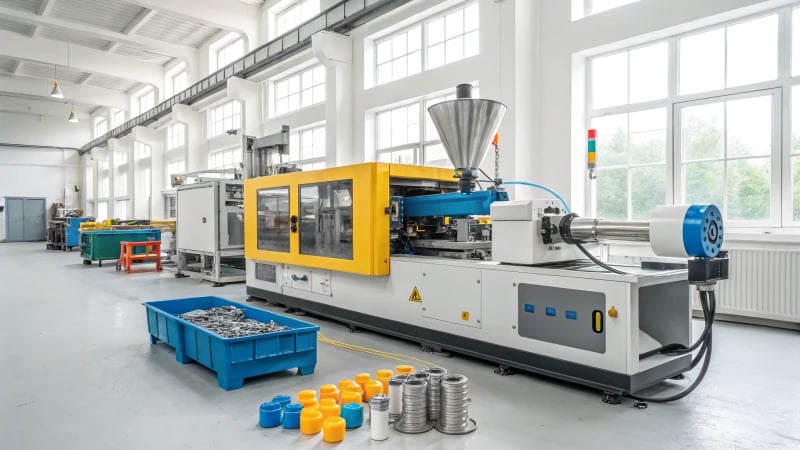
Process Principles Explained
Injection Molding:
Imagine this: I was standing in a factory for the first time, watching as tiny plastic pellets were transformed into precise, detailed components. Injection molding was the magic happening before my eyes. Here, the journey begins with those pellets being fed into a heated barrel. The real wizardry is in the rotating screw, which melts the plastic and pushes it into a mold cavity at high pressure. It’s like watching a sculptor work with clay but with machines. What comes out of this process are parts with incredibly tight tolerances and intricate details, just like the keys on your keyboard.
Rotational Molding:
On the flip side, rotational molding reminds me of my childhood days when I’d spin my bike wheels just to see how fast they could go. This process starts with plastic powder or liquid inside a hollow mold. As it spins in an oven, the plastic melts and coats the mold’s interior, creating large, hollow items like storage tanks or playground slides. It’s fascinating to see how simple rotation can craft such durable products.
Criteria | Injection Molding | Rotational Molding |
---|---|---|
Process | High-pressure injection | Biaxial rotation in heat |
Material State | Molten plastic | Powdered or liquid plastic |
Product Detail | Highly detailed and complex | Generally less detailed, hollow shapes |
Mold Design and Cost
Designing molds feels like solving a puzzle where every piece must fit perfectly. In injection molding, these molds are complex and costly because they need to withstand high pressures—kind of like building a fortress. They’re crafted from durable steel to ensure precision in controlling plastic flow.
Rotational molds, however, are simpler and less expensive—imagine building a sturdy house without needing earthquake-proof foundations. They’re typically made from aluminum and don’t face the same pressure demands, making them ideal for creating those massive, hollow pieces without intricate details.
Material Usage and Product Characteristics
In our world of creation, injection molding is like having a vast palette of thermoplastics to paint with. It’s perfect for crafting intricate designs with thin-walled sections—ideal for mass production where every piece must be just right. On the other hand, rotational molding is about making big, bold statements with durable products having uniform wall thickness—perfect for things that need strength and resilience.
Production Speed and Volume
If you’re in a hurry, injection molding is your go-to. Its high speed suits high-volume demands—imagine producing thousands of identical items swiftly like an efficient assembly line. Rotational molding, though slower, takes its time to create medium-volume items with care and precision.
Understanding these differences lets us appreciate why each method fits specific needs by balancing complexity, volume, and material considerations in manufacturing diverse plastic products.
Injection molding uses high pressure for detailed parts.True
High pressure in injection molding ensures precision and detail.
Rotational molding is faster than injection molding.False
Rotational molding is slower, suitable for medium-volume production.
How Do Mold Design and Costs Compare Between These Methods?
Ever wondered why your mold design might cost an arm and a leg or just a fraction? Dive into the nuances of injection versus rotational molding to uncover how these methods shape your budget and product design.
Injection molds, made from high-grade steel, are costly due to complexity and precision. Rotational molds, often aluminum, are simpler and cheaper, ideal for making large hollow products.
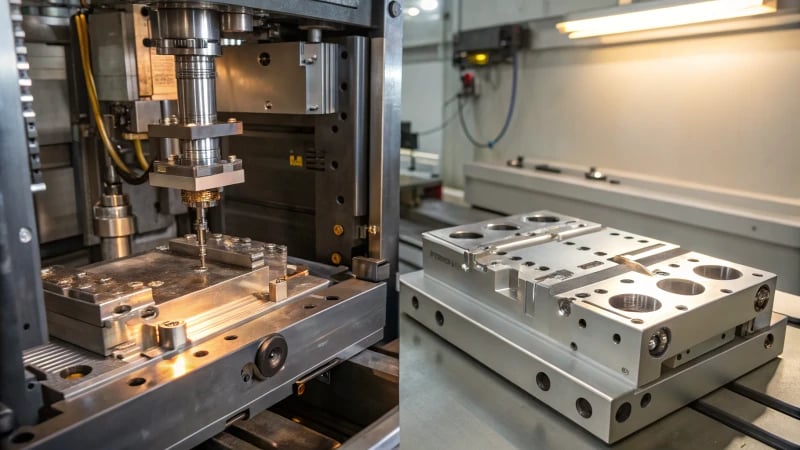
I still remember the first time I had to choose between injection and rotational molding for a project. The decision felt monumental because it wasn’t just about picking a method—it was about aligning with my project’s goals, budget, and timeline.
Injection Molding: Precision at a Price
Injection molding is like crafting a piece of art. It demands precision and high-quality materials because the molds have to endure immense pressure. I once worked on a project where the design process1 was so intricate that it felt like piecing together a puzzle, ensuring each component fit perfectly.
Aspect | Injection Molding |
---|---|
Material | High-grade steel |
Complexity | Highly complex |
Cost | Expensive |
Precision | High |
The beauty of injection molding lies in its ability to create complex shapes with tight tolerances. It’s perfect for high-volume production when every piece needs to be identical and flawless.
Rotational Molding: Cost-Effective Simplicity
On the other hand, rotational molding feels more like a hands-on craft project. The molds, often made of aluminum, are less complex and thus cheaper. I recall working on a line of large storage tanks where this method was ideal due to its simplicity and cost-effectiveness.
Aspect | Rotational Molding |
---|---|
Material | Aluminum |
Complexity | Simple |
Cost | Less expensive |
Precision | Moderate |
While rotational molds may not deliver the same level of detail as injection molds, they excel in producing durable, hollow-bodied products. This process shines when uniform wall thickness is crucial for strength and longevity.
Comparing Material Usage and Product Characteristics
Both methods share a love for thermoplastics but diverge in their final offerings. Injection molding, with its superior surface finish, supports intricate designs, making it a top choice for complex parts with thin walls.
In contrast, rotational molding’s strength lies in creating robust products with consistent wall thickness. I learned that when designing playground equipment, this uniformity is a game-changer for safety and durability.
Production Speed and Volume Considerations
The speed of injection molding is a marvel—it’s like watching a well-oiled machine at work, churning out parts rapidly for large-scale production.
Rotational molding, however, takes its time, almost like slow-cooking to perfection. Its leisurely pace is better suited for lower volume productions where quality trumps quantity.
Choosing the right method boils down to what matters most for your project. Whether it’s achieving precision or optimizing cost-efficiency, understanding these elements is crucial in making informed decisions2.
Injection molds are made from aluminum.False
Injection molds use high-grade steel for durability under pressure.
Rotational molding is suitable for large, hollow products.True
Rotational molding excels in creating large, hollow-bodied items like tanks.
What Types of Materials Are Best Suited for Each Molding Technique?
Ever wondered how the right material can make or break your next big project? Dive into the world of molding techniques and discover the perfect match for your needs.
Injection molding suits thermoplastics like polycarbonate and polypropylene for complex shapes, while rotational molding excels with polyethylene for large, hollow items.
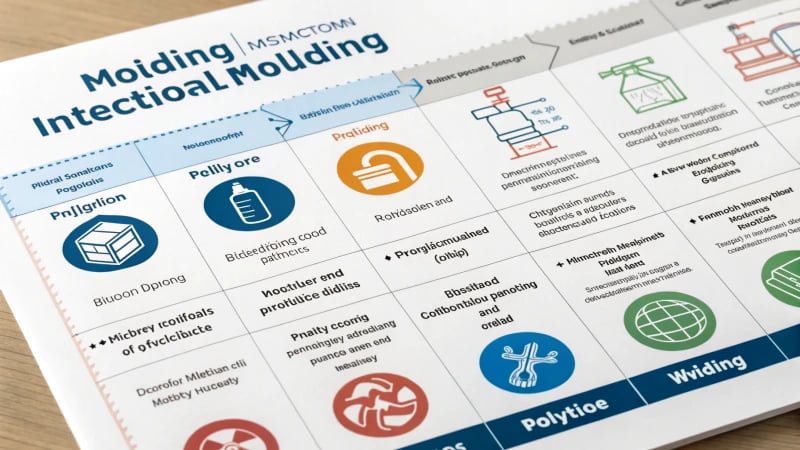
Injection Molding Materials
I remember my first project involving injection molding. The stakes were high, and picking the right material felt daunting. But soon enough, I realized that thermoplastics were my best friends. These materials could withstand the fiery temperatures and immense pressure of the process without breaking a sweat.
Material | Characteristics | Applications |
---|---|---|
Polycarbonate | High impact resistance, transparency | Eyewear lenses |
Polypropylene | Chemical resistance, lightweight | Robust yet easy-to-handle items |
These materials are not only versatile but also allow for a good surface finish, essential for aesthetic products.
Why Thermoplastics?
Thermoplastics are like the Swiss Army knife of materials. Their excellent mold flow properties allow them to squeeze into even the tiniest mold cavities effortlessly. They’re also perfect for mass production3 because they cool quickly and repeat the process consistently.
Rotational Molding Materials
When I first encountered rotational molding, I was amazed by how it created those massive, hollow structures. The secret sauce here is Polyethylene (PE). It’s been my go-to when working on larger-than-life projects.
Material | Characteristics | Applications |
---|---|---|
Polyethylene | Low cost, good impact resistance | Vast surfaces demanding strength |
Polyethylene’s ability to form uniform wall thicknesses without needing high pressures is a lifesaver for vast surfaces that demand strength.
Advantages of Polyethylene
I find polyethylene incredibly flexible and strong, making it a perfect candidate for molds that don’t need to endure high pressures. It’s a cost-effective option that doesn’t compromise on quality, especially when tackling large-scale production4.
Understanding these materials’ ins and outs has been invaluable in my journey as a product designer5. It’s this knowledge that empowers us to make decisions that truly optimize our manufacturing processes and end-product performance.
Polycarbonate is used in rotational molding.False
Polycarbonate is used in injection molding, not rotational molding.
Polyethylene offers low-cost solutions for large items.True
Polyethylene's low cost and versatility make it ideal for large products.
How Does Production Speed Affect Manufacturing Decisions?
Ever wonder how the speed of your production line can make or break your manufacturing decisions?
Production speed influences manufacturing by affecting cost efficiency, capacity, and quality. Faster production may reduce costs but risk quality, necessitating a balanced approach for optimal outcomes.

The Role of Production Speed in Cost Efficiency
I remember the first time I saw our new high-speed injection molding machine in action. The mesmerizing rhythm of the machine produced parts at a pace I’d never thought possible. We were reducing our per-unit cost6 significantly because we could churn out so many more products in the same timeframe. But, of course, there was that hefty initial investment in the equipment that made us all a bit nervous. It felt like we were betting on a horse that had never raced before.
Factor | Impact on Cost Efficiency |
---|---|
High Speed | Lower per-unit costs |
Initial Investment | Higher upfront costs |
Production Capacity and Scalability
When we cranked up the speed, our production capacity soared. Suddenly, fulfilling those large orders wasn’t a headache anymore. I recall how injection molding became our go-to for mass-producing high-volume parts, like phone casings. But then there was rotational molding – much slower, yet perfect for our smaller runs where precision mattered more than speed.
Quality Control Challenges
Here’s the thing: while speeding up our processes was thrilling, it came with its own set of hurdles. Rapid production meant a higher risk of defects slipping through if we weren’t vigilant. I remember spending long nights tweaking our quality assurance systems7 to keep our standards intact, especially with injection molding’s fast pace.
Balancing Speed with Quality
Finding that sweet spot between speed, quality, and cost became an art form. We had to decide when to embrace the slower processes like rotational molding for intricate designs and when to unleash the faster methods for simpler items. This balancing act was crucial for optimizing our production strategies8.
Real-World Examples
Take, for instance, when we switched to injection molding for our high-volume consumer electronics parts. It was a game-changer for efficiency. Yet, for custom components, rotational molding remained our best ally. By adapting to different speeds, we found the flexibility to thrive in various market scenarios, proving that understanding and balancing these dynamics is key to manufacturing success.
High production speed lowers per-unit costs.True
Increased throughput spreads fixed costs over more units, reducing costs.
Rotational molding is faster than injection molding.False
Rotational molding is slower, suitable for smaller runs, unlike fast injection.
Which method best suits your product needs?
Have you ever felt overwhelmed trying to choose the right manufacturing process?
Choose injection molding for high-volume, intricate designs with thin walls. Opt for rotational molding for large, uniform-thickness hollow products in lower volumes.
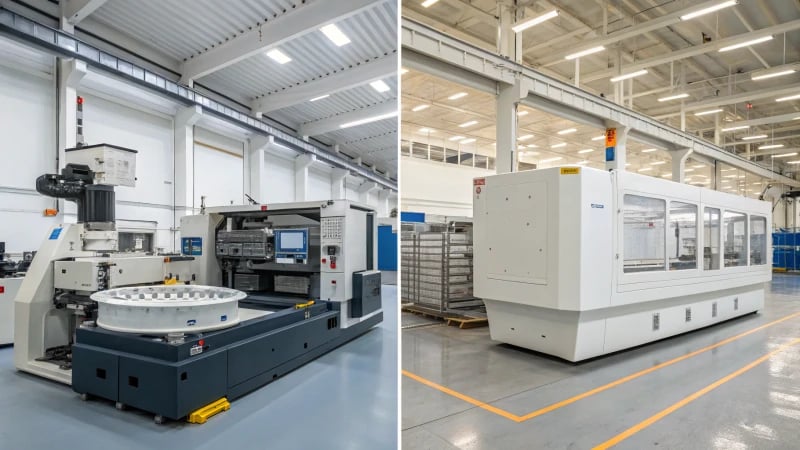
Understanding Injection Molding and Rotational Molding
I remember my first dive into the world of manufacturing. It felt like standing at a crossroads, where each path had its own challenges and rewards. Injection molding and rotational molding were these two paths. Injection molding is like a precise artist at work. Imagine feeding plastic pellets into a heated barrel, where they melt and get injected under high pressure into a detailed mold. It’s the go-to choice when you need intricate designs with tight tolerances.
Factor | Injection Molding | Rotational Molding |
---|---|---|
Mold Complexity | High – precise shapes possible | Lower – simpler mold design |
Material Form | Thermoplastic pellets | Powder or liquid thermoplastics |
Mold Design and Cost Considerations
From my experience, navigating mold design feels like balancing on a tightrope between cost and detail. With injection molding, you’re investing in precision engineering for your molds. They might be pricey, but they deliver consistently detailed products. On the flip side, rotational molds are easier on the wallet and perfect for less intricate designs.
Evaluating Material Usage and Product Characteristics
Whenever I evaluate material usage, I think about the vast landscape of possibilities that injection molding offers. You can mold a variety of thermoplastics into diverse shapes and finishes. Conversely, rotational molding is your best friend for large, hollow structures like tanks or containers—imagine them as sturdy guardians of uniform thickness.
Comparing Production Speed and Volume
In the fast-paced world of manufacturing, speed can be your ally or your adversary. Injection molding typically blitzes through production cycles, perfect for high-volume needs. Each cycle feels like a quick sprint.
Aspect | Injection Molding | Rotational Molding |
---|---|---|
Production Speed | Fast – high volume | Slower – larger products |
Volume Suitability | Ideal for high volume | Best for low to medium volume |
Understanding these factors helps me align my product needs with the right manufacturing method. Keeping the specific requirements9 in mind is crucial for achieving the best results.
Injection molding is faster than rotational molding.True
Injection molding cycles are quicker, ideal for high-volume production.
Rotational molding is best for detailed, complex shapes.False
Rotational molding suits simpler designs; injection molds handle complexity.
Conclusion
Injection molding and rotational molding are distinct processes; the former excels in high-volume, detailed parts, while the latter is ideal for large, hollow products with uniform thickness.
-
Discover how gate and runner systems control plastic flow in injection molding, crucial for precision. ↩
-
Explore key factors influencing the decision between these molding techniques. ↩
-
Exploring mass production benefits helps in understanding thermoplastic’s efficiency in large-scale manufacturing. ↩
-
Discover how polyethylene’s properties enhance rotational molding processes, offering insights into its widespread usage. ↩
-
Learn why choosing the right materials is vital in product design, impacting both functionality and aesthetics. ↩
-
Learn how production speed influences cost efficiency, helping you make informed decisions about investment and pricing. ↩
-
Explore strategies to maintain quality in high-speed manufacturing processes, ensuring product reliability and customer satisfaction. ↩
-
Discover effective strategies for balancing speed and quality in manufacturing to optimize production outcomes. ↩
-
Learn more about aligning manufacturing methods with specific product requirements. ↩