Choosing the right molding technique can feel like navigating a labyrinth of options.
Injection molding injects molten material into a mold, whereas compression molding presses pre-heated polymer into shape. The primary difference lies in the material introduction and shaping processes.
I remember my first big project where I had to choose between these two methods. It felt like deciding between night and day because each offered unique advantages. Injection molding was perfect for high-volume production with intricate designs, while compression molding excelled in simplicity and cost-effectiveness for large parts. Understanding the specifics of each process helped me make informed decisions that aligned with project goals and budget constraints. Exploring their distinct benefits, limitations, and applications can make a world of difference in your design journey.
Injection molding uses higher pressure than compression molding.True
Injection molding requires higher pressure to inject material into the mold.
Compression molding is faster than injection molding.False
Injection molding is generally faster due to its automated process.
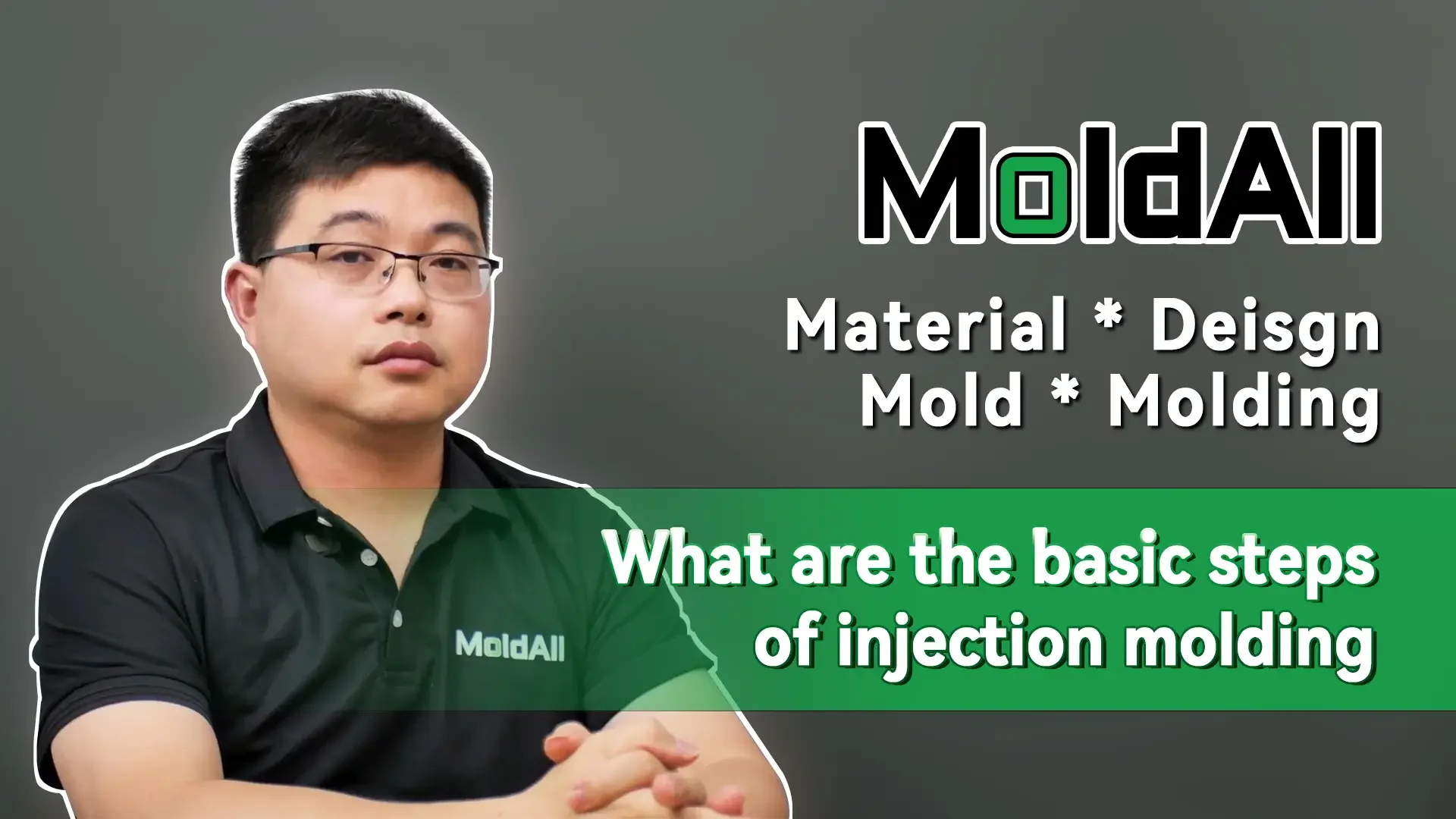
- 1. How Does Injection Molding Work?
- 2. Why Choose Compression Molding for Your Manufacturing Needs?
- 3. Which Molding Process Is More Cost-Effective?
- 4. What Types of Materials Are Best Suited for Each Method?
- 5. How Do Molding Techniques Impact Product Design?
- 6. What Machinery Do You Need for Different Molding Processes?
- 7. Conclusion
How Does Injection Molding Work?
Ever wondered how the humble plastic toy you played with as a kid was made? Dive into the fascinating world of injection molding with me!
Injection molding involves melting plastic pellets, injecting them into a mold, cooling, and then releasing a solid part. It’s efficient for mass production, offering speed, repeatability, and consistent product quality.
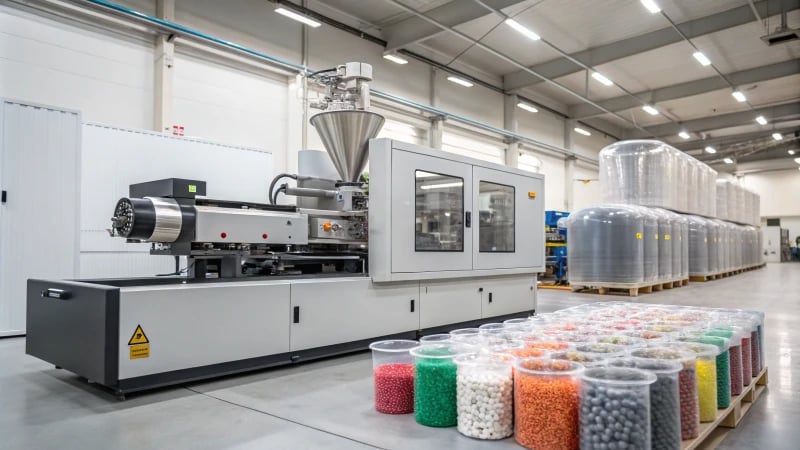
The Basics of Injection Molding
When I first learned about injection molding, it was like discovering the secret behind all those gadgets I used growing up. Essentially, the process involves several critical stages: melting, injecting, cooling, and ejecting. Let’s break it down together:
Stage | Description |
---|---|
Melting | Plastic pellets are heated until they become a molten liquid, making them ready for injection1. |
Injection | The liquid plastic is injected into a metal mold under high pressure, filling the mold cavity completely. |
Cooling | The mold is cooled to solidify the plastic, ensuring it takes on the mold’s shape accurately. |
Ejection | Once cooled, the mold opens, and the finished product is ejected, ready for inspection2. |
Types of Injection Molding Machines
Choosing the right machine can feel like picking a car—you want the best fit for your needs:
- Hydraulic Machines: These are like the SUVs of injection molding—powerful and versatile3, perfect for large parts.
- Electric Machines: Precision and energy efficiency4 are their game, ideal for crafting smaller, intricate parts.
- Hybrid Machines: The best of both worlds, combining hydraulic strength with electric precision.
Key Considerations in Injection Molding
I’ve found that careful planning can make or break a project. Here are some aspects to consider:
- Material Selection: It’s like choosing ingredients for a recipe—the right material affects durability and functionality.
- Mold Design: A well-thought-out design ensures consistency and minimizes defects, much like a blueprint for success.
- Cycle Time Optimization: Streamlining cycle times boosts productivity and cuts costs. Tools like CAD software5 can be your best friend here.
Injection molding is not just a manufacturing process; it’s a craft that transforms ideas into tangible reality. Understanding these steps can truly enhance our design prowess and lead to exceptional product quality.
Injection molding involves only three stages.False
Injection molding involves four stages: melting, injection, cooling, and ejection.
Electric machines are more energy-efficient than hydraulic ones.True
Electric machines offer precision and energy efficiency, ideal for small parts.
Why Choose Compression Molding for Your Manufacturing Needs?
Ever wondered why compression molding is a go-to technique for so many industries? Let me share why it’s a game-changer, especially if you’re in the automotive or electronics fields.
Compression molding is cost-effective and versatile, producing large, intricate parts with minimal waste. It’s ideal for high-volume production, ensuring consistent quality and durability.
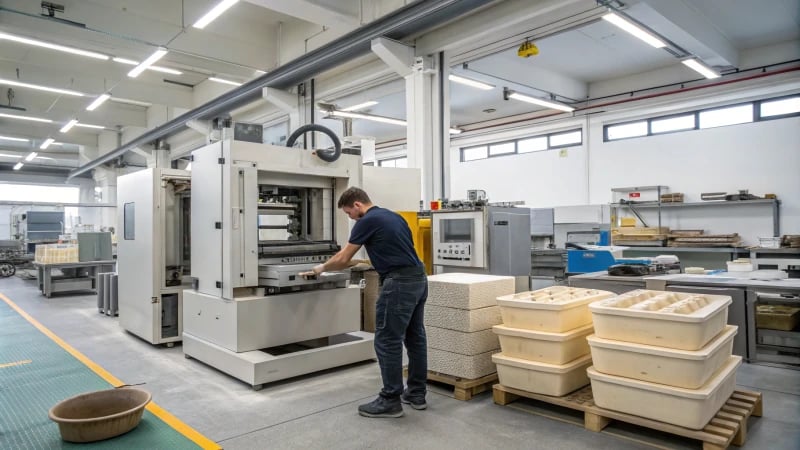
I remember the first time I encountered compression molding at work. It was like witnessing magic—the transformation of raw materials into sleek, durable components with such precision and efficiency. I was hooked! This method not only saved us money but also opened up a world of possibilities in terms of design and material choices.
Cost-Effectiveness
When I first proposed using compression molding for our project, the team was skeptical about the costs. But once we crunched the numbers, it became clear: the initial setup cost was significantly lower than other methods like injection molding. It felt like a win-win—maintaining quality without breaking the bank. It’s perfect for us when we need to manufacture on a large scale6.
Material Versatility
One of my favorite things about compression molding is its adaptability. We’ve worked with everything from thermosetting resins to advanced composites. It’s like being a kid in a candy store—so many choices to fit exactly what we need, whether it’s heat resistance or extra strength.
Efficient Production Process
The process itself is surprisingly straightforward. I remember being amazed at how little waste we produced when preheated materials were placed into the mold cavity. It was a moment of pride to see our environmental impact shrink while boosting our bottom line. Plus, with the short cycle time, we could meet tight deadlines without compromising quality.
Consistent Quality and Precision
In industries like automotive and aerospace, precision isn’t just important—it’s crucial. Compression molding consistently delivers on this front. I’ve seen it firsthand how uniform pressure across the mold results in parts that meet precise specifications every single time.
Table: Comparison of Molding Techniques
Technique | Setup Cost | Cycle Time | Material Use |
---|---|---|---|
Compression Molding | Low | Moderate | Minimal Waste |
Injection Molding | High | Short | Moderate Waste |
Blow Molding | Moderate | Long | High Waste |
This table perfectly captures why we choose compression molding so often—it just checks all the right boxes for us in terms of setup cost and material efficiency. If you’re curious about how different methods compare7 and want to explore based on specific industry needs, take a closer look at factors like part complexity or production volume.
Compression molding has higher setup costs than injection molding.False
Compression molding actually has lower setup costs compared to injection molding.
Compression molding results in minimal material waste.True
The process is efficient, ensuring minimal waste and cost savings.
Which Molding Process Is More Cost-Effective?
Navigating the maze of molding processes can feel like a daunting task, especially when your budget is on the line.
Injection molding is more cost-effective for high-volume production with lower per-unit costs and faster cycles, while blow molding is economical for simpler, hollow designs in smaller quantities.
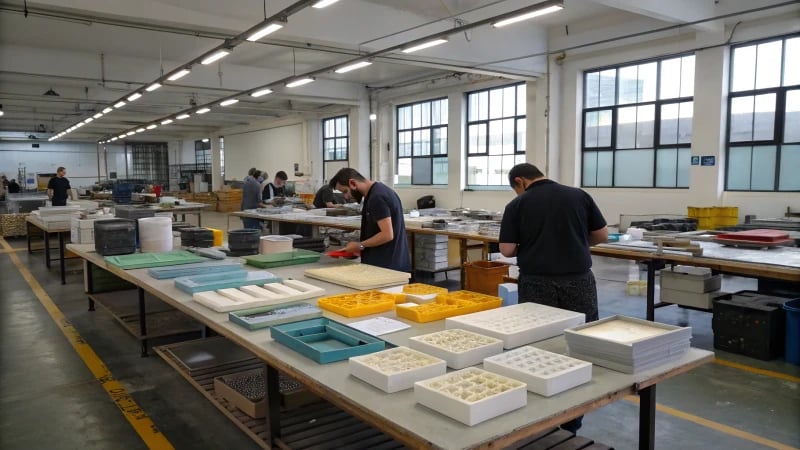
Comparing Injection Molding and Blow Molding
When I first started exploring molding processes, the sheer variety of options felt overwhelming. Injection Molding quickly stood out for its ability to churn out complex shapes at high volumes. The initial tooling costs might make you wince, but trust me, they’re a small price to pay when you consider the low per-unit cost for large-scale production. This method was a lifesaver when I needed intricate parts for consumer electronics, where every detail mattered.
Aspect | Injection Molding | Blow Molding |
---|---|---|
Initial Cost | High (due to mold design) | Lower |
Cycle Time | Shorter | Longer |
Complexity | Suitable for complex designs | Limited to simpler shapes |
When to Choose Blow Molding
On the flip side, Blow Molding saved my day when I needed to produce hollow objects like bottles or containers. With generally lower tooling costs, it’s perfect for smaller production runs. If your project doesn’t require the complexity of injection molding but needs cost savings, blow molding could be your new best friend.
Jacky might find blow molding beneficial for projects that don’t demand intricate detailing but prioritize cost efficiency in smaller batches.
Factors Influencing Cost-Effectiveness
- Volume of Production: In my experience, injection molding shines when the demand is high. The economies of scale significantly reduce costs, making it a no-brainer for large orders. However, blow molding holds its ground for lower volumes.
- Design Complexity: Often, the design requirements dictate the choice of process. Intricate designs with varying wall thicknesses are better suited for injection molding8.
- Material Considerations: Both methods support a range of materials. The right material choice can further enhance cost efficiency, especially when balancing strength and weight.
Understanding these factors helps align your production goals with your budget constraints. Jacky could use these insights to make informed decisions that boost his company’s manufacturing prowess while keeping costs in check. By doing so, he ensures quality and affordability go hand in hand in his designs. Exploring further details on manufacturing methods9 could offer additional perspectives on optimizing production strategies.
While evaluating these factors, it’s also worth considering industry trends and technological advancements that could impact future cost structures in molding processes.
Injection molding has higher initial tooling costs.True
Injection molding requires complex molds, increasing initial setup costs.
Blow molding is ideal for intricate part designs.False
Blow molding is suited for simpler shapes, not intricate designs.
What Types of Materials Are Best Suited for Each Method?
Have you ever wondered why certain pans just seem to work better for different cooking methods?
Select materials based on cooking methods: use cast iron for slow cooking to benefit from its heat retention, and choose stainless steel for quick frying due to its even heat distribution.
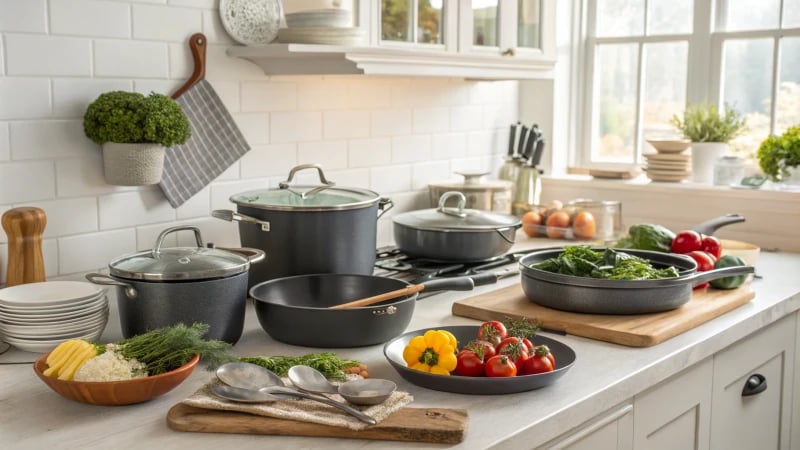
I remember the first time I used a cast iron skillet—it was a hand-me-down from my grandmother, who swore by its magical powers. I was skeptical at first, but as I slowly simmered a hearty stew, I noticed how the flavors seemed to develop in a way I’d never experienced before. It was as if the pot itself was imparting wisdom from countless meals cooked before.
Cast Iron: Ideal for Slow Cooking
That experience taught me that cast iron’s superb heat retention makes it a powerhouse for slow-cooking methods like braising or simmering. Its ability to hold a stable temperature allows flavors to meld beautifully, turning simple ingredients into a symphony of taste.
Stainless Steel: Perfect for Quick Frying
On the other hand, I turned to stainless steel when I wanted to whip up something quickly. The even heat distribution meant my food cooked uniformly without any hot spots. Plus, its non-reactive surface was perfect for my favorite tomato-based sauces, ensuring the flavors stayed true.
Material | Best Method | Benefits |
---|---|---|
Cast Iron | Slow Cooking | Excellent heat retention |
Stainless Steel | Quick Frying | Even heat distribution |
Non-stick Coating | Gentle Sautéing | Easy cleanup and food release |
Copper | Precision Cooking | Superior heat control |
Non-stick Coating: Gentle Sautéing
For those lazy Sunday mornings when making breakfast feels like an art form, I reach for my non-stick pan. Perfect for delicate foods like eggs or fish, it lets me use less oil, which is always a bonus when I’m trying to eat a bit healthier.
Copper: Precision Cooking
And then there’s copper. My uncle, a retired chef, introduced me to this material when I started experimenting with sauces and candies. Copper’s superior control over cooking temperatures is unmatched, allowing me to make precise adjustments and perfect my creations without fear of burning or overcooking.
Understanding these materials has transformed my kitchen game, making me feel like I’ve unlocked a secret level in culinary mastery. For more insights on heat retention properties10, explore resources that delve into material science and cooking performance. Discovering how the interaction between metals11 can revolutionize your kitchen experience is fascinating and empowers you to optimize your culinary techniques.
So, next time you’re in the kitchen, remember that selecting the right material for the right method is your ticket to unlocking new culinary potentials. Happy cooking!
Cast iron is ideal for quick frying.False
Cast iron is best suited for slow cooking due to heat retention.
Copper cookware offers superior heat control.True
Copper provides precise temperature management, ideal for precision cooking.
How Do Molding Techniques Impact Product Design?
Have you ever wondered how the art of molding shapes our everyday products?
Molding techniques impact product design by affecting material selection, production efficiency, and surface finish. Designers balance these factors to optimize aesthetics, functionality, and cost-effectiveness.
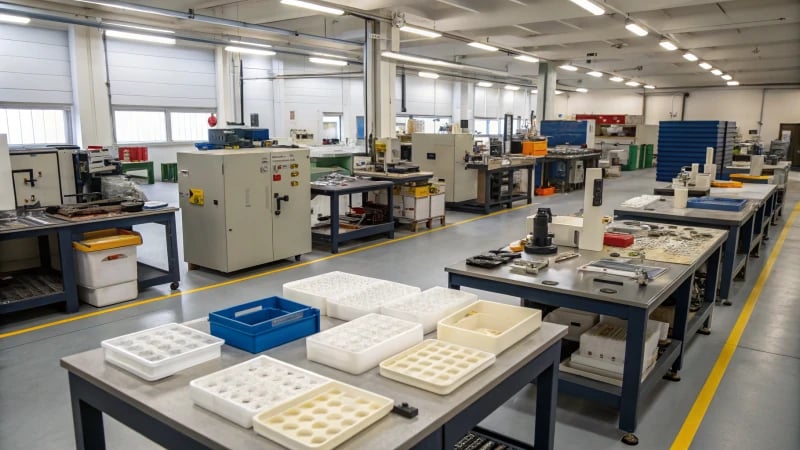
The Role of Molding Techniques in Material Selection
When I first started working in product design, I remember being amazed at how different molding techniques demanded unique material choices. It was like finding the right dance partner—the perfect balance of compatibility and chemistry. Take injection molding, for example; it’s a go-to for thermoplastics due to its versatility and efficiency. On the other hand, compression molding reminded me of those slow-burn friendships—perfect for thermosetting plastics with a little more patience and precision required. Understanding these subtleties helped me select appropriate materials12 that didn’t just look good on paper but performed well in real life.
Production Efficiency and Cost Considerations
The excitement of seeing my designs come to life never gets old, but I quickly learned that production efficiency is key to making that happen smoothly. Injection molding became my ally in large-scale projects—it’s like having a fast car in a slow race. Its ability to churn out thousands of parts with minimal waste was a game-changer. But for those times when I needed creativity to flow into complex shapes, rotational molding13 was my tool of choice, even if it meant longer cycle times.
Technique | Ideal For | Pros | Cons |
---|---|---|---|
Injection Molding | High-volume production | High efficiency, low waste | High initial tooling cost |
Compression Molding | Strong, complex shapes | Excellent strength properties | Longer cycle times |
Rotational Molding | Large, hollow items | Uniform wall thickness | Slow production speed |
Surface Quality and Aesthetic Appeal
When I was working on a sleek electronics project, the surface finish was everything. Injection molding came through with its ability to create those smooth, detailed surfaces that just felt right under your fingertips. But there were times I needed blow molding’s charm—for instance, when creating a bottle that had to hold its own in both design and function. Sure, the finishes weren’t as precise, but they were just what I needed for hollow products like bottles.
Impact on Design Flexibility
I’ve always found joy in experimenting with design flexibility. Some projects demanded quick changes and custom shapes, and thermoforming techniques14 were my best friends during those times. They allowed me to test ideas rapidly without the hefty price tags of other methods. However, every technique came with its own set of limitations, and navigating these was part of the art of design.
By diving deep into these techniques, I learned that molding isn’t just about shaping materials; it’s about shaping possibilities. Understanding these nuances has not only made me a better designer but also opened doors to innovation and efficiency in my projects.
Injection molding is ideal for high-volume production.True
Injection molding efficiently produces large quantities with minimal waste.
Rotational molding produces the fastest cycle times.False
Rotational molding is slower, ideal for complex shapes and uniform thickness.
What Machinery Do You Need for Different Molding Processes?
Have you ever wondered what machinery is behind the molding magic we encounter every day?
Different molding processes require specific machinery: injection molding uses an injection molding machine, and blow molding uses a blow molding machine. Selecting the appropriate machinery is vital for precise and efficient production.
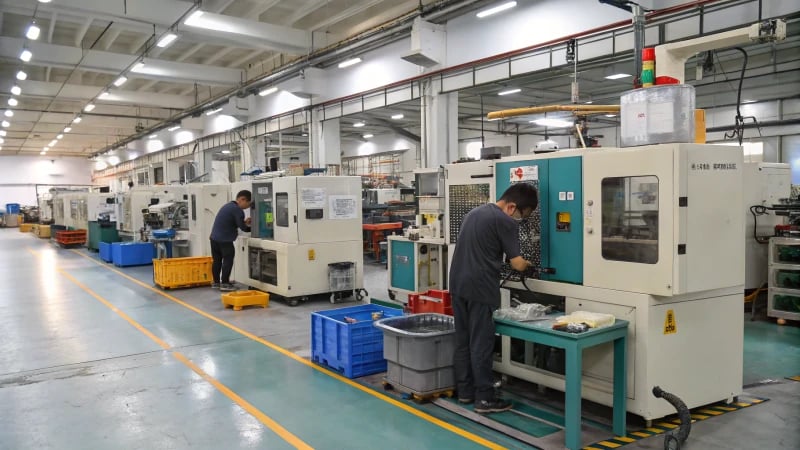
I remember the first time I walked into a manufacturing plant. The hum of machinery was almost melodic, each piece of equipment playing its part in this mechanical orchestra. Let’s dive into the specific machinery needed for various molding processes—something I find both fascinating and crucial for anyone in our field.
Injection Molding
Injection molding has always intrigued me with its precision and efficiency. At its heart is the injection molding machine, a marvel of engineering with its hopper15, barrel, screw, and nozzle, all working together to melt and inject materials. Then there’s the mold base, typically steel or aluminum, which securely holds the mold cavity. The clamping unit, like a steadfast guardian, keeps the mold shut tight during the injection. You can find more details about these components here16.
Blow Molding
Blow molding reminds me of my childhood days when I would watch glassblowers create magic from molten glass. The process uses an extruder to melt plastic into a parison—a fascinating spectacle in itself. The blow mold then shapes the molten form as air is blown in through the blow pin.
Machinery Component | Function |
---|---|
Extruder | Melts plastic |
Blow Mold | Shapes part |
Blow Pin | Inflates parison |
If you’re as curious as I was back then, check out more about these tools here17.
Compression Molding
This process is like watching dough being pressed into perfect cookie shapes. Compression molding requires a press to apply pressure and shape the material. The mold cavity and core work together to form the final product. And let’s not forget the preheater, which gets everything ready beforehand.
- Compression Molding Press: Applies pressure to shape material within the mold.
- Mold Cavity and Core: Form the shape of the finished product.
- Preheater: Prepares material before molding.
For more on this process, explore here18.
Rotational Molding
Rotational molding takes me back to science classes where we learned about centrifugal force. The rotational molding machine spins the mold bi-axially, coating its interior evenly with powdered plastic. Once shaped, it cools in cooling chambers—truly an intriguing dance of science and art.
- Rotational Molding Machine: Rotates mold bi-axially to coat interior evenly.
- Cooling Chambers: Help solidify molten plastic after shaping.
- Powder Loading Station: Where raw materials are prepared for molding.
If you’re curious about the machinery behind this dance, visit here19. This method excels at creating large, hollow objects like tanks and containers.
Choosing the right machinery isn’t just about technical specs; it’s about bringing our designs to life. Understanding each component’s role is crucial for enhancing efficiency and product quality, allowing us to transform raw materials into everyday wonders.
Injection molding requires a blow mold.False
Injection molding uses a mold base, not a blow mold.
Rotational molding involves bi-axial rotation.True
The mold rotates around two axes to evenly coat the interior.
Conclusion
This article explores the differences between injection molding and compression molding, highlighting their processes, advantages, and applications to help designers choose the right technique for their projects.
-
Explore detailed insights into the injection molding process stages and their importance in manufacturing. ↩
-
Discover methods to ensure quality control in inspecting injection molded products. ↩
-
Understand why hydraulic machines are preferred for producing larger components. ↩
-
Learn about the energy-efficient benefits of using electric injection molding machines. ↩
-
Find out which CAD software enhances precision in mold design. ↩
-
Learn how compression molding supports large-scale manufacturing with cost-effective solutions. ↩
-
Compare various molding techniques to choose the best fit for your needs. ↩
-
Learn why injection molding is favored for complex designs and high-volume production. ↩
-
Stay updated on new technologies and trends impacting manufacturing processes for cost savings. ↩
-
This link provides in-depth analysis of how different materials retain heat, crucial for selecting cookware. ↩
-
Discover how metal properties affect cooking processes, enhancing your understanding of material compatibility. ↩
-
Discover which materials are most compatible with injection molding to enhance your product designs. ↩
-
Learn about the benefits of rotational molding and how it can improve your manufacturing process. ↩
-
Understand the differences between thermoforming and injection molding to choose the right process. ↩
-
Discover how hoppers facilitate material feeding in injection molding, crucial for continuous operation. ↩
-
Explore comprehensive diagrams and explanations of injection molding machine components. ↩
-
Learn about the essential parts of blow molding machines for efficient production. ↩
-
Understand compression molding tools to optimize material shaping processes. ↩
-
Gain insights into rotational molding setups for creating large hollow products. ↩