Did you ever have the problem of picking the correct way to produce something? I have and it really affects how well a product does.
Injection molding is often chosen over blow molding for products that need high dimensional accuracy and complex designs. This method is great at producing precise electronic parts. Automotive interiors benefit from injection molding. It also produces small plastic toys and medical device housings. It replicates intricate details. Maintaining tight tolerances is another strong point.
In my journey as a product designer, I’ve noticed that injection molding really shines for creating precise electronic parts and complex designs. For example, the small plastic gears in mobile phones need to fit perfectly to work well. Injection molds replicate every tiny detail. Blow molding struggles with such complexity.
Now, let’s look at automotive interiors and small plastic toys that delight children. I’ve been amazed at how injection molding creates detailed dashboard panels and toy features with finesse. Blow molding can’t compete here. In medical devices, precision becomes even more crucial. Injection molding provides the exact details needed.
Injection molding is better for precision electronic parts.True
Due to its ability to achieve high dimensional accuracy, injection molding excels in producing precision electronic components.
Blow molding is preferred for complex product designs.False
Injection molding outperforms blow molding when it comes to creating intricate designs and maintaining tight tolerances.
- 1. What Makes Injection Molding the Preferred Choice for Precision Parts?
- 2. How Does Injection Molding Enhance Automotive Interior Design?
- 3. Why Are Small Plastic Toys Ideal for Injection Molding Techniques?
- 4. How Does Injection Molding Impact the Production of Medical Devices?
- 5. How Can Designers Optimize Material Selection for Different Molding Processes?
- 6. Conclusion
What Makes Injection Molding the Preferred Choice for Precision Parts?
Injection molding stands as a popular method for creating precise parts in many industries. But why is it the preferred method? This process is fascinating and worth exploring!
Injection molding is preferred for precision parts. It offers unmatched accuracy and replicates intricate details well. This method provides high production efficiency. It suits electronics, automotive components, toys and medical devices. Injection molding is very ideal for these items.
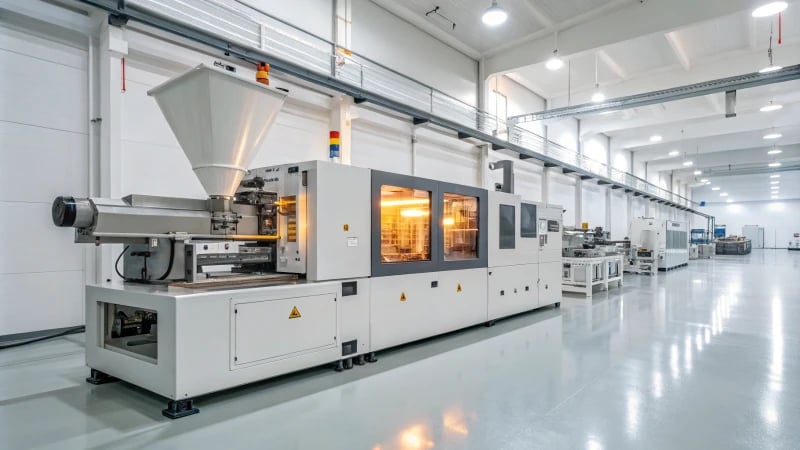
Unmatched Precision in Manufacturing
Injection molding truly stands out for its accuracy. I once worked on a project designing buttons for mobile phones. Each button needed perfect precision for both function and looks. Designing these buttons taught me the importance of detail and accuracy.
I was amazed by the precise construction of molds. Mold crafting through precision machining was meticulous. Each mold matched the product’s shape exactly. When molten plastic entered these molds at high pressure, it filled every crevice completely. The outcome was fantastic. The product had accurate dimensions and a flawless surface.
Other methods like blow molding can’t match this precision. They struggle with intricate internal designs. It’s like trying to capture a detailed painting with a blurry photo. It’s just impossible.
Aesthetic and Functional Excellence in Automotive Parts
Injection molding impresses me in crafting automotive interior parts. It’s about functionality and precise detail. Dashboard panels have complex shapes and need beautiful textures to attract the eye.
On a project with a car maker, we made molds for such parts. We used mold designs for awesome textures and patterns. For safety, flame-retardant plastics were selected for crucial areas. In car design, every detail matters.
Component Type | Key Requirements | Injection Molding Benefits |
---|---|---|
Dashboard Panels | Complex shapes, aesthetic detail | High-quality textures and patterns |
Center Console Buttons | Safety standards | Customizable plastic materials |
Efficient Production of Small Plastic Toys
Small plastic toys come alive through injection molding. I recall working with dolls needing perfect delicate features. Multi-cavity molds changed the game for us. We produced many units at once, maintaining quality each time. Watching intricate designs take shape was rewarding.
Blow molding lacks this precision. It struggles with uniform thickness and detail. It’s like comparing a skilled artisan to generic mass production. The artistic charm gets lost.
Meeting High Standards in Medical Device Manufacturing
Medical device manufacturing demands top precision. I visited a facility making housings for medical pumps. The tight tolerances felt like a high-wire act! Every part had to meet strict precision and quality standards.
Injection molding gave us control over process parameters closely, ensuring that every product meets industry regulations every time—consistent accuracy and stability were achieved.
Medical Device Type | Required Features | Injection Molding Advantages |
---|---|---|
Medical Pump Shell | High dimensional accuracy | Control over process parameters |
Testing Device Housing | Surface quality and stability | Ability to meet medical standards |
Why Choose Injection Molding?
Injection molding’s precision works wonders across various fields like electronics, cars, toys, and medical devices—injection molding1 continues to be my choice for its quality and efficiency.
Advanced tech and innovative mold designs help in optimizing production processes while ensuring each product meets standards perfectly.
Injection molding produces high-precision automotive parts.True
Injection molding excels in creating complex shapes and detailed textures for automotive components, ensuring both functionality and aesthetics are met.
Blow molding can replicate intricate designs better than injection molding.False
Blow molding struggles with maintaining uniform thickness and intricate shapes, making injection molding the superior choice for detailed designs.
How Does Injection Molding Enhance Automotive Interior Design?
Do you ever wonder about the sleek designs of modern car interiors? I certainly do! Injection molding plays a very important role in automotive design. It is not just a manufacturing process. It changes the game by combining precision and creativity. This combination meets our changing tastes.
Injection molding improves automotive interior design. It offers precision manufacturing. Manufacturers choose customizable materials for safety and aesthetics. This process supports efficient mass production of complex parts. Injection molding is crucial in creating modern vehicle interiors. These interiors meet consumer demands.
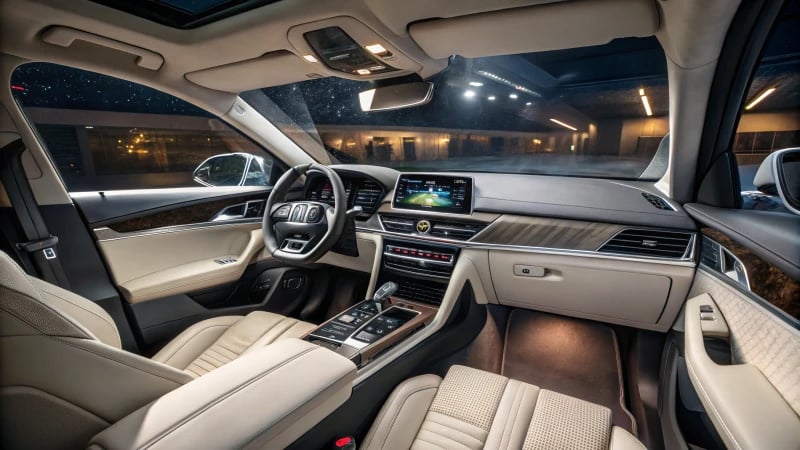
Precision and Detail in Design
I remember feeling amazed by injection molding when I first touched a perfectly crafted dashboard panel. Precision plays a huge role in creating car interiors. Parts like the dashboard and center console buttons need to fit perfectly. Injection molding helps achieve this. It provides very high dimensional accuracy that allows all pieces to fit seamlessly.
In one project, we designed a new dashboard for a luxury car. We faced the challenge of crafting a complex design with tiny details. Injection molding helped us replicate these intricate shapes accurately. The parts didn’t just work well; they also gave the vehicle a very elegant look.
Customization of Materials
Injection molding offers great flexibility in material selection. I, as a designer, enjoy choosing plastics that meet certain performance needs. For instance, I often use ABS for dashboard panels because of its high impact resistance and nice finish.
Material | Properties | Applications |
---|---|---|
ABS (Acrylonitrile Butadiene Styrene) | High impact resistance, good surface finish | Dashboard panels, trim pieces |
PC (Polycarbonate) | Excellent clarity, high heat resistance | Light covers, instrument panels |
Nylon | Good wear resistance, high strength | Interior fittings, mechanical components |
Choosing the right material is vital for achieving durability and meeting safety standards. Flame-retardant plastics are essential in some cases. I’ve noticed how this customization greatly impacts compared to other techniques like blow molding.
Mass Production Efficiency
Efficiency proves to be essential in my experience as a designer. Injection molding supports multi-cavity molds. This means manufacturers produce multiple parts at the same time. This feature really changed our production processes.
In one instance, we optimized a design using multi-cavity molds to swiftly and economically produce thousands of identical dashboard parts. Manufacturing costs and lead times reduced significantly. This freed up resources for other innovative projects.
Aesthetic Enhancements
Injection molding’s beauty extends beyond function to aesthetics. I have been really impressed by the ability to incorporate textures and patterns directly into mold designs. Each part not only serves a purpose but adds visual appeal.
In a recent interior project, we experimented with various finishes from matte to glossy, keeping up with the latest design trends. This feature plays a crucial role in elevating customer satisfaction and staying competitive in the auto market.
To learn more about the aesthetic capabilities of injection molding, check out this resource: explore design techniques2.
Injection molding ensures high precision in automotive interior parts.True
Injection molding allows for exceptional dimensional accuracy, crucial for fitting dashboard panels and buttons perfectly in vehicle interiors.
Blow molding achieves the same detail as injection molding.False
Blow molding cannot replicate the intricate designs and precision of injection molding, making it less effective for automotive interiors.
Why Are Small Plastic Toys Ideal for Injection Molding Techniques?
If you have ever been amazed by the tiny details on a toy, you might think about how they get created. Learning about injection molding techniques can help you see the wonders of toy design and production. Small plastic toys are a perfect match for this process. This process really suits them well.
Small plastic toys suit injection molding perfectly. They have complex designs and need high production efficiency. This method provides exact copies of detailed shapes. Material flexibility and safety rules are important. It helps create strong and attractive toys.
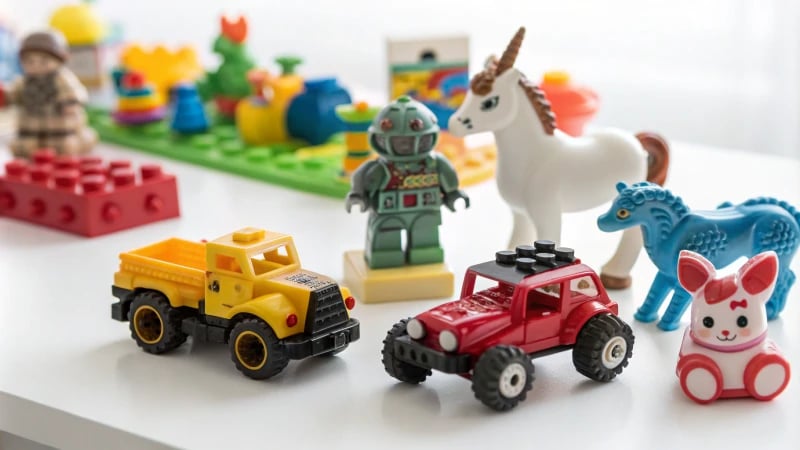
Precision and Detail in Production
I recall the first time I held a beautifully crafted toy figurine. The tiny features made it seem alive. Injection molding achieves such precision, allowing for high accuracy in producing small plastic toys with intricate designs, such as facial features on dolls and complex structures on toy cars.
The process starts with a mold that matches the desired shape, which is then filled with molten plastic under high pressure. This captures every detail in the final product. For example, injection molding excels in creating fine details in adorable toy figurines, enabling manufacturers to produce thousands of units with consistent quality.
Efficiency through Mass Production
One of the standout benefits of using injection molding for small plastic toys is its capacity for mass production. I often think about the stress of tight manufacturing deadlines; it can be overwhelming! By utilizing multi-cavity molds, manufacturers can significantly increase output without sacrificing quality.
Here’s a simple comparison between different manufacturing techniques:
Technique | Production Speed | Detail Replication | Cost Efficiency |
---|---|---|---|
Injection Molding | High | Excellent | Very High |
Blow Molding | Moderate | Fair | Moderate |
3D Printing | Low | Good | Low |
From this table, it’s evident that injection molding leads to a high production speed, which is essential for toy manufacturers aiming to meet market demands.
Material Versatility
Materials in injection molding also play a crucial role. This is really fascinating! Manufacturers select from various plastics, each offering unique properties tailored to specific product needs. For example:
- ABS Plastic: Known for strength and durability, perfect for robust toys.
- Polypropylene (PP): Lightweight and flexible, ideal for rough handling.
- Polystyrene (PS): Affordable and easy to mold and paint.
Choosing the right material improves safety and durability—two things I always prioritize in toy design.
Complex Shapes and Textures
The complexity of shapes and textures possible with injection molding amazes me; it’s another reason manufacturers love this method. Molds capture intricate patterns and textures that increase aesthetic value while enhancing tactile experiences for children.
Moreover, injection molding allows different colors and finishes during production seamlessly. Toys become vibrant and attractive—unlike blow molding, which struggles with such detailed designs due to its process limitations.
For a deeper understanding of how these aspects contribute to the overall efficiency of toy production, check out our resources on manufacturing processes3.
Safety Considerations
Today, safety standards for children’s toys are more strict than ever; safety is always on my mind when designing toys. Injection molding assists in meeting these regulations by controlling material selection and production processes precisely.
Using high-quality plastics that meet standards ensures that toys are non-toxic and safe. The consistency achieved through injection molding reduces the risk of hazardous defects. When facing these challenges, I refer to best practices in toy safety regulations4 to maintain compliance and consumer trust.
Injection molding allows for high precision in toy production.True
The injection molding process ensures that intricate designs of toys are accurately replicated, leading to high precision and dimensional accuracy in the final product.
Small plastic toys can only be made from ABS plastic.False
Small plastic toys can be made from various materials, including ABS, polypropylene, and polystyrene, each offering unique properties for different toy requirements.
How Does Injection Molding Impact the Production of Medical Devices?
Ever thought about how important medical devices are crafted with exactness? Injection molding plays a vital role, providing the precision and reliability that healthcare depends on daily.
Injection molding plays a crucial role in making medical devices. It creates high-precision parts at a fast pace. These parts meet strict rules for safety and functionality. This process combines speed with careful detail. This precision is essential in healthcare.
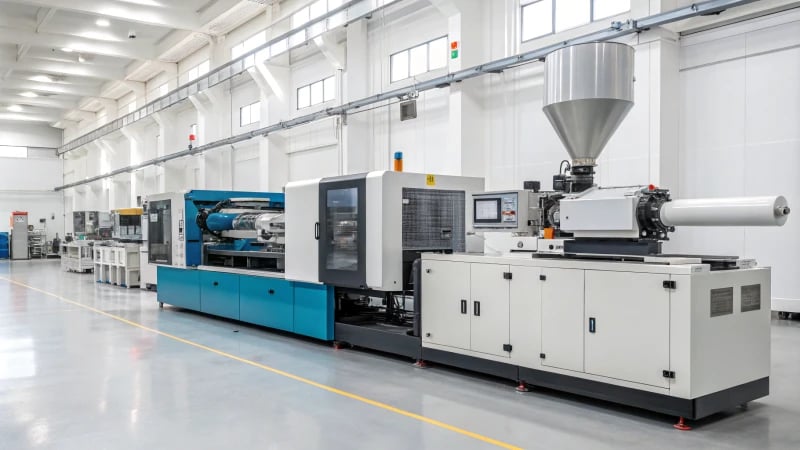
Importance of Injection Molding in Medical Devices
I still remember the first time I entered a place where people produced medical devices. Machines hummed. Engineers focused. Intricate parts came together like a puzzle. It was fascinating! Injection molding plays a key role here. This process crafts each component with precision and care. It is vital in creating medical devices. Let’s explore why this method is very essential in manufacturing.
Injection molding is critical in the manufacturing of medical devices due to its precision and accuracy. Medical devices, such as injection pumps and testing equipment, require components that meet stringent dimensional specifications.
The injection molding process allows for the creation of high-precision parts with excellent surface quality. For instance, when producing a medical device housing, manufacturers can ensure that each component fits perfectly, thereby guaranteeing the device operates correctly. The ability to create detailed designs means that intricate internal structures are replicated accurately, which is essential in medical applications.
Efficiency in Mass Production
One of the significant advantages of injection molding is its capability for mass production. This efficiency is crucial in the medical field, where the demand for devices can be high. By utilizing multi-cavity molds, manufacturers can produce multiple components simultaneously, significantly reducing production time.
Feature | Injection Molding | Blow Molding |
---|---|---|
Dimensional Accuracy | High | Low |
Production Speed | Fast | Moderate |
Complexity of Design | High | Moderate |
Surface Quality | Excellent | Fair |
For example, small medical devices like testing kits can be produced quickly and efficiently through injection molding, ensuring that they are readily available for healthcare providers.
Material Versatility
Injection molding also offers flexibility in material selection. Various plastics can be chosen based on the specific requirements of the medical device, such as biocompatibility, strength, or thermal resistance.
This versatility allows designers to select materials that enhance safety and functionality. For instance, plastics with flame retardants are used for devices that may be exposed to high temperatures, which is a common requirement in medical environments.
Regulatory Compliance
In the healthcare sector, compliance with regulatory standards is non-negotiable. Injection molding processes can be tailored to meet the stringent regulations set by health authorities, ensuring that all products adhere to safety and quality standards.
By controlling various parameters in the injection molding process, manufacturers can maintain consistency in product quality, which is vital for regulatory approval.
To learn more about best practices for regulatory compliance in medical device manufacturing, check out this informative resource5.
Injection molding ensures high precision in medical devices.True
The injection molding process creates parts with stringent dimensional specifications, crucial for the functionality of medical devices.
Blow molding is more efficient than injection molding for medical devices.False
Injection molding offers faster production speeds and higher accuracy than blow molding, making it superior for medical applications.
How Can Designers Optimize Material Selection for Different Molding Processes?
Have you felt confused by the many material options for designs? I definitely have felt that way! Designers must really understand how to pick the best materials for different molding methods. This knowledge truly changes our creations. Let’s explore this adventure together.
Designers need to understand material properties like tensile strength and thermal stability. They should study molding techniques such as injection molding and blow molding. Cost efficiency is important too. Designers need to tailor material choices for specific applications like medical devices or toys. Sustainability factors really matter and should be included. Sustainability is crucial.
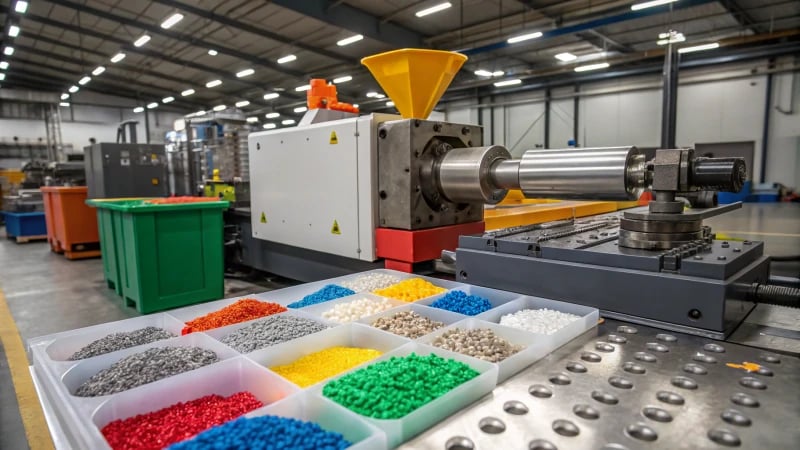
Understanding Material Properties
Throughout my career as a designer, I discovered that choosing materials involves more than selecting what appears appealing on paper. It’s about grasping the story each material narrates. Key properties include tensile strength, impact resistance, and thermal stability. These characteristics significantly influence the performance of the molded product in real-world applications. For instance, materials like ABS and polycarbonate are often chosen for precision electronic parts due to their high dimensional accuracy and excellent surface finish. This makes them ideal for components such as plastic buttons6 found in mobile phones.
Analyzing Molding Techniques
The molding process sometimes resembles a puzzle. Different molding processes, such as injection molding and blow molding, have unique capabilities and limitations that affect material selection. Injection molding excels at producing detailed parts with complex geometries, making it suitable for automotive interior parts like dashboard panels. In contrast, blow molding is more suited for hollow objects but struggles with intricate shapes. Designers need to weigh these factors when selecting materials based on the intended manufacturing process.
Cost and Efficiency Considerations
Cost is always a factor, right? Cost-effectiveness is another critical factor in material selection. Early in my career, I struggled to find a balance between performance and affordability while debating the use of high-performance materials for medical device housings. These materials offered excellent qualities but were expensive! Conducting detailed cost analyses became vital to produce high-quality designs without overspending. A simple comparison table can help illustrate these considerations:
Material Type | Performance Characteristics | Cost Impact |
---|---|---|
ABS | Good surface finish, high impact resistance | Moderate |
Polycarbonate | Excellent strength, thermal stability | High |
PP (Polypropylene) | Lightweight, cost-effective | Low |
Nylon | High tensile strength, good wear resistance | Moderate to High |
Tailoring Material Choices for Applications
Adapting material choices based on their application has become a natural skill. The application dictates the choice of material; for small plastic toys, designers often opt for vibrant materials like polystyrene that allow bright colors and safe finishes. Injection molding helps create these intricate toy designs beautifully. However, in medical devices, durability and biocompatibility are critical to meeting safety standards.
Sustainability Factors
Sustainability in design holds significant importance for me. In today’s market, sustainability is becoming increasingly important; it feels satisfying to know that by choosing eco-friendly materials we can have a positive impact on the planet. I have started using recyclable plastics and bio-based resources in my designs. As the industry evolves, sustainable practices can enhance a brand’s reputation while still meeting performance requirements for products like automotive interior parts or medical devices. To learn more about choosing sustainable materials, check sustainable design practices7.
Optimizing material selection is more than a task; it’s an adventure in creativity and responsibility.
Designers must understand material properties for optimal selection.True
Understanding material properties like tensile strength and impact resistance is essential for designers to select the best materials for specific molding processes.
Blow molding is ideal for producing detailed automotive parts.False
Blow molding is not suitable for intricate shapes; injection molding is preferred for detailed automotive components like dashboard panels.
Conclusion
Injection molding excels in creating precise electronic parts, automotive interiors, small toys, and medical devices due to its high accuracy and ability to replicate intricate designs.
-
Discover why injection molding is ideal for precision parts production and how it compares with other manufacturing methods. ↩
-
Discover how injection molding technology improves automotive design aesthetics and functionality. It’s crucial for professionals looking to innovate in vehicle interiors. ↩
-
Learn about the advantages of using injection molding for small plastic toys and how it enhances production efficiency and design capabilities. ↩
-
Explore detailed insights into material selection for toy manufacturing and how it impacts product quality. ↩
-
Discover how injection molding contributes to the precision and safety of medical devices. This link offers valuable insights for professionals in the industry. ↩
-
This link will provide you with in-depth strategies and examples to refine your material selection process effectively. ↩
-
Learn about innovative materials that are revolutionizing the molding industry for better performance. ↩