Curious about how a little change in injection speed possibly changes your whole production process?
Injection speed is important for how well injection molds work. It affects how fast products are made, how good they are and how efficient the process is. Faster speeds mean shorter production times. But they also cause defects and might harm molds. This situation shows the need for balance in optimizing results. Balance is very important here.
When I began experimenting with mold designs, I felt surprised by how a simple thing like injection speed could change the whole production process. Injection speed could make it work well or fall apart. One must not only push for faster results but find a perfect balance between speed and quality. This balance lets us fill the molds quickly, reducing the time needed for each cycle. Once, I worked on a project where changing the injection speed by just a little bit saved a few seconds per cycle, greatly improving productivity.
However, challenges still exist. If speed is too high, products might show ugly flow marks or, even worse, the mold might break. I learned that slowing down at times actually saves time because it keeps the product quality high and avoids costly repairs. For instance, once a small change in speed saved us from stopping production for a week due to mold repairs. Experiences like these show why understanding the details of injection speed is very important for successful manufacturing.
Higher injection speeds reduce molding cycle time.True
Higher speeds fill molds faster, cutting cycle time significantly.
Excessive injection speed improves product quality.False
Too fast speeds cause defects like flow marks, harming quality.
- 1. Why Should You Consider Increasing Injection Speed?
- 2. Can Faster Injection Speeds Lead to Quality Issues?
- 3. How Does Injection Speed Influence Mold Longevity?
- 4. What Factors Should I Consider When Adjusting Injection Speed?
- 5. How Can Manufacturers Optimize Injection Speed for Better Productivity?
- 6. Conclusion
Why Should You Consider Increasing Injection Speed?
Initially, I learned that changing the speed of injection turned our production line into something amazing. Adjusting this one element acted like finding a secret ability. Interested in how this simple shift might really improve both efficiency and quality in molding? Let’s find out!
Increasing injection speed in molding really improves productivity. It reduces cycle times and refines the demolding steps. But, finding the right balance is crucial. This balance prevents quality problems and mold damage. Mold damage needs to be avoided.
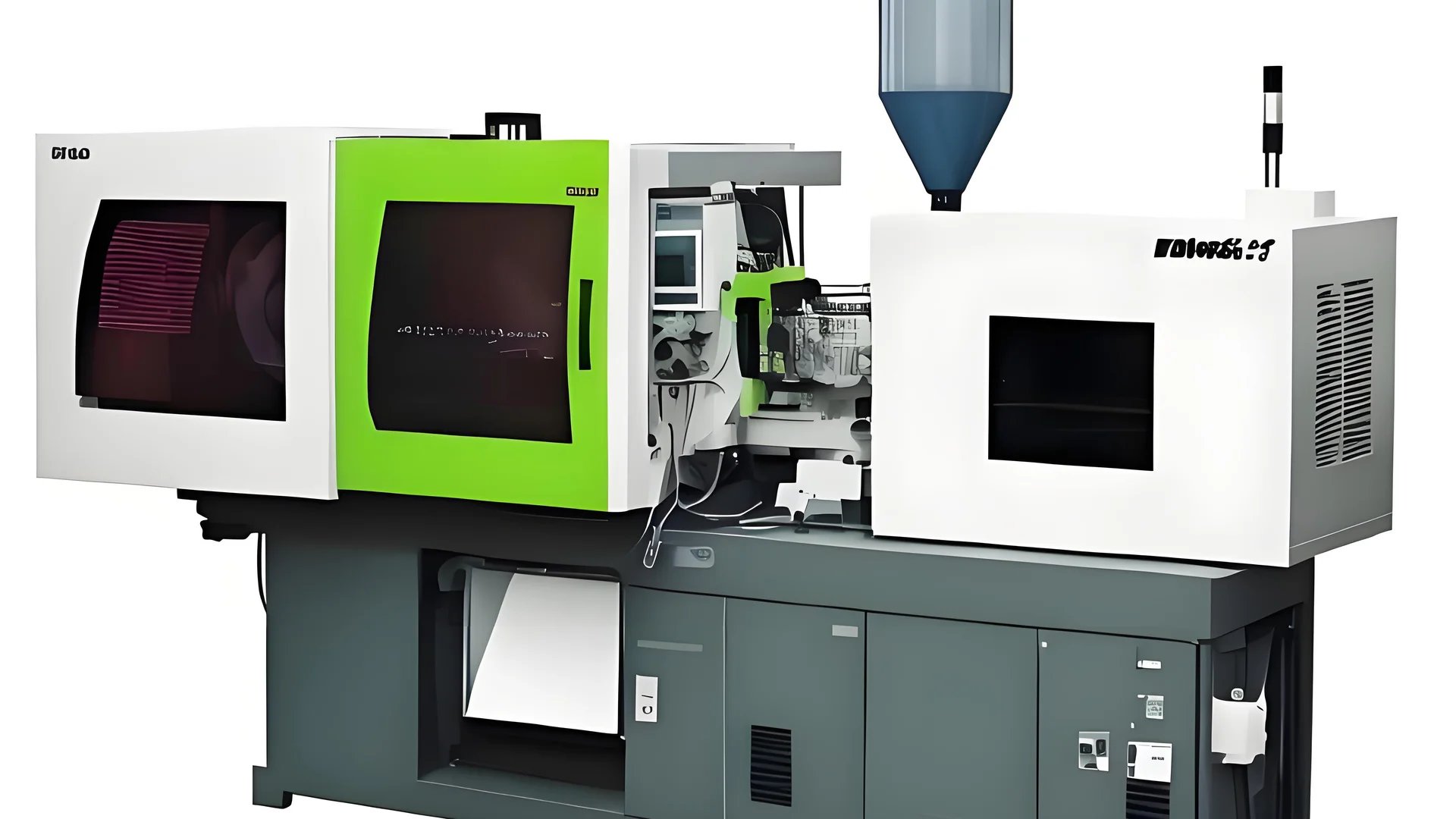
Increasing Productivity with Faster Injection
Small changes truly fascinate me. Quickening injection speed is a change that greatly reduces molding cycle time1. I recall seeing a tiny plastic part, usually filled in 10-15 seconds, finished in just 5-8 seconds. It felt like a magic trick, suddenly allowing more cycles every hour without sweating.
Cycle Time | Normal Speed | Increased Speed |
---|---|---|
Small Parts | 10-15 seconds | 5-8 seconds |
This higher efficiency lets us meet more demand without extra resources. It’s like discovering an extra gear when it’s truly needed.
Enhancing Demolding Process
Speed helps not just in filling molds quickly; it also improves demolding time2. With precise speed, products come out with even internal stresses and excellent quality. Think of a high-quality product ready for packaging instantly after demolding. It feels like a dream come true, especially for those who really care about surface quality.
Balancing Risks: Quality and Mold Condition
However, everything isn’t perfect. High-speed injections are wonderful for efficiency but risk quality issues or mold harm. I once pushed speeds too high, resulting in a "spray" effect. It was terrible to see air trapped and flow marks ruining clear products.
To avoid these pitfalls, it’s crucial to control injection speed3 carefully. Very high speeds can damage molds by generating significant impact forces, potentially leading to downtime for repairs. Frequent high-speed injections might cause core breakage or cavity wear.
Potential Issues | Consequences |
---|---|
Flow Marks | Product rejection, increased scrap rate |
Mold Damage | Downtime for repairs, decreased output |
In the end, finding the ideal balance is crucial, where productivity wins over risks. I always listen for industry best practices4. Each new idea helps me choose wisely.
Higher injection speeds reduce molding cycle time.True
Faster injection fills the mold quicker, shortening cycle time.
Excessive injection speed improves product quality.False
Too fast speeds cause defects like flow marks, harming quality.
Can Faster Injection Speeds Lead to Quality Issues?
Have you ever felt the thrill of speeding things up, then paused to think it might be too quick for comfort?
Quick injection speeds may cause issues such as flow marks and trapped air. While these speeds certainly increase productivity, too much speed often results in defects. This highlights a very important fact. Careful planning is needed.
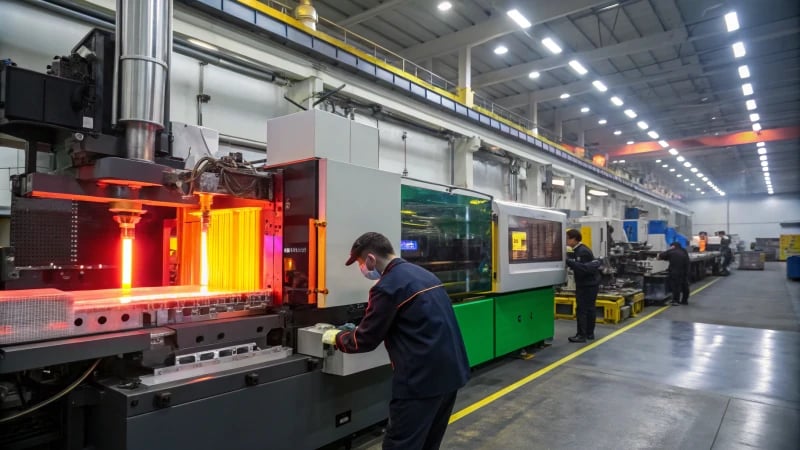
Impact of Faster Injection Speeds on Productivity
Increase in Productivity
I recall seeing a high-speed injection mold for the first time. It was like an efficient machine racing to finish quickly. The molding time disappeared in mere seconds, from 10-15 seconds down to just 5-8 seconds. This accelerated cycle5 brought big changes to our production line, increasing productivity without losing quality.
Each saved second allowed more cycles in our shifts, increasing output without needing more workers or extra hours. It was about real efficiency, not just numbers. Products moved faster through the stages. Sometimes, like with high-appearance plastics, the finish was perfect, ready to pack immediately. It felt like finding a quick route during my daily travel.
Quality Concerns with High Injection Speeds
Potential Quality Issues
But there was a challenge – a lesson from doing and learning. Pushing the speeds too far? It felt like running fast on slippery ground. The "spray" issue became our problem, causing flow marks and trapping air, especially in clear plastics.
Quality Issue | Cause | Effect |
---|---|---|
Flow Marks | Uneven filling due to fast speed | Unqualified product quality |
Trapped Air | Rapid injection trapping air | Structural defects |
These flaws weren’t just about looks; they made products useless and raised our scrap rates.
Risks to Mold Integrity
Mold Damage Risks
The molds were vital, too. High speeds didn’t just harm products; they affected molds. I learned that too much force could break parts of the mold, leading to costly repairs and stopping production.
Excessive speeds also pose risks to molds by generating impact forces that damage cores and cavities. This necessitates repairs and halts production, severely affecting productivity.
Adjusting those speeds became a careful task, balancing speed with durability. It required precise calibration6. This taught me that finding the perfect balance wasn’t just about avoiding stops but keeping our processes going for a long time.
By bringing these lessons into daily work, we learned to adjust without losing quality. Curious about other methods? Looking into mold design strategies7 could maybe further improve production results.
Higher injection speeds increase productivity.True
Faster injection fills molds quicker, completing more cycles in less time.
Excessive injection speed can damage molds.True
High-speed injections cause impact force, risking mold core and cavity damage.
How Does Injection Speed Influence Mold Longevity?
I remember the day my mentor, Mike, talked about how important injection speed is in molding. It felt like learning a hidden code for mold life and effectiveness.
Injection speed affects mold lifespan by changing stress levels during molding. The right speed is important for both work output and mold quality. Too fast and it may damage molds and cut short their life.
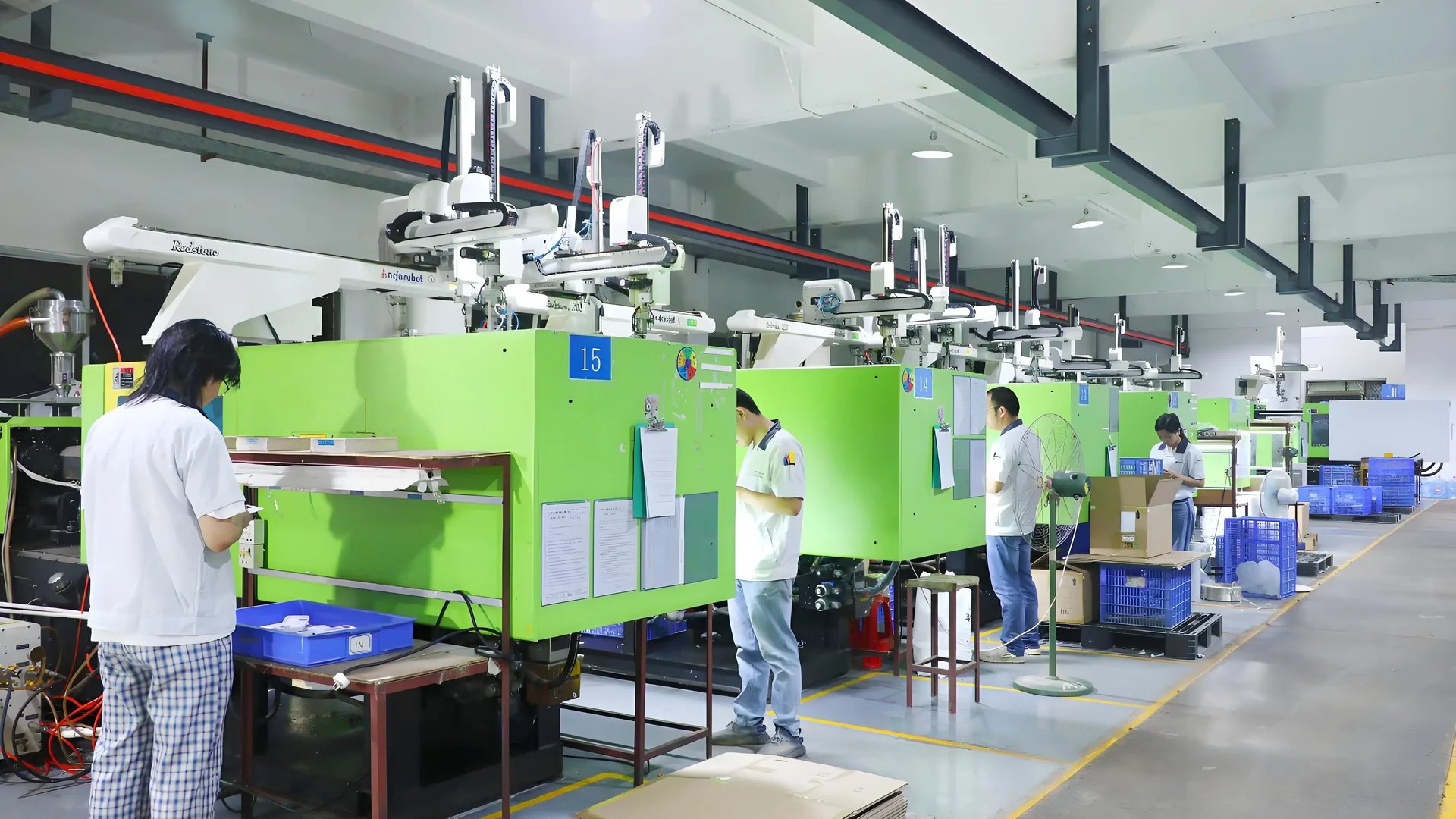
The Role of Injection Speed in Mold Longevity
Injection speed directly impacts the stress exerted on molds during each cycle. Higher speeds allow for quicker filling of the mold cavity8, shortening the molding cycle and increasing productivity. This is particularly useful in high-demand scenarios where reducing cycle times can lead to substantial gains.
I remember a project with a strict deadline where finding the perfect injection speed was crucial. Adjusting it felt like tuning a fragile instrument because even small changes could lead to very different outcomes. The correct speed can greatly reduce cycle times, letting us produce more parts without losing quality. For example, in a project with small plastic pieces, changing the speed lowered our fill time from 10 seconds to just 5. That really helped us meet our production goals.
Injection Speed | Cycle Time Reduction | Impact on Mold |
---|---|---|
Low | Long | Minimal Stress |
Optimal | Reduced | Balanced Stress |
High | Short | High Stress |
But everything is not always perfect. I have seen how pushing speeds too high can cause problems. Once, we increased speed and got defects like flow marks and air traps, especially in clear products. These defects slowed us down because we had to start over, messing up our schedule and creating more waste.
Risk Factors for Mold Damage
There’s a thin line between increasing production speed and risking mold damage. Overly high injection speeds create significant impact forces that can damage mold components. Frequent high-speed cycles may result in core breakage or cavity wear, leading to costly repairs and downtime.
I have had many sleepless nights worrying about mold wear from too much speed. It’s stressful to think about downtime and repair costs, like when we had to stop production for days due to core breakage. This situation taught me the value of regular machine checks and understanding material behavior.
To mitigate these risks, it is crucial to find an optimal speed that balances productivity with mold longevity9. Finding the right balance requires experience, intuition, and sometimes a bit of guessing.
In practice, achieving this balance requires a thorough understanding of material behavior under various speeds and the potential implications on mold integrity. Engineers must be vigilant in monitoring injection parameters and maintaining regular maintenance schedules to ensure that molds remain in peak condition over extended production runs.
I often rely on past lessons and advice from industry experts like Mike. He highlights careful monitoring and regular upkeep as key ways to keep molds lasting longer while staying productive.
Higher injection speeds increase productivity.True
Faster injection reduces cycle time, allowing more cycles per hour.
Excessive injection speed reduces mold lifespan.True
High speed causes impact force that damages mold parts, needing repairs.
What Factors Should I Consider When Adjusting Injection Speed?
Altering the speed of injection during molding resembles walking through a maze without a guide. Let’s uncover the secrets together to elevate your production efficiency and product quality.
I think about a few things when I change the injection speed. Mold design, material features and what the product needs all matter. Fast speeds might really lower the cycle time. But they might also cause defects like flow marks. Finding the perfect balance is important for the best production.
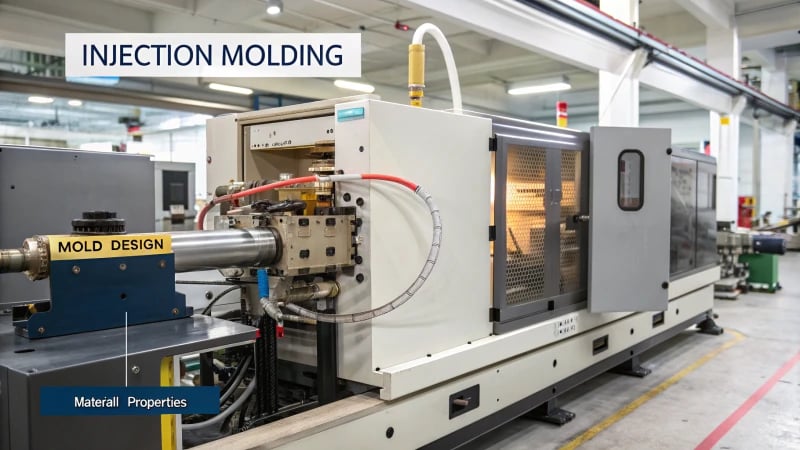
Influence of Mold Design
I recall the first time dealing with a complicated mold with many cavities. The challenge felt immense. I needed to adjust the injection speed very carefully to fill each cavity equally. This experience taught me that complex molds, like intricate patterns, need special speeds to avoid mistakes.
- Cavity Count: When using molds with many cavities, I discovered slower speeds often help fill evenly.
- Complex Features: Intricate designs need careful speed adjustments to prevent defects.
Material Properties
The range of materials is huge, each with unique characteristics. Thermoplastics often seem tough, but high-viscosity materials really require slower speeds to avoid problems such as flow marks.
- Viscosity: This factor has often led me to reconsider and slow down my speed methods.
- Thermal Sensitivity: For temperature-sensitive materials, controlling the speed becomes essential to avoid heat-related damage.
Product Characteristics
The final use of a product usually sets the speed at which I work. Products needing high visual quality require patience and slower speeds for a perfect finish.
Feature Requirement | Recommended Speed |
---|---|
High Aesthetic | Slower |
Structural Strength | Moderate |
Rapid Production | Faster |
Impact on Productivity
Changing injection speed changes productivity a lot. Fast speeds reduce molding cycle time10, enabling more cycles quickly. In making small plastic items, I’ve slashed cycle times from 10-15 seconds to only 5-8 seconds.
Still, too much speed may cause defects like "spray" issues, requiring extra work or rejection. I’ve had mold damage due to high speeds which caused delays, especially under tight deadlines!
Finding balance with real-world trials and expert consultation11 is crucial for process optimization. This wisdom has been very valuable in staying competitive without losing quality.
Higher injection speeds reduce molding cycle time.True
Faster injection fills molds quicker, reducing the cycle time.
Excessive speed never damages molds in injection molding.False
High speeds can damage mold components, requiring repairs.
How Can Manufacturers Optimize Injection Speed for Better Productivity?
Understanding the details of injection molding feels like solving a difficult puzzle. Each piece must fit perfectly. Really, everything needs to be precise. The process often seems intricate. Every step requires careful attention. Mistakes might lead to problems.
Manufacturers need to balance speed and quality to make injection faster. Fast fill rates help, but product quality matters too. Shorter cycle times help with quicker demolding. Better demolding means more efficiency and quicker results. Productivity goes up. Mold and product quality remain intact. A very good balance is key.
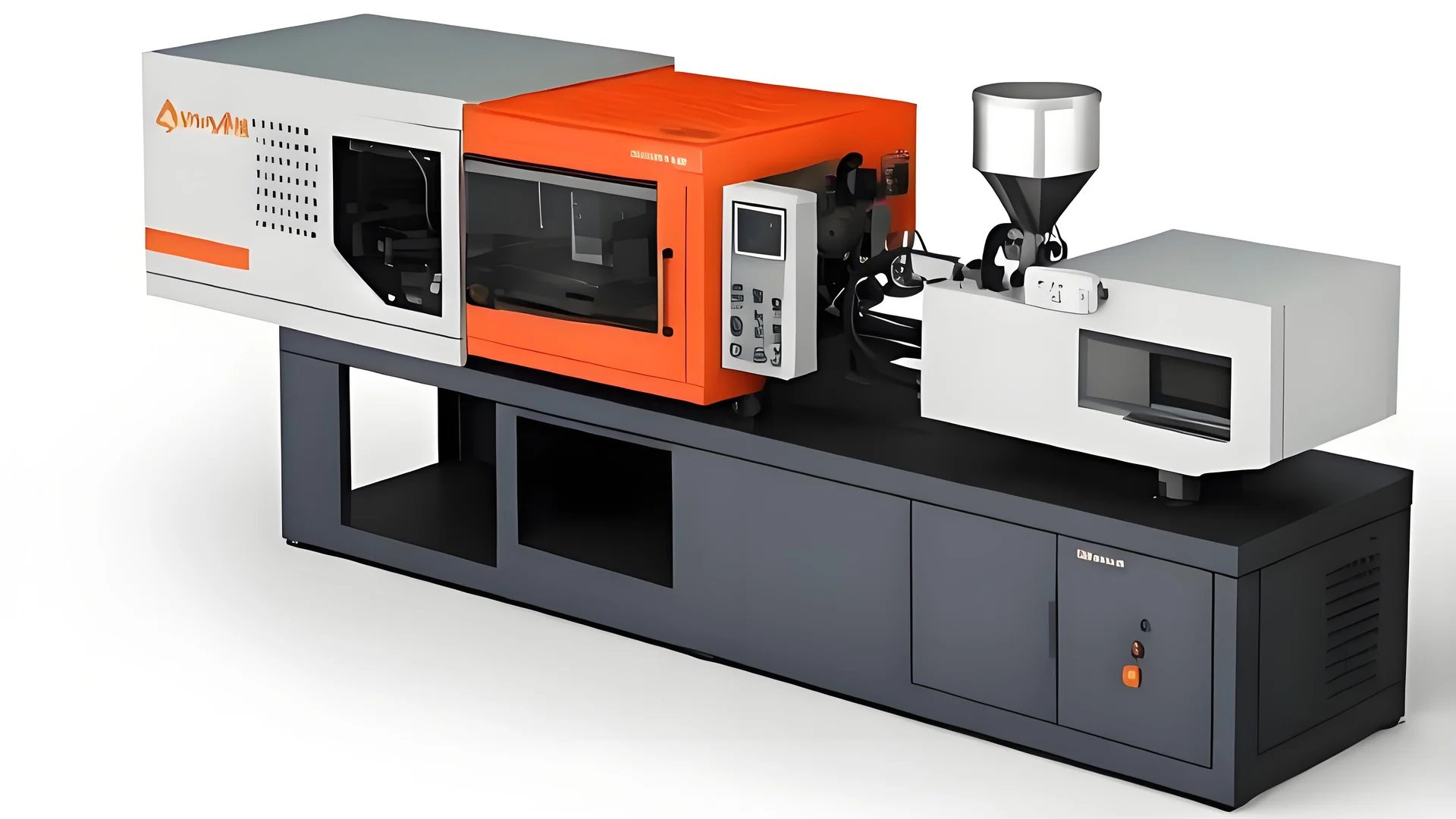
Understanding Injection Speed’s Impact
Injection speed in molding initially seemed straightforward, but it is actually the core of the process. The molten plastic must fill a mold quickly, and this speed is crucial. Small changes can sometimes shave seconds off fill times. For instance, a 15-second job can turn into 8 seconds with the right tweak—it’s like finding a shortcut on a busy road.
Balancing Speed and Quality
Once, I faced an issue with a clear product where increasing injection speed too much caused ugly flow marks. This was a tough lesson: balancing speed and quality is very important. Fast speeds offer quicker cycles but also risk issues like trapped air, which is problematic for products that must look perfect.
Parameter | Benefit |
---|---|
Higher Speed | Shorter Fill Time |
Balanced Speed | Reduced Defects |
Optimal Speed | Faster Demolding |
Optimizing for Shorter Cycle Times
Finding the right injection speed feels rewarding. During one project, optimizing speed not only improved surface look but also made demolding faster. This change was huge for our electronic products as it sped up production without dropping quality.
Mitigating Risks of Mold Damage
Being too aggressive with injection speed can be costly. I’ve seen mold parts wear out from constant high-speed hits, leading to downtime for repairs which can disrupt production plans significantly.
Striking the Right Balance
Finding balance isn’t just about quick adjustments; it’s strategic planning. Using tools like special simulation software12 has been very useful for me as they offer insights into which settings work best. This helps me walk the line between speed and quality without falling off.
Higher injection speeds reduce molding cycle time.True
Rapid injection fills mold cavities faster, shortening cycle times.
Excessive speed decreases mold longevity.True
High speed causes impact damage to molds, requiring repairs.
Conclusion
Injection speed significantly impacts productivity in molding, balancing faster cycle times with quality and mold integrity to optimize production efficiency while minimizing defects and damage risks.
-
Learn about techniques to shorten molding cycles by increasing injection speed, enhancing production efficiency. ↩
-
Discover how fast injection speeds lead to better product quality and quicker transitions to subsequent processes. ↩
-
Understand the potential quality and mold integrity risks associated with high-speed injections. ↩
-
Explore industry best practices for optimizing injection speed without compromising product quality. ↩
-
Discover how accelerated molding cycles enhance productivity and efficiency. ↩
-
Learn about precise calibration methods to maintain mold integrity at high speeds. ↩
-
Explore innovative design strategies to optimize mold performance and production quality. ↩
-
Understanding mold cavities can help you optimize design for better stress distribution and longer mold life. ↩
-
Explore ways to extend mold lifespan by balancing injection speed with material and design considerations. ↩
-
Details how adjusting injection speed can optimize the cycle time, increasing productivity. ↩
-
Provides insights from experts to guide you in refining your injection molding processes effectively. ↩
-
Explore how simulation tools can predict outcomes and improve decision-making in setting injection speeds. ↩