Do you ever think about how fast injection molding affects the quality of plastic products?
Injection speed directly affects the quality of plastic products. It changes how they look and feel inside. Fast speeds might create problems like lines or trapped air. Slow speeds might cause incomplete filling or dull looks. Correct speed is crucial. It is very important to keep the product in good condition.
Comprehending how injection speed influences plastic product quality resembles solving a puzzle. Small changes sometimes transform outcomes. Experiences in overcoming these challenges show how to optimize production. Balancing speed and perfection is tricky yet rewarding.
High injection speed causes flow marks in plastics.True
High speed can cause uneven flow, leading to visible marks.
Slow injection speed improves surface gloss of plastics.False
Slow speed often results in poor gloss due to incomplete filling.
How Does Injection Speed Affect Molded Product Appearance?
Have you ever thought about why some molded products seem off? The answer often hides in how fast the material gets injected.
Fast injection speed causes surface problems. Flow marks show up. Weld lines appear. Air gets trapped, leading to flaws. Flash forms at the edges. Surface quality suffers. Inside, density becomes uneven. Stress also results. These issues weaken the product. They really compromise its condition.
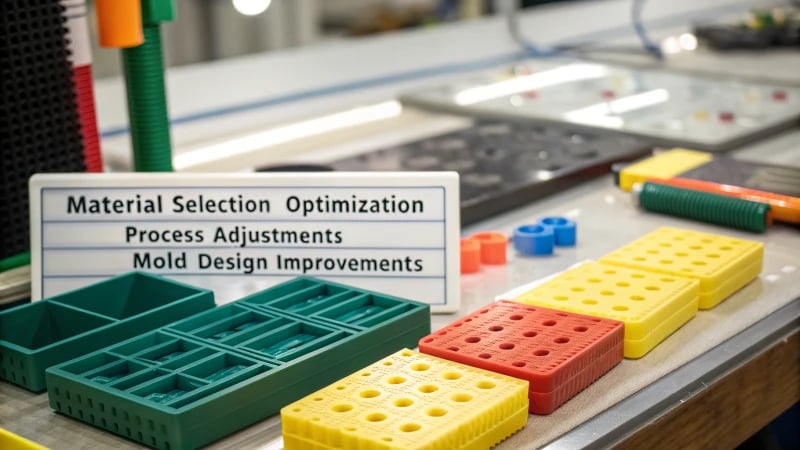
Appearance Quality Challenges
The first time I noticed high injection speed signs on a final product, I’ll never forget. It was a shiny casing for an electronic gadget I helped design, but the surface had flow marks and weld lines. The problem? Fast injection caused turbulence in the melt flow.
- Flow Marks and Weld Marks: These show up when the melt enters the mold cavity too fast. It’s like pouring a thick milkshake into a tiny cup too quickly, resulting in messy patterns. In molds with several gates, this speed stops the melt from mixing well at different entry points, leaving ugly weld marks.
- Air Entrapment and Scorching: Picture blowing up a balloon inside a box without letting any air escape. High-speed injection traps air in the cavity like this, compressing it until it overheats, creating black spots or streaks.
- Flash Formation: This issue causes lots of trouble. Too much speed leads to too much pressure, allowing plastic to leak out where it shouldn’t, creating flash that needs careful trimming.
Issue | Cause | Effect on Appearance |
---|---|---|
Flow Marks & Weld Marks | High-speed turbulence & poor gate melding | Surface defects |
Air Entrapment & Scorching | Trapped air leading to high-temperature spots | Black spots/streaks |
Flash Formation | Pressure exceeding mold clamping force | Excessive material overflow |
Internal Quality Effects
Appearance issues are just part of the story. I once worked on a component looking flawless outside but showed cracks in stress tests. Fast injection left stress inside the product, reducing its strength.
- Internal Stress: This resembles building a house of cards too quickly – it stands until you touch it, then it all falls. High-speed injection may leave stresses that result in warping or cracking over time.
- Uneven Density: I’ve seen precision parts suffer from this due to fast, complex melt dynamics. It’s like baking a cake and finding dense and airy sections – it fails for critical use.
Learn more about how internal stress affects1 product durability to improve your design work.
Practical Considerations
Managing injection speed is similar to finding the ideal pace on a bike – not too fast to lose balance, nor too slow to stall. Speed adjustment based on product needs is critical to keeping appearance and function intact.
Look into techniques to tackle flow mark issues2 and achieve better surfaces in your projects.
Stay updated on how to reduce uneven density3 in precise components, ensuring top performance in demanding situations.
High-speed injection causes flow marks.True
Turbulence from high-speed injection leads to visible flow marks.
Air entrapment does not affect appearance quality.False
Trapped air can cause scorching, leading to black spots on the surface.
How Does Slow Injection Speed Influence Internal Product Characteristics?
Ever thought about how fast injection molding changes the quality of plastic items?
Slow injection speeds often cause molds to fill incompletely. This results in short shots and poor surface gloss. It can also alter crystallinity. Collectively, these elements affect the product’s internal qualities and how it performs. Mold designers need to watch injection speed closely. This is very important.
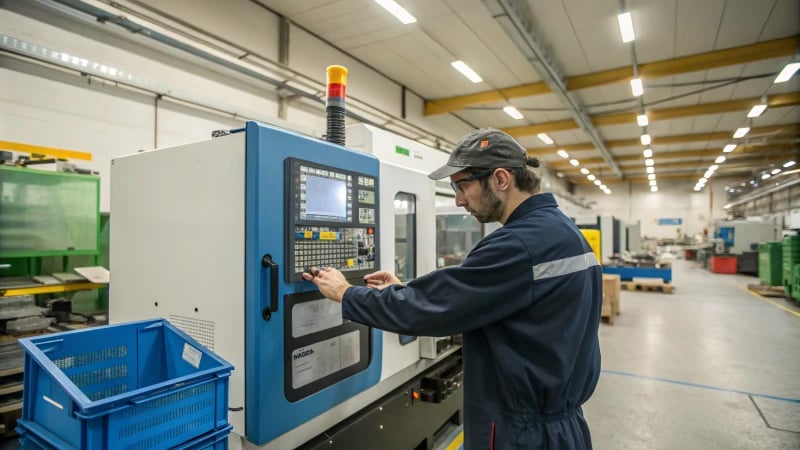
How Injection Speed Affects Appearance Quality
Short Shot: Picture working really hard on a design, only to see it fail. That’s the reality with slow injection speed. I recall my first project when the mold didn’t fill properly. It felt like watching a movie that buffers. This incomplete filling, called a "short shot," leaves you with an unfinished item that doesn’t meet the standards.
Factor | Effect |
---|---|
Short Shot | Incomplete mold filling |
Surface Gloss | Poor due to rapid temperature drop |
Dull Surface Gloss: Picture polishing something for a shiny finish, but ending up with a dull look. Slow injection speed results in this dullness. The melt cools too fast, unable to catch the mold’s shiny details. The finish looks poor.
Changes in Internal Quality and Crystallinity
For those using plastics like polypropylene (PP) and polyamide (PA), slow speeds mean higher risks. They allow too much crystallization, changing material properties. Toughness decreases, while hardness rises—like a cake that’s either too hard or too soft—never ideal.
Lamination and Weak Bonding: In multilayer molding, slow speeds spoil layer bonding. I remember a project where parts wouldn’t stick together, resulting in low-quality output.
Learn more about crystallinity change4 to understand its impact.
Examining Slow Speed Effects in Injection Molding
- Crystallinity Change: Slow speeds affect cooling rates. This influences crystallization, altering toughness and hardness.
- Weak Bonding: Slow speeds in multilayer molding lead to layers that don’t bond well, reducing product quality.
To know more about lamination issues5, check out studies on multilayer injection molding problems.
Understanding how slow injection speed affects these factors is crucial for mold designers. It really helps us improve manufacturing methods for better results and avoid failures when plans don’t go as intended.
Slow injection speed causes incomplete mold filling.True
The melt may not fill the mold before cooling, causing short shots.
Slow speeds increase product toughness in crystalline plastics.False
Slow speeds reduce toughness by allowing excessive crystallization.
Can Injection Speed Affect the Density Distribution of Plastic Products?
Do you ever think about how injection speed affects your plastic products?
Injection speed affects how dense plastic products are. Fast injection might create uneven density due to turbulence. Slow injection probably results in defects. Short shots and poor bonding might happen.
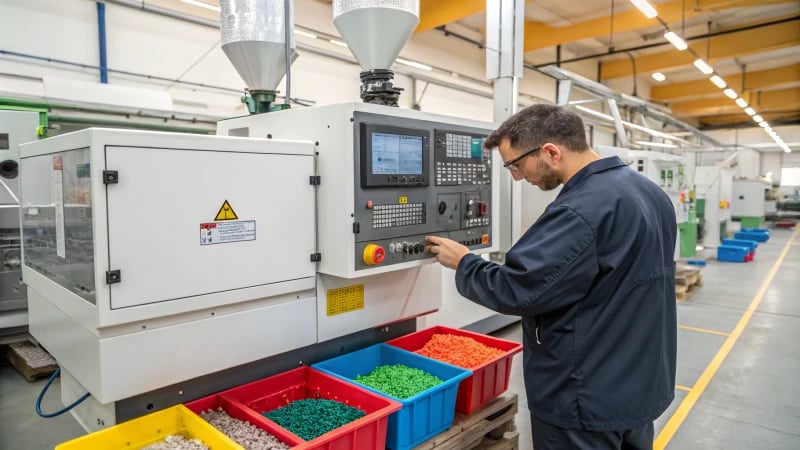
Personal Insights on Injection Speed
In my early days with plastic molds, a project taught me a lot about injection speed’s importance. The task seemed simple – a sleek casing for a gadget. We were ready to start quickly but encountered problems.
Effects of High Injection Speed
-
Appearance Quality
I remember feeling surprised by flow marks and weld lines6 on test pieces. They looked like small rivers crossing the surface, spoiling the smooth look we wanted. Our injection speed was too high, causing turbulence inside the mold. This turbulence left marks. Air got trapped too, causing black spots and scorching happened like magic!
-
Internal Quality
There was also the issue of flash. Imagine creating a design carefully, only for it to overflow at the edges due to too much pressure. It created a mess needing extra work. Worse, internal stresses appeared; these stresses went unnoticed until pieces cracked after some tests.
Effects of Low Injection Speed
-
Appearance Quality
Slowing down didn’t solve everything. I remember a prototype that wasn’t filled completely; it looked incomplete! This happens when the melt fails to fill the cavity quickly enough before cooling.
-
Internal Quality
The surface quality also declined; our casings appeared dull instead of glossy. Slower speed allowed more crystal formation in crystalline plastics, changing properties unexpectedly.
Learning from Case Studies on Density Distribution
Over time, fast and slow speeds both showed downsides. It’s a delicate task to find the perfect speed that ensures appearance and quality meet well.
Speed Type | Appearance Defects | Internal Issues |
---|---|---|
Fast | Flow marks, Flash | Internal stress, Uneven density |
Slow | Short shot, Poor gloss | Crystallinity changes |
Through trial and many mistakes—and yes, some frustration too—I have learned exploring real-world cases and projects is crucial. Understanding how different injection speeds7 affect plastic products helps us decide better on future designs. This way, achieving an ideal balance for excellent quality is possible. The lessons learned are significant.
Fast injection speed causes uneven density.True
Fast speeds create turbulence, leading to uneven density distribution.
Slow injection speed prevents all surface defects.False
Slow speeds can cause short shots and poor bonding, leading to defects.
Why is Injection Speed Critical for Avoiding Product Defects?
You know the moment when everything fits together perfectly and you suddenly understand how something works? That’s the feeling when you grasp how injection speed in molding operates.
Injection speed holds a key role in molding. Fast injection speed causes flow marks and traps air. A slow speed leads to short shots and dull surfaces. Balance is vital. Avoid defects by balancing speed.
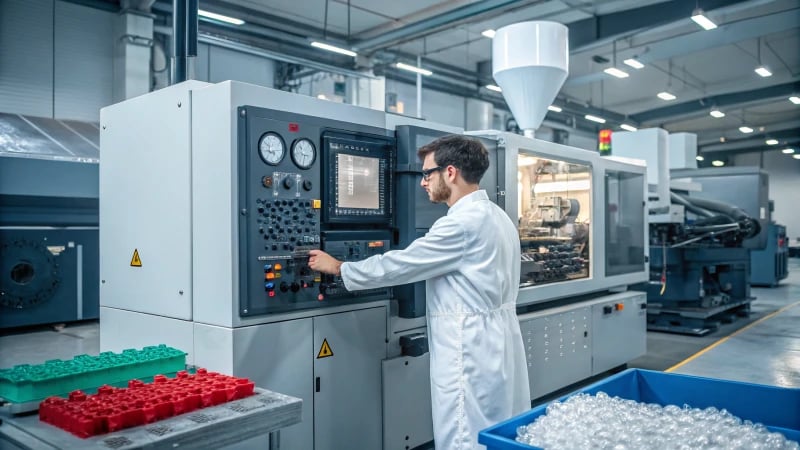
The Impact of Very Fast Injection Speed
Think about pouring soda too quickly. You get bubbles and a messy overflow. This happens in molding if speed is too fast. I used to think faster speed was better, but soon, I saw problems like appearance issues due to high speed causing turbulence. It felt like trying to control a wild river inside a small mold.
I worked on a project with high speed to meet deadlines. The result? Flow marks and weld lines appeared—ugly! We also had air trapped causing black spots. My boss wasn’t happy! Also, there was flash, where plastic went where it shouldn’t, needing more work to fix.
Some problems aren’t visible at first, like residual stress. This can cause warping or cracking later. Picture a gear breaking after a few uses—not good! Uneven density also matters in precise parts, where every detail counts.
Defect Type | Cause | Impact |
---|---|---|
Flow Marks | Turbulence due to high-speed melt | Surface imperfections |
Air Entrapment | Air trapped due to rapid cavity filling | Scorching or blemishes |
Flash | Excessive cavity pressure | Additional processing required |
Internal Stress | Quick cavity fill leading to residual stress | Deformation and cracking |
Uneven Density | Complex flow dynamics | Performance issues in precision parts |
Problems of Slow Injection Speed
On the other hand, I tried going slow, hoping to fix these issues. But slow isn’t always better. Imagine a cake half-baked—you get a short shot, a product that’s only partly filled.
The surface can turn dull if the melt cools fast—like painting with a dry brush. My products looked dull, like they faded before use.
For plastics like PP or PA, slow speed can mess up crystallinity; I’ve seen them become brittle, not strong. Multi-component molds suffer at slow speed, leading to lamination problems.
Defect Type | Cause | Impact |
---|---|---|
Short Shot | Incomplete cavity fill before cooling | Incomplete product shape |
Poor Surface Gloss | Melt temperature drop during flow | Dull product appearance |
Crystallinity Change | Prolonged crystallization time | Altered physical properties |
Lamination Issues | Slow flow leading to weak layer bonding | Compromised product integrity |
Learning from these challenges showed me that balancing speed is an art, not just technology. Knowing both extremes helps my designs not only look nice but also work well. It’s about finding the perfect balance where efficiency meets quality—this lets us create products we truly feel proud of.
High injection speed causes flow marks.True
Rapid injection leads to turbulence, creating flow marks on surfaces.
Slow injection speeds improve surface gloss.False
Slow speeds drop melt temperature quickly, reducing surface gloss.
Conclusion
Injection speed significantly impacts plastic product quality, affecting appearance and internal properties. Balancing speed is crucial to avoid defects like flow marks, short shots, and uneven density.
-
Discover how internal stress impacts product durability and how to mitigate it for better performance. ↩
-
Learn effective techniques to reduce flow marks and enhance surface quality. ↩
-
Find out methods to address uneven density for improved precision component performance. ↩
-
Understanding crystallinity helps in assessing its impact on product toughness and hardness. ↩
-
Exploring lamination issues offers insights into enhancing layer bonding in injection molding. ↩
-
Discover how fast injection speeds cause flow and weld marks, affecting surface quality. ↩
-
Explore case studies showing how varying injection speeds affect products across industries. ↩