Do you ever think about how injection pressure changes the world of plastics? A journey behind the scenes awaits you.
Pressure during injection determines plastic product quality. It really affects surface smoothness, strength and inside structure. Right pressure fills the mold completely. This action reduces defects like flash or stress marks. The product looks better and lasts longer. This is very important.
Understanding the complex interaction between pressure and plastic changes how you make things. Imagine cooking pasta. With little heat, it remains hard. With too much, it becomes mushy. It’s the same with injection molding. Correct pressure gives shiny surfaces, accurate dimensions and good quality.
Once, I tested pressure settings to improve plastic parts’ transparency. Initially, pressure was too high. Parts had ugly flow marks like morning fog. Lowering pressure, I reached the perfect balance. Clarity and strength came together flawlessly. Each change in pressure taught me more about keeping shape and reducing stress.
I’ve realized injection pressure is an art needing precision and patience. It’s not just a machine setting. Whether you need strong car parts or perfect seal density, knowing this key detail helps you make great products.
High injection pressure improves surface quality of plastics.True
Higher pressure ensures better mold filling, enhancing surface finish.
Low injection pressure increases internal stress in plastics.False
Insufficient pressure can cause incomplete filling, but not directly stress.
What Happens When Injection Pressure is Too High or Too Low?
Have you ever thought about why your molded products sometimes lack perfection? It’s all due to the pressure!
High injection pressure creates defects like flash and extra internal stress. These problems spoil the surface quality and weaken strength. Low pressure has its own issues. It causes incomplete mold filling. This results in short shots and wrong sizes.
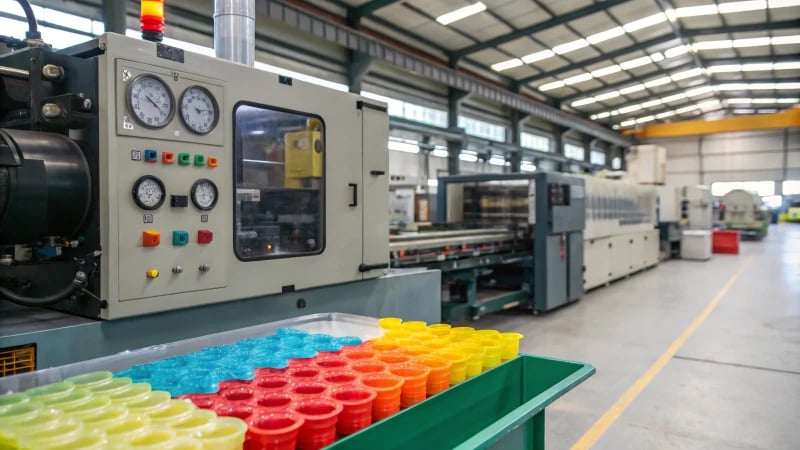
Effect on Appearance and Function
- Surface Quality: Recently, I worked with clear plastics and set the injection pressure too high. The result was unattractive flow and gas marks that ruined the clarity and shine I wanted. It was a hard lesson. High pressure causes turbulent flow, which leads to surface problems. On the other side, low pressure causes short shots, leaving your product looking incomplete.
Pressure Level | Effects on Surface |
---|---|
Too High | Flow Marks, Gas Marks |
Too Low | Short Shots |
- Dimensional Accuracy: Too much pressure widens the mold cavity, making products shrink after demolding. Once, I was confident in the design measurements, but the pieces ended up smaller. Not enough pressure results in low density, making sizes not match the specifications.
Influence on Mechanical Properties
-
Strength and Toughness: I learned over time that adequate pressure strengthens products by compacting their structure. However, excess pressure causes stress, reducing toughness. This is particularly true in automotive parts1 where breakage isn’t an option.
-
Hardness and Stiffness: High pressure increases crystallinity in plastics, enhancing hardness. This feature is useful but risky if overdone. A thin line exists between improving properties and damaging the material’s natural structure.
Internal Quality Performance
-
Density and Porosity: Proper pressure reduces pores and increases density. This is crucial for high-density products like seals. A low-pressure setting once resulted in more pores, affecting quality.
-
Internal Stress: High pressure brings significant internal stress, risking deformation or cracking over time. Getting the pressure right is like finding the right track on a vinyl record – vital for stability and durability of products.
Grasping these subtleties has been key to optimizing injection molding settings2 to achieve quality goals. This journey involved much trial and error; yet each mistake brought me closer to mastering the art of pressure balance.
High injection pressure causes flow marks.True
High pressure leads to turbulent flow, causing surface defects like flow marks.
Low injection pressure improves dimensional accuracy.False
Low pressure results in insufficient density, causing size discrepancies.
How does injection pressure affect surface quality?
Ever thought about why some plastic items look perfect and others don’t? The secret lies in using the right injection pressure!
Injection pressure greatly affects the surface quality of molded plastics. High pressure often leads to defects like flash. Low pressure, on the other hand, may cause incomplete fills. Finding the perfect balance helps the product look its best. Performance is really important too. The right pressure helps.
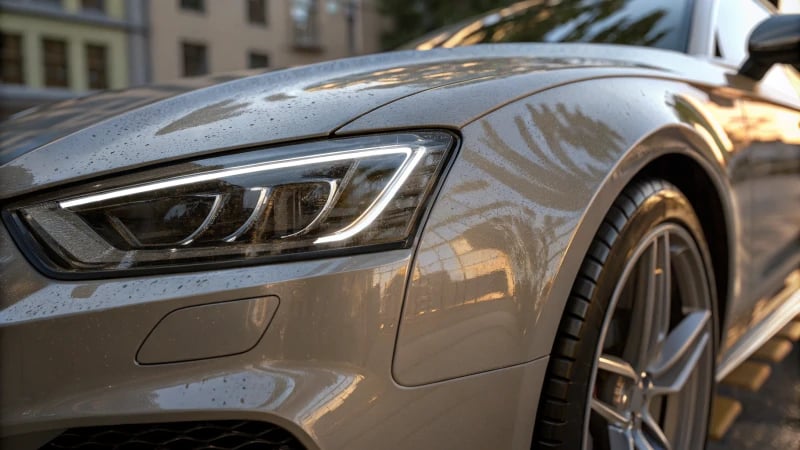
Impact on Appearance Performance
Plastic molding is really a sensitive process. Small defects like flashes and flow marks often ruin pieces. It’s similar to baking a cake with an oven that’s too hot, ending up crispy instead of soft and fluffy.
Excessive pressure pushes the plastic out of mold seams, creating flashes3 that spoil the product’s smooth appearance. Lower pressure results in incomplete pieces, much like when paint runs out and the wall looks spotty.
Pressure Level | Potential Effects |
---|---|
High | Flashes, flow marks |
Low | Incomplete filling |
Dimensional Accuracy
Getting sizes accurate is very important. I once misjudged this in a design and learned a hard lesson. Too much pressure causes parts to rebound or deform, like squeezing into clothes that are too tight.
Insufficient pressure results in products not reaching their intended design, much like a soufflé that falls flat.
Mechanical Properties: Strength and Toughness
Achieving a balance between strength and toughness resembles keeping a relationship healthy. Excessive pressure causes internal stress, risking sudden breaks, like bending a plastic ruler until it snaps.
Internal Quality: Density and Porosity
Internal quality depends on pressure. High pressure makes material dense, reducing porosity, much like removing bubbles from dough. Low pressure leads to porous, weak material, similar to bread with too many air pockets.
Ensuring proper density is crucial in making watertight seals4. Think of sealing an envelope without gaps to protect an important letter.
Managing Internal Stress
Let’s discuss internal stress in products. High pressure causes internal stresses that warp or crack over time, much like a bridge overloaded with weight. It might initially seem fine, but eventually cracks become visible.
Finding the right injection pressure is vital for a stable product. For more tips on achieving balance in injection pressure, explore injection molding techniques5 for better product results.
High injection pressure causes flashes on plastic surfaces.True
Excessive pressure forces plastic melt out of mold, creating flashes.
Low injection pressure improves dimensional accuracy.False
Inadequate pressure leads to incomplete filling, reducing accuracy.
How Does Injection Pressure Affect Mechanical Strength?
Have you ever asked yourself why that ideal mold wasn’t correct? Sometimes, pressure holds the secret.
Injection pressure affects mechanical strength by changing density and crystal formation. Correct pressure fills and packs the material well. It improves strength. Too much pressure creates stress and flaws.
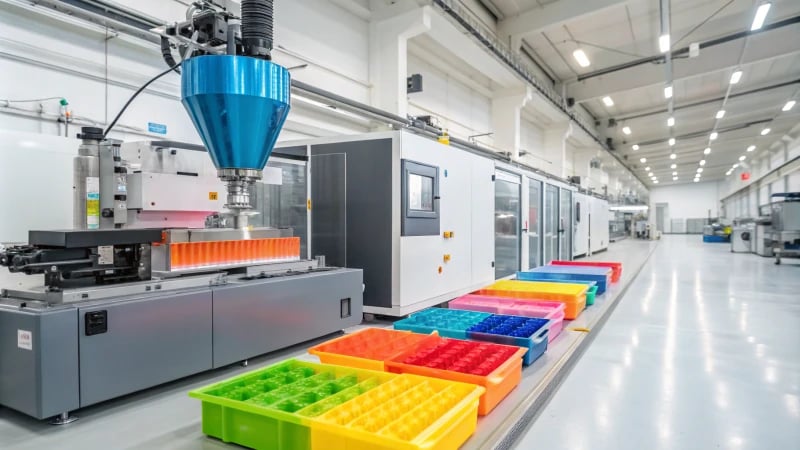
Surface Quality and Appearance Performance
Injection pressure has a significant influence on the surface quality of molded products. When set too high, the melt may escape through mold gaps, causing flash that deteriorates surface flatness. This can lead to defects like flow marks, especially noticeable in transparent products.
Pressure Level | Effect |
---|---|
Too High | Flash, turbulent flow marks |
Too Low | Incomplete filling, short shots |
For instance, automotive parts require flawless surfaces, which are compromised if the pressure is not optimal. Understanding these effects6 can prevent costly production errors.
Dimensional Accuracy
The dimensional accuracy of products is also closely tied to injection pressure. Excessive pressure might lead to mold expansion, causing dimensional rebound post-demolding. Conversely, low pressure results in insufficient filling, affecting product dimensions.
Strength and Toughness
Appropriate injection pressure enhances the internal structure, leading to denser products and improved strength. However, excessive pressure can induce internal stress, reducing toughness. This is crucial for components like automotive parts that must withstand substantial forces without cracking.
Injection Pressure | Mechanical Impact |
---|---|
Optimal | Denser structure, higher strength |
Excessive | Increased internal stress, less tough |
Hardness and Stiffness
Pressure changes impact crystallization and molecular arrangement. Higher pressure boosts crystallinity in plastics, increasing hardness and stiffness. Yet, too much pressure might disrupt material structure, compromising performance.
Internal Quality Performance
- Density and Porosity: High injection pressure compacts the melt, enhancing density and minimizing porosity. Lower pressures lead to more pores and lower density, affecting quality.
- Internal Stress: Excessive pressure introduces significant internal stress, potentially causing deformation over time. Setting optimal pressure reduces such risks.
For example, seals demand high density for effective sealing; understanding pressure settings7 ensures product reliability. Proper injection pressure management is key to maintaining high-quality standards in manufacturing.
Explore further insights8 on how adjusting injection parameters can refine product properties effectively.
High injection pressure increases density and reduces porosity.True
High pressure compacts the melt, enhancing density and minimizing porosity.
Excessive pressure improves the toughness of molded products.False
Excessive pressure induces stress, reducing toughness in molded products.
How Does Injection Pressure Impact Internal Stress and Density?
Have you ever thought about how the pressure applied in injection molding affects your product’s success?
Injection pressure affects internal stress and density by changing melt flow, crystallization and how molecules line up. High pressure increases density. It also raises internal stress, which impacts product performance. This is crucial.
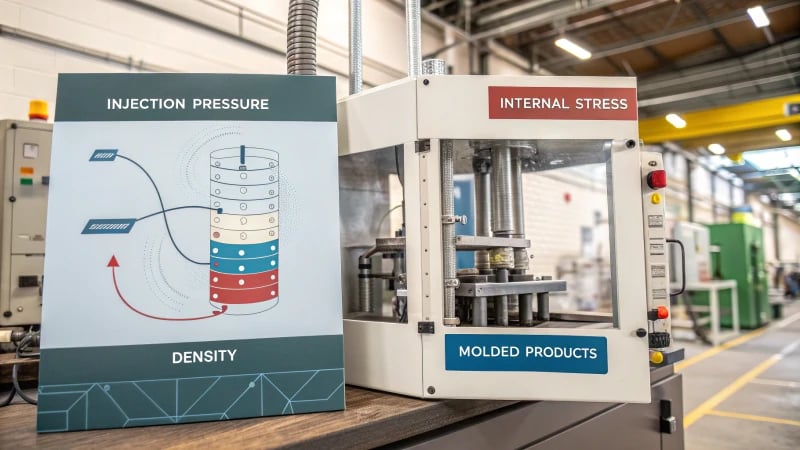
Surface Quality and Dimensional Accuracy
Injection pressure plays a vital role in product quality, impacting both surface quality and the exact size of the finished piece. High pressure often feels like using a double-edged sword; it might fill the mold well but may also cause defects like flash or flow marks. I remember a batch of clear parts turning cloudy due to a small pressure mistake.
Conversely, low pressure may lead to incomplete fillings or short shots, giving the surface an unfinished look. This balance is crucial for achieving the right appearance.
Pressure Level | Surface Defect | Dimensional Impact |
---|---|---|
High | Flash, Flow Marks | Smaller Size After Rebound |
Low | Incomplete Filling, Short Shots | Insufficient Density |
Strength, Toughness, and Stiffness
Correct injection pressure can really change a product’s strength and toughness. It feels like adding the perfect spice to a dish. Properly set pressure lets the melt fill the entire cavity, creating a strong internal structure. Excessive pressure risks making parts strong yet rigid.
Parts needing to withstand external forces, such as those in vehicles, rely on this balance. Too much pressure sometimes causes so much stress that parts crack during tests. Strength and toughness9 depend heavily on how well the melt fills the cavity.
Density and Porosity Considerations
An early mentor often said, "Density is destiny in molding." Time proved this true. High injection pressure compacts the melt, lowering porosity. This is vital for products like seals where density affects sealing performance.
Too little pressure creates products full of holes, like Swiss cheese; they don’t hold up well. Finding the perfect pressure spot for density and stress is essential. Density impact10 can be evaluated by analyzing porosity changes under different pressures.
Internal Stress Management
Managing internal stress is akin to balancing on a tightrope. Excessive pressure causes issues like deformation or cracking over time. I’ve seen products warp in storage from poorly managed stress during production.
Setting the right injection pressure manages these stresses, keeping the product stable and long-lasting. Internal stress control11 remains crucial for sustaining product quality over its entire life.
High injection pressure reduces product porosity.True
High pressure compacts the melt, reducing porosity and increasing density.
Low injection pressure improves surface gloss.False
Low pressure can cause incomplete filling, reducing surface quality and gloss.
Conclusion
Injection pressure critically influences plastic product quality, affecting surface finish, dimensional accuracy, strength, and internal stress. Optimal pressure balances aesthetics and performance for durable molded products.
-
Discover the significance of toughness in automotive components and its relation to injection pressure. ↩
-
Explore guidelines to optimize injection molding settings for superior product quality. ↩
-
Explore common causes of flash defects and how to prevent them in the injection molding process. ↩
-
Understand the impact of porosity on sealing efficiency in high-density plastic products. ↩
-
Learn about various techniques to optimize injection molding parameters for better product outcomes. ↩
-
Learn how different levels of injection pressure impact surface quality and avoid common defects in molded products. ↩
-
Understand the critical role of injection pressure in achieving optimal product density and minimizing porosity. ↩
-
Discover strategies for adjusting injection parameters to enhance product properties and ensure high-quality manufacturing outcomes. ↩
-
Understanding this link helps improve product durability by managing melt fill efficiency. ↩
-
Explores how adjusting pressure influences porosity and overall material quality. ↩
-
Guides on controlling stresses for enhanced product longevity and performance. ↩