Have you ever thought about how a minor change in pressure during injection might change the entire life of a plastic item?
Injection pressure directly affects the mechanical, size and physical traits of plastic items. Correct pressure increases strength, damage resistance and accuracy. Wrong pressure causes issues like internal stress and size mismatches.
I remember the first time I worked on an injection molding project. The learning was difficult. I discovered how important injection pressure was as I played with the settings. It felt like finding the balance between a firm handshake and a painful grip. This tiny change could mean the difference between a strong product and one that breaks easily.
For example, when building something as tough as a support for buildings, getting the injection pressure right helped the product hold weight without breaking. In the same way, when designing car bumpers, too much pressure made them fragile, but just enough pressure made them strong against hits.
This experience taught me that injection pressure affects the strength, toughness and size stability of plastic products. Like when I worked on a mobile phone case design; the perfect fit needed precision. High pressure caused the case to shrink after molding; low pressure meant it wouldn’t fit well with internal parts.
Injection pressure also affects weight and density. It’s very fascinating how such a small detail can impact every part of product design. This ranges from making sure aerospace parts are the right weight to keeping insulation properties in electronics. Every change felt like tuning an instrument, where every little adjustment added to the harmony of the final product.
High injection pressure reduces internal stresses in plastics.True
Correctly set high pressure can optimize polymer flow, reducing stress.
Injection pressure has no effect on dimensional accuracy.False
Pressure affects material flow and cooling, impacting final dimensions.
How Does Injection Pressure Influence Mechanical Properties?
Do you ever think about why small details in factories have such great impact?
Injection pressure greatly affects mechanical traits such as strength, toughness and stability. Proper control helps increase load-bearing capacity, impact resistance and precise fitting. These factors are crucial for top product quality.
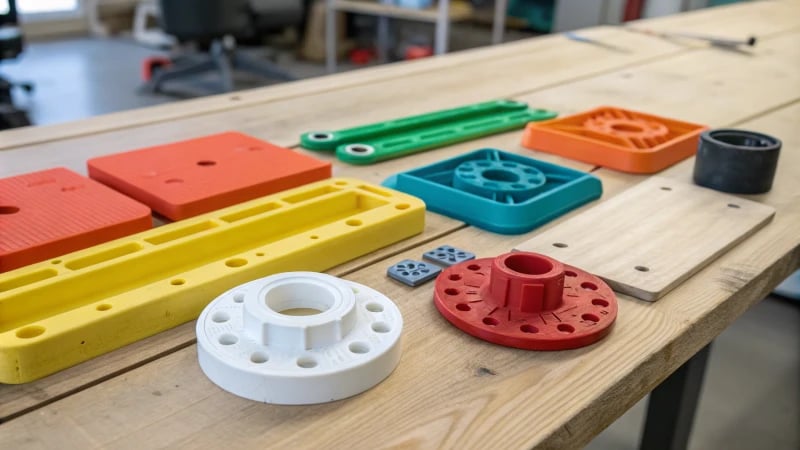
Strength and Load-Bearing Capacity
The first time I learned about injection pressure1‘s importance was during a project on plastic parts for building supports. Pressure levels decide if a structure stands strong or falls apart. Proper injection pressure allows the plastic melt to fill the mold completely, creating a dense structure that holds loads without collapsing. But if pressure is too low, weak points can form, like holes or incomplete areas, risking the part’s strength. Weak points are dangerous.
Parameter | Effect on Strength |
---|---|
High Pressure | Enhances compactness |
Low Pressure | Causes structural defects |
Toughness and Impact Resistance
Once, I worked on car bumpers and truly learned about toughness. Very high pressure might cause internal stress, weakening the bumper’s strength. Correct pressure helps spread the melt evenly, increasing toughness. The bumper becomes a solid shield, absorbing hits during crashes. This taught me that adjusting pressure is key in molding techniques2 for better impact resistance.
Dimensional Stability
Achieving dimensional stability was quite difficult in my early work. High pressure caused parts to change shape after cooling due to stress relief. Correct pressure control makes parts fit perfectly with others, like in electronic cases. Incorrect pressure often resulted in annoying issues like gaps or misfits.
Physical Properties
In projects focused on density and weight, I saw how crucial pressure control is. In aerospace, higher pressures compress the melt more, raising density which is important for weight needs. Also, injection pressure impacts thermal and electrical properties in special plastics.
- Density and Weight: To achieve needed density without extra weight, careful pressure control is important.
- Thermal and Electrical Performance: Correct pressure influences crystallinity in plastics, bettering thermal conductivity and electrical insulation.
Learning these details about injection pressure was vital for my growth as a mold designer. It makes a difference between just meeting standards and achieving high product performance. With strong pressure management methods3, products not only meet but exceed expectations.
High injection pressure enhances strength.True
High pressure densifies the material, boosting load-bearing capacity.
Excessive pressure improves impact resistance.False
Excessive pressure induces stress, reducing impact resistance.
How Does Injection Pressure Influence Dimensional Stability?
Do you ever think about how injection pressure affects the perfection of your molded pieces? Pressure is crucial for accuracy. It really is.
Injection pressure is very important for dimensional stability. It affects how plastic flows into the mold. Proper pressure makes the density even throughout the piece. This helps reduce internal stresses. Deformation and size changes are minimized over time.
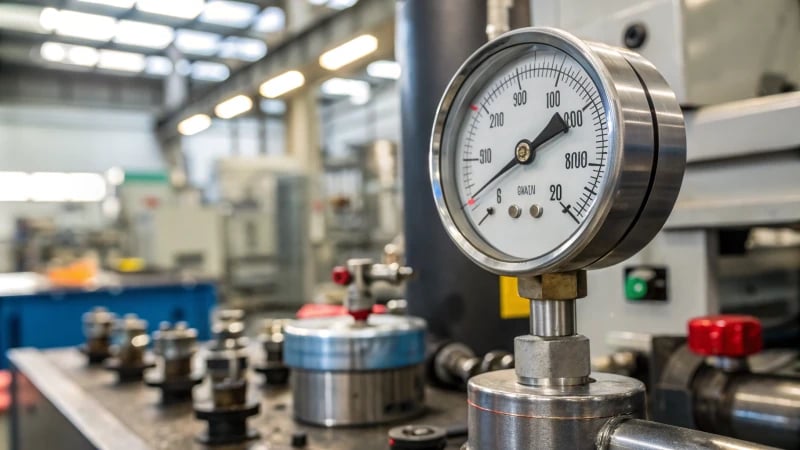
The Role of Injection Pressure in Mechanical Properties
I remember my early days in plastic molding. Injection pressure felt like magic. Balancing force and gentleness was key. Over time, I learned. Injection pressure is very important for plastic’s strength. Imagine building a strong support. Without correct pressure, the part breaks under weight. Correct pressure fills every small space, creating a solid structure.
However, there is a twist. Very high pressure brings trouble. Internal stresses make parts weak. I faced this with a car bumper; one mistake and the bumper cracks instead of protects.
Mechanical Properties | Impact of Injection Pressure |
---|---|
Strength | Improved with sufficient pressure |
Toughness | Decreases with excessive pressure |
Dimensional Stability and Long-term Changes
Achieving perfect shape stability is challenging. Too much pressure and parts shrink after cooling—it’s like finding tighter jeans after washing. Little pressure causes uneven density, leading to changes over time.
Especially with things like electronic equipment housings4, precise pressure is a must. These housings must fit well with other parts; any small change affects the whole setup.
Impact on Physical Properties: Density and Beyond
Let’s discuss density—it’s not just a number; it’s a key characteristic. High pressure raises density, which could be good or bad based on use. For example, in aerospace, every gram matters; too much density is a disadvantage.
For plastics with special properties, correct pressure is vital as it affects traits like heat conduction or insulation—crucial for components like insulating shells5 in electronics.
Physical Properties | Effect of Pressure |
---|---|
Density | Increases with higher pressure |
Thermal Properties | Affected by crystallinity adjustments |
Through many experiments, I found how controlling pressure changes everything—products not only meet but often surpass expectations in both performance and quality.
High injection pressure increases product density.True
Higher pressure compacts molecular structures, raising density.
Excessive injection pressure enhances toughness.False
Too much pressure introduces stresses, reducing toughness.
Can Injection Pressure Impact the Physical Properties of Plastics?
Have you ever thought about how pressure changes your plastic designs completely? Pressure matters a lot. It transforms the shape and strength of plastic creations. It surprises many. It fascinates those who learn about it. Simple pressure influences every aspect. Effects can be noticeable and sometimes invisible. But they are real.
Injection pressure affects the physical traits of plastics, such as strength and density. Proper control remains crucial for performance. Incorrect settings might cause defects. Performance revolves around this aspect. Reduced functionality may also result from wrong adjustments.
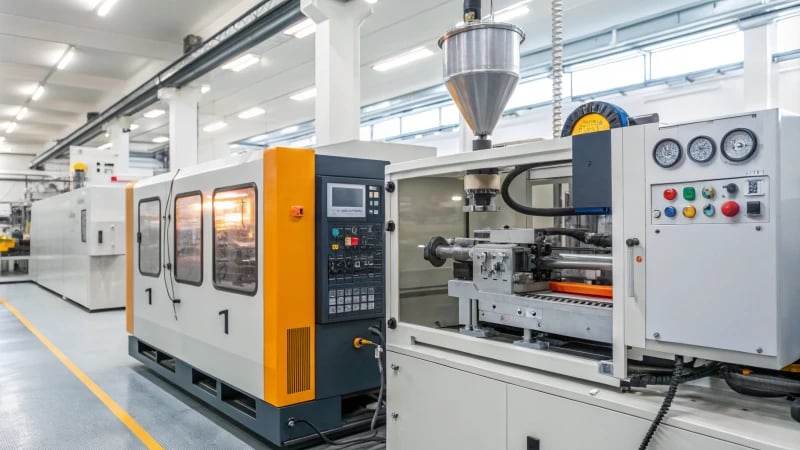
Understanding the Role of Injection Pressure
I remember the first time I understood how important injection pressure is. It was late at night in the workshop. I was trying to get a mold perfect for a new project. The difference between a perfect part and a flawed one was all about pressure settings. Injection pressure is very important because it helps the plastic completely fill the mold, enhancing the strength and load-bearing capacity6 of components. This strength is key for parts used in tough places, like building supports, where failure is not an option.
Mechanical Properties: Strength and Toughness
Controlling injection pressure is like walking a tightrope. High pressure pushes molecular chains close together, which increases strength. But too much pressure causes internal stresses that weaken toughness and impact resistance7. Crafting something like an automobile bumper requires precision; the bumper must take a hit without breaking.
Property | Impact of Injection Pressure |
---|---|
Strength | Increased with optimal pressure. |
Toughness | Reduced with excessive pressure. |
Dimensional Stability | Affected by both high and low pressures. |
Dimensional Stability Concerns
Injection pressure affects dimensional stability too. High pressures sometimes cause parts to change in size after cooling due to rebound effects from internal stress release, resulting in size discrepancies after demolding. Low pressure might lead to parts with uneven density, which hurts long-term dimensional stability8 and can lead to deformation.
For parts needing exact sizes, like in electronic housings, maintaining accurate matching accuracy9 through controlled pressure is vital to ensure components fit seamlessly without gaps or looseness.
Exploring Physical Properties: Density and Weight
Injection pressure affects plastic density as well. High pressures produce denser, heavier products, impacting applications where weight really matters, such as in aerospace or portable electronics. Correct pressure helps meet design needs without adding unnecessary weight.
For plastics with special thermal or electrical traits, managing pressure carefully really matters. Proper settings can enhance crystallinity, improving thermal conductivity10 and electrical insulation.
In summary, understanding how injection pressure affects physical properties can change manufacturing methods and improve product quality across various applications. Applying this knowledge well helps avoid defects and improves plastic component performance.
High injection pressure increases plastic strength.True
Optimal pressure compacts molecular chains, enhancing strength.
Excessive injection pressure improves toughness.False
Too much pressure induces internal stresses, reducing toughness.
How Do You Set Injection Pressure for Optimal Manufacturing?
Ever thought about how injection pressure could improve or ruin your manufacturing process?
Setting injection pressure correctly involves balancing the mechanical, size and physical traits of plastics. Correct pressure helps in achieving strength and toughness in the product. It also leads to precise dimensions. Certain thermal or electrical features develop as desired too.
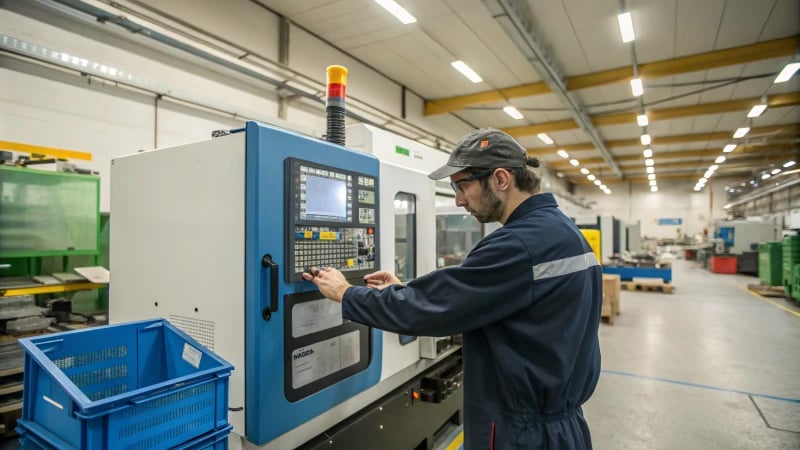
Understanding Mechanical Properties
One time, I worked on a project focused on getting the right injection pressure for a plastic part used in building supports. The part had to handle heavy loads. I carefully adjusted the pressure so the plastic filled the mold perfectly, ensuring tightly arranged molecular structures like strength and load-bearing capacity11. It was like fitting a puzzle piece into place. This care meant the part didn’t just meet, it went beyond load expectations.
However, I learned that too much pressure could be harmful. Excessive pressure can introduce internal stresses, reducing toughness and impact resistance12. I once worked on car bumpers and found that extra pressure caused internal stresses. The bumpers turned out less resistant to impacts than expected. Now, I always find that perfect zone where pressure strengthens toughness without causing cracks.
Keeping Dimensional Stability
Dimensional stability is something I’ve come to value over time. High pressure might cause products to rebound post-demolding due to stress release, affecting long-term use. Insufficient pressure can lead to density variations and deformation.
I remember working on a mobile phone case that needed to fit very precisely with the circuit board inside. Proper control ensures matching accuracy13 with other components; this precision is crucial in applications like electronic housings, where fit is essential. High pressure would shrink the case after molding; low pressure risked density changes. Perfect fit required several tries but mattered a lot, keeping the case snug and safe around those delicate parts.
Managing Physical Properties
In another project, making parts for an aerospace task needed careful pressure control to maintain weight and density. Injection pressure influences the density and weight14 of plastic products. Wrong pressure made parts too heavy, affecting aircraft performance. It felt like balancing on a tightrope – precision mattered.
When plastics had unique thermal or electrical properties, such as in insulation tasks, it was important to get the pressure just right. For plastics with special thermal or electrical attributes, accurate pressure enhances their properties by preventing defects that could risk safety.
Property | Impact of Injection Pressure |
---|---|
Strength | Improves with adequate pressure |
Toughness | Reduced by excessive pressure |
Dimensional Accuracy | Achieved through precise control |
Density | Affected by high pressures |
Thermal Properties | Enhanced with proper crystallinity |
These practices not only helped refine manufacturing processes but also made sure our final products consistently met quality standards. Adjusting injection pressure correctly really improves product performance and longevity. It’s been quite a journey to master this side of manufacturing, but seeing great results always feels very worthwhile.
Excessive injection pressure reduces product toughness.True
High pressure introduces internal stresses, decreasing toughness.
Low injection pressure increases dimensional stability.False
Insufficient pressure can cause deformation, reducing stability.
Conclusion
Injection pressure significantly influences the strength, toughness, and dimensional stability of plastic products. Proper control enhances performance while incorrect settings can lead to defects and reduced functionality.
-
Learn how injection pressure influences the strength and load-bearing capacity of plastic products. ↩
-
Discover techniques in injection molding that enhance impact resistance through precise pressure control. ↩
-
Explore strategies for managing injection pressure effectively to optimize product quality. ↩
-
Understand why precise dimensions are crucial for electronic housings to ensure compatibility. ↩
-
Learn about how pressure affects the thermal conductivity and insulation properties of plastics. ↩
-
Explore how proper injection pressure settings enhance the strength and load-bearing capacity of plastics. ↩
-
Learn why excessive injection pressure can reduce toughness and how it affects product performance. ↩
-
Discover how varying pressures can affect long-term dimensional stability in plastic products. ↩
-
Find out why precise injection pressure ensures accurate fitting with other components. ↩
-
Understand how proper injection pressure can enhance thermal conductivity and electrical insulation in plastics. ↩
-
Discover how injection pressure impacts the mechanical strength of molded plastics. ↩
-
Learn why excessive injection pressure can compromise toughness and how to avoid it. ↩
-
Understand how to achieve precise dimensional accuracy with proper injection pressure. ↩
-
Explore how controlling injection pressure affects the weight and density of products. ↩