The exciting relationship between injection pressure and molded parts decides the success of a design. These forces shape our plastic creations in interesting ways.
Injection pressure plays a key role in molding. It decides how parts look, how accurate they are and how strong they become. The right pressure creates smooth surfaces and exact sizes. It also leads to strong parts. Wrong pressure results in problems. Issues may include flash, shrinkage and stress.
I recall long ago, watching in amazement as a colleague skillfully changed the injection pressure on a machine. A small change could turn an ugly lump into a perfect piece. That day, I learned that knowing injection pressure is not just technical – it’s an art.
Injection pressure affects more than just machines. It shapes beauty and usefulness. Too much pressure results in ugly marks or, worse, weak spots that might break. Too little pressure creates parts that don’t have the strength to last long.
Finding the perfect injection pressure proves challenging. It is very important for the best performance of molded parts. Accurate pressure leads to a shiny surface or perfect shape. The right pressure truly matters. Molded parts respond differently to various pressures. Let’s explore how this happens.
Higher injection pressure reduces shrinkage marks.True
Increased pressure fills molds more completely, minimizing shrinkage.
Incorrect injection pressure enhances mechanical strength.False
Incorrect pressure can introduce defects, weakening the part's structure.
- 1. Why is Injection Pressure Important in Molding?
- 2. How Does Injection Pressure Influence Surface Quality?
- 3. How Does Injection Pressure Impact Dimensional Stability?
- 4. Why is Internal Quality Dependent on Injection Pressure?
- 5. How Does Varying Injection Pressure Affect Product Quality?
- 6. Conclusion
Why is Injection Pressure Important in Molding?
I remember the first time I found out about injection pressure in molding. It felt like uncovering the secret to flawless products.
Injection pressure in molding pushes molten plastic into a mold cavity. This force is crucial. Quality, appearance and mechanical properties of the final product rely on it.
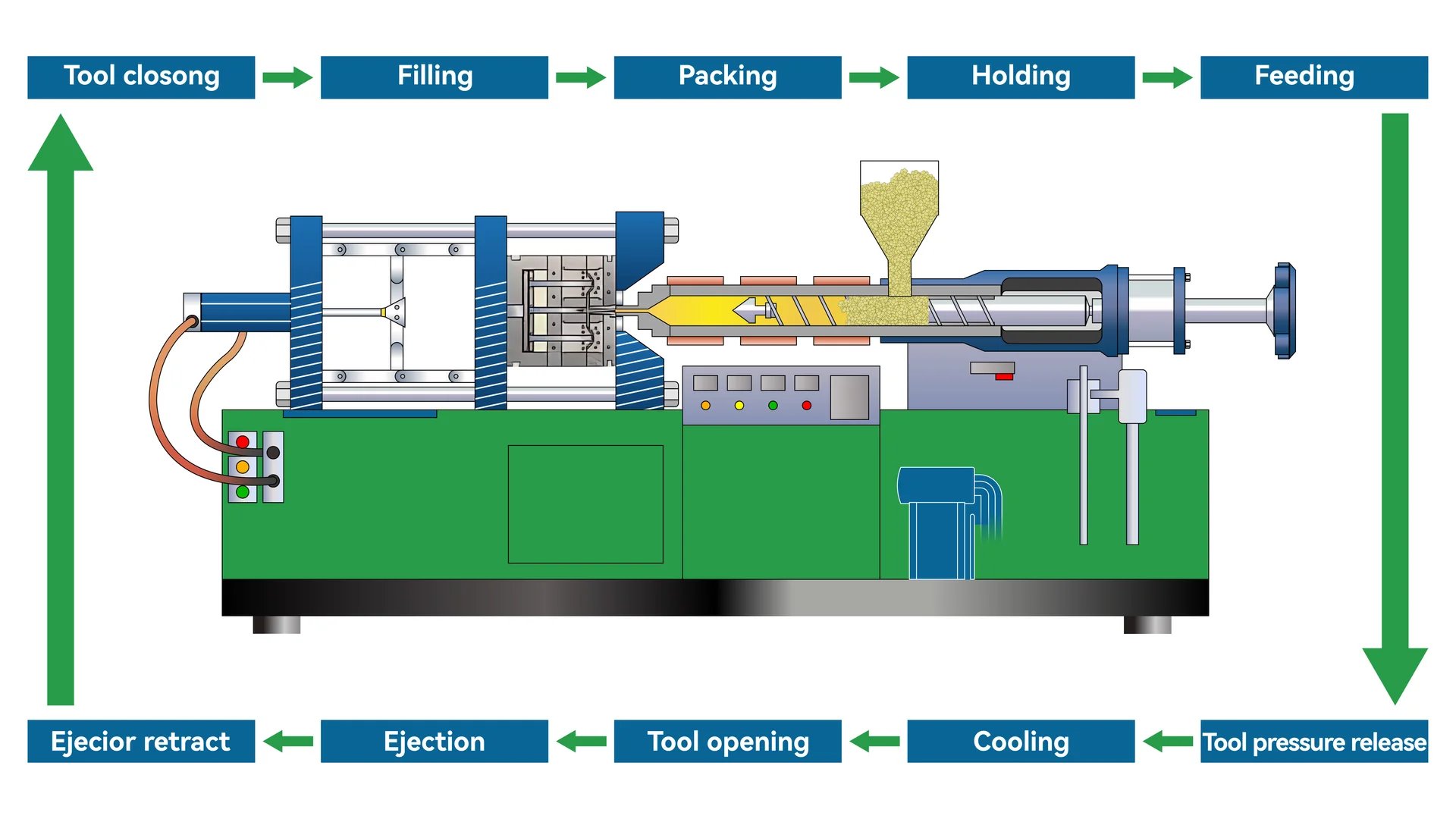
Importance of Injection Pressure
Injection pressure is a pivotal parameter in injection molding that impacts several aspects of the final product:
- Appearance Quality: Notice small defects like flash and weld marks1? These often happen due to wrong pressure settings. Finding the right pressure is like choosing the perfect gear when driving uphill.
- Dimensional Accuracy: Think of a jigsaw puzzle. Every piece must fit exactly. Proper pressure keeps parts stable and uniform, ensuring they fit snugly and accurately.
- Internal Quality: Imagine bread with air pockets. Not ideal, right? Good pressure reduces these pockets, making products dense and reliable.
- Mechanical Properties: Strength and toughness are like the backbone of a strong house. They are essential. Tuning the pressure improves these important traits.
Balancing Appearance Quality
Flash: High injection pressure can cause plastic to overflow, like squeezing too much toothpaste from the tube. This results in ugly flash, compromising neatness.
Surface Gloss: Achieving a glossy and smooth surface is the goal. Too little pressure leaves a dull, imperfect finish.
Achieving Dimensional Accuracy
In complex molds, injection pressure acts like a conductor in an orchestra:
- Dimensional Stability: It means getting that perfect fit after demolding.
- Wall Thickness Uniformity: Pressure must be just right to keep thickness even.
Property | Effect of Pressure |
---|---|
Flash | High pressure causes flash |
Surface Gloss | Low pressure causes defects |
Dimensional Stability | Correct pressure ensures stability |
Improving Internal Quality
Proper pressure reduces internal pores and boosts density. It’s like making sure your favorite chocolate bar has no air bubbles—solid through and through.
Residual Stress: High pressure may increase stress, leading to cracks or deformation during use. Adjusting pressure can mitigate these issues.
Optimizing Mechanical Properties
This process changes how molecules arrange in the plastic, like stacking blocks carefully. Adjusting parameters influences tensile strength and toughness, making products durable and appealing by adjusting parameters2.
Understanding injection pressure helps engineers refine designs, creating products that are both practical and visually attractive.
High injection pressure causes flash.True
Excessive pressure forces plastic melt to overflow, creating flash.
Low injection pressure improves surface gloss.False
Insufficient pressure can lead to shrinkage marks, reducing gloss.
How Does Injection Pressure Influence Surface Quality?
Some plastic items shine with a perfect, glossy finish, while others look dull and flawed.
Injection pressure plays an important role in injection molding. It directly affects how the surface looks. Correct pressure settings stop problems like flash, dull surfaces and weld marks. A smooth finish results from the right pressure. It’s really important for high-quality products.
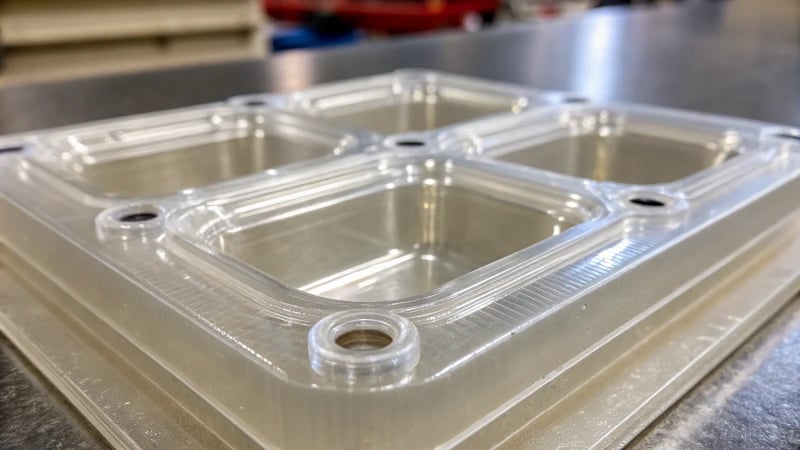
The Role of Injection Pressure in Appearance Quality
Pressure plays a vital role in how an injection molded part3 looks. It is truly fascinating. I once worked on a project where the pressure was slightly wrong. This mistake led to a part with unsightly flash – a thin plastic piece overflowing from the mold. At first, it seemed small, but once noticed, it became hard to ignore. Flash does not just ruin the look; it also affects the size and accuracy.
Conversely, another time, I dealt with too little pressure. The result was dull parts with visible weld marks where the plastic failed to flow and fuse well. It was a learning experience. Correct pressure is crucial for a smooth, glossy finish.
Defect | Cause |
---|---|
Flash | Excessive pressure |
Poor Gloss | Inadequate pressure |
Weld Marks | Insufficient pressure |
Impact on Dimensional Accuracy
Injection pressure also affects how well parts keep their intended size and shape. Proper pressure allows the plastic to be packed correctly, creating stable and even wall thickness. But applying excessive pressure can cause internal stress, which may lead to deformation after demolding.
Moreover, uniform wall thickness is achieved by balancing the pressure to ensure even distribution of the melt.
Internal Quality and Mechanical Properties
Inside the part, pressure influences density4 and stress. Proper pressure increases mechanical quality by lowering porosity and increasing density. However, excessive pressure can lead to internal stress that increases the risk of cracks or deformations over time.
Knowing these effects is key to setting the right injection pressure. This helps achieve both a good look and strong structure in molded parts.
Property | Effect of Pressure |
---|---|
Density | Increased with adequate pressure |
Porosity | Decreased with sufficient pressure |
Residual Stress | Increased with high pressure |
High injection pressure can cause flash defects.True
Excessive pressure forces material out of the mold, causing flash.
Insufficient injection pressure improves surface gloss.False
Low pressure leads to poor gloss due to incomplete mold filling.
How Does Injection Pressure Impact Dimensional Stability?
Have you ever thought about how a small change in injection pressure could greatly improve or ruin your molding process?
Injection pressure plays an important role in keeping molded parts stable in size. Correct pressure gives even compaction, reducing deformation and improving precision. Low pressure leads to uneven density. Excessive pressure causes stress and deformation.
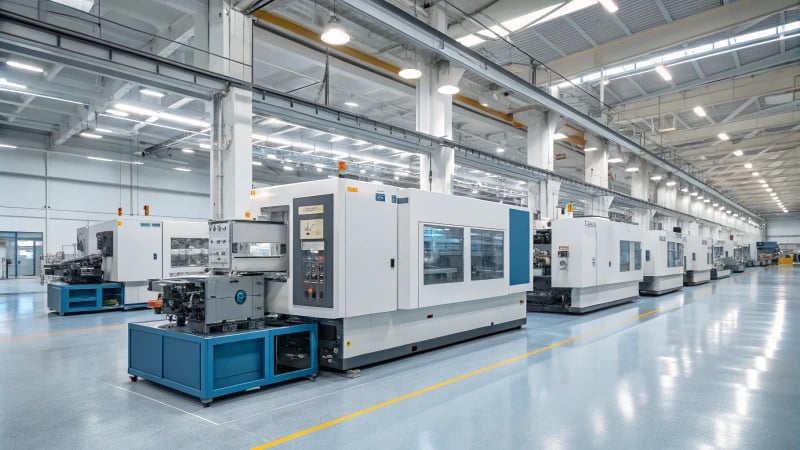
The Role of Injection Pressure in How Parts Hold Their Shape
When I began working with injection molding, I quickly saw how even small changes in injection pressure changed the process. Think of baking a cake; if the oven temperature isn’t right, the cake might collapse or be uneven. In the same way, injection pressure controls how plastic melt fills and packs in the mold. Correct pressure gives a stable part. If it’s slightly off, problems like deformation could occur.
Factors Influencing Stability
- Residual Stress: Consider residual stress as small annoyances that grow over time. High pressure bottles these until the part warps. Managing pressure reduces stress, leading to better stability.
- Wall Thickness Differences: Icing a multi-layer cake and getting even layers can be hard. Uneven pressure creates similar problems with wall thickness, affecting uniformity5. Balanced pressure helps keep thickness consistent, even in complex shapes.
Pressure Level | Effect on Dimensional Stability |
---|---|
Low | Uneven density, poor accuracy |
Optimal | Good stability, consistent output |
High | Deformation due to residual stress |
Look and Quality Issues
- Flash: Imagine overfilling a coffee mug until it spills. Excess pressure causes flash, risking both appearance and accuracy. Proper settings prevent this.
- Surface Gloss and Weld Lines: Right pressure is like smoothing frosting on a cake. It ensures an even fill for a polished look, reducing flaws like weld lines6.
Keeping Mechanical Properties
- Density and Porosity: Proper kneading helps bread rise evenly. Correct pressure compresses the melt, increasing density and strength. Low pressure can create air pockets like under-kneaded dough.
- Strength and Toughness: Injection pressure changes the plastic’s molecular structure, just like a perfect recipe affects the dessert’s texture. Proper settings give parts strength and toughness, making them last longer.
Understanding these factors helps me adjust injection settings for steady, reliable results. This accuracy is crucial for designers like Jacky, who balance looks and function in manufacturing scenarios.
Summary of Effects
Mastering injection pressure is like finding the perfect cooking temperature. It’s crucial for keeping shapes stable by tackling things like residual stress and maintaining even density distribution to create high-standard products.
High injection pressure causes residual stress.True
High pressure induces stress, leading to potential deformation post-release.
Low injection pressure improves wall thickness uniformity.False
Low pressure leads to uneven density and thickness variations in the mold.
Why is Internal Quality Dependent on Injection Pressure?
Ever thought about why injection pressure really matters in molding? It goes beyond a technical term. It holds the key to creating top-quality parts!
Injection pressure plays an essential role in injection molding. It directly shapes the internal quality of parts. Strong parts free from defects rely on this pressure. Density and porosity depend heavily on it. Residual stress also relates to this pressure. Parts stay robust with the right pressure. The process really needs this precise control.
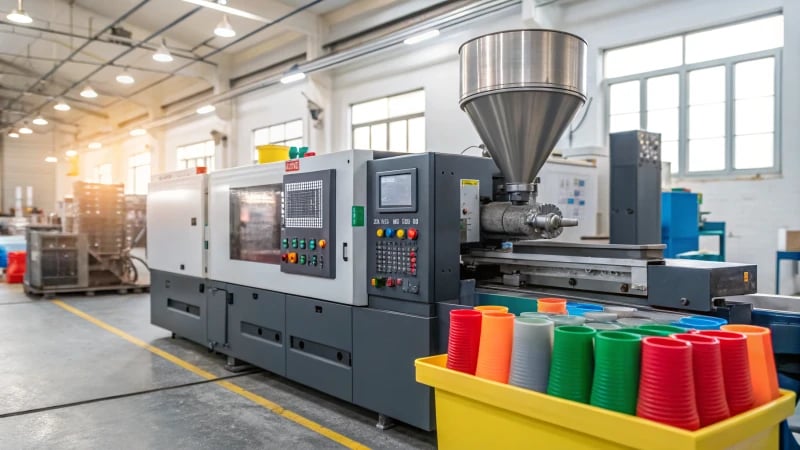
Influence on Density and Porosity
I recall the first time tiny air bubbles ruined some perfectly shaped parts. That day, I understood how important injection pressure really is. Think of packing a suitcase: more pressure pushes out more air. Injection molding works the same way. Correct pressure packs the melt tightly, lowering air gaps and making the part stronger. Insufficient pressure leaves weak areas in the part.
Injection pressure significantly impacts the density7 and porosity of molded parts. Adequate pressure compacts the melt, reducing internal voids and enhancing mechanical integrity. Conversely, low pressure can trap air, leading to porosity and weak spots.
Pressure Level | Effect on Porosity |
---|---|
High | Low porosity |
Low | High porosity |
Residual Stress Considerations
Residual stress is tricky! It secretly causes unexpected cracks or bends. I once made a batch of parts that seemed perfect until they cracked with little pressure. Excessive injection pressure was the problem, causing high residual stress. Finding the right balance, using enough pressure to keep strength but not too much, is like walking on a thin wire.
Residual stress is another factor where injection pressure plays a pivotal role. High pressure increases residual stress, potentially causing cracks or warping. However, proper control can mitigate these issues, ensuring reliability and longevity of parts.
- High Pressure: Raises stress and chance of bending; increases risk of deformation.
- Moderate Pressure: Keeps a balance between stress and strength; balances structural integrity.
Mechanical Properties Improvement
The link between pressure and material strength reminds me of a science project where tight molecules created strong materials. In molding, the right pressure lines up polymer chains, giving better strength and toughness. Straying from this can lead to faults, similar to a weak house collapsing under weight.
Injection pressure affects the arrangement of polymer chains, impacting strength and toughness8. Optimal pressure aligns molecules for better tensile and impact strength while improper levels lead to defects.
The following table illustrates how pressure variations affect mechanical properties:
Property | Low Pressure | Optimal Pressure | High Pressure |
---|---|---|---|
Tensile Strength | Low | High | Medium |
Impact Toughness | Poor | Excellent | Good but stress-prone |
Dimensional Accuracy and Uniformity
At first, I wondered why some parts had uneven thickness or bent shapes. It was confusing until I realized injection pressure holds the secret to stability and smoothness. Proper pressure fills the mold evenly, much like pouring cake batter – too much or too little can ruin it.
Injection pressure is directly tied to dimensional stability and wall thickness uniformity. Adequate pressure ensures even filling, maintaining part dimensions post-molding. Low or high pressures can cause deviations or uneven wall thicknesses.
- Dimensional Stability: Depends on good melt packing; linked to proper melt compaction.
- Uniform Wall Thickness: Comes from even pressure spread; achieved through balanced distribution.
Mastering injection pressure is not just about adjusting settings; it’s both an art and science that refines each part to near perfection. Understanding these details optimizes processes for any designer9, forming a base for anyone dedicated to excellence.
High pressure reduces porosity in molded parts.True
High injection pressure compacts the melt, reducing internal voids.
Low injection pressure improves tensile strength.False
Low pressure leads to poor polymer chain alignment, weakening strength.
How Does Varying Injection Pressure Affect Product Quality?
Have you ever thought about how altering injection pressures could really change your product’s quality? This balance is very delicate. It decides the final outcome.
Different injection pressures affect mechanical properties. They change the appearance, size accuracy and inside quality. High pressures often result in flash. Low pressures might cause weld marks. Density sometimes becomes uneven.
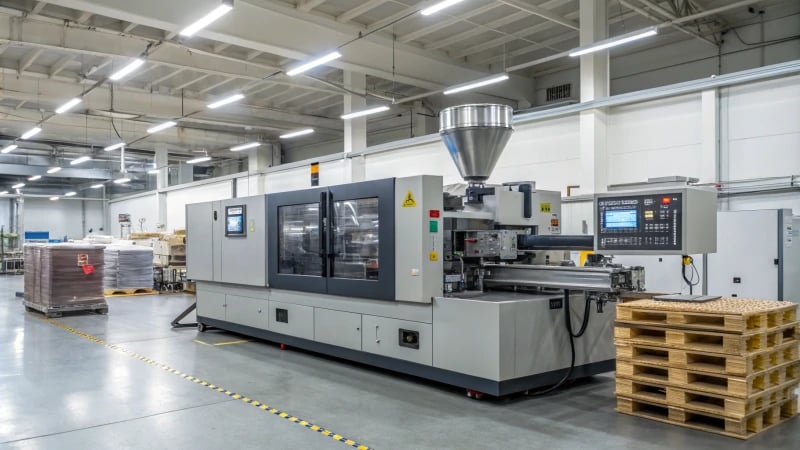
Appearance Quality
Flash and Surface Gloss
When I first began designing molds, I felt amazed by how injection pressure, though simple, could greatly affect the outcome. High injection pressure may lead to flash—a problem I saw many times—where molten plastic spills over and spoils clean lines. Conversely, appropriate pressure ensures a smooth glossy surface10 on sleek electronics. However, low pressure might cause shrinkage or flow marks instead.
Weld Marks
Oh, weld marks! Pressure affects the flow and fusion of plastic melt. Without enough pressure, parts do not fuse well at confluence points, leading to visible weld marks. I remember prototypes that looked like patchwork because of this issue.
Dimensional Accuracy
Stability and Uniformity
Pressure affects stability. Injection pressure directly relates to dimensional stability. High pressure can cause deformation from leftover stress, while low pressure results in uneven density and incorrect sizes.
Pressure | Effect on Wall Thickness |
---|---|
High | May cause local thickening |
Low | Leads to uneven distribution |
Internal Quality
Density and Porosity
Once, a client returned parts due to internal pores—too little pressure trapped gas. Sufficient pressure compacts melt, increasing part density and minimizing internal pores. Finding the right balance is key to preventing these flaws.
Residual Stress
High pressure raises residual stress, which can crack or deform parts during use. Proper control is crucial for reliable components.
Mechanical Properties
Strength and Toughness
Using the right pressure arranges molecular chains tightly for strength and toughness. Appropriate pressure enhances tensile and bending strength; wrong settings can really spoil these properties.
For more on optimizing mechanical properties11, research is ongoing.
Learning these interactions helped me improve processes for better products. Designers must consider these aspects for successful manufacturing plans.
High injection pressure leads to flash defects.True
Excessive pressure causes plastic to overflow mold gaps, creating flash.
Low injection pressure improves dimensional accuracy.False
Low pressure often results in uneven density and inaccuracies.
Conclusion
Injection pressure significantly influences the appearance, dimensional accuracy, internal quality, and mechanical properties of molded parts, making precise control essential for optimal product performance.
-
This link explains how varying injection pressures can result in flash and weld marks, affecting the product’s aesthetic quality. ↩
-
Explore this link to learn methods of adjusting molding parameters to improve mechanical properties like strength and toughness. ↩
-
Explore how injection pressure affects various aspects of molded parts’ appearance and performance. ↩
-
Learn effective strategies for optimizing injection pressure to achieve ideal product quality. ↩
-
Learn how balanced injection pressure ensures consistent wall thickness across molded parts. ↩
-
Understand how adequate pressure reduces weld marks, improving surface quality. ↩
-
Discover how varying injection pressures influence the density and porosity of molded parts. ↩
-
Learn about the impact of injection pressure on the strength and toughness of plastic parts. ↩
-
Explore how understanding injection pressure aids designers in optimizing mold designs. ↩
-
Explore how optimal injection pressure contributes to achieving a smooth, glossy surface finish in molded parts. ↩
-
Discover how injection pressure influences the mechanical properties of molded parts, including strength and toughness. ↩