Have you ever marveled at how precisely some products fit together? It’s often thanks to the wonders of injection molding!
Injection molding can achieve a dimensional accuracy of up to ±0.02mm, making it highly suitable for manufacturing precision parts. Factors such as mold quality, plastic material properties, and process parameters significantly influence the final accuracy.
But wait! There’s so much more beneath the surface that contributes to this level of precision. Let’s dive deeper into the factors that make injection molding a standout choice for manufacturing.
Injection molding achieves accuracy of ±0.02mm.True
Injection molding can produce parts with tight tolerances up to ±0.02mm.
- 1. What Is the Role of Mold Quality in Injection Molding Accuracy?
- 2. How Do Plastic Material Properties Affect Injection Molding Precision?
- 3. Which Injection Molding Process Parameters Are Crucial for Precision?
- 4. How Does Equipment Precision Impact the Accuracy of Injection Molding?
- 5. Conclusion
What Is the Role of Mold Quality in Injection Molding Accuracy?
The quality of the mold is pivotal in achieving precision in injection molding, influencing both dimensional and shape accuracy.
Mold quality directly affects the precision of injection-molded parts. High-quality molds ensure accurate dimensions and shapes, while wear and low-quality materials can cause deviations. Advanced processing techniques and robust materials enhance mold performance, crucial for maintaining accuracy.
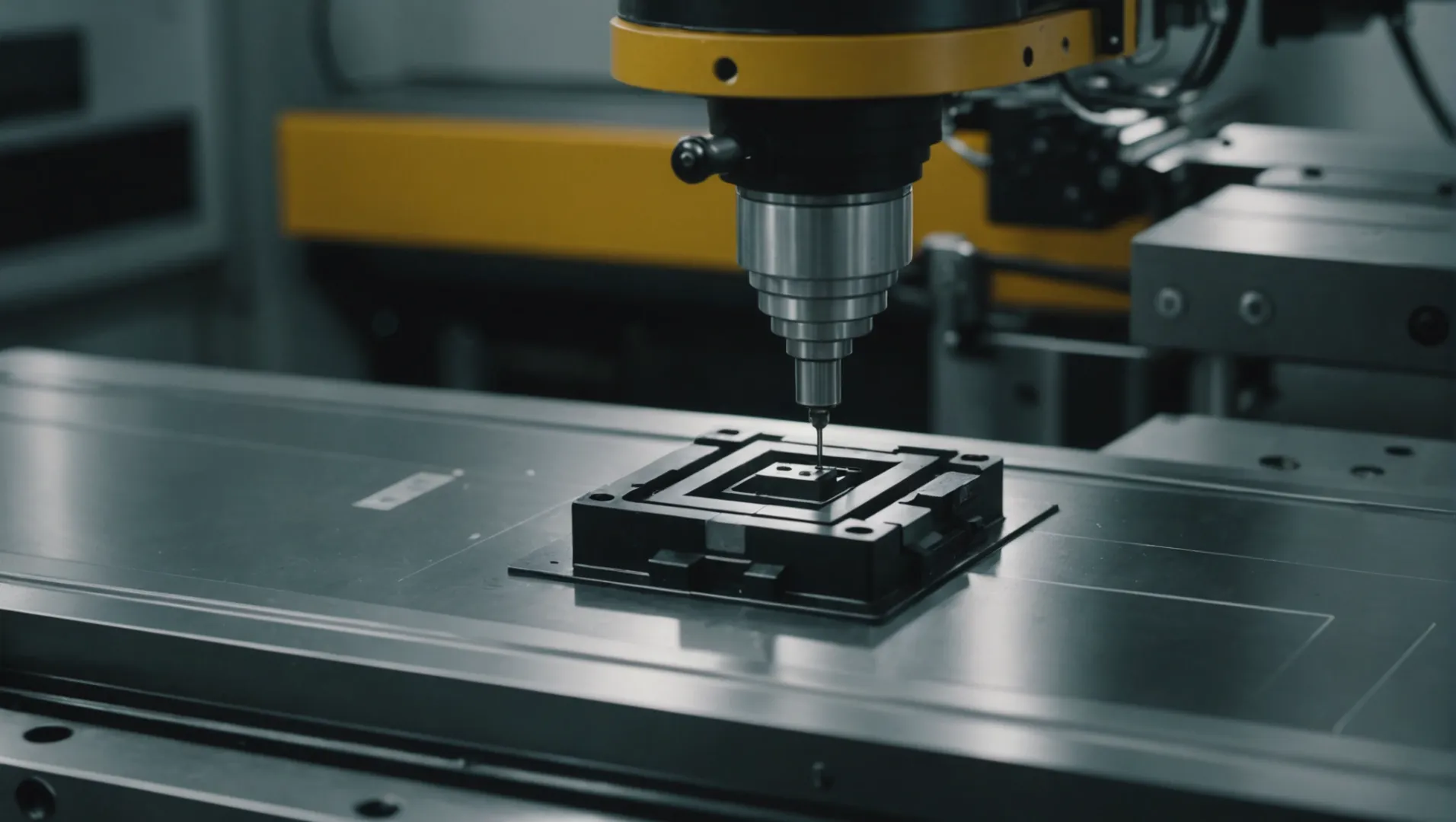
Importance of Mold Quality
Mold quality is the foundation of precision in injection molding. A well-crafted mold ensures that the dimensions and shapes of the parts are as close to the design specifications as possible. It is the blueprint from which all parts are derived, making its accuracy paramount.
- Dimensional Accuracy: High-quality molds can achieve remarkable dimensional precision. For instance, precision injection molding can maintain tolerances within ±0.02mm, essential for applications like electronic equipment housings where precise assembly is critical.
- Shape Accuracy: Molds accurately replicate the intended shape, but complex designs might introduce challenges. With superior mold quality, even intricate shapes can be molded with minimal deviations.
Factors Contributing to Mold Quality
-
Manufacturing Precision
The mold’s manufacturing process must adhere to strict precision standards to ensure it produces consistent parts. Advanced technologies such as CNC machining and EDM (Electrical Discharge Machining) are often employed to achieve the required precision.
-
Material Selection
The choice of materials for mold construction significantly impacts its longevity and performance. High-grade steels and alloys are commonly used to withstand the pressures of repeated use without significant wear.
-
Wear and Tear
Over time, molds can wear down, leading to inaccuracies in the molded parts. Regular maintenance and timely refurbishing are crucial to prolonging mold life and maintaining part accuracy.
Challenges and Solutions
- Complexity of Design: Complex parts may require intricate molds, increasing the risk of inaccuracies. Advanced simulation software can help anticipate and mitigate potential issues before actual production.
- Cost vs. Quality Trade-Off: High-quality molds are more expensive but essential for high-precision parts. Investing in quality up front often reduces long-term costs associated with defective parts and remanufacturing.
In conclusion, understanding how mold quality impacts injection molding1 provides insights into achieving high precision and minimizing errors in production.
High-quality molds ensure ±0.02mm precision.True
Precision injection molding can maintain tolerances within ±0.02mm.
Low-quality molds do not affect shape accuracy.False
Low-quality molds can cause deviations in the shape of molded parts.
How Do Plastic Material Properties Affect Injection Molding Precision?
Understanding the properties of plastic materials is crucial in determining the precision of injection molded parts.
Plastic material properties such as shrinkage rate and fluidity directly affect injection molding precision. High fluidity ensures better mold filling, while low shrinkage rates maintain dimensional accuracy.
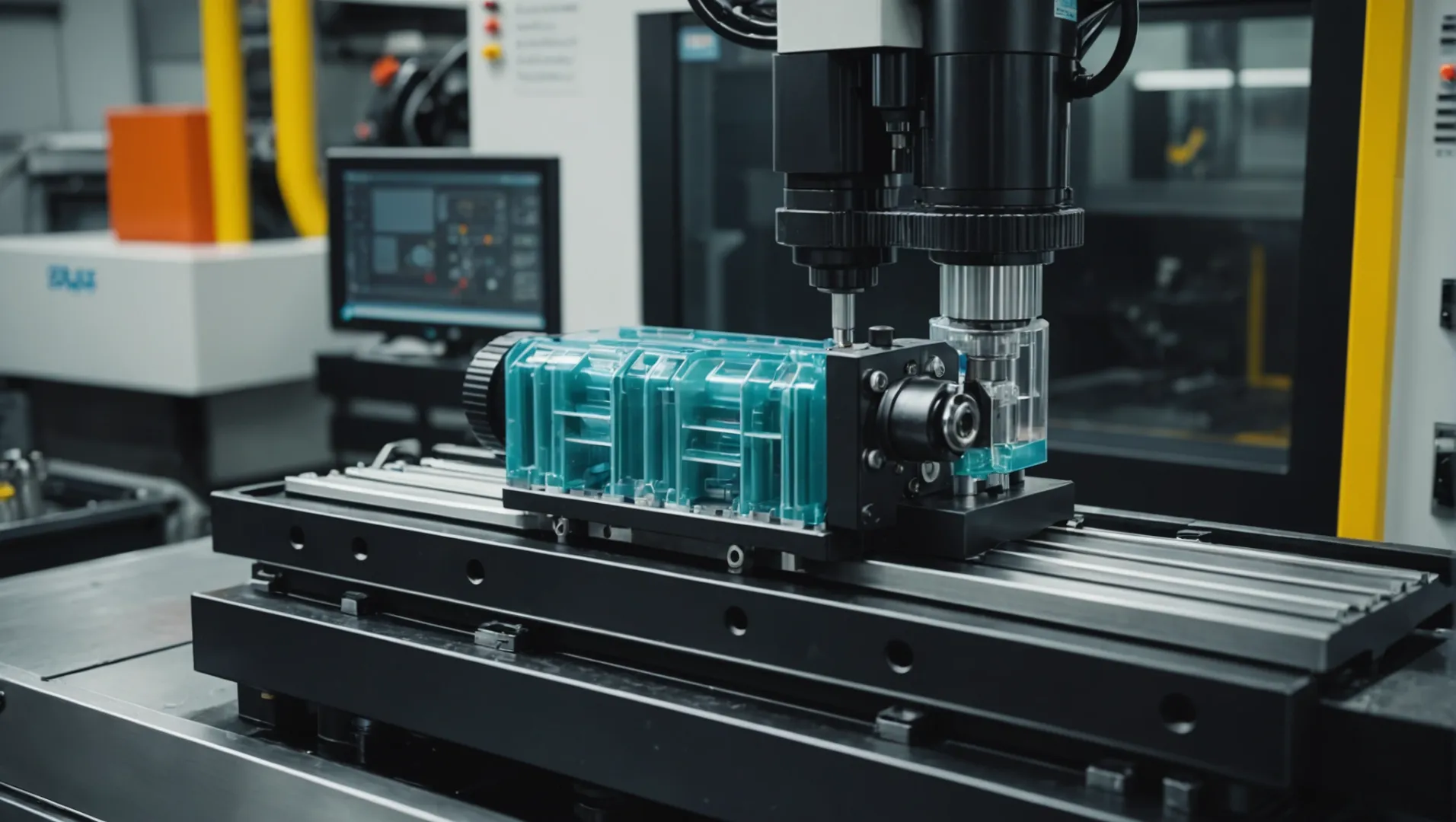
The Role of Shrinkage Rate
Shrinkage rate is a key factor in determining the final dimensions of an injection molded part. During cooling, plastics tend to contract, which can lead to variations from the intended design. Materials with lower shrinkage rates, such as polycarbonate and certain engineering plastics, provide higher precision, minimizing dimensional deviations.
Example: Consider using ABS plastic versus high-density polyethylene (HDPE) for a component requiring tight tolerances. ABS, with its lower shrinkage rate, would maintain better dimensional accuracy compared to HDPE.
Fluidity of Plastic Materials
Fluidity affects how well the plastic can fill intricate mold designs. High fluidity plastics ensure complete mold filling, reducing the likelihood of defects like short shots or voids. This property is especially important for complex geometries where precision is paramount.
Example: Liquid crystal polymers (LCPs) are often chosen for their excellent flow characteristics when manufacturing intricate electronic connectors where precision is critical.
Mechanical Properties and Their Impact
The mechanical properties of a plastic, such as tensile strength and elasticity, also play a role in molding precision. Stiffer plastics may resist deformation during the cooling process, leading to more precise parts. However, these materials may also be more prone to warping if not processed correctly.
Selecting the Right Material for Precision
Choosing the appropriate plastic material requires balancing several properties to meet the desired precision level. Consider the end-use environment, mechanical requirements, and cost constraints.
Property | Influence on Precision | Example Materials |
---|---|---|
Shrinkage Rate | Affects dimensional accuracy | Polycarbonate, ABS |
Fluidity | Determines mold filling capability | LCPs, Polypropylene |
Mechanical Strength | Influences resistance to deformation | Nylon, PEEK |
In summary, understanding how each property affects molding precision allows manufacturers to make informed decisions and optimize their injection molding processes for maximum accuracy. The selection of materials should align with the specific requirements of the end-use application2, ensuring both performance and cost-effectiveness.
High fluidity plastics improve mold filling.True
High fluidity ensures complete mold filling, reducing defects in intricate designs.
ABS plastic has a higher shrinkage rate than HDPE.False
ABS has a lower shrinkage rate than HDPE, providing better dimensional accuracy.
Which Injection Molding Process Parameters Are Crucial for Precision?
Achieving precision in injection molding relies heavily on fine-tuning various process parameters. But which ones are most crucial?
Critical injection molding process parameters include injection pressure, temperature, speed, holding time, and cooling time. These factors ensure that the plastic fully fills the mold, maintaining dimensional accuracy and minimizing defects. Adjusting these parameters appropriately can significantly enhance the precision of the molded parts.
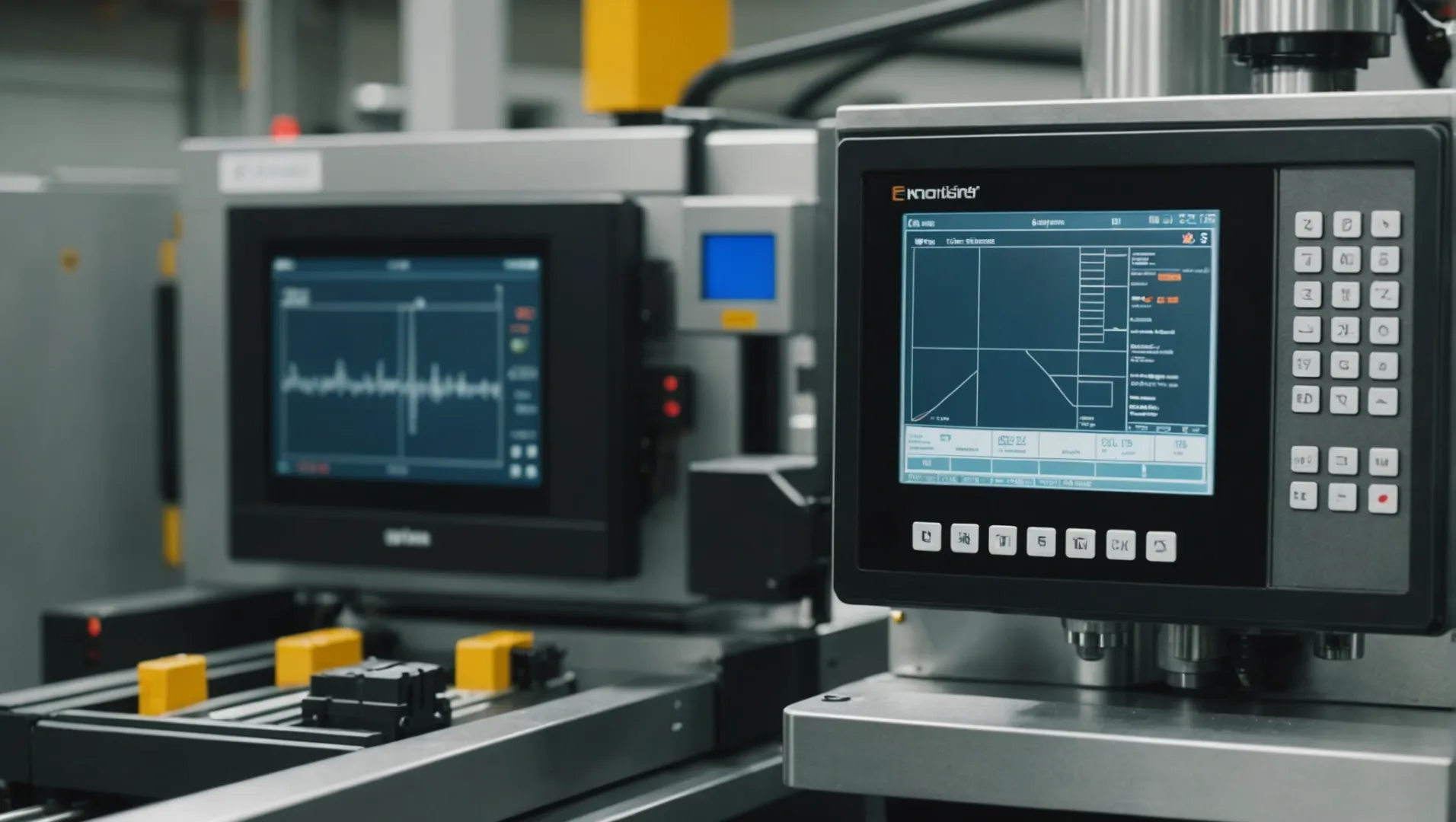
Injection Pressure and Speed
Injection pressure is essential for ensuring the molten plastic reaches all areas of the mold. High pressure can lead to better filling but may also cause flashing if not controlled. For instance, when producing parts with intricate details, maintaining an optimal pressure helps achieve higher accuracy.
Similarly, injection speed determines how fast the mold is filled. A faster injection speed may lead to increased shear rates, affecting the material properties and potentially leading to warpage or other defects. By carefully balancing speed and pressure, manufacturers can improve the precision of their products.
Temperature Control
The temperature of both the plastic melt and the mold surface is a key factor in achieving precision. Consistent melt temperature ensures uniform flow and filling, reducing the risk of flow marks or incomplete fills. On the other hand, a stable mold temperature helps minimize cooling-related issues like shrinkage.
For example, in electronic housing production, precise temperature control is vital to ensure components fit together seamlessly without gaps or misalignments.
Holding and Cooling Time
The holding time ensures that the plastic remains under pressure after initial filling to compensate for material shrinkage. Insufficient holding time may result in sinks or voids within the final product. Conversely, too long a holding time can lead to increased cycle times and reduced productivity.
Cooling time is equally important as it dictates when the part can be safely ejected without deformation. Proper cooling avoids internal stresses that could lead to warpage or cracking.
The Balance of Parameters
Understanding the interplay of these parameters3 is crucial for achieving optimal results. For instance, increasing injection speed might require adjustments in holding time to compensate for potential shrinkage issues.
In summary, precise control and adjustment of injection molding process parameters like pressure, temperature, speed, holding, and cooling time are fundamental to manufacturing parts with high dimensional accuracy.
Injection pressure affects mold filling accuracy.True
Proper injection pressure ensures the mold is fully filled, enhancing accuracy.
Cooling time has no impact on part deformation.False
Cooling time affects when parts can be ejected without deforming.
How Does Equipment Precision Impact the Accuracy of Injection Molding?
Precision equipment plays a pivotal role in achieving the high accuracy required in injection molding processes.
Equipment precision ensures consistent and accurate control over parameters like pressure and speed, directly impacting the accuracy of injection molded parts. Proper maintenance and calibration are crucial for optimal performance.
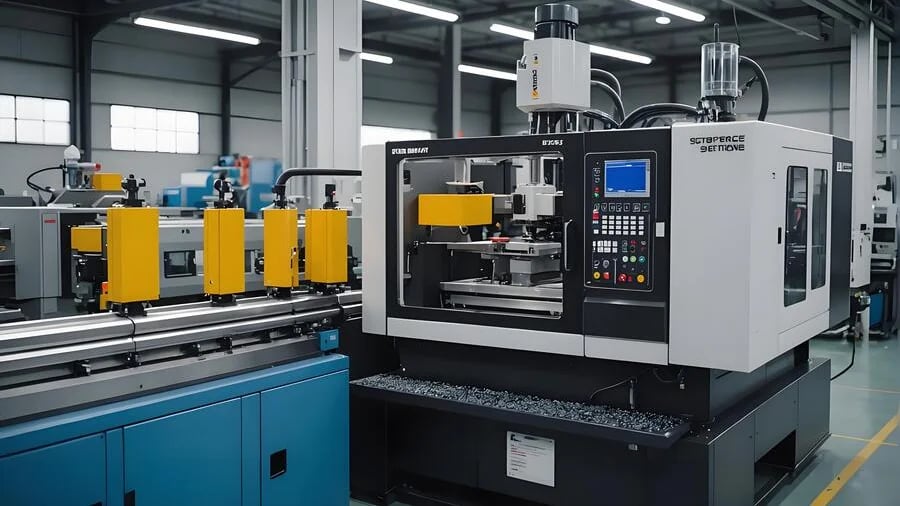
Importance of Injection Molding Machine Precision
Injection molding machines are at the heart of the manufacturing process. Their precision affects how accurately they can control critical parameters such as pressure, temperature, and speed. High-precision machines provide stable performance, allowing manufacturers to maintain tight tolerances, essential for producing precision parts. For instance, a deviation of just a few degrees in temperature can cause significant changes in part dimensions.
Installation Accuracy
Proper installation of the mold within the machine is another critical aspect. Misalignments can lead to issues like eccentricity or deformation in the final product. Even a slight misalignment during mold installation can result in significant dimensional errors. Regular maintenance checks ensure that the installation remains precise, minimizing the risk of defects.
Influence of Equipment Wear and Maintenance
As with any machinery, wear and tear are inevitable. Over time, components like screws and barrels can degrade, impacting precision. Regular maintenance schedules help identify and replace worn parts before they affect production quality. The more consistent the equipment’s performance, the more reliable the output.
Role of Calibration
Calibration is crucial for ensuring that equipment operates within specified parameters. Precision machines require regular calibration to maintain their ability to deliver consistent results. By periodically calibrating equipment, manufacturers can prevent drifts in performance that lead to inaccuracies.
Control Systems and Technology
Modern injection molding machines are equipped with advanced control systems that enhance precision. These systems allow for precise adjustments of process parameters in real-time, reducing variability in product dimensions. Understanding control systems4 used in injection molding can provide insights into how technology aids in achieving high precision.
In summary, equipment precision not only influences the current production cycle but also has long-term effects on the manufacturing process’s reliability and efficiency. By investing in high-quality machines and maintaining them regularly, manufacturers can achieve and sustain high levels of accuracy in their injection molding processes.
High-precision machines maintain tight tolerances.True
Precision machines ensure stable performance, crucial for tight tolerances.
Calibration is unnecessary for precision equipment.False
Regular calibration prevents performance drifts, maintaining precision.
Conclusion
Injection molding can produce parts with incredible precision by optimizing mold quality, material selection, and process parameters.
-
Learn how mold quality impacts precision in injection molding processes.: Injection molding is an efficient manufacturing process for mass-producing parts with complicated geometry, consistent quality, and attractive appearance. ↩
-
Explore factors influencing material choice for specific applications.: Other Miscellaneous Considerations · Will the part have to meet any regulatory requirements? · Is UL94 Flame retardant rating required? · Should the material have … ↩
-
Explore how different parameters influence each other during injection molding.: The rate at which molten plastic is injected into the mold affects the filling pattern, part density, and overall quality. ↩
-
Learn how control systems enhance precision and reduce variability.: In fact, many injection molding process monitoring and control systems can identify trends in inefficiencies in a process and can automatically correct them … ↩