If you have ever thought about why your project’s money is so limited after buying a special mold, you are not alone. We will explore why injection molds require a big expense.
Injection molds are expensive due to high design and material costs, complex manufacturing processes, and precision requirements that ensure product quality and durability. These factors make mold production a substantial investment for businesses.
The first explanation helps understand simple reasons for high mold expenses. Learning more about each factor can give good ideas for keeping costs low. Look closely at what increases these expenses and think about ways to reduce costs.
High material costs drive up injection mold expenses.True
Steel of good quality and special materials such as beryllium copper cost a lot.
What Design Challenges Make Injection Molds Costly?
Creating injection molds involves difficult tasks that add to their high expense. What unique design difficulties do they present?
Injection mold design challenges include high precision requirements, multiple design iterations, and intricate mold structures. These factors necessitate advanced design tools and expert knowledge, driving up costs.
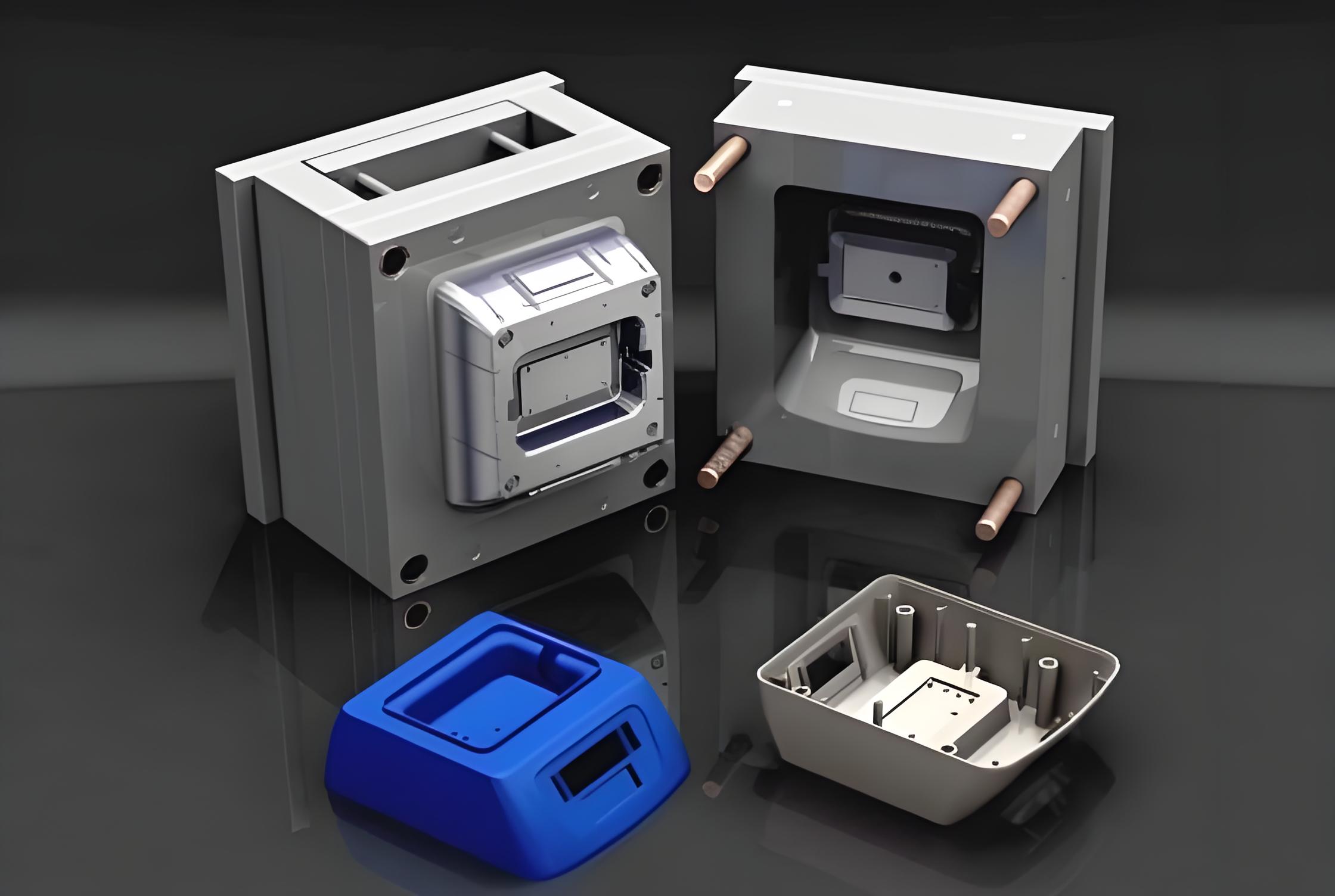
High Precision Requirements
One of the foremost challenges in designing injection molds1 is achieving high precision. For industries like electronics and automotive, where even the smallest deviation can result in significant issues, molds must adhere to tight tolerances. Designers employ advanced CAD software and precision measuring equipment to ensure accuracy, which involves both substantial time and financial investment.
Complex Mold Structures
Injection molds often need to accommodate intricate geometries. Products such as intricate plastic housings or complex connectors require molds with sophisticated runner systems and complex core-cavity designs. These structures demand extensive expertise in both mechanical design and material engineering. As a result, such complexity not only extends the design phase but also inflates costs due to the need for specialized skills.
Multiple Design Iterations
During the design process, it’s common for multiple iterations to be necessary to optimize mold efficiency and output quality. Each iteration involves reassessing and modifying the mold’s design to address potential production issues or improve the final product’s quality. This iterative process requires significant resources, including the designer’s time and use of specialized software tools.
Advanced Design Tools and Expertise
To tackle these challenges effectively, designers need a robust understanding of the injection molding process and familiarity with various plastic materials. They often rely on cutting-edge design software that can simulate mold performance, helping to identify and correct potential issues before physical trials. Moreover, continuous professional development and staying updated with technological advancements are essential, adding to the overall design costs.
The intricate nature of injection mold design2 necessitates collaboration across multiple fields, from engineering to material science, which further compounds expenses. However, understanding these challenges offers opportunities to innovate and explore cost-effective solutions without compromising on quality.
High precision is crucial in injection mold design.True
Exactness is crucial to reach narrow limits, especially in electronics.
Complex mold structures simplify the design process.False
Complex shapes confuse planning, needing expert abilities.
How Does Material Choice Impact Mold Costs?
The selection of materials is crucial for determining mold costs, influencing both production expenses and the quality of the finished product.
Material choice directly impacts mold costs due to factors like material properties, availability, and required treatment. High-quality materials ensure mold durability but often come at a higher price. Balancing material cost with performance is essential for optimizing overall production expenses.
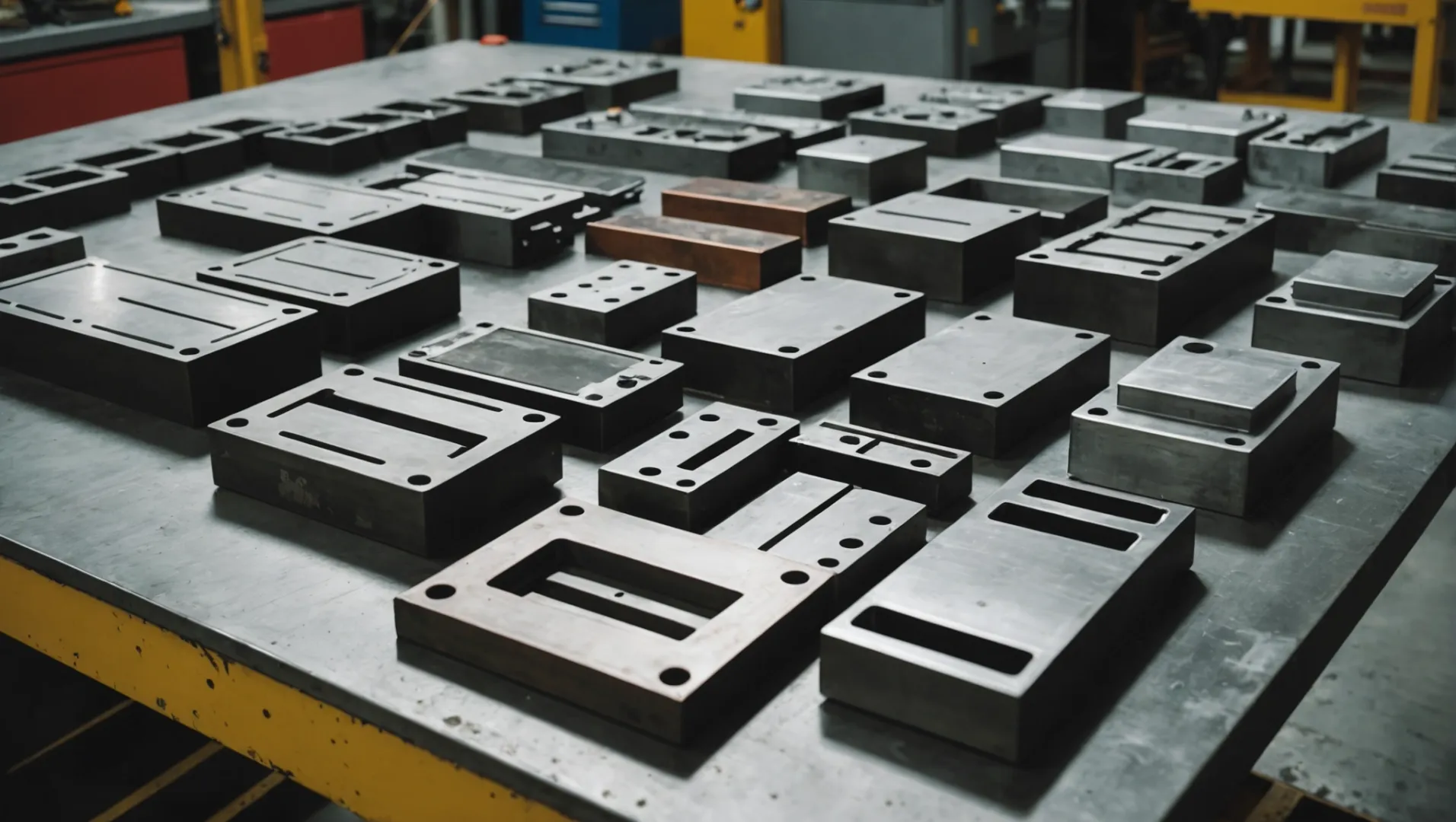
The Role of Material Properties
Material traits like hardness, strength, and wear resistance greatly affect mold expenses. Top-grade steel is frequently utilized for molds that bear intense pressure and high heat during the injection process. Although these materials promise longevity and efficiency, they cost more. Picking materials such as P20 or H13 steel secures durability but raises initial prices.
Availability and Cost of Materials
Mold material availability varies widely based on location and market trends. Unique materials like beryllium copper or stainless steel, often needed for precise uses, may be rare and pricey. Obtaining these materials could involve international supply chains, adding extra logistic expenses.
Heat Treatment and Surface Treatment
Many materials need extra processes such as heat treatment to boost their traits. These procedures upgrade material performance by raising hardness and corrosion resistance, yet also increase production costs. Molds needing fine surface finishes3 might undergo detailed polishing that further heightens expenses.
Balancing Cost with Performance
In the end, selecting mold materials involves balancing cost and efficiency. Companies should consider initial costs against potential for extended mold life and lower upkeep needs. Using budget-friendly approaches4 like choosing substitute materials with similar advantages can help control expenses without losing quality.
Material Type | Characteristics | Impact on Cost |
---|---|---|
P20 Steel | Tough, adaptable, easy to machine | Moderate to High |
H13 Steel | Strong, heat-resistant | High |
Beryllium Copper | Excellent conductivity, wear-resistant | Very High |
Stainless Steel | Rust-resistant, visually appealing | High |
Alternative Alloys | Depends on specific uses | Varies |
Knowing these factors lets manufacturers decide smartly, balancing efficiency needs with budget limits.
High-quality steel molds are always more cost-effective.False
Though strong, top-grade steel molds possess high starting prices, not always economical.
Beryllium copper is a cost-effective mold material.False
Beryllium copper costs a lot because it has great ability to carry electricity and resists damage from use.
What Are the Key Steps in the Mold Manufacturing Process?
The process of building an injection mold includes several careful stages, each important for achieving the final item’s good quality and long life.
The key steps in the mold manufacturing process include design, material selection, machining, assembly, testing, and refinement. Each phase is crucial in crafting a precise and durable mold that meets specific production needs.
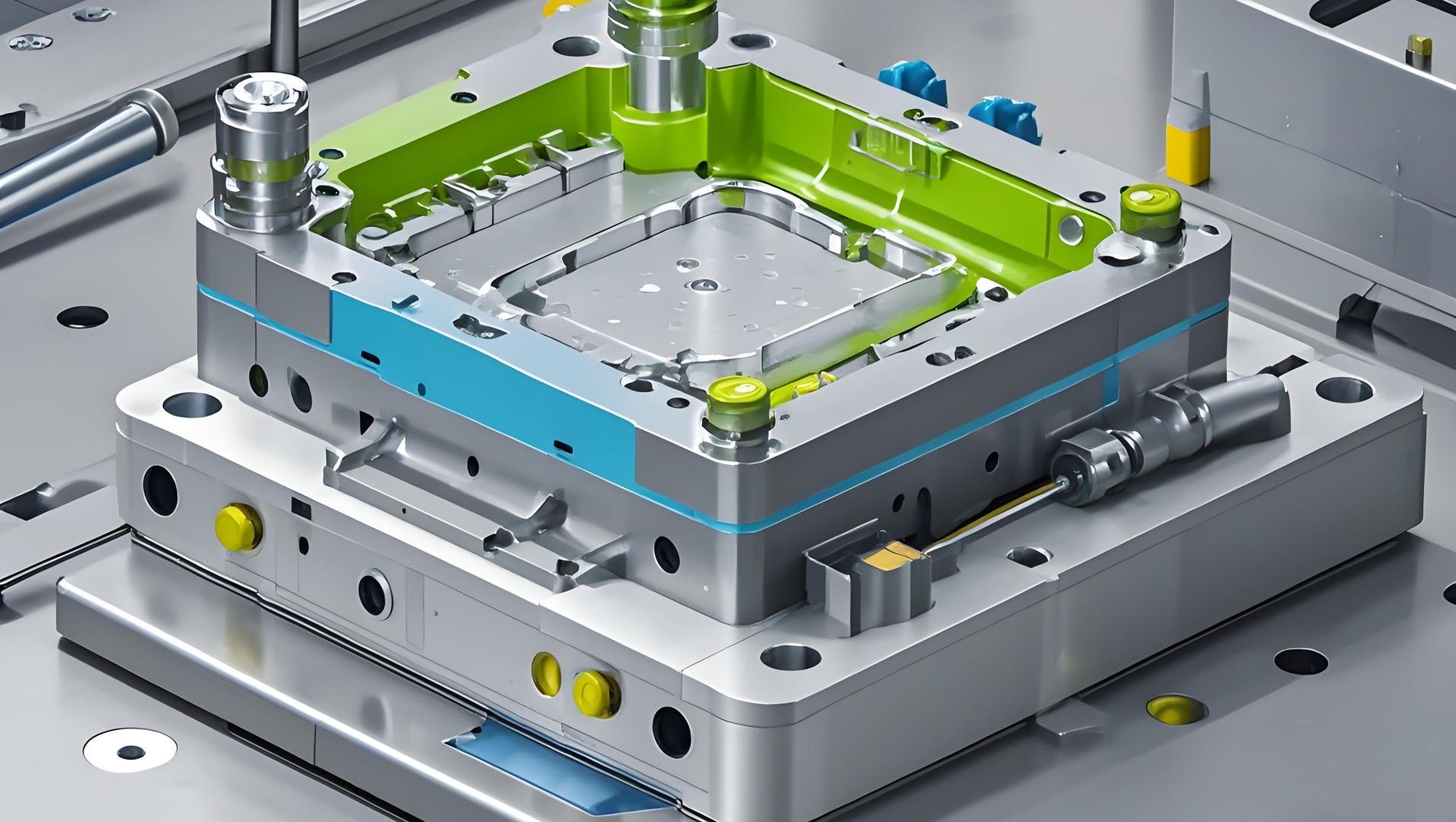
Design and Planning
The first step of creating a mold involves design and planning. Designers develop detailed plans, considering the product’s size, how the material moves, and cooling paths. This stage often takes multiple tries to polish the design and meet all needs.
Material Choice
Picking the right material is important for strength and function. Tough steel like P20 or H13 is often chosen for its hardness and wear resistance. Sometimes, for specific uses like clear parts, different materials such as beryllium copper are needed.
Machining and Building
Finalized designs lead to precise machining. Advanced tools, including CNC machines5 and EDM (Electrical Discharge Machining), shape the mold’s cavities and cores. Precision is key for perfect fittings, which are essential for a mold’s purpose.
Table: Common Machining Processes
Process | Purpose |
---|---|
CNC Machining | Accurately cuts mold pieces |
EDM | Forms complex shapes in tough materials |
Wire Cutting | Adds fine details to detailed mold features |
Assembly
After machining, mold pieces come together. Careful alignment and fitting are crucial for proper mold function during use. Skilled workers assemble the parts, keeping strict measurements.
Testing and Improving
With the mold complete, testing begins. Trial runs with injection molding machines6 create sample pieces. Detected flaws or issues require changes.
Improvement and Completion
In the last step, improve the mold based on test findings. Changes might involve surface polishing or adjusting sizes to enhance function. When fine-tuned, the mold is prepared for mass production.
Each part of this process is important, with skilled workers making sure every detail helps create a mold that produces high-quality plastic items successfully.
Design is the first step in mold manufacturing.True
Design and planning start the mold production process.
CNC machining is used for initial mold assembly.False
CNC machining provides accurate cutting. It does not join parts together.
Can Injection Mold Costs Be Reduced Without Compromising Quality?
High-quality injection molds are very important but expensive. Is it possible to reduce costs without losing quality?
Yes, injection mold costs can be reduced through strategic design optimization, material selection, and efficient manufacturing practices, all while maintaining product quality and performance standards.
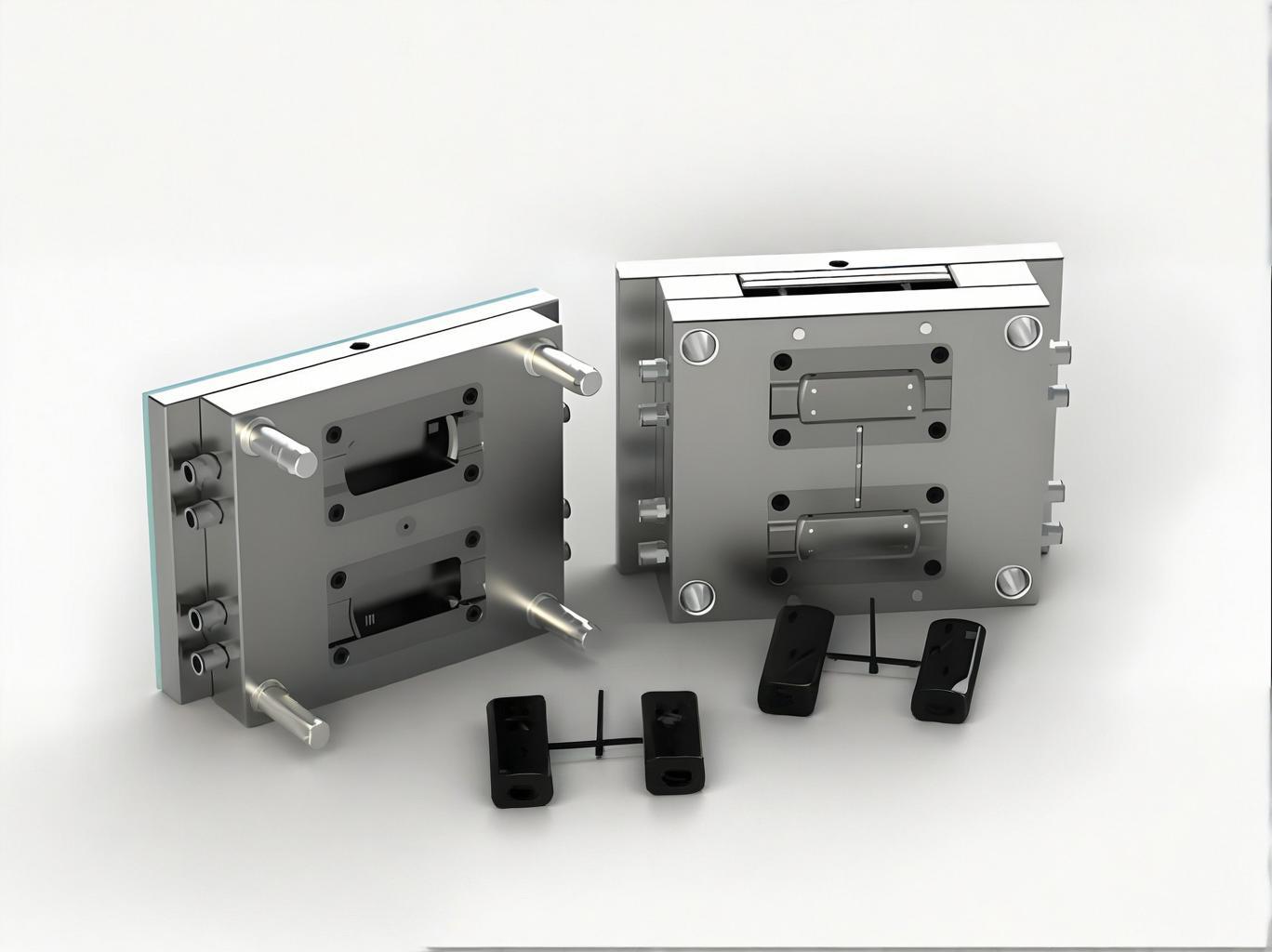
Simplifying Design for Cost Savings
A good method to lower injection mold expenses is design improvement. This uses special software to imagine and tweak the mold design, probably cutting down on the number of tries required. By concentrating on the early design phase, likely mistakes can be spotted quickly, lowering the chance of expensive fixes.
Example: Applying design principles that suit manufacturing7 helps engineers build molds that are simpler and cheaper to create without losing the final product’s quality.
Selecting Budget-Friendly Materials
Choosing materials that find a balance between price and performance is another way. Good steel like P20 or H13 is often needed for strength, but looking for other options for non-crucial mold parts might save cash. Special treatments or coatings could also make the mold last longer without high costs.
Example: Using high-strength aluminum8 for some sections can cut costs while keeping important precision and quality.
Improving Production Steps
Increasing manufacturing efficiency can cut costs a lot. Methods like lean manufacturing, which focuses on cutting waste, can smooth out processes. Buying high-precision machinery might lead to quicker production and lower labor expenses.
Example: Using automation technologies9 in the assembly line can improve reliability and decrease human mistakes, thus cutting waste and rework expenses.
Increasing Communication and Teamwork
As many molds are designed and created in different places, better communication and teamwork are vital. Using digital collaboration tools aligns everyone involved in the project, reducing hold-ups and mix-ups.
Example: Adding a cloud-based project management system10 allows real-time updates and good handling of multi-team tasks.
Performing Detailed Trial Mold Testing
Trial mold testing costs a lot, but it is crucial for quality. However, using simulation software during the design phase allows companies to foresee possible problems before physical tests start, saving both time and resources.
Example: Using virtual testing platforms11 finds errors early, decreasing the number of real-world trials necessary.
Design optimization reduces mold costs without quality loss.True
Refining strategic design reduces mistakes. It lowers expenses and keeps quality.
Using high-strength aluminum compromises mold quality.False
Aluminum helps lower expenses and keep accuracy for parts that are not very important.
Conclusion
Knowing mold expenses helps to choose wisely. Solving design issues, picking the right materials and ensuring accuracy benefits competitiveness and controls costs well.
-
Explore how precision impacts mold design complexity and cost.: Precision injection molding machines require product dimensional accuracy to be generally within 0.01 to 0.001 mm. ↩
-
Discover the advanced tools essential for precise mold design.: Design Phase Computer-Aided Design (CAD) and computer-aided manufacturing (CAM) software are utilized to create 3D models and simulate the injection molding … ↩
-
Learn about techniques to achieve high-quality surface finishes on molds.: Surface finish is a key consideration when manufacturing molds to control quality of molded parts, part release from the mold and lifespan of the mold. ↩
-
Discover approaches to choosing economical mold materials without losing quality.: One alternative may be using sliding shutoffs, pass-through cores or by changing the parting line and draft angles to provide an easier mould build. These … ↩
-
Learn about the role of CNC machines in precision mold fabrication.: CNC machining is the leading production style for mold making. Molds are most commonly machined out of tool steel and stainless steel, but aluminum is also … ↩
-
Understand how trial molds help refine injection mold designs.: A mold trial is the test injection molding step conducted in the product development and manufacturing process after the mold is completed but before mass … ↩
-
Learn how DFM principles optimize mold design for cost savings.: See how designing with moldability in mind can help you avoid manufacturing advisories in quoting, save you development time, and reduce production costs. ↩
-
Discover how aluminum reduces mold costs without quality loss.: Aluminum boasts impressive thermal conductivity, facilitating efficient heat dissipation. This characteristic helps maintain the optimal mold temperature, … ↩
-
Explore how automation cuts costs in mold production.: Automation improves the injection molding process by making it easier to safely and accurately perform operations that ensure part consistency, precision, and … ↩
-
See how cloud solutions enhance coordination in manufacturing.: Streamline projects with WorkOtter’s secure, cloud-based manufacturing project management software. Optimize resources & boost efficiency. ↩
-
Find out how virtual testing minimizes trial costs.: With the best-in-class analysis technology, Moldex3D can help you carry out in-depth simulation of the widest range of injection molding processes and to … ↩