Ever stood at a manufacturing crossroads, pondering which path to take for your next big project?
Injection molding is ideal for high-volume, intricate designs, whereas thermoforming suits simpler, smaller batches. Key differences include tooling costs, production speed, and material adaptability, making each process suitable for different production needs.
Choosing between injection molding and thermoforming can feel like deciding on the best route for a road trip. While both methods will get you to your destination, the journey differs significantly. Injection molding offers the thrill of mass production with complex designs, much like a high-speed train—efficient and precise. On the other hand, thermoforming is more akin to a leisurely drive through scenic routes, ideal for smaller, simpler projects where flexibility is key.
Understanding these methods isn’t just about knowing the basics; it’s about aligning them with your vision and goals. Dive deeper into the nuances of each approach, as these insights can profoundly influence your design and manufacturing strategy. Let’s explore how factors like cost efficiency, material selection, and practical applications play a vital role in determining which process is your perfect match.
Injection molding is suitable for complex shapes.True
Injection molding efficiently creates intricate designs due to precise molds.
Thermoforming is costlier than injection molding for tooling.False
Thermoforming generally has lower tooling costs compared to injection molding.
- 1. How Does Injection Molding Work?
- 2. How Does the Thermoforming Process Work?
- 3. How Can I Enhance Design Flexibility in Product Development?
- 4. How Do Costs Compare Between Injection Molding and Thermoforming?
- 5. What Material Should I Choose for Each Manufacturing Method?
- 6. What Techniques Work Best for Different Applications?
- 7. Conclusion
How Does Injection Molding Work?
Ever wondered how your favorite gadgets come to life? Dive into the world of injection molding, a process that shapes the very essence of modern manufacturing.
Injection molding melts plastic pellets and injects them into molds to produce uniform and intricate parts, ideal for mass production.
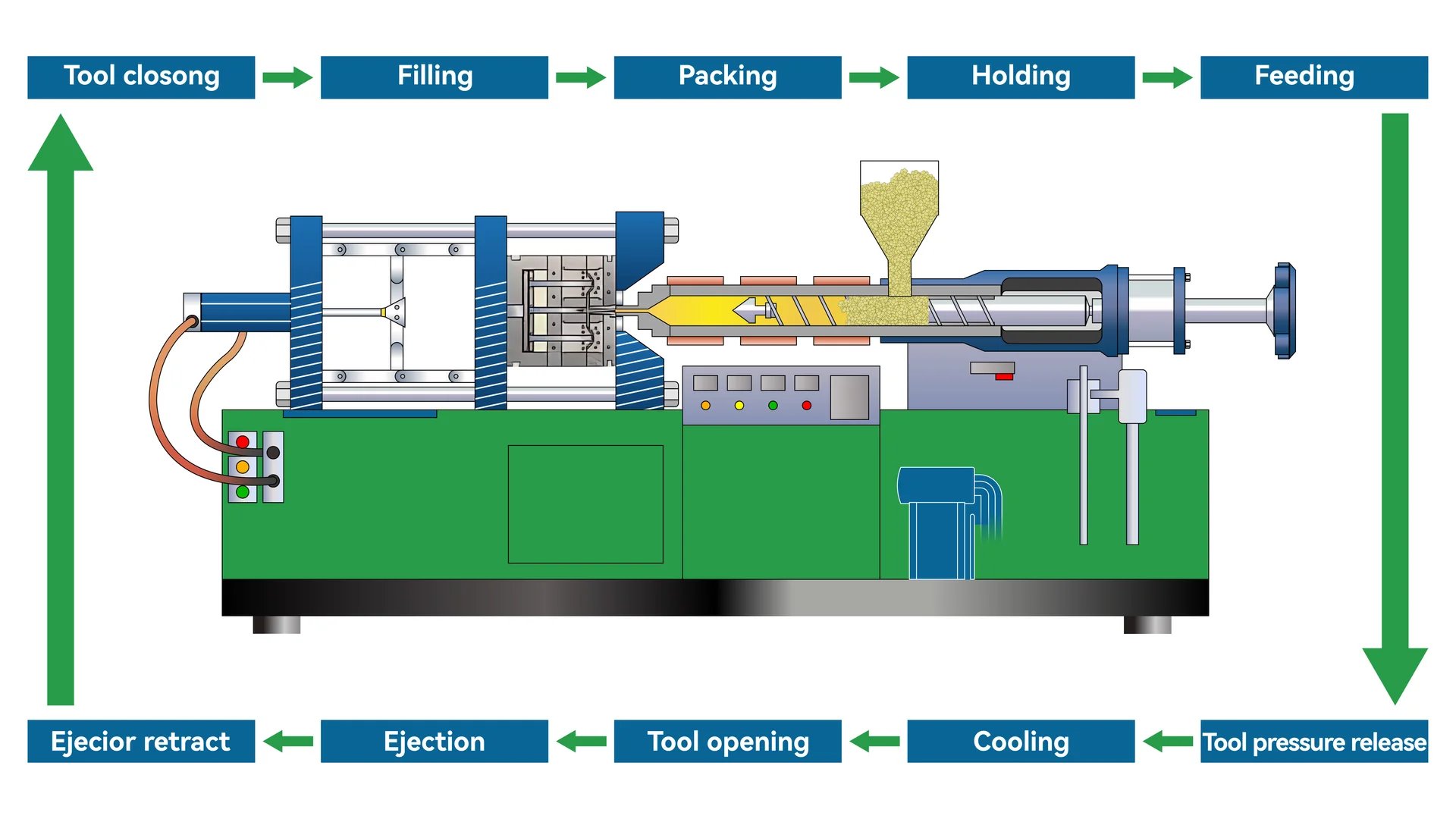
Understanding the Injection Molding Process
Whenever I think about injection molding, I’m reminded of the first time I watched this process unfold in a factory. It felt like witnessing magic—transforming tiny plastic pellets into essential parts for everyday gadgets. Let me walk you through this fascinating process.
-
Material Selection: My journey usually begins with selecting the right material. Just like choosing the perfect ingredients for a recipe, picking the right thermoplastics or elastomers is crucial for ensuring the final product meets all performance and aesthetic needs.
-
Melting: Once I’ve got the materials, it’s time to melt them. Picture feeding plastic pellets into a hopper—like filling a funnel with grains—and watching them flow into a heated barrel. Here, they melt, much like chocolate chips in a warm pan.
-
Injection: The real magic happens when this molten plastic gets injected into a mold cavity. Imagine a powerful force guiding every drop into the most intricate corners of a mold, ensuring even the tiniest details are captured.
-
Cooling: After the mold fills up, cooling begins. This stage reminds me of waiting for cookies to cool down; the part solidifies as it loses heat, readying itself to be revealed.
-
Ejection: Finally comes the moment of truth—the mold opens, and ejector pins gently push the finished part out, like a cake popping out of its tin.
Advantages of Injection Molding
Reflecting on its benefits, I appreciate injection molding for its high efficiency and precision:
- High Efficiency: It’s perfect for producing large quantities without compromising on detail.
- Complex Designs: Allows for intricate and detailed part designs.
- Consistency: Provides uniformity in parts, crucial for quality control.
- Material Flexibility: Suitable for various materials, including recycled plastics that I always try to incorporate.
Challenges in Injection Molding
But it’s not all smooth sailing:
- Initial Costs: The initial costs can be daunting, akin to investing in high-quality kitchenware for serious cooking.
- Design Limitations: Complex designs need careful planning to avoid issues like warping—something that keeps me on my toes during every project.
- Material Waste: Although efficient, some material waste is inevitable during initial trials and setup.
Understanding these nuances helps me fine-tune designs for injection molding1, ensuring they’re both functional and beautiful. Every step requires precision and creativity to truly harness this technique’s potential in manufacturing applications2.
Injection molding uses molten metal for part production.False
Injection molding primarily uses molten plastic, not metal, for parts.
High upfront costs are a challenge in injection molding.True
The initial investment in molds and machinery is expensive.
How Does the Thermoforming Process Work?
Ever looked at your plastic phone case and wondered how it came to be? Enter the fascinating world of thermoforming, a process that shapes the everyday items we often take for granted.
Thermoforming involves heating plastic sheets until pliable, then molding and trimming them into products like packaging, trays, and car parts.
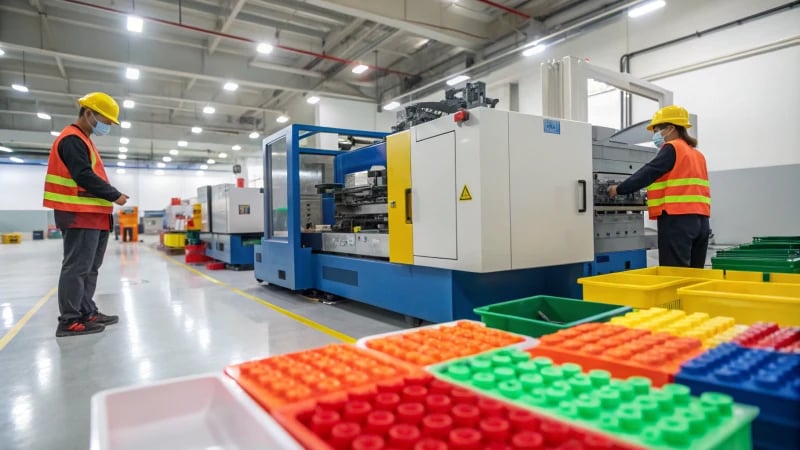
Understanding Thermoforming Basics
When I first learned about thermoforming, I was captivated by how something as ordinary as a plastic sheet could transform into complex shapes with just a bit of heat. Imagine taking a piece of flexible material and, with a bit of engineering magic, turning it into anything from a simple food tray to intricate automotive panels. The process is divided mainly into vacuum forming3, which uses vacuum pressure to mold the plastic, and pressure forming, which adds air pressure for those extra details.
- Vacuum Forming: I remember my first vacuum forming project; it felt like watching a magician pull a rabbit out of a hat as the plastic sheet morphed over the mold.
- Pressure Forming: This adds finesse with air pressure, perfect for when you need those fine details.
Steps in the Thermoforming Process
Here’s a simple breakdown of how it all works:
Step | Description |
---|---|
Heating | The plastic sheet is warmed up to become as pliable as a piece of clay. |
Forming | It’s then draped over a mold, which feels like pressing cookie dough into shape—only hotter. |
Cooling | The newly shaped plastic cools down to hold its form. |
Trimming | Finally, any excess is cut away, leaving a polished product. |
Applications of Thermoforming
In my career, I’ve seen thermoforming used in some pretty cool ways:
- Packaging: Those clear plastic containers and clamshells we see everywhere? Yep, they’re born from this process.
- Automotive: From durable dashboards to sleek interior panels, thermoforming helps design those robust components.
Types of Materials Used
Materials like Polyethylene terephthalate4 (PET), High-impact polystyrene (HIPS), and Polyvinyl chloride (PVC) are my go-tos because they strike that sweet spot between strength and flexibility. These materials ensure durability and clarity across various products.
For more on picking the right material for your next project, check out material selection for thermoforming5.
Thermoforming uses a plastic sheet heated to flexibility.True
Thermoforming involves heating plastic sheets until they become pliable.
Pressure forming uses only vacuum pressure for shaping.False
Pressure forming involves additional air pressure beyond vacuum pressure.
How Can I Enhance Design Flexibility in Product Development?
Ever found yourself tangled up in the design process, wondering if there’s a better way to adapt to those pesky last-minute changes?
Enhance design flexibility in product development by adopting agile methodologies like Scrum, enabling rapid adaptation and iteration compared to traditional Waterfall approaches.
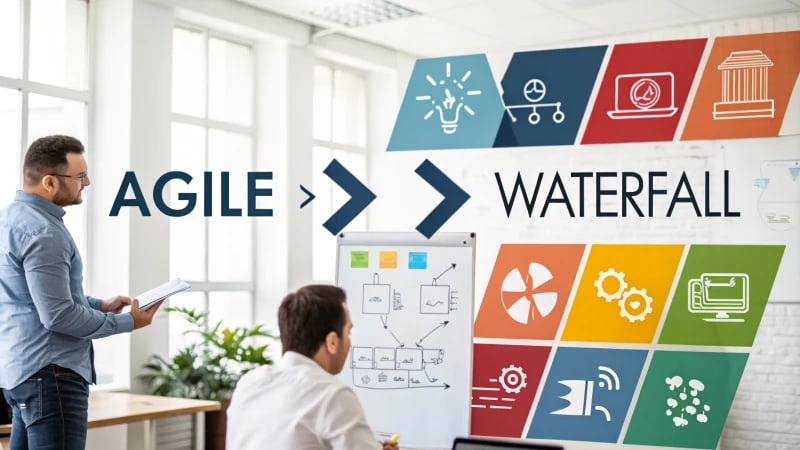
Understanding Design Flexibility
Picture this: you’re knee-deep in a project, and suddenly, a new market trend emerges or a client requests a last-minute change. That’s where design flexibility becomes a lifesaver. It’s the ability to pivot or tweak designs without breaking the bank or the timeline. This adaptability is crucial for keeping up with ever-shifting market demands6 and satisfying client needs.
Agile vs. Waterfall
I remember the first time I faced a major design overhaul late in the project. It felt like trying to steer a massive ship with a tiny paddle. That’s why understanding different methodologies can be such a game-changer.
Feature | Agile | Waterfall |
---|---|---|
Flexibility | High, with iterative cycles | Low, with a linear approach |
Feedback Loops | Regular stakeholder feedback | Limited to end-of-phase reviews |
Change Management | Adaptable at any stage | Difficult after initial phases |
Agile methodologies like Scrum and Kanban are like having a Swiss Army knife; they allow for frequent adjustments and close collaboration with stakeholders, fostering continuous improvement7. Waterfall is more like a freight train—once it’s on its track, changing direction can be quite the ordeal.
Prototyping for Flexibility
In my experience, prototyping is like having a sneak peek into the future. Whether using rapid prototyping or 3D printing, getting immediate feedback helps you spot potential issues before they balloon into costly problems. A dynamic prototype8 can be a real eye-opener, highlighting design flaws well before you hit full-scale production.
Impact of Technological Advancements
The rise of AI and machine learning is like adding rocket fuel to our design processes. These technologies offer predictive insights and automation, helping identify potential issues before they arise and suggesting solutions. This kind of foresight transforms the design environment into something incredibly nimble and responsive.
Industry-Specific Considerations
Working in consumer electronics has taught me that an agile mindset is crucial. The pace at which technology evolves and consumer preferences shift is relentless. By embracing agile methods, we can keep our designs not only relevant but also ahead of the curve.
Through understanding these methodologies and leveraging new technologies, designers like us can ensure our processes remain flexible enough to meet both aesthetic and functional demands efficiently. It’s all about staying adaptable in this ever-evolving landscape.
Agile methodologies offer higher design flexibility than Waterfall.True
Agile's iterative cycles and adaptability allow for continuous design adjustments.
Waterfall is more adaptable to changes than Agile methodologies.False
Waterfall's linear approach limits changes after initial phases, reducing flexibility.
How Do Costs Compare Between Injection Molding and Thermoforming?
Choosing between injection molding and thermoforming for your project can feel like standing at a crossroads. Each path offers distinct cost implications that could make or break your budget.
Injection molding has higher initial tooling costs but lower per-unit costs for large volumes. Thermoforming features lower setup costs but higher per-unit expenses due to production constraints.
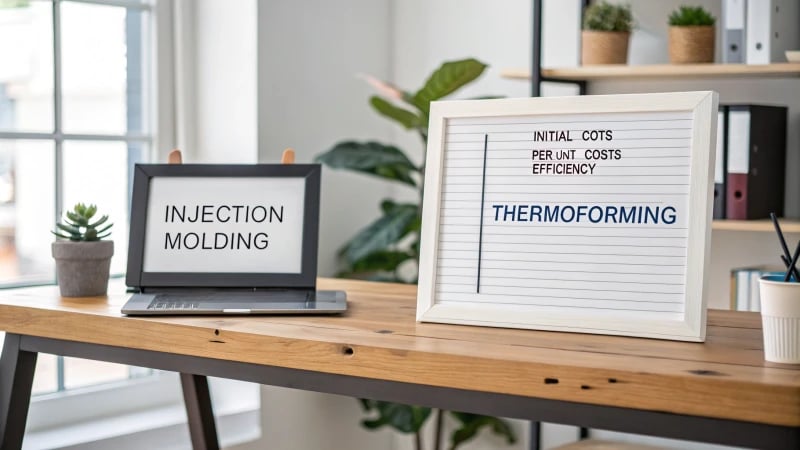
Initial Tooling Costs
I still remember the first time I had to decide between injection molding9 and thermoforming for a project at work. The decision wasn’t easy, especially when considering the initial tooling costs. Injection molding demands a significant investment upfront—those detailed molds, often made from durable materials to withstand high pressure, can be quite pricey. I’ve seen quotes reach tens of thousands of dollars, which can be daunting. On the flip side, thermoforming uses less expensive materials like aluminum or even wood for tooling, which was a real relief to my budget back then.
Production Volume and Cost Efficiency
I learned early in my career that production volume can flip the cost equation. Injection molding shines when you’re dealing with high-volume production because the hefty tooling cost gets diluted over a larger number of units, making each piece cheaper. I’ve always likened it to buying in bulk at a warehouse club—more upfront but savings down the road. Thermoforming, however, is my go-to for low to medium volume projects. It’s like ordering just the right amount from your favorite local shop, perfect for smaller batches without breaking the bank.
Process | Low Volume Costs | High Volume Costs |
---|---|---|
Injection Molding | High | Low |
Thermoforming | Moderate | Moderate to High |
Design Complexity and Material Waste
In my experience, injection molding is akin to having an artist’s entire palette at your disposal. You can create intricate designs and complex shapes thanks to its versatility with materials. However, it’s not all rosy—there’s often more material waste10, which I always try to minimize given its impact on both cost and the environment. Thermoforming may not offer as much design complexity, but it’s like a minimalist approach to art—simple and elegant, with less material wastage.
Speed and Flexibility
If you’re in a rush, thermoforming can feel like ordering fast food—it’s quick to set up and great for rapid prototyping or short production cycles. On the other hand, injection molding is more like preparing a gourmet meal—it takes longer to get everything just right, but once you do, it delivers efficiently for large-scale production.
For designers like me, weighing these factors is crucial in choosing the most cost-effective method for any project. Whether it’s the precision offered by injection molding or the adaptability of thermoforming, understanding each process’s nuances helps optimize both design and cost-effectiveness. I’ve found that by carefully evaluating these aspects, I can better align my projects with their specific needs and constraints.
Injection molding has lower per-unit costs for large volumes.True
The initial tooling cost is spread across many units, reducing per-unit cost.
Thermoforming is ideal for high-volume production.False
Thermoforming suits low to medium volumes due to higher per-unit costs.
What Material Should I Choose for Each Manufacturing Method?
Ever found yourself staring at a list of materials, wondering which one is the magic ingredient for your project?
Select materials based on manufacturing methods: use thermoplastics like ABS for injection molding and metals like aluminum and steel for CNC machining to ensure efficiency and quality.
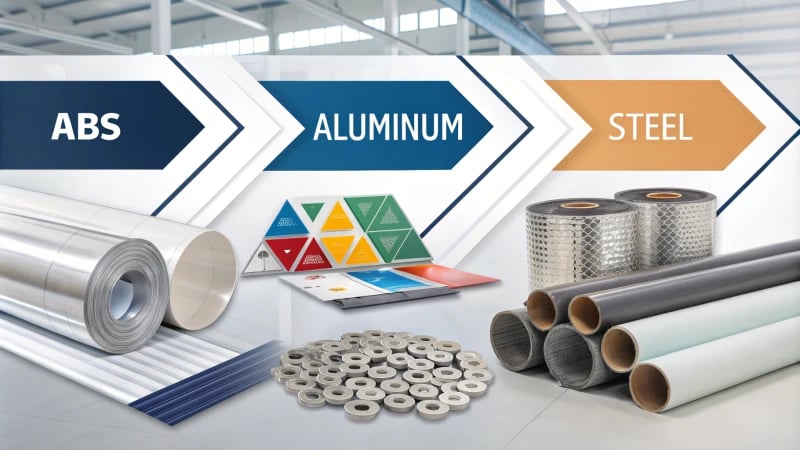
Injection Molding Materials
I’ve always been fascinated by how injection molding can crank out thousands of identical parts with such precision. When I first started, choosing the right material felt like finding a needle in a haystack. For injection molding, the material needs to withstand both high pressure and temperature. Common materials include:
- Thermoplastics: Acrylonitrile Butadiene Styrene (ABS) and Polycarbonate were my go-tos because they were not only durable but also molded beautifully.
- Thermosets: Sometimes I ventured into using thermosets when I needed parts to resist heat better, though they were a bit trickier to work with. Learn more about thermoset properties11
Choosing the right thermoplastic12 was all about balancing strength, flexibility, and cost. I remember a project where I spent days just testing different materials to see which one would hold up best under stress.
CNC Machining Materials
CNC machining was where I could let my inner perfectionist shine. Metals like aluminum and steel were staples in my workshop, chosen for their strength and the way they could be precisely shaped to meet tight tolerances. I still recall the first time I worked with titanium; its strength blew me away, but so did the cost! On the other hand, plastics like Delrin and Nylon were saviors when low friction was a must.
Selecting materials for CNC machining meant considering the end application—whether it required corrosion resistance13 or particular thermal properties.
3D Printing Materials
3D printing felt like playing with a futuristic toy. The sheer range of materials was liberating yet daunting. Polymers like PLA and PETG were my starting point for prototypes—easy to handle and forgiving if mistakes were made. When I needed something more durable, metals like stainless steel or titanium stepped in, offering strength without the bulk.
Composites caught my attention when I needed to enhance specific properties like strength-to-weight ratio. Picking the right material often meant diving into understanding the printing technology used14, as not all printers played well with all materials.
Method | Material Options | Key Considerations |
---|---|---|
Injection Molding | Thermoplastics, Thermosets | Durability, cost |
CNC Machining | Metals, Plastics | Precision, application |
3D Printing | Polymers, Metals, Composites | Flexibility, technology |
These insights can be a real game-changer for designers like us when we’re knee-deep in material selection decisions. By focusing on factors such as strength, flexibility, and thermal resistance, we can craft products that don’t just look good but perform superbly too.
Understanding these material options has definitely empowered me to push the boundaries of product quality while keeping an eye on production efficiency. Whenever I’m stumped or need that extra bit of expertise, diving into more detailed resources or consulting with material experts has been invaluable.
Material Property Considerations
Getting to grips with mechanical properties was something I had to learn early on. Elements like tensile strength, flexibility, and thermal conductivity weren’t just buzzwords; they directly impacted my designs and manufacturing efficiency15. Analyzing these properties helped me ensure compatibility with my chosen production methods and achieve the desired product features.
Reflecting on these experiences reminds me how crucial it is to stay informed and adaptable in this ever-evolving field.
ABS is a common thermoplastic for injection molding.True
ABS is durable and easy to mold, ideal for injection molding.
CNC machining cannot use plastics like Delrin.False
CNC machining can use plastics such as Delrin for low friction applications.
What Techniques Work Best for Different Applications?
Finding the perfect technique for your project can feel like choosing the right tool in a designer’s toolkit—essential for success.
Choose Agile for dynamic, evolving projects and Waterfall for stable, linear ones. Tailor your approach based on goals, team dynamics, and desired outcomes.
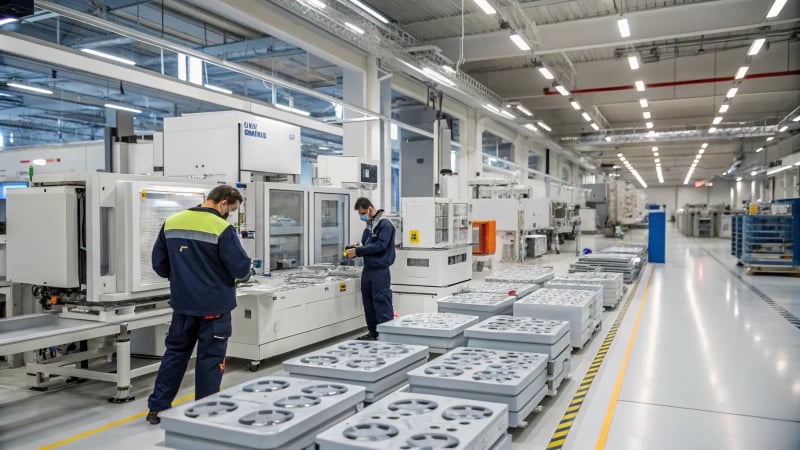
Agile for Dynamic Projects
When I first dove into the world of Agile, it felt like trading my ruler for a sketchpad—suddenly, everything was about flexibility and rapid iteration. Agile methodologies are designed for projects that thrive on change and continuous feedback. I remember working on a software development project where user needs were shifting faster than the autumn leaves. Agile became our best friend, allowing us to adapt swiftly and keep the project aligned with user expectations.
Example: Software Development
In the realm of software development, Agile empowers teams to adapt quickly16 to changes. This approach is perfect when requirements are expected to evolve, ensuring the end product grows alongside user needs.
Technique | Best Suited Application | Key Benefits |
---|---|---|
Agile | Software Development | Flexibility, User-focused |
Waterfall | Construction Projects | Structure, Predictability |
Waterfall for Structured Tasks
Remember those days when every step was planned out like a carefully drafted blueprint? That’s where Waterfall shines—projects with clearly defined stages and stable goals. I once worked on a construction project where precision was key; every phase needed completion before the next could begin, minimizing risks associated with unexpected changes.
Example: Construction Projects
Construction projects benefit immensely from Waterfall due to their linear nature. With predefined stages, Waterfall ensures17 each phase is meticulously completed before progressing, safeguarding against overlap or sudden shifts.
Machine Learning Techniques
Venturing into machine learning is like stepping into a futuristic workshop. Each technique caters to unique needs—supervised learning fits predictive analytics perfectly, while unsupervised learning excels in clustering tasks. Picture a finance team forecasting future trends using regression models; that’s supervised learning in action.
Example: Predictive Analytics
Supervised learning techniques like regression models are ideal for predicting outcomes based on historical data. This is especially critical in sectors like finance where anticipating future trends is crucial.
For a deeper dive into aligning techniques with your project’s unique demands, explore detailed case studies and industry insights. Learn more18 about matching applications with specific methodologies.
Agile is best for projects with evolving requirements.True
Agile's flexibility allows teams to adapt to changing needs efficiently.
Waterfall is ideal for projects with undefined stages.False
Waterfall requires clearly defined stages and stable requirements.
Conclusion
Injection molding and thermoforming differ in production volume, cost efficiency, design complexity, and material adaptability, making each method suitable for specific manufacturing needs.
-
Learn how to optimize design processes specifically for injection molding to ensure quality and efficiency. ↩
-
Discover various manufacturing applications of injection molding to see its versatility in production. ↩
-
Discover the advantages of vacuum forming and how it enhances production efficiency. ↩
-
Learn why PET is favored in thermoforming due to its excellent durability and clarity. ↩
-
Find expert advice on selecting the best materials for different thermoforming applications. ↩
-
Understanding how market trends affect design flexibility helps align products with consumer needs effectively. ↩
-
Learning about continuous improvement aids in enhancing design processes through iterative refinements. ↩
-
Exploring dynamic prototyping reveals how early testing and feedback improve design outcomes. ↩
-
Discover detailed insights into how initial tooling costs impact injection molding expenses. ↩
-
Explore how material waste differs between injection molding and thermoforming processes. ↩
-
Explores detailed properties of thermoset materials suitable for high-temperature applications. ↩
-
Guides on selecting optimal thermoplastics based on application needs. ↩
-
Provides insights into materials that offer corrosion resistance in CNC applications. ↩
-
Discusses the relationship between 3D printer types and compatible materials. ↩
-
Highlights how material choice can enhance manufacturing processes. ↩
-
Discover how Agile methodologies enhance software development through flexibility and user-centric approaches. ↩
-
Understand why the Waterfall model works well in structured environments like construction projects. ↩
-
Gain insights into which machine learning techniques suit specific applications. ↩