Do you feel stressed trying to pick between injection molding and other ways of manufacturing? I really understand – this choice probably changes everything!
Injection molding offers high precision, scalability, and cost efficiency for mass production, unlike CNC machining, 3D printing, or blow molding, which excel in customization, prototyping, or simpler designs.
Let’s explore the world of manufacturing processes. I have experienced standing at the crossroads, considering the advantages and disadvantages of each method. It’s not only about selecting a process. It’s about knowing how it suits your project’s needs. Injection molding is famous for its precision and versatility. However, it has high costs that may leave you thinking. In contrast, extrusion molding offers simplicity and lower costs. Let’s clarify these details to brighten your path.
Injection molding is more precise than CNC machining.True
Injection molding offers higher precision in creating complex shapes compared to CNC machining, which can have limitations based on the material and tooling used.
Extrusion molding is cheaper than injection molding.True
Extrusion molding generally has lower setup costs and material waste, making it a more cost-effective option for certain products compared to injection molding.
- 1. What Makes Injection Molding Stand Out Compared to Other Processes?
- 2. How Does Material Utilization Differ Between Injection Molding and Extrusion?
- 3. How Does Production Efficiency Influence Costs in Injection Molding?
- 4. What Are the Labor Requirements for Injection Molding Compared to Other Methods?
- 5. How Do Equipment and Mold Costs Compare Across Manufacturing Techniques?
- 6. When Should You Choose Injection Molding for Production?
- 7. Conclusion
What Makes Injection Molding Stand Out Compared to Other Processes?
Have you ever wondered why people often praise injection molding as the best manufacturing method? Many industries consider it a top choice. Let’s explore the advantages together.
Injection molding is famous for its efficiency, precision and versatility in materials. It is an economical choice for large-scale production. This method allows for complex designs with very little waste. Operational costs decrease as a result. High-quality outcomes do not need to be expensive.
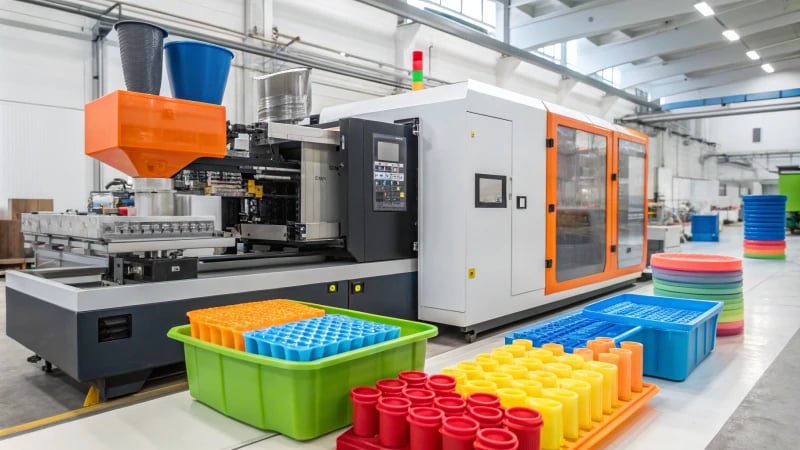
Injection Molding Overview
Injection molding is an interesting process. I have learned to appreciate it over the years. It transforms raw materials into detailed designs that meet both practical and visual needs. This method is very efficient and precise, always surprising me. Let’s look at what makes injection molding different from other manufacturing techniques.
Efficiency and Speed
Injection molding is known for its remarkable efficiency in producing large quantities of identical parts. Unlike processes such as extrusion molding, which often require lengthy setup times, injection molding enables rapid cycle times once the mold is prepared. For instance, a cycle may take only 15 to 60 seconds, depending on the complexity of the part. This rapid production rate translates to:
- High output: Suitable for large-scale production.
- Reduced lead times: Quick turnaround on new designs.
Moreover, the overall production efficiency1 can be enhanced through automation, further reducing labor costs and time.
Precision and Complexity
One of the standout features of injection molding is its ability to produce highly complex parts with tight tolerances. The precision achieved in this method is significantly greater than in many other processes, such as 3D printing or machining. The capability to create intricate designs is beneficial in industries like consumer electronics, where aesthetic appeal and functionality are crucial.
Process | Precision Level | Complexity |
---|---|---|
Injection Molding | High | Very High |
Extrusion Molding | Moderate | Low |
3D Printing | Variable | Variable |
Such precision allows designers like Jacky to meet both functional and aesthetic requirements seamlessly.
Material Versatility
Injection molding supports a wide range of thermoplastic materials. This versatility is particularly advantageous when considering material properties such as strength, flexibility, and temperature resistance. Moreover, additives can be incorporated during the injection process, enabling:
- Custom material properties: Tailored to specific application needs.
- Enhanced performance characteristics: Such as improved durability.
This adaptability contrasts with other processes that may have limitations in material types or performance outcomes. For more on material selection for injection molding2, click here.
Cost Considerations
While the initial investment in injection molding equipment and molds can be high, it is important to consider long-term cost savings. The ability to produce large volumes with minimal waste contributes to a lower cost per unit over time. For example:
- High initial cost: Due to complex machinery and mold fabrication.
- Lower operational costs: Achieved through efficiency and reduced waste.
Cost Factor | Injection Molding | Other Processes |
---|---|---|
Equipment Cost | High | Low |
Material Waste | Moderate | Low |
Labor Cost | Moderate | Low |
Labor Efficiency
Injection molding often requires fewer operators compared to other manufacturing methods due to its automation capabilities. This automation can significantly reduce labor costs and increase production efficiency. For instance:
- Extrusion molding may need 1-2 operators.
- Injection molding can operate with 1 operator monitoring multiple machines.
This reduction in labor need contributes to overall savings and efficiency in production operations. To explore more about automation in injection molding3, check this link.
Injection molding produces parts faster than extrusion molding.True
Injection molding can achieve cycle times of 15 to 60 seconds, making it faster than extrusion molding, which has longer setup times.
Injection molding is less precise than 3D printing.False
Injection molding offers higher precision and complexity compared to 3D printing, making it superior for intricate designs.
How Does Material Utilization Differ Between Injection Molding and Extrusion?
Do you ever think about how injection molding and extrusion compare in using materials? Let us explore the differences. These differences might affect how efficiently you produce things. Costs could be different too.
Material utilization varies a lot between injection molding and extrusion. Extrusion usually provides higher material efficiency. It produces less waste. Injection molding generates more waste. Its intermittent nature and complex mold designs contribute to this.
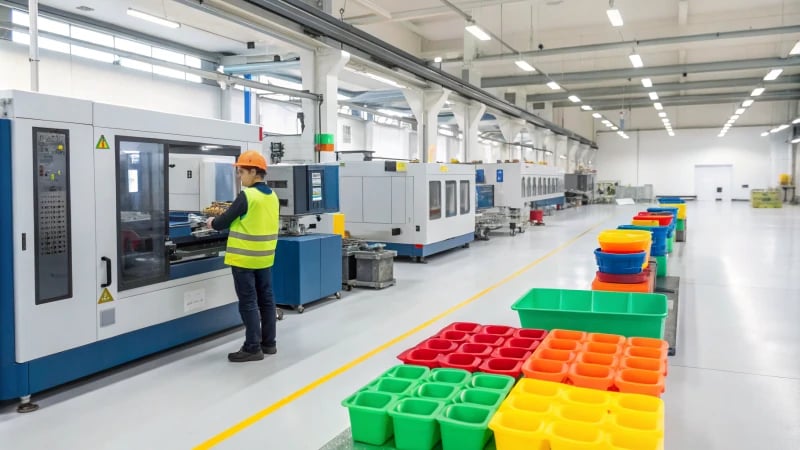
Understanding Material Utilization in Extrusion Molding
Extrusion molding is a continuous production process that typically utilizes thermoplastic materials. The material utilization rate in this method is notably high, particularly when producing long strip products like pipes and profiles.
For instance, in a plastic pipe extrusion process, most waste occurs during the equipment’s initial debugging and at the end of production. During normal operations, the waste generated is minimal, demonstrating a strong efficiency in material use.
This efficiency can be attributed to the relatively simple design of extrusion molds, which allows for quick production cycles and reduces the complexity associated with waste management. Explore more about efficiency in extrusion4.
Feature | Detail |
---|---|
Production Type | Continuous |
Typical Materials | Thermoplastics |
Waste Generation | Low (mainly at start/end) |
Example Product | Plastic pipes |
Material Utilization in Injection Molding
Conversely, injection molding involves an intermittent production process. Although it also primarily uses thermoplastic materials, this method requires precise control over the amount of material injected per cycle.
One notable drawback is the generation of waste in the form of gates and runners—components necessary for ensuring product quality but which contribute significantly to overall material costs. For example, when creating plastic shells, gate and runner materials can account for approximately 10% to 30% of the total material used. This necessitates recycling efforts, which can further escalate costs.
Feature | Detail |
---|---|
Production Type | Intermittent |
Typical Materials | Thermoplastics |
Waste Generation | Higher (gates/runners) |
Example Product | Plastic shells |
Comparative Analysis of Material Utilization
When comparing the two methods, several factors come into play that influence material efficiency:
- Production Efficiency: Extrusion has a continuous flow which minimizes waste, whereas injection molding’s cycle-based approach can lead to higher waste.
- Material Waste: The design of molds impacts waste levels; simpler designs in extrusion result in lower waste compared to the complex molds used in injection molding.
- Recycling Costs: The need for recycling excess materials in injection molding adds to operational costs, making effective management crucial.
By understanding these differences, manufacturers can make informed decisions regarding which process is more suitable for their specific projects, balancing factors such as cost and material efficiency. For more insights on choosing molding methods, check out some keywords5.
Extrusion molding has a higher material utilization rate than injection molding.True
Extrusion molding's continuous process minimizes waste, making it more efficient in material use compared to the intermittent nature of injection molding.
Injection molding generates less waste than extrusion molding.False
Injection molding produces significant waste from gates and runners, leading to higher overall waste compared to the low waste in extrusion processes.
How Does Production Efficiency Influence Costs in Injection Molding?
Do you ever think about how production efficiency truly affects costs in injection molding? It’s an interesting subject. Efficiency influences not only costs but also the whole manufacturing process. Let’s explore this exciting topic together!
Production efficiency affects costs in injection molding significantly. Manufacturers reduce expenses for equipment, material, energy and labor by improving efficiency. This results in lower total production expenses. Efficiency plays a very important role.
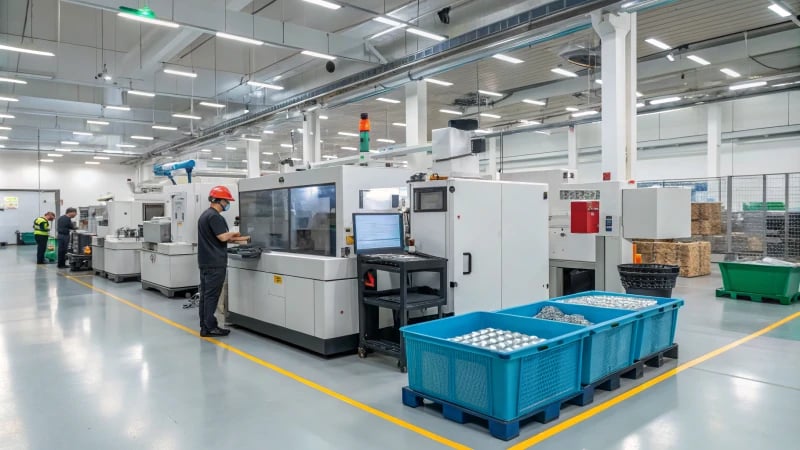
Understanding Production Efficiency
Production efficiency in injection molding refers to the ability to produce parts with minimal waste of resources while maximizing output. It is influenced by several factors such as machine capability, cycle time, and operational practices.
For example, a well-tuned injection molding machine can reduce cycle times significantly, leading to increased throughput. This improved efficiency translates to lower per-unit costs, as fixed costs are spread over a larger number of products.
Factors Affecting Production Efficiency
-
Machine Capability
The type of injection molding machine can greatly affect efficiency. We once bought a precision machine. Although it was expensive, the long-term savings were clear due to reduced cycle times and energy savings. -
Cycle Time
Reducing cycle time directly impacts production efficiency. We once cut cycle time by 30 seconds per part. This small change allowed us to make thousands more parts weekly, lowering labor and energy costs per unit significantly. -
Automation
Automated systems can enhance efficiency by minimizing human error and streamlining processes. For example, implementing robotic arms for part ejection reduced human mistakes and made processes much smoother.
Impact on Cost Structure
Injection molding’s cost structure is heavily influenced by production efficiency. Here’s how:
Cost Component | Effect of Increased Efficiency |
---|---|
Equipment Cost | Lower per unit cost due to amortization over more units produced. |
Material Cost | Higher material utilization reduces waste, leading to lower costs. |
Energy Cost | More efficient machines consume less power over time. |
Labor Cost | Reduced manual intervention lowers overall labor expenses. |
Production Efficiency vs. Equipment Cost
The equipment costs associated with injection molding are significant. Precision machinery that enhances production efficiency often comes with a hefty price tag. For instance, high-quality machines can range from hundreds of thousands to millions of yuan! From my experience, investing in such machines benefits performance and lowers costs over time.
Energy Consumption and Production Efficiency
The energy consumption during injection molding is another critical factor. Efficient machines require less energy due to optimized heating and cooling cycles.
Example:
A well-optimized injection molding machine might consume 20% less energy compared to older models. This reduction in energy consumption can significantly lower operational costs, especially over long production runs.
Waste Management and Material Costs
Material waste is a significant concern in injection molding. Increased production efficiency can help minimize waste generation. For example, we were excited when our scrap rate fell from 15% to 5% after optimization; this reduction was not just in numbers but meant big savings for us.
Moreover, recycling waste materials effectively further reduces overall material costs. Learn more about waste management6.
Conclusion on Efficiency’s Role in Cost Control
In summary, enhancing production efficiency in injection molding can lead to substantial cost reductions across various components like equipment, material, energy, and labor costs. Each of these aspects plays a crucial role in the overall economics of injection molding operations. Readers interested in diving deeper should explore best practices in production efficiency7.
Higher production efficiency reduces labor costs in injection molding.True
Efficient processes minimize manual intervention, leading to lower overall labor expenses.
Precision machines always have lower initial costs than standard machines.False
While precision machines may have higher upfront costs, they save money long-term through efficiency gains.
What Are the Labor Requirements for Injection Molding Compared to Other Methods?
Ever thought about how different manufacturing methods compare in terms of labor requirements? Knowing these differences might really help improve production efficiency and save costs. Let’s explore how injection molding stacks up against other techniques!
Injection molding usually requires more workers than extrusion molding. The process is complex and needs experienced operators. Injection molding often demands 3-5 operators. These operators focus on quality control and process management. Extrusion molding works well with only 1-2 operators.
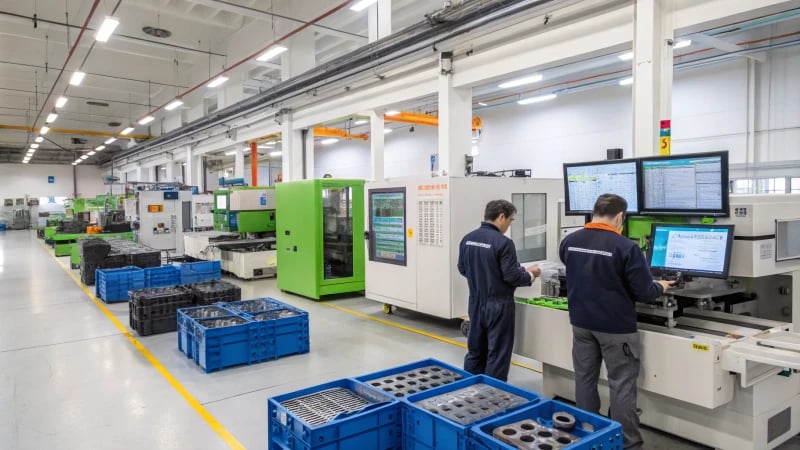
Understanding Labor Requirements in Manufacturing Methods
Labor requirements are crucial in determining the efficiency and cost-effectiveness of manufacturing methods. When comparing injection molding to other techniques like extrusion molding and CNC machining, significant differences arise.
Injection molding involves complex operations that necessitate skilled labor to manage equipment and ensure quality control. The injection process has multiple steps, including mold closing, injection, and cooling, each requiring precise control and attention. For instance, I remember visiting a factory where the average number of operators needed for an injection molding machine ranged from three to five, depending on the complexity of the product and the automation level.
In contrast, extrusion molding is characterized by its simpler operation. The equipment typically requires only one or two operators to oversee the continuous production process. This simplicity results in lower labor costs and less specialized training for workers.
To explain further, a detailed analysis of labor costs8 I read during my studies showed that extrusion molding demands significantly less manpower due to its automated nature.
Equipment Complexity and Labor Demand
Method | Equipment Complexity | Required Operators | Labor Cost |
---|---|---|---|
Injection Molding | High | 3-5 | High |
Extrusion Molding | Low | 1-2 | Low |
CNC Machining | Moderate | 2-4 | Moderate |
The tools for injection molding are like a finely-tuned machine, requiring more skilled technicians for setup and maintenance compared to simpler systems like extrusion molding. Technicians must understand intricate aspects such as pressure control and temperature settings well. I recall my first time seeing an injection molding machine in motion – it was captivating! This translates to higher labor costs and a greater need for ongoing training in injection molding.
Conversely, in CNC machining, operators must also have skills to program machines but generally manage fewer variables than those required for injection molding. Each method’s distinct labor needs can deeply influence production costs and efficiency. Curious about labor’s effect on production choices? This detailed study9 is worth exploring.
Quality Control and Labor Intensity
Quality assurance is another area where labor demands vary greatly across methods. In injection molding, quality checks are essential at each stage to prevent defects such as flash or shrinkage. I remember a project where each team member was vigilant with these checks; it felt like a shared mission to ensure a perfect product! This often requires dedicated personnel for inspection tasks, contributing to higher labor intensity.
On the other hand, extrusion processes might only require periodic checks, thus needing fewer personnel focused on quality control.
In summary, labor needs greatly influence how different manufacturing methods operate. Complexity, needed skills, and quality control efforts determine workforce size while affecting overall production efficiency and costs.
Injection molding requires more skilled labor than extrusion molding.True
Due to its complex operations, injection molding needs skilled technicians for setup and quality control, unlike simpler extrusion processes.
CNC machining has lower labor costs than injection molding.True
CNC machining requires fewer operators and less specialized training compared to the high demands of injection molding labor.
How Do Equipment and Mold Costs Compare Across Manufacturing Techniques?
Have you ever thought about the costs of different manufacturing methods? Let me take you on a journey through the complex details of equipment and mold expenses in both extrusion and injection molding. The information might change your approach to future projects!
Equipment and mold costs differ greatly between manufacturing methods. Injection molding often costs more. It uses very complex machinery and molds. Extrusion usually presents lower expenses. This is because of simpler designs and better use of materials. Knowing these differences really supports informed choices in product design. It really helps.
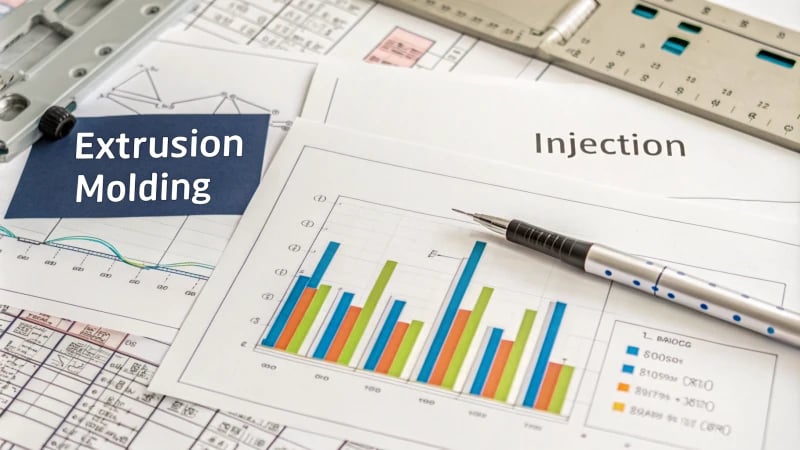
Understanding Equipment Costs in Manufacturing Techniques
When comparing the equipment costs of different manufacturing techniques, it’s essential to look at the complexity and functionality of the equipment used.
Extrusion Molding Equipment Costs
- Simple Structure: Extrusion molding equipment typically consists of an extruder, mold, traction device, cooling device, and cutting device. I remember my first time with extrusion. It worked smoothly, making everything look simple.
- Cost Efficiency: The price of an extruder can range from tens of thousands to hundreds of thousands of yuan. A small plastic pipe extrusion machine is generally more affordable compared to more complex machinery.
- Mold Affordability: Molds for extrusion processes are simpler and cheaper to produce, with costs often ranging from a few thousand to tens of thousands of yuan. The short design and manufacturing cycle further minimize costs.
Injection Molding Equipment Costs
- Higher Investment: In contrast, injection molding machines are significantly more expensive. Precision models can cost anywhere from hundreds of thousands to millions of yuan due to their intricate functionalities. It’s like comparing a luxury car to an average sedan.
- Mold Complexity: The molds used in injection molding also carry a hefty price tag, as they require meticulous design and fabrication. A complex mold can easily cost hundreds of thousands of yuan, with longer production cycles further impacting costs.
Material Costs Comparison
When analyzing material costs, understanding the types of materials used and waste generated is crucial.
Manufacturing Technique | Material Type | Material Cost Factors | Waste Generation |
---|---|---|---|
Extrusion Molding | Thermoplastics | Market price and type determine costs; high material utilization | Minimal waste during production |
Injection Molding | Thermoplastics | Requires precise material control; recycling needed for waste | Significant waste from gates and runners |
Production Efficiency and Energy Costs
The efficiency of production processes plays a vital role in overall costs, particularly regarding energy consumption.
Extrusion Molding Efficiency
- Continuous Production: This method boasts high production efficiency. Once the machinery is set up, products can be produced continuously, significantly reducing per-unit energy costs.
- Stable Energy Consumption: Energy costs are relatively predictable and primarily dependent on equipment power and local electricity prices.
Injection Molding Efficiency
- Cyclical Production: In contrast, injection molding follows a cyclical process, which results in lower overall production efficiency. Each cycle can take seconds to minutes, leading to higher energy usage per unit produced.
- Higher Energy Demands: The need for instant high pressure during injection increases energy consumption alongside substantial energy requirements for heating and cooling molds.
Labor Costs Analysis
Labor requirements vary widely between these manufacturing techniques, impacting overall cost structures.
Extrusion Molding Labor Requirements
- Low Labor Demand: The automation in extrusion molding leads to fewer labor needs. Typically, only one or two operators are required to monitor the machinery and maintain quality control.
Injection Molding Labor Requirements
- Complex Operations: Conversely, injection molding demands more skilled labor due to the complexity of operations and quality checks. Operators must ensure precision throughout the entire injection cycle, which translates to higher labor costs.
Summary of Cost Differences
Understanding the cost differences across manufacturing techniques boils down to several key factors:
- Equipment Complexity: Injection molding equipment and molds incur higher costs due to their complexity.
- Material Utilization: Extrusion processes yield less waste enhancing cost-effectiveness.
- Production Methods: The continuous nature of extrusion contributes to lower time and energy costs compared to the cyclical nature of injection molding.
- Labor Demand: Higher labor requirements in injection molding lead to increased overall costs.
For those seeking further insights into cost calculators or specific pricing details related to these techniques, consider exploring resources about manufacturing equipment costs10.
Extrusion molding equipment is generally cheaper than injection molding.True
Extrusion molding equipment has a simpler structure, leading to lower costs compared to the complex machinery required for injection molding.
Injection molding produces more waste than extrusion molding.True
Injection molding generates significant waste from gates and runners, while extrusion processes minimize waste during production.
When Should You Choose Injection Molding for Production?
Injection molding goes beyond being a simple manufacturing process. It is a game changer for many industries. Once in a while, injection molding is the top choice. Let’s explore situations where this method truly excels.
Injection molding suits high-volume production. It handles intricate designs well. This method offers cost efficiency in mass manufacturing. Material versatility adds to its advantages, allowing various product designs. Quick turnaround times are another benefit. These qualities likely make injection molding a favorite for industries requiring precision. Scalability in their products is important for these sectors.
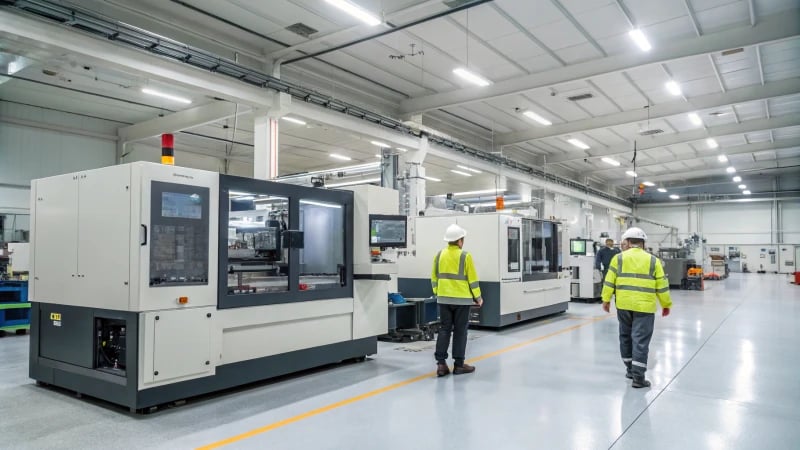
High Volume Production Needs
Injection molding offers incredible efficiency for high-volume production. Think of a project where thousands of identical plastic parts were needed for a new electronic device. The speed after setup was remarkable. Although creating the first mold required a big investment, the cost for each unit dropped significantly once production started. It felt like a movie factory.
Complex Part Design
Some designs are complex and many methods struggle with them. Injection molding excels in creating intricate pieces. A project involved designing a detailed casing that seemed impossible with other methods like 3D printing11. Injection molding brought those complex shapes to life easily. It was like magic watching the precise designs turn into real objects.
Table: Comparison of Design Complexity Across Methods
Method | Complexity Handling | Suitable For |
---|---|---|
Injection Molding | High | Detailed parts like housings and enclosures |
3D Printing | Moderate | Prototypes and low-volume items |
Extrusion Molding | Low | Simple shapes like pipes and profiles |
Cost Efficiency in Mass Production
Cost is important. Injection molding has high initial costs, raising concerns. However, these costs become manageable in mass production. For instance, a mobile phone casing project showed great material savings over time. Even though the startup cost was high, material savings justified the expense. It was like uncovering treasure after hard work.
Material Versatility
Injection molding is very adaptable. Choosing materials for a durable yet flexible healthcare product was essential. This method offered many thermoplastics that suited our needs across various applications including automotive parts or medical devices – this process satisfies material choices without losing quality.
Shorter Lead Times for Production
Every moment counts in today’s fast-paced market. Once molds are ready, injection molding is swift. A project required an early launch to grab an opportunity. Thanks to injection molding, this was possible! Quick production helped deliver the product to customers before competitors could catch up. The rapid turnaround was crucial.
In conclusion, knowing when to use injection molding changes the game for manufacturers wanting to refine their strategies. Each case presents unique benefits to meet market needs successfully. Curious about how injection molding compares to other methods? Check out these resources12 for more insight!
Injection molding is best for high-volume production needs.True
This method excels in producing large quantities of identical parts efficiently, making it ideal for high-demand industries.
Injection molding is unsuitable for complex part designs.False
Contrary to this claim, injection molding actually supports intricate geometries and high precision, making it ideal for complex designs.
Conclusion
Explore the differences between injection molding and other manufacturing methods regarding cost, efficiency, precision, and material use to make informed production decisions.
-
Discover how injection molding compares to other manufacturing processes and learn about its unique advantages. ↩
-
Explore the key benefits of injection molding that could influence your production decisions. ↩
-
Learn more about the cost implications of using injection molding versus other methods. ↩
-
Clicking this link provides deeper insights into optimizing material usage for various production methods, enhancing your knowledge for better design decisions. ↩
-
This link offers comprehensive guidance on managing waste effectively in injection molding processes, essential for cost reduction. ↩
-
Discover how optimizing production efficiency can lead to significant cost savings in injection molding processes. ↩
-
Learn about the best practices for enhancing production efficiency and reducing costs in injection molding operations. ↩
-
Explore this link to find relevant studies comparing labor needs across manufacturing methods, aiding in decision-making for efficient production. ↩
-
Learn more about CNC machining’s labor demands through this link, helping you understand its implications for production efficiency. ↩
-
Explore this link for comprehensive cost calculators that can help you better estimate your expenses based on different manufacturing techniques. ↩
-
This link provides a detailed analysis of injection molding scenarios and applications that can enhance your understanding of its advantages. ↩
-
Explore case studies that showcase successful applications of injection molding in various industries to see its effectiveness in action. ↩