Handling the world of manufacturing processes feels overwhelming for many people. Choosing wisely truly elevates your product’s quality and efficiency. Let’s explore the details together!
Choose injection molding for complex, precise designs and material flexibility, while extrusion is ideal for simpler shapes and large production volumes. Consider shape complexity, accuracy, and batch size when deciding between the two methods.
As a product designer, I often face a tough decision. Choosing between injection molding and extrusion is challenging. Each method has unique strengths. Understanding the details really helps a lot. For example, when I worked on complex toy dolls, I chose injection molding. I used it for intricate internal structures and unique shapes. However, in large-scale production of simple plastic parts, extrusion saved a lot of time. It was a very efficient choice! Let’s explore these factors more deeply. Find the best fit for your own projects.
Injection molding is best for complex shapes.True
Injection molding excels in producing intricate designs with high precision, making it the preferred choice for complex shapes.
Extrusion is suitable for high-precision parts.False
Extrusion generally produces simpler shapes and is not ideal for high precision compared to injection molding.
- 1. What are the key differences between injection molding and extrusion?
- 2. How does part complexity influence the choice of manufacturing process?
- 3. How does production volume influence the choice between injection molding and extrusion?
- 4. Which industries truly thrive with injection molding instead of extrusion?
- 5. How do material properties affect the choice between injection molding and extrusion?
- 6. Conclusion
What are the key differences between injection molding and extrusion?
Have you ever thought about how plastic toys or strong car parts are created? Knowing the differences between injection molding and extrusion helps us see many new options for designing products. Let’s explore these interesting plastic-making methods together!
Injection molding and extrusion are very different processes. Product shape complexity, dimensional accuracy, production batch size and material choice vary between them. Injection molding suits intricate designs. It offers high precision. Extrusion shines with simpler, continuous forms.
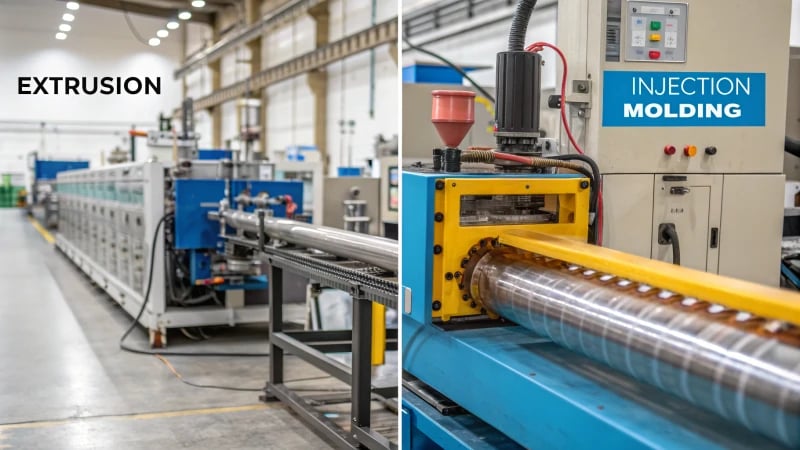
Product Shape Complexity
I think about product design, especially when creating a playful plastic toy doll. The shape’s complexity could greatly influence the project’s success. Injection molding excels in this area. It works like a magical tool. It creates intricate three-dimensional shapes. Delicate features, hollow interiors and complex connections become possible.
On the contrary, I have experienced limitations with extrusion. It focuses on items with consistent cross-sectional shapes. It works efficiently for simpler designs. Achieving fine details feels like forcing a square peg into a round hole. It doesn’t quite fit!
Product Dimensional Accuracy Requirements
Dimensional accuracy holds great importance for me as a designer. I remember the stress of fitting tiny components in electronic devices. Buttons and small gears in mobile phones demanded precise fits. Injection molding becomes my best ally here. It meets strict dimensional tolerances. Its meticulous mold design and precise process control impress me.
Extrusion controls length effectively. However, three-dimensional accuracy sometimes feels uncertain. I have faced moments of needing extra precision. Extrusion often falls short. This serves as a reminder that process choice hinges on details.
Production Batch Size
Large-scale production amazes me with injection molding’s efficiency. I have worked on projects requiring swift production of disposable plastic tableware. Multi-cavity molds allowed us to produce multiple pieces simultaneously. It really saves time. It feels like having an assembly line at hand.
While extrusion boasts speed, it lacks in cost-effectiveness for many small, complex products. Understanding each process’s suitability for different production needs has shaped my design approach. It is fascinating in many ways.
Flexibility in Material Selection
The flexibility of injection molding in material selection is wonderful. I feel empowered to use diverse thermoplastics. High-viscosity and high-performance plastics become accessible.
Industries like automotive benefit greatly from this.
I remember using nylon and polycarbonate for vehicle interior components. Injection molding’s versatility helped us meet aesthetic and performance goals under various conditions.
Extrusion can handle many materials too, yet complex shapes with high-performance plastics pose challenges sometimes.
These moments remind me of the vital role of material choice.
Key Factors | Injection Molding | Extrusion |
---|---|---|
Product Shape Complexity | High complexity achievable | Limited to continuous shapes |
Dimensional Accuracy | High precision for small parts | Easier control in length |
Production Batch Size | Multi-cavity molds for mass production | Faster speed but lower cost-effectiveness |
Material Selection Flexibility | Wide range of thermoplastics available | Some restrictions for complex shapes |
Injection molding is better for complex 3D shapes than extrusion.True
Injection molding excels in creating intricate three-dimensional shapes, unlike extrusion which is limited to simpler forms.
Extrusion can achieve higher production speeds than injection molding.True
While extrusion may have faster production speeds, it lacks the cost-effectiveness of injection molding for complex products.
How does part complexity influence the choice of manufacturing process?
Do you ever think about how a product’s design details guide the manufacturing process? This journey combines creativity with precise engineering. Let’s explore this world together!
Part complexity greatly influences choices in the manufacturing process. It decides shape details and how precise measurements need to be. It also determines the size of production batches and how flexible material selection can be. Understanding these factors is very important. It helps to improve production efficiency. It also helps to achieve high-quality results.
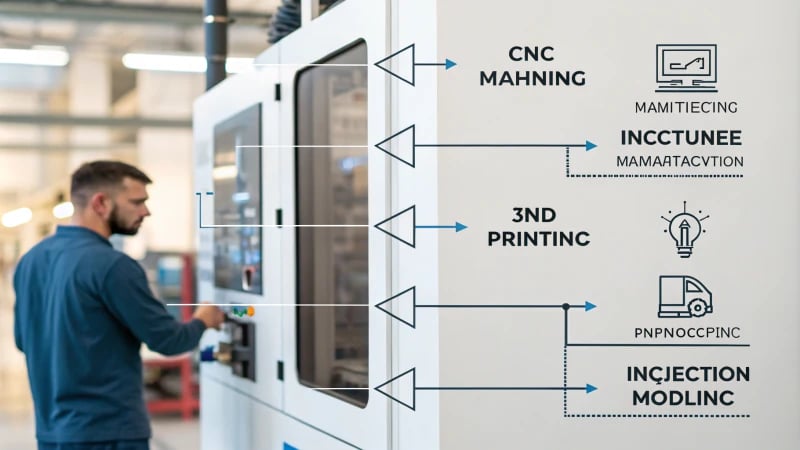
Understanding Product Shape Complexity
Part complexity significantly impacts the choice of manufacturing processes, particularly when it comes to product shape.
For example, when producing parts with intricate three-dimensional geometries, injection molding1 stands out as an optimal method.
This is especially true for items like plastic toy dolls, which often feature various fine shapes, hollow interiors, and complex connection structures. In contrast, extrusion molding mainly produces continuous shapes, making it less suitable for these complex designs.
Manufacturing Process | Ideal For | Limitations |
---|---|---|
Injection Molding | Complex 3D Shapes | Higher initial costs |
Extrusion Molding | Continuous Shapes | Limited design flexibility |
Dimensional Accuracy Requirements
Another critical factor influenced by part complexity is the need for dimensional accuracy. High-precision parts, such as those found in electronic devices, benefit greatly from injection molding.
This process allows for rigorous control over molding parameters and precise mold design. For instance, components like mobile phone buttons and small gears require strict dimensional tolerances that injection molding can consistently meet.
On the other hand, while extrusion molding may achieve good accuracy in length, controlling complex three-dimensional dimensions can be challenging.
Production Batch Size Considerations
The scale of production also plays a crucial role. In large-scale manufacturing scenarios, the efficiency advantages of injection molding become apparent.
By utilizing multi-cavity molds, multiple products can be produced simultaneously in a single injection cycle. For example, I remember producing disposable plastic items for a major event where designing a multi-cavity mold allowed several parts to be produced at once, optimizing mass production and reducing unit costs.
Although extrusion molding may offer faster production speeds, its efficiency does not match that of injection molding for producing numerous small and complex-shaped products.
Batch Size | Process Preference |
---|---|
Large Scale | Injection Molding |
Small Scale | Flexible depending on design |
Flexibility in Material Selection
Finally, material selection flexibility is heavily influenced by part complexity. Injection molding accommodates a wide range of thermoplastics, including high-performance engineering plastics.
For instance, in the automotive sector, materials like nylon and polycarbonate are often utilized to produce intricate interior parts via injection molding.
While extrusion molding can work with various materials, it may face restrictions when handling special high-performance materials designed for complex shapes. This makes injection molding a more versatile option for manufacturers looking to innovate with materials.
In summary, part complexity affects the choice of manufacturing process through shape intricacies, dimensional accuracy needs, production batch sizes,
and material flexibility. Understanding these dynamics helps designers and manufacturers optimize their processes for better quality and cost-effectiveness.
Injection molding is ideal for complex 3D shapes.True
Injection molding excels in producing intricate three-dimensional geometries, making it suitable for complex designs like plastic toy dolls.
Extrusion molding is best for high-precision electronic parts.False
Extrusion molding struggles with dimensional accuracy needed for high-precision parts, unlike injection molding which maintains strict tolerances.
How does production volume influence the choice between injection molding and extrusion?
Have you ever thought about how production volume influences your choice between injection molding and extrusion? In my experience with product design, I found that this decision is both technical and personal. It often represents the specific needs of the project.
Production volume is very important when choosing between injection molding and extrusion. Large quantities often favor injection molding because it is efficient and saves money. Small quantities possibly favor extrusion. Extrusion has faster setups and lower costs.
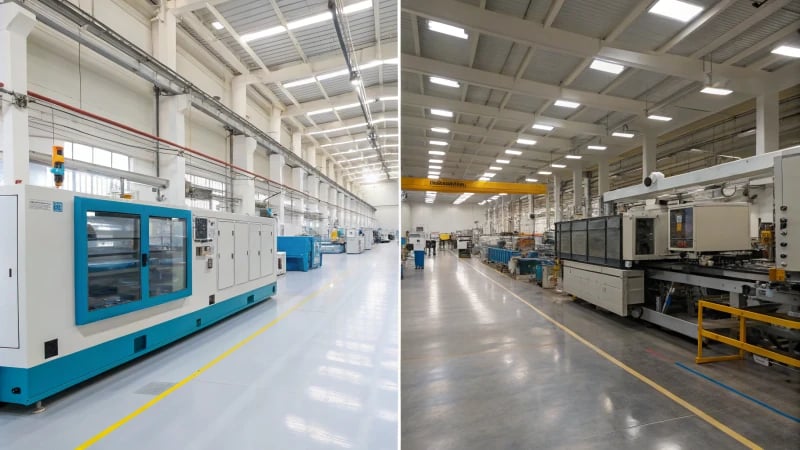
Understanding Production Volume in Manufacturing
When I first explored manufacturing, I quickly saw how important production volume is in deciding between injection molding and extrusion. Each method has its own strengths. Knowing these strengths helps optimize processes for specific needs.
For example, I worked on a project needing a small batch of detailed plastic parts. At first, I thought about using extrusion for its faster setup. But injection molding became the right choice due to its precision. This precision proved very crucial for electronic components where even tiny errors could lead to failure.
Production Batch Size and Its Implications
Considering production volume means evaluating batch size expectations. Here’s a quick summary from my experience:
Batch Size | Recommended Method | Reasons |
---|---|---|
Small Scale | Extrusion | Faster setup times, lower initial costs. |
Medium Scale | Injection Molding | Balances efficiency and complexity. |
Large Scale | Injection Molding | Multi-cavity molds can significantly reduce costs. |
In large-scale productions, injection molding is truly efficient. I worked on a project for disposable plastic tableware. Using multi-cavity molds, we produced many parts in one go, cutting production time and cost per unit. It dramatically changed the high-demand environment.
Complexity of Product Shapes
Complexity always interested me. With intricate designs, injection molding truly excels. Once, I designed plastic toy dolls needing detailed internal parts, like ribs and bosses for functionality. Achieving this with extrusion would have been very hard, maybe even impossible.
Consider these cases:
- Plastic Toy Dolls: These need detailed shapes and hollow interiors. Injection molding does this effortlessly.
- Disposable Tableware: Extrusion is possible but injection molding adds extra detail and variety.
Dimensional Accuracy Requirements
Increasing production volume raises the need for accuracy. I learned how critical this is in electronics, where precision dictates a product’s success. Injection molding, with precise mold design and careful process control, ensures even tiny components like phone buttons or plastic gears meet strict standards.
From my experiences, while extrusion keeps accuracy along its length, getting precision in complex three-dimensional shapes is often very challenging.
Material Flexibility and Production Volume
Material flexibility is key in deciding the right method based on production volume. Injection molding supports a range of thermoplastics, including advanced materials for high-performance uses.
I once worked on automotive interior parts using nylon and polycarbonate in injection molding. This met performance needs and allowed adaptation as specifications changed:
- Low Volume: We used quality materials without huge upfront costs.
- High Volume: Changing materials as needed helped keep product quality consistent.
Understanding how production volume influences manufacturing choices has empowered me to decide wisely, aligning with design and market demands. For more insights on material selection and its effect on production efficiency, check out this resource2.
Injection molding is preferred for high production volumes.True
Higher production volumes benefit from injection molding's efficiency and cost-effectiveness, making it the preferred choice for large-scale manufacturing.
Extrusion is ideal for complex product shapes.False
While extrusion is faster for small runs, it struggles with complex shapes compared to injection molding, which excels in detail and accuracy.
Which industries truly thrive with injection molding instead of extrusion?
Ever wondered why some industries grow rapidly with new production methods? Injection molding is a significant advancement. But which sectors truly benefit? Let’s explore together!
Injection molding is a very important process for industries like automotive, consumer electronics, medical devices, packaging and toys. It creates complex shapes. It also keeps dimensions accurate. This process supports large-scale production in an efficient way. It is really useful.
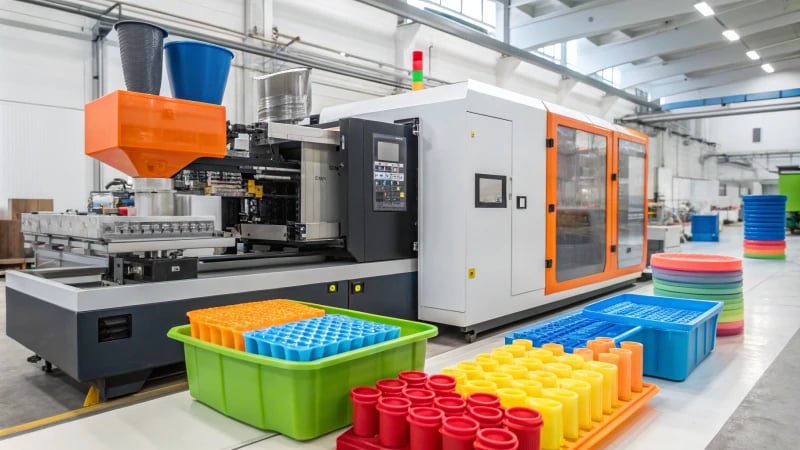
The Automotive Industry
Injection molding is essential in the automotive sector. Car parts face stress daily. They need to be strong and precise. Interior components like dashboards, tiny clips, and fasteners all rely on it. I remember visiting a factory that used injection molding. They created parts from strong materials like nylon and polycarbonate. Watching those molds churn out identical parts was amazing! It’s not just about speed; it’s about making sure every piece fits perfectly, which improves vehicle safety and performance significantly. Learn more about automotive applications3.
Consumer Electronics
Precision is crucial in consumer electronics. I have often marveled at how injection molding creates intricate components like buttons and casings that fit together perfectly. The stringent dimensional accuracy required for products such as smartphones or tablets means that injection molding’s precise control over the production process is invaluable. I worked on a smartphone project where every millimeter mattered, allowing us to produce high-quality parts that were really reliable and functional. The outcome? Happy customers and fewer product returns! Explore more on consumer electronics4.
Medical Devices
In medicine, quality and compliance are essential. Injection molding plays a key role in making parts like syringes and valves that must stay sterile and reliable. I felt proud working on a project creating housings for medical devices using high-grade plastics that survived tough sterilization processes. Every mold was designed with care, guaranteeing quality and safety while maintaining compliance with strict regulatory standards. Discover medical device manufacturing5.
Packaging Industry
The packaging sector has changed thanks to injection molding. Unique containers, caps, and closures are possible because of material flexibility. I attended a workshop where a company showed how multi-cavity molds boost output while cutting costs, enhancing product safety and shelf life! Check out packaging innovations6.
Toys and Consumer Goods
Let’s talk about toys! As a fan of toy design creativity, I admire how injection molding enables complex shapes and vibrant colors. Manufacturers can create toys with intricate designs that may include multiple colors and moving parts, enhancing playability and visual appeal while supporting efficient large-scale production demands. I visited a toy factory that made dolls with intricate designs—everything from fine shapes to hollow interiors—and it was fascinating to see this method create fun products kids adore! View trends in toy manufacturing7.
Injection molding is preferred in automotive for complex parts.True
The automotive industry benefits from injection molding due to its ability to create high-strength, complex parts efficiently and cost-effectively.
Consumer electronics rely on injection molding for precision components.True
Injection molding is crucial in consumer electronics for producing intricate components that require tight tolerances and high dimensional accuracy.
How do material properties affect the choice between injection molding and extrusion?
Do you ever think about how the materials we pick influence how we produce things? I have worked in product design for many years. Knowing these details has really changed my work. This knowledge truly matters.
Material properties like viscosity, thermal stability and dimensional accuracy are crucial. These factors are important when choosing between injection molding and extrusion. Lower viscosity is beneficial for injection molding. This method works well for complex designs. Higher viscosity fits extrusion better. Extrusion suits continuous shapes.
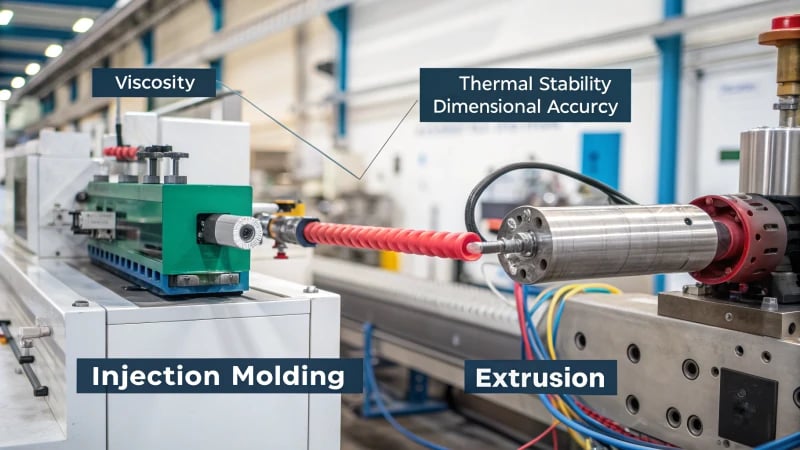
Understanding Material Properties
Material properties play a crucial role in determining the suitability of either injection molding or extrusion for a specific application. Each process has its own strengths, which are influenced by the characteristics of the materials being used.
1. Viscosity of Materials
The viscosity of a material affects how easily it flows during processing. Injection molding generally requires materials with lower viscosity for better flow into molds, especially when creating complex shapes. In contrast, extrusion can handle materials with higher viscosity, allowing for continuous shapes. This makes material viscosity8 a key consideration in the decision-making process.
2. Thermal Properties
Thermal properties such as melting temperature and heat resistance influence processing conditions. For instance, injection molding can accommodate high-performance engineering plastics, which often have higher melting points, allowing for greater flexibility in product design. Extrusion, however, may struggle with these materials if they require specific heating conditions to maintain integrity throughout the process.
Comparison of Manufacturing Methods
Here’s a comparison table that highlights how different material properties affect each method:
Property | Injection Molding | Extrusion |
---|---|---|
Viscosity | Lower viscosity preferred | Can work with higher viscosity |
Thermal Stability | High thermal stability required | Moderate thermal stability accepted |
Shape Complexity | Complex shapes easily produced | Limited to continuous shapes |
Dimensional Accuracy | High precision achievable | Limited dimensional control |
Batch Size | Efficient for large batches | Better for smaller batch runs |
Practical Applications
- Injection Molding: Ideal for intricate designs like plastic toy dolls9 with multiple internal structures, thanks to its ability to create complex geometries.
- Extrusion: Suited for producing items like pipes and profiles that have a constant cross-section, which is easier to manage with less stringent dimensional tolerances.
Material Selection Flexibility
The choice of materials is also vital. Injection molding offers broader flexibility as it can accommodate various thermoplastics including high-viscosity options. For instance, automotive applications often leverage nylon or polycarbonate to manufacture durable components. On the other hand, extrusion may face restrictions when dealing with certain high-performance materials due to their processing conditions. Understanding material compatibility10 helps in making informed decisions regarding the manufacturing method.
Through careful analysis of these factors, product designers can optimize their processes to meet both aesthetic and functional requirements effectively.
Injection molding is better for complex shapes than extrusion.True
Injection molding excels in producing intricate designs due to its ability to fill molds with precision, unlike extrusion which is limited to continuous shapes.
Extrusion can handle materials with lower viscosity effectively.False
Extrusion is designed for higher viscosity materials, allowing continuous production, while injection molding requires lower viscosity for better flow into molds.
Conclusion
This article explores when to choose injection molding over extrusion based on shape complexity, dimensional accuracy, production batch size, and material selection flexibility.
-
Discover how part complexity affects manufacturing choices for better efficiency and quality outcomes. ↩
-
Explore insights on how production volume impacts your choice between injection molding and extrusion processes for better decision-making. ↩
-
Explore this link to discover detailed comparisons and insights into injection molding advantages across different industries. ↩
-
This resource will provide you with a deeper understanding of injection molding’s role in consumer electronics manufacturing. ↩
-
Find out how injection molding meets medical device requirements through precision and compliance. ↩
-
Learn about innovative packaging solutions made possible by injection molding technology. ↩
-
Delve into the toy industry to see how injection molding supports creative design and mass production. ↩
-
Discover how different material properties influence manufacturing choices and improve your production efficiency. ↩
-
Learn about the practical applications of each manufacturing method based on material characteristics. ↩
-
Find out more about material compatibility and its implications for manufacturing processes. ↩