Exploring the world of manufacturing might seem really overwhelming. Choices like injection molding and extrusion appear confusing. I understand this because I once struggled with decisions affecting my entire project.
Choose injection molding when needing complex shapes and high dimensional accuracy. It is perfect for large production batches and versatile material choices. Injection molding suits intricate designs in consumer electronics. Extrusion is faster but less efficient for complex parts. Knowing these differences really helps in manufacturing decisions.
Understanding your product deeply matters, not just selecting a method. Imagine you are designing a plastic toy with many details. Think about small features adding personality to the toy. Injection molding suits this situation well. It captures complex shapes. Tiny ribs and curves on a doll’s body come alive through this method. When producing simple and uniform parts, consider extrusion. This method works faster, but lacks complexity.
Precision also plays a crucial role. I remember a project for an electronic device where every detail was vital. Injection molding kept strict measurements accurately. This precision was very important. Speaking of production volume, injection molding works excellently when making many parts fast. Multi-cavity molds for disposable tableware reduce costs and maintain quality.
Now, consider how each method fits your special project needs. Let’s explore these choices together. You will probably feel more confident in your future decisions.
Injection molding is better for complex shapes than extrusion.True
Injection molding excels in creating intricate designs, while extrusion struggles with complex geometries, making it the preferred choice for detailed products.
Extrusion is more efficient for large production batches than injection molding.False
While extrusion is faster, injection molding offers better efficiency for high-quality, large batch production due to its precision and versatility.
- 1. What are the key differences between injection molding and extrusion?
- 2. How does production batch size influence the choice of molding process?
- 3. What types of products benefit most from injection molding?
- 4. How do I choose the best materials for injection molding versus extrusion?
- 5. How does design complexity influence my choice of manufacturing processes?
- 6. Conclusion
What are the key differences between injection molding and extrusion?
Curious about how complex plastic toys appear? Let’s explore the captivating world of injection molding and extrusion. These two important manufacturing processes have key differences.
Injection molding and extrusion have different uses because of product complexity, accuracy, batch size and material flexibility. Injection molding suits complex designs. It achieves precise parts. Extrusion fits simpler shapes well. Extrusion is also perfect for continuous forms.
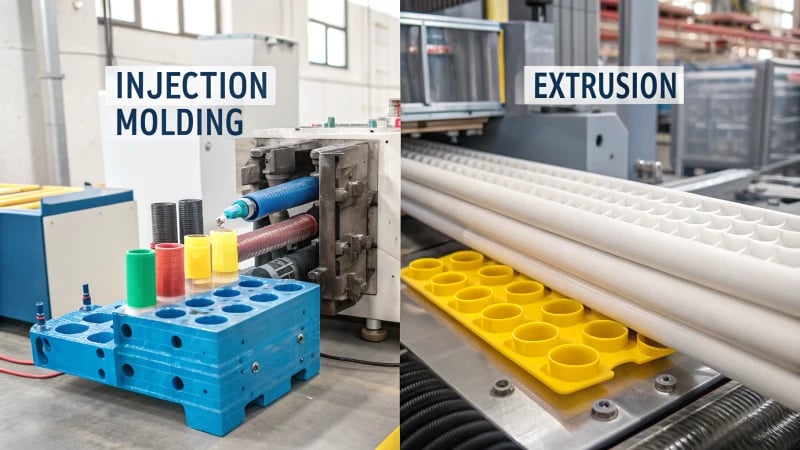
Understanding Injection Molding
Injection molding feels magical when crafting parts. Molten material flows into a mold, and soon, you have complex shapes ready. I worked on a toy project for a company where we designed a line of dolls. Injection molding handled the complex internals like ribs and undercuts easily. It is perfect for making precise parts, especially in electronics. I watched how mobile phone buttons were made; the precision was amazing!
The magic of injection molding is in its multi-cavity molds. Many products get created at once, which is great for large-scale production. I remember seeing a multi-cavity mold making disposable tableware. It was exciting to see efficiency cut costs and speed up production.
Advantages of Injection Molding
- Complex Shapes: This method excels at creating products with detailed designs, fueling creative ideas.
- High Precision: Tiny parts needing precise accuracy? Injection molding handles it well, especially in consumer electronics.
- Mass Production: Multi-cavity molds drastically lower per-unit costs, which is vital for large productions.
Exploring Extrusion
Now, let’s discuss extrusion. This process focuses on consistency. Imagine pushing material through a die to make long items like pipes or sheets. I often see extrusion with simpler shapes; while efficient, it lacks the detail of injection molding.
Strengths of Extrusion
Feature | Injection Molding | Extrusion |
---|---|---|
Product Shape Complexity | High | Low |
Dimensional Accuracy | High | Moderate |
Production Batch Size | Large-scale production | Continuous production |
Material Flexibility | High | Moderate |
- Continuous Production: Extrusion’s nonstop creation of steady shapes suits large volumes of similar parts.
- Material Options: While extrusion handles various materials, it struggles with high-performance engineering plastics compared to injection molding.
Key Considerations
When choosing between these methods, consider a few factors:
- Product Design Complexity: Projects with detailed designs and features lead me to choose injection molding.
- Production Scale: For large batches of simple shapes, extrusion often saves money.
- Material Characteristics: Material properties matter – a lot! Injection molding generally offers more flexibility in choosing materials.
For those wanting to learn more about these manufacturing processes, explore resources that dive into injection molding vs extrusion1. Whether designing the next big thing in consumer electronics or just curious about plastic manufacturing, understanding these differences empowers your design decisions and improves your projects.
Injection molding is ideal for complex product shapes.True
Injection molding excels in creating intricate designs, making it suitable for products with elaborate geometries like toys and electronic components.
Extrusion allows for continuous production of simple shapes.True
Extrusion is a continuous process that produces consistent cross-sectional shapes, making it efficient for manufacturing simpler components like pipes.
How does production batch size influence the choice of molding process?
Have you ever thought about how the size of a production batch influences the molding process we pick? This question is important for everyone in manufacturing. It was important for me when I first began!
Production batch size greatly affects the choice of the molding process. Large-scale production prefers injection molding. It is efficient and creates complex shapes. The unit costs are lower. This decision has a direct impact on cost-effectiveness and product quality in manufacturing. It really changes both cost and quality.
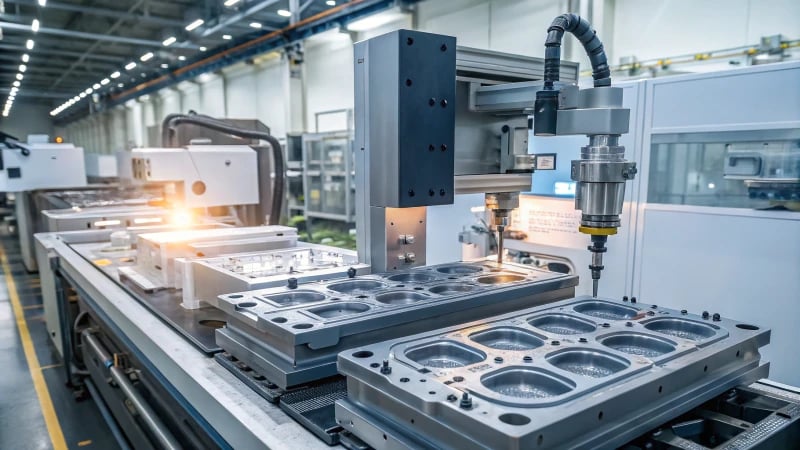
Understanding Production Batch Size in Molding Processes
Production batch size refers to the number of units produced in a single manufacturing run. This factor significantly influences the choice of molding processes, as it determines efficiency, cost-effectiveness, and ultimately, product quality.
Large Batch Production:
When dealing with large-scale production, the efficiency advantage of injection molding becomes more pronounced. This method can utilize multi-cavity molds, allowing for the simultaneous production of multiple products in one injection cycle.
For instance, consider the production of disposable plastic tableware. By designing a multi-cavity mold, manufacturers can produce several pieces at once, reducing unit costs significantly.
Production Method | Advantages for Large Batch Production |
---|---|
Injection Molding | High efficiency with multi-cavity molds; reduced unit costs; ideal for complex shapes |
Extrusion Molding | Faster production speed; less suited for intricate designs |
However, while extrusion molding can produce items quickly, it may not match the cost-effectiveness of injection molding when creating numerous small and complex-shaped products. This leads us to the next point of consideration.
Influence of Product Shape Complexity
The shape complexity of the product also plays a crucial role in determining the most suitable molding process. Injection molding excels at producing parts with intricate three-dimensional shapes.
For example, when designing plastic toys like dolls, the body parts often require complex internal structures. In contrast, extrusion molding is primarily suited for continuous shapes, making it less capable of handling intricate designs efficiently. For further insights on product shape complexity, explore product design complexities2.
Dimensional Accuracy Requirements
Another critical aspect is the dimensional accuracy required by the product. Small parts that demand high precision benefit from injection molding, which can produce components like mobile phone buttons or small gears with tight tolerances.
In comparison, while extrusion can manage length accuracy relatively well, controlling other special three-dimensional dimensions proves to be more challenging. For those interested in understanding accuracy in molding processes, check out precision in manufacturing3.
Flexibility in Material Selection
Moreover, injection molding offers greater flexibility when it comes to material selection. It accommodates a variety of thermoplastics, including high-viscosity and high-performance engineering plastics.
This is particularly relevant in industries like automotive manufacturing where materials such as nylon and polycarbonate are essential for producing interior parts. While extrusion also allows for diverse materials, it may face limitations when dealing with complex shapes made from specialized materials. To learn more about material selection in molding processes, refer to molding materials guide4.
By analyzing these factors from my experiences,
i’ve learned how production batch size affects molding process choices. Each method offers benefits suited to specific production needs and product requirements.
Large batch sizes favor injection molding over extrusion molding.True
Larger production batches benefit from injection molding's efficiency and cost-effectiveness, making it the preferred choice for high-volume manufacturing.
Extrusion molding is ideal for complex-shaped products.False
Extrusion molding is less suited for intricate designs, making it unsuitable for complex-shaped products compared to injection molding.
What types of products benefit most from injection molding?
Have you ever thought about how complex plastic toys or perfectly fitting electronic parts get created? Injection molding is the process that creates many products we use every day. Let’s explore the interesting world of injection molding and learn which products really gain from using this method.
Injection molding is very useful for products with complex shapes. It offers high precision and suits large production volumes. It also provides flexible material choices. The automotive industry benefits greatly from this method. The electronics and consumer goods industries also use these advantages. They improve their manufacturing processes by using injection molding.
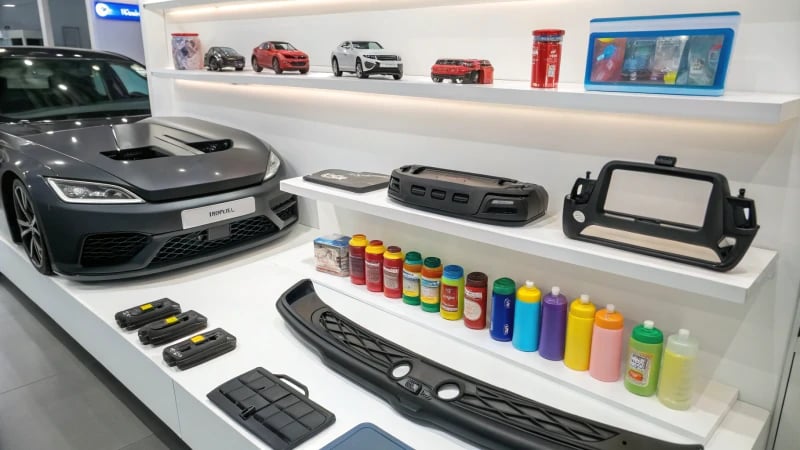
Complex Shapes and Structures
Injection molding has a special charm. It helps us create complex forms, delivers exactness and produces large amounts quickly. I remember first seeing injection molding at a factory. The machines moved with amazing speed, making plastic parts for household electronics. It truly impressed me.
Injection molding stands out with its ability to form detailed three-dimensional shapes. Think about plastic toy dolls. Their parts have fine designs and hollow spaces that other methods can’t create. I worked on a project to build dolls with unique faces and clothes. Injection molding made it easy to form these detailed pieces, unlike extrusion molding, which works better with simple shapes.
I look back and realize that injection molding unlocked creativity impossible otherwise.
Precision and Dimensional Accuracy
Precision matters for small parts in electronics. I once worked on a mobile phone prototype needing perfectly sized plastic buttons. Injection molding delivered high accuracy, meeting tight tolerance levels crucial for device function.
When precision is vital, injection molding stands out as the best choice.
Molding Type | Dimensional Accuracy |
---|---|
Injection Molding | High precision, suitable for small parts |
Extrusion Molding | Easier to control length, harder for shapes |
As evident, injection molding stands out when precision is paramount.
Production Volume Efficiency
Production efficiency really matters in manufacturing. During a project on disposable plastic tableware, we used multi-cavity molds to make many pieces at once. Watching colorful plates and cups come off the line fast was satisfying.
Though extrusion molding can be quicker, it doesn’t match injection molding for low-cost, large-scale complex shapes.
Production Volume | Injection Molding | Extrusion Molding |
---|---|---|
Low | Less efficient | Fast |
Medium | Balanced | Moderate |
High | Highly efficient | Less effective |
Material Versatility
Material versatility is key. Injection molding permits a broad range of thermoplastics, such as nylon and polycarbonate, which are vital for car industry use.
On a project, we picked a strong material for car interior parts. These parts needed strength in various conditions. Extrusion molding has merits but struggles with complex shapes using some materials.
The versatility of injection molding allows designers to choose the best material for their specific application, ensuring optimal performance and durability.
By understanding these core benefits – complex shape creation, precision needs, production efficiency and material flexibility – I feel ready to decide on manufacturing processes for my designs. Explore more on topics like product design best practices5 and material selection strategies6.
What do you think? Are you ready to see what injection molding offers for your next project?
Injection molding is ideal for complex product shapes.True
Injection molding excels in creating intricate designs, making it perfect for products like toy dolls that require detailed and complex shapes.
Extrusion molding is better for producing small, precise parts.False
Injection molding provides higher precision for small parts compared to extrusion molding, which is less effective for intricate shapes.
How do I choose the best materials for injection molding versus extrusion?
Choosing the correct materials for injection molding or extrusion seems difficult. However, it is not as hard as it seems! Let us explore the best materials for each process. These materials really help in turning your ideas into reality.
To choose between injection molding and extrusion materials, think about their abilities. Injection molding excels in creating intricate shapes. It is great for precision with materials such as nylon and polycarbonate. Extrusion suits simpler forms. It works best with thermoplastics like polyethylene and polystyrene.
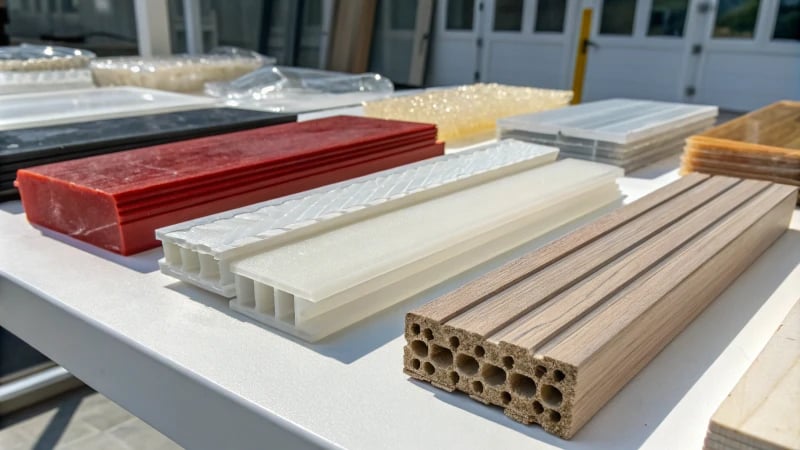
Understanding Material Suitability
When choosing materials for either injection molding or extrusion, it’s essential to consider the specific characteristics and requirements of the intended product.
Injection Molding typically excels with:
- Thermoplastics: These are versatile and can be melted and molded multiple times. Common examples include polypropylene (PP) and acrylonitrile butadiene styrene (ABS).
- Engineering Plastics: For high-performance applications, materials like nylon (PA) and polycarbonate (PC) are often favored due to their strength and durability.
In contrast, Extrusion is generally more suitable for:
- Thermoplastic Polyolefins: Such as polyethylene (PE) and polystyrene (PS), which can be continuously processed into sheets or films.
- Flexible Materials: Including rubber-like compounds that can be extruded into various shapes and forms.
Material Properties and Their Applications
The choice of material can significantly affect the product’s performance in real-world applications. Below is a comparative table of suitable materials and their characteristics:
Material Type | Injection Molding Characteristics | Extrusion Characteristics |
---|---|---|
Polypropylene (PP) | Good chemical resistance, ideal for packaging | Often used for films and sheets |
Acrylonitrile Butadiene Styrene (ABS) | High impact resistance, excellent surface finish | Not typically used in extrusion |
Nylon (PA) | High strength and temperature resistance | Can be extruded, but typically less common |
Polycarbonate (PC) | Excellent toughness and clarity | Limited due to processing difficulty |
Polyethylene (PE) | Can create complex shapes, widely used in consumer goods | Great for continuous profiles and packaging |
Complexity of Product Shapes
One of the major advantages of injection molding is its ability to create complex three-dimensional shapes that extrusion cannot easily replicate. For example, intricate designs like those found in plastic toy dolls7 can be effectively produced through injection molding, thanks to its capacity to handle complex geometries.
Conversely, extrusion is best for simpler, continuous shapes such as pipes or sheets where complexity is minimal.
Dimensional Accuracy Requirements
Injection molding stands out in industries requiring high precision, such as electronics. Parts like small plastic gears8 or mobile phone buttons often need tight tolerances that injection molding can provide due to its precise mold designs.
In contrast, while extrusion offers a degree of control, the dimensional accuracy in three-dimensional aspects can be challenging, making it less suitable for applications demanding strict specifications.
Production Batch Size Considerations
For large-scale production, injection molding becomes more advantageous due to its efficiency. Multi-cavity molds allow for multiple products to be produced in a single cycle, making it ideal for mass production9 of items like disposable plastic tableware.
While extrusion has a fast production speed, it may not yield the same cost-effectiveness in scenarios where small and complex-shaped products are required.
Flexibility in Material Selection
Another point of distinction lies in the flexibility of material selection. Injection molding supports a wide range of thermoplastics, including high-viscosity materials that are critical in industries like automotive. For example, parts made from nylon or polycarbonate are crucial for automotive interior components10.
On the other hand, extrusion can be limited when dealing with certain high-performance materials due to processing constraints, particularly when producing complex shapes.
Injection molding is ideal for producing complex shapes.True
Injection molding excels at creating intricate three-dimensional designs, unlike extrusion, which is better suited for simpler forms.
Extrusion is more efficient for large-scale production than injection molding.False
While extrusion has fast production speeds, injection molding's multi-cavity molds make it more efficient for mass-producing complex items.
How does design complexity influence my choice of manufacturing processes?
As a designer, I often struggle with the details of complicated designs. These complex designs influence my decisions in manufacturing, too. Let’s explore this important topic together!
Design complexity strongly influences your selection of manufacturing methods. It decides factors like shape possibility, needed precision, production size and material adaptability. Understanding these effects helps in choosing smarter options. This can really enhance production efficiency and truly improve product quality.
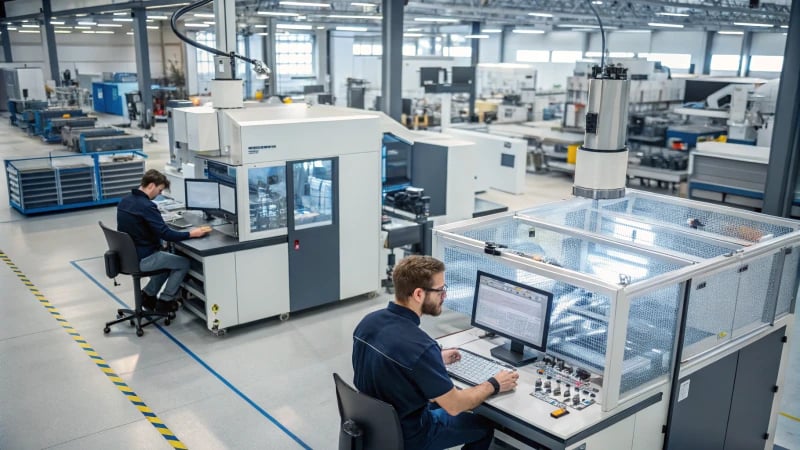
Product Shape Complexity
Design complexity really influences my choice of manufacturing process. It helps improve production efficiency and quality. Years of experience have shown me how every design decision affects the entire process. It shapes the final product in unexpected ways.
Once, I worked on a project with plastic toys. The toys had detailed, three-dimensional shapes with hollow parts. I realized choosing the right manufacturing method was very important. Injection molding allowed me to create complex shapes easily. I remember the thrill of seeing the first sample. It captured all the fine details perfectly!
Extrusion molding only works for continuous shapes. It would not have worked for those toys. The shape complexity strongly decides my manufacturing path. I see this as a critical part of designing. You can learn more about these processes by exploring complex product shapes11.
Dimensional Accuracy Requirements
I also learned a lot from a project with electronic devices. High precision was crucial for tiny parts like buttons and gears on mobile phones. Injection molding provided excellent control. We could meet strict accuracy needs by designing precise molds and processes.
Producing tiny parts with tight tolerances brought a sense of relief. Extrusion molding would struggle with such accuracy. Check out how to achieve high precision in manufacturing12.
Production Batch Size
I saw how batch size affects manufacturing choices. Large productions benefit from injection molding. I worked on disposable plastic tableware with a multi-cavity mold. Producing many parts in one cycle was efficient and cost-effective.
Though extrusion is fast, it’s not as cost-effective for large volumes of complex shapes. Explore ways to improve your production by checking production batch strategies13.
Flexibility in Material Selection
Material flexibility is very important in my projects. Injection molding works with many thermoplastics, including engineering plastics for cars. I used nylon and polycarbonate for vehicle parts. Knowing these materials last was satisfying.
Extrusion handles various materials but has limits with complex shapes or high-performance needs. Examine material selection guidelines14 for your design needs.
Summary Table of Manufacturing Processes
Feature | Injection Molding | Extrusion Molding |
---|---|---|
Shape Complexity | High | Limited |
Dimensional Accuracy | High | Moderate |
Production Batch Size | High Efficiency | Faster Production Speed |
Material Flexibility | Wide Range | Some Limitations |
These experiences teach me about design complexity and its effects on manufacturing processes. Each project is a learning chance that guides me toward smarter decisions that boost efficiency and quality.
Injection molding is ideal for complex product shapes.True
Injection molding excels in creating intricate geometries, making it suitable for products with complex shapes like toys and components requiring fine details.
Extrusion molding offers high dimensional accuracy.False
Extrusion molding generally struggles with maintaining high dimensional accuracy compared to injection molding, especially for complex designs.
Conclusion
Learn when to choose injection molding over extrusion for manufacturing based on shape complexity, accuracy needs, production scale, and material selection.
-
Clicking this link will provide you with comprehensive comparisons and case studies that highlight the differences between these two manufacturing methods. ↩
-
Clicking this link will provide you with deeper insights into production batch sizes and their impact on manufacturing efficiency. ↩
-
This link will offer a detailed overview of precision requirements in various manufacturing processes, enhancing your understanding. ↩
-
Explore this link to discover different material options available for various molding techniques and their applications. ↩
-
Discover detailed insights into how injection molding enhances product design across various industries. This knowledge can elevate your projects. ↩
-
Explore expert opinions on the benefits of injection molding. Understanding these can inform your design and production strategies. ↩
-
Explore this link to discover detailed comparisons on materials suited for different manufacturing processes, enhancing your knowledge for better decision-making. ↩
-
Explore this link to discover detailed comparisons on materials suited for different manufacturing processes, enhancing your knowledge for better decision-making. ↩
-
Explore this link to discover detailed comparisons on materials suited for different manufacturing processes, enhancing your knowledge for better decision-making. ↩
-
Explore this link to discover detailed comparisons on materials suited for different manufacturing processes, enhancing your knowledge for better decision-making. ↩
-
This link provides insights into how product shapes influence manufacturing methods, enhancing your design strategy. ↩
-
Gain deeper knowledge on achieving dimensional accuracy in production, essential for high-quality outputs. ↩
-
Explore effective batch production strategies that can help you maximize efficiency and reduce costs. ↩
-
Learn about selecting the right materials for complex designs to enhance performance and manufacturability. ↩