Ever felt like you’re trying to crack the code on injection molding UHMWPE? You’re not alone.
Injection molding UHMWPE involves heating the polymer to its melting point, injecting it into a mold under high pressure to create durable, detailed shapes, ideal for robust components due to its toughness and low friction.
I remember the first time I encountered UHMWPE. I was both fascinated and intimidated by its potential. It’s not just about getting the polymer into the mold; it’s about mastering each step, from selecting the right temperature to ensuring the mold design accommodates its unique properties. When done right, it opens up a world of possibilities in creating components that are both resilient and efficient. Let’s explore these nuances together and uncover how this material can transform your designs.
UHMWPE can be injection molded without heating.False
UHMWPE must be heated to its melting point for injection molding.
UHMWPE has exceptional impact resistance.True
UHMWPE is known for its high impact resistance and durability.
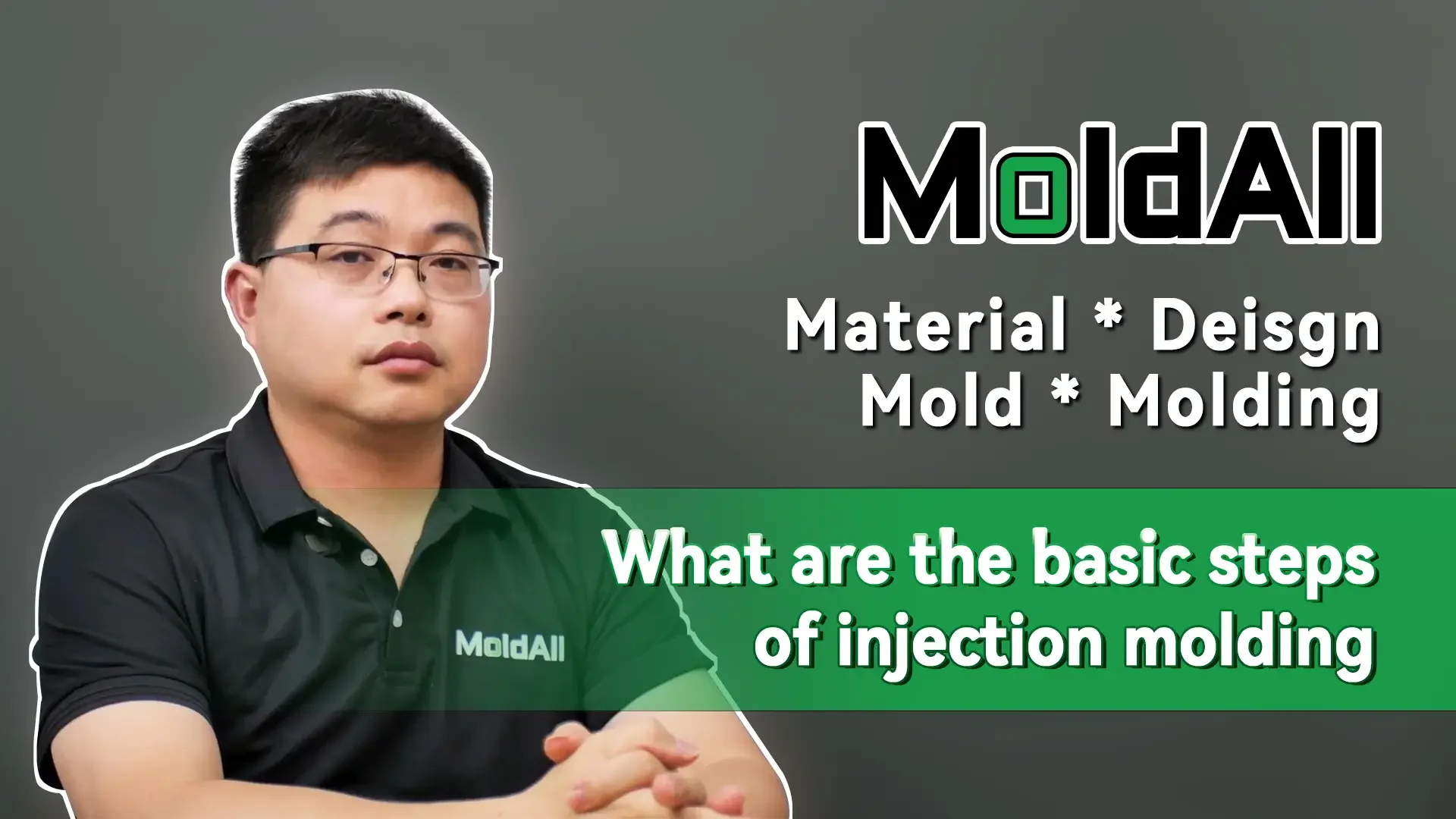
- 1. How Does UHMWPE Differ from Other Polymers in Injection Molding?
- 2. What makes UHMWPE a standout choice for injection molding?
- 3. What Challenges are Associated with Injection Molding UHMWPE?
- 4. How can you optimize the injection molding process for UHMWPE?
- 5. How is UHMWPE Transforming Various Industries?
- 6. Conclusion
How Does UHMWPE Differ from Other Polymers in Injection Molding?
Ever wonder what makes UHMWPE the superhero of polymers in injection molding?
UHMWPE in injection molding offers unmatched durability and wear resistance due to its high molecular weight, but presents unique processing challenges compared to other polymers.
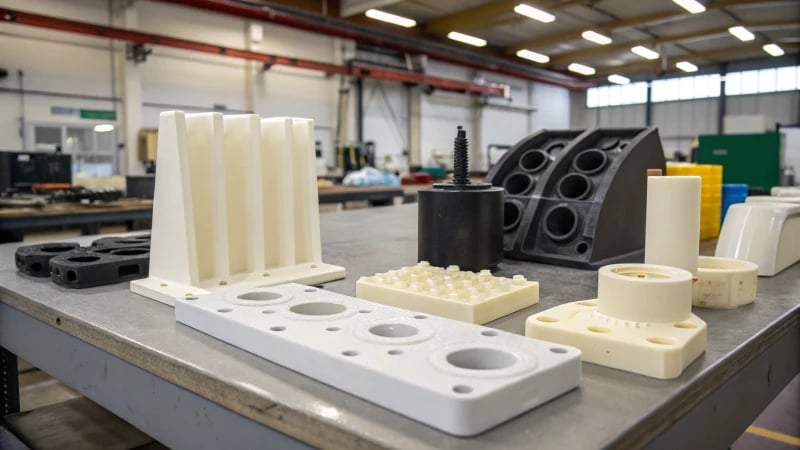
What Makes UHMWPE Stand Out?
When I first encountered Ultra-High Molecular Weight Polyethylene (UHMWPE), I felt like I was meeting the Hercules of polymers. With a molecular weight stretching between 3.1 to 5.67 million amu, it boasts toughness that’s practically legendary. Imagine designing a product that needs to last; UHMWPE is your go-to. But here’s the catch – while its wear and abrasion resistance are off the charts, injection molding1 it is no walk in the park. You have to get that temperature just right due to its high viscosity, something that took me a while to master.
Comparing UHMWPE with HDPE
Property | UHMWPE | HDPE |
---|---|---|
Molecular Weight | 3.1 to 5.67 million amu | 0.2 to 0.35 million amu |
Wear Resistance | Excellent | Good |
Processing Ease | Challenging due to high viscosity | Easier |
Back when I was just starting out, I remember puzzling over the difference between UHMWPE and HDPE. Both are polyethylene, yet their molecular weight sets them worlds apart in properties.
I’ve seen firsthand how UHMWPE’s impressive wear resistance2 makes it perfect for high-stress applications like conveyor belts and bulletproof vests—nothing HDPE can match up to in those scenarios.
Processing Challenges with UHMWPE
Here’s where things get tricky. The same high molecular weight that gives UHMWPE its strength also means it has a much higher melting point compared to other polymers, making the injection molding process more demanding. I remember my first time trying to mold it; it felt like trying to tame a wild horse. Specialized equipment and skills are a must-have to handle its high viscosity, requiring advanced techniques3 and carefully controlled cooling rates.
Applications and Industry Implications
UHMWPE finds its way into many corners of industry where durability and low friction are non-negotiable, such as medical implants, gears, and liners. If you’re making decisions in industries that demand high-performance materials, understanding these material applications4 is crucial.
Sure, you might face higher initial processing costs with UHMWPE due to these challenges; however, think of it as an investment. Its longevity often leads to cost savings in long-term projects5, which can really add up over time.
UHMWPE has a higher molecular weight than HDPE.True
UHMWPE's molecular weight ranges from 3.1 to 5.67 million amu, while HDPE's is 0.2 to 0.35 million amu.
UHMWPE is easier to process than HDPE in injection molding.False
UHMWPE's high viscosity makes it challenging to process compared to HDPE.
What makes UHMWPE a standout choice for injection molding?
Ever wondered why UHMWPE is the unsung hero of injection molding? Let me take you on a journey through its remarkable properties that make it indispensable in many industries.
UHMWPE is ideal for injection molding due to its high impact resistance, low friction, excellent chemical resistance, and outstanding wear properties, making it suitable for demanding industrial applications.
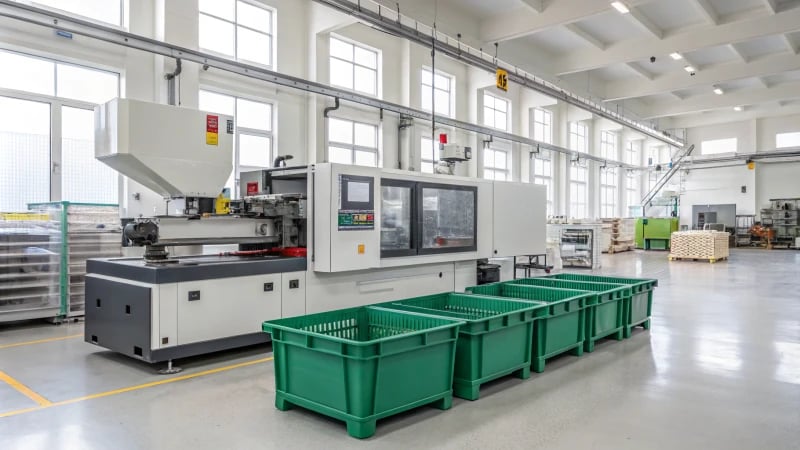
High Impact Resistance
There was a time when I was working on a project that required materials to withstand heavy impacts. I remember testing various materials, and UHMWPE stood out remarkably. Its ability to absorb shocks without cracking made it an ideal candidate for our gears and conveyor belts. It’s like having a superhero shield that doesn’t buckle under pressure, ensuring long-lasting durability.
Low Friction and Wear Resistance
I recall this one design challenge where parts had to glide smoothly over each other without wearing down quickly. UHMWPE, with its low friction, felt like discovering a secret ingredient. It not only reduced wear but also extended the lifespan of our machinery. Imagine how a well-lubricated chain keeps your bicycle running smoothly—UHMWPE does just that for industrial parts, reducing the need for frequent replacements.
Property | Benefit |
---|---|
Low Friction | Reduces wear and tear, extending product life |
High Impact | Withstands heavy impacts without damage |
Chemical Resistance
In environments where chemicals are part of the daily grind, maintaining material integrity is crucial. I once worked on a project in the chemical processing sector and found UHMWPE‘s resistance invaluable. It stood firm against corrosive substances where other materials failed, proving its worth in environments where resilience is key.
Cost-Effectiveness
Despite its premium properties, the long-term savings with UHMWPE are impressive. It was during a budget review that I realized how much we saved on maintenance and replacements. When you look at the bigger picture—including downtime and replacement costs—investing in UHMWPE isn’t just about immediate savings; it’s about strategic foresight.
By tapping into these advantages, we can design products that not only meet rigorous functional demands but also promise longevity and reliability across various fields. Curious about unlocking more design possibilities with UHMWPE? Exploring more about UHMWPE6 might just spark your next big idea.
UHMWPE is ideal for high-impact applications.True
UHMWPE withstands significant impact, making it suitable for durable applications.
UHMWPE has a high coefficient of friction.False
UHMWPE is known for its low coefficient of friction, reducing wear.
What Challenges are Associated with Injection Molding UHMWPE?
When I first encountered the task of injection molding UHMWPE, it felt like tackling a complex puzzle. With its unique properties, the challenges seemed endless, but understanding them was key to mastering the process.
Injection molding UHMWPE is challenging due to high melt viscosity, difficult mold filling, and low thermal conductivity, leading to cooling issues and warping risks.
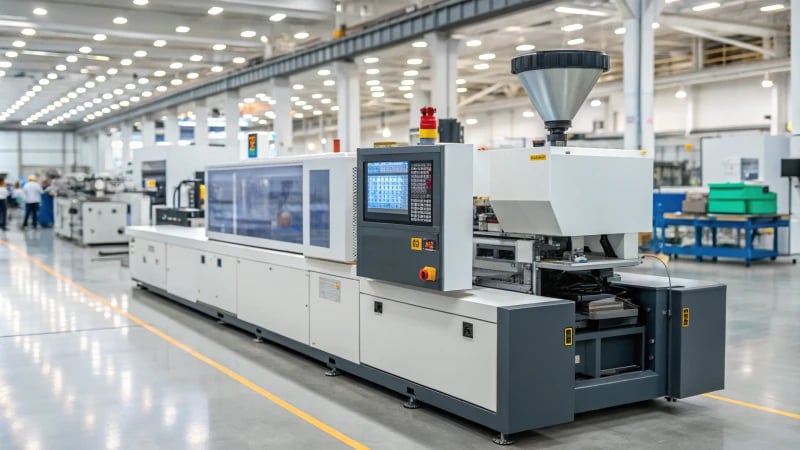
High Melt Viscosity
I remember the first time I worked with UHMWPE; it felt like trying to push honey through a tiny straw. Its high melt viscosity means it’s not the easiest material to coax into all those little nooks and crannies of a mold. In my experience, adjusting the temperature and pressure was like finding that sweet spot in a recipe—too much or too little and you risk defects like voids or incomplete fills.
Processing Parameter | Effect on UHMWPE |
---|---|
Higher Temperature | Improves flow |
Increased Pressure | Enhances filling |
Extended Cooling Time | Reduces warping |
Low Thermal Conductivity
This property reminds me of baking cookies in an oven that heats unevenly. You end up with some cookies burnt and others undercooked. Similarly, UHMWPE‘s low thermal conductivity can lead to warping or shrinkage if cooling isn’t handled just right. Precise temperature control is critical, and I’ve found that a consistent cooling strategy can make all the difference during the molding process7.
Material Degradation
Despite its durability, UHMWPE can degrade if it gets too hot for too long—kind of like leaving chocolate in a warm car. I’ve seen firsthand how implementing effective temperature control measures8 can prevent this degradation, ensuring the material retains its integrity.
- Tip: I always use infrared thermography to keep an eye on mold surface temperatures. It’s like having an extra set of eyes to help fine-tune settings.
Mold Design Considerations
When it comes to mold design, it’s crucial to think about where gates and runners are placed, akin to planning the layout of a new kitchen. Adequate venting is essential to avoid those pesky trapped gases that cause defects. Designing with these considerations in mind not only enhances material flow but also trims down cycle time.
Consider using simulation software as your crystal ball for predicting potential issues before committing to physical prototyping9. This proactive approach has saved me countless hours and resources.
In summary, injection molding UHMWPE is all about understanding its quirks and tailoring your process to manage these unique challenges. With patience and precision, it’s possible to achieve outstanding results.
UHMWPE has high melt viscosity affecting mold flow.True
UHMWPE's high melt viscosity makes it difficult to fill intricate mold details.
Low thermal conductivity in UHMWPE prevents warping.False
Low thermal conductivity causes uneven cooling, leading to potential warping.
How can you optimize the injection molding process for UHMWPE?
Imagine you’ve finally cracked the code to optimize injection molding for UHMWPE, enhancing every component’s durability and precision.
To optimize UHMWPE injection molding, ensure precise temperature control, slow cooling rates, and low pressures to manage its high viscosity and enhance product quality.
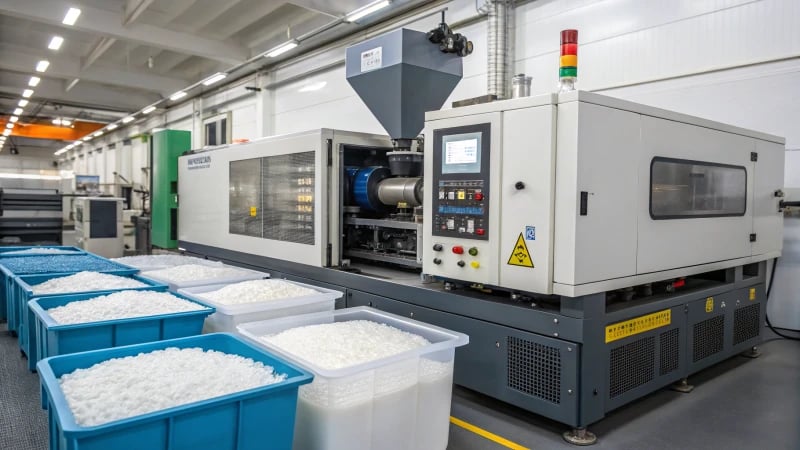
Understanding UHMWPE‘s Unique Properties
When I first encountered Ultra-High Molecular Weight Polyethylene (UHMWPE), I was blown away by its incredible durability and abrasion resistance. It’s like the superhuman of polymers, perfect for industrial components10 and medical devices. However, working with such a robust material brings its own set of challenges, especially in the injection molding process.
Given its high viscosity, UHMWPE demands specific adjustments to molding parameters to ensure everything runs smoothly. It’s a bit like trying to navigate a supercar on a winding road—precision is key.
Key Parameters for Optimization
Temperature Control
Temperature control in this process is akin to keeping a perfect soufflé from collapsing—it’s crucial. By maintaining a consistent mold temperature, I prevent premature solidification and reduce defects. Usually, the sweet spot is between 180°C to 200°C, but sometimes, when dealing with complex geometries11, I have to fine-tune things a bit.
Pressure Management
Pressure management with UHMWPE reminds me of adjusting the pressure in a bike tire—too much, and it could burst; too little, and it won’t ride well. Due to its density, UHMWPE works best with lower injection pressures. This not only protects the molds and machinery from wear but also ensures uniform filling12 without damage.
Parameter | Recommended Range |
---|---|
Mold Temperature | 180°C – 200°C |
Injection Pressure | Low |
Importance of Cooling Rate
The cooling phase is like letting a freshly baked loaf cool—rush it, and you risk disaster. A slow cooling rate prevents warping and maintains dimensional stability. I’ve found that utilizing a consistent cooling system13 enhances the final product’s quality.
Mold Design Considerations
Designing molds for UHMWPE has its own art. It’s like sketching out a plan that must account for material flow and shrinkage rates. Rounded corners and streamlined flow paths are my go-to strategies to reduce stress concentrations, minimizing defects14. With these design tweaks, production cycles are more efficient, and product performance improves noticeably.
By understanding and adjusting these key aspects, I’ve been able to significantly optimize the injection molding process for UHMWPE. This not only ensures high-quality outputs but also minimizes waste—making the process as efficient as possible.
UHMWPE requires high injection pressures for molding.False
UHMWPE benefits from lower injection pressures to prevent mold wear.
Consistent mold temperature is crucial for UHMWPE molding.True
Maintaining temperature prevents premature solidification and defects.
How is UHMWPE Transforming Various Industries?
Ever wondered how a single material could revolutionize multiple industries? Meet UHMWPE, a game-changing plastic that’s changing the face of medical, automotive, and food processing sectors.
UHMWPE is revolutionizing industries like medical, automotive, and food processing with its wear resistance, low friction, and high impact strength, ideal for gears, liners, and implants.
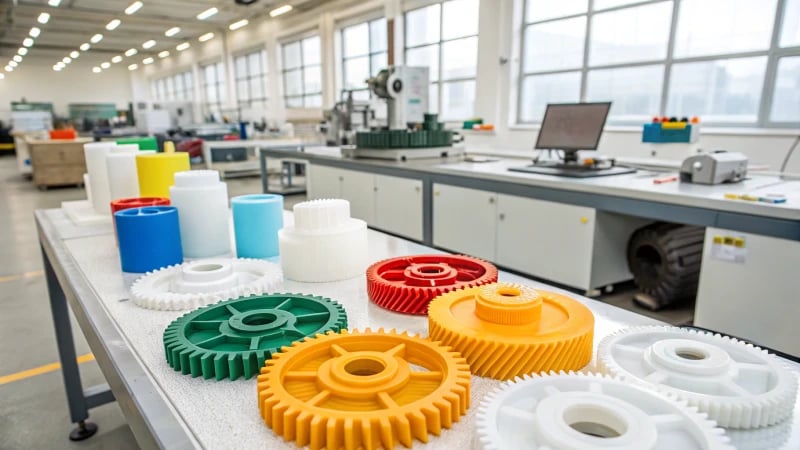
Medical Applications
When I first learned about Ultra High Molecular Weight Polyethylene (UHMWPE), it was during a project on joint replacements. This material’s ability to mimic the smoothness of natural cartilage while being incredibly durable blew my mind. In medical settings, it’s a favorite for hip and knee implants because its biocompatibility reduces wear debris, a major concern in prosthetics. I recall visiting a manufacturing plant where they were crafting orthopedic implants with UHMWPE plates and screws—truly fascinating to see how such a small component could enhance mobility.
- Joint Replacements: UHMWPE‘s durability significantly reduces wear debris15 in prosthetics.
- Orthopedic Implants: Its compatibility with human tissue makes it ideal for plates and screws.
Automotive Industry
Working in product design often means keeping up with the latest materials that can withstand harsh conditions. In the automotive industry, UHMWPE is my go-to for parts like gears and bearings. It’s fascinating how this plastic can extend the lifespan of these components by reducing maintenance needs. Plus, when I worked on a project involving car liners, UHMWPE‘s abrasion resistance was invaluable in protecting against the constant wear and tear vehicles endure daily.
- Gears and Bearings: Provides longevity and reduced upkeep compared to conventional materials.
- Car Liners: Offers robust protection against continuous use.
Food Processing Equipment
Food safety is paramount, and UHMWPE is a game-changer here too. I remember consulting for a food processing company struggling with product sticking issues on conveyor belts. Switching to UHMWPE-lined equipment not only minimized contamination risks but also made cleaning a breeze, cutting down production downtime significantly.
Application | Benefits |
---|---|
Conveyor belts | Easy to clean, reduces downtime |
Chute liners | Minimizes product residue |
Industrial Applications
I’ve also seen UHMWPE‘s impact in heavy industries where machinery undergoes severe wear and tear. During a tour of a large plant, I witnessed how conveyor rollers made from injection molded UHMWPE outlasted traditional materials, saving the company significant replacement costs over time. The precision molding allows for complex shapes without losing any of the material’s beneficial properties.
- Conveyor Rollers: They extend conveyor system life by resisting abrasion.
- Guide Rails: Ensure smooth operations in manufacturing lines.
Using injection molding16 techniques with UHMWPE is like having the best of both worlds—durability and precision in one package. It’s no wonder it’s become a preferred choice for challenging applications across different industries.
UHMWPE is used in hip and knee implants.True
UHMWPE's biocompatibility and wear resistance make it ideal for joint replacements.
UHMWPE is unsuitable for food processing equipment.False
UHMWPE's non-toxic nature makes it suitable for food processing applications.
Conclusion
Injection molding UHMWPE involves heating the polymer, injecting it into molds under high pressure, and managing unique challenges like high viscosity and cooling rates for durable components.
-
Explore this link to understand the specific requirements and techniques for successfully molding UHMWPE components. ↩
-
Learn about how UHMWPE’s wear resistance compares to other common polymers used in industry applications. ↩
-
Discover the specialized methods required for molding high viscosity materials like UHMWPE. ↩
-
Find out how various industries utilize UHMWPE’s unique properties for specialized applications. ↩
-
Understand the economic advantages of UHMWPE over the lifespan of products compared to other materials. ↩
-
Explore various industries benefiting from UHMWPE’s unique properties. ↩
-
Discover effective cooling techniques to prevent warpage and shrinkage in molded parts. ↩
-
Explore methods for maintaining optimal temperature during the injection molding process. ↩
-
Find out how simulation tools can enhance mold design by predicting issues before production. ↩
-
Explore how UHMWPE benefits various industries with its properties, offering insights into suitable applications and optimizations. ↩
-
Learn about advanced techniques for molding complex shapes, essential for optimizing UHMWPE processes. ↩
-
Discover methods to achieve uniform filling in molds, crucial for handling materials like UHMWPE. ↩
-
Find out about cooling system technologies that enhance product quality by maintaining uniform temperatures. ↩
-
Understand strategies to minimize defects, improving efficiency and product quality in UHMWPE molding. ↩
-
Explore why UHMWPE is favored in medical implants for its durability and biocompatibility. ↩
-
Understand why injection molding is ideal for shaping UHMWPE into precise components. ↩