Injection molding is a fascinating blend of science and artistry. But can it really tackle the intricate challenge of threaded molds?
Yes, injection molding machines can effectively inject threaded molds. By implementing specific mold designs and optimized processes, high-quality threaded plastic components can be produced efficiently. Key considerations include precise mold design, appropriate process settings, and reliable demolding mechanisms.
While the answer is affirmative, the success of injecting threaded molds hinges on several critical factors. From precise mold designs to choosing the right materials, understanding these elements is vital for producing defect-free threaded components. Let’s explore these key considerations in detail.
Injection molding machines can inject threaded molds.True
Machines can produce threaded components with precise mold design and process.
What Are the Key Design Considerations for Threaded Molds?
Designing threaded molds requires precision and expertise. What key factors ensure success?
Key design considerations for threaded molds include precise thread structure, suitable demolding mechanisms, and optimal material selection. Ensuring these elements align with the product requirements guarantees high-quality injection-molded threads.
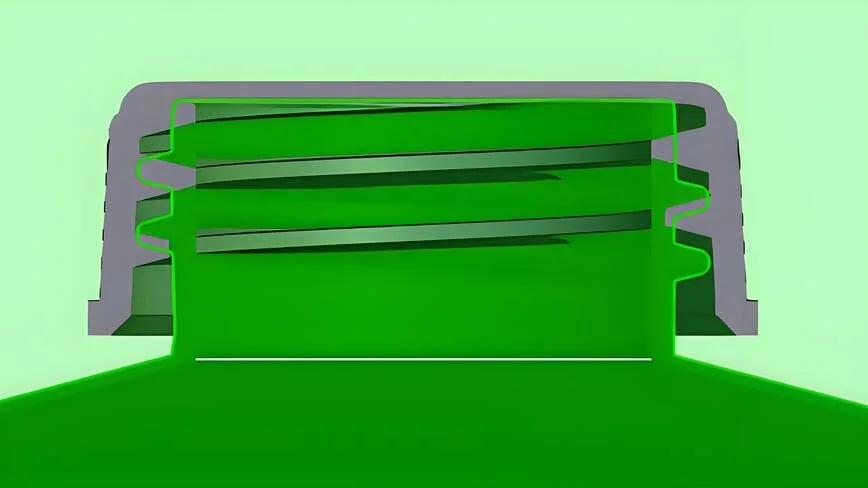
Precise Thread Design
Designing threaded molds begins with understanding the thread’s role and its specifications. Parameters such as pitch, tooth shape, and depth must be meticulously calculated to align with the intended application. This precision ensures that the threads function as expected without compromising the product integrity1.
For instance, a coarse thread may be suitable for applications requiring quick assembly, while a fine thread might be needed for tight seals. Additionally, the mold should be engineered to allow for consistent thread dimensions, minimizing variations that can lead to assembly issues.
Effective Demolding Mechanisms
The demolding phase poses unique challenges due to the threaded design. Unlike non-threaded parts, which can often be ejected straightforwardly, threaded components require special attention to prevent damage. Mechanisms like rotary demolding or slider systems are commonly employed to facilitate smooth ejection.
Each mechanism has its advantages; rotary demolding is ideal for continuous threads, while sliders can handle more complex geometries. Selecting the right method is crucial for maintaining thread quality2.
Material Selection
Choosing the appropriate material for the injection molding process significantly impacts the final product’s performance. Materials with high fluidity and low shrinkage rates are preferred as they fill the intricate thread details more effectively.
Polypropylene and nylon are popular choices due to their excellent moldability and strength. However, each project may require different material properties based on environmental conditions, such as temperature resistance3 or chemical exposure.
Balancing Design and Process Parameters
The interplay between design and process parameters cannot be overlooked. Temperature, pressure, and speed settings must be optimized to complement the mold design. This balance ensures complete filling of the thread cavities without introducing defects such as voids or misalignments.
In conclusion, understanding these key considerations in threaded mold design allows manufacturers to produce reliable, high-quality components that meet specific application demands.
Precise thread design prevents assembly issues.True
Accurate thread design ensures components fit correctly, avoiding misalignments.
Nylon is a poor choice for threaded mold material.False
Nylon is favored for its strength and moldability in threaded applications.
How Do Injection Molding Parameters Affect Thread Quality?
Achieving high-quality threads in injection molding requires precise control of various parameters.
Injection molding parameters such as temperature, pressure, and speed critically influence thread quality. Precise control ensures threads are formed correctly without defects. Adjusting these settings based on the specific material and design requirements is essential to produce durable and accurate threaded components.
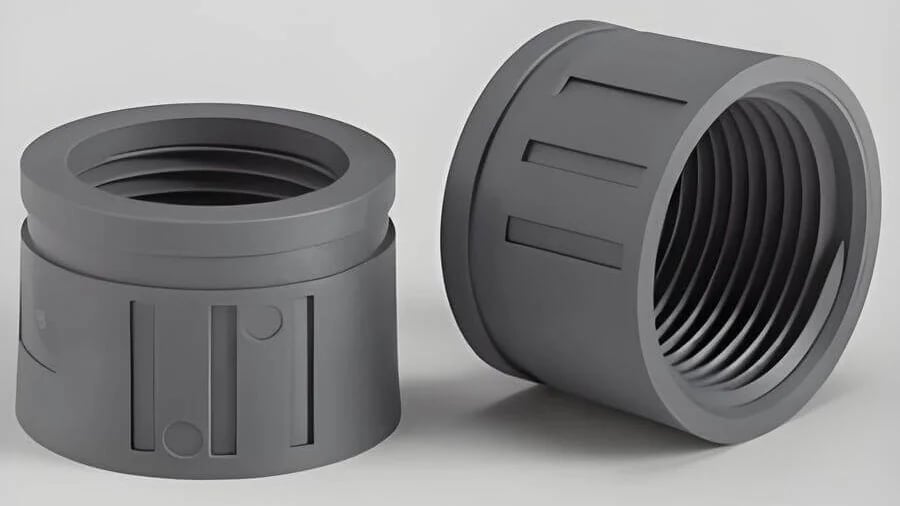
The Role of Temperature
Temperature plays a crucial role in determining the quality of molded threads4. Both the barrel temperature and the mold temperature must be carefully controlled. If the temperature is too low, the polymer may not flow adequately, leading to incomplete threads or poor surface finish. Conversely, excessive temperatures can cause material degradation, affecting the strength and appearance of the threads.
The Impact of Pressure
Injection pressure directly influences the ability to fill the mold cavity completely, especially in areas where threads are present. High pressure ensures that the molten material reaches every part of the mold, forming well-defined threads. However, excessively high pressure can lead to flash formation or damage to the mold, particularly in delicate thread structures.
Speed and Its Effects
Injection speed must be optimized to balance fill time and material shear rate. A slower speed might not generate sufficient flow to fill intricate thread details, while a higher speed could introduce defects like jetting or weld lines. It’s essential to find a middle ground that allows for smooth flow without compromising thread integrity.
Fine-Tuning for Specific Materials
Different polymers behave uniquely under varying injection molding conditions. For instance, thermoplastic elastomers5 may require lower temperatures and pressures compared to polycarbonate resins. Adjusting parameters to suit the specific material properties ensures that threads maintain their intended dimensions and performance characteristics.
Evaluating Threaded Mold Designs
The design of the threaded mold itself can influence how sensitive it is to parameter changes. Well-designed molds consider factors like draft angles and venting to accommodate variations in process settings. This adaptability helps maintain thread quality across different production runs, reducing scrap rates and improving overall efficiency.
High temperature degrades thread quality in injection molding.True
Excessive temperatures can cause material degradation, affecting thread strength.
Injection speed has no effect on thread quality.False
Speed affects flow and can introduce defects like jetting or weld lines.
What Challenges Might Arise During the Demolding Process?
Demolding can be a tricky part of injection molding, especially with threaded molds. What hurdles might you face?
The demolding process in threaded injection molding can present challenges such as increased resistance due to the thread geometry, potential product deformation, and the need for specialized demolding mechanisms. Ensuring smooth demolding requires careful mold design and the use of technologies like rotary or slider demolding systems.
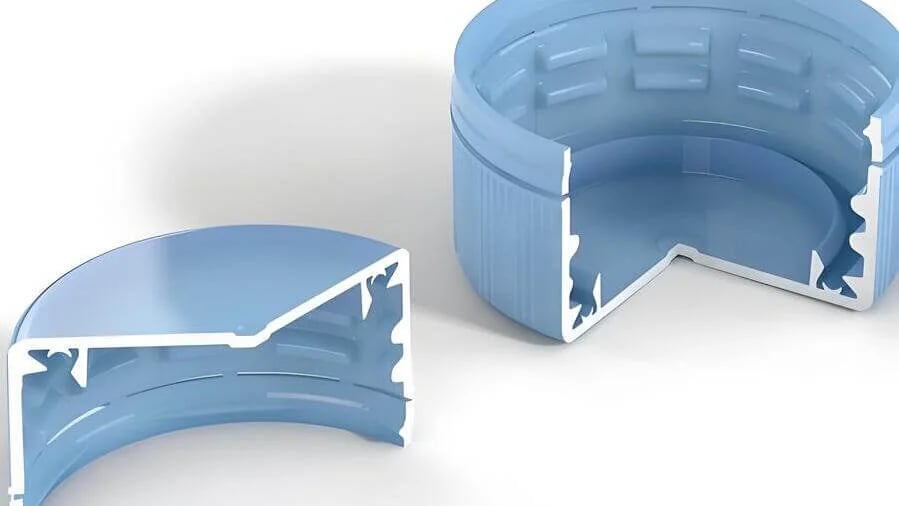
Thread Geometry and Resistance
Threaded molds inherently create a more complex surface area, which can increase friction during the demolding process6. The spiral nature of threads means that the mold must accommodate this geometry to avoid damaging the product upon ejection.
When the design doesn’t precisely align with the thread’s pitch and depth, it can lead to increased resistance. This resistance can cause the product to stick in the mold or deform, leading to defects or increased wear on the mold itself.
Specialized Demolding Mechanisms
To counteract these challenges, specialized mechanisms are often employed:
- Rotary Demolding: This involves rotating the mold components in sync with the thread’s pattern to gently release the part without excessive force.
- Slider Demolding: This mechanism uses sliders that move aside as the mold opens, allowing for easier release of complex thread geometries.
These systems require precise engineering and synchronization with the mold’s movement to prevent any damage to the thread during ejection.
Material Considerations
The choice of material is another critical factor in smooth demolding. Some plastics have higher shrinkage rates or more rigid properties, making them more challenging to demold without damage. Selecting materials with good flow properties and low shrinkage can help mitigate these issues.
To ensure a successful demolding process, both the material’s characteristics and the mechanical aspects of the mold must be harmonized. This includes choosing materials that complement the mold’s design and can withstand the forces applied during ejection.
Temperature and Cooling Rates
The cooling rate of the material also plays a significant role. If the material cools too quickly or unevenly, it can contract around the threads, increasing demolding difficulty. Optimizing temperature settings and ensuring uniform cooling can alleviate this problem by reducing stresses within the material.
By understanding these factors and implementing strategic solutions, manufacturers can effectively navigate the challenges of demolding in threaded injection molding.
Threaded molds increase demolding resistance.True
Thread geometry creates more surface area, increasing friction during demolding.
Rotary demolding damages thread patterns.False
Rotary demolding gently releases parts without excessive force, preventing damage.
Which Materials Are Best Suited for Threaded Injection Molding?
Choosing the right materials is crucial for successful threaded injection molding, ensuring durability and precision.
Materials such as polypropylene, nylon, and ABS are ideal for threaded injection molding. They offer excellent flow properties, dimensional stability, and strength, making them suitable for producing intricate threaded components. Selecting the right material depends on the specific requirements of the product, such as thermal resistance, flexibility, and load-bearing capacity.
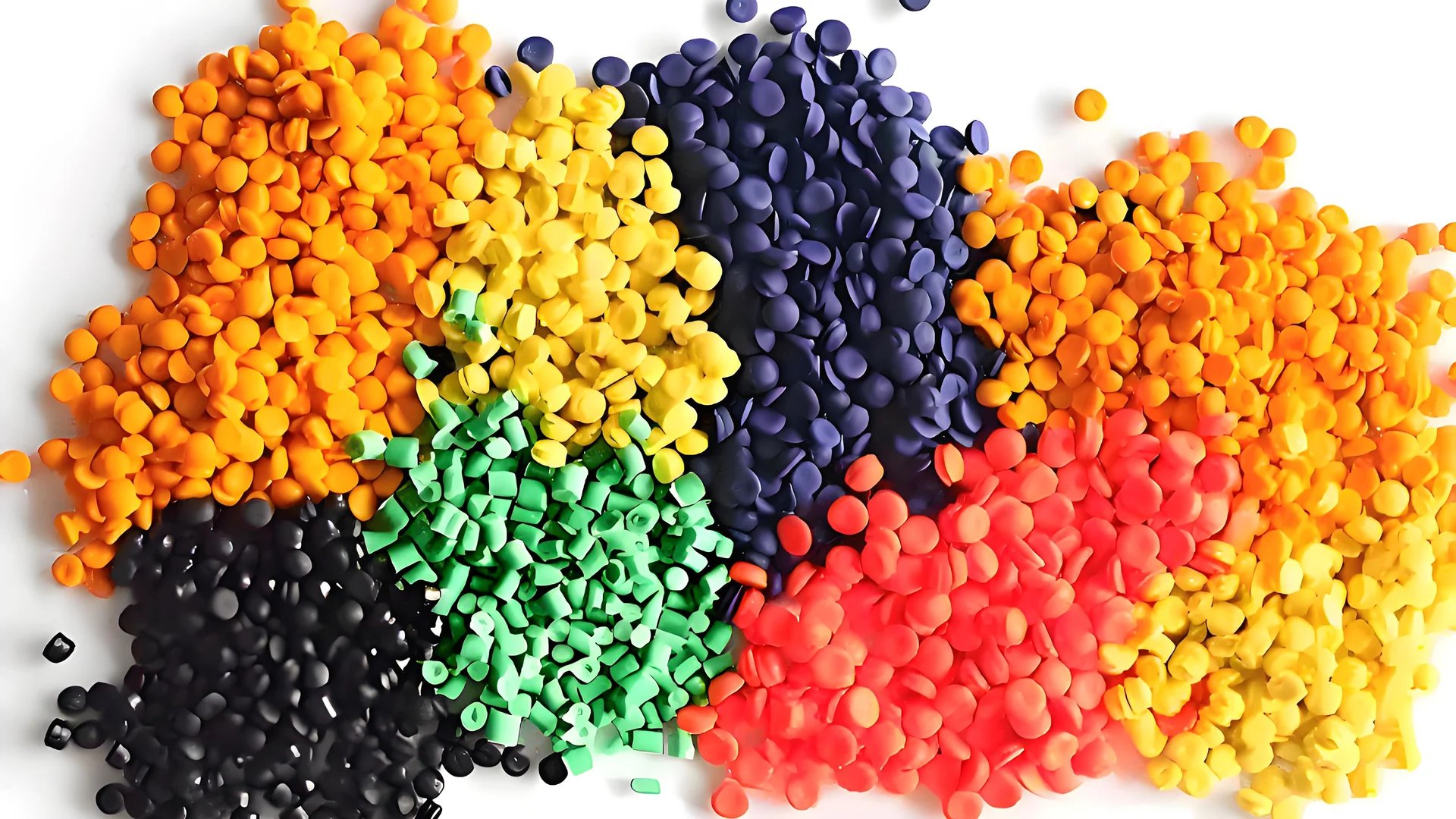
Importance of Material Selection
The selection of materials for threaded injection molding7 is crucial because it influences the final product’s quality, performance, and cost-effectiveness. Choosing a suitable material affects not only the molding process but also the part’s end-use functionality.
Key Material Properties
-
Flowability: Materials with high flowability ensure that the molten plastic fills the intricate threaded sections of the mold efficiently. This reduces the risk of voids and ensures uniformity.
-
Thermal Resistance: For applications requiring exposure to heat, materials like polycarbonate or high-temperature nylons are preferred due to their ability to withstand high temperatures without deforming.
-
Dimensional Stability: Materials such as ABS (Acrylonitrile Butadiene Styrene) and polypropylene are known for maintaining their shape and size after cooling, which is essential for maintaining thread accuracy.
-
Toughness and Flexibility: Some applications may require materials that provide a balance between toughness and flexibility. Nylon is often used due to its excellent mechanical properties and resilience.
Popular Materials for Threaded Injection Molding
Material | Characteristics | Applications |
---|---|---|
Polypropylene | Good chemical resistance, low density | Containers, automotive parts |
Nylon | High tensile strength, wear resistance | Gears, bearings |
ABS | Impact resistance, easy to process | Consumer goods, electronics |
Polycarbonate | High impact strength, transparent | Optical disks, eyewear |
Considerations Based on Application
When selecting materials for threaded injection molding, it’s essential to consider the end-use conditions:
- Chemical Exposure: If the product will be exposed to chemicals, materials like polypropylene or nylon should be chosen for their excellent chemical resistance.
- Load-Bearing Requirements: For parts that must bear loads or stress, opt for materials with high tensile strength such as nylon.
Industry Examples and Case Studies
In the automotive industry, nylon8 is often used for components that require high strength and wear resistance. Similarly, consumer electronics frequently employ ABS due to its easy processing and aesthetic finish.
By understanding these material properties and application needs, manufacturers can optimize their injection molding processes to produce high-quality threaded components efficiently.
Polypropylene has low thermal resistance.True
Polypropylene is known for its chemical resistance but not high thermal resistance.
Nylon lacks dimensional stability in molding.False
Nylon is recognized for its excellent mechanical properties and dimensional stability.
Conclusion
In conclusion, injection molding machines can indeed handle threaded molds, provided the design, process, and materials are meticulously optimized. With the right approach, manufacturers can achieve excellent results.
-
Precise thread design ensures functional and high-quality molded parts.: Just carefully consider thread size and pitch when designing your part to avoid threads that might strip more easily than metal counterparts. ↩
-
Explore effective demolding techniques to prevent damage to threaded parts.: Demoulding mechanism for threaded products of injection mould · 1) The Huff die is used for external threads; · 2) The flap-type core mold is … ↩
-
Discover materials best suited for producing durable threaded components.: Learn how to select the right material for your injection molding design with this technical overview of thermoplastic resins. ↩
-
Discover how temperature impacts thread quality in molding processes.: A temperature control system consists of three components: the mould, the temperature control unit and a heat transfer medium. Certain conditions have to be … ↩
-
Explore how thermoplastic elastomers affect molding parameters.: Another difference is that TPEs can be processed on conventional injection molding machines. The resin is heated beyond its melting point, … ↩
-
Learn about common challenges in demolding threaded parts.: (1) There is no demoulding angle on the top and bottom of tooth. (2) Tooth surface is not polished enough or surface is rusted. (3) Tooth … ↩
-
Discover why certain plastics excel in threaded injection molding.: Large volume industrial injection molds are made from steel. Short run or prototype can be made from aluminum. The difference is how long you’d expect one to … ↩
-
Explore how nylon is utilized in automotive components.: The largest nylon market today, with more than 40% of the total demand, is in automobiles and transportation equipment. Recently, the use of plastics in … ↩