Injection molding shapes our everyday lives in ways we often overlook—let’s explore how it impacts plastic thickness!
The injection molding process significantly affects plastic part thickness through variables such as injection pressure, time, holding pressure, mold temperature, melt temperature, and gate design. These factors influence fill capacity, shrinkage, and uniformity, critical for achieving design specifications.
But there’s so much more beneath the surface! Join me as we dive deeper into each factor that can help optimize your designs and processes.
Insufficient injection pressure leads to thinner plastic parts.True
Low pressure causes incomplete cavity filling, reducing part thickness.
What Role Does Injection Pressure Play in Part Thickness?
Injection pressure is a crucial parameter that influences the thickness and quality of plastic parts in injection molding.
Injection pressure directly impacts the thickness of plastic parts by controlling the flow of molten material into the mold. Insufficient pressure leads to thinner parts, especially in complex areas, while excessive pressure can cause defects like local thinning or flash, affecting the part’s dimensional accuracy.

Understanding Injection Pressure
Injection pressure refers to the force applied to the molten plastic as it is injected into the mold cavity. This pressure determines how well the cavity is filled and, consequently, the final thickness of the molded part.
Insufficient Injection Pressure
When injection pressure is too low, the molten plastic struggles to fill the entire mold cavity. This issue is particularly evident in areas far from the gate or in molds with intricate designs. For instance, manufacturing large parts with low injection pressure may result in insufficient thickness at the edges or center due to incomplete filling. This can lead to parts that do not meet design specifications, impacting performance and reliability.
Effects of Excessive Injection Pressure
Conversely, excessive injection pressure can cause the plastic melt to move too quickly through the cavity. This rapid movement might lead to issues such as breaking through weaker sections of the part, resulting in localized thinning or defects like flash around the edges. Such problems can compromise the overall dimensional accuracy of the plastic part.
Balancing Injection Pressure for Optimal Thickness
Achieving the correct balance in injection pressure is vital. It requires careful consideration of factors such as mold design1, material type, and part complexity. Engineers must conduct thorough simulations and tests to determine the optimal pressure settings that ensure uniform thickness without introducing defects.
Injection pressure plays a pivotal role in ensuring parts meet their intended specifications by influencing how thoroughly and uniformly a mold is filled. By understanding and correctly adjusting this parameter, manufacturers can produce high-quality parts with consistent thickness and minimal defects.
High injection pressure causes flash defects.True
Excessive pressure can lead to flash, affecting part accuracy.
Low injection pressure ensures uniform thickness.False
Insufficient pressure leads to incomplete filling and uneven thickness.
How Do Holding Pressure and Time Influence Thickness?
Understanding the role of holding pressure and time is crucial in achieving desired part thickness in injection molding.
Holding pressure and time are critical in determining plastic part thickness. Adequate holding pressure compacts the melt, reducing shrinkage and ensuring dimensional accuracy. Similarly, holding time allows complete solidification, preventing shrinkage and defects like depressions. Both factors need careful calibration to balance quality and efficiency.
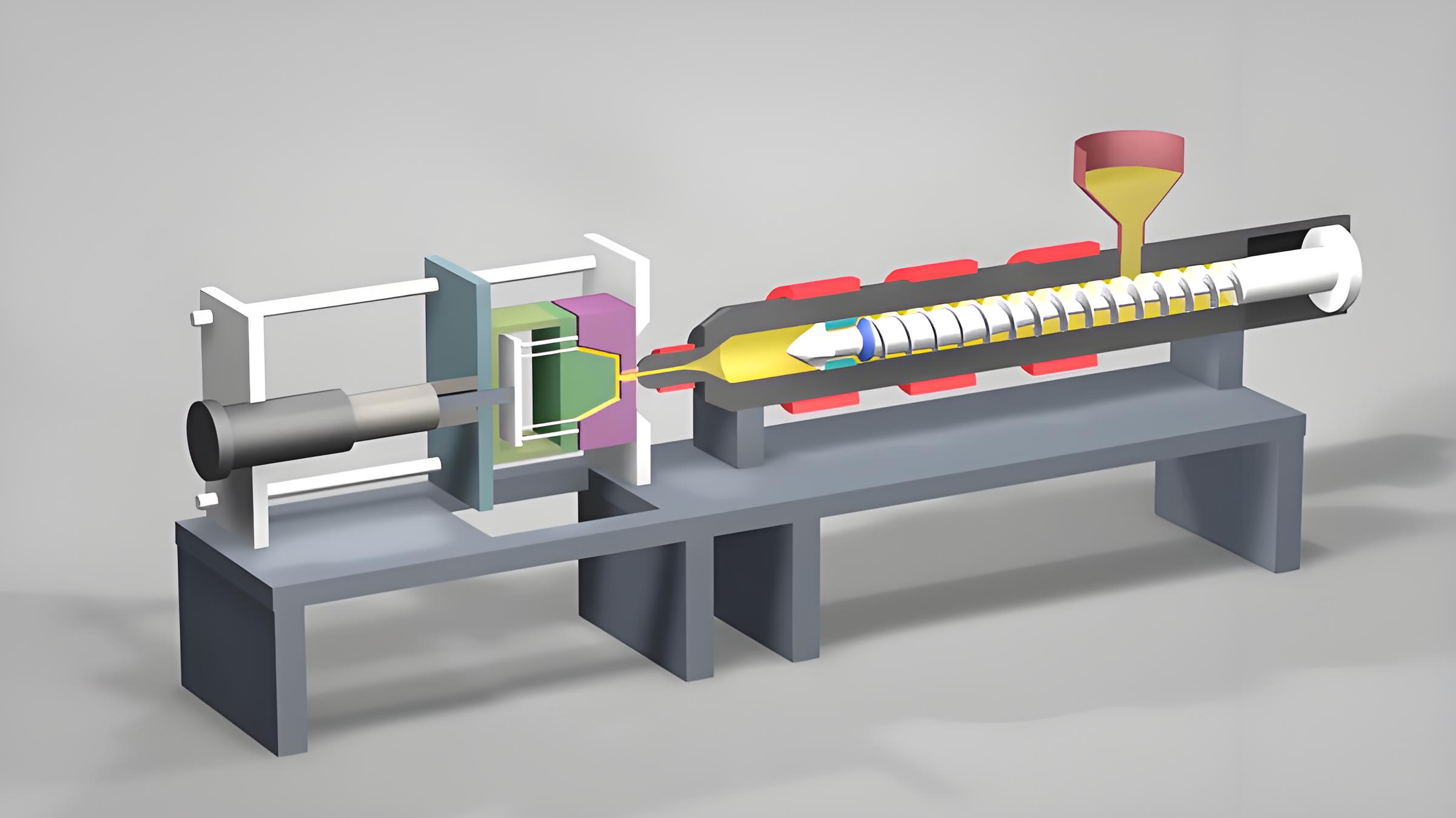
The Role of Holding Pressure
Holding pressure is applied once the initial injection phase fills the mold cavity. This pressure ensures the molten plastic remains compacted within the mold, compensating for any material shrinkage that occurs as the part cools and solidifies.
-
Insufficient Holding Pressure: When holding pressure is too low, the plastic may shrink excessively during cooling, leading to thinner parts that fail to meet design specifications. This is particularly problematic in areas further from the gate where pressure loss is more significant. For example, large automotive components require consistent pressure to avoid varying thicknesses across the part.
-
Excessive Holding Pressure: On the other hand, too much pressure can lead to issues such as flash—a thin layer of excess material along the parting line of the mold—due to excessive force on the mold. This might also cause stress within the plastic, leading to warping or cracking post-production.
Importance of Holding Time
Holding time determines how long the holding pressure is applied after the mold is filled. It ensures that the part maintains its shape and thickness until it cools enough to be removed from the mold.
-
Short Holding Time: If the holding time is insufficient, the plastic may begin to shrink before it has fully solidified, leading to defects such as sink marks or voids, which compromise both appearance and structural integrity.
-
Extended Holding Time: While a longer holding time can enhance dimensional stability and minimize thickness variation, it can also reduce production efficiency by increasing cycle time. Additionally, extended holding may induce residual stresses that could result in post-molding deformations.
Balancing Quality and Efficiency
To achieve optimal results, manufacturers must balance holding pressure2 and time with other parameters like mold and melt temperatures. For instance, higher temperatures may require adjustments in pressure and time settings to maintain quality without sacrificing efficiency.
Example Table: Influence of Holding Parameters on Part Quality
Parameter | Low Setting Impact | High Setting Impact |
---|---|---|
Holding Pressure | Shrinkage, thin parts | Flash, internal stress |
Holding Time | Sink marks, voids | Increased cycle time, residual stress |
In conclusion, fine-tuning these parameters based on specific material properties and part design is essential for producing high-quality plastic components in injection molding. By understanding these nuances, manufacturers can better predict outcomes and adjust processes accordingly.
Holding pressure reduces part shrinkage.True
Adequate holding pressure compacts the melt, reducing shrinkage.
Extended holding time decreases production efficiency.True
Longer holding time increases cycle time, reducing efficiency.
Why Is Mold Temperature Critical for Thickness Control?
Mold temperature is a crucial factor in injection molding, directly impacting the thickness and quality of plastic parts.
Mold temperature affects plastic part thickness by influencing melt cooling rate, fluidity, and shrinkage. Optimal mold temperature ensures consistent thickness, avoiding defects like uneven fill or excessive shrinkage, which can compromise design specifications and part performance.

The Role of Mold Temperature in Cooling and Fluidity
The temperature of the mold3 plays a pivotal role in determining how quickly the plastic melt cools once injected into the cavity. If the mold temperature is too low, the melt cools rapidly, which increases viscosity and reduces fluidity. This makes it difficult for the melt to fill the cavity fully, leading to thinner sections, especially in intricate or distant areas of the mold.
Conversely, if the mold temperature is too high, it slows down the cooling process. While this may seem beneficial for filling, it can result in excessive shrinkage as the part cools outside the mold. Such shrinkage often leads to parts that exceed the designed thickness, impacting both aesthetics and functionality.
Balancing Mold Temperature for Optimal Results
Finding the right balance in mold temperature is crucial for ensuring uniform thickness across a plastic part. Ideally, the mold temperature should be high enough to allow complete cavity filling but low enough to prevent excessive shrinkage and cycle time extension. This balance ensures that the part adheres closely to its design specifications without unnecessary material usage or increased production costs.
Mold Temperature | Effect on Part Thickness | Potential Issues |
---|---|---|
Too Low | Thinner sections; poor fill | Material shortage, unevenness |
Optimal | Consistent thickness | Stable dimensions |
Too High | Excessive thickness/shrinkage | Extended cycles, high costs |
Impact on Production Cycle and Costs
Maintaining an optimal mold temperature not only influences part quality but also affects production efficiency. A higher than necessary mold temperature will increase cycle times due to prolonged cooling periods, raising energy consumption and production costs. On the other hand, too low a temperature may necessitate additional processing steps to correct defects, further impacting cost-effectiveness.
Understanding these nuances helps manufacturers optimize their injection molding processes4 to achieve desired outcomes with minimal waste and cost.
Optimal mold temperature prevents excessive shrinkage.True
Correct mold temperature ensures parts adhere to design without extra shrinkage.
High mold temperature reduces production costs.False
Higher temperatures increase cycle times, raising energy use and costs.
How Does Gate Design Affect Uniformity in Thickness?
Gate design is crucial in ensuring uniform thickness in plastic parts produced by injection molding. A well-designed gate can optimize flow and fill.
Gate design influences thickness uniformity by determining flow rate and distribution of the plastic melt within the mold cavity. Proper gate size and placement ensure even flow, preventing thickness variations in the final product.

The Impact of Gate Size on Flow
In the injection molding process, the size of the gate plays a critical role in controlling the flow of plastic melt into the mold cavity. A small gate size5 restricts the flow, slowing down the entry of the melt and potentially leading to thinner sections of the plastic part, particularly in areas far from the gate or in complex geometries. On the other hand, a larger gate size allows for a more robust flow, enhancing the fill and potentially improving thickness uniformity.
Gate Size | Impact |
---|---|
Small | Restricted flow; thinner sections |
Large | Robust flow; improved uniformity |
Optimal Gate Placement for Uniformity
The position of the gate is equally important. Improper placement, such as positioning the gate too close to an edge or corner, can lead to uneven flow patterns within the mold cavity. This irregularity often results in differences in thickness across the part. Ideally, gates should be placed in positions that promote symmetrical filling, ensuring consistent pressure and temperature across the entire part.
For example, centrally located gates help achieve uniform radial flow, reducing variations in wall thickness. For complex parts, multiple gates or hot runner systems can be employed to maintain a balanced fill.
Balancing Multiple Factors
While gate design is pivotal, it must be considered alongside other factors such as injection pressure and mold temperature. A high melt temperature6, for example, can compensate for smaller gate sizes by enhancing fluidity, but it also risks material degradation if not managed correctly. Conversely, lower temperatures might require larger gates to achieve similar results without sacrificing part quality.
Case Study: Large Part Injection Molding
Consider a scenario where a large plastic part is produced with a small gate size. The restricted flow might cause insufficient filling, leading to thinner sections at the extremities. By redesigning the gate to a larger size or relocating it to a more central position, manufacturers can achieve better thickness uniformity across the part.
In conclusion, careful consideration of gate size and placement is vital for achieving uniform thickness in injection-molded parts. Optimizing these factors ensures better control over flow dynamics and enhances the quality of the finished product.
Large gate size improves thickness uniformity.True
A larger gate size allows robust flow, enhancing fill and uniformity.
Improper gate placement leads to even flow patterns.False
Improper placement causes irregular flow, resulting in thickness differences.
Conclusion
Mastering these aspects of injection molding can significantly enhance the quality of your plastic parts. Embrace these insights to elevate your designs to new heights!
-
Mold design intricacies impact fill quality, influencing final part thickness.: The quality and make of the mold allows injection molders to ensure high tolerance, identify defects, maintain precision, choose the right raw materials, as … ↩
-
Explore how holding pressure affects plastic part consistency.: Holding pressure means that the screw does not immediately retract after injection but continues to apply pressure to the molten material at the … ↩
-
Learn about setting optimal temperatures for precise part molding.: An optimal setting at 50℃ ensures balanced flow and solidification. … PPS can withstand high temperatures, making it suitable for demanding applications. POM, … ↩
-
Explore methods to reduce costs while maintaining quality.: 9 Tips to Reduce Injection Moulding Costs … Using a core cavity, as shown, can be a cost-effective method of moulding tall walls and ribbed surfaces. ↩
-
Explore how gate size directly impacts plastic flow and part uniformity.: This is because the gate size determines the shear stress molten plastic will experience as it fills out your part. ↩
-
Learn about balancing melt temperature with gate design for optimal results.: This high melt temperature to low mold temperature ratio often results in compromised part properties and an unstable part. ↩