Ever wondered why injection molding is the go-to choice for so many manufacturers? Let me share why it captivates my imagination.
Injection molding is fast and cost-effective due to automation, short cycle times, and efficient material use, reducing costs significantly. Its high production rates make it ideal for large-scale manufacturing, supporting strong business outputs.
As I explored the world of manufacturing, I often felt amazed by how injection molding works. Machines perform tasks like a well-rehearsed dance. Automation levels are truly high. Machines do everything from heating to cooling plastic with little human help. I once visited a factory where machines worked non-stop for hours. They produced parts almost on their own. The molding cycle is very short. For thin items, it takes just seconds. This rapid pace seems magical with the large quantities produced.
Cost-effectiveness really stands out to me. Initial investment in molds might be big. However, with mass production, that cost spreads over many units. I recall projects with thousands of components made. Each piece became much cheaper. Material use is also impressive, with almost every scrap recycled and reused. This saves money and cuts down waste. Manufacturers and the planet both benefit!
Injection molding has short cycle times for production.True
Short cycle times in injection molding enhance efficiency, allowing rapid production of large quantities of parts.
Injection molding is only suitable for small-scale manufacturing.False
Contrary to this claim, injection molding is ideal for large-scale manufacturing due to its efficiency and cost-effectiveness.
What are the key advantages of automation in injection molding?
Have you ever thought about how automation changes the world of injection molding? Let’s explore the advantages of this technology. It is a real game-changer for manufacturers like us. Efficiency and cost-effectiveness come together in ways we never imagined before.
Automation in injection molding enhances efficiency, reduces cycle times, lowers costs, and improves material usage, revolutionizing manufacturing processes.
Efficient Production Method
I was really surprised by how much automation helps in injection molding when I first learned about it. Injection molding machines autonomously handle tasks, from moving plastic materials to removing finished products. This innovation was truly groundbreaking. I have seen machines work for hours without needing supervision. This shift allows operators like myself to focus on monitoring and adjusting operations instead of constant manual oversight. It is a refreshing change.
Picture a modern facility where a machine continuously produces plastic products based on its programming. It feels like being part of a well-functioning system. The efficiency gained is amazing and is a reason why many companies welcome this technology.
Short Molding Cycle
A thrilling part of injection molding automation is the speed of the cycle. For smaller, thin-walled products, cycles last only a few seconds. Technologies like hot runner molds keep plastic in a molten state, allowing us to fill molds quickly. Seeing products come out of machines at high speed remains exciting. Innovations in mold cooling design shorten the cycle while maintaining quality.
Cost Advantage Factors
Let’s explore the financial benefits. Automation drastically cuts production costs using batch production cost sharing. Once, our team invested in an expensive, complex mold. At first, it was intimidating, but mass production spread the mold’s cost over thousands of units. Each product became more affordable. It was a wise investment that really paid off.
High material usage rates were a nice shock. Automated systems maintain precise injection control, minimizing waste and creating recycling opportunities. This conserves resources and lowers raw material costs. It is always a win!
Summary of Key Advantages
In summary, automating injection molding really changes manufacturing for the better. By using this technology, we increase operational efficiency and enjoy cost savings through optimized resource use and reduced waste. I have seen firsthand that faster production cycles and lower costs do not lower quality. Automation is an appealing choice for anyone in modern manufacturing.
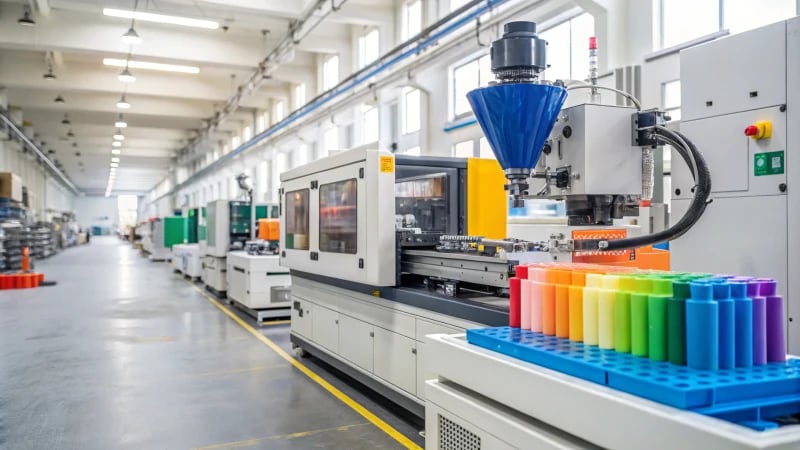
Main Benefits of Automation in Injection Molding
The main benefits of automation in injection molding are very impressive. Automation uses efficient production processes. These processes probably reduce human errors. They also lower cycle times. Productivity really increases. Companies save a lot of money with good resource management. Trust me; these changes can really transform manufacturing.
Efficient Production Method
Automation in injection molding significantly boosts production efficiency. With a high degree of automation, the injection molding machine can autonomously execute multiple tasks such as conveying plastic raw materials, heating, melting, injection filling, pressure holding, cooling, and demolding.
This automation minimizes human intervention, allowing operators to focus mainly on monitoring and minor adjustments. For instance, in a modern facility, a single injection molding machine can operate continuously for hours without supervision, ensuring that production runs smoothly and efficiently.
Short Molding Cycle
The injection molding cycle is notably short, especially for small and thin-walled products. The efficiency of the injection system and rapid mold cooling contribute to cycle times that can range from just a few seconds to over ten seconds.
Utilizing advanced technologies like hot runner molds keeps the plastic melt in a molten state, enhancing production speed. This innovation allows faster filling and solidification processes, thus shortening the overall cycle time. Check out this in-depth analysis1 of how mold technologies are changing production.
Cost Advantage Factors
One of the key benefits of automation is the reduction in production costs through batch production cost sharing. Although initial mold costs may be high, they are distributed across a large volume of products, leading to lower costs per unit.
Cost Factors | Explanation |
---|---|
Mold Production Cost | High initial costs but shared across many units reduces unit cost. |
High Material Utilization | Accurate injection volume minimizes waste and allows recycling of scraps. |
Additionally, high material utilization rates lead to reduced raw material expenses. Automated systems ensure precise control over injection volumes, significantly minimizing material waste and allowing for recycling of scraps, which further cuts costs.
Summary of Key Advantages
To summarize, the automation of injection molding processes not only enhances operational efficiency but also offers significant cost savings through optimized resource use and minimized waste. By leveraging technology, manufacturers can achieve faster production cycles and lower costs while maintaining high-quality standards. These advantages make automation a compelling choice for modern manufacturing environments.
Automation boosts efficiency in injection molding processes.True
Automated injection molding machines execute tasks autonomously, enhancing production efficiency and reducing the need for human intervention.
Short molding cycles are achieved through advanced technologies.True
Technologies like hot runner molds significantly reduce cycle times, allowing for faster filling and solidification of products in injection molding.
How Does the Short Molding Cycle Affect Production Efficiency?
Do you ever think about how a short molding cycle changes production efficiency? Reducing cycle time leads to many benefits for manufacturers. It is fascinating. This simple change can have big effects.
Short molding cycles enhance production efficiency by reducing cycle times and costs, improving material usage, and increasing automation and output.
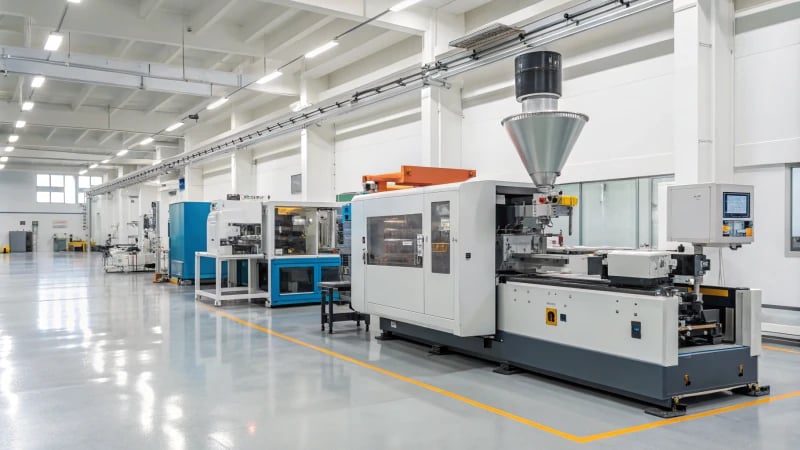
Understanding the Short Molding Cycle
The effect of short molding cycles in injection molding feels like finding a secret power in manufacturing. When I first learned about this process, I realized its role in increasing production efficiency.
Typically, the cycle encompasses several stages: injection, pressure holding, cooling, mold opening, and ejection. Each of these phases is designed to be as quick as possible, particularly for small and thin-walled products. For instance, a molding cycle can take anywhere from a few seconds to over ten seconds,
which is significantly shorter than traditional manufacturing processes. This efficiency is largely attributed to advanced technologies such as high-performance injection systems and rapid cooling mechanisms.
The Role of Automation in Short Molding Cycles
Automation has transformed production efficiency for me. One of the most significant advantages of short molding cycles is the integration of automation into the production process.
- High Degree of Automation: Automation means fewer mistakes. It increases consistency and quality, enabling high-scale production. Machines perform complex tasks with very little human involvement. I remember visiting a modern factory where machines produced products for hours without stopping.
- Continuous Operation: Automated systems allow non-stop production, raising output without ongoing manual work. Watching production increase is thrilling.
This automation not only streamlines the process but also mitigates risks associated with human errors, ultimately improving the overall efficiency of production.
Cost Efficiency Through Short Molding Cycles
Short molding cycles bring big cost savings that enhance production efficiency.
Cost Factor | Explanation |
---|---|
High Material Utilization | Efficient injection molding controls injection volume precisely. This reduces waste, allowing even recycling of materials. It benefits budget and sustainability. |
I have worked on projects using recycled plastics, which lower costs and support sustainability. This is something I really care about.
Enhanced Production Output
Each second saved in the cycle boosts production significantly.
- Faster Turnaround Times: Quick cycles mean faster production times, allowing us to deliver products swiftly. This speed is essential when demand increases suddenly.
- Scalability: Rapidly scaling operations without big investments is transformative. I have seen companies succeed by adapting quickly to market demands.
This ability to ramp up production quickly helps businesses stay competitive in fast-paced markets.
Conclusion on Short Molding Cycle Benefits (No Conclusion Yet)
Short molding cycles have a deep impact on production efficiency. There is much more to learn about short molding cycles . Understanding these cycles allows manufacturers to make smart decisions about optimizing their injection molding processes.
Short molding cycles reduce production time significantly.True
Short molding cycles streamline the manufacturing process, allowing for faster production times and increased output.
Automation in short molding cycles decreases product quality.False
In fact, automation enhances consistency and reduces errors, improving overall product quality during short molding cycles.
How Does Material Utilization Affect Overall Costs?
When I first entered the world of manufacturing, I quickly realized that using materials wisely is not just a technical term. It is vital for reducing costs in production. Let’s explore how this idea affects profits.
Efficient material utilization minimizes production waste and raw material expenses, leading to enhanced efficiency and increased profitability in manufacturing processes like injection molding.
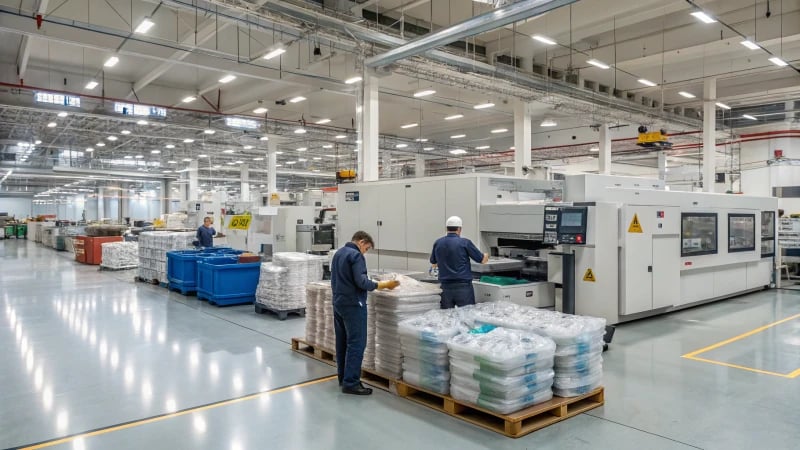
Understanding Material Utilization
Material usage is more than just a catchy term; it’s essential for manufacturing success. I remember starting in product design. Back then, each penny spent on materials felt heavy on my shoulders. Using raw materials efficiently helps businesses lower costs. It also supports a sustainable manufacturing approach.
Material utilization refers to how effectively raw materials are used in the manufacturing process. High material utilization not only reduces waste but also contributes significantly to overall production costs. For manufacturers, the goal is to achieve optimal utilization rates to minimize costs while maximizing output.
For instance, in injection molding, the ability to control the injection volume precisely ensures that the right amount of plastic is used for each product. This efficiency leads to lower expenses associated with raw material procurement. Additionally, any waste generated, such as gates and runners, can often be recycled and reused, further enhancing material utilization.
The Role of Efficient Production Methods
Efficient production methods improve material use. Automated processes like injection molding amazed me. They boosted production efficiency. These machines do many tasks – from moving raw materials to cooling products. All this happens with little human help.
Example: I saw an advanced injection molding factory where machines worked for hours, producing endless units without breaks. It was like watching a perfect machine in action. Lower labor and efficient machines reduced the company’s costs.
Efficient production methods play a crucial role in material utilization. Automated processes like injection molding allow for high accuracy and consistency in production. These methods can reduce the cycle time of production, enabling manufacturers to produce large quantities quickly without sacrificing quality.
Cost Advantage Factors
The cost benefits of great material use are big. At first, mold investment seems huge; however, when mass production begins, the mold cost is shared among many products.
Cost Factor | Explanation |
---|---|
Batch Production Cost Sharing | The mold cost is distributed across all units produced, drastically reducing the cost per unit. A mold that costs tens of thousands can yield millions of products. |
High Material Utilization | Precise control over injection volumes minimizes waste and allows for recycling of excess materials, further lowering raw material costs. |
Implications of Rising Raw Material Prices
Today’s changing market brings higher material prices; this is a major challenge for manufacturers who must change their strategies to stay profitable. Optimizing material usage is crucial.
As raw material prices fluctuate, manufacturers must adapt their strategies to maintain profitability. Effective material utilization becomes more critical in this context. By optimizing processes and minimizing waste, companies can cushion themselves against rising costs.
For example, implementing advanced technologies such as hot runner systems can help maintain molten plastic in the runners, preventing waste and speeding up the overall production process. This not only preserves resources but also enhances production efficiency.
For those interested in optimizing material use in manufacturing, explore advanced strategies2 that can help mitigate costs effectively.
High material utilization reduces overall production costs.True
Maximizing raw material efficiency minimizes waste, leading to lower expenses in manufacturing processes, thus reducing overall production costs.
Inefficient production methods increase material waste.True
Using outdated or manual processes often leads to higher waste rates, which directly raises costs and reduces profitability for manufacturers.
Which Industries Truly Thrive with Injection Molding Techniques?
Have you ever thought about how some industries easily produce excellent products? That’s the magic of injection molding! This fascinating process helps many sectors create top-quality items. Let me guide you through these industries that benefit greatly from it.
Injection molding is vital for industries such as automotive, consumer electronics, medical devices, packaging, and aerospace, offering efficient, cost-effective production and effective material use.
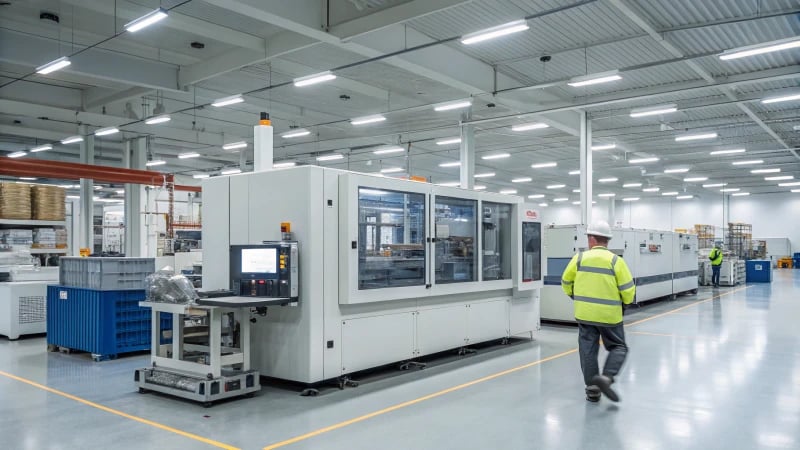
Automotive Industry
The automotive industry really benefits from injection molding. Parts like dashboards, bumpers, and interiors are made with precision. I once visited a car plant and saw parts made at incredible speed.
Lightweight plastic components are an advantage. They reduce vehicle weight and improve fuel efficiency. This is important in today’s eco-conscious world. Injection molding automation speeds up production and helps meet the high demand in this industry.
Consumer Electronics
Injection molding plays a big role in consumer electronics. Your smartphone or tablet case is made using this technique. When I unbox a gadget, I admire its design and functionality, made possible by injection molding.
The technique allows quick and efficient production of complex designs. Advanced mold technologies give design flexibility, enabling the production of unique ideas quickly. Learn more about design flexibility3.
Medical Devices
Precision is very important in the medical field. Injection molding helps create components for syringes, inhalers, and surgical tools. Each piece must meet strict safety standards.
I have witnessed how injection molding’s speed and accuracy ensure reliable medical products. In an industry where quality saves lives, strict quality controls matter greatly. Explore quality control measures4.
Packaging Industry
Let’s consider the packaging sector. Injection molding has changed how containers, bottles, and caps are made. Quick molding cycles help companies respond to market demands, which is necessary today.
Packaging companies can innovate and follow trends while producing large quantities efficiently. This responsiveness enables them to adapt their products faster than competitors. See trends in packaging innovation5.
Aerospace Industry
The aerospace industry uses injection molding for lightweight yet strong materials. Components for aircraft interiors and exteriors rely on this method.
Cost savings with injection molded parts over time are significant, especially when considering long-term durability under extreme conditions that offer performance advantages as well as safety benefits for aerospace applications. Understand aerospace applications6.
In summary, in automotive, consumer electronics, medical devices, packaging or aerospace, injection molding changes the game by boosting efficiency and reducing costs.
The automotive industry heavily relies on injection molding.True
Injection molding is crucial for producing complex automotive parts efficiently, enhancing vehicle performance and reducing weight.
Consumer electronics do not benefit from injection molding techniques.False
Contrary to this claim, consumer electronics use injection molding for creating durable and detailed plastic housings.
Conclusion
Injection molding combines automation with short cycle times and efficient material use, resulting in significant cost savings and high production rates for manufacturers.
-
Discover how automation can enhance your injection molding process and lead to significant cost savings. ↩
-
Understanding these strategies will enhance your knowledge of cost-saving practices in manufacturing. ↩
-
Discover how different industries leverage injection molding for efficiency and cost savings. ↩
-
Explore how injection molding impacts production in consumer electronics. ↩
-
Learn about the role of injection molding in medical device manufacturing. ↩
-
Find out how injection molding shapes modern packaging solutions. ↩