Have you ever thought about how those shiny plastic items are made? Let’s explore the amazing world of injection molding together!
Injection molding melts raw materials using a smart injection system. The system includes a barrel, screw and accurate temperature controls. This process helps thermoplastic materials reach their melting points. Uniform heating occurs, leading to great production quality.
When I started my path in manufacturing, I quickly discovered that injection molding is an amazing process. The process begins with a complex injection system made up of a barrel, screw and nozzle. Imagine the barrel as a warm oven for plastic materials. Heat changes them from solid to liquid. Each plastic type melts at its own temperature. I remember learning that polypropylene melts between 160-220℃. This was a big realization. Precise temperature can really change the final product.
The screw turns inside the barrel and does an important job. I was truly fascinated watching it move and mix the plastic. It creates heat by shearing, melting the plastic well. This magic really happens in the temperature control system. Nobody likes burnt plastic ruining their work!
These parts work together in harmony. This technology lets us produce high-quality molded parts.
Injection molding uses precise temperature controls for melting.True
Temperature controls in injection molding ensure uniform heating of thermoplastic materials, crucial for effective melting and production quality.
The injection molding process involves a cooling phase after melting.True
After melting, injection molding includes a cooling phase to solidify the material into the desired shape before ejection.
What are the key components of an injection molding machine?
Have you ever wondered how an injection molding machine works? Knowing its main parts could really change the game for those in manufacturing. This knowledge was truly important for me when I began.
The main parts of an injection molding machine include the injection system, which has a barrel, screw and nozzle. These parts are essential. Characteristics of plastic materials are important in the process. A precise temperature control system also plays a very crucial role. It keeps the right conditions for melting and molding. The system keeps everything steady and allows for perfect results.
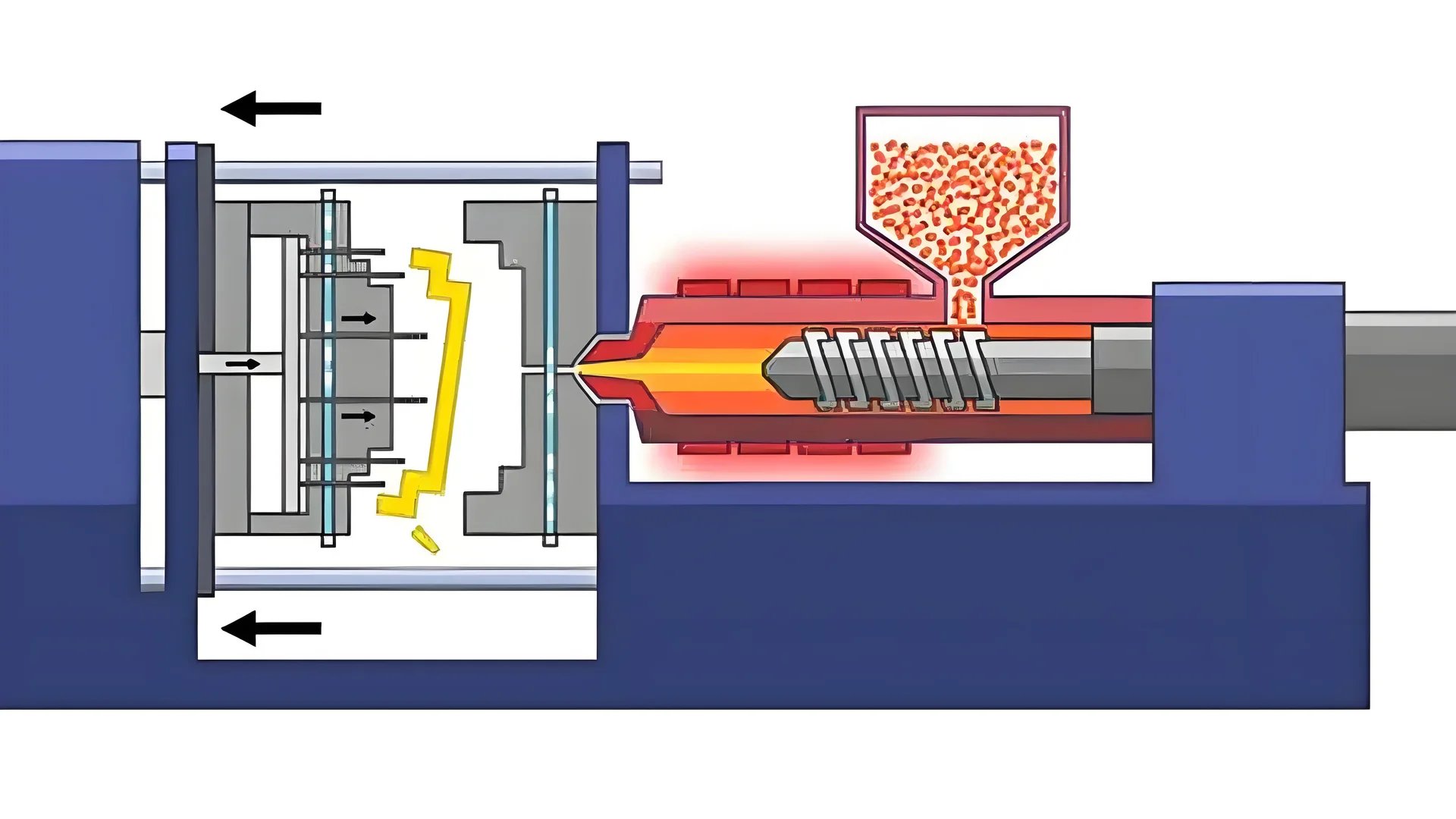
Injection System of Injection Molding Machine
The injection system is the heart of an injection molding machine, comprising several crucial components.
-
Barrel: This is where the plastic raw materials are heated and melted. The barrel is equipped with heating coils that maintain varying temperatures along its length to cater to different plastics’ melting points. For instance, polypropylene (PP) melts between 160-220°C, while polycarbonate (PC) requires about 220-260°C.
-
Screw/Plunger: The screw plays a vital role in conveying the plastic forward through the barrel while also aiding in the melting process by generating shear heat. As the screw rotates, it mixes the plastic evenly, ensuring optimal melting.
-
Nozzle: This component delivers the molten plastic into the mold cavity. It must be designed to prevent premature cooling and ensure a smooth flow of the melted material.
Characteristics of Plastic Raw Materials and the Role of the Screw
Understanding the characteristics of thermoplastics is essential for effective processing:
-
Thermoplastics: These materials are typically granular or powdered and can transition from solid to liquid when heated. The molecular chains loosen, enabling the material to flow into molds.
-
Function of the Screw: As the screw rotates, it compresses and heats the plastic particles, causing them to melt faster due to shear heat. This is particularly beneficial for high-viscosity materials where quick melting is necessary.
Property | Polypropylene (PP) | Polycarbonate (PC) |
---|---|---|
Melting Temperature | 160-220°C | 220-260°C |
Viscosity | Low | High |
Temperature Control and Feedback Mechanism
The temperature control system is integral to maintaining quality:
-
Temperature Sensors: These devices monitor real-time temperatures within the barrel, ensuring that they remain within specified limits.
-
Heating Device: Adjusts power based on feedback from sensors; increasing power when temperatures drop and reducing it when temperatures exceed set thresholds. This ensures a stable molten state for consistent quality.
The precise control of temperature not only aids in preventing material degradation but also enhances the quality of injection molded parts, ensuring they meet design specifications effectively.
For further exploration, you may want to investigate how temperature control impacts product quality1 or delve into the role of injection systems in modern manufacturing .
The barrel is responsible for melting plastic in injection molding.True
The barrel heats and melts plastic raw materials, ensuring they reach the correct temperature for molding.
The screw in an injection molding machine cools the plastic material.False
The screw generates shear heat to melt plastic, but it does not cool it; rather, it aids in melting.
How does temperature control impact the melting process?
Ever wondered how temperature control influences the melting process in manufacturing? This topic fascinates many because it impacts product quality and performance. Let’s explore this!
Temperature control directly influences the efficiency and quality of the melting process. Materials need to reach their required melting points without breaking down. Good temperature management probably leads to consistent and high-quality production.
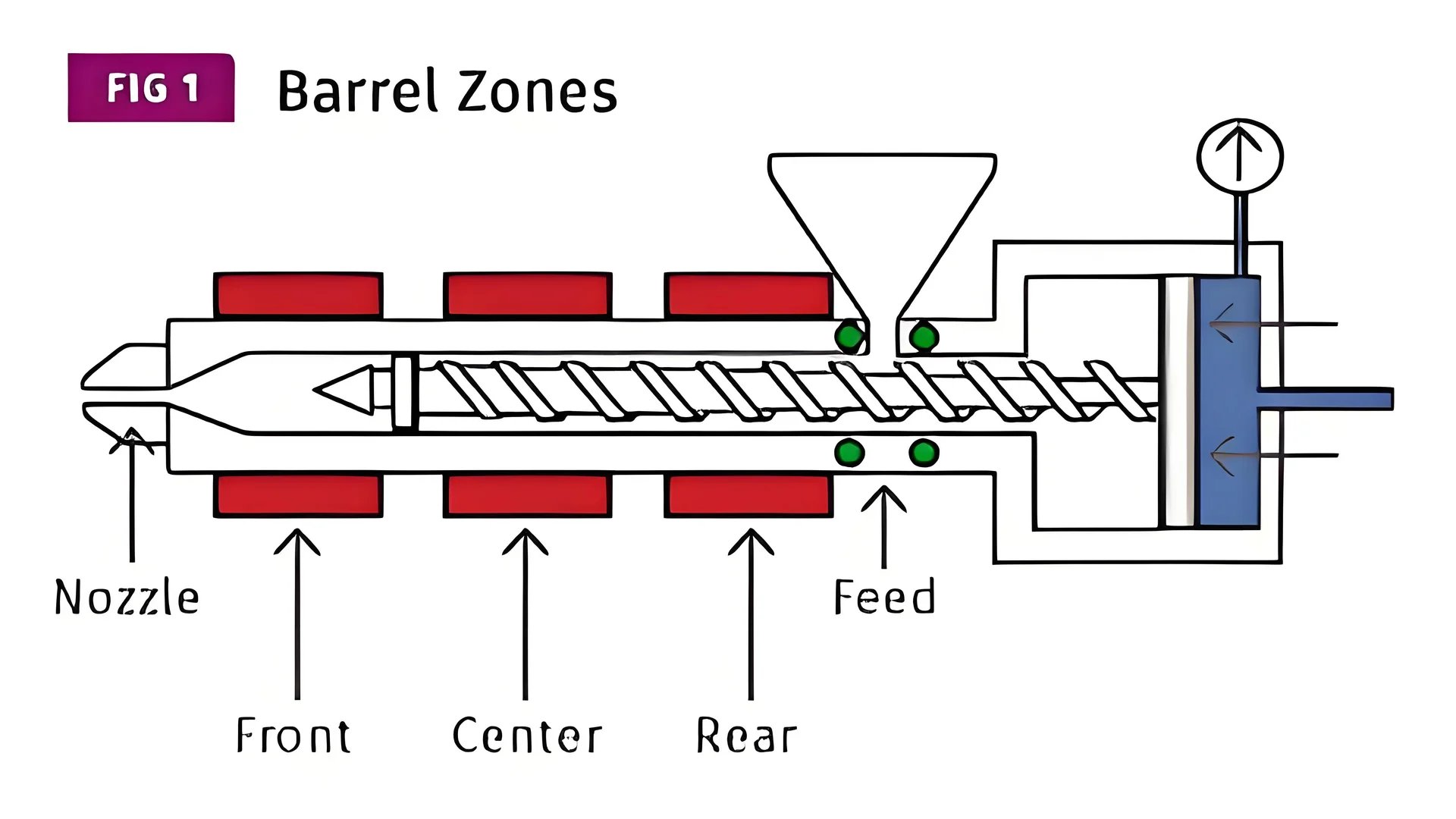
The Importance of Temperature Control in Melting
Temperature control is essential! In methods like injection molding, materials get heated to specific temperatures to work well. For example, thermoplastics show that each material has its own melting point; polypropylene (PP) melts around 160-220°C while polycarbonate (PC) needs temperatures between 220-260°C. Using an effective heating system2 can make a significant difference.
At first, I faced problems because I did not understand how wrong temperatures could spoil a batch. Low temperatures prevent proper melting, causing defects. And if it’s too high? I found out that overheating destroys materials’ qualities and my efforts.
Mechanisms of Heat Transfer
The injection molding machine’s barrel is where everything happens. A heating coil transfers heat to raw plastic materials. Here’s a basic explanation of it:
Stage | Description |
---|---|
1 | Heating coils activate and raise barrel temperature |
2 | Heat transfers through barrel wall to the plastic |
3 | Plastic reaches melting point and becomes viscous |
4 | Viscous plastic is injected into molds |
I learned this process depends heavily on exact temperature control systems. Any mistake may cause major production problems. I have seen what occurs when issues arise.
Feedback Mechanism in Temperature Control
Modern injection molding machines have an impressive feedback mechanism. Imagine this: sensors watch the temperature all the time. Here’s how it works:
- Temperature Sensors: They keep an eye on the barrel’s temperature.
- Automatic Adjustments: If the temperature falls low, the heating elements come on; if it rises too high, cooling starts.
- Stable Conditions: This system keeps plastic in a stable melted state, avoiding damage from excess heat and incomplete melting from lack of heat.
Using a strong feedback control system changed my production’s quality and efficiency. It felt like having a reliable partner ensuring everything runs smoothly. Implementing a robust feedback control system3 enhances production quality and efficiency.
Role of Screw Design in Melting Process
Now, let’s talk about the screw in the injection molding machine – it’s the hidden hero of melting! The design allows for:
- Pushing Material: The rotating screw pushes plastic materials forward through the heated barrel.
- Shear Heating: As materials press together, heat is generated through shear forces, helping faster melting.
- Mixing Evenly: The screw mixes materials so evenly, ensuring consistent melting and product quality.
I clearly remember working with thick plastics; the shear heating effect sped up their melting. Moments like these show why understanding these processes is very important.
In summary, precise temperature control is key for getting materials to melt properly in industrial processes. My experiences taught me that handling temperature well not only improves production efficiency but also product quality.
Temperature control is essential for optimal melting in manufacturing.True
Proper temperature management ensures materials reach their melting points, enhancing product quality and efficiency during the melting process.
Excessive heat during melting can lead to material decomposition.True
Too much heat can damage materials, negatively affecting their physical properties and compromising the final product's quality.
What characteristics of thermoplastics affect their melting behavior?
Thermoplastics resemble magic clay in the world of manufacturing. These materials melt and reshape with a little heat. They really transform. What causes these changes? Let’s explore this!
The melting of thermoplastics depends on their molecular structure, crystallinity, viscosity and temperature control systems. These features are crucial for determining how well a thermoplastic melts and works in different uses.
Molecular Structure of Thermoplastics
The molecular structure of thermoplastics is important. I first learned about polymer chains and was surprised by their ability to change in heat. When temperatures rise, the forces holding these chains together weaken. Thermoplastics then change from solid to liquid. This is a big difference from thermosetting plastics, which harden forever. For example, polyethylene is easier to mold than polypropylene due to its lower melting temperature. Choosing the right material is necessary for each project.
Crystallinity and Its Impact
Crystallinity greatly affects melting behavior. Higher crystallinity means higher melting temperatures because molecules are more ordered. I researched melting points carefully when I had to design a high-temperature component. Information is critical when designs must face tough conditions.
Viscosity and Flow Behavior
Viscosity affects how thermoplastics melt. I see viscosity as a material’s flow resistance. High molecular weight thermoplastics resist flow at low temperatures. Once melting temperatures are reached, they flow easily. This understanding helps with better design decisions, especially in injection molding with complex shapes.
Temperature Control Mechanisms
Temperature control is key in an injection molding machine. The injection system includes the barrel, screw and nozzle. The barrel heats and melts the raw plastic. I remember watching the heating coils work their magic in a machine. Real-time monitoring by temperature sensors keeps the barrel within the desired range. Heating coils increase heat if it’s too cool and reduce it if too hot. This balance ensures quality in both melt and final products.
In short, knowing how molecular structure, crystallinity, viscosity and temperature control affect thermoplastic melting helps us as designers and engineers. Each project becomes easier when considering these properties. This leads to better choices and products. My industry experience shows how these technical details strongly impact my work and design success.
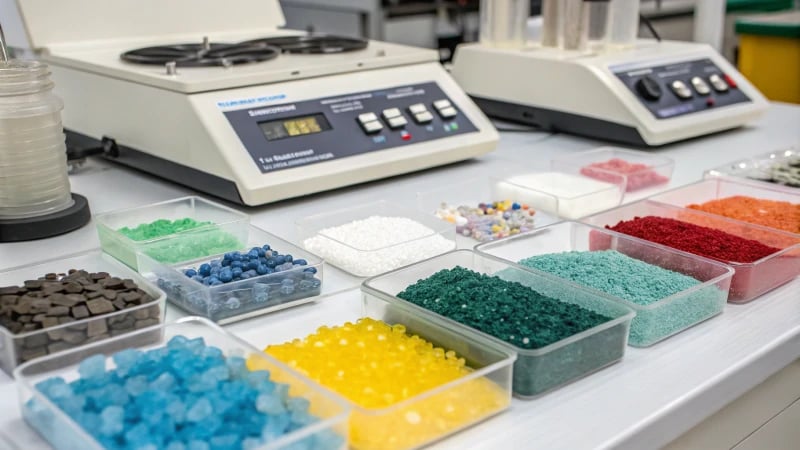
Melting Behavior of Thermoplastics
The melting behavior of thermoplastics depends on several important factors. Their molecular structure has a strong influence. Crystallinity also plays a significant role. Additionally, viscosity affects melting. Temperature control mechanisms in processing machines are vital. These elements are very important. Understanding them is necessary for product design or manufacturing. Anyone working with these materials must study these factors. In my experience, these factors really impact practical applications.
Molecular Structure of Thermoplastics
Thermoplastics possess a unique molecular structure characterized by long, flexible polymer chains. This structure is crucial in determining how thermoplastics melt under heat.
When exposed to increasing temperatures, the forces between these molecular chains weaken, allowing the material to transition from solid to liquid.
This behavior is fundamentally different from thermosetting plastics, which do not melt but rather harden permanently upon heating.
For example, polyethylene4 has a lower melting temperature compared to polypropylene5, which affects their application in various manufacturing processes.
Crystallinity and Its Impact
The degree of crystallinity in thermoplastics significantly influences their melting behavior. Crystalline regions within a thermoplastic can create varying melting points due to their ordered arrangement.
Thermoplastic | Crystallinity (%) | Melting Temperature (°C) |
---|---|---|
Polyethylene | 30-60 | 120-130 |
Polypropylene | 40-70 | 160-220 |
Polycarbonate | 40-50 | 220-260 |
Higher crystallinity generally leads to a higher melting temperature. This property must be considered when selecting materials for specific applications, especially in high-temperature environments.
Viscosity and Flow Behavior
The viscosity of thermoplastics is another critical characteristic that affects their melting behavior. Viscosity refers to a material’s resistance to flow, which decreases as temperature rises.
Thermoplastics with high molecular weight tend to have higher viscosity at lower temperatures, making them harder to process initially. However, once they reach their melting point, the viscosity drops significantly, allowing for easier molding and shaping.
Understanding the viscosity behavior of materials can lead to better design choices in the injection molding process, particularly when working with complex shapes or intricate designs.
Temperature Control Mechanisms
Effective temperature control is vital in the melting process of thermoplastics. The injection system of the injection molding machine6 incorporates a barrel, screw, and nozzle designed to achieve precise temperature settings.
Feedback Mechanisms in Injection Molding Machines
- Real-time Monitoring: Temperature sensors provide real-time data on the barrel’s temperature, ensuring it remains within the desired range.
- Heating Device Adjustment: If the temperature falls below the set point, the heating coils increase power to maintain optimal conditions. Conversely, they reduce power if the temperature exceeds the threshold.
This sophisticated feedback mechanism is critical for maintaining the quality of both the plastic melt and the final molded products.
In summary, the characteristics of thermoplastics—such as molecular structure, crystallinity, viscosity, and effective temperature control—are crucial factors influencing their melting behavior during processing. Understanding these properties enables better decision-making for engineers and designers in their respective applications.
Thermoplastics melt due to weakened molecular chain forces.True
The melting behavior of thermoplastics is caused by the weakening of forces between their long, flexible polymer chains when exposed to heat, allowing them to transition from solid to liquid.
Higher crystallinity leads to lower melting temperatures in plastics.False
In thermoplastics, higher crystallinity generally results in higher melting temperatures, impacting material selection for high-temperature applications.
Why is the feedback mechanism essential for quality control in injection molding?
Do you ever think about why some plastic products look so perfect? I realized that feedback in injection molding changes everything. It helps keep everything running very smoothly. Temperature stays under control. Defects probably decrease a lot.
The feedback system in injection molding is critical for keeping quality consistent. It does this by holding the exact temperature steady. This reduces defects and increases the process’s reliability. The system achieves this through real-time changes.
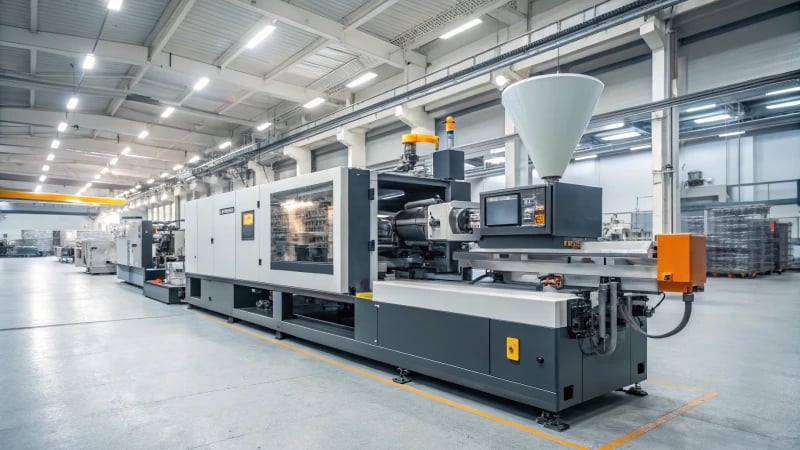
Understanding the Role of the Feedback Mechanism
The feedback system in injection molding is like the quiet hero of manufacturing, working to keep everything on track. I remember the first time I saw it work; it seemed almost magical. This system focuses on exact temperature control, which is very important for melting plastic materials perfectly. When I began in this field, I did not know how critical it was to keep that molten state stable. Stable molten plastic means a perfect product. Unstable molten plastic means many defects.
When there is a temperature change, the feedback system activates to fix it immediately. It is like a parent who knows when their child needs help and jumps in quickly. The temperature control system7 uses sensors to keep track of temperatures and adjusts the heating power. This fast action is vital for stopping problems like material breakdown or not melting fully, which can really hurt quality.
The Components of the Feedback Mechanism
-
Temperature Sensors
- These sensors are strategically placed throughout the barrel to monitor temperature variations continuously.
- They provide instant data to the control system, allowing for quick adjustments.
-
Heating Device Control
- The heating coils are regulated based on sensor feedback, ensuring optimal temperatures are maintained.
- This reduces energy waste and improves consistency across batches.
Importance of Consistency in Temperature Control
This feedback mechanism truly shines because of its consistency. Picture this: as a designer, I wish my products to be excellent. The system always works to keep the best temperatures, giving me peace of mind. Different plastics melt at different temperatures. This is like how some people like their coffee hot, while others prefer it iced.
Plastic Type | Melting Temperature Range (°C) |
---|---|
Polypropylene (PP) | 160 – 220 |
Polycarbonate (PC) | 220 – 260 |
By keeping the right temperature for each type of plastic, the feedback system makes sure every batch looks and works as it should. For someone like Jacky, who designs consumer electronics, this is especially important. Jacky does not want designs to fail due to temperature problems. No one wants that.
Reducing Defects Through Feedback Loops
I have seen how this feedback system helps lower production defects:
- If temperatures rise suddenly, the control lowers power to stop overheating. It is like reducing heat when cooking if things get too hot.
- If temperatures drop suddenly, the system increases power so melting happens correctly.
These quick changes are smart and necessary for lowering risks in manufacturing mistakes. A good feedback system lets us reach higher quality standards and make better products.
Conclusion of Insights
In my journey in injection molding, it is clear that the feedback system is very important for keeping quality control. Its real-time adjustments keep processes efficient and products high-quality. As I continue to improve production practices, understanding this system’s importance empowers me. I hope it inspires you too!
Feedback mechanisms ensure consistent quality in injection molding.True
By regulating temperature, feedback systems help maintain uniformity in molded parts, crucial for quality control.
Temperature sensors are unnecessary for effective injection molding.False
Temperature sensors are essential for monitoring and adjusting conditions to prevent defects during the injection molding process.
Conclusion
Injection molding efficiently melts thermoplastics using a barrel, screw, and precise temperature control, ensuring quality production through effective heating and cooling processes.
-
Clicking this link will provide detailed insights on injection molding systems, enhancing your understanding and application in design. ↩
-
Explore this link for deeper insights into how temperature influences material properties during melting processes. ↩
-
Click here to learn more about feedback mechanisms in industrial heating systems and their significance. ↩
-
Explore insights on how thermoplastic properties influence melting behavior to enhance your understanding for practical applications. ↩
-
Gain deeper insights into the role of viscosity in thermoplastics to optimize your design processes. ↩
-
Learn about effective temperature control in injection molding machines to improve production efficiency. ↩
-
Explore this link to learn how feedback mechanisms can significantly improve quality control in manufacturing processes. ↩