Ever wondered how those PVC fittings are made so efficiently?
Injection molding machines are a powerhouse for producing PVC fittings, thanks to their knack for managing thermoplastic materials like PVC with precise controls and custom molds.
Diving into the world of injection molding, I remember my first encounter with these machines. It was like watching magic, the way molten PVC is injected into custom molds to create elbows and tees. But it’s not all wizardry—there’s a dance of precise temperature controls and mold designs that makes it all happen. Yet, I quickly learned that PVC is a bit of a diva, needing just the right touch to prevent overheating. With the right stabilizers and meticulous process control, though, it all comes together in a symphony of production efficiency. It’s a blend of art and science, much like my journey in mold design.
Injection molding machines are efficient for PVC fittings.True
These machines manage thermoplastic materials like PVC with precision.
Custom mold designs have no impact on efficiency.False
Custom molds enhance production by optimizing material flow and design.

- 1. Why is PVC a top choice for injection molding?
- 2. How Do Custom Mold Designs Impact PVC Fitting Production?
- 3. What Are the Key Process Controls in Injection Molding PVC?
- 4. What Challenges Arise with PVC Heat Stability in Injection Molding?
- 5. How Do Additives and Stabilizers Affect PVC Processing?
- 6. Conclusion
Why is PVC a top choice for injection molding?
Have you ever wondered what makes PVC such a star in the world of injection molding?
PVC stands out for injection molding thanks to its compatibility with thermoplastic machinery, customizable mold designs, and precise control over processing conditions, ensuring top-notch fittings.
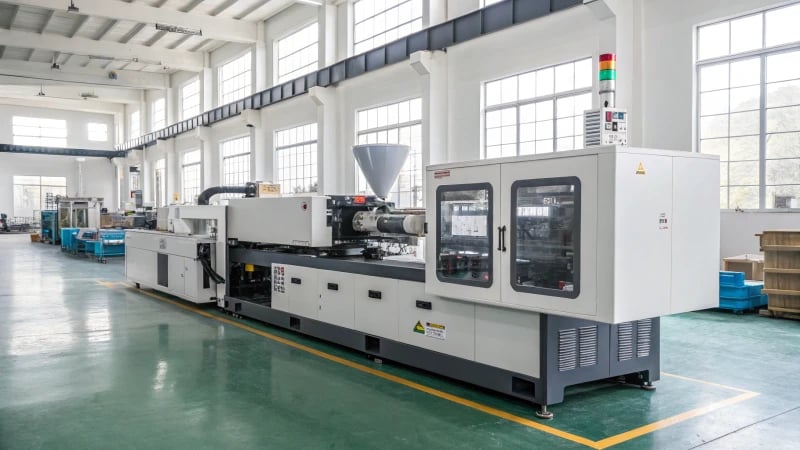
Material Compatibility
I remember the first time I worked with PVC1—it was like discovering a hidden gem. Injection molding machines handle thermoplastics like PVC effortlessly. The machine’s barrel and screw adapt to the right temperature and pressure, typically around 170 – 200°C, making the whole process feel like a well-choreographed dance.
Custom Mold Design
Creating custom molds for PVC fittings always brings out the artist in me. Whether it’s crafting an elbow or a tee, these molds are designed with precision cavities that mirror the desired fitting’s shape. The molten PVC flows into these cavities and, as it cools, turns into the perfect piece—like magic!
Feature | Description |
---|---|
Flexibility | Allows for intricate designs |
Durability | Ensures long-lasting fittings |
Process Control
One of my favorite aspects of injection molding with PVC is the control it offers. Tinkering with parameters like injection speed and cooling time feels like fine-tuning an instrument. These adjustments ensure that each fitting is top quality, fully filled, and dimensionally stable.
Challenges in Using PVC
Heat Stability
Handling PVC does require precision, especially with heat. A slight misstep can lead to degradation, releasing corrosive hydrochloric acid—a lesson I learned early on. Accurate temperature control is non-negotiable here.
Additives and Stabilizers
Choosing the right additives2 is like picking spices for a recipe—essential for enhancing PVC‘s heat stability. The right mix ensures your product’s quality stays intact.
Understanding these elements is crucial for designers3, guiding them to make smart choices in their manufacturing processes.
Explore more on injection molding techniques4 to further refine your designs.
PVC requires a processing temperature of 170 - 200°C.True
PVC is typically processed in injection molding at 170 - 200°C.
Custom molds for PVC cannot create intricate designs.False
PVC allows for intricate designs due to its flexibility in molding.
How Do Custom Mold Designs Impact PVC Fitting Production?
Have you ever wondered how custom mold designs can transform the production of PVC fittings? Let’s dive into the details and uncover their pivotal role.
Custom mold designs are crucial in PVC fitting production, dictating the shape, precision, and efficiency of the process. They ensure that molds align with specific requirements, impacting both the quality and cost-effectiveness of the final product.
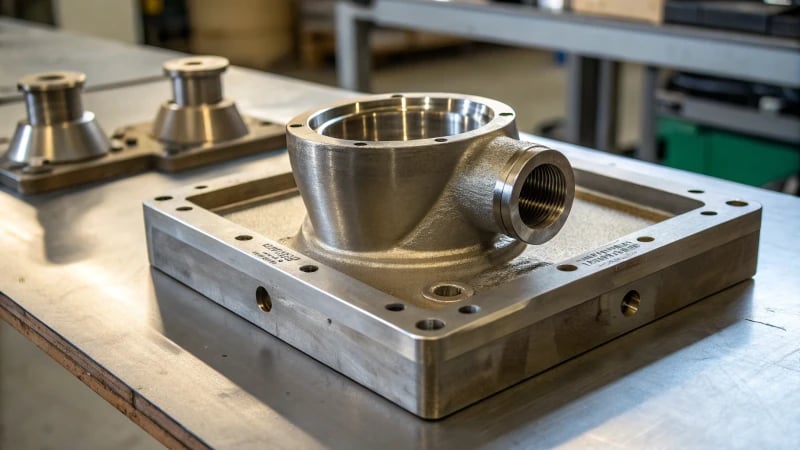
Importance of Custom Mold Designs
Imagine the excitement of watching a mold take shape, knowing that each curve and cavity will define a product’s future. Custom molds aren’t just about fitting pieces together; they’re about creating a symphony of design and function. For instance, when I first began working with PVC fittings like elbows and tees, I learned that each mold dictates not only the product’s shape but also its material compatibility5 with materials like PVC. The complexity of the mold directly influences how efficiently we can produce durable products.
Material Compatibility and Mold Design
Reflecting on my early days in mold design, I remember the challenge of ensuring that our molds could withstand high temperatures while maintaining precise shapes. PVC, being a thermoplastic, requires molds that can handle temperatures ranging from 170°C to 200°C without losing form. This meant creating robust molds capable of withstanding not just heat but the demands of consistent production cycles.
PVC Type | Typical Temperature Range (°C) |
---|---|
Standard PVC | 170 – 200 |
Additive-enhanced PVC | Varies based on additives |
Process Control and Its Role
Tight process control in injection molding is akin to conducting an orchestra where every instrument needs perfect timing. I often find myself engrossed in fine-tuning parameters like injection speed and holding pressure. This meticulous attention ensures that every PVC fitting meets its exact specifications, free from defects. Proper process control6 is essential for achieving this precision.
Challenges in Designing for PVC
I’ve faced my fair share of challenges, especially with PVC’s narrow processing window. Ensuring heat stability is critical to avoid degradation, which not only affects the product but can damage equipment too. Selecting the right additives7 and stabilizers becomes crucial to maintain quality and efficiency throughout the process.
Examples of Effective Mold Designs
A memorable project involved designing a mold for PVC couplings. We incorporated intricate cooling channels that significantly reduced cycle time while maintaining quality. This optimization allowed us to enhance production speed without sacrificing the product’s precision.
For further insights8, exploring case studies offers valuable lessons in overcoming these common challenges through real-world applications and adjustments I’ve seen firsthand how thoughtful design can drive efficiency and innovation.
Custom molds enhance PVC fitting durability.True
Custom molds ensure precise material compatibility, enhancing durability.
PVC molds operate at 150°C to 180°C.False
PVC molds typically operate between 170°C and 200°C, not lower.
What Are the Key Process Controls in Injection Molding PVC?
Ever wondered how those seemingly simple PVC fittings are crafted with such precision? Let’s dive into the fascinating world of injection molding and explore the secrets behind its magic.
To master injection molding PVC, focus on temperature control, mold design, and injection speed. These elements are vital for preserving material integrity and producing top-notch fittings every time.
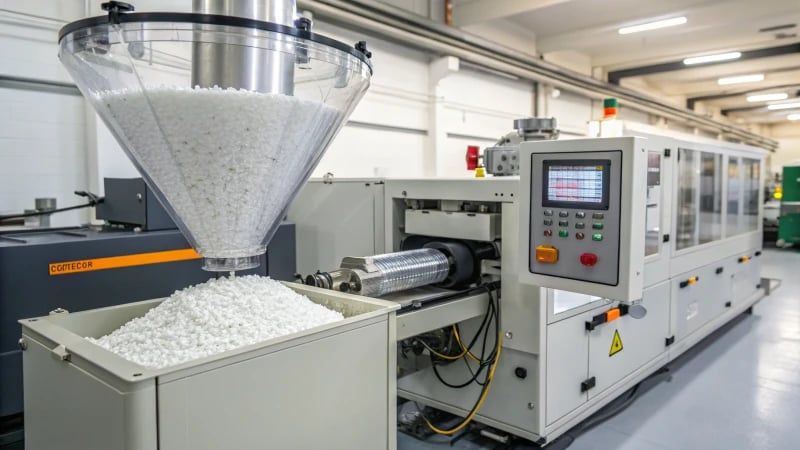
Temperature Management
When I first delved into the world of injection molding9, temperature management was like learning to control fire—it was both daunting and thrilling. Ensuring the machine barrel stays between 170°C and 200°C is crucial because overheating PVC can release corrosive hydrochloric acid. The precision required here reminds me of those times when a slight deviation meant starting over from scratch.
Mold Design
I remember working on my first custom mold; it felt like crafting a work of art. The mold had to perfectly mirror the shape of the PVC fitting—be it an elbow or a coupling—so that the molten PVC could fill every nook and cranny. The satisfaction of seeing a dimensionally stable product emerge from a mold I helped design was unparalleled.
Feature | Description |
---|---|
Material Compatibility | Handles thermoplastic materials, making it suitable for PVC. |
Mold Design | Tailored for different fittings with precise cavity shapes. |
Injection Speed and Pressure
Fine-tuning injection speed and pressure took me back to my early days in the field, grappling with the balance needed to achieve perfection. These settings ensure the PVC flows just right and compensates for shrinkage during cooling. Achieving this balance can be challenging but mastering it is key to producing high-quality outputs.
Additives and Stabilizers
Using additives felt like playing the role of a chemist. These substances improve PVC‘s heat stability during molding, and understanding their interplay is crucial to overcoming processing challenges10. Selecting the right stabilizers can prevent decomposition and enhance product characteristics, ensuring that every piece meets the highest standards.
PVC barrel temperature should be 170°C to 200°C.True
Maintaining this temperature range prevents PVC degradation and ensures quality.
Overheating PVC releases nitrogen gas.False
Overheating PVC releases hydrochloric acid, not nitrogen gas.
What Challenges Arise with PVC Heat Stability in Injection Molding?
Diving into PVC injection molding is like a rollercoaster ride of challenges and solutions.
PVC heat stability in injection molding poses a challenge due to its narrow processing window and tendency to decompose at high temperatures, releasing corrosive gases. Proper temperature control and using stabilizers are vital to prevent degradation and ensure the quality of the final product.
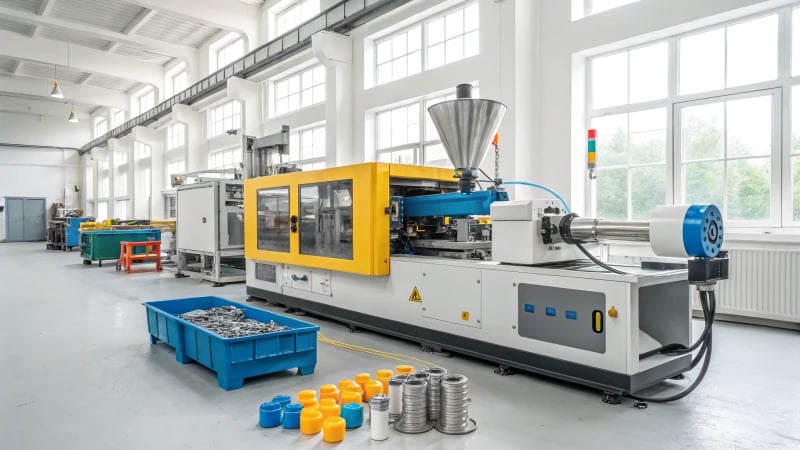
Understanding Heat Stability in PVC
Ah, the art of injection molding! Picture this: I remember the first time I watched a machine churn out PVC fittings11, mesmerized by its precision and speed. However, what looks seamless often masks the intricate dance of managing heat stability. PVC, a thermoplastic marvel, demands attention with its narrow processing window. It’s like handling a delicate soufflé—too much heat, and things can get ugly. When PVC decomposes, it releases hydrochloric acid, a silent saboteur that can corrode your beloved equipment.
Parameter | Typical Value for PVC |
---|---|
Temperature Range | 170 – 200°C |
Pressure | Varies |
Cooling Time | Optimized per design |
Role of Additives and Stabilizers
Back when I first started working with PVC, I learned quickly that additives and stabilizers were my best allies. These magic ingredients improve PVC‘s resilience against heat fluctuations. Selecting the right type and amount is crucial—it’s like cooking, where too much salt can ruin the dish.
Examples of Common Additives:
- Calcium-based stabilizers: Boost thermal stability.
- Lubricants: Keep friction in check during processing.
Process Control in Injection Molding
To master PVC molding, I found that controlling every aspect of the process is akin to conducting a symphony. Fine-tuning injection speed, holding pressure, and cooling time ensures the PVC doesn’t just fill the mold but becomes the masterpiece you envisioned.
- Injection Speed: Ensures complete mold filling.
- Holding Pressure: Compensates for shrinkage.
I recall tweaking holding pressure12 settings obsessively to avoid defects like warping or dimensional instability. Each adjustment felt like a step closer to perfection.
Challenges in Mold Design
Designing molds for PVC is a test of endurance and creativity. The mold must withstand thermal stress while defying corrosion from hydrochloric acid. It’s about choosing materials and coatings that not only survive but thrive under pressure.
In summary, navigating the challenges of PVC’s heat stability is a journey through technology, material science, and a splash of intuition. Each decision influences the final product, underscoring the importance of precision and innovation in this field. Embrace these elements to truly master the craft of PVC injection molding13.
PVC decomposes above 200°C in molding.True
PVC decomposes, releasing hydrochloric acid, above 200°C during molding.
Calcium stabilizers increase PVC's thermal stability.True
Calcium-based stabilizers enhance PVC's resistance to heat degradation.
How Do Additives and Stabilizers Affect PVC Processing?
Ever wonder what makes PVC so versatile and reliable? It’s all about the additives and stabilizers!
Additives and stabilizers are essential in PVC processing, enhancing thermal stability, flexibility, and material integrity. They prevent degradation, ensuring precise molding and durable products. Choosing the right mix is crucial for optimal performance.
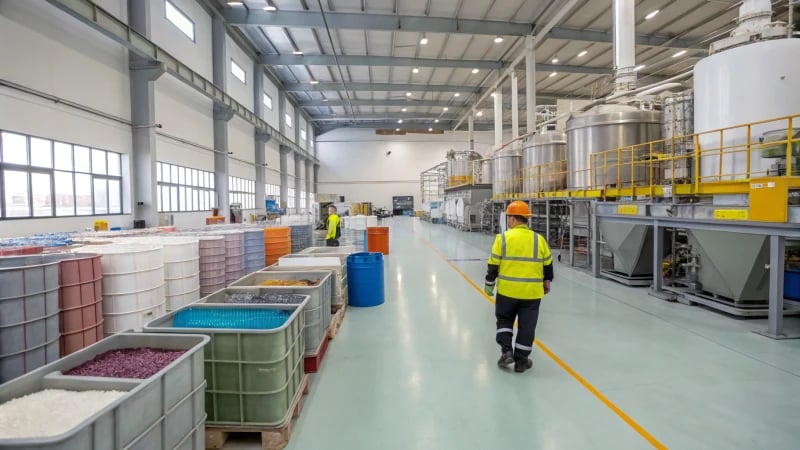
Understanding Additives in PVC Processing
When I first dipped my toes into the world of PVC processing, I quickly learned that additives are like the secret ingredients that can make or break a recipe. These compounds, ranging from plasticizers to pigments, transform PVC into a material that can meet a myriad of application demands. I remember a project where we needed PVC to be super flexible. Thanks to plasticizers, the PVC didn’t just meet expectations—it exceeded them!
Additive Type | Function |
---|---|
Plasticizers | Enhance flexibility |
Fillers | Improve strength |
Pigments | Add color |
Impact Modifiers | Increase toughness |
Role of Stabilizers in PVC Processing
Working with PVC also taught me the importance of stabilizers. These unsung heroes ensure that during the high-heat processing, our material doesn’t degrade. I recall an early oversight on my part when we didn’t use the right stabilizer mix—let’s just say the results weren’t pretty! Since then, I’ve been meticulous about picking stabilizers that keep everything solid, literally.
Types of Stabilizers
- Lead Compounds: Once the gold standard for heat stability, but now they’re stepping back due to environmental concerns.
- Calcium-Zinc Blends: A greener choice that’s gaining popularity in my circles.
- Organic Stabilizers: The new kids on the block, offering sustainable solutions without compromising quality.
The Impact on Injection Molding
PVC‘s adaptability in injection molding is another aspect that fascinates me. With the right additives, material compatibility14 ensures that the material flows perfectly into custom-made molds for fittings like elbows and tees. It’s almost like magic watching molten PVC transform into exactly what you envisioned. The precision control we have over parameters like injection speed is crucial—I once learned the hard way how even a slight misstep can lead to incomplete mold fillings.
Challenges with Heat Stability
Heat stability was one of those things I underestimated until faced with the consequences. PVC‘s narrow processing window means it’s essential to manage temperatures carefully to prevent decomposition and equipment damage. Stabilizers are vital here, acting as a shield against harsh chemical reactions. Trust me, once you’ve experienced an equipment malfunction due to hydrochloric acid release, you won’t skimp on this step again.
For further insights into managing heat stability15 in PVC processing, consult resources detailing best practices and innovative solutions in materials science.
Conclusion
As I continue my journey in PVC processing, one thing remains clear: the judicious selection of additives and stabilizers isn’t just a technical necessity; it’s an art form that balances performance, environmental consciousness, and cost. Dive deeper into this fascinating world through specialized resources to enhance your manufacturing processes efficiently.
Plasticizers make PVC more flexible.True
Plasticizers are added to PVC to increase its flexibility and softness.
Lead compounds are eco-friendly stabilizers.False
Lead compounds offer heat stability but raise environmental concerns.
Conclusion
Injection molding machines efficiently produce PVC fittings through precise temperature control, custom mold designs, and careful process management, ensuring high-quality products while addressing challenges like heat stability.
-
Learn about PVC’s properties and why it’s compatible with injection molding. ↩
-
Discover how additives can enhance PVC’s performance in injection molding. ↩
-
Understand the role of professionals like Jacky in the PVC molding industry. ↩
-
Expand your knowledge on modern techniques used in injection molding. ↩
-
Learn about how injection molding machines handle various PVC types, ensuring proper material compatibility. ↩
-
Discover techniques to maintain precise control over parameters crucial for high-quality PVC fittings. ↩
-
Explore how additives improve heat stability and quality during PVC processing. ↩
-
Investigate case studies showcasing successful custom mold designs in PVC fitting production. ↩
-
Understanding temperature control helps prevent material degradation and equipment damage. ↩
-
Learn how additives enhance heat stability and overall product quality. ↩
-
Discover how injection molding machines produce a variety of PVC fittings efficiently. ↩
-
Explore the impact of holding pressure on the quality and stability of molded PVC parts. ↩
-
Learn about the stabilizers that improve PVC’s heat resistance during manufacturing. ↩
-
Discover how additives enhance material flow and compatibility during injection molding for improved manufacturing efficiency. ↩
-
Learn effective strategies for controlling heat stability in PVC processing to prevent equipment damage and ensure product quality. ↩