Ever wondered just how adaptable injection molding can be? Let me take you on a journey through its fascinating capabilities with both plastic and metal parts.
Injection molding efficiently produces complex plastic parts using diverse materials. Metal parts require metal injection molding (MIM), which is effective but entails higher costs and complexities.
When I first delved into the world of injection molding, I was blown away by its efficiency in producing intricate plastic designs. From toy components to intricate electronic device buttons, the possibilities seemed endless. But when it came to metal parts, things got a little trickier. Metal injection molding (MIM) seemed like a secret club with its own rules—complex but fascinating.
Despite the hurdles, MIM‘s ability to handle small, intricate metal pieces intrigued me. It reminded me of assembling tiny model planes as a kid, where precision was everything. However, I quickly learned that unlike plastic, metal brought along challenges like cost and technical precision that required careful navigation. Yet, the allure of creating delicate metal parts kept me hooked, much like piecing together those childhood models. Through it all, I realized that while injection molding is a master of plastic, it’s also an art form when applied to metal.
Injection molding is ideal for high-volume plastic parts.True
Injection molding efficiently produces complex, high-volume plastic parts.
Metal injection molding (MIM) is cost-effective for all metal parts.False
MIM is costly due to complex processes, suitable for specific needs.
- 1. Why is Injection Molding the Best Choice for Plastic Parts?
- 2. How does adapting to diverse materials improve production?
- 3. What Are the Complexities Involved in Metal Injection Molding?
- 4. Is Injection Molding Cost-Effective for Large-Scale Manufacturing?
- 5. Why is Precision Control Vital in Injection Molding?
- 6. What Are the Limitations of Metal Parts in Injection Molding?
- 7. Conclusion
Why is Injection Molding the Best Choice for Plastic Parts?
Ever wondered why injection molding is the go-to method for crafting plastic parts?
Injection molding is ideal for plastic parts due to its material versatility, ability to produce complex shapes, efficiency in mass production, cost-effectiveness, and high precision.
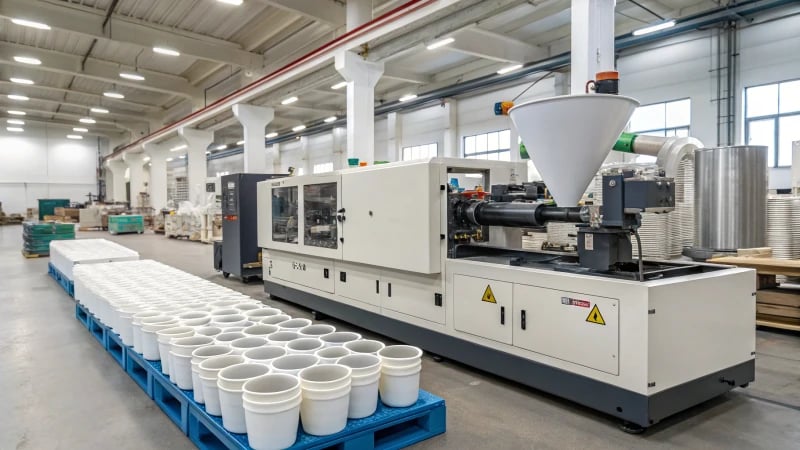
Material Diversity Adaptation
One of the first things I learned when diving into the world of injection molding was its incredible versatility with different plastic materials. It reminded me of a chef with access to an endless spice rack. Each material, from thermoplastics like polypropylene1 to thermosetting plastics such as epoxy resin, offers unique characteristics. This adaptability lets us tailor processes to craft parts with just the right properties, whether it’s for a gadget housing or an automotive component.
Material Type | Examples | Characteristics |
---|---|---|
Thermoplastics | Polypropylene, PE | Easy to shape, recyclable |
Thermosetting Plastics | Epoxy Resin, Phenolic Resin | Heat-resistant, durable |
Complex Shape Manufacturing
Remember trying to build intricate models as a kid? Injection molding is like having a magic tool that makes those dreams possible, only on a much grander scale. Whether it’s tiny toy parts or buttons for electronic devices, multi-cavity molds can handle them all at once. Even when faced with complex structures featuring undercuts or thin walls, injection molding meets the challenge head-on.
Efficient Large-Scale Production
When I first saw an injection molding machine in action, it was like witnessing an orchestra of efficiency. Once the mold is set, it can churn out massive quantities with consistent quality at a speed that would make any assembly line proud. This is especially prevalent in industries like plastic packaging2, where producing thousands of bottles or boxes is just another day at the office.
Cost-Effectiveness
Despite what some might think about initial mold costs, injection molding proves its worth as production scales. I remember a project where we reduced costs dramatically by optimizing material use—less waste means lower expenses. It’s an economic powerhouse for mass-produced components.
Precision and Quality Control
One of my favorite aspects of injection molding is its precision. By fine-tuning parameters like temperature and pressure, we achieve remarkable dimensional accuracy and surface finish. This is crucial in sectors requiring tight tolerances, such as electronics, where even a slight deviation can lead to big issues.
In conclusion, injection molding’s balance of material diversity, complexity management, efficiency, cost savings, and precision makes it indispensable in modern manufacturing. As someone who’s been in the trenches with this technology, I can vouch for its status as a cornerstone method in producing plastic parts3. Whether you’re designing for functionality or aesthetics, it offers the flexibility and reliability you need to bring your visions to life.
Injection molding is suitable for thermoplastics only.False
It accommodates both thermoplastics and thermosetting plastics.
Injection molding allows for multi-cavity mold use.True
Multi-cavity molds enable simultaneous production of multiple components.
How does adapting to diverse materials improve production?
Ever wondered how embracing a mix of materials can completely transform the way we produce things?
Adapting to diverse materials boosts production by allowing manufacturers to tailor solutions, enhance efficiency, cut costs, enable intricate designs, optimize resource use, and improve product quality.
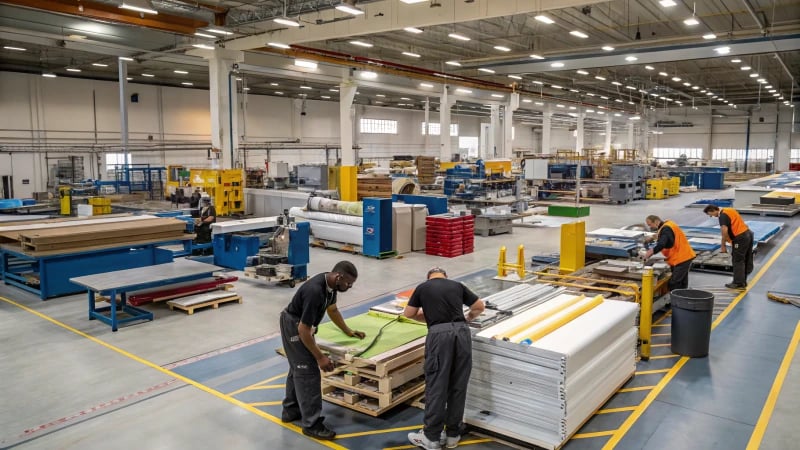
The Role of Material Diversity in Production
I’ve always been fascinated by the magic that happens when you start mixing things up—especially in manufacturing. When I first dived into the world of product design, the idea of using different materials to create something new was like a lightbulb moment. It was as if I’d stumbled upon a treasure chest, each material offering unique advantages that could cater to different market demands. Adapting to these materials is not just about keeping up with trends; it’s about creating versatile products that truly meet the diverse needs of today’s consumers.
Exploring Plastic Parts
Take plastic parts, for instance. I remember working on a project where we were tasked with designing small, intricate components for electronic devices. We turned to injection molding—a technology that allowed us to experiment with various plastics like thermoplastics and thermosetting plastics. Each type had its own set of physical and chemical properties, which was like having a palette of colors to paint with.
Type | Examples | Applications |
---|---|---|
Thermoplastics | Polypropylene (PP), Polycarbonate (PC) | Packaging containers, automotive interiors |
Thermosetting | Phenolic resin, Epoxy resin | Electrical components, durable goods |
The ability to mold these into complex shapes made our job not only easier but also more efficient. This adaptability meant we could quickly produce large quantities without compromising on quality, transforming industries like packaging with rapid production of items like plastic bottles and boxes.
Metal Parts Production
Then there’s the world of metals. While traditional methods have their place, the introduction of metal powder injection molding (MIM)4 opened new doors. The first time I saw MIM in action, I was amazed at how it could create small, detailed metal components more cost-effectively than traditional methods. However, the process is no walk in the park. It involves meticulous steps—from mixing metal powder with binders to precise control during sintering. Despite these challenges, the reduction in waste and precision offered by MIM makes it worth every effort.
Balancing Cost and Efficiency
Balancing cost and efficiency is another area where material diversity shines. I’ve learned that while initial investments in molds can be hefty, they pay off as production scales up and per-unit costs drop significantly. By tapping into diverse materials, we can tweak production strategies to minimize waste and enhance precision through quality control techniques5. This ensures that the final product is not only high-quality but also competitively priced.
Understanding these dynamics has been crucial for me as a designer. It allows me to blend aesthetics with function, ensuring scalability and efficiency across various stages of production. Embracing material diversity isn’t just about keeping up with the competition—it’s about driving innovation and aligning with sustainable practices for long-term success.
Additional Considerations
This concept isn’t limited to one industry. From textiles to agriculture, adapting to diverse materials can revolutionize how sectors operate. For instance, exploring case studies or academic research can shed light on how different industries leverage material diversity to bolster resilience and sustainability. It’s a fascinating journey that shows just how interconnected our world truly is.
Thermoplastics are used in electrical components.False
Thermosetting plastics, not thermoplastics, are typically used in electrical components.
MIM reduces waste compared to traditional metal methods.True
Metal injection molding (MIM) reduces waste by producing precise shapes with minimal excess material.
What Are the Complexities Involved in Metal Injection Molding?
Ever wondered what makes metal injection molding (MIM) so challenging yet captivating? Let’s dive into its intricate dance of precision and complexity.
Metal injection molding involves complexities like high material costs, intricate processes such as mixing and sintering, and potential performance issues, demanding precise control and expertise.
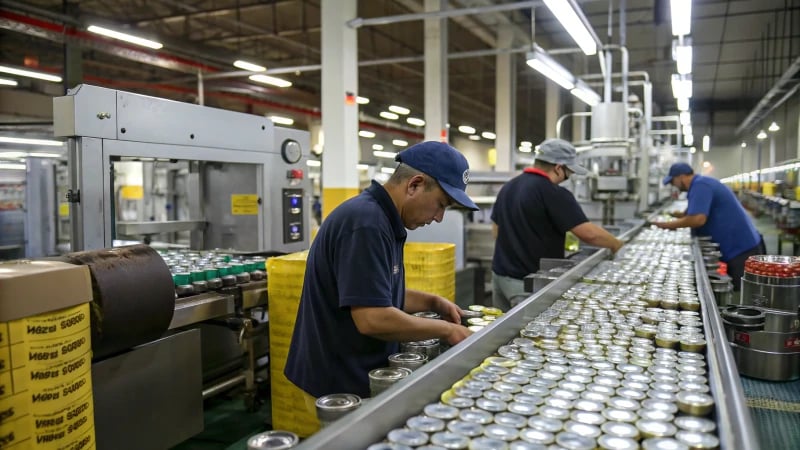
Material Costs and Economic Considerations
You know, back when I first dipped my toes into the world of manufacturing, the sticker shock of metal powder costs in MIM really caught me off guard. It’s a bit like walking into a high-end store when you’re used to thrift shops. These powders are essential but come with a hefty price tag. Add to that the necessity for specialized equipment and skilled labor, and suddenly, the financials of a project look quite different.
Cost Component | Impact on MIM |
---|---|
Metal Powder | High initial cost |
Equipment | Specialized needs |
Skilled Labor | Increased demand |
Complex Process Phases
I remember my first project involving MIM; it felt like juggling flaming swords. Each phase—mixing, molding, debinding, and sintering—demands meticulous attention. One misstep, and you’ve got defects on your hands. It’s this careful choreography that ensures the final product is up to snuff.
- Mixing: Combines metal powder with binders.
- Injection Molding: Shapes the part using molds.
- Debinding: Removes binders from the molded part.
- Sintering: Solidifies the part through heat.
Every step is meticulously monitored6 to ensure quality. Any deviation can lead to defects in the final product.
Material Performance Limitations
Despite its many perks, MIM can sometimes leave you scratching your head over material inconsistencies. I once had a project where, despite our best efforts, the sintering process left us with uneven densities in the parts. It’s like baking a cake and realizing it’s undercooked in the middle. This is particularly true if sintering parameters aren’t tightly controlled—a significant concern7 for applications demanding high-performance metal parts.
Manufacturing Feasibility and Design Challenges
Designing for MIM can be a thrilling puzzle. Think of it as crafting a complex sculpture from metal; only instead of clay, you’re dealing with intricate molds. The challenge lies not just in creating these molds but ensuring the finished part meets all functional requirements.
Design Aspect | Challenge |
---|---|
Mold Complexity | Advanced design |
Mechanical Properties | Consistency issues |
I’ve found that achieving consistent mechanical properties can sometimes feel like trying to predict the weather—tricky at best.
Understanding these complexities isn’t just academic; it’s crucial for turning the potential of MIM into tangible success. By navigating these hurdles thoughtfully, we can truly unlock what this technology has to offer while sidestepping its inherent pitfalls.
Metal powder is the most expensive component in MIM.True
Metal powder has a high initial cost, impacting MIM's economics.
MIM parts always have consistent material density.False
Inconsistent density can occur if sintering parameters aren't controlled.
Is Injection Molding Cost-Effective for Large-Scale Manufacturing?
Ever wondered if injection molding is the financial superhero your large-scale production needs? Let me take you through the cost-effectiveness of this manufacturing marvel.
Injection molding is cost-effective for large-scale manufacturing due to efficient production and material versatility. Although mold costs are high initially, they decrease per-unit costs significantly as production volume rises, making it ideal for producing plastic parts.
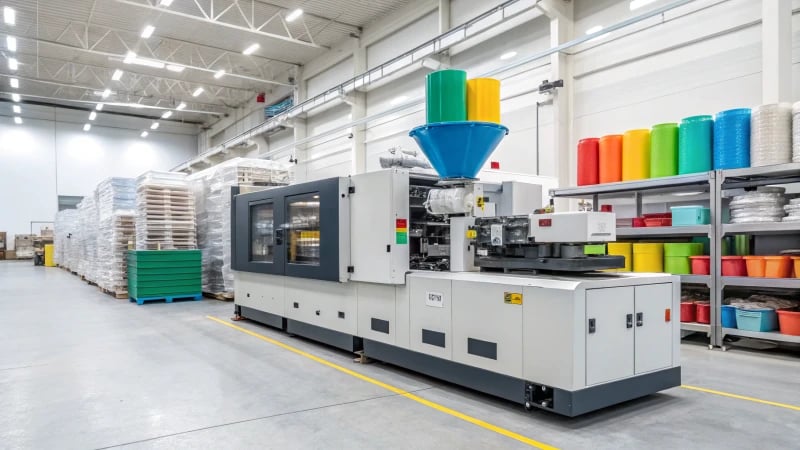
Understanding Cost Structures
When I first dove into the world of injection molding, I was stunned by the upfront mold costs. It felt like buying a luxury car just to hit the road for the first time. But then, as production ramped up, I saw how these initial investments paid off—like getting the keys to a factory that churns out quality parts at lightning speed. Once the mold is ready, it’s like having a golden ticket to rapid and consistent production.
Cost Factor | Description |
---|---|
Mold Costs | High initial cost; varies by complexity and material used. |
Material Costs | Plastic materials like PP, PE are relatively affordable and highly utilized. |
Production Speed | Rapid once setup; ideal for thousands to millions of parts. |
Material Versatility and Suitability
One of my favorite things about injection molding is its adaptability to a wide range of materials, especially plastics. Imagine working with a palette where every color is a different type of plastic—each with its own unique flair. This process lets you create intricate shapes effortlessly. Need multiple small parts, like toy components or electronic device buttons? Multi-cavity molds have got you covered!
Plastic materials such as thermoplastics and thermosetting plastics dominate this arena. Their diversity enables a plethora of applications, from sleek electronics to robust automotive interiors. Using multi-cavity molds feels like having an efficient assembly line at your fingertips.
Learn more about complex shape manufacturing8.
Considerations for Metal Parts
I remember when I first explored Metal Injection Molding (MIM)—it was like stepping into a new realm where metals behaved more like plastics. Though primarily known for plastics, injection molding can work wonders on metal parts too, albeit with more complexity and cost.
While MIM can craft small, intricate components, it requires precision akin to a maestro conducting an orchestra during stages like sintering.
Factor | Plastic Parts | Metal Parts |
---|---|---|
Material Adaptation | Wide variety of plastics; affordable | Limited to special metals; costly |
Production Efficiency | Highly efficient for large-scale production | Less efficient; higher precision needed |
Curious? Learn more about MIM processes9.
Balancing Initial Investment and Long-Term Savings
For folks like Jacky, balancing the initial mold costs against long-term savings is a tightrope act. It reminds me of planning a road trip—carefully plotting each stop to ensure you get the most miles per gallon. Injection molding is particularly beneficial for large-scale production, where the unit costs shrink as output grows.
Optimizing designs for injection molding can be like finding secret shortcuts on your GPS—reducing material waste through effective gate design boosts overall cost-effectiveness.
Utilizing tools like cost calculators can assist in financial planning10 by estimating potential savings and ensuring the process aligns with budgetary goals.
Injection molding is cost-effective for large-scale production.True
High initial mold costs are offset by low per-unit costs at scale.
Metal injection molding is cheaper than plastic injection molding.False
Metal injection molding is more costly and complex than plastic.
Why is Precision Control Vital in Injection Molding?
Ever wondered how precision can transform plastic into perfection?
Precision control in injection molding is crucial for high-quality output, enhancing dimensional accuracy, minimizing defects, and ensuring parts meet exact specifications by optimizing temperature, pressure, and speed.
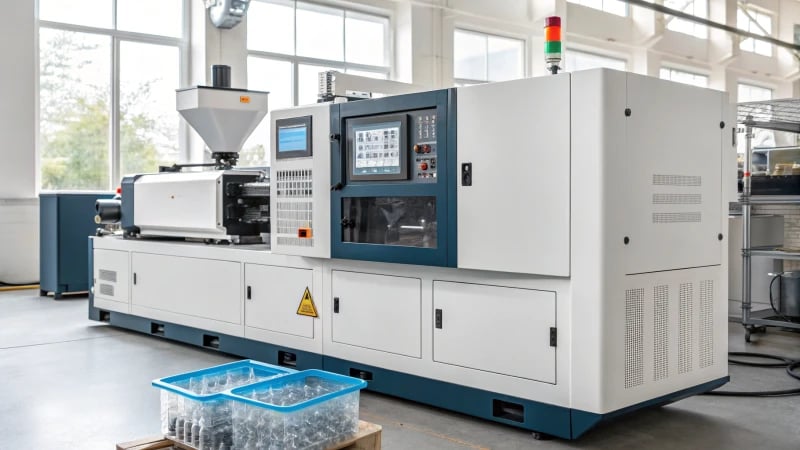
Importance of Precision in Injection Molding
As someone who thrives on turning ideas into tangible products, I know firsthand the magic of injection molding. It’s like the Swiss Army knife of manufacturing processes, letting me create plastic parts11 in all shapes and sizes. Whether I’m dealing with thermoplastics or thermosetting plastics, each material brings its own quirks and charms that I need to understand to achieve precision.
Key Parameters Affecting Precision
- Temperature Control: Imagine trying to bake a cake with an unreliable oven—it’s a disaster waiting to happen. Similarly, managing temperature precisely ensures my plastic melts just right, sidestepping potential defects.
- Pressure Regulation: Consistency is key. By keeping pressure steady, I avoid issues like air pockets or incomplete fillings that could ruin a perfect mold.
- Speed Adjustment: Tweaking injection speed isn’t just about getting the job done faster; it’s about nailing that surface finish and structural integrity.
Quality Control Measures
In my line of work, quality isn’t just a buzzword—it’s my mantra. Every parameter is like a puzzle piece that needs to fit perfectly, especially when crafting precision electronic housings where even the tiniest deviation could spell trouble.
Application in Plastic and Metal Parts
While I’ve primarily danced with plastic components, I occasionally dabble in the world of metal parts12. Here, precision control takes on a new level of importance. Metal powder injection molding (MIM) lets me create those small, intricate metal components that traditional methods might balk at.
Material Type | Characteristics |
---|---|
Thermoplastics | Includes PP, PE, PS; versatile for various applications |
Thermosetting Plastics | Used for parts requiring heat resistance |
Metal Powder | Used in MIM for intricate metal component production |
Precision control isn’t just about perfection—it’s about possibility. Multi-cavity molds are like a dance of precision, crafting multiple parts like toy components or electronic device buttons simultaneously.
Cost-Effectiveness and Efficiency
In an industry where margins matter, reducing waste through precision control isn’t just smart—it’s essential. While those initial mold investments might make anyone wince, scaling up production transforms them into wise choices. For example, in large-scale production13, I can churn out plastic packaging with speed and consistency that’s almost poetic.
To wrap it up, precision control isn’t just a technical necessity—it’s the heart of quality assurance and cost management in injection molding. By mastering process parameters, I’ve found it’s possible to not only meet but exceed production expectations.
Precision control reduces waste in injection molding.True
Precision control minimizes material waste by optimizing process parameters.
Metal parts cannot be produced using injection molding.False
Metal powder injection molding allows for metal part production.
What Are the Limitations of Metal Parts in Injection Molding?
When I first dived into the world of injection molding, the challenges with metal parts were eye-opening, shaping my journey in design.
Metal injection molding (MIM) is limited by high costs, intricate processes, and material constraints, impacting its feasibility compared to traditional methods.
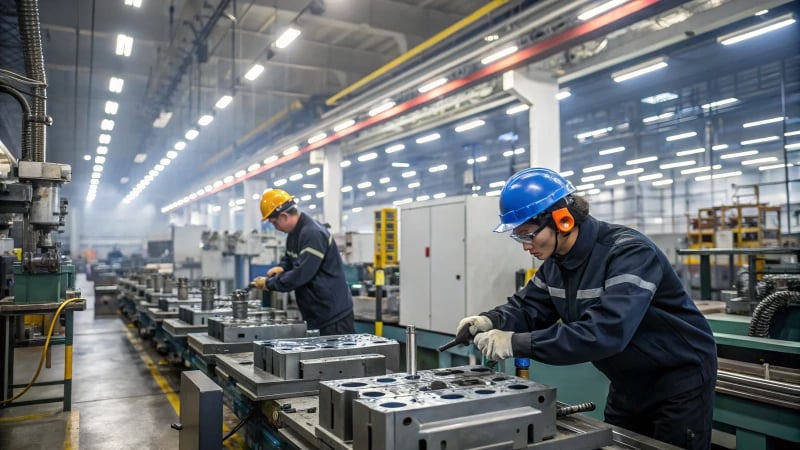
Cost and Process Complexity
I remember the first time I tried to incorporate metal injection molding into a project. The complexity was daunting. MIM involves multiple intricate stages14, from mixing metal powder with binders to precise sintering. Each of these steps not only adds layers of complexity but also significantly ups the cost. I quickly learned that just the price of metal powder could make or break a budget.
Process Stage | Description | Impact on Cost |
---|---|---|
Mixing | Combining metal powder with a binder | High material cost |
Injection Molding | Shaping the material into molds | Precision required |
Debinding & Sintering | Removing binders and solidifying parts | Time-consuming process |
Every phase demands precision control, which can escalate technical difficulties and costs. Through my experiences, I’ve realized that understanding these factors is vital when assessing MIM‘s viability for different projects.
Material Performance Limitations
There’s something about watching a design come to life that always gets me excited. But with MIM, I’ve noticed that performance can be a hit or miss due to sintering conditions15. Inconsistent density during sintering can impair mechanical properties, sometimes making them inferior to parts made through casting or forging. This inconsistency has occasionally impacted the durability and functionality of products in critical applications I’ve worked on.
Applicability for Complex Structures
While MIM allows for intricate designs, its efficiency shines primarily with small, high-precision parts. I learned early on that for larger components, traditional methods might be more suitable due to cost-effectiveness and material performance. Exploring alternative metal forming techniques16 is something I always consider when dealing with bigger or simpler designs.
In summary, while MIM can produce complex and precise metal parts, it’s often accompanied by higher costs and potential performance trade-offs compared to conventional methods like casting or forging. Evaluating the specific needs of your project is essential in guiding whether MIM is the best approach or if other methods might be more advantageous in terms of cost, quality, and feasibility.
MIM is cost-effective for large metal components.False
MIM is not cost-effective for large components due to high material costs.
Sintering can affect metal part durability in MIM.True
Inconsistent density during sintering can impair mechanical properties.
Conclusion
Injection molding excels in producing plastic parts efficiently, while metal injection molding (MIM) offers precision for small metal components despite higher costs and complexities.
-
Discover why polypropylene is favored in injection molding for its versatility and cost-effectiveness. ↩
-
Learn how injection molding revolutionizes plastic packaging by enabling fast production and consistent quality. ↩
-
Explore comprehensive insights into why injection molding is the go-to method for producing diverse plastic components. ↩
-
Discover the advantages of using metal powder injection molding for producing intricate metal parts. ↩
-
Learn about quality control techniques that ensure high precision in injection molding processes. ↩
-
Learn techniques to maintain quality throughout the complex MIM process. ↩
-
Discover factors influencing material density for better product outcomes. ↩
-
Explore how injection molding efficiently produces complex shapes, enhancing design flexibility. ↩
-
Discover how Metal Injection Molding works and its applications in producing intricate metal parts. ↩
-
Find tools to calculate injection molding costs for better financial planning and decision-making. ↩
-
Exploring this link provides insights into the variety of shapes and functionalities achievable through injection molding. ↩
-
This link offers detailed information on how MIM technology produces complex metal parts efficiently. ↩
-
Discover how large-scale production in injection molding reduces costs and improves efficiency. ↩
-
Understand each stage’s impact on cost and complexity in MIM. ↩
-
Explore sintering’s role in affecting mechanical properties of metals. ↩
-
Discover more cost-effective or performance-efficient metal forming methods. ↩