Interested in how plastic boxes are created? Join this journey into the intriguing world of injection molding!
Injection molding machines create plastic boxes by melting raw plastic and injecting it into molds under high pressure. Once cooled, the plastic solidifies, adopting the mold’s shape, thus enabling diverse design possibilities efficiently.
When I first learned about injection molding, I was really amazed. These machines turn raw plastic into perfectly shaped boxes. They do this by heating and melting the plastic. The melted plastic is then injected under high pressure into a mold. Once it cools, the plastic takes the shape of the mold. This shape can be a simple square or a box with very intricate designs. This process mixes science and artistry. I truly appreciate this in my work.
This article explores the detailed workings of injection molding. It covers mold design considerations and discusses process parameters. The article also shares tips for better production efficiency. This guide provides valuable information for everyone. It helps experienced designers like me. It also helps beginners understand plastic box manufacturing.
Injection molding machines use high pressure to form plastic boxes.True
Injection molding relies on high pressure to inject molten plastic into molds, shaping it efficiently.
Plastic boxes are made by cooling raw plastic in open molds.False
Plastic boxes are formed in closed molds, not open, allowing precise shaping as the plastic cools.
What makes injection molding the best choice for producing plastic boxes?
Do you ever think about how factories craft plastic boxes so precisely? Injection molding is the secret method behind this process. I am excited to tell you about the incredible benefits it brings to producing plastic boxes.
Injection molding is ideal for plastic box production due to its flexibility, cost-effectiveness, and precision, enabling accurate shaping of complex designs for large quantities.
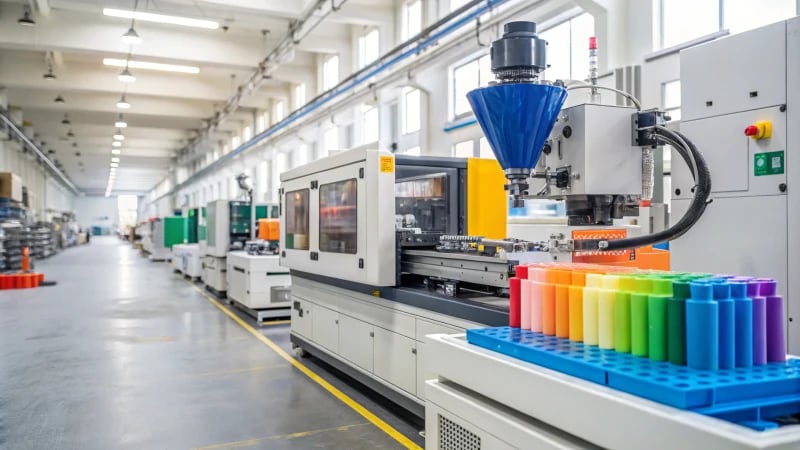
Process Feasibility
Injection molding is really great for making plastic boxes. This method allows the creation of complex shapes impossible with other techniques. The working principle involves heating and melting plastic raw materials, then injecting this molten plastic into a closed mold under high pressure. This process ensures that both simple and intricate designs can be realized effectively.
For example, whether producing a straightforward square box or a box with complex features such as undercuts, injection molding can meet these requirements as long as the appropriate mold is designed. This flexibility is pivotal in product design, ensuring that manufacturers can cater to various market demands.
Key Points of Mold Design
The magic of injection molding involves the mold design too. Every detail truly matters. Each element of the mold must be just right. These details can very much affect the final product. Close attention is necessary to create high-quality items.
Important considerations include:
Aspect | Description |
---|---|
Parting Surface | The choice of parting surface impacts demolding efficiency. A well-designed surface minimizes marks on the product. |
Gate Design | Commonly, a side gate allows for even filling of the mold, while a point gate can minimize visual impact on the box. |
Cooling System | An optimized cooling system prevents defects by ensuring even cooling, which is crucial for maintaining product integrity. |
These design elements must be carefully balanced to achieve an optimal production outcome.
Process Parameter Control
Control of many process parameters is crucial:
- Temperature Control: Setting the right temperature is important for the plastic type. For polypropylene (PP), barrel temperature is usually set between 180-220℃. Mold temperature around 30-50℃ gives a nice surface finish.
- Pressure Control: Injection pressure must be precise to avoid defects such as incomplete fills or unwanted flash. Proper holding pressure helps keep uniform wall thickness and dimensional stability.
- Speed Control: The speed of injection affects filling; controlling it helps avoid bubbles or marks. Managing the mold’s opening and closing speeds improves efficiency without causing wear on molds.
Learning these parameters took trial and error; however, it truly changed the quality of products significantly.
Advantages Over Other Methods
Compared to other techniques, injection molding has several benefits:
- Efficiency in High-Volume Production: Perfect for big productions; it really reduces cycle times compared to blow molding or thermoforming.
- Cost-Effectiveness: Initial mold cost is high; yet unit costs drop with high volume due to less waste and shorter production times.
- Precision and Consistency: The level of accuracy and repeatability is something I depend on; this is vital in industries like consumer electronics.
In summary, my experience shows injection molding isn’t just a production method; it truly is a powerful tool for creating plastic boxes with great form and function.
Injection molding allows for complex shapes in plastic boxes.True
The process's precision enables the creation of intricate designs, making it suitable for diverse product requirements.
Injection molding is less efficient than blow molding for large runs.False
In fact, injection molding is more efficient for high-volume production compared to blow molding, reducing cycle times significantly.
How does mold design affect the quality of plastic boxes?
Designing molds goes beyond technical needs. It is an art that influences the quality of plastic boxes. Mold design shapes their quality. Thoughtful design creates exceptional products. This matters to everyone.
Mold design affects plastic box quality by influencing material flow, cooling speed, and strength. Factors like gate design and separation surface strategy are crucial, and controlling process parameters enhances product quality.
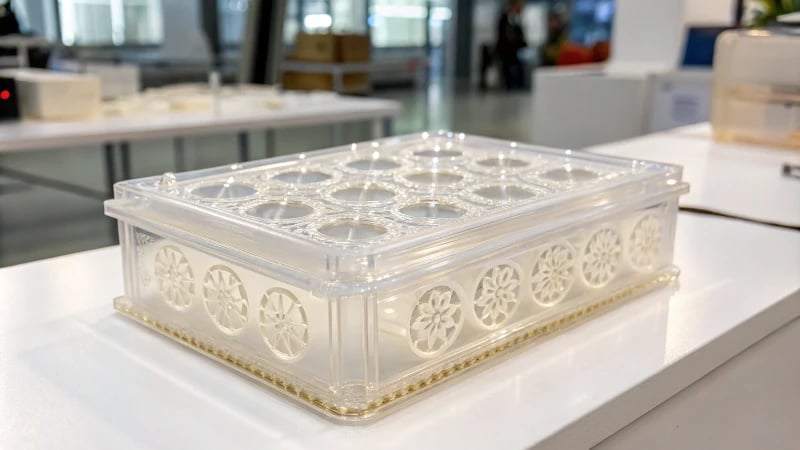
Understanding Mold Design Principles
Mold design is a critical factor that greatly impacts the quality of plastic boxes. The design process involves several key elements, including the choice of materials, dimensions, and the intricacies of the mold itself. Each of these aspects plays a role in determining the final quality of the product.
For instance, selecting the right type of plastic is paramount. The properties of the plastic, such as its melting temperature and viscosity, will dictate how effectively it can be molded. A well-designed mold ensures that the plastic is evenly distributed, minimizing defects such as warping or uneven thickness.
Key Factors in Mold Design
-
Parting Surface Design
The parting surface must be strategically designed to ensure smooth demolding of the plastic box.- Simple Structures: For straightforward designs, a flat parting surface may suffice.
- Complex Designs: For boxes with intricate features, like undercuts, innovative parting techniques such as sliders or inclined surfaces are required to prevent damage during removal.
-
Gate Design
The gate serves as the entrance for molten plastic into the mold cavity.- Side Gates: Commonly used for uniform filling, ensuring consistent wall thickness.
- Point Gates: Ideal for high-aesthetic applications as they minimize visible marks on the final product.
Each gate type influences how well the material fills the mold and affects surface finish and structural integrity.
Gate Type | Advantages | Disadvantages |
---|---|---|
Side Gate | Even filling, good for thicker walls | May leave marks on visible areas |
Point Gate | Minimal impact on aesthetics | Potential for uneven filling |
Cooling System Design
A properly designed cooling system is vital for maintaining product quality.
- Cooling Channels: These should be designed to ensure even cooling throughout the mold. Options include:
- Linear Channels: Simple but effective for standard shapes.
- Spiral Channels: More complex but beneficial for intricate designs.
An efficient cooling system helps prevent defects such as shrinkage or warping, thereby enhancing the overall durability and appearance of the plastic box.
Process Parameter Control
-
Temperature Control: The right temperature settings during injection molding ensure optimal flow and finish. For example, controlling barrel temperatures based on the specific type of plastic can lead to better melt consistency.
-
Pressure Control: Proper injection pressure is crucial for achieving full cavity fill without defects. Too low pressure may lead to incomplete filling, while excessive pressure can cause material flash.
-
Speed Control: Adjusting injection speed is essential to avoid common issues like air bubbles or weld lines in thicker-walled products like plastic boxes.
In conclusion, each aspect of mold design—from parting surfaces to cooling systems—plays a pivotal role in determining the quality of plastic boxes produced. By paying attention to these design elements, manufacturers can optimize their processes to deliver high-quality products.
Proper mold design minimizes defects in plastic boxes.True
Effective mold design ensures even material distribution, reducing issues like warping and uneven thickness, thus enhancing the quality of plastic boxes.
Cooling system design has no impact on product quality.False
A well-designed cooling system is crucial for preventing defects like shrinkage or warping, directly affecting the durability and appearance of plastic boxes.
What are the common challenges in the injection molding process?
Injection molding looks like a magic trick. It shapes raw plastic into beautiful products. Problems hide behind this magic. These challenges sometimes confuse us. Let’s dive into these hurdles. Let’s explore ways to solve them!
Injection molding challenges encompass process feasibility, mold design limits, and temperature and pressure control, along with speed management. Addressing these issues is vital for maintaining product quality and enhancing manufacturing efficiency.
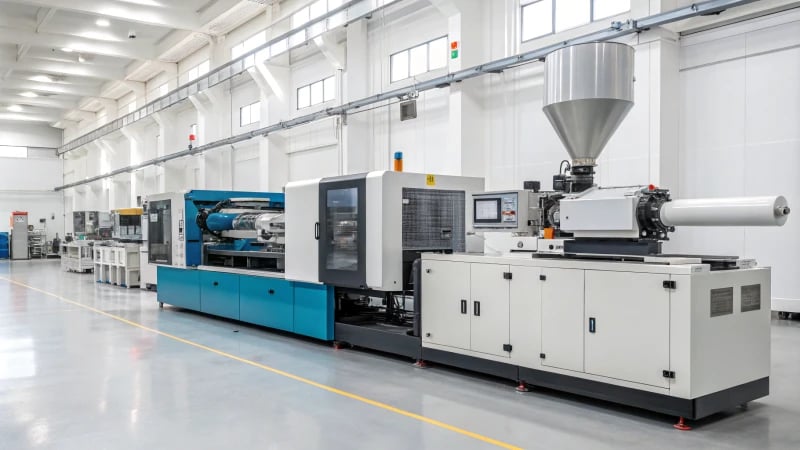
Injection molding is a widely used manufacturing process, yet it comes with its fair share of challenges. Understanding these challenges can help designers and manufacturers mitigate risks and enhance production efficiency.
1. Process Feasibility Challenges
A significant challenge in injection molding is determining if a design can actually be produced. I recall being tasked with creating a unique plastic box with intricate details and undercuts. The excitement was real until I realized that these details might cause problems without a good mold design.
- Mold Design Complexity: Complex designs impact mold costs and production times. Early on, I learned that mastering mold design techniques is key to avoiding delays and problems.
2. Mold Design Constraints
The mold design can create magic but may cause defects if done incorrectly. Key elements must be remembered:
Design Element | Description |
---|---|
Parting Surface | The choice between a simple or complex parting surface affects demolding efficiency and quality. |
Gate Location | The placement of gates influences the flow of plastic and can affect surface finish if not done right. |
Cooling System Design | Adequate cooling channels are essential for uniform cooling, preventing warping and surface defects. |
Explore mold design best practices1 for a deeper understanding.
3. Temperature and Pressure Control
Temperature and pressure control are really important in injection molding. Once, I had a batch of underfilled products because the injection pressure was too low. This experience showed me how vital these settings are for quality products.
Recommended Settings:
Parameter | Recommended Value |
---|---|
Barrel Temperature | 180-220℃ (for PP) |
Mold Temperature | 30-50℃ (for PP) |
Injection Pressure | Varies based on product dimensions |
Learn more about temperature control in injection molding2 for additional insights.
4. Speed Control Challenges
Injection speed can be tricky. I’ve seen wrong speeds lead to bubbles or marks in the final product. This outcome is not desirable after all the design efforts. Additionally, a mold that opens and closes too quickly can wear out faster than expected.
Understanding these parameters allows better planning and execution of the injection molding process, resulting in high-quality outputs without unwanted defects.
By examining these common challenges, I have found ways to improve production and reduce risks in injection molding. For further insights, consider researching common injection molding defects3. Understanding these issues not only betters my designs but also leads to products that meet aesthetic and functional needs.
Mold design complexity affects production cycle time.True
Complex mold designs can increase production time and costs, requiring skilled designers to mitigate challenges effectively.
Temperature control is irrelevant in injection molding.False
Temperature control is crucial; improper settings can lead to defects like underfilling or flash in molded products.
How can you optimize process parameters for better results?
Improving process settings is a journey. It focuses on increasing efficiency and product quality in manufacturing. Practical strategies have helped me get better results in injection molding. Let me share these strategies with you.
Optimize process parameters in injection molding by precisely controlling temperature, pressure, and speed to enhance plastic product quality.
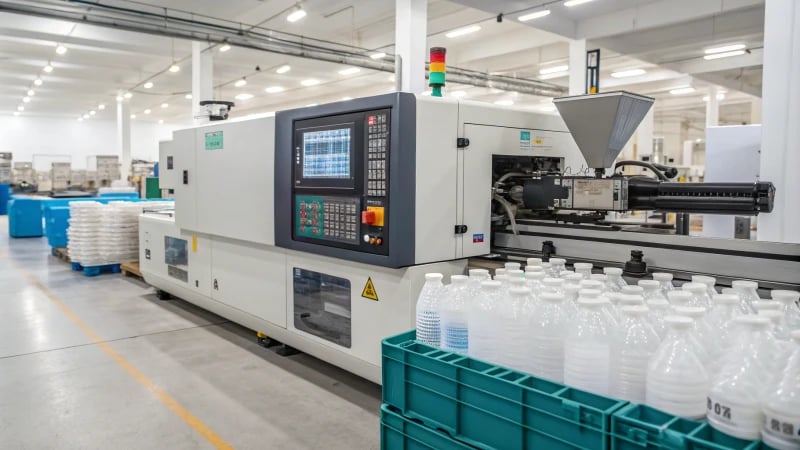
Understanding Process Parameters
To optimize process parameters effectively, one must first understand what these parameters are. In injection molding, the key parameters include temperature, pressure, and speed of injection. Each of these plays a critical role in the production of high-quality plastic products, such as plastic boxes.
For example, setting the barrel temperature correctly is crucial for melting the raw materials fully, which can affect the fluidity of the plastic. Common settings for polypropylene (PP) can range from 180-220℃. Understanding these basics can help identify areas for improvement.
Temperature Control Strategies
Temperature management is vital in achieving optimal results. Here are some strategies:
Parameter | Recommended Range | Purpose |
---|---|---|
Barrel Temperature | 180-220℃ | Ensure full melting and fluidity |
Mold Temperature | 30-50℃ | Improve surface quality of plastic boxes |
Explore more about temperature control methods by looking at temperature control methods4.
Pressure Optimization Techniques
The pressure applied during injection directly affects the final product’s quality. Here’s how to manage it:
- Injection Pressure: It should be tailored based on the product’s dimensions and wall thickness. Insufficient pressure may lead to incomplete filling, while excessive pressure can cause defects like flash.
- Holding Pressure: This is crucial for maintaining density and dimensional accuracy. Proper holding pressure compensates for any shrinkage that occurs during cooling.
Understanding these nuances can significantly impact production outcomes, and delving deeper into pressure optimization5 could provide more insights.
Injection Speed Considerations
The speed at which the plastic is injected also influences product quality:
- An appropriate injection speed helps in evenly filling the mold cavity, preventing issues like bubbles or weld lines.
- Managing the mold opening and closing speed is equally important. While faster speeds improve efficiency, they can also lead to increased wear and tear.
For a more comprehensive guide on this topic, check out injection speed optimization6.
The Role of Mold Design in Parameter Optimization
The design of the mold itself plays a significant role in optimizing process parameters. Key aspects include:
- Parting Surface Design: A well-designed parting surface can facilitate easier demolding, particularly for complex shapes like plastic boxes with undercuts.
- Gate Design: Choosing the right type of gate, such as side gates or point gates, can impact how evenly the plastic fills the mold, which in turn affects quality and appearance.
- Cooling System Design: A proper cooling system layout ensures uniform cooling, preventing warping or deformation.
Each of these elements interacts with process parameters to enhance overall efficiency. To learn more about mold design considerations7, explore specialized resources.
Temperature control is critical for high-quality plastic products.True
Proper temperature management ensures full melting and fluidity of materials, affecting product quality significantly.
Faster injection speeds always improve product quality.False
While faster speeds enhance efficiency, they may lead to defects like increased wear or bubbles in the product.
Conclusion
Explore how injection molding machines efficiently create plastic boxes through precise temperature, pressure control, and innovative mold design techniques.
-
Learn how to address common injection molding challenges effectively for improved production outcomes. ↩
-
Explore best practices in mold design to overcome typical issues faced during the injection molding process. ↩
-
Discover key factors affecting temperature control in injection molding to enhance product quality. ↩
-
Explore methods to refine your manufacturing processes, leading to improved efficiency and product quality. ↩
-
Learn about effective pressure management techniques to enhance product quality and reduce defects. ↩
-
Understand the importance of injection speed and its impact on manufacturing outcomes. ↩
-
Find out how mold design influences process optimization and product quality. ↩