Have you ever thought about how small changes in injection molding might change your product’s weight?
Product weight in injection molding depends on factors like injection volume, pressure, speed, melt temperature and mold temperature. Changing these factors affects the weight. This change influences the final product.
I remember starting in injection molding. It felt like figuring out a dance between science and art. Every factor, like screw stroke or mold warmth, tells a story in shaping the final item. Understanding this is not just about getting the right size but about creating a process that balances speed and quality.
Think about the screw stroke. Like a conductor, it controls how much plastic goes into the mold. A small increase adds weight to the product. But this is just one part of a bigger play. Adjusting pressure and speed adds precision. It fills every corner without extra pressure. But too much can cause flaws, like flash marks. Flaws remind me there’s more to learn.
Holding parameters are next. Like a careful parent, they keep pressure and time right so the product doesn’t shrink during cooling. They add a little push at the perfect moment. Understanding how melt temperature affects flow was like finding a missing piece. A small change improves flow, filling the mold better.
Mold warmth wraps up this dance. A cooler mold stiffens quickly and stops filling. A warmer mold helps transitions, like how a warm talk opens doors.
Each change is a step to mastering this skill. It’s a journey of adjustment that mirrors my growth. By changing these factors, we achieve the right size and also create an efficient process. We craft items that meet design goals and work well.
Increasing injection volume increases product weight.True
More material injected into the mold results in a heavier product.
Higher mold temperature decreases product weight.False
Higher mold temperatures can lead to better flow, filling more volume.
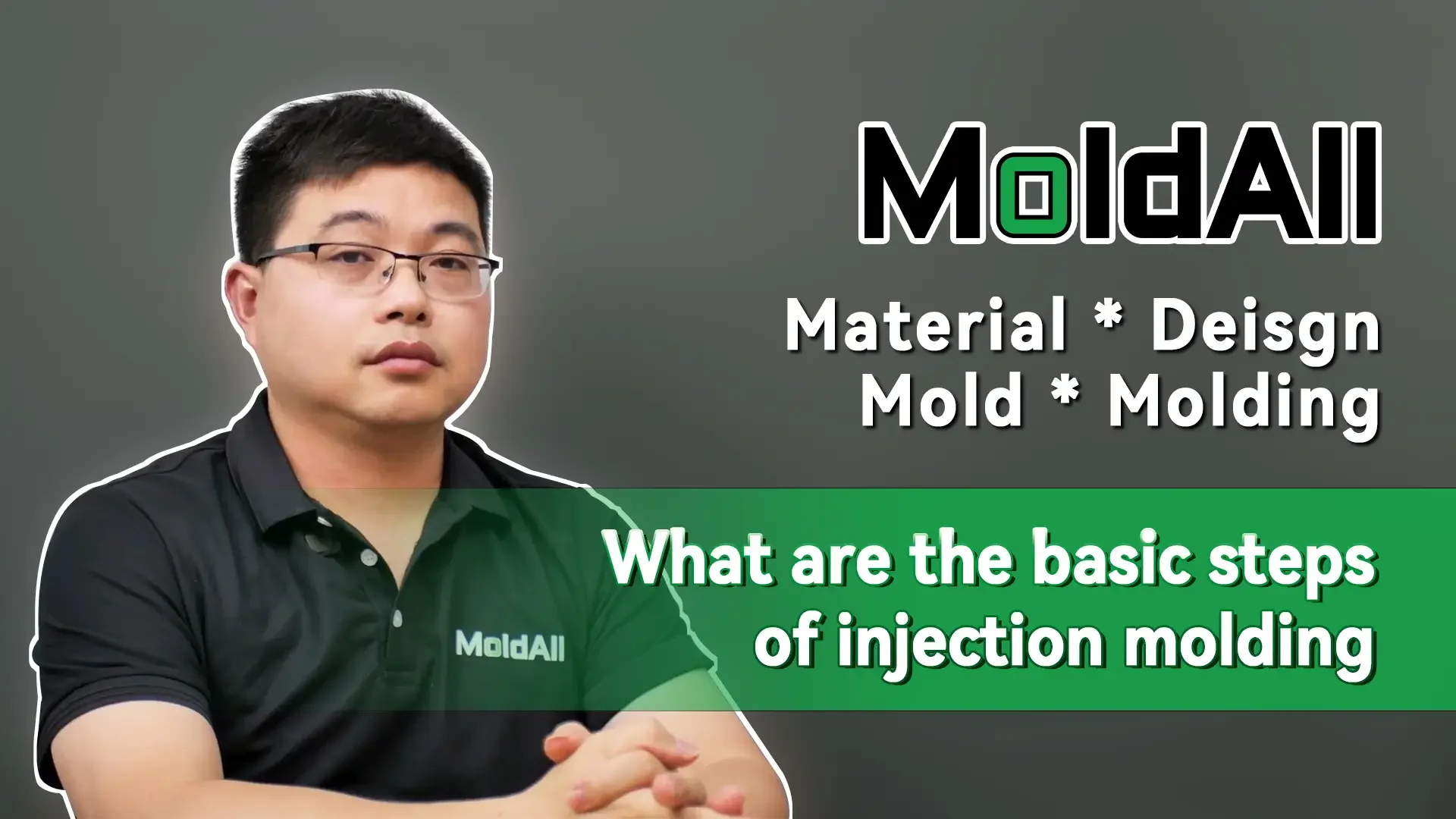
How Does Screw Stroke Influence Product Weight?
Do you ever think about how a small change in a machine affects the weight of your products?
Screw stroke acts like the heartbeat of an injection molding machine. It controls how much plastic melt moves into the mold. Adjusting the screw stroke finely tunes the product’s weight. This balance brings the perfect mix of material and quality in every piece. Perfect mix.
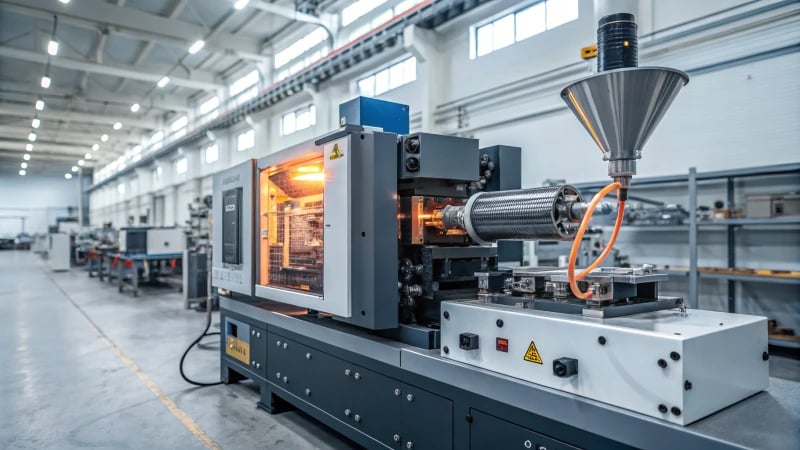
The Mechanics of Screw Stroke
In my early days with injection molding, I watched a machine with fascination. A simple screw movement decided many things. Screw stroke tells how much plastic melt goes into the mold. Important action. This action decides the material used to fill the mold cavity in each cycle.
Picture adjusting the screw stroke like turning a faucet. Open it wider, more water flows, just like a longer stroke means more plastic and a heavier product. Tightening the faucet (shortening the stroke) gets less flow and lighter products. Understanding this is crucial for meeting weight needs.
Parameter | Effect on Product Weight |
---|---|
Screw Stroke Increase | Higher product weight |
Screw Stroke Decrease | Lower product weight |
Interplay with Other Parameters
Injection Pressure and Speed:
Think of blowing up a balloon. Too much air too fast, it might pop or change shape. High injection pressure and speed help the plastic fill the mold well, possibly adding weight. However, excessive pressure1 causes defects, necessitating balance.
Holding Parameters:
Imagine holding parameters like caretaking during cooling. Right holding pressure and time prevent unwanted weight loss due to shrinkage by managing how much plastic melt remains in the cavity.
Temperature Considerations:
When coffee is too hot, you wait for the perfect sip. Melt and mold temperatures influence flow and mold filling. Higher melt temperatures improve flow, maybe increasing weight but very high might lower quality. Maintaining optimal mold temperatures2 assures smooth operations without making it too thick.
Practical Applications
Daily, I control screw stroke like magic. In industries like automotive or aerospace, where weight consistency3 cannot be ignored, adjustments matter for matching strict standards.
By knowing screw stroke details and how they connect to other factors, design quality and production efficiency improve. The goal is high-quality results, time and again, with perfect balance in every product.
Longer screw stroke increases product weight.True
A longer screw stroke allows more material into the mold, increasing weight.
Higher injection speed decreases product weight.False
Higher injection speed can increase product weight by filling molds faster.
How Do Injection Pressure and Speed Affect Product Weight?
Have you ever thought about how changing the pressure and speed of an injection affects a product’s final weight?
Injection pressure and speed are vital for filling the mold cavity. These factors directly affect product weight. High values may help fill the mold. However, if too high, they risk defects. A balance is important. Achieving this balance improves both weight and quality.
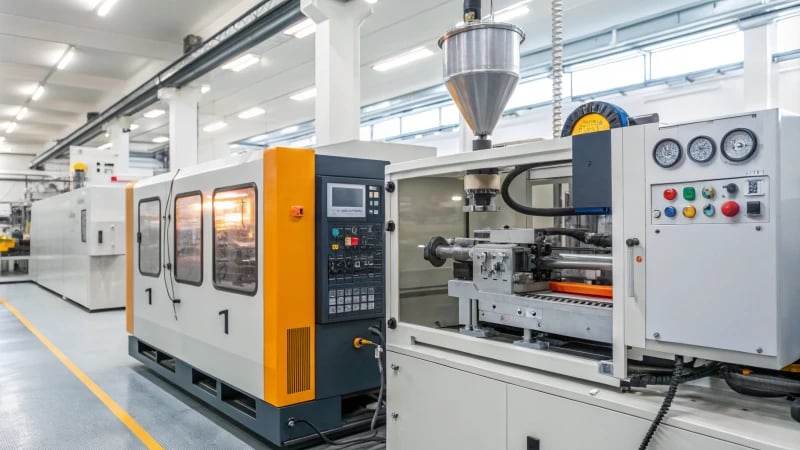
Injection Pressure: The Power Behind the Process
Injection pressure pushes melted plastic into every part of the mold. At first, I thought more pressure was always good. It seemed obvious – more pressure means better fill, right? But too much pressure can spill, just like too much cake batter overflows. This truth comes from experience and trying different methods over time.
Injection Pressure | Effect on Product Weight |
---|---|
Low | Incomplete fill, lighter |
Moderate | Optimal fill, balanced |
High | Full fill, risk of defects |
Understanding the balance required4 is essential for optimal results.
Injection Speed: Rate of Filling Matters
Speed is very important too. Pushing plastic too quickly reminded me of pouring pancake batter too fast – a mess happens. On the other hand, the right pace allows an even, smooth fill without stress or issues.
Injection speed refers to how quickly the plastic melt is pushed into the mold cavity. A higher speed can lead to a more complete fill but may cause issues such as material degradation. Therefore, careful control5 of speed is crucial.
Balance Between Pressure and Speed
Pressure and speed working together is like finding the perfect balance in a recipe. Important factors include screw stroke, which decides how much material goes into the mold each time and holding parameters that keep the mold’s shape after injection.
- Screw Stroke: Connects to how much is injected.
- Holding Parameters: Influence post-injection form.
- Cooling Rates: Affect shrinkage and weight.
The combination of these parameters impacts overall effectiveness and requires considering other factors like holding parameters6 and cooling rates.
Practical Ideas for Designers
Designers, like Jacky, work hard to create precise molds. They explore how these factors interact. Filling the mold well also means thinking about melt and mold temperatures. These temperatures change the flow and product weight. By choosing the right settings, both appearance and function meet high standards without losing efficiency or quality.
For designers like Jacky, understanding these dynamics is crucial for creating efficient molds that meet production requirements. They must account for various factors such as melt temperature7 and mold temperature to ensure functional and aesthetic goals are achieved without compromising on efficiency or quality.
My journey with MoldAll showed me how changing these elements brings new opportunities. Each project is a learning chance, adjusting settings like a chef perfecting a dish until the molded piece is just right.
Higher injection pressure increases product weight.True
Higher pressure ensures full mold fill, increasing product weight.
Excessive speed prevents material degradation.False
Excessive speed can cause material degradation, not prevent it.
Why Are Holding Pressure and Time Crucial for Product Weight?
Ever thought about why the correct pressure and timing are so crucial in injection molding? These things probably determine the weight and quality of the finished product. Let’s explore how these elements play a crucial role.
Holding pressure and time are vital in injection molding. They assist the plastic melt in reducing shrinkage, which helps keep the product weight stable. Correct calibration stops flaws. Consistent quality stays the same during production.
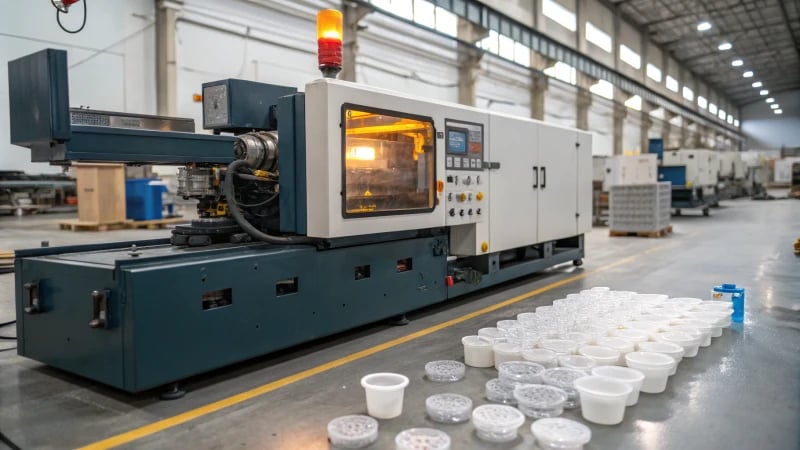
Understanding the Role of Holding Pressure
Picture packing your suitcase for a big trip. You press down to fit everything neatly, just like holding pressure in injection molding. This pressure keeps the material tight in the mold right after injection. It fills gaps as the material cools and shrinks. Not enough pressure might leave you with a lighter product than planned, like forgetting an extra pair of shoes.
Consider a scenario where an injection molding machine is set with low holding pressure. In this case, cooling causes extra shrinkage, making a lighter product. Conversely, increasing the holding pressure allows more melt to enter the cavity, thereby increasing product weight. However, it’s crucial to balance as excessive pressure can lead to defects such as flash.
Parameter | Effect |
---|---|
Low Holding Pressure | Inadequate shrinkage compensation |
Optimal Holding Pressure | Proper weight maintenance |
High Holding Pressure | Risk of defects like flash |
Importance of Holding Time
Holding time is like baking cookies until they’re just right. You don’t want them undercooked. In molding, holding time sets how long the pressure stays. Longer times help control shrinkage but too long wastes material or slows the process.
Cutting holding time short might not fill the mold fully, reducing weight. By increasing holding time gradually, companies notice a link between longer times and stable product weight stability.
The relationship between holding time8 and product weight can be illustrated by adjusting the holding time in an experimental setup.
Balancing Pressure and Time for Optimal Results
Balancing holding pressure and time is vital for quality in injection molding. Higher pressure helps with shrinkage but avoid defects like flashing by finding a balance.
- Melt Temperature Influence: Higher melt temperature improves flow, maybe reducing holding pressure needs.
- Mold Temperature Factors: Changing mold temperature affects cooling rates, influencing both pressure and time settings needed.
Mastering these helps create a steady manufacturing process with consistent product weights. It’s like having the perfect cookie recipe!
Investigate further into melt temperature adjustments9 to see how they impact holding parameters and ultimately product quality.
Low holding pressure leads to lighter products.True
Without enough holding pressure, shrinkage isn't compensated, reducing weight.
Excessive holding time decreases product weight.False
Longer holding time usually increases weight by allowing more material flow.
How Does Melt Temperature Affect Product Weight?
Did you ever think about how the warmth of plastic influences your final product? I want to show you the amazing part melt temperature plays in injection molding.
Melt temperature controls how plastic flows during injection molding. Very high temperatures let plastic flow easily, filling molds better and increasing product weight. However, really high temperatures might cause damage and problems.
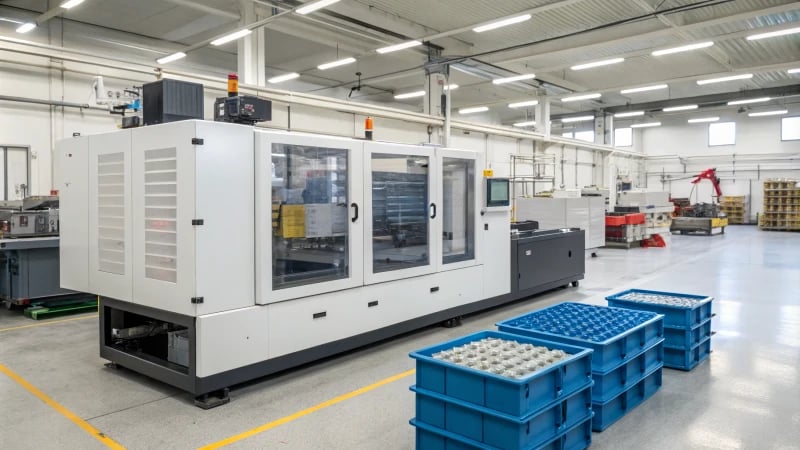
Understanding Melt Temperature and Its Role
Think about baking and how important the oven temperature is for the perfect loaf of bread. In injection molding, melt temperature holds similar importance. When plastic heats to the right level, it flows smoothly into the mold, just like a perfect cake batter spreads in a pan. I once forgot this in a project and it felt like biting into an uncooked cake.
How Melt Temperature Influences Product Weight
Fluidity and Fill
-
Higher Melt Temperature:
- Imagine pouring batter into a cupcake mold; if it’s too thick, it won’t fill properly. Similarly, higher melt temperatures make plastic more liquid, filling the mold better.
- This result often increases product weight.
-
Lower Melt Temperature:
- When batter is cold and thick, it doesn’t spread well. With lower melt temperatures, plastic becomes less fluid and might not fill the mold fully.
- This leads to lighter products as less material fills the space.
Risks of Excessive Melt Temperature
Raising the heat too much is tempting, but danger lurks. Excessively high temperatures can damage the plastic, similar to overbaking a cake that becomes a hard, inedible lump. In molding, too much pressure can cause overflow, known as flash.
Parameter | Effect on Weight | Considerations |
---|---|---|
Higher Melt Temperature | Increases weight | Risk of degradation and potential for flash |
Lower Melt Temperature | Decreases weight | Potential for incomplete filling |
Optimizing Melt Temperature
Finding the right melt temperature is a skill, not just a dial adjustment. It is something learned through practice and patience, balancing temperature with factors like injection pressure and speed—just as a skilled chef balances flavors.
- Adjust injection pressure and speed with the temperature settings for ideal flow.
- Keep an eye on holding pressure and time to combat shrinkage—similar to letting a loaf cool properly.
- Remember the overall mold temperature10; it’s like preheating your oven—it affects cooling rate and viscosity.
Finding this balance is crucial. Consider it a symphony with each part finely tuned for best results. Over time, I learned this skill by always aiming to meet product standards while reducing waste. Understanding these dynamics really helps improve efficiency and quality.
While melt temperature is key, it must work with other factors like injection volume parameters11 and holding parameters for successful results.
Conclusion
It’s intriguing how temperature affects product weight. By combining this knowledge with process changes, we achieve not only the right weight but also improve quality while cutting costs. This mix of science and art fuels my passion for molding—constantly driving me to hone my methods. As we make strides in this field, I’m eager to see what new areas await us next! Keep experimenting and learning—that’s where the magic happens! Happy molding!
Higher melt temperatures increase product weight.True
Increased fluidity allows more material to fill the mold, raising weight.
Lower melt temperatures prevent product degradation.False
While lower temperatures reduce degradation, they risk incomplete filling.
How does mold temperature influence product weight?
Do you ever ask yourself why your molded products differ in weight even when everything appears perfect?
Mold temperature really changes product weight. It does this by altering how fast the plastic cools and flows. Warmer molds probably let plastic spread more, creating heavier items. On the other hand, cooler molds freeze it quickly. This rapid cooling results in lighter products.
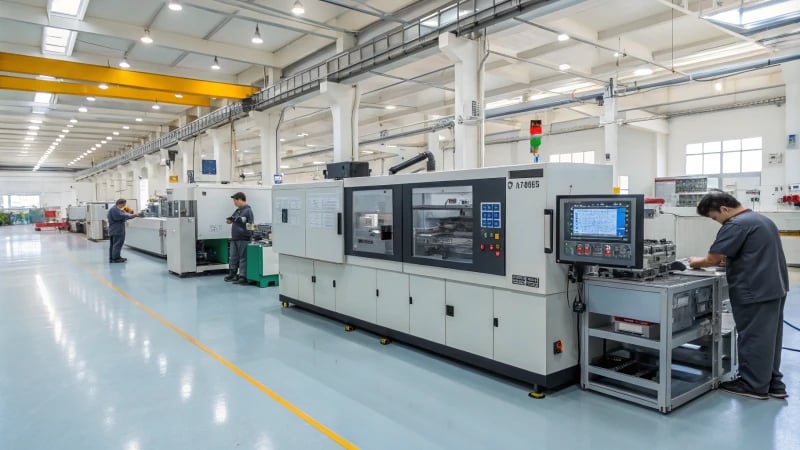
The Role of Mold Temperature
I once began exploring injection molding. There was this project where our phone cases turned out with different weights. I couldn’t understand why. It puzzled me until my mentor highlighted something key: mold temperature. It’s amazing how this small detail can decide if your product feels solid or weak.
In the injection molding process, mold temperature determines how quickly the plastic melt cools and solidifies. A higher mold temperature keeps the plastic fluid longer, enhancing its flowability. This increased fluidity ensures the mold cavity is completely filled, potentially increasing product weight.
Cooling and Flow Dynamics
-
High Mold Temperature:
- Enhanced Flow: More heat allows the plastic to stay liquid longer and fill every mold corner.
- Increased Weight: More material remains in the cavity, resulting in a heavier product.
- Potential Downsides: Watch out! Excess heat might cause warped forks or spoons that won’t stack well.
-
Low Mold Temperature:
- Rapid Cooling: The plastic hardens fast, possibly leaving some mold areas unfilled.
- Decreased Weight: Less material results in a lighter item.
Temperature | Effect on Product Weight |
---|---|
High | Increased due to enhanced flow |
Low | Decreased due to rapid cooling |
Adjusting Injection Molding Settings
Although mold temperature is crucial, it doesn’t act alone. Changing injection settings12 can alter the weight too. I remember increasing the screw stroke slightly once. It felt magical! The product weight increased as more material got injected. Likewise, adjusting injection pressure and speed helps cover the mold better.
Considering Holding Settings
In the holding phase, balance is important. I remember a project where changing the holding pressure was key. Keeping pressure while cooling ensures extra material fills the mold. Raising both holding pressure and time can bulk up your item. Really, it’s a delicate balance between holding settings13 and mold temperature that takes real skill.
Mold Temperature and Product Quality
Experimenting with temperature can improve weight, yet quality could suffer. I’ve learned this the hard way! Higher temperatures improve flow but might weaken the plastic materials’ integrity. Lower settings help with stability but might not completely fill the mold cavity effectively for best results14. Finding that perfect balance takes practice; however, nailing it through trial and error can change everything.
High mold temperature increases product weight.True
Higher temperatures enhance flowability, ensuring complete cavity filling.
Low mold temperature results in heavier products.False
Rapid cooling at low temperatures hinders complete filling, reducing weight.
Conclusion
Injection molding parameters like screw stroke, pressure, speed, melt and mold temperatures significantly influence product weight. Adjusting these factors ensures optimal filling and quality in molded products.
-
Explore how excessive injection pressure can lead to defects such as flashing and warping, which impact product quality. ↩
-
Learn about optimal mold temperatures to ensure proper flow and filling during injection molding processes. ↩
-
Discover strategies for enhancing design efficacy, crucial for producing consistent and high-quality molded products. ↩
-
Learn techniques to achieve optimal injection pressure, avoiding defects while ensuring full mold filling. ↩
-
Discover methods for managing injection speed to enhance product quality without causing defects. ↩
-
Explore why holding parameters are crucial for maintaining product weight during molding. ↩
-
Understand how adjusting melt temperature impacts material flow and product weight. ↩
-
Explore how varying holding times affect product weight stability and quality in injection molding. ↩
-
Learn how adjusting melt temperature can optimize holding parameters for better product quality. ↩
-
Explore how mold temperature affects cooling rate and viscosity, impacting final product weight. ↩
-
Find actionable strategies to enhance injection molding efficiency and product quality through parameter optimization. ↩
-
Explore how various injection molding parameters like screw stroke and pressure influence product weight. ↩
-
Understand the role of holding pressure and time in enhancing product weight during injection molding. ↩
-
Discover best practices for determining optimal mold temperatures that balance product weight and quality. ↩