Ever wondered how those handy nylon cable ties hold everything together so perfectly?
An injection molding machine produces nylon cable ties by heating and injecting molten nylon into a mold, ensuring durability and flexibility through precise mold design, material selection, and cooling processes.
Thinking back to my first encounter with the intricacies of mold design, I remember feeling both awe and a bit of intimidation. It’s fascinating how these molds, like a meticulous architect’s blueprint, dictate the strength and flexibility of something as seemingly simple as a cable tie. Each tiny detail, from the cavity shaping the tie’s body to the teeth in its locking mechanism, plays a critical role.
Choosing the right material was another revelation. Nylon is not just chosen at random; its tensile strength and flexibility are precisely what make it perfect for withstanding pressure without snapping. This was a game-changer for me in understanding why material selection is key.
The actual injection process is an art in itself. I recall standing next to the humming machine, watching as molten nylon was injected into the mold at exact temperatures. It’s this process that transforms raw nylon into the sleek, reliable ties we depend on daily. After cooling, they’re ready to be used—or occasionally undergo a little smoothing to make sure they’re cable-friendly.
Every step in this journey from design to production reveals just how much care goes into crafting these indispensable tools.
Nylon cable ties are made from melted nylon material.True
Injection molding involves melting nylon to form cable ties.
Cooling is unnecessary in the injection molding process.False
Cooling is essential for solidifying the molded nylon shape.

- 1. What Makes Mold Design Crucial for Cable Ties?
- 2. Why is Nylon the Preferred Material for Cable Ties?
- 3. What Steps are Involved in the Injection Molding Process?
- 4. How Does Cooling Affect the Quality of Nylon Cable Ties?
- 5. Are There Any Necessary Post-Processing Steps for Cable Ties?
- 6. Conclusion
What Makes Mold Design Crucial for Cable Ties?
Mold design for cable ties is like crafting the perfect tool for every tight spot. Let me walk you through the essentials that make these everyday heroes as durable and reliable as they are.
Mold design is vital for cable ties, focusing on precise cavity creation, material selection (e.g., Nylon 6/6), and optimizing the injection molding process for efficiency and accuracy.
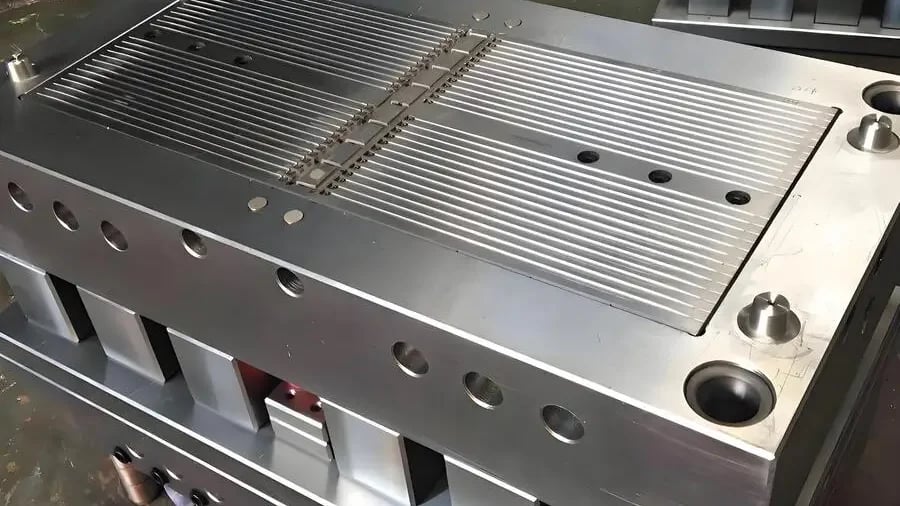
Understanding Mold Design for Cable Ties
When I first delved into mold design, I was fascinated by how each detail mattered, especially with something as common yet vital as cable ties. The mold must shape these long, slender pieces with meticulous precision. It’s not just about forming their body but also crafting the intricate head with a ratchet mechanism that ensures a secure lock. Every time I see a perfectly aligned set of teeth and pawl, I remember those late nights at the factory, adjusting and readjusting until everything clicked perfectly.
The precise alignment1 of teeth and pawl structures is essential for the tie’s locking function.
Material Selection: Nylon’s Role
Choosing the right material is a lot like choosing a partner for life—it needs to be resilient, flexible, and dependable. Nylon 6 and Nylon 6/6 fit this bill perfectly for cable ties. Their high tensile strength and excellent flexibility remind me of how they hold up under pressure without breaking a sweat. And let’s not forget their chemical resistance, which makes them so versatile in various environments. Back in my early days, I remember testing different materials and feeling the thrill when we finally found that nylon was the answer.
Property | Nylon 6 | Nylon 6/6 |
---|---|---|
Tensile Strength | High | High |
Flexibility | Excellent | Excellent |
Resistance | Strong | Strong |
Injection Molding Process
Think of the injection molding process as baking a cake—you heat up your ingredients (in this case, nylon) until they’re just right before pouring them into a mold. For Nylon 6, it’s heated to 220 – 250°C, and for Nylon 6/6, it’s 260 – 290°C. Then comes the art of maintaining the perfect pressure to fill the mold completely, compensating for shrinkage as it cools. Watching the nylon solidify into a perfectly shaped cable tie is like seeing your cake rise just right in the oven.
Understanding this process2 can significantly enhance production efficiency and product quality.
Post-Processing Needs
Once during a project, I realized how crucial post-processing can be. Imagine having a great product but with slightly rough edges—those need smoothing out to ensure safety and quality. Most ties are ready to go after ejection, but sometimes those finishing touches can make all the difference.
Explore post-processing techniques3 for improving product quality and safety standards.
Together, these elements create an efficient production process, ensuring every cable tie meets expectations. By focusing on these key factors, designers like Jacky can optimize mold designs for better outcomes.
Nylon 6/6 is more flexible than Nylon 6.False
Both Nylon 6 and Nylon 6/6 have excellent flexibility, as per the table.
Injection molding requires holding pressure.True
Holding pressure ensures complete filling of the mold and compensates for shrinkage.
Why is Nylon the Preferred Material for Cable Ties?
Ever wondered why nylon is the star of the show when it comes to cable ties?
Nylon is favored for cable ties due to its high tensile strength, flexibility, and resistance to abrasion and chemicals, ensuring durability and reliability across diverse environments.
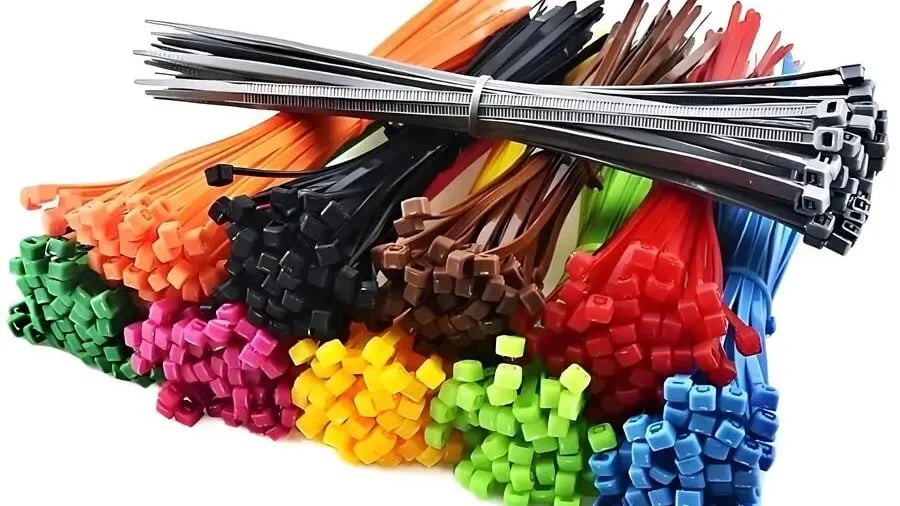
I remember the first time I had to organize a tangled mess of cables behind my desk. It was a daunting task until I discovered nylon cable ties. Their strength and flexibility were impressive, and I couldn’t help but wonder what made them so effective. Let’s dive into the reasons why nylon stands out.
High Tensile Strength and Flexibility
One of the first things I noticed about nylon cable ties was their ability to hold everything securely without any sign of strain or breakage. The high tensile strength of nylon ensures that once the cables are bundled, they stay put. Plus, the flexibility meant I could twist and turn them to fit different needs without a hitch. It’s like they adapt to whatever challenge you throw at them.
Resistance to Abrasion and Chemicals
I learned that nylon 6 and nylon 6/6 are particularly tough against wear and tear, which is a game-changer for demanding environments. Whether it’s the constant friction or exposure to various chemicals like oils or solvents, these cable ties don’t back down. Their resilience is crucial for anyone working in industries where such conditions are a daily reality.
Property | Nylon 6 | Nylon 6/6 |
---|---|---|
Melting Point | 220-250°C | 260-290°C |
Chemical Resistance | Excellent | Excellent |
Abrasion Resistance | High | High |
Mold Design and Injection Molding Process
Creating these handy tools involves a fascinating process that starts with mold design. It needs precision to shape both the body and the ratchet mechanism. I once visited a factory where they used an injection molding machine4—heating nylon to just the right temperature before injecting it into molds. Watching the transformation from molten liquid to a solid, robust tie was mesmerizing.
Practical Applications in Various Industries
Nylon cable ties are everywhere—from construction sites to electrical panels. Their versatility makes them invaluable across industries. I’ve seen them used to tidy up server rooms and even in creative projects. They truly are a testament to nylon’s superior properties, which designers like Jacky5 leverage in creating efficient solutions.
Nylon cable ties have high tensile strength.True
Nylon's tensile strength allows it to hold cables securely without breaking.
Nylon 6/6 has a lower melting point than Nylon 6.False
Nylon 6/6 has a higher melting point (260-290°C) than Nylon 6 (220-250°C).
What Steps are Involved in the Injection Molding Process?
Injection molding might sound technical, but it’s like baking the perfect cake – every step matters! Let’s dive into the stages that transform raw materials into useful plastic products.
The injection molding process includes designing a mold, selecting material, injecting melted material, cooling, solidification, and ejecting the product, ensuring high-quality plastic products.
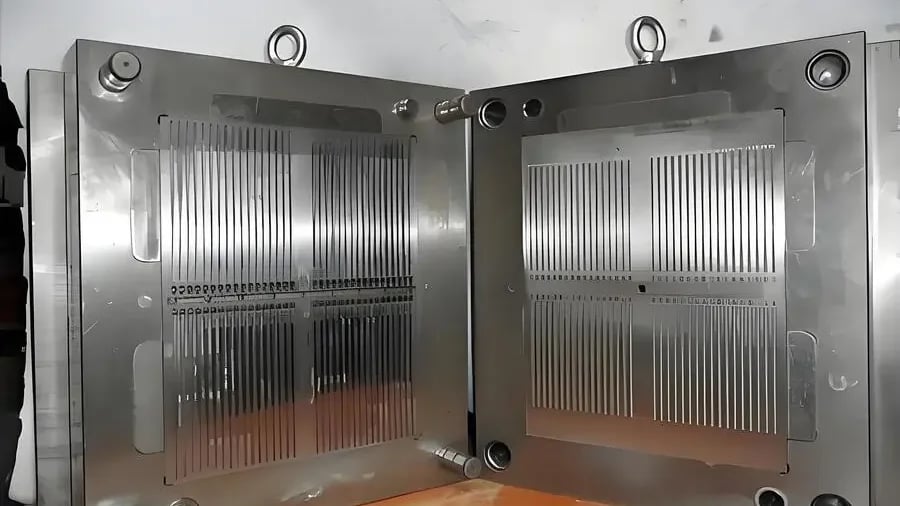
Mold Design
The magic begins with mold design, a process I liken to crafting a custom cookie cutter. Every detail counts. Imagine needing a mold for nylon cable ties; it’s got to nail the thin, long shape and the intricate locking mechanism. I once designed a mold for a client who was super particular about the dimensions—talk about nerve-wracking! But seeing the final product fit perfectly was worth every sleepless night.
Component | Considerations |
---|---|
Body | Flat, narrow profile |
Head | Includes teeth and pawl |
Material Selection
Choosing the right material feels like picking ingredients for a recipe. Nylon 6 or Nylon 6/6 often get the nod for their strength and flexibility. These materials remind me of how adaptable my trusty old hiking boots are—they handle every condition thrown at them, much like these nylons do across various environments. Understanding these properties helps in choosing the best material6 for your specific application.
Injection Process
Now comes the part where we heat things up! The nylon is fed into the machine, reaching its melting point—around 260°C for Nylon 6/6. I remember the first time I watched this process; it was like watching an artist pour molten glass. The pressure fills every crevice of the mold, ensuring every detail is captured.
Understanding these steps not only highlights the precision involved in injection molding7 but also underscores why each phase is essential for achieving quality in plastic manufacturing.
Cooling and Solidification
Patience is key here. The cooling stage is like letting a freshly baked cake sit before you slice it—too soon, and you risk a mess. Proper cooling ensures our piece doesn’t warp and stays dimensionally stable.
Ejection of Finished Part
Finally, the moment of truth. When that mold opens and the part is ejected, it’s akin to unveiling a masterpiece. For something like nylon cable ties, there might be some post-processing, like smoothing edges. I’ve seen how smoothing those little details can make all the difference.
Mold design is the last step in injection molding.False
Mold design is the first step, crucial for product specifications.
Nylon 6/6 melts at approximately 260°C.True
The injection process heats Nylon 6/6 to its melting point of 260°C.
How Does Cooling Affect the Quality of Nylon Cable Ties?
Remember the last time you struggled with a brittle cable tie snapping? It all boils down to the cooling process.
Proper cooling of nylon cable ties ensures optimal mechanical properties, such as tensile strength and flexibility, by preventing warping and enhancing durability.
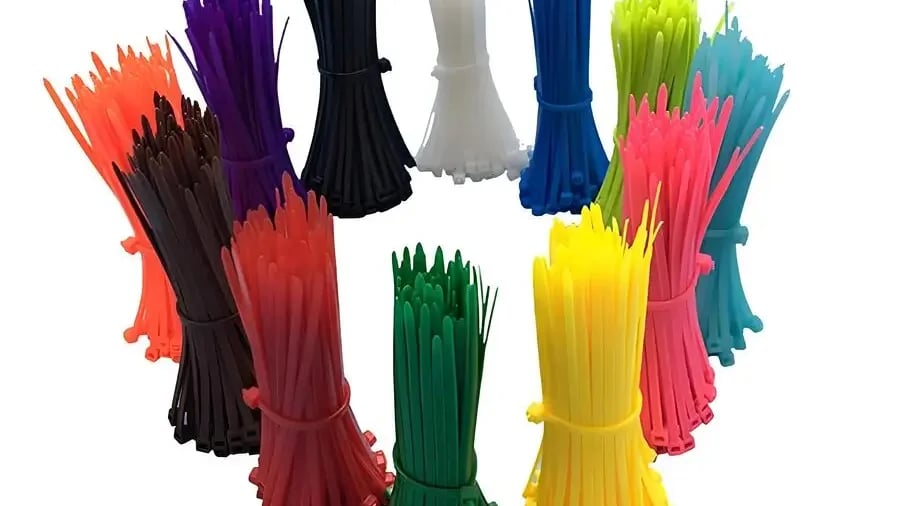
I remember my first encounter with the intricacies of cable ties during a project. It was one of those moments where every snapped tie felt like a mini crisis. I later learned that the secret behind their strength and flexibility lies in the cooling process during manufacturing.
The Role of Cooling in the Injection Molding Process
In the injection molding process8, nylon is heated into a molten state, then injected into a mold. Once injected, the cooling phase begins. This phase is crucial, as it determines how well the nylon solidifies into a sturdy cable tie.
Importance of Cooling Time:
Factor | Impact |
---|---|
Rapid Cooling | May lead to internal stresses and brittleness |
Slow Cooling | Ensures uniformity and reduces warping |
I can’t stress enough how finding that sweet spot in cooling time makes all the difference in avoiding defects.
Cooling’s Impact on Mechanical Properties
- Tensile Strength: Proper cooling ensures high tensile strength, which is crucial for cable ties9 to hold under tension without breaking.
- Flexibility: Adequate cooling keeps ties flexible, avoiding brittleness from uneven cooling.
Environmental Factors and Cooling
During one of my outdoor installations, I realized how cooling impacts performance in different environments:
- Outdoor Settings: Here, ties need a cooling process that boosts resistance to temperature swings, preventing early degradation.
- Electrical Installations: In these setups, cooling affects heat management, ensuring ties don’t melt or deform under electrical currents.
These insights underline why cooling is a pivotal step in making reliable nylon cable ties. If you’re curious about material selection and mold design, check out nylon material properties10.
Rapid cooling increases brittleness in nylon cable ties.True
Rapid cooling can lead to internal stresses, making the ties brittle.
Slow cooling decreases tensile strength of nylon cable ties.False
Slow cooling helps maintain high tensile strength by reducing warping.
Are There Any Necessary Post-Processing Steps for Cable Ties?
Cable ties might seem straightforward, but have you ever wondered if they need a bit of TLC after being molded? Let’s dive into what really happens when these unsung heroes of organization are freshly made.
Post-processing for cable ties typically involves minimal steps like smoothing sharp edges to prevent cable damage, with most ties usable straight from the mold.
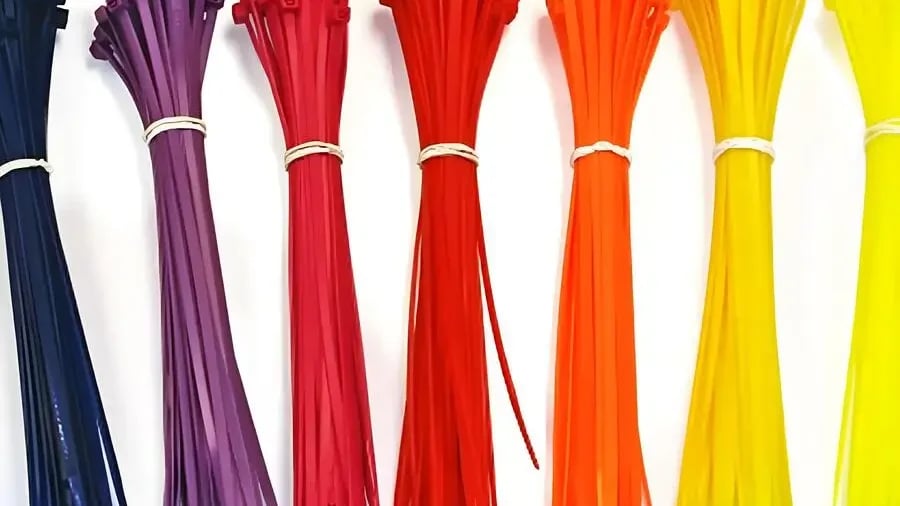
Understanding Cable Tie Production
Let’s talk about how these handy little tools come into existence. Imagine a busy injection molding machine buzzing away, turning plain old nylon into the cable ties we can’t live without. It all starts with a precisely designed mold that shapes the tie and its locking mechanism. The nylon heats up, melts down, and is then pressured into the mold, where it cools and solidifies. It’s kind of like baking, but at much higher temperatures!
When Post-Processing is Necessary
Now, let me share a little tidbit from my own experiences. I remember visiting a manufacturing floor and seeing a batch of cable ties getting a quick makeover. They were smoothing out edges to make sure nothing would snag or scratch. This process is crucial when ties are used in sensitive environments where even the tiniest nick can be a problem.
- Edge Smoothing: Sharp edges can damage cables, so manufacturers sometimes smooth them out11 for safety.
- Quality Inspection: Just like how you’d check the icing on a cake, a thorough inspection ensures each tie meets high standards.
Factors Influencing Post-Processing Decisions
- Material Quality: Good nylon means less fuss later.
- Intended Application: Extra care if they’re going to delicate places.
- Environmental Resistance: Testing for UV resistance is key for outdoor use.
Comparing Post-Processing Requirements
Process Step | Necessary for Cable Ties? |
---|---|
Edge Smoothing | Sometimes |
Quality Inspection | Often |
UV Resistance Test | Depends on use |
For further reading on edge treatments, see industry standards12.
Practical Considerations for Designers
Designers like Jacky know this dance well. With ten years in the field, Jacky’s learned that post-processing is more than just a step—it’s about ensuring product durability and client happiness. He balances the benefits of these steps with the costs and time involved, always looking for ways to optimize and satisfy.
By understanding these nuances, professionals can fine-tune their designs and stay ahead of client needs. For more on design strategies, check out these tips13.
Cable ties always require edge smoothing post-molding.False
Edge smoothing is sometimes necessary, but not always required.
Quality inspection is often needed for cable ties.True
Quality inspection ensures ties meet industry standards and are defect-free.
Conclusion
Injection molding machines produce nylon cable ties through precise mold design, material selection, and controlled cooling processes, ensuring durability and flexibility for various applications.
-
This link elaborates on aligning teeth and pawl structures, crucial for effective cable tie functionality. ↩
-
Understanding these steps enhances efficiency and quality in cable tie production. ↩
-
Discover techniques to refine molded products, ensuring higher safety and performance standards. ↩
-
Understand the detailed process of molding nylon into durable cable ties through injection techniques. ↩
-
Learn how designers like Jacky optimize nylon’s properties for creating efficient, reliable products. ↩
-
Learn about different types of nylon and their specific properties to make informed material choices. ↩
-
Explore detailed steps involved in injection molding to better understand each phase of this manufacturing process. ↩
-
This link explains the injection molding process, helping you understand each step involved in manufacturing nylon cable ties. ↩
-
Learn about the mechanics behind cable ties and their applications in various settings. ↩
-
Explore detailed properties of different types of nylon used in cable ties for better material selection. ↩
-
Smoothing sharp edges enhances safety by preventing potential damage during use. ↩
-
Understanding industry standards ensures that products meet quality benchmarks. ↩
-
Durability-focused design tips can enhance product longevity and user satisfaction. ↩