Have you ever thought about how those detailed plastic items we use every day are made? Injection molding changes the way things are manufactured. I am really excited to explore its wonders with you!
Injection molding is essential in manufacturing, enabling efficient, high-speed production of precise, complex plastic parts crucial for industries like automotive and consumer electronics.
I have traveled through the world of manufacturing. I have seen the wonders of injection molding. This process is not only about creating plastic shapes. It crafts precision and quality that people often overlook. Once, when designing car interior parts, I felt amazed. The mold cavity replicated every curve and compartment perfectly. It resembles sculpting but brings mass production to an art form.
In this blog, we explore the depths of injection molding. The process shapes product development. It promises quality and improves overall efficiency in manufacturing. Join me on this exciting journey!
Injection molding enhances production rates in manufacturing.True
This claim highlights how injection molding significantly increases the speed of production, making it essential for various industries.
Injection molding is only used in the automotive industry.False
This claim is false as injection molding is utilized across multiple industries, including consumer electronics and more.
How Does Injection Molding Impact Product Design?
Do you wonder how injection molding shapes everyday products? This process is fascinating. It influences everything from tiny gadgets to big car parts. Let’s explore its effect on product design.
Injection molding impacts product design by dictating shapes through mold geometry, ensuring quality with cooling systems, enhancing efficiency with reusable molds, and requiring designs to balance aesthetics and functionality.
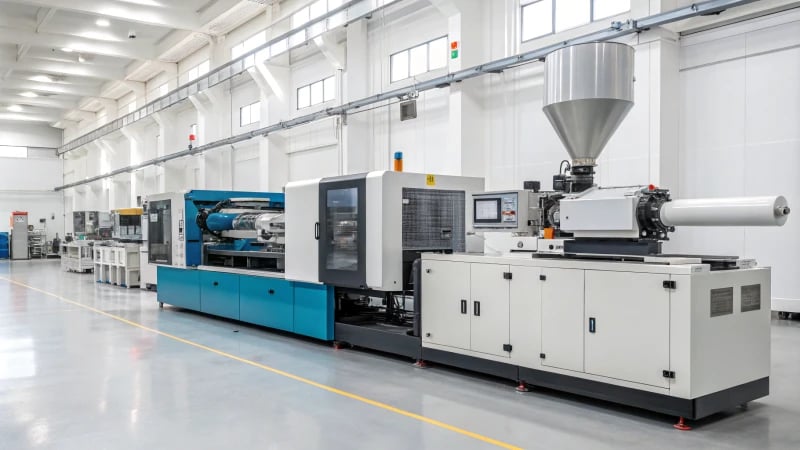
The Role of Mold Design in Shaping Products
Injection molding greatly changes product design, impacting shape, quality, efficiency and function. It’s incredible how a simple mold influences a design’s success. I worked on ergonomic kitchen tools where mold geometry captured smooth curves, pleasing to look at and comfortable to hold. The mold controls everything – shape, fit and even how fun it is to use!
Mold design shapes the core of our products. The mold cavity acts as a blueprint for creation. A carefully planned mold allows complex shapes that decide a product’s usefulness. For instance, designing a car’s center console mold involved considering curves and button spots. It was vital for perfect assembly fit.
Moreover, the precision of the mold affects the dimensional accuracy of the produced parts. I worked on molds for precision electronics needing micron-level tolerances! It was challenging, but seeing tiny details creating flawless products felt rewarding.
Quality Control Through Mold Features
Quality control shines in injection molding. The cooling system integrated into the mold keeps designs intact. Uneven cooling caused warping in large items like plastic sheets. I learned using cooling channels that match the mold’s shape avoids defects and makes high-quality parts.
Feature | Effect | Example |
---|---|---|
Cooling System | Prevents warping | Large plastic sheets |
Ejection Mechanism | Ensures smooth demolding | Thin-walled products |
The ejection mechanism releases products smoothly without damage. In a thin-walled container project, improper ejection risked breaking them. Techniques like push plate ejection solved such challenges.
Enhancing Production Efficiency
Injection molding excites with its production efficiency. A designed mold keeps creating identical parts swiftly once set. A well-tuned mold for plastic bottle caps could produce hundreds per minute! It’s magical to see on the factory floor.
Additionally, the structure of the mold can directly influence cycle times. Hot runner systems drastically cut cooling times, speeding up and cutting production costs.
Balancing Aesthetics and Functionality
Finally, balancing looks and function is crucial in product design through injection molding’s impact on aesthetics and functionality. Mold design can improve both product appeal and usability by incorporating textures that enhance grip or visual appeal without compromising performance.
Understanding injection molding’s impact on shape, quality and efficiency is central to my designer journey. This knowledge allows creating better products that meet both aesthetic and functional needs—leading to innovative designs users love.
Injection molding enhances production efficiency through reusability.True
Reusability of molds allows for the rapid production of identical parts, improving manufacturing efficiency.
Cooling systems in molds prevent product warping during production.True
Well-designed cooling systems ensure uniform cooling, preventing warping and maintaining product integrity.
What Are the Key Factors for Ensuring Quality in Injection Molding?
Have you ever wondered how those perfect plastic parts are created? The world of injection molding is complex. I am excited to talk about the important things needed for quality production. Let’s explore this interesting process together!
Ensuring quality in injection molding involves precise mold design, effective cooling to prevent warping, reliable ejection for safe demolding, and optimized production practices for consistency.
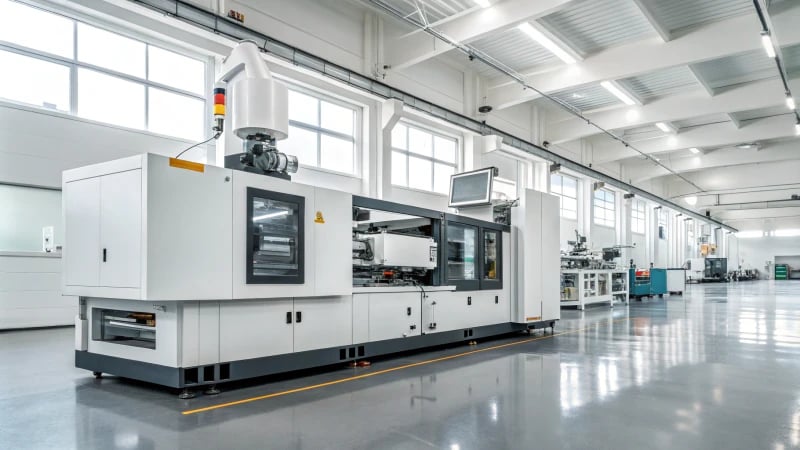
Injection Molding: Key Factors for Quality
Injection molding is a complex process where several factors converge to determine the quality of the final product. Understanding these key factors is essential for ensuring high-quality output. Let’s explore the most critical aspects that influence injection molding quality.
Shape of Molded Plastic Products
The shape of the molded plastic product is primarily dictated by the cavity of the injection mold. Accurate design of the mold cavity is crucial in creating various complex parts. For instance, in the production of automotive interior components, the mold can be crafted to replicate the intricate design of a car’s center console. This includes features such as curved surfaces and button holes, allowing molded parts to fit seamlessly during assembly.
Mold Design Aspect | Example | Impact on Quality |
---|---|---|
Geometry | Complex shapes for automotive interiors | Ensures fit and aesthetic integrity |
Dimensional Accuracy | High-precision molds for electronics | Maintains functionality and compatibility |
The dimensional accuracy of these molds can be controlled down to microns. This precision ensures that the injection molded product meets stringent design specifications, which is especially vital for components like electronic equipment housings.
Ensuring Quality of Plastic Products
Another pivotal factor is the quality assurance mechanisms incorporated within the molding process. The cooling system plays a significant role in maintaining product integrity. An efficiently designed cooling channel ensures that the plastic cools evenly within the mold cavity.
For example, when manufacturing large plastic sheets, uneven cooling can lead to warping or excessive internal stress. Implementing conformal cooling channels—where the cooling medium flows closely alongside the product’s shape—can significantly mitigate these issues.
Ejection Mechanism
The ejection mechanism is also fundamental in ensuring the quality of molded products. After cooling, a smooth ejection process helps prevent damage to the plastic parts. For thin-walled components, improper ejection could lead to breakage. Adopting suitable ejection methods, such as push plate or push rod ejection, can enhance demolding efficiency without compromising product integrity.
Improving Injection Molding Production Efficiency
Efficiency in production directly correlates with quality outcomes in injection molding. Since injection molds are reusable, their design and durability allow for rapid production runs. For instance, a well-constructed mold for bottle caps can yield dozens or even hundreds of caps per minute, which significantly boosts production efficiency.
Additionally, the structural design of molds can also optimize injection cycle time. Utilizing hot runner molds helps maintain plastic in a molten state throughout the process, thereby shortening cycle times and enhancing throughput. This setup reduces cooling time at the gate compared to traditional cold runner systems, leading to more efficient production cycles.
By considering these factors—shape design, cooling systems, ejection mechanisms, and mold efficiency—manufacturers can ensure higher quality outputs in injection molding processes. For more insights on optimizing your injection molding operations, consider exploring advanced techniques1 that could enhance your designs further.
Mold design significantly impacts the quality of injection molded parts.True
The accuracy and complexity of mold design directly influence the fit and aesthetic integrity of molded products, ensuring high-quality outcomes.
Uneven cooling can lead to warping in plastic products.True
Implementing efficient cooling systems is crucial to prevent issues like warping or internal stress during the injection molding process.
How Does Injection Molding Supercharge Production Efficiency?
Have you ever thought about how those smooth, complex plastic parts are created so quickly? Injection molding is the secret. It changes production efficiency in amazing ways. Let’s explore the magic of this powerful method!
Injection molding enhances production efficiency through refined mold design, effective cooling, reliable ejection, and reusable molds. Hot runner technology notably accelerates production cycles, playing a crucial role in the process.
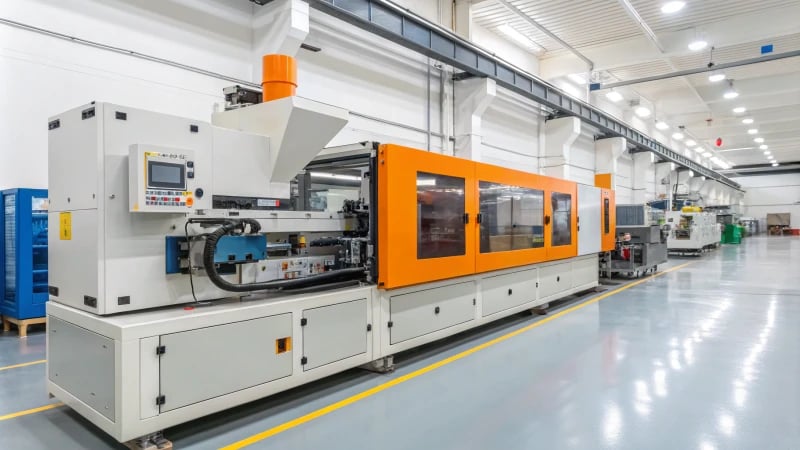
The Impact of Mold Design on Efficiency
When I first entered the injection molding industry, I felt amazed. Mold design really affects efficiency. The shape of the mold decides how the final product looks and feels.
For instance, I worked on a project for an automotive company where we had to create a center console. The mold cavity matched the car’s curves perfectly, allowing us to produce a complex part in one piece. This minimized assembly time and sped up production significantly.
Mold Feature | Impact on Efficiency |
---|---|
Complex geometries | Allows for multi-functional parts, reducing assembly needs |
Dimensional accuracy | Minimizes rework and defects |
Quality Control through Cooling Systems
Cooling systems in molds taught me a big lesson about maintaining product quality, which directly affects efficiency. Consistent cooling keeps products high in quality and prevents issues such as warping.
We faced warping when producing large plastic sheets, which was really frustrating. However, by using conformal cooling channels that followed the parts’ shape exactly, we achieved even cooling. This innovation improved output quality and efficiency significantly.
Ejection Mechanisms and Their Role
Ejection mechanisms might look minor, but they are crucial for efficiency. A well-designed ejection system matters because it removes parts from molds without harm.
In our case of producing thin-walled products, the push plate ejection method saved us from breakages during demolding. This efficient process sped up production and reduced waste considerably.
Reusability of Injection Molds
Reusability is one of the best features of injection molds. Once the design and manufacturing process are perfect, a mold can produce thousands of identical parts before needing maintenance.
For example, I worked with a mold for bottle caps that produced dozens per minute! This not only increased productivity but also dropped material waste significantly. Efficiency grows when we embrace mold reusability; it’s truly amazing.
Hot Runner Technology Enhancements
Hot runner systems have changed our production cycles dramatically. Unlike traditional cold runner systems, hot runners keep plastic molten during injection, which speeds up the process greatly.
We integrated this technology into our processes; cycle times shrank almost overnight! It felt like a secret weapon for production!
For more detailed information about hot runner systems2, click here.
Conclusion
Injection molding is like a hidden treasure in manufacturing. Advanced mold designs and new technologies make it shine brighter by controlling quality, reducing cycle times, and achieving high output through reusability. I am really excited to see new advancements as they will probably open new doors for creativity and productivity.
Precision molds reduce production errors in manufacturing.True
High dimensional accuracy from precision molds minimizes defects, leading to improved efficiency and quality in production processes.
Hot runner systems increase injection molding cycle times.False
Hot runner technology maintains molten plastic, reducing cooling time and significantly speeding up the injection process, enhancing overall efficiency.
What Industries Truly Thrive Thanks to Injection Molding Technology?
Injection molding technology has changed how we produce everyday items. It plays a very important role in many industries. Which sectors really gain the most from this creative production method? Let’s find out!
Injection molding technology significantly benefits automotive, consumer electronics, medical devices, packaging, and toy industries by enabling efficient production of high-quality, sector-specific plastic parts.
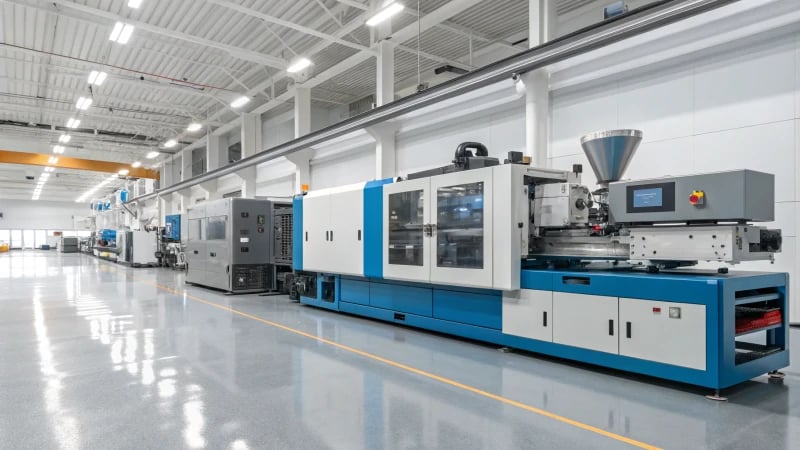
Injection Molding Technology
Injection molding technology profoundly shapes our daily lives. Many people do not notice its influence. I vividly recall my first encounter with this technology while working on a consumer electronics project. I watched intricate designs come alive with precision. This experience opened my eyes to the method’s vast possibilities.
Automotive Industry
The automotive sector relies heavily on injection molding. I remember shopping for cars and noticing every detail. Parts like the dashboard and interior trims stand out. Manufacturers use injection molding to create functional and attractive components.
Component Type | Benefits of Injection Molding |
---|---|
Dashboards | Complex shapes, aesthetic appeal |
Interior Trims | Functional, visually appealing |
This technology produces complex shapes. For example, a car’s center console must fit beautifully with the interior.
High-precision molds help meet strict quality standards. Every component, from button holes to storage areas, is crafted perfectly. This results in less waste and great efficiency. People working under tight schedules appreciate this.
Consumer Electronics
Consumer electronics benefit hugely from injection molding. Durable and lightweight components are essential. Smartphones and laptop buttons, for example, owe much to this process.
A company I worked with used hot runner systems. These systems speed production while maintaining high quality. Innovation like this is crucial in a fast-paced and evolving industry.
Component Type | Benefits of Injection Molding |
---|---|
Housings | Lightweight, durable |
Buttons | Complex shapes, tactile feedback |
Connectors | High precision, scalability |
Medical Devices
Injection molding greatly impacts the medical device industry. Precision and safety become top priorities here. The technology creates intricate parts like syringes and surgical tools that meet strict safety standards.
Reusing molds keeps production precise and cost-effective. This approach benefits manufacturers significantly.
Packaging Industry
In packaging, injection molding excels. Speed and efficiency stand out in this sector. Bottle caps and containers need rapid production rates.
Companies produce hundreds of units per minute while maintaining quality.
Packaging Type | Production Speed |
---|---|
Bottle Caps | Hundreds per minute |
Containers | Rapid production |
Good cooling systems during production are vital as they help prevent defects, avoiding costly waste seen in many processes.
Toys and Recreation
The toy industry highlights injection molding’s creative potential. Childhood toys with vibrant colors and intricate designs often emerge from this technology.
Thanks to injection molding, manufacturers create colorful and detailed toys at a low cost while ensuring safety for children remains a priority.
High-quality molds produce engaging action figures and building blocks that hold detailed textures that captivate young minds.
Injection molding profoundly transforms various industries; I witnessed its magic firsthand—efficiency, quality, and creativity thrive because of this incredible technology.
Injection molding is essential for the automotive industry.True
The automotive sector relies on injection molding for producing complex components like dashboards and panels, ensuring high quality and efficiency in manufacturing.
Consumer electronics do not benefit from injection molding.False
This statement is false; consumer electronics utilize injection molding for lightweight, durable components like housings and connectors, enhancing production speed and quality.
Conclusion
Injection molding is crucial in manufacturing, allowing for efficient production of precise plastic parts while enhancing quality and speed across multiple industries.