Understanding injection molding machines resembles solving a difficult puzzle. Many pieces must fit together correctly. Each part has its own role. Some parts are very complex. Others are simpler. All parts are important. The entire process probably needs precision. Precision often leads to success.
Selecting the correct injection molding machine starts with checking your product’s size and weight. The projected area helps decide the clamping force. Product weight is important for determining injection volume. Proper calculations are essential. The machine’s abilities should fit the production needs. This match increases work speed. It really improves quality.
I remember the first time I picked an injection molding machine. It felt like choosing the perfect shoes for a big event. Understanding projected area and clamping force was crucial. This part is very important. But, I soon saw there was more to learn. Mold size needed to match. Other factors, like injection pressure, also mattered. Many things required my focus. Come with me as I explore how these details influence an important choice in manufacturing.
Clamping force depends on product's projected area.True
The clamping force is calculated using the projected area, injection pressure, and safety coefficient.
Injection volume is 100% of theoretical volume.False
The actual injection volume is typically 80%-90% of the theoretical volume.
How Does Product Size Influence Machine Selection?
Have you ever thought about how a product’s size could really transform the whole process of choosing a machine?
Product size influences the choice of machinery by determining the needed clamping force and mold size. Larger items need machines with stronger clamping force. Product weight also affects the needed injection volume. It is very important to align these factors. Efficient production depends on this alignment.
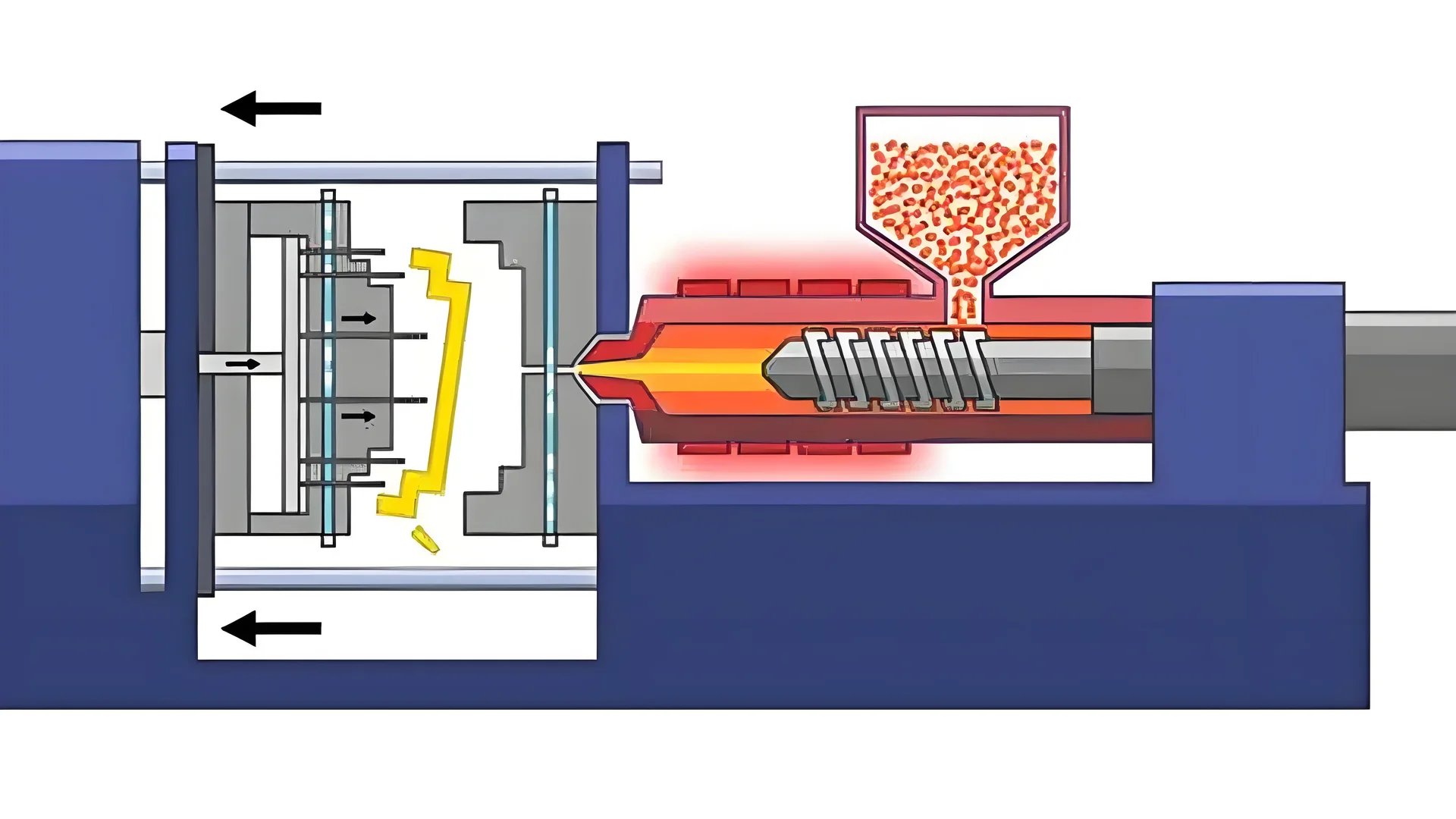
Tonnage and Clamping Force
Product size plays a crucial role in selecting the tonnage of an injection molding machine. The clamping force is like the machine’s hug for keeping your product tight and secure. To calculate this for every product, you start with its area on the mold’s surface. For example, in one project, we had to work with a gadget having a 10,000 mm² area. With an injection pressure of 50 MPa, we required about 65 tons of clamping force. This means a machine with at least that capacity is necessary to give the gadget just the right hug—a very firm hug.
Mold Size Considerations
Mold size was something I didn’t understand until I tried fitting a car bumper mold into a small machine. Imagine forcing an oversized sweater into a tiny drawer! Large products necessitate larger molds, requiring injection molding machines with adequate template size and tie rod spacing. Matching mold and machine sizes is vital—like finding jeans that really fit well.
Injection Volume Based on Product Weight
Sometimes, I dealt with products of various weights. Different weights needed different volumes from the machine. By determining the product’s volume through its weight and material density, one can choose an appropriate machine. For instance, a 100g item with 1.2g/cm³ density meant about 83.3 cm³ volume—more math than I thought! Knowing if the machine could handle this volume meant avoiding spills or incomplete shots.
Injection Pressure Requirements
Oh, and injection pressure! Heavier products needed more pressure to fill every mold part—just like making sure your cake batter fills every pan corner. Machines have different pressures and choosing one that matches your product’s needs is essential to avoid flaws.
In these ways, dealing with product size, clamping force, mold size, and injection pressure felt like solving a tricky puzzle. Once I knew each part’s role in ensuring quality1 production outcomes, finding the right machine was less scary and more about getting good results.
Larger products need larger mold sizes.True
Larger products require molds that fit their size, influencing machine choice.
Heavier products need lower injection pressure.False
Heavier products generally require higher injection pressure for complete filling.
Why is product weight crucial in machine choice?
I recall the first moment I understood how important product weight is in picking the right machine. It felt like a light turned on in my mind. Suddenly, everything made sense!
The weight of a product is very important. It plays a big role in how much a machine injects. Heavier items usually need machines with more pressure. They really need higher pressure for full mold filling. Lighter items might need less force. Matching machine strength with product weight is crucial for best results.
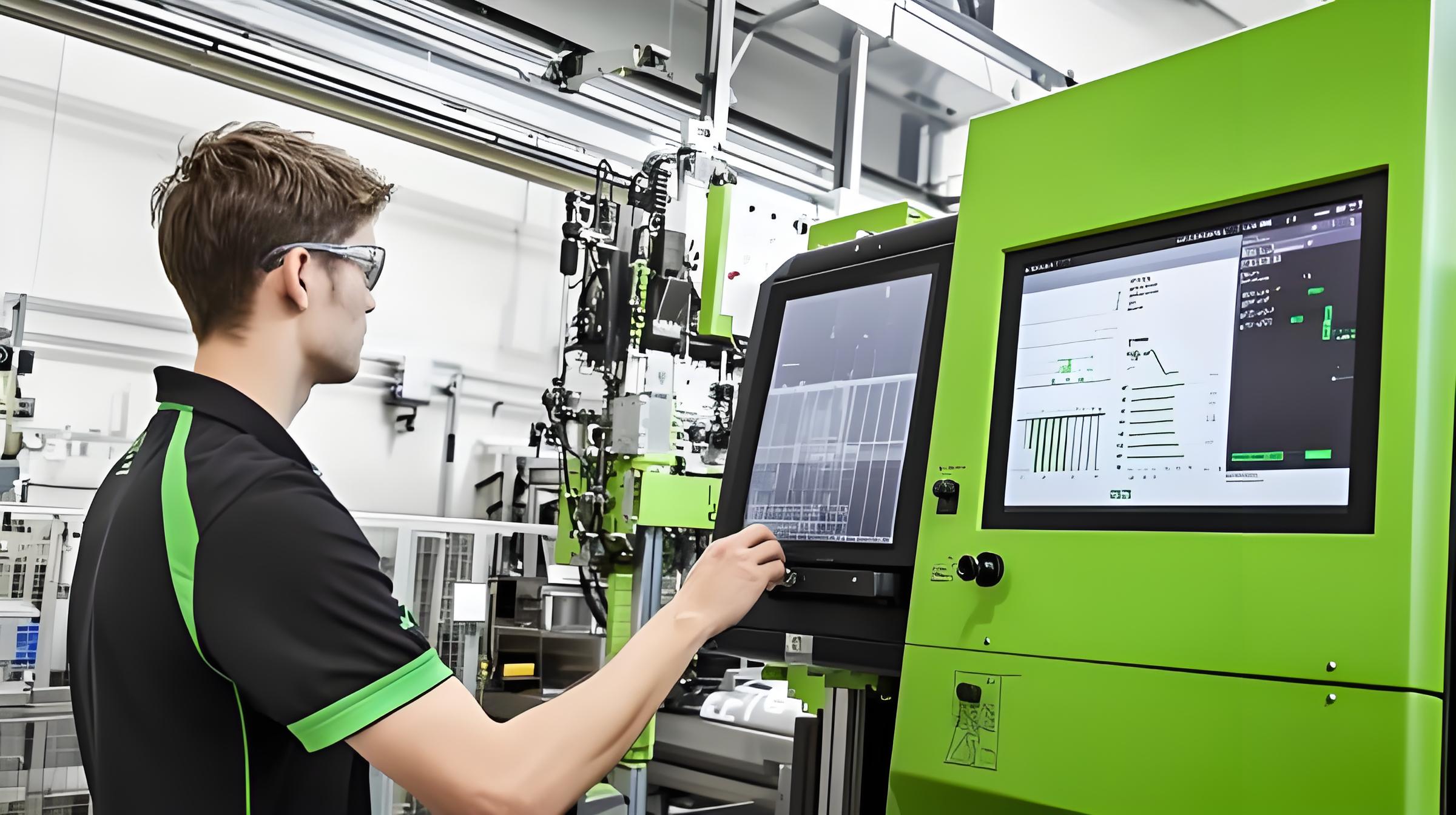
Understanding Injection Volume Needs
When I started, I learned something important about product weight and injection volume. Imagine holding a 100g item in your hand. You can feel it, right? Using the material’s density of 1.2g/cm³, that weight becomes a volume of about 83.3cm³. The machine chosen needs to handle more than this volume. This is crucial—really crucial for smooth production.
The weight of a product is directly related to the injection volume2 that a machine must handle. When selecting a machine, knowing the product’s weight helps in calculating the needed injection volume by converting it through the density of the material.
Injection Pressure and Product Weight
Picture squeezing the last bit of toothpaste from a tube—that kind of pressure is needed for heavier products in injection molding. I worked on a project with dense, thick items where the machine needed lots of pressure to fill every part of the mold.
Product weight also influences the required injection pressure3. Heavier products may need higher pressures to ensure thorough cavity filling and avoid defects like short shots.
Such considerations are vital when manufacturing components like automotive parts or large packaging units, where consistency and precision are paramount. Machines that can’t deliver adequate pressure can result in incomplete or flawed products, leading to increased waste and cost.
Tonnage Selection Based on Product Size
I struggled with tonnage selection at first; it connects to product size and weight. Then I visualized it like choosing the right clamping force—think of a big car bumper mold.
While product weight is critical, it interplays with size, affecting tonnage selection. The projected area of a product helps determine the clamping force needed from a machine, calculated using a formula involving injection pressure and safety factors.
This delicate balance means manufacturers must carefully assess both weight and size to select machines that provide sufficient clamping force without overinvesting in excessive capacity. Large molds require machines with adequate template sizes and spacing to accommodate these dimensions without compromising efficiency or quality.
Understanding injection volumes, pressures, and tonnage4 changed my manufacturing work significantly.
Projected area affects clamping force selection.True
The projected area determines the required clamping force for the injection molding machine.
Product weight doesn't influence injection volume choice.False
Product weight is converted to volume to ensure the machine meets injection volume needs.
Why Is Mold Compatibility Crucial in Choosing an Injection Molding Machine?
Have you ever thought about how mold compatibility could really affect your injection molding process?
Choosing the right machine for mold compatibility is crucial. Mold compatibility affects clamping force and injection volume. These factors depend on the product’s size and weight. A good match allows for smooth production. Smooth and efficient production is very important.
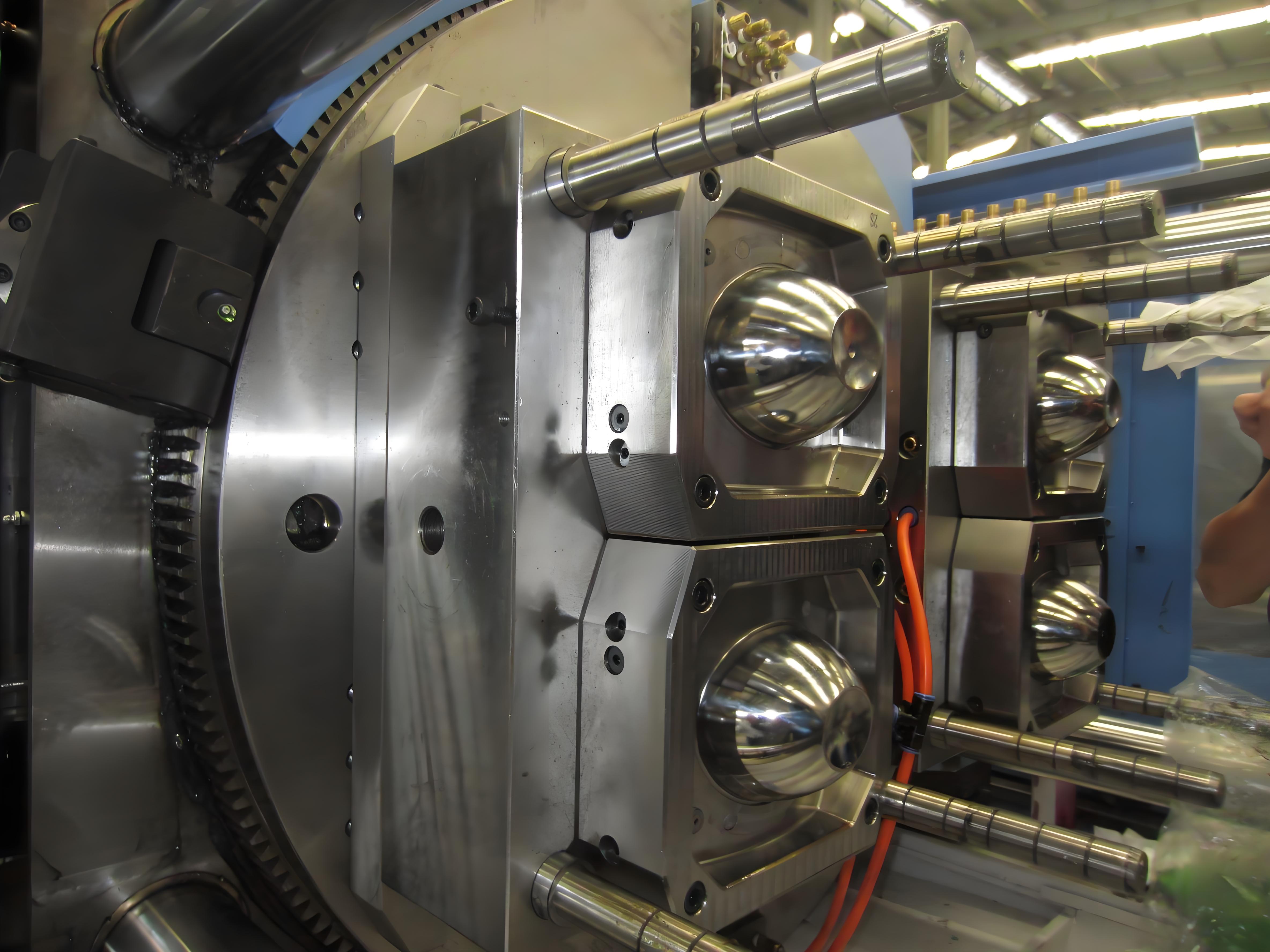
Understanding Clamping Force Needs
When I began exploring injection molding, I learned that clamping force plays an important role. Imagine it like placing a puzzle piece correctly – the right force keeps everything together. We calculate this force using the formula (F = p \times A \times S). At first, it seems tricky, but it’s simple once you break it down. For example, if you work with a product with a projected area of (10000mm^{2}) and an injection pressure of 50MPa, you need a clamping force near 65t. This ensured my chosen injection molding machine5 handled the mold well, keeping production smooth.
Matching Mold Size with Machine Capacity
In the beginning, I overlooked the importance of matching mold size with machine capacity. I once tried using a machine too small for a big car bumper mold. The mold was huge, needing a machine with enough template size and space between rods. This experience taught me that having the right machine setup avoided delays and ensured high-quality output from the manufacturing process6.
Determining Injection Volume Needs
I remember my first short shot incident. It showed me why matching injection volume needs is crucial. You convert product weight to volume using material density. Once, for a product weighing 100g with a density of 1.2g/cm³, the machine needed to handle an injection volume over 83.3cm³. This precise matching prevented annoying defects and preserved product quality.
Adjusting for Injection Pressure Variations
Different products require different pressures. I learned this after many attempts. Heavier products often need higher pressures to fill the mold fully. Choosing a machine that managed these changes was essential to avoid issues like incomplete fills. For example, with thicker products, picking machines that allowed higher pressures helped keep quality stable across batches. Proper injection pressure7 adjustments made a real difference.
Clamping force depends on product's projected area.True
The clamping force is calculated using the product's projected area on the mold.
Injection volume should be 100% of theoretical volume.False
Actual injection volume is typically 80%-90% of the theoretical volume.
How can I balance injection pressure with product requirements?
Finding the right balance between injection pressure and product needs often seems like an art. How is this achieved perfectly?
Balancing injection pressure with product needs involves checking product size and weight. Choosing the correct injection molding machines is crucial. Adjusting pressure settings is also important. Factors include projected area, clamping force and injection volume. These factors influence quality and efficiency.
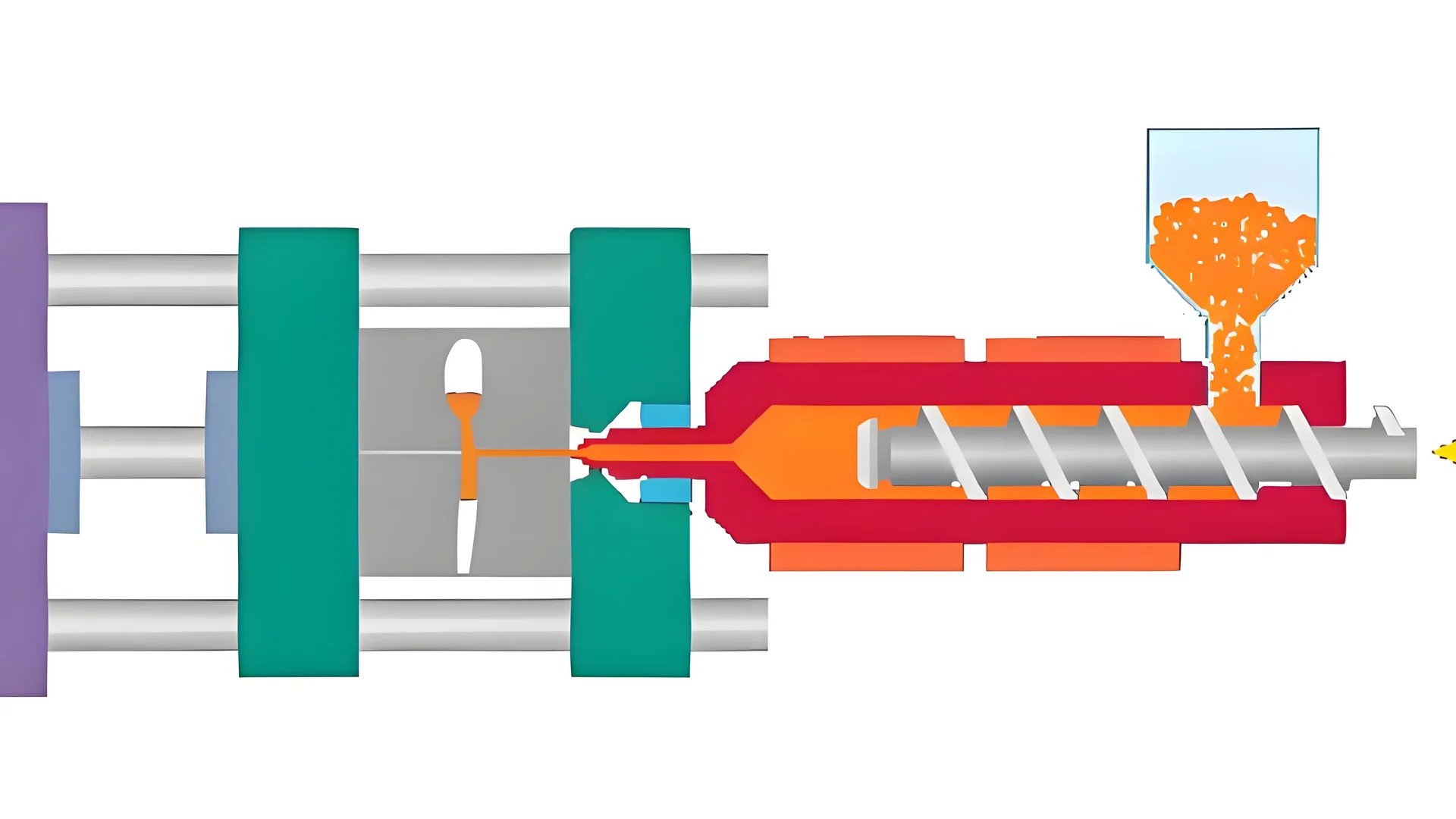
Understanding Product Size and Injection Pressure
When it comes to determining the ideal injection pressure for a product, size plays a pivotal role. The projected area of the product on the mold’s parting surface dictates the necessary clamping force. This force can be calculated using the formula (F = p \times A \times S), where (F) is the clamping force, (p) is the injection pressure, (A) is the projected area, and (S) is a safety coefficient.
For instance, with a product area of (10000mm^2) and an injection pressure at (50MPa), using a safety coefficient of 1.3, would require a clamping force of approximately (650,000N). It’s crucial to select an injection molding machine that exceeds this requirement. Selecting the right machine8 is integral for achieving proper balance.
Matching Mold Size with Injection Equipment
Understanding how mold size impacts machine choice was a big realization. Larger products necessitate molds that require machines with ample template size and tie rod spacing. For example, I worked on a project for a large car bumper; finding a proper machine was crucial due to its significant space requirements.
Ensuring the mold’s thickness aligns with the machine’s capabilities is also crucial for successful demolding. This aspect influences not only the choice of machine but also how effectively injection pressure is utilized across different products.
Considering Product Weight and Injection Volume
Another critical factor is product weight. It determines the required injection volume, which in turn affects machine selection. By calculating the theoretical injection volume using screw diameter and stroke, manufacturers can ensure that their chosen machines meet or exceed these needs.
For example, a 100g item with 1.2g/cm³ density requires more than (83.3cm³) in injection volume. Ensuring that the selected machine can handle this volume efficiently is essential for maintaining consistent product quality.
Adjusting Injection Pressure for Heavier Products
Heavier items generally need more injection pressure for even plastic distribution inside the mold cavity. This reminded me of heavy, thick-walled plastic pieces needing machines capable of generating higher pressures to prevent flaws such as short shots.
By recognizing these factors and adjusting them accordingly, manufacturers can effectively balance injection pressure with product requirements, leading to improved production outcomes. Explore more on machine adjustments9 for optimal efficiency in injection molding processes.
Projected area determines clamping force needed.True
The clamping force is calculated using the product's projected area.
Heavier products need lower injection pressure.False
Heavier products require higher injection pressure for complete mold filling.
Conclusion
Selecting the best injection molding machine involves considering product size and weight, which determine clamping force, mold size, injection volume, and pressure requirements for efficient production.
-
Learn about how injection pressure affects product quality and process efficiency. ↩
-
Learn how injection volume impacts machine choice and efficiency. ↩
-
Discover how pressure influences product quality and machine requirements. ↩
-
Understand how to determine necessary tonnage for specific products. ↩
-
Learn why clamping force ensures proper mold function. ↩
-
Explore tips for setting up machines for large molds. ↩
-
Discover how to adjust pressure for optimal results. ↩
-
Discover how to select machines tailored to product dimensions. ↩
-
Learn about key adjustments for efficient production. ↩