I remember the first time I faced the daunting world of injection molding—it was like trying to fit a square peg into a round hole!
One injection molding machine can’t accommodate every mold due to differing requirements in clamping force, injection capacity, and mold size. Each machine is built to meet specific criteria tailored to particular mold specifications, ensuring efficient production without risking damage to the equipment or compromising product quality.
I learned the hard way that not every machine is a one-size-fits-all solution. It was a steep learning curve, but once I understood the unique factors that determine compatibility, I could confidently match machines to molds. In this article, I’ll walk you through these key considerations, like clamping force and injection capacity, so you can avoid my early missteps and make informed decisions for your projects.
One injection molding machine fits all molds.False
Machines have specific clamping force and size requirements for molds.
Mold size affects injection machine compatibility.True
Different machines are designed to handle specific mold sizes efficiently.
- 1. How Do You Determine the Clamping Force Required for a Mold?
- 2. How Does Injection Capacity Affect Mold Compatibility?
- 3. Why Is Mold Size Crucial in Machine Selection?
- 4. What Role Does Injection Pressure Play in Mold Matching?
- 5. How Do You Choose the Perfect Machine for Your Project?
- 6. Conclusion
How Do You Determine the Clamping Force Required for a Mold?
Ever wondered what keeps those molds in perfect shape during injection molding? It’s all about finding the right clamping force!
Clamping force in injection molding is influenced by mold size, cavity pressure, part complexity, and material choice. Calculating these factors accurately ensures machines perform optimally, yielding flawless products.
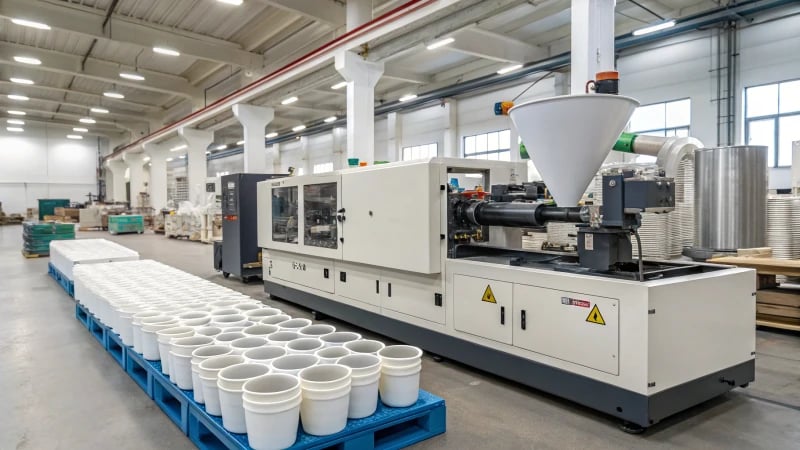
The Role of Mold Size and Complexity
The size and complexity of a mold directly impact the clamping force required. I’ve found that larger molds with intricate details demand a higher force to ensure they stay closed, preventing issues like flash. This is when excess material seeps through mold gaps, something I’ve learned to avoid by carefully considering each mold’s unique features.
Mold Feature | Clamping Force Impact |
---|---|
Large Size | Requires more force |
Complex Design | Increases force needs |
Material Properties and Their Influence
Different materials exert varying pressures within the mold. Once, while working with high-viscosity plastics, I realized they require greater clamping forces due to their flow characteristics. Understanding material behavior is crucial for determining the suitable force.
- High Viscosity: Greater force needed to contain the material.
- Low Viscosity: Requires less clamping force.
Importance of Cavity Pressure
Cavity pressure within the mold must be considered. It affects how tightly the mold needs to be held together. I’ve often relied on specific formulas to calculate this pressure, ensuring machines are set up correctly.
Injection Molding Machine Capabilities
Not every machine can deliver the necessary clamping force for every mold. Machines have specific ratings, and exceeding these can lead to operational failures. I’ve learned to match machine capabilities with mold requirements diligently.
- Machine Clamping Rating: Choose machines with appropriate ratings for your molds.
- Potential Issues: Insufficient force leads to defects like flash2.
Understanding these factors helps me select the right machine and settings for each mold, ensuring efficient and high-quality production. For more insights, explore our detailed guide on injection molding fundamentals3.
Larger molds require less clamping force.False
Larger molds need more force to prevent issues like flash.
High-viscosity materials need more clamping force.True
High viscosity exerts more pressure, needing greater clamping force.
How Does Injection Capacity Affect Mold Compatibility?
Ever wondered why your mold just doesn’t fit right with a particular injection molding machine? Let’s dive into the nitty-gritty of injection capacity and its impact on mold compatibility, a topic that has kept me intrigued since my early days in the mold industry.
Injection capacity influences mold compatibility by determining if the machine can inject enough material to completely fill the mold. If the capacity is too low, it results in incomplete fills, affecting the quality of the parts produced.
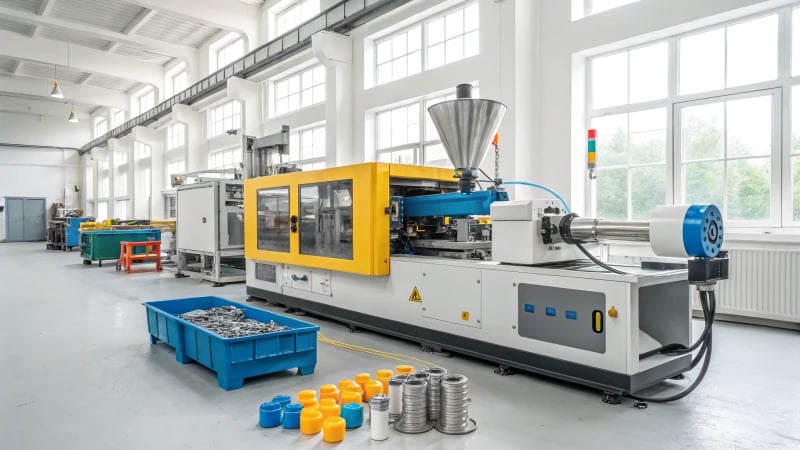
Understanding Injection Capacity
Imagine back when I was still learning the ropes at the mold factory, trying to wrap my head around why certain machines worked seamlessly with some molds but not others. Injection capacity, as it turns out, is like the unsung hero here. It refers to the maximum amount of molten plastic a machine can inject into a mold in a single shot. This factor is pivotal for determining whether a machine can handle different sizes and complexities of parts.
A mismatch in this capacity often leads to those frustrating issues like incomplete fills or annoying product defects, something I’ve had to troubleshoot more times than I care to admit.
Machine Type | Injection Capacity |
---|---|
Small Part Machine | Low Capacity |
Large Part Machine | High Capacity |
The Role of Shot Volume
Back in the day, I recall working on a project that demanded precise calculations of shot volume—a crucial aspect determined by the volume of the part and the runner system. Picture this: you’re using a small machine, trying to create large containers. The limited shot volume can lead to defects like short shots4, where parts aren’t fully formed. Trust me, seeing a product come out half-baked after putting in so much effort can be disheartening.
Adjusting Injection Pressure and Speed
Injection capacity isn’t merely about volume; it also involves fine-tuning the pressure and speed at which material is injected. I learned this firsthand while working on a mold with intricate details—it needed high-pressure, high-speed injections to ensure proper filling. In contrast, simpler designs are more forgiving and don’t require such precise adjustments.
The Importance of Clamping Force
I remember the first time I experienced a mold opening slightly during injection due to insufficient clamping force. It resulted in flashing5, an issue that underscored how crucial it is for injection capacity to align with clamping force. Both need to be evaluated together to prevent costly errors.
Consideration | Influence on Compatibility |
---|---|
Injection Capacity | Determines max shot volume |
Clamping Force | Prevents mold opening during injection |
Evaluating Mold Size and Platen Dimensions
One day, I realized that beyond capacity and force, the physical size of a mold also matters. It has to fit within the machine’s platens; otherwise, it’s a no-go. There were times when I had molds that exceeded these dimensions or didn’t fit between the tie-bars, rendering them incompatible.
In summary, understanding how injection capacity affects mold compatibility is essential for optimizing production. By ensuring that injection molding machines meet all necessary requirements—capacity, pressure, speed, and size—manufacturers can avoid costly errors and enhance product quality. Consider exploring how different machines cater to varied production needs6 for further insights. This alignment ensures efficiency and effectiveness in production processes.
High injection capacity prevents short shots.True
Higher capacity ensures enough material fills the mold, avoiding incomplete parts.
Clamping force is unrelated to injection capacity.False
Both are crucial; insufficient clamping can cause mold opening during injection.
Why Is Mold Size Crucial in Machine Selection?
Imagine standing before a giant machine, knowing that the size of the mold you’re about to use could make or break the entire production process.
Mold size is crucial in machine selection because it affects clamping force requirements, injection capacity, and platen dimensions. Choosing the wrong mold size can lead to inefficiencies or equipment damage.
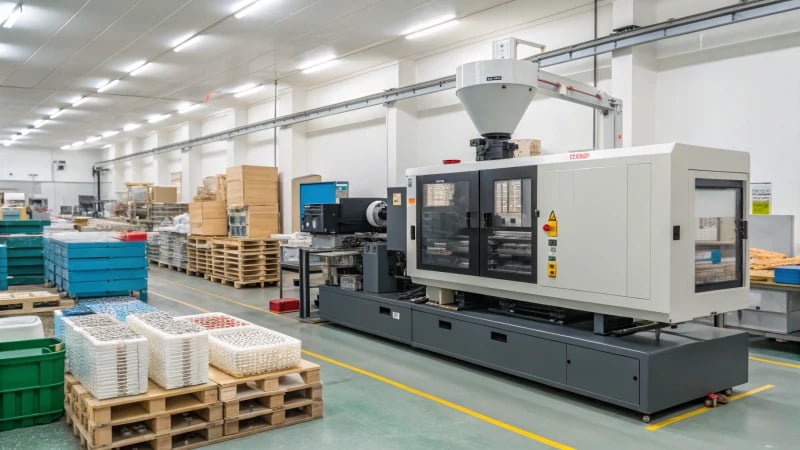
Clamping Force Requirements
I remember the first time I realized that not all injection molding machines were created equal. It was like trying to fit a square peg in a round hole. The clamping force needed to keep the mold closed during injection was far greater than I anticipated. It’s essential because this force prevents flash7 from ruining the integrity of the part. Larger molds, especially those with extensive cavity areas, demand higher clamping forces. I learned this lesson the hard way with a mold for a large automotive part.
Consider this table for clarity:
Mold Type | Clamping Force Needed |
---|---|
Small Toy Mold | Few Tons |
Large Automotive Part | Hundreds of Tons |
Injection Capacity and Shot Volume
There was this one time I tried using a machine designed for small parts to produce a large container. Spoiler alert: it didn’t end well. The injection capacity8 must align with the mold’s shot volume needs. If not, you’ll find yourself with incomplete molds or quality issues, a mistake I won’t soon forget.
Mold Size and Machine Platen Dimensions
Have you ever tried to cram too many groceries into a bag that’s just too small? That’s what it’s like when molds don’t fit the platens of your machine. Inadequate fit leads to improper mounting, affecting production efficiency. The spacing between tie-bars also limits what molds you can use.
Injection Pressure and Speed Requirements
Different molds require varying injection pressures and speeds based on part complexity and material type. One of my early projects taught me that high-pressure injection might be needed for intricate details, while others benefit from controlled speeds. Aligning machine capabilities with these needs is essential for quality outcomes.
Larger molds require higher clamping forces.True
Larger molds, especially with extensive cavity areas, need more force to prevent flash.
Small machines can handle large container molds.False
Small machines often lack the injection capacity needed for large items.
What Role Does Injection Pressure Play in Mold Matching?
Ever wonder how injection pressure can make or break your mold design?
Injection pressure is key to ensuring your mold fills properly and the final part meets quality standards. It must align with the mold’s specifications to avoid defects, making it crucial for effective mold matching.
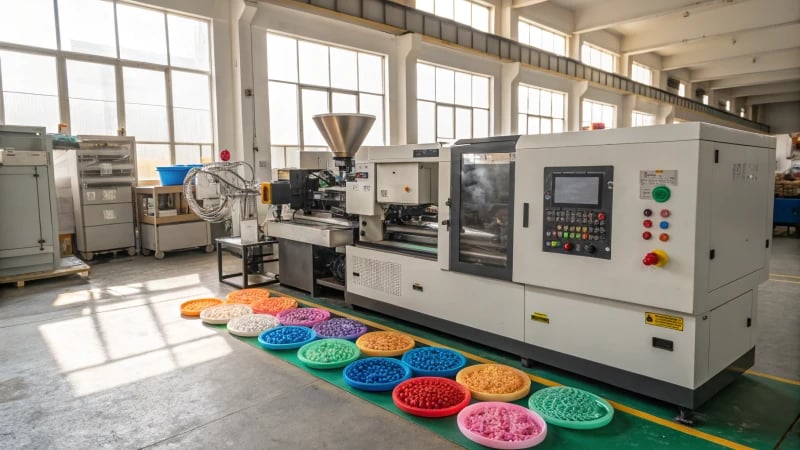
Understanding Injection Pressure
When I first started working with injection molds, I quickly learned that injection pressure is like the heartbeat of the process. It’s crucial for making sure that every nook and cranny of the mold is filled with precision. The right pressure captures all the tiny details, which is essential if you’re dealing with complex designs. I remember a project where a slight adjustment in pressure made all the difference in capturing those intricate details—saving us from redoing an entire batch!
Injection Pressure Parameters:
Parameter | Description |
---|---|
High Pressure | Suitable for intricate, thin-walled designs. |
Low Pressure | Used for simpler, thicker components. |
Injection Pressure and Part Quality
I’ve seen firsthand how injection pressure can define the strength and quality of molded parts. It’s fascinating how high pressure can eliminate pesky air pockets, enhancing the part’s density9 and integrity. However, I also learned the hard way that too much pressure can cause flashing, where excess material seeps out—think of it as an embarrassing spillover at a dinner party!
Matching Mold and Machine Requirements
Through trial and error, I realized that not every machine is a match for every mold. Each mold demands specific injection pressures based on its complexity. I once faced a situation where using the wrong machine resulted in an underfilled mold, which taught me the importance of having adjustable settings on our machines.
Key Considerations:
- Material Type: Different plastics need different pressures.
- Part Geometry: Complex designs require precise pressure control.
- Mold Design: Larger molds often need higher pressure for complete filling.
Getting these factors right ensures that injection pressure is perfectly matched to the mold, boosting both production efficiency and product quality10. Designers like us must factor these variables into our planning to avoid costly mistakes.
The Balance Between Pressure and Speed
Finding the sweet spot between injection pressure and speed is an art. I’ve learned that while high-speed injection with low pressure works wonders for thin-walled parts, too much speed or pressure can compromise quality. Industry expert Mike Tang11 often emphasizes integrating these considerations during the design phase, leading to better efficiency and cost savings. Implementing these insights has been a game-changer in my projects.
High pressure is needed for thin-walled designs.True
Thin-walled designs require high pressure to capture intricate details.
Excessive pressure can cause mold flashing.True
Too much pressure leads to material escaping, causing flashing defects.
How Do You Choose the Perfect Machine for Your Project?
Ever stood in front of a lineup of machines, feeling like you’re picking a partner for a dance? It’s all about finding that perfect match!
To optimize machine selection for different projects, consider key factors like clamping force, injection capacity, mold size, and pressure needs. Each project has unique demands, so tailor your machine choice to fit those specific requirements.
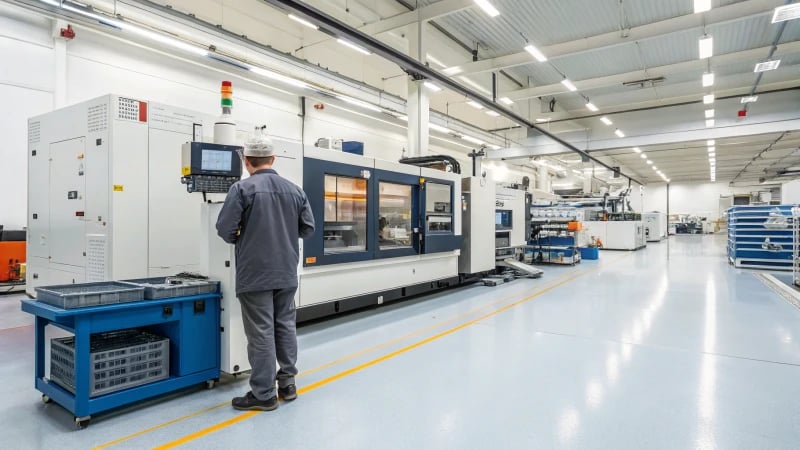
Understanding Clamping Force Requirements
Choosing a machine with the appropriate clamping force is critical. Machines need to exert enough force to keep the mold closed during injection. For instance, a mold for a large automotive part12 requires significantly higher clamping force than one for a simple plastic toy. If the clamping force is insufficient, it may cause flash or damage the mold.
Mold Type | Required Clamping Force |
---|---|
Small Toy Mold | A few tons |
Large Automotive Part | Hundreds of tons |
Injection Capacity and Shot Volume
The injection capacity of the machine must align with the shot volume needed for the mold. Machines designed for smaller parts may not suffice for larger items like a plastic container13. Mismatched capacities can lead to incomplete mold filling.
- Small Machines: Best for compact parts.
- Large Machines: Suitable for large products requiring more material.
Mold Size and Machine Platen Dimensions
The mold must fit within the machine’s platens. Check the platen dimensions and tie-bar spacing to ensure compatibility. If a mold exceeds these dimensions, it won’t mount correctly, leading to potential operational issues.
Key Considerations:
- Mold dimensions
- Platen size
- Tie-bar spacing
Injection Pressure and Speed Requirements
Different projects demand varying injection pressures and speeds. Complex shapes or thin-walled sections may require high-speed, high-pressure injections. Ensure your machine can adjust to these requirements to avoid issues with product quality14.
Pressure/Speed Needs
- High-pressure: For intricate details.
- Controlled speed: For standard parts.
Understanding these factors allows for better optimization of machine selection based on specific project needs. Each project has unique demands that necessitate careful consideration of machine capabilities and specifications. Engage in a thorough analysis to match machine features with project requirements effectively.
Large automotive parts need higher clamping force than toys.True
Large molds require more force to remain closed during injection.
Small machines are ideal for large product molds.False
Small machines lack capacity for large molds, causing incomplete fills.
Conclusion
Injection molding machines are not universally compatible with all molds due to varying clamping force, injection capacity, mold size, and pressure requirements essential for optimal production quality.
-
Learn how to calculate cavity pressure to ensure molds are optimally designed and machines perform efficiently. ↩
-
Discover the causes of flash in injection molding and how proper clamping force prevents this defect. ↩
-
Explore a comprehensive guide on injection molding basics to enhance your knowledge and skills. ↩
-
Discover how inadequate injection capacity leads to short shots and impacts product quality. ↩
-
Understand how flashing occurs due to mismatched clamping force and its effects on molds. ↩
-
Explore various machines designed for different production needs and capacities. ↩
-
Learn about ‘flash’ in molding and how incorrect clamping can lead to production issues. ↩
-
Understand injection capacity and its impact on choosing the right machine for your mold. ↩
-
Discover how injection pressure influences material density, affecting part integrity and performance. ↩
-
Explore the relationship between injection pressure and overall product quality during molding. ↩
-
Learn about Mike Tang’s contributions to the mold industry and his insights on injection pressure management. ↩
-
This link explains how clamping force affects automotive mold processes. ↩
-
Discover how different machines handle large plastic container molds. ↩
-
Learn about how injection pressure influences the quality of molded products. ↩