Ever wondered how injection molding changes with the size of the parts?
Injection molding for large parts requires robust materials and larger machines, while small parts need precision molds and less material. Mold design complexity and material selection also vary significantly between the two.
I remember the first time I designed a small, intricate part for a gadget—every detail mattered, from the tiniest screw to the precise curves of the plastic. In contrast, when working on larger components, I quickly realized that strength and durability were key players. It was like moving from crafting a delicate piece of jewelry to building a sturdy piece of furniture. Understanding these nuances isn’t just about making things; it’s about making them right for their purpose. The experience taught me that knowing when to opt for precision or robustness could make all the difference in delivering a successful product.
Large parts need larger injection molding machines.True
Large parts require machines with bigger clamping forces to accommodate size.
Small parts use more material than large parts in molding.False
Small parts generally use less material, optimizing cost and efficiency.
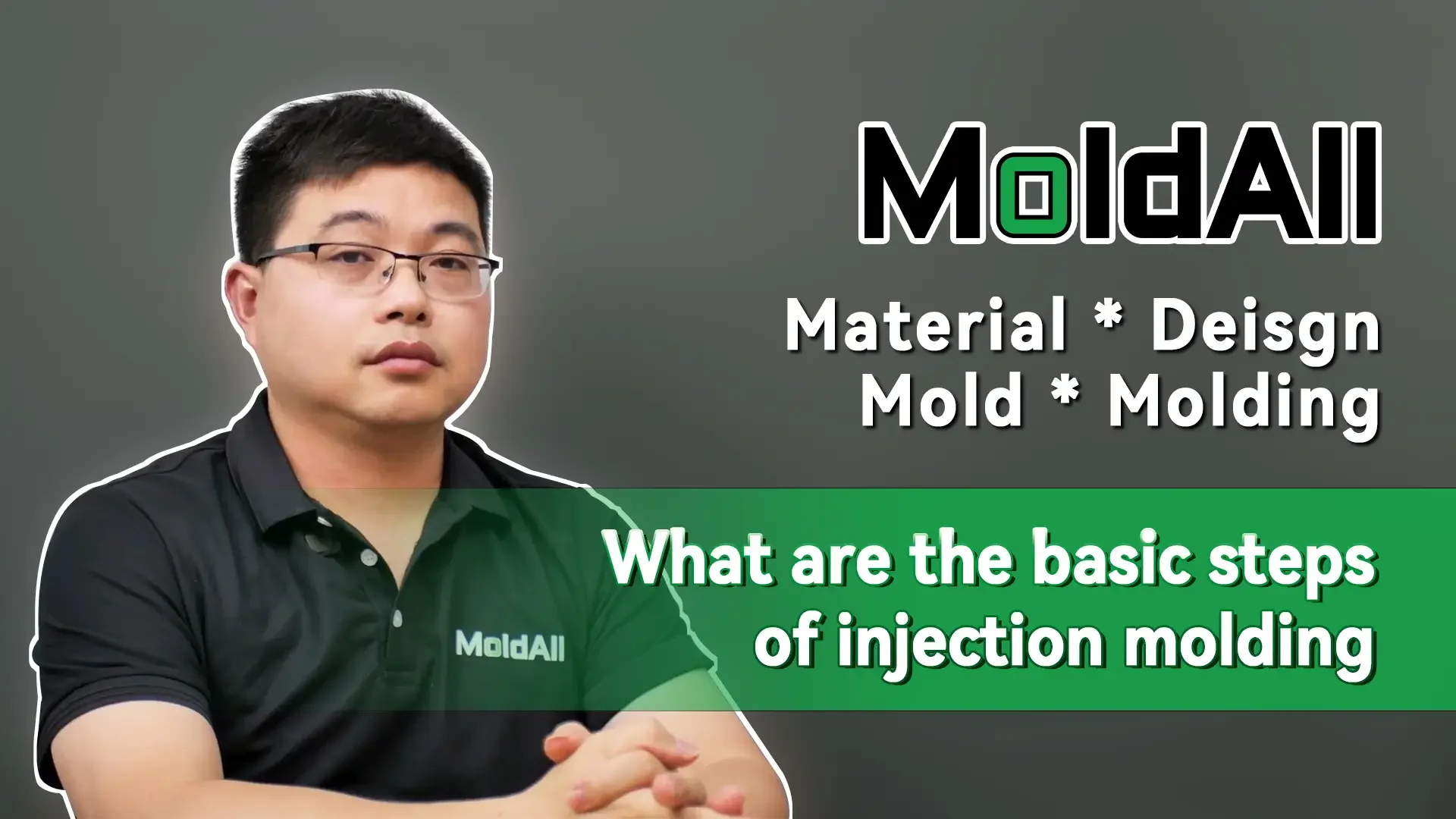
- 1. How Does Mold Design Vary for Large and Small Parts?
- 2. What Materials Are Best Suited for Different Part Sizes?
- 3. How Do Machine Requirements Differ for Large vs. Small Parts?
- 4. How Does Size Affect Costs in Injection Molding?
- 5. How does cycle time affect the production of various sized parts?
- 6. What Challenges Are Unique to Large vs. Small Part Molding?
- 7. Conclusion
How Does Mold Design Vary for Large and Small Parts?
Ever wondered how designing molds for different part sizes affects production? Let’s dive into the intricacies that make or break efficiency and quality.
Mold design for large parts focuses on robust structures and cooling, while small parts prioritize precision and material efficiency.
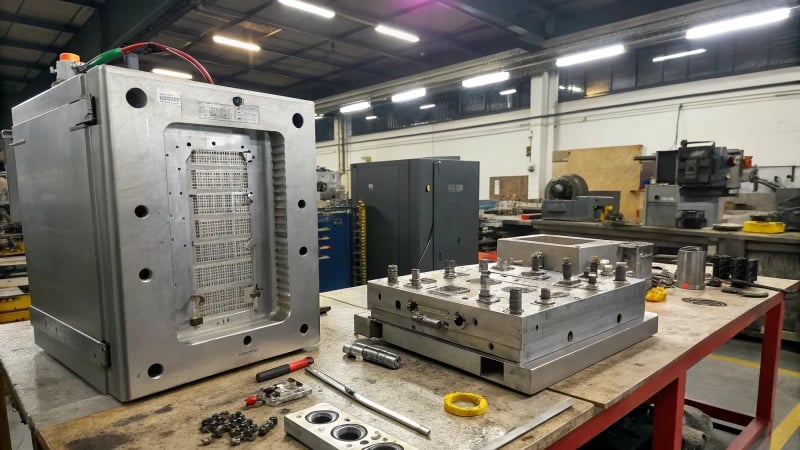
Key Differences in Mold Design
In my early days of mold design, I remember tackling a project for a hefty part that required a mold built like a tank. Large parts demand robust structural support to handle the intense pressure during injection. This often involves using stronger materials1 and adding features like support ribs to keep everything in place.
On the flip side, when dealing with tiny components, precision becomes my best friend. The mold must capture every detail with accuracy, sometimes calling for advanced machining processes2. This precision, while crucial, can also ramp up both the cost and time it takes to create the mold.
Aspect | Large Parts | Small Parts |
---|---|---|
Structural Support | High | Moderate |
Detail Precision | Moderate | High |
Cooling System Complexity | High | Low to Moderate |
Cooling Rate Considerations
Cooling rates can be a real game-changer, too. I once worked on a large mold that needed a maze of cooling channels to keep temperatures even, avoiding any nasty warping surprises. Smaller molds, however, tend to get away with simpler systems but require pinpoint temperature control3 to ensure every little detail is spot-on.
Material and Cost Implications
Material choices can seriously impact the bottom line. I’ve found that large molds often need more material, which can crank up costs. However, if you’re working on high-volume production, investing in top-grade materials for durability can be worth it.
Conversely, small molds might not use as much material but often call for premium grades to hit those precision marks, potentially leading to higher expenses.
Understanding these nuances helps me tailor design strategies that align with both functional demands and budget constraints. It’s all about striking the right balance to make the project a success.
Larger molds require more robust structural support.True
Larger parts need stronger molds to withstand injection pressure.
Smaller molds typically use simpler cooling systems.False
Smaller molds require precise temperature control, not simpler systems.
What Materials Are Best Suited for Different Part Sizes?
Ever found yourself tangled in the web of choosing the right materials for parts of different sizes? Trust me, I’ve been there, and it’s like being a kid in a candy store.
Selecting the right material for part sizes involves balancing strength, weight, and cost. Metals like aluminum suit small, precise parts, while larger components benefit from composites providing lightweight strength.
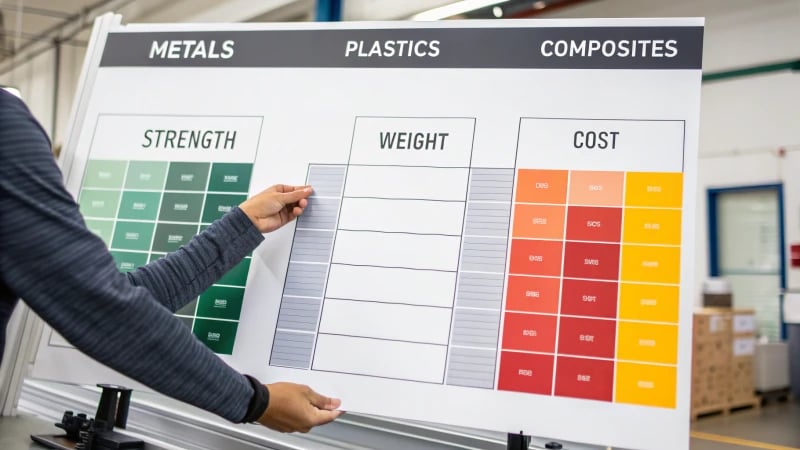
Understanding Material Properties
Navigating the world of material selection is akin to choosing the perfect tool for a job—a task I know all too well as someone who’s spent countless hours tweaking designs to meet both function and form. For small parts, where precision is key, I often lean towards metals like aluminum and stainless steel. Their machinability and strength make them reliable partners in crafting those minute details that matter. Meanwhile, large parts often call for the use of composite materials4 due to their remarkable weight-to-strength ratios.
Common Materials and Their Applications
Here’s a handy table to understand which materials are suitable for different part sizes:
Material | Small Parts | Large Parts |
---|---|---|
Aluminum | High precision, lightweight | Moderate strength |
Stainless Steel | Corrosion resistance | Heavy-duty components |
Composites | Less common | Lightweight structures |
Plastics | Intricate designs | Cost-effective large parts |
Exploring Cost and Performance
Cost is always a consideration in my projects, and that’s where plastics5 often save the day. Their moldability and lower cost make them ideal for producing small to medium-sized parts without breaking the bank.
For large-scale applications, I’ve seen materials like composites6 or advanced alloys become the go-to, especially when performance and durability are non-negotiable. Although they come with a heftier price tag, their longevity and reliability often make them worth every penny in the long run.
Considering Environmental Impact
In today’s world, I can’t overlook the environmental implications of my material choices. Using eco-friendly materials7 such as recyclable metals or biodegradable plastics not only supports sustainability goals but also aligns with many clients’ values. These are particularly important in projects where environmental impact is a top priority.
By carefully selecting materials based on part size and application needs, I strive to optimize performance and efficiency, making each project not only successful but also responsible.
Aluminum is ideal for high-precision small parts.True
Aluminum offers machinability and strength, suitable for precision.
Plastics are not cost-effective for large parts.False
Plastics are indeed cost-effective for producing large parts.
How Do Machine Requirements Differ for Large vs. Small Parts?
Ever tried to fit a square peg into a round hole? That’s what choosing the wrong CNC machine for your part size feels like.
Large part machining needs powerful, stable machines; small parts require precision and speed-focused machinery. Choosing the right machine ensures optimal performance and quality.
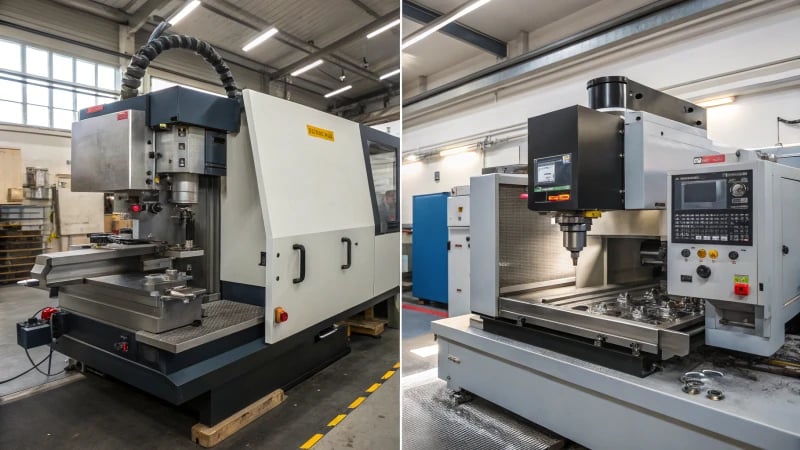
Power and Stability
When I first started working with large parts, I quickly realized how crucial it was to have machinery that could handle the weight and stress. Imagine trying to carve a giant sculpture with a pocket knife—it’s just not feasible. Large parts demand machines with substantial horsepower and stability. Heavy-duty CNC mills or lathes are my go-tos because they’re built to manage those intense forces without buckling under pressure.
Machine Type | Ideal For |
---|---|
Heavy-Duty CNC | Large Parts |
Precision CNC | Small Parts |
In my experience, small parts are a different ballgame altogether. It’s all about precision and speed8—think of it like crafting intricate jewelry rather than building a skyscraper. The machines I use for these tasks are nimble, with high spindle speeds and impeccable accuracy. They might not look like much compared to their hulking counterparts, but they get the job done beautifully.
Work Envelope and Tooling
The concept of the work envelope really hit home when I had to machine an unusually large piece. It was like playing a game of Tetris, trying to fit everything just right. Large parts need machines with expansive work envelopes to give me the room I need to maneuver those big chunks of material. You’ll often find bigger tables and tool holders in these setups.
Conversely, working on small parts means I focus on delicate tooling9. Here, micro-tools and high-speed spindles are essential—they help me achieve that detailed finesse without compromising the integrity of the part. It’s a delicate dance that demands the right tools.
Cooling and Chip Management
Cooling is something I underestimated until I saw a project warp due to overheating—it was a hard lesson learned. Larger parts can generate a lot of heat, so advanced cooling systems are non-negotiable. They prevent warping and ensure everything stays on track.
On the flip side, small parts don’t produce as much heat but managing chips is crucial. Efficient chip evacuation systems keep things precise by preventing buildup that could mess with the accuracy of my work.
All in all, selecting the right machine for the part size isn’t just about efficiency; it’s about ensuring quality and precision in every single project. For more insights on selecting machine types, check out resources on CNC machining capabilities10.
Large parts require machines with higher horsepower.True
Larger parts exert more force, needing machines with higher horsepower.
Small parts need machines with large work envelopes.False
Small parts require precision and speed, not large work envelopes.
How Does Size Affect Costs in Injection Molding?
Diving into the world of injection molding, I quickly learned that part size can make a huge difference in costs. Let’s break down why size really does matter.
The cost of injection molding is influenced by part size due to increased material usage, mold size, and machine time, with larger parts incurring higher expenses.
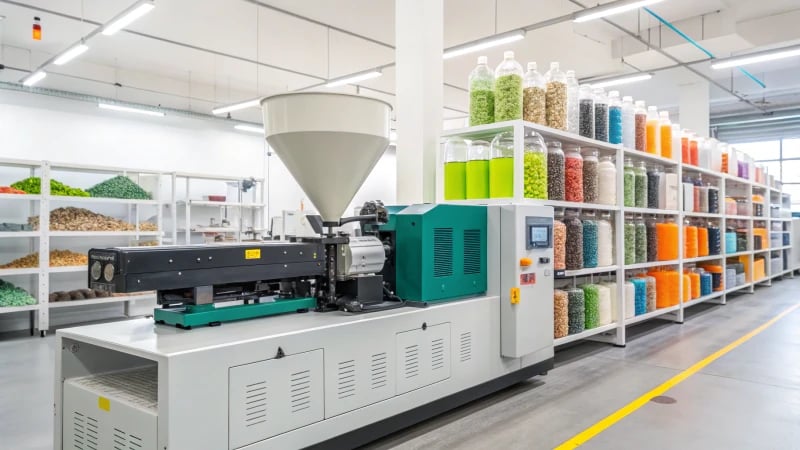
Understanding Material Costs
I remember the first time I tackled a project involving larger molded parts; I was floored by the material costs. It was like realizing my grocery bill doubled when my kids hit their teenage years! Larger parts demand more raw material, which can really drive up expenses. And if you opt for high-performance polymers instead of standard plastics, well, that’s like splurging on gourmet ingredients—it’ll cost you more. For a deep dive into different materials and how they impact costs, take a look at our material comparison guide11.
Tooling and Mold Size Impact
Then there’s the tooling to think about. Larger molds aren’t just big; they require complex machining processes that push tooling expenses higher. It’s similar to needing a custom-built kitchen for a chef’s dream home—more intricate and pricier than standard setups. To get a clearer picture of how mold dimensions affect pricing, check out our breakdown of tooling costs in injection molding12. And don’t forget, handling these larger molds might need specialized equipment, just like moving a piano requires professional movers.
Machine Time and Cycle Duration
Ah, the joys of machine time! Larger parts mean longer cooling requirements and cycle times, which can pile on the operational costs. It reminds me of waiting for a turkey to roast on Thanksgiving—longer than I’d like, but essential for a perfect meal. Understanding machine cycle efficiency13 can help you fine-tune your production schedule and cut down on waste.
Factor | Small Parts | Large Parts |
---|---|---|
Material Usage | Lower | Higher |
Mold Size | Smaller | Larger |
Cycle Time | Shorter | Longer |
Setup Fees | Lower | Higher |
Setup Fees and Production Runs
And let’s not overlook setup fees. They can be heftier for larger parts because precise calibration and testing are crucial. It’s like setting up a telescope: it takes time to get just right. These fees spread over the production run, meaning higher quantities can lower the cost per unit—like buying in bulk at the warehouse store. For tips on optimizing production runs, visit our setup fee analysis14.
Larger injection molds increase tooling costs.True
Bigger molds need complex machining, raising tooling expenses.
Smaller parts require longer machine cycle times.False
Smaller parts generally have shorter cycle times, reducing costs.
How does cycle time affect the production of various sized parts?
Cycle time in manufacturing is like the heartbeat of production, dictating the rhythm and pace at which parts of all sizes come to life.
Cycle time impacts part production by balancing speed and quality. Short cycles increase throughput but may reduce quality, while longer cycles enhance precision but slow production. Optimal balance is key for efficiently producing parts of varying sizes.
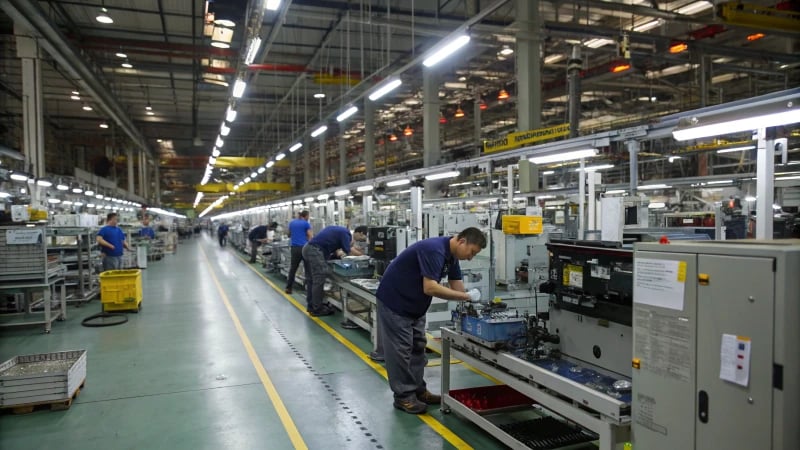
Understanding Cycle Time in Manufacturing
Have you ever thought about how quickly things move on a factory floor? Cycle time is that crucial number that tells us how long it takes to make one part from start to finish. It’s like the stopwatch of manufacturing, clicking away to measure our efficiency and cost-effectiveness. I remember when I first started in this field, and my mentor would always emphasize how a shorter cycle time could mean higher throughput. But, as exciting as that sounds, it could also lead to more defects if not handled carefully.
Impact on Various Sized Parts
Producing parts of different sizes adds another layer of complexity to cycle time management. Larger parts need more material and time, so naturally, their cycle times stretch longer. On the other hand, smaller parts can zip through production faster with reduced cycle times. However, the real challenge? Ensuring every part, big or small, meets the quality standards we strive for.
Part Size | Typical Cycle Time | Challenges |
---|---|---|
Small | Short | Precision |
Medium | Moderate | Balance |
Large | Long | Efficiency |
Balancing Cycle Time and Quality
Finding that sweet spot between cycle time and quality is like juggling. Longer cycles might promise better quality, but they slow down overall output. I’ve seen firsthand how effective quality management systems15 can help keep standards high without dragging out cycle times.
Strategies for Optimization
I’ve discovered a few tricks over the years to optimize these processes:
- Lean Manufacturing: This is all about cutting out waste and smoothing out operations.
- Automation: By automating certain tasks, we enhance consistency and cut down cycle time.
- Continuous Improvement: It’s crucial to regularly review and tweak processes to keep up with evolving production demands.
By getting a handle on cycle time, we can juggle efficiency and quality like pros, tailoring our approach to suit different sized parts perfectly. For those looking to dive deeper into boosting manufacturing efficiency, checking out resources on manufacturing best practices16 can be a great start.
Shorter cycle times always lead to higher throughput.False
While shorter cycle times can increase throughput, they may also increase defects.
Larger parts require longer cycle times due to more material.True
Larger parts need additional material and processing time, extending cycle times.
What Challenges Are Unique to Large vs. Small Part Molding?
Navigating the world of molding can feel like an intricate dance, especially when tackling large versus small parts. Let’s dive into the unique hurdles each size presents and how they shape your manufacturing journey.
Large part molding faces challenges in material flow and cooling, whereas small part molding demands high precision and tight tolerance. Understanding these differences is essential for effective injection molding.
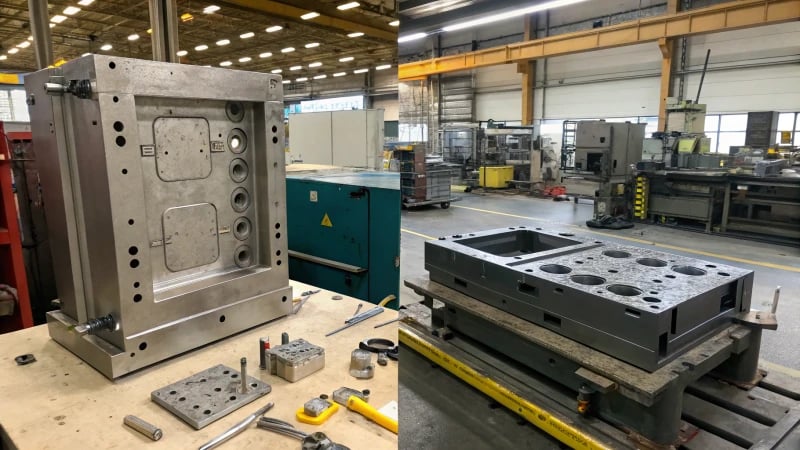
Differences in Material Behavior
I remember the first time I dealt with molding large parts. It felt like trying to wrangle a beast; the sheer volume of material meant that maintaining consistent material flow17 was no small feat. The risk of material stress and potential warping kept me on my toes. On the flip side, small parts are like crafting delicate jewelry—precision in material distribution is non-negotiable, as every tiny cavity in the mold must be filled perfectly to avoid defects.
Production Costs Considerations
Oh, those endless discussions on budget constraints! Large part molding demands a bigger chunk of your budget due to the sheer amount of raw materials needed and the prolonged cycle times, not to mention the necessity of investing in quality cooling systems. On the other hand, crafting small parts can be deceptively costly—achieving the required precision and maintaining rigorous quality controls often mean higher expenses.
Aspect | Large Parts | Small Parts |
---|---|---|
Material Volume | High | Low |
Cycle Time | Longer due to cooling needs | Shorter but requires precision |
Cost | Higher due to volume | Potentially high due to precision |
Design Considerations
In my design work with large parts, accommodating shrinkage and ensuring even cooling have always been critical. I once found that tweaking the design with variable wall thicknesses made a world of difference. For small parts, the real challenge lies in maintaining tight tolerances and preventing warpage. I’ve seen advanced design software18 work wonders in optimizing these designs.
Recognizing these unique challenges isn’t just about troubleshooting—it’s about empowering yourself to make informed decisions that ensure efficiency and quality in both large and small part molding processes. For further insights, explore resources on injection molding techniques19.
Large parts require more substantial material volumes.True
Large parts need more material, increasing flow and stress issues.
Small part molding has longer cycle times than large parts.False
Small parts have shorter cycles but need precision, unlike large parts.
Conclusion
Injection molding varies significantly for large and small parts, affecting mold design, material selection, machinery requirements, and costs. Understanding these differences is crucial for efficient production.
-
Explore material options that enhance mold durability for larger parts. ↩
-
Discover advanced machining techniques that improve precision for small part molds. ↩
-
Learn about systems that ensure precise temperature control in mold design. ↩
-
Explore how composites offer superior weight-to-strength ratios for large components. ↩
-
Learn how plastics provide cost-effective solutions with flexibility in design. ↩
-
Explore how composites offer superior weight-to-strength ratios for large components. ↩
-
Uncover eco-friendly alternatives like recyclable metals and biodegradable plastics. ↩
-
Understanding precision CNC machining capabilities will help in selecting the right machine for small part production. ↩
-
Delicate tooling ensures accuracy and prevents damage when machining small components. ↩
-
Choosing the right CNC machine can improve production efficiency and product quality. ↩
-
Discover various materials used in injection molding and their specific cost implications. ↩
-
Gain insights into how mold size and complexity affect tooling costs. ↩
-
Learn about optimizing machine cycles to improve production efficiency. ↩
-
Understand how setup fees impact overall production costs. ↩
-
Explore methods to maintain high-quality standards without extending production cycle times excessively. ↩
-
Discover proven strategies to enhance efficiency in manufacturing processes, particularly for varying part sizes. ↩
-
Understanding material flow is crucial for preventing defects in large molds, ensuring consistent quality. ↩
-
Using the right design software can streamline the mold design process, enhancing precision and efficiency. ↩
-
Learning about varied techniques can provide valuable strategies for tackling size-specific molding challenges. ↩