Have you ever paused to think about how those durable HDPE bottles come to be? Let’s dive into this intriguing process together!
Injection molding machines produce specific parts of HDPE bottles, like caps and handles. While they can make preforms, the complete bottle typically requires blow molding for full formation, making injection molding a supporting rather than primary method.
Join me as we explore the fascinating integration of injection and blow molding processes that optimize the production of HDPE bottles!
Injection molding can create complete HDPE bottles.False
Injection molding is used for parts like caps, not full bottles.
What is the Role of Injection Molding in HDPE Bottle Production?
Curious about injection molding’s place in making HDPE bottles? Discover its unique role here.
Injection molding contributes by crafting parts like caps and handles for HDPE bottles, not the full bottle.
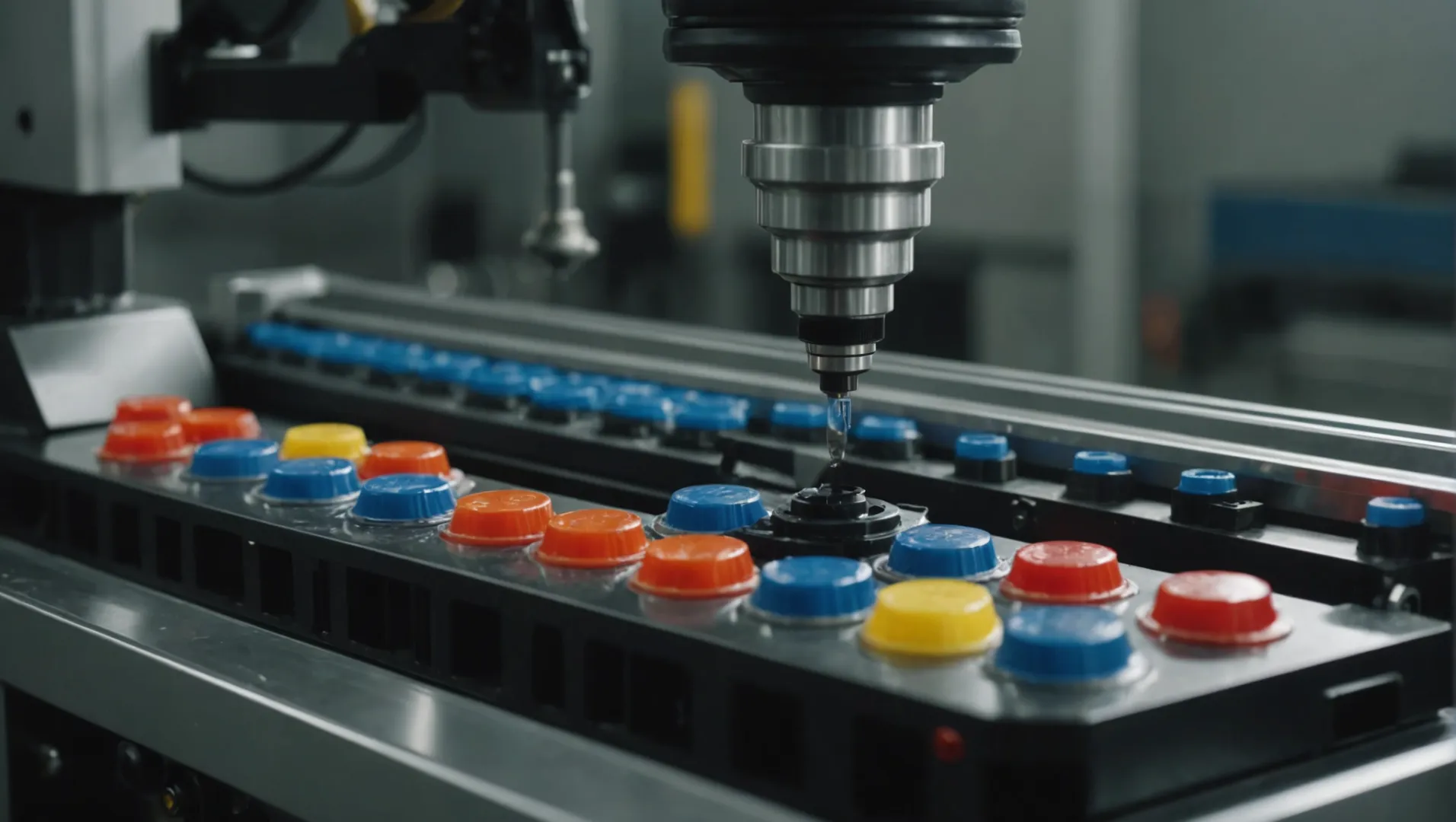
Understanding Injection Molding’s Contribution
Injection molding plays a distinct role1 in the production of high-density polyethylene (HDPE) bottles. While not primarily used for manufacturing the bottles themselves, this process is essential for creating specific components such as bottle caps and handles. These parts require precise shapes and durability, which injection molding machines are well-suited to produce.
Process Overview
Injection molding involves melting plastic pellets and injecting them into molds under high pressure. The molds are designed to form specific parts like preforms, which can later be transformed into complete bottles through additional methods like blow molding. Here’s a brief comparison of the role of injection molding versus blow molding:
Method | Primary Use | Role in HDPE Bottle Production |
---|---|---|
Injection Molding | Producing detailed parts | Caps, handles, and bottle preforms |
Blow Molding | Forming hollow containers | Complete bottle formation |
The Synergy with Blow Molding
While injection molding is not the primary method for creating entire HDPE bottles, it works in tandem with blow molding to optimize production. Injection molding machines produce preforms, which are then heated and inflated into full bottles by blow molding machines. This collaboration between the two methods enhances production efficiency and reduces costs.
Limitations of Injection Molding
Despite its usefulness in part production, injection molding is not suitable for creating hollow structures necessary for bottles. Specialized blow molding equipment is required to achieve the desired shape and integrity of HDPE bottles efficiently.
Explore more about why injection molding cannot serve as the primary method2 for bottle production, focusing instead on complementary roles that enhance overall manufacturing strategies. These insights underscore the importance of utilizing the right technology for each stage of the manufacturing process.
Injection molding is used for making HDPE bottle caps.True
Injection molding crafts precise, durable parts like caps.
Injection molding creates the entire HDPE bottle.False
Blow molding, not injection molding, forms complete bottles.
How Do Blow Molding and Injection Molding Work Together?
Uncover the synergy between blow molding and injection molding in HDPE bottle production, blending two technologies for optimal results.
Blow molding and injection molding work together by combining their strengths; injection molding creates precise components like caps, while blow molding efficiently forms the bottle’s body.
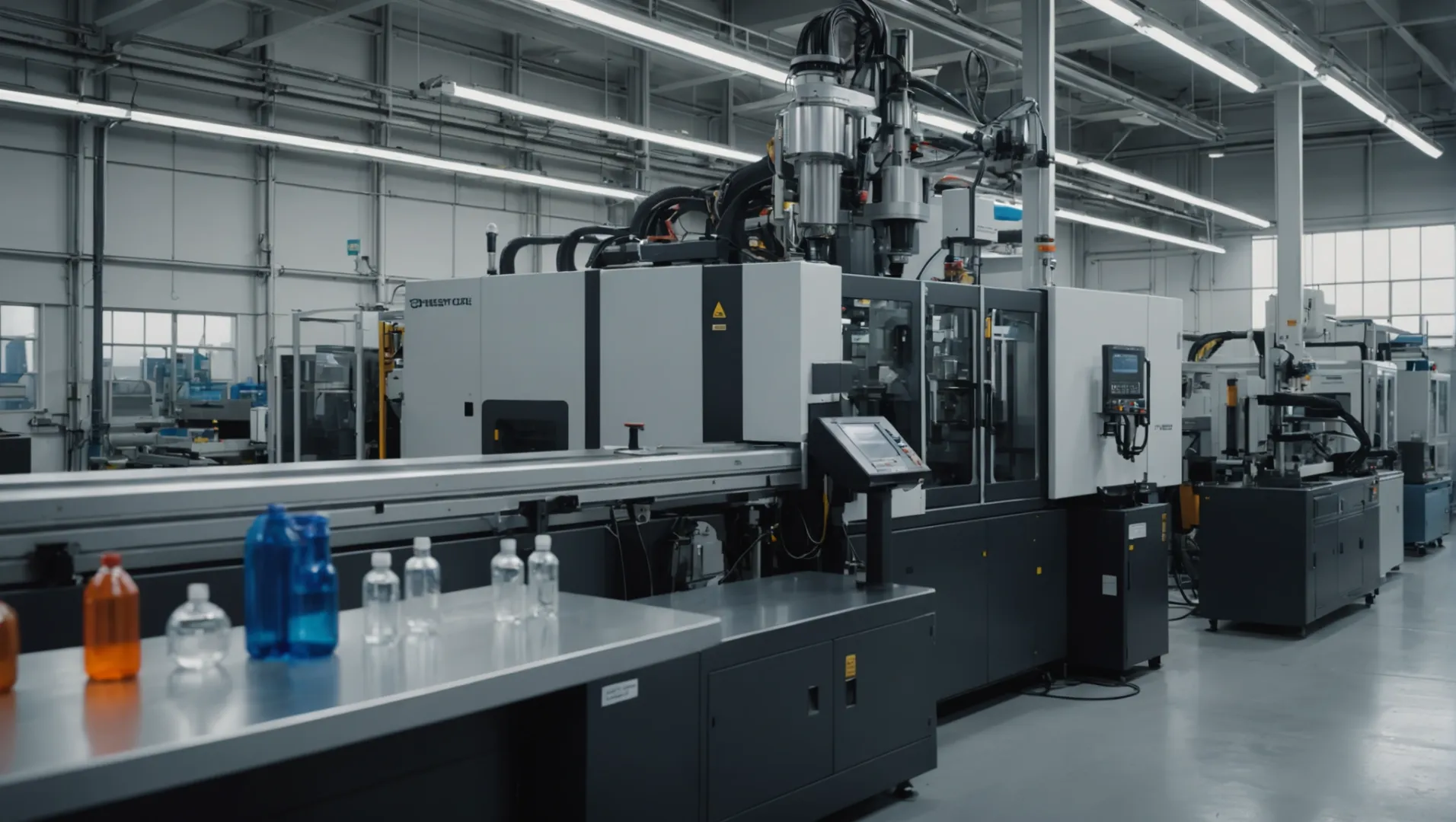
The Synergistic Relationship Between Molding Techniques
In the world of plastic manufacturing, injection molding3 and blow molding often work hand in hand to produce high-quality HDPE (high-density polyethylene) bottles. Each technique leverages its unique strengths, resulting in a seamless production process.
Injection Molding: Precision in Parts
Injection molding is crucial in crafting precise components of a bottle. It excels at producing intricate parts such as caps, handles, and threads with exceptional accuracy. This precision ensures that the final product is functional and reliable.
For instance, bottle caps require exact dimensions to fit securely onto bottles, preventing leaks and ensuring freshness. Injection molding can consistently produce these components with tight tolerances.
Blow Molding: Forming the Body
While injection molding is essential for smaller parts, blow molding takes over for the main body of the bottle. Specialized blow molding machines efficiently heat and expand HDPE granules into hollow structures. This method is ideal for creating large, seamless shapes with uniform wall thickness.
Blow molding’s efficiency makes it the preferred choice for producing the main body of HDPE bottles. The process allows for high-volume production with minimal waste, significantly reducing costs.
Integrating Both Processes
The integration of these two methods begins with injection molding creating preforms or specific parts. These preforms are then transferred to blow molding machines to expand and form complete bottles. This transition is smooth due to the compatibility of materials and processes.
A typical production line may look like this:
Step | Process | Description |
---|---|---|
1 | Injection Molding | Creation of precise parts like caps and handles |
2 | Preform Injection | Molding of preforms for the bottle body |
3 | Blow Molding | Expansion of preforms into full bottle structures |
By combining these techniques, manufacturers can produce robust and reliable HDPE bottles that meet industry standards and consumer expectations.
Understanding how these two techniques complement each other provides insight into why they are both indispensable in modern plastic manufacturing.
Injection molding creates precise bottle components.True
Injection molding is used for making detailed parts like caps.
Blow molding forms the bottle's intricate components.False
Blow molding is used for forming the main body, not small parts.
Why Isn’t Injection Molding the Primary Method for HDPE Bottles?
Curious why injection molding isn’t the go-to for HDPE bottles? Discover the reasons behind this preference in manufacturing.
Injection molding isn’t the primary method for HDPE bottles due to its complexity and cost. Blow molding, in contrast, offers a direct, efficient way to produce bottles, reducing the steps and materials involved.
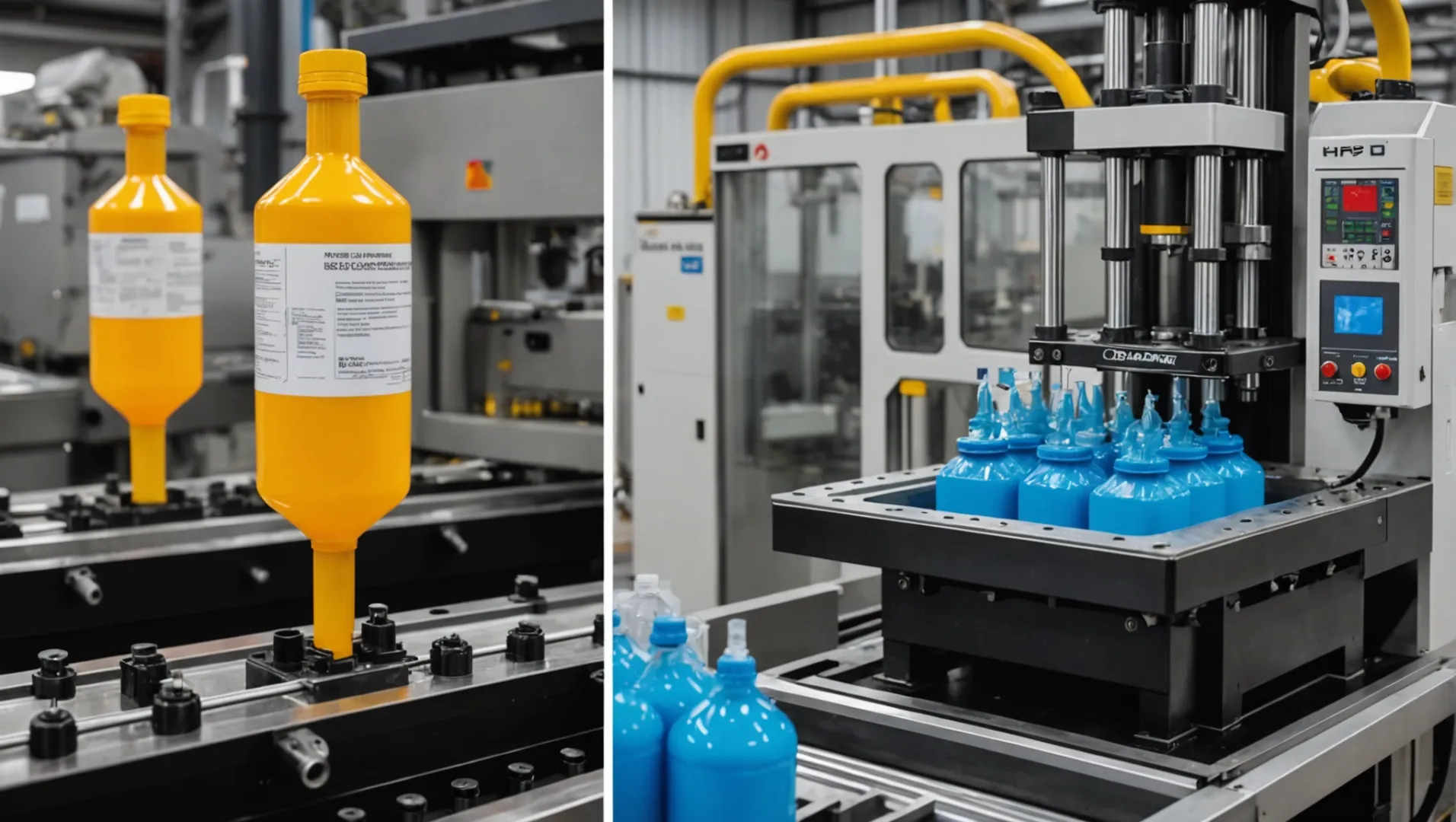
Understanding Injection Molding Limitations
Injection molding machines are adept at creating intricate plastic parts. However, when it comes to HDPE bottles, they face limitations. This method involves injecting molten plastic into molds to form preforms, which are later reshaped. For HDPE bottles, this process is often complex and costly compared to alternatives.
While injection molding is excellent for manufacturing precise components4 like caps and handles, crafting an entire bottle requires additional steps. The preform made through injection molding still needs to be blow molded to achieve its final shape. This extra step makes the process less appealing for mass production.
The Efficiency of Blow Molding
Blow molding stands out as the preferred technique for HDPE bottles due to its efficiency. This method melts HDPE granules and directly blows them into molds, forming complete bottles in one step. It eliminates the need for preform creation, streamlining production and reducing costs.
Method | Steps Involved | Cost Implications |
---|---|---|
Injection Molding | Preform creation + blow molding | Higher due to multiple steps |
Blow Molding | Direct bottle formation | Lower; single-step process |
With its higher production speed and lower costs, blow molding is naturally favored in large-scale operations.
Integration of Both Methods
Despite its drawbacks as a standalone method, injection molding isn’t entirely sidelined. It plays a crucial supporting role in the production of certain bottle parts. For example, injection molding’s precision is unparalleled in making threaded caps that require exact specifications.
In industries where precision and mass production are equally important, combining both methods can be beneficial. Injection molding ensures that detailed components meet quality standards, while blow molding efficiently handles bulk bottle production.
Explore how these techniques complement each other in the plastic manufacturing landscape5. This synergy highlights why injection molding remains integral to certain stages of HDPE bottle production.
Injection molding is more costly for HDPE bottles.True
Injection molding involves additional steps, increasing complexity and cost.
Blow molding requires preform creation for HDPE bottles.False
Blow molding directly forms bottles, eliminating preform creation.
What Are the Advantages of Using Blow Molding for HDPE Bottles?
Discover the efficiency of blow molding in crafting HDPE bottles and why it’s preferred over other methods.
Blow molding is ideal for HDPE bottles due to its high production efficiency, cost-effectiveness, and ability to directly form complete bottles from HDPE granules.
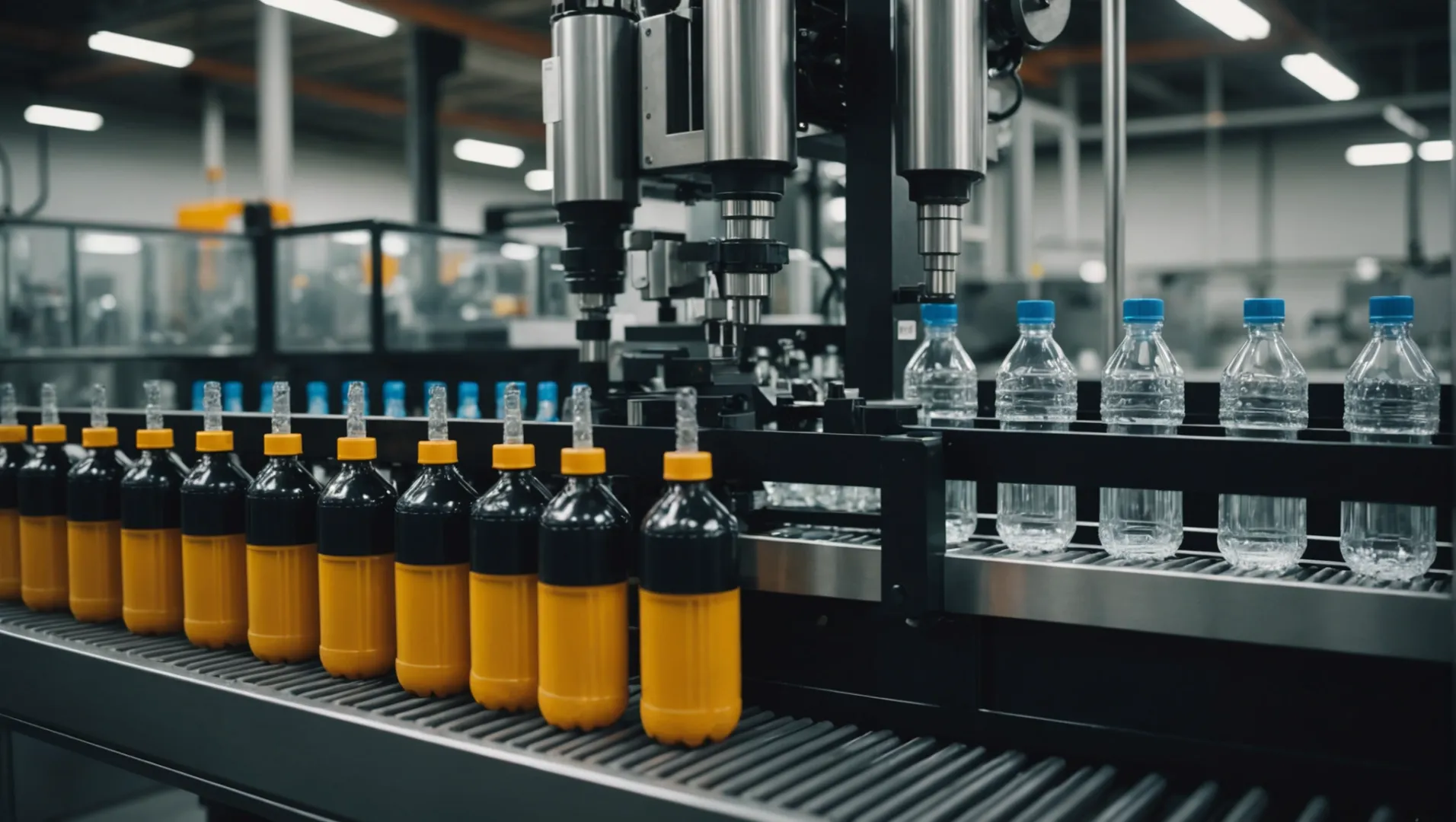
Understanding Blow Molding for HDPE Bottles
Blow molding stands out as a versatile method for producing HDPE bottles6. Unlike other techniques, it directly shapes molten plastic into hollow objects by inflating them within a mold. This process is efficient, allowing manufacturers to produce large quantities rapidly.
Advantages of Blow Molding
-
High Production Efficiency: Blow molding machines can continuously produce HDPE bottles with minimal downtime. This efficiency is crucial for meeting high demand in industries such as packaging and consumer goods.
-
Cost-Effectiveness: The simplicity of the blow molding process contributes to lower production costs. Compared to injection molding, which involves multiple steps to achieve the final product, blow molding reduces labor and energy expenses.
-
Design Flexibility: Blow molding offers remarkable flexibility in bottle design. Manufacturers can easily adjust mold designs to create various shapes and sizes, accommodating diverse market needs without significant changes in the production line.
-
Material Utilization: This method makes optimal use of HDPE material, minimizing waste. The direct heating and expansion of granules ensure that most of the material forms part of the bottle, reducing scrap.
How Blow Molding Outperforms Other Methods
In the realm of plastic bottle production, blow molding excels where injection molding7 falls short. While injection molding is excellent for detailed parts like caps or handles, it lacks the capability to efficiently form complete bottles from start to finish.
A comparative analysis between these methods reveals that blow molding integrates better with large-scale manufacturing setups. Its ability to streamline the production process from raw material to final product makes it indispensable for companies looking to optimize output and reduce costs.
By leveraging these advantages, businesses can meet consumer demands efficiently, maintain competitive pricing, and uphold quality standards in the ever-evolving market of HDPE bottle manufacturing.
Blow molding is more cost-effective than injection molding.True
Blow molding reduces labor and energy expenses, lowering costs.
Injection molding offers better design flexibility than blow molding.False
Blow molding allows easy adjustments in mold designs for various shapes.
Conclusion
Injection molding plays a key role in producing specific components of HDPE bottles, but relies on blow molding for complete bottle formation. Together, they enhance manufacturing efficiency.
-
Discover the specific role of injection molding in crafting bottle parts.: HDPE injection molding uses high-density polyethylene (HDPE), a cost-effective thermoplastic with good tensile strength and high impact resistance. ↩
-
Learn why injection molding isn’t used for entire bottle creation.: The substantial initial expenditure necessary for tooling the mold in HDPE injection molding is one of the most prominent disadvantages of this manufacturing … ↩
-
Learn how injection molding creates precise bottle components.: With injection molding, molten plastic is injected into a mold cavity under high pressure, creating a part all at once. Both processes are … ↩
-
Explore how injection molding excels in creating precise plastic parts.: It minimises molding costs and is a highly repeatable way of producing plastic or elastomeric parts with high precision. Once set up, it can … ↩
-
Discover the synergy between blow and injection molding in production.: Injection molding is used for complex solid components whereas blow molding is used for thin-walled hollow parts. ↩
-
Learn how blow molding enhances production efficiency for HDPE bottles.: Versatility – Compared to other plastics used by reputable blow molding manufacturers, HDPE is incredibly versatile. · Lightweight – As mentioned … ↩
-
Understand why blow molding is preferred for complete HDPE bottle formation.: Injection molding is used for complex solid components whereas blow molding is used for thin-walled hollow parts. ↩