Ever wondered if glass-filled nylon could be your game-changer in injection molding? It just might be!
Injection molding with glass-filled nylon is highly effective, providing enhanced strength, stiffness, and heat resistance compared to regular nylon, making it ideal for demanding applications.
I remember the first time I considered using glass-filled nylon for a project—it felt like stepping into unknown territory. Yet, as I delved deeper, I discovered its unique properties that set it apart from other materials. In the following sections, I’ll share insights into how glass-filled nylon compares to other materials and what you need to keep in mind when working with it. Join me as we explore how this amazing material can elevate your designs and manufacturing processes to new heights.
Glass-filled nylon enhances strength in injection molding.True
Glass-filled nylon increases strength, making it suitable for robust applications.
Glass-filled nylon is unsuitable for high-temperature applications.False
Glass-filled nylon offers excellent heat resistance, ideal for high-temperature uses.
- 1. What Makes Glass-Filled Nylon So Special?
- 2. What Makes Glass-Filled Nylon Stand Out from Other Materials?
- 3. What Are the Advantages of Using Glass-Filled Nylon in Injection Molding?
- 4. What are the Challenges in Molding Glass-Filled Nylon?
- 5. What Applications Benefit Most from Glass-Filled Nylon?
- 6. What are the key processing conditions for glass-filled nylon?
- 7. Conclusion
What Makes Glass-Filled Nylon So Special?
When I first started working with glass-filled nylon, I was amazed by its strength and versatility. It’s a go-to material for many engineers, including myself, in challenging applications.
Glass-filled nylon is nylon with glass fibers, enhancing its strength, stability, wear, and heat resistance, ideal for demanding engineering applications.
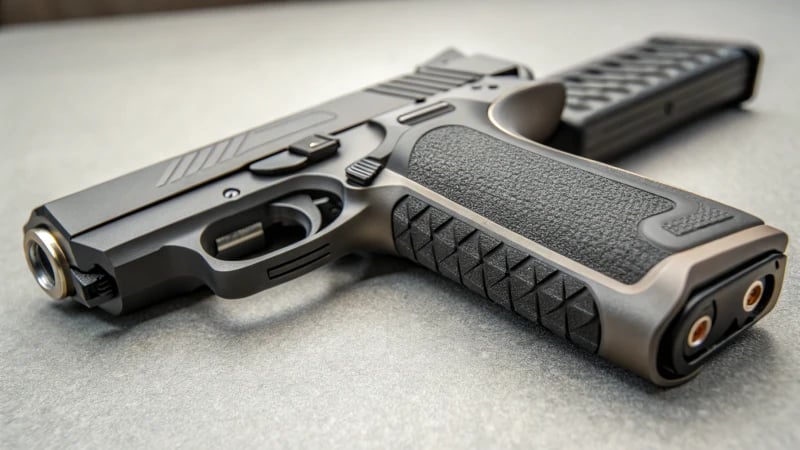
Mechanical Properties of Glass-Filled Nylon
I remember the first time I encountered glass-filled nylon in my design work. It was like discovering a hidden superpower for my projects. The addition of glass fibers transforms regular nylon into a material with exceptional mechanical strength. Imagine being able to design components that can withstand significant loads without bending or breaking—that’s what glass-filled nylon offers. Its tensile strength is remarkably high, which means it can handle pressure like a champ.
Property | Value |
---|---|
Tensile Strength | Up to 260 MPa |
Flexural Modulus | 6,000 to 10,000 MPa |
Impact Resistance | High |
Thermal Properties
Thermal stability is another reason I keep coming back to glass-filled nylon for my designs. It can withstand temperatures up to 120°C without losing its integrity—pretty impressive, right? This makes it ideal for parts that need to perform reliably under heat stress. Plus, its reduced thermal expansion compared to unfilled nylon means it maintains performance consistency even when temperatures fluctuate. Knowing these thermal characteristics1 allows me to design with confidence, predicting how the material will behave under different conditions.
Chemical Resistance and Applications
Then there’s the chemical resistance—it’s like the icing on the cake for this wonder material. Glass-filled nylon stands up well against oils, solvents, and even some acids. This opens up a world of possibilities for its use in environments where exposure to such substances is common.
- Automotive Components: Perfect for engine covers and other parts exposed to high temperatures and chemical fluids.
- Industrial Gears: With its excellent wear resistance and strength, it’s often my material of choice for gears that require durability.
For anyone weighing options between materials like glass-filled nylon and aluminum2, it’s crucial to look at their specific properties and how they fit your project’s needs.
By delving into these properties, I’ve been able to make smarter decisions in my designs, ensuring they are both high-performing and durable.
Glass-filled nylon can withstand temperatures up to 120°C.True
Glass-filled nylon maintains its strength at temperatures up to 120°C.
Glass-filled nylon has lower tensile strength than standard nylon.False
The addition of glass fibers increases the tensile strength of nylon.
What Makes Glass-Filled Nylon Stand Out from Other Materials?
When I first stumbled upon glass-filled nylon, I was curious about how it compared to other materials I’d worked with. Let’s dive into what makes this polymer so intriguing.
Glass-filled nylon is notable for its superior strength and thermal resistance compared to standard polymers, making it ideal for demanding applications, albeit with higher costs and reduced flexibility.
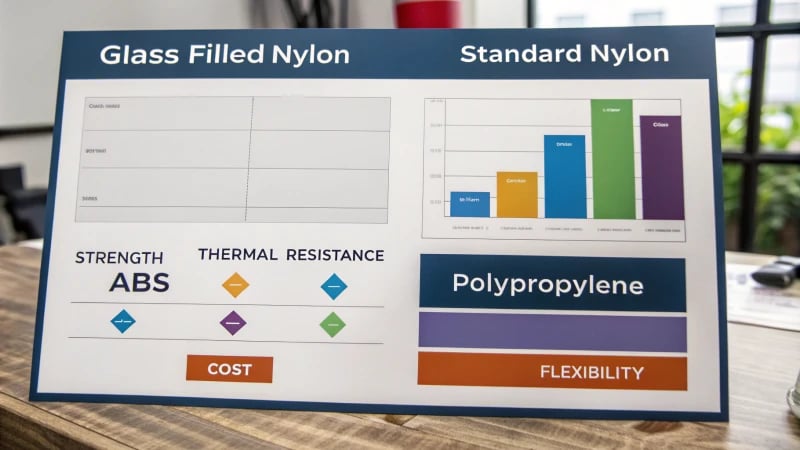
Understanding the Composition of Glass-Filled Nylon
Imagine you’re piecing together a puzzle that needs to withstand a lot of wear and tear. Glass-filled nylon is like adding steel reinforcements to your favorite puzzle piece. By weaving glass fibers into the nylon matrix, it significantly ramps up the tensile and compressive strengths, making it ideal for applications requiring robust structural integrity3. I’ve found it particularly impressive when working on projects where structural integrity is non-negotiable, like crafting parts that have to endure high stress or temperatures.
Comparing Mechanical Properties
A comparison between glass-filled nylon and other materials can be summarized in the following table:
Material | Tensile Strength | Flexibility | Cost |
---|---|---|---|
Glass-Filled Nylon | High | Low | High |
Standard Nylon | Moderate | Moderate | Low |
Polycarbonate | High | High | High |
ABS | Low | High | Low |
Through trial and error, I’ve learned that while glass-filled nylon offers fantastic strength, it doesn’t bend as easily as materials like polycarbonate or ABS.
Advantages Over Standard Polymers
One of the most compelling reasons I gravitate toward glass-filled nylon is its superior performance in structural applications. Whether I’m working on automotive parts or machinery components, its high strength-to-weight ratio is a game-changer for engineered components4. Plus, its thermal resistance means it can handle those unexpected temperature spikes without breaking a sweat.
Potential Drawbacks
On the flip side, I’ve noticed that adding glass fibers can make the material more brittle in some scenarios. It’s also pricier than standard options like nylon or ABS, which can be a dealbreaker if you’re managing a tight budget for large-scale production.
Applications in Industry
In industries like automotive and electronics design, glass-filled nylon has become a staple for me. Its resilience against mechanical stresses and heat makes it perfect for things like brackets and gears. And let’s not forget about the aesthetic qualities5 it offers—ideal for consumer products that need both style and substance.
All in all, while glass-filled nylon brings a lot to the table in terms of strength and thermal stability, you really have to weigh these benefits against its cost and flexibility to determine if it’s the right fit for your project.
Glass-filled nylon has higher tensile strength than ABS.True
The table shows glass-filled nylon has high tensile strength, while ABS is low.
Glass-filled nylon is more flexible than polycarbonate.False
The table indicates polycarbonate has high flexibility, unlike glass-filled nylon.
What Are the Advantages of Using Glass-Filled Nylon in Injection Molding?
Ever wondered why glass-filled nylon is the go-to for injection molding? Let me take you through the perks that make this material a superstar in manufacturing.
Glass-filled nylon enhances injection molding by providing exceptional strength, rigidity, and thermal stability, making it ideal for demanding environments and improving the durability and efficiency of molded components.
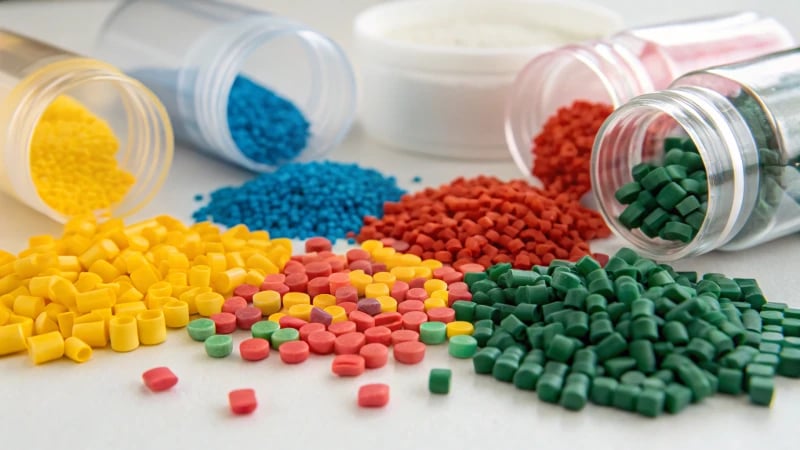
Enhanced Mechanical Properties
I remember the first time I came across glass-filled nylon in a project. I was skeptical about its claims. But once I saw its mechanical properties6 in action, I was hooked. The addition of glass fibers transforms this material into something robust and unyielding. It’s like turning a regular old bike into a high-performance sports car—suddenly, you’re dealing with a different beast entirely. This makes it perfect for applications needing tough components like automotive engine parts or industrial gears.
Thermal Stability and Resistance
Let’s talk about temperature swings. Imagine your part is like a seasoned actor who can perform just as well in the heat of a desert or the chill of an Arctic winter. That’s glass-filled nylon for you—it maintains its shape and strength across a range of temperatures, so there’s no fear of it buckling under pressure. I can’t count the number of times I’ve seen it outperform other materials in high-heat situations.
Improved Dimensional Stability
Precision is key, right? During my years in design, I’ve learned that even the slightest dimensional error can throw a project off course. Thankfully, glass-filled nylon shrinks less during the cooling phase7 of molding, ensuring every piece fits perfectly. It’s like having a tailor who gets your measurements right every single time.
Property | Standard Nylon | Glass-Filled Nylon |
---|---|---|
Tensile Strength (MPa) | 70-90 | 120-210 |
Modulus of Elasticity | 2-4 GPa | 7-12 GPa |
Thermal Resistance | Moderate | High |
Dimensional Stability | Variable | Excellent |
Resistance to Wear and Chemical Exposure
In industries like automotive and electronics, where every part must last as long as possible, glass-filled nylon is a hero. It’s resistant to wear and chemicals, enduring harsh conditions without losing its integrity. I always think of it as wearing armor; no matter how tough the journey, it comes out unscathed.
Cost-Effectiveness and Application Versatility
Initially, I was wary about the cost, thinking about budget constraints in past projects. But the durability and reduced maintenance costs over time made it worth every penny. Whether it’s for consumer electronics or industrial machinery8, this material adapts like a chameleon to whatever application you throw at it.
Glass-filled nylon has higher tensile strength than standard nylon.True
Glass fibers enhance tensile strength, making it 120-210 MPa versus 70-90 MPa.
Glass-filled nylon is less resistant to chemical exposure than standard nylon.False
It is more resistant due to its enhanced durability and wear properties.
What are the Challenges in Molding Glass-Filled Nylon?
Ever tried molding glass-filled nylon? It can feel like juggling a handful of challenges!
Molding glass-filled nylon is challenging due to increased brittleness, higher tool wear, and potential cost issues, requiring specialized techniques and materials to address these difficulties effectively.
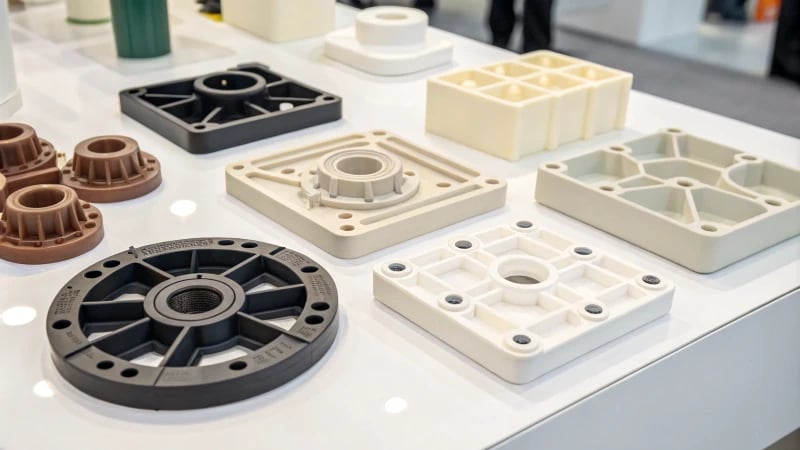
Understanding the Properties of Glass-Filled Nylon
I remember the first time I worked with glass-filled nylon. This composite material, blending nylon with glass fibers, promises enhanced strength and rigidity. It’s like adding some muscle to your designs, which is fantastic, but it also means facing a few curveballs in the molding process.
Property | Description |
---|---|
Strength | Increased tensile strength |
Rigidity | Higher modulus of elasticity |
Brittleness | More prone to cracking |
The Impact on Tool Wear
The abrasive nature of glass fibers can really chew up tools—I’ve been there, watching my tools wear down faster than I’d like. This translates to frequent maintenance and replacements, which can be a real budget buster. I’ve learned that using wear-resistant materials9 for mold construction can be a lifesaver.
Challenges in Surface Finish
Getting that smooth, sleek finish with glass-filled nylon isn’t always a walk in the park. The inherent texture can leave you with a less-than-perfect surface, especially if you’re working on consumer-facing components. I’ve found that techniques like post-mold finishing or using specific mold coatings can make all the difference in achieving that polished look.
Cost Implications
The costs can add up quickly—more tool wear, extra surface finishing steps—it all impacts the bottom line. Weighing these costs against the benefits of glass-filled nylon can be quite the balancing act. Sometimes exploring alternative materials that offer similar advantages10 without the hefty price tag is worth considering.
Mitigating Challenges with Process Adjustments
Over the years, I’ve learned that tweaking processing parameters like temperature and pressure can alleviate some of the challenges. Collaborating closely with material suppliers has also provided invaluable insights into optimizing these parameters for better outcomes.
Need for Specialized Equipment
With its unique properties, glass-filled nylon demands specialized equipment that can handle the extra pressures and wear. I’ve found that investing in or leasing such equipment is crucial for manufacturers looking to incorporate this material into their production lines.
By addressing these aspects strategically, manufacturers can leverage the benefits of glass-filled nylon while minimizing its potential drawbacks, ultimately achieving efficient and high-quality production outcomes. Exploring new techniques11 and innovations in the field can further enhance these efforts.
Glass-filled nylon increases tool wear during molding.True
The abrasive nature of glass fibers in the composite leads to increased tool wear.
Glass-filled nylon offers a smoother surface finish than pure nylon.False
The texture of glass fibers makes achieving a smooth finish more difficult.
What Applications Benefit Most from Glass-Filled Nylon?
Have you ever wondered how some materials can completely revolutionize industries? Glass-filled nylon is one of those game-changers!
Glass-filled nylon, known for its strength, stiffness, and heat resistance, is ideal for automotive, aerospace, and electronics applications, such as engine covers, gears, and circuit board holders.
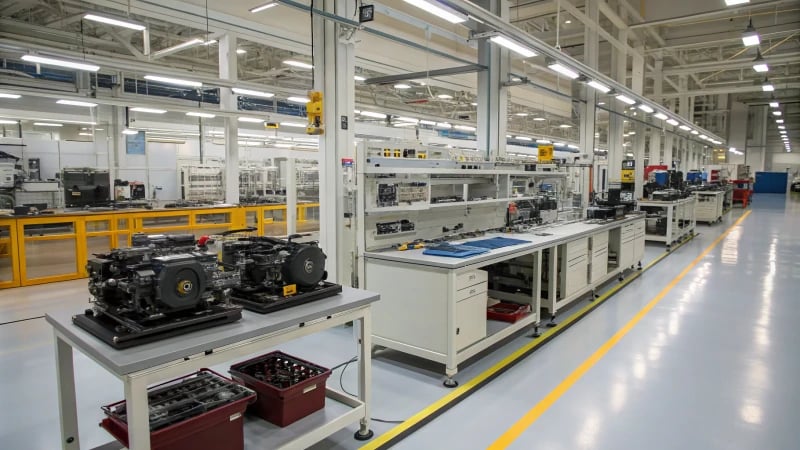
When I first encountered glass-filled nylon in my work as a mold designer, it felt like discovering a hidden gem. Its ability to transform everyday components with its unique blend of strength and lightweight properties immediately caught my attention.
Automotive Industry Applications
In the automotive world, glass-filled nylon12 is a bit of a superhero. I remember working on a project where we needed to replace heavy metal parts with something more efficient. The lightweight nature of glass-filled nylon was a perfect fit, allowing us to create lighter vehicles that consumed less fuel—a win for both performance and the environment.
Component | Benefits |
---|---|
Engine Covers | Lightweight, heat resistant |
Air Intake Manifolds | Enhanced durability, cost-effective |
Aerospace Sector Usage
Working with glass-filled nylon in the aerospace sector was another eye-opener. The challenge was always about reducing weight without sacrificing strength, and this material delivered time and again. I recall designing brackets and housings that had to endure extreme conditions; glass-filled nylon offered the precise molding and durability we needed.
Electrical and Electronics Industry
In my experience with electronics, maintaining insulation under varied temperatures is crucial. Glass-filled nylon’s excellent insulation properties13 made it a staple in connectors and circuit board holders. It was thrilling to see how it met our high-performance standards so consistently.
Application | Advantage |
---|---|
Connectors | Superior insulation, thermal stability |
Circuit Board Holders | Precise fit, high strength |
Consumer Goods Manufacturing
Beyond industrial applications, I’ve seen glass-filled nylon perform impressively in consumer goods. For instance, in designing parts for power tools and appliances, its impact resistance and chemical durability were vital. It’s fascinating how this material continues to meet both aesthetic and functional needs across so many fields.
Overall, choosing glass-filled nylon14 is driven by its versatility, making it a favorite for replacing traditional materials and achieving superior product performance. It feels good to know that my work with such a dynamic material can make a real difference.
Glass-filled nylon is used in engine covers for weight reduction.True
Glass-filled nylon's strength-to-weight ratio makes it ideal for engine covers.
In aerospace, glass-filled nylon is not used due to weight issues.False
Aerospace uses glass-filled nylon to reduce weight while maintaining strength.
What are the key processing conditions for glass-filled nylon?
Navigating the ins and outs of processing glass-filled nylon can feel like mastering a complex puzzle.
For glass-filled nylon, it’s all about balancing moisture content, melting temperature, and injection pressure. Start by pre-drying the material at 80°C for 4-8 hours to avoid defects, and aim for a molding temperature between 260°C and 290°C to get the best results.
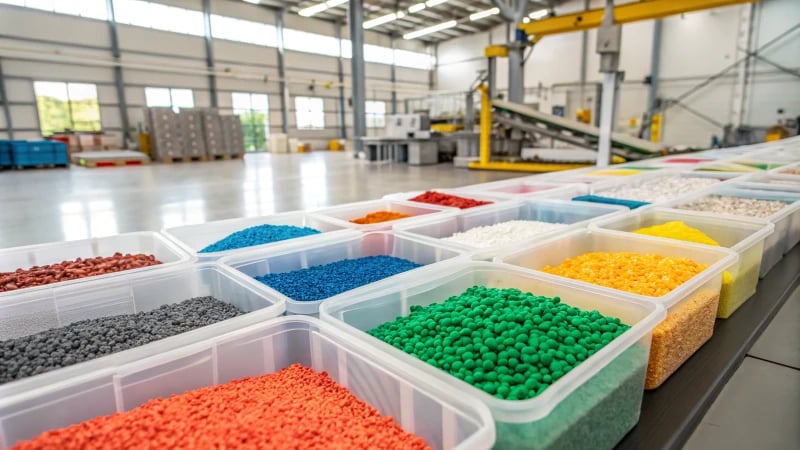
Understanding Glass-Filled Nylon
Let me take you back to my first encounter with glass-filled nylon. Imagine me, a wide-eyed newbie in the mold factory, watching as seasoned experts handled this composite material like it was second nature. Glass-filled nylon, a mix of nylon and glass fibers, boasts mechanical properties15 that are nothing short of impressive. It significantly enhances tensile strength and rigidity, making it perfect for applications that demand durability.
Moisture Management
I’ve learned that managing moisture is crucial—like preparing your dough just right before baking. The same goes for glass-filled nylon. Pre-drying it at 80°C for 4-8 hours can save you from headaches later on, such as hydrolysis or unsightly surface defects. I remember relying on a trusty dehumidifying dryer to ensure everything stayed within the 0.20% moisture limit.
Moisture Control | Recommended Action |
---|---|
Initial Moisture | Max 0.20% |
Drying Temperature | 80°C |
Drying Duration | 4-8 hours |
Temperature Settings
Temperature control—it’s like playing a game of chess where every move counts. During injection molding, I keep melt temperatures between 260°C and 290°C. This careful setting ensures a smooth melt flow and minimizes the risk of warping16.
Injection Pressure and Speed
Finding the sweet spot in injection pressure and speed can be tricky, but it’s essential for quality. I usually go for moderate speeds to avoid shear heating. Pressures in the range of 750 to 1500 bar often work wonders, but these settings can vary based on mold design and part geometry.
Injection Parameter | Typical Range |
---|---|
Injection Pressure | 750-1500 bar |
Mold Temperature | Variable |
Cooling Time | Based on thickness |
Cooling Time and Ejection
Cool down time—it’s like letting a cake rest before you dig in. For glass-filled nylon, rushing this stage might induce internal stresses. Allocating adequate cooling time ensures full crystallization, ultimately boosting part performance.
By understanding these processing conditions17, I’ve seen firsthand how consistent adjustments can lead to exceptional part quality and performance. Each parameter is like a piece of the puzzle that needs to fit perfectly for the best results.
Glass-filled nylon requires drying at 80°C for 4-8 hours.True
Drying at 80°C for 4-8 hours prevents moisture-related defects.
Melt temperatures for glass-filled nylon should be 300°C to 320°C.False
Recommended melt temperatures are 260°C to 290°C for optimal flow.
Conclusion
Glass-filled nylon enhances injection molding with superior strength, thermal stability, and chemical resistance, making it ideal for demanding applications in automotive, aerospace, and electronics industries.
-
Explore how glass-filled nylon performs under varying temperature conditions. ↩
-
Find out how glass-filled nylon measures up against aluminum for specific applications. ↩
-
Learn how structural integrity impacts material performance and why it’s crucial in engineering applications. ↩
-
Explore why materials with high strength-to-weight ratios are favored in engineering and design. ↩
-
Discover how glass-filled nylon’s appearance enhances product design in consumer electronics. ↩
-
Explore how glass fibers enhance nylon’s strength and stiffness, making it ideal for demanding applications. ↩
-
Understand why glass-filled nylon exhibits less shrinkage during cooling, ensuring precision in molded parts. ↩
-
Discover how glass-filled nylon’s versatility suits various industrial applications, enhancing performance and durability. ↩
-
Learn about materials that can reduce tool wear in molding applications, extending tool life. ↩
-
Discover other materials that offer similar strength and rigidity without the same challenges. ↩
-
Investigate recent advancements and methods to improve molding efficiency and product quality. ↩
-
Discover why automotive manufacturers prefer glass-filled nylon for creating lighter, more efficient vehicles. ↩
-
Learn how glass-filled nylon’s insulation properties benefit electronic component design. ↩
-
Understand how consumer goods benefit from the durability and versatility of glass-filled nylon. ↩
-
Discover how glass fibers enhance the mechanical properties of nylon, offering superior strength and stability for various applications. ↩
-
Learn methods to avoid warping during injection molding, ensuring dimensional accuracy and product quality. ↩
-
Explore effective processing conditions that lead to high-quality plastic parts with minimal defects. ↩