Do you ever think about how small details in production decide the final appearance of a product?
Different gate types in injection molding, such as direct sprue, side, spot, submerged, and scalloped, affect product appearance by influencing surface finish, visible marks, and structural integrity.
When I first explored injection molding, I was amazed by how a small gate affects a product’s appearance and feel. Each gate type serves a unique role. Understanding these roles felt like cracking a secret code for perfect designs. The choice might influence the strength of a large plastic drum. It might also impact the shiny finish of a fancy cosmetic cap. Selecting the correct gate type is crucial. It feels like picking the perfect tool from a craftsman’s kit to craft a masterpiece.
Direct sprue gates enhance product surface finish.False
Direct sprue gates often leave visible marks, affecting surface finish.
Submerged gates minimize visible marks on products.True
Submerged gates are designed to reduce visible gate marks on surfaces.
- 1. What are the advantages and disadvantages of using a direct sprue?
- 2. How Does Side Gating Enhance Product Aesthetics?
- 3. When Should You Use Spot Gates for Injection Molding?
- 4. Why Are Submerged Gates Preferred for High-Quality Finishes?
- 5. How Do Scalloped Gates Improve Surface Uniformity?
- 6. How can I optimize gate design for better product appearance?
- 7. Conclusion
What are the advantages and disadvantages of using a direct sprue?
Entering the world of injection molding feels like navigating a maze of choices. Selecting the right gating system is challenging. Direct sprue is one option. This option has its own advantages and disadvantages.
Direct sprue in injection molding lets material go straight into the mold’s center. This method is great for large and thick-walled items that really need strength. Visible marks may appear around the gate area. Stress might also develop there.
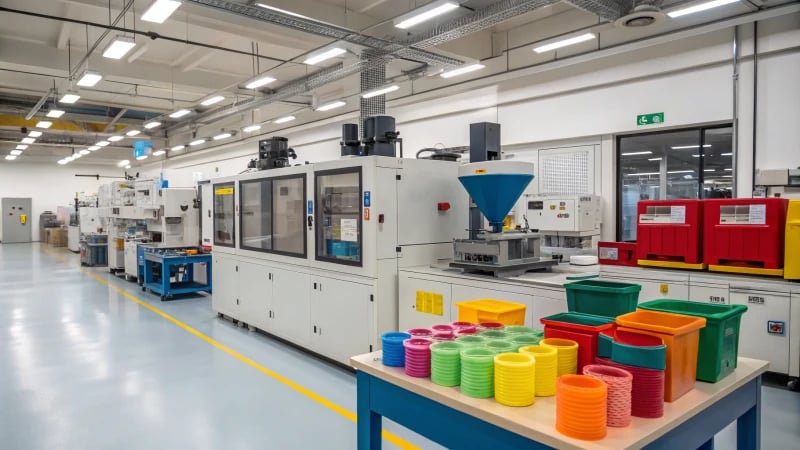
Understanding Direct Sprue
A direct sprue1 is a type of gating in injection molding where molten material flows straight into the mold cavity from the center. This method is particularly advantageous for products that need to be both large and mechanically robust.
Advantages of Direct Sprue
- Great for Large Products: When creating big, thick items, this method acts like a strong base. It helps fit everything perfectly and maintains the right pressure.
- Strong Structure: Imagine making something tough like a large plastic drum. Direct sprue supports it well, keeping it strong under pressure.
Advantage | Description |
---|---|
Structural Strength | Ensures strong mechanical properties for large items. |
Pressure Efficiency | Offers effective pressure management during molding. |
Disadvantages of Direct Sprue
But, like any friend, direct sprue has quirks. Visible sprue marks can remind you of a dinner party with a centerpiece that’s too bold.
- Visible Sprue Marks: These are noticeable bumps that might not look nice if you want a smooth finish.
- Possible Stress: The forceful entry creates tension around the gate. This may cause deformation or defects like fusion marks, which isn’t ideal if you desire a polished look.
Disadvantage | Description |
---|---|
Appearance Issues | Leaves noticeable marks on finished products. |
Stress Induction | Can introduce stress points leading to defects. |
Comparing With Other Gating Types
When comparing direct sprue with others like side gating2 or submerged gates3, it’s like comparing different fruits. Side gating might be more flexible in appearance since it doesn’t call for attention from the center.
Consider alternatives like spot gates4, which have tiny entry points perfect for precision—like minimalist artists in the gating world. On the other hand, direct sprue appears bold in managing looks.
Looking closely at these techniques shows us how each meets specific needs and quality demands. Every method offers different trade-offs, much like choosing between style and comfort in shoes for a long day.
Direct sprue is ideal for large products.True
Direct sprue supports large items by ensuring even pressure distribution.
Direct sprue eliminates all surface defects.False
It can leave visible marks, causing potential surface defects.
How Does Side Gating Enhance Product Aesthetics?
Have you ever thought about why some products have a perfect appearance? The secret is probably in how they are shaped.
Side gating improves how products look by placing the gate on the side. This placement reduces visible marks. It also helps material flow smoothly. This method suits products where appearance truly matters.
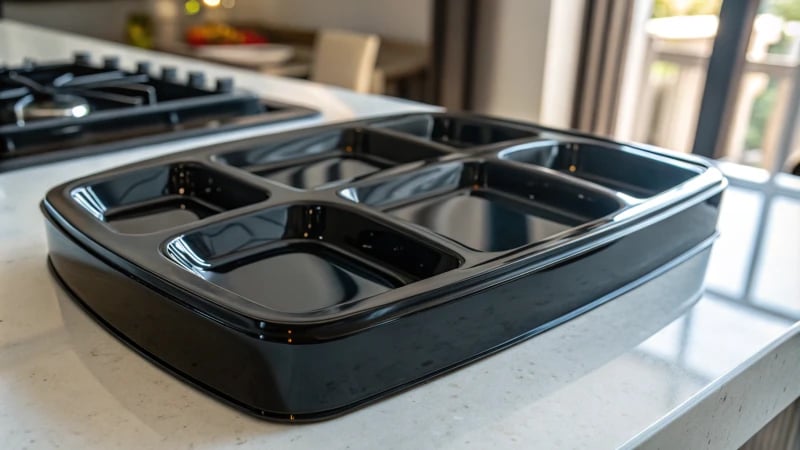
Understanding Side Gating in Mold Design
Let me show you a craft that combines art and science. The first time I saw side gating in action, it amazed me. It felt like watching an artist at work. The gate was carefully placed on the side of the product, avoiding those center marks that can ruin beauty. Side gating lets me focus on the looks of products, especially for products where every detail truly matters.
Advantages of Side Gating
-
Flexible Placement: Side gating offers a lot of flexibility. The side gate can be placed to suit different product designs. Imagine working on electronic casings5 or plastic pipes6. A smooth front is very important, and side gating achieves that.
-
Enhanced Flow Control: With side gating, the melt flows gently into the cavity like a smooth stream, reducing defects like fusion marks. A controlled flow is crucial for a smooth, perfect finish.
-
Improved Surface Quality: Surface quality is essential for many projects. Side gating avoids direct impact on key surfaces, maintaining the pristine look needed for high-end electronics or optical product housings7. Remember, surface quality can really matter.
Challenges and Considerations
Side gating is not always easy; it leaves a mark on the side. However, these marks are usually less noticeable and can be reduced with extra work like polishing or grinding. Balancing looks with function can be hard in products with high appearance demands. Precise mold design is important to avoid gate marks or melt flow issues.
Gate Type | Advantages | Disadvantages |
---|---|---|
Direct Sprue | Suitable for large, symmetrical products | Visible central marks, potential for residual stress |
Spot Gates | Small surface traces, good for thin-walled products | High shear rate may lead to defects |
Submerged Gates | Hidden gate marks, ideal for high-quality appearances | Complex design requirements, potential for clogging |
For high-demand appearance products, further optimization might be necessary to balance aesthetics and functional requirements effectively by reducing gate size. Ensuring precise mold design is crucial to mitigate potential issues like gate marks or melt flow8 challenges.
Real-World Applications
In real-world use, side gating is a secret weapon for industries focused on great looks. I have seen it transform cosmetic containers and smartphone cases9, making these items not only functional but also visually stunning. Side gating allows for complex designs without losing visual appeal.
Side gating helps me create products that meet and often exceed expectations by offering a polished edge that’s hard to surpass. The results are both beautiful and functional.
Side gating reduces visible gate marks on products.True
Side gating positions the gate on the side, minimizing central marks.
Direct sprue methods enhance product surface quality.False
Direct sprue often leaves unsightly marks, reducing surface quality.
When Should You Use Spot Gates for Injection Molding?
Spot gates bring a big change when accuracy and looks are important. Wondering when they really stand out? Let’s explore!
Spot gates shine in crafting small, detailed items where looks matter. They leave very few marks. This is perfect for precise products like toys and phone buttons. Appearance is key.
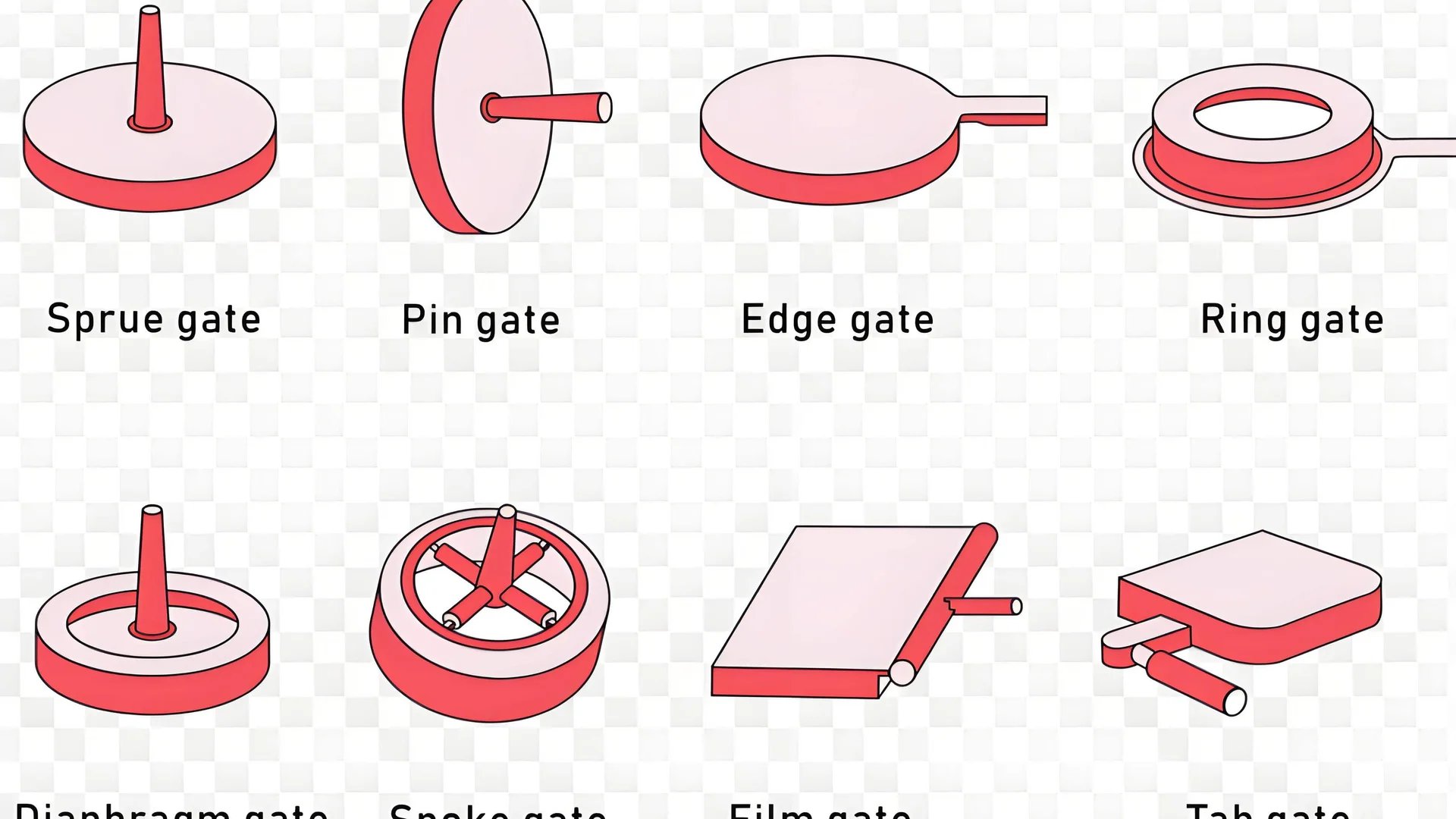
Understanding the Benefits of Spot Gates
I recall my first project with spot gates – creating tiny action figures for a collectible series. The challenge was huge, as these figures needed not only precision but also a perfect finish to attract collectors. Spot gates came to the rescue! Their tiny "dot-like" gate left very few marks on the surface. This kept each figure looking charming.
Spot gates, also known as pin-spot gates, offer unique advantages in injection molding. They are particularly beneficial when producing small, intricately designed products that demand high aesthetic appeal. The small inlet size of spot gates resembles a "dot," which significantly minimizes visible marks on the product surface.
This makes spot gates an excellent choice for molding items like precision plastic toys10 and cell phone buttons11. These products not only require a clean finish but also maintain structural integrity. By allowing the melt to enter the cavity at higher speeds and pressures, spot gates ensure efficient filling of thin-walled and complex shapes.
Advantages | Applications |
---|---|
Minimal surface traces | Precision plastic toys |
High-speed cavity entry | Cell phone buttons |
Considering the Challenges
However, there are challenges to face. Spot gates cause high shear rates, which may damage heat-sensitive plastics. I learned this the hard way during a project with delicate material. It resulted in ugly black spots on our prototype.
While spot gates offer notable benefits, they also present challenges that must be addressed. Due to their small size, the melt experiences a high shear rate, which can lead to decomposition in heat-sensitive plastics. This might result in defects like black spots that mar the product’s appearance.
Additionally, during demolding, there is a risk of the plastic being pulled at the gate, leading to uneven traces. Designing an effective demolding method is crucial to avoid such issues.
Demolding requires careful thought. Using the wrong technique may lead to uneven traces, pulling the plastic and ruining the smooth finish. Designing a good demolding method was key to overcoming these obstacles.
When to Choose Spot Gates
From my experience, spot gates are best when appearance is very important along with structural strength. They’re ideal for parts in consumer electronics, combining beauty and function perfectly.
Opt for spot gates when the product’s appearance is paramount and structural demands are stringent. For example, if manufacturing components for consumer electronics12, where aesthetics and functionality are equally important, spot gates can provide the desired balance.
For larger or thicker products where looks matter less, try alternatives like direct sprue13. These are great for products focusing on mechanical strength over appearance, such as strong plastic drums.
Ultimately, choosing the right gate is like selecting the right tool for a task; it should always match your product’s design needs and materials involved in the injection molding process14.
Spot gates minimize visible marks on molded products.True
Spot gates' small inlet size reduces surface traces, enhancing aesthetics.
Spot gates are ideal for large, thick products.False
Spot gates suit small, intricate designs; direct sprues fit large items.
Why Are Submerged Gates Preferred for High-Quality Finishes?
Have you ever thought about why some products appear perfect with no effort? Submerged gates could be the secret.
Submerged gates in injection molding smartly conceal gate marks by placing them below the surface. This feature suits products where appearance is very important. Their complex design raises the aesthetic quality. These gates provide a polished finish.
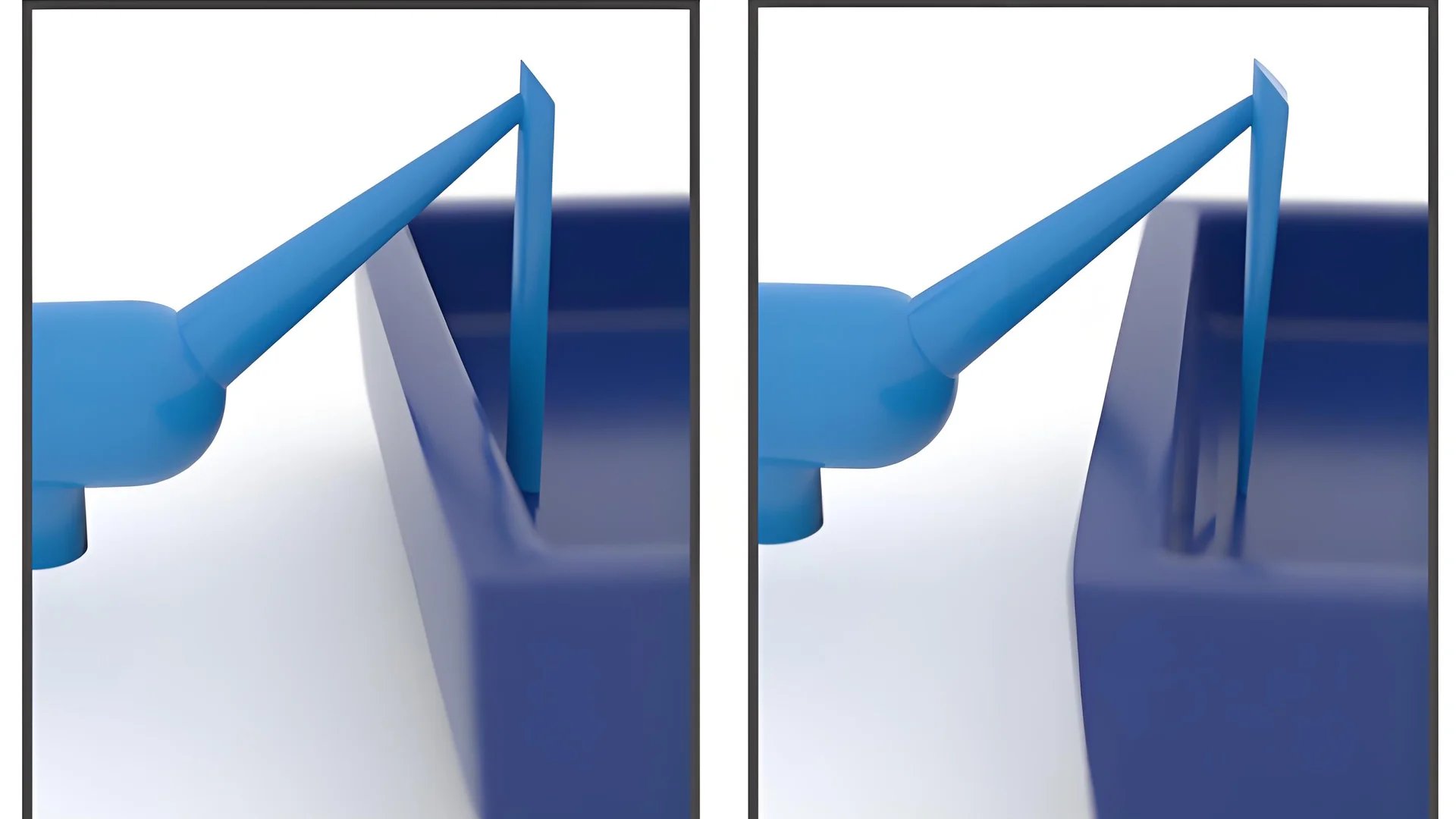
Understanding Submerged Gates
I remember discovering submerged gates during my early days in mold design. It felt like finding a hidden treasure in injection molding. These gates hide the entry points inside the mold, ensuring the product’s visible surface remains untouched by gate marks. This attribute makes them particularly suitable for high-end applications like cosmetic packaging15, where every detail is important.
Advantages of Submerged Gates
- Hidden Gate Marks: By placing the gate on the side or bottom of a product, submerged gates leave no visible trace, maintaining the product’s aesthetic integrity.
- Improved Aesthetics: These gates allow the melt to flow from a concealed position, enhancing the visual appeal of products such as luxury cosmetic caps16.
Feature | Benefit |
---|---|
Hidden Placement | No visible gate marks |
Complex Design | Allows intricate molding |
I still remember working on a high-end cosmetic line. The client wanted everything to be perfect with no exceptions. We picked submerged gates because they left no marks. It was exactly what we needed.
Challenges in Using Submerged Gates
Worthwhile things often require effort. Despite their benefits, submerged gates need exact mold design to avoid problems like gate clogging. Poor planning might lead to less material and flaws in looks.
- Complexity in Design: Crafting these gates necessitates meticulous attention to detail to ensure smooth melt flow and prevent defects such as short shots.
- Potential for Clogging: If not designed properly, these gates can clog, affecting both appearance and product quality17.
Comparing with Other Gate Types
Submerged gates are my choice for a clean finish; meanwhile, other gate types also have their unique benefits:
- Direct Sprue (Center Sprue): Provides strong gates but leaves noticeable marks. I remember using them on large plastic drums where strength mattered more than looks.
- Side Gating: Offers flexible placement but may require post-processing; I’ve seen it work well for plastic pipes where controlling melt flow is crucial.
- Spot Gates (Pin-Spot Gates): Ideal for small parts but can lead to plastic decomposition if not managed with care.
- Scalloped Gates: Ensure even filling but may extend cycle time.
Understanding these differences helps in choosing the right gate type for each application, balancing between aesthetic needs18 and functional requirements. Through careful consideration and design, submerged gates have consistently set a high standard in quality manufacturing.
Submerged gates eliminate visible gate marks.True
Submerged gates are designed to hide entry points, preventing visible marks.
Direct sprue gates improve product aesthetics.False
Direct sprue gates leave visible marks, which can affect aesthetics.
How Do Scalloped Gates Improve Surface Uniformity?
Picture shaping a smooth, shiny instrument panel with an excellent finish. There are no flow marks visible. Scalloped gates probably create this magic!
Scalloped gates distribute molten material evenly. They spread it in a fan shape. This method reduces flow marks. It very much improves the surface’s finish quality. Large flat surfaces benefit greatly from this process.
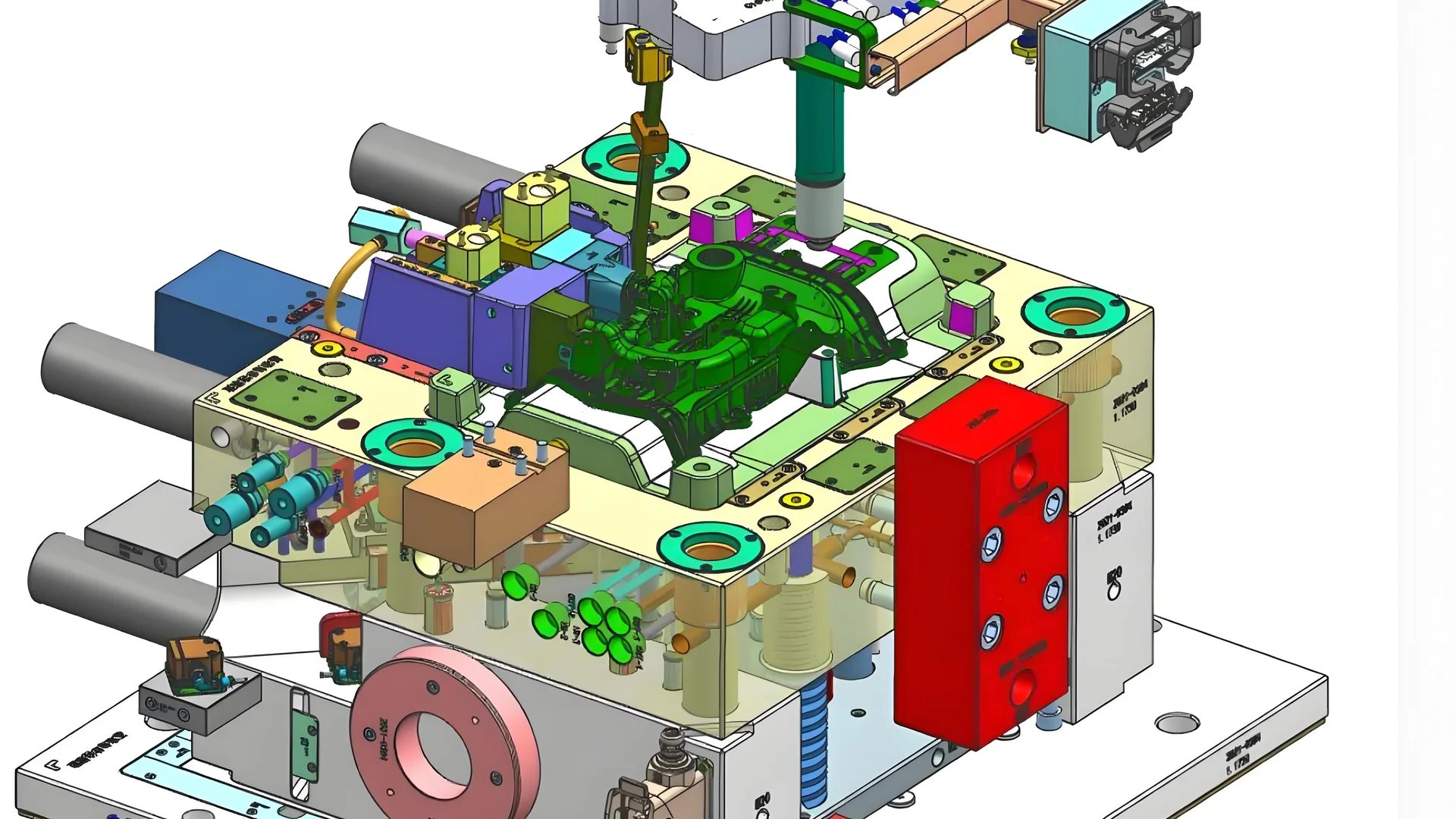
Understanding Scalloped Gates
I remember the first time I saw scalloped gates. It felt like finding a secret ingredient that fixed everything. These fan-shaped wonders spread melted material evenly across a space. They are perfect for products that need to be flat and flawless. Picture it – whether it’s a plastic flat plate or an instrument panel, scalloped gates help achieve that smooth, glossy finish we all want.
Advantages of Scalloped Gates
- Even Material Distribution: Watching the material spread perfectly felt like a small victory each time. It greatly reduces ugly flow marks19.
- Improved Aesthetic Quality: Seeing that final glossy finish is amazing – like shining a gem until it sparkles. It’s truly rewarding.
Advantage | Description |
---|---|
Even Distribution | Reduces flow marks by spreading material evenly. |
Enhanced Appearance | Offers a smooth, glossy finish for better aesthetic appeal. |
Challenges and Considerations
Every good thing has its challenges. I’ve faced some issues with scalloped gates too:
- Wide Gate Traces: The traces they leave can be annoying, like a shadow that needs clever mold design to hide them.
- Solidification Time: Patience becomes important because the large size can slow down production if not handled well.
Suitable mold design is essential to cover gate traces20 effectively.
Comparisons with Other Gating Techniques
Choosing the right gate is important, like picking the correct tool for a job.
- Direct Sprue (Center Sprue): Offers strength but leaves marks that aren’t always nice. It’s ideal for large plastic drums.
- Side Gating: Provides flexibility but may need more polishing for a top-quality look.
- Spot Gates: Excellent for high-speed, high-pressure tasks but might pull off during demolding.
Opting for scalloped gates involves balancing a perfect surface finish with efficient cycle times. If you love the look of high-quality flat products like I do, scalloped gates are probably the best choice.
Scalloped gates reduce flow marks on surfaces.True
Scalloped gates distribute material evenly, minimizing flow marks.
Solidification time is shorter with scalloped gates.False
Scalloped gates have longer solidification times due to their size.
How can I optimize gate design for better product appearance?
Do you ever look at a faulty item and ask yourself what happened?
I select gate types like spot or submerged gates to improve how the product looks. Product geometry and material properties influence this choice. Correct gate positioning reduces visible marks. This action improves aesthetics.
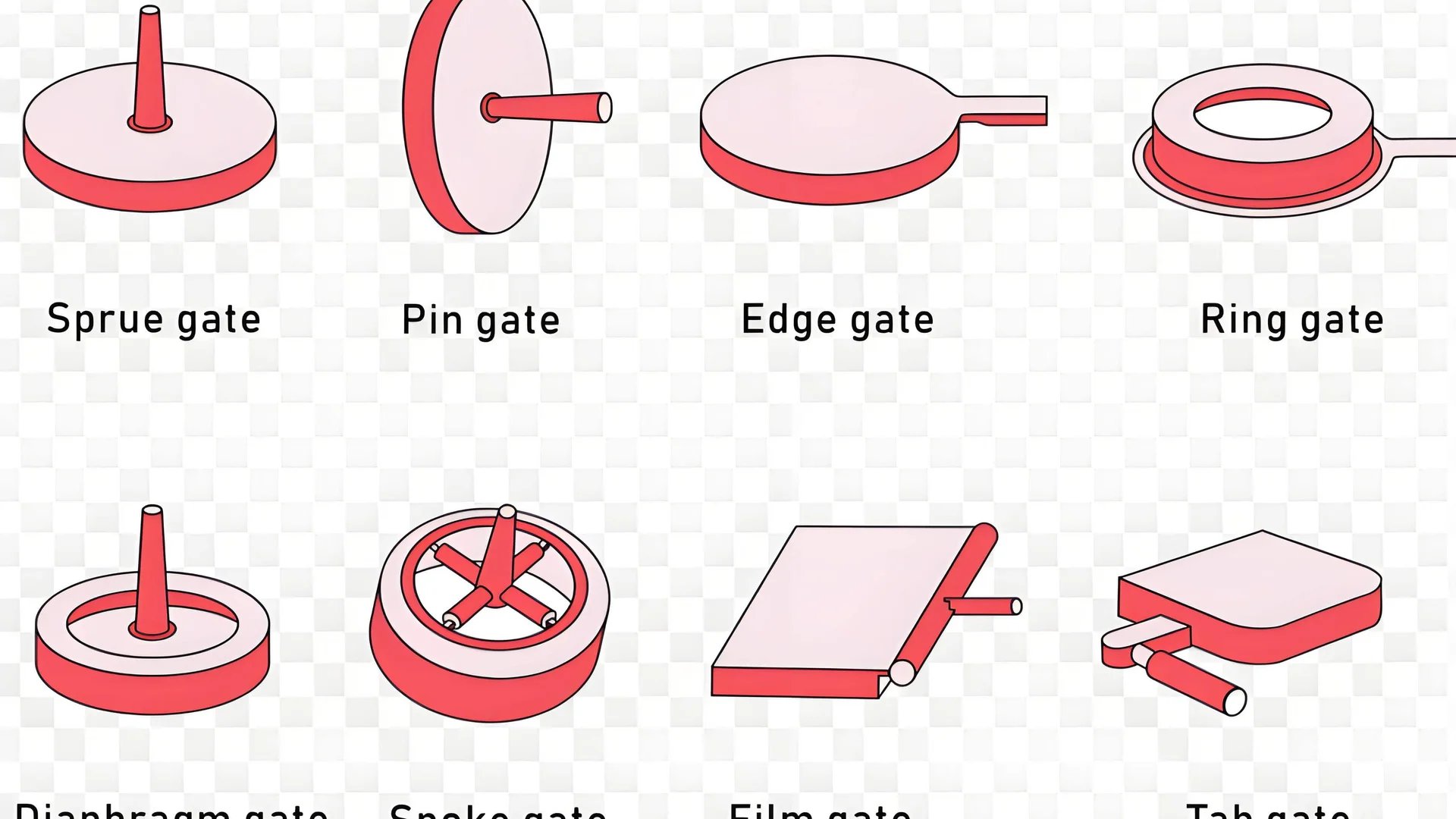
Understanding Different Gate Types and Their Impact
Optimizing gate design relies on understanding various gate types. Each type offers pros and cons that affect the final product. For instance, direct sprue gates suit large, symmetrical items well because they provide direct pressure. Unfortunately, they sometimes leave visible marks.
Direct Sprue
Advantages | Disadvantages |
---|---|
Provides direct pressure for large, thick-walled products. | Leaves visible sprue marks, causing potential deformation and fusion marks. |
On the other hand, side gating offers flexibility but also leaves marks.
Side Gating
- Advantages: Allows flexible placement, controls melt flow, reduces fusion marks.
- Disadvantages: Leaves side marks; needs more processing to remove them from products with high appearance demands.
Spot Gates: Precision Choice
Spot gates work best for items needing top quality in appearance. They are small and tidy, ideal for precision items like plastic toys21. Once used, gate marks were almost invisible—a significant improvement.
Spot Gates
Advantages | Disadvantages |
---|---|
Small traces; high-speed filling beneficial for thin-walled products. | Risk of plastic decomposition due to high shear rates affecting appearance. |
Unseen Options: Submerged Gates
Submerged gates are essential when appearance is crucial as they hide the entry point—very useful for luxury cosmetic packaging.
Submerged Gates
- Advantages: Perfect for smooth surfaces on elite products requiring flawless finishes.
- Disadvantages: Complicated design requires care to prevent flow issues.
Improving Look with Scalloped Gates
Scalloped gates excel in wide cavities but demand precise mold design. In one project for instrument panel shells, they helped achieve a shiny finish.
Scalloped Gates
- Advantages: Uniform filling across wide spaces minimizes surface flaws.
- Disadvantages: Takes longer to solidify, slowing production cycles.
Choosing the correct gate type goes beyond technical elements. It involves balancing gate features with product needs for excellent results in injection molding22.
Direct sprue gates are ideal for small precision products.False
Direct sprue gates are better suited for large, thick-walled products.
Submerged gates improve appearance by hiding entry marks.True
Submerged gates conceal the entry point, minimizing visible marks.
Conclusion
Different injection molding gate types, including direct sprue, side gating, spot gates, submerged gates, and scalloped gates, significantly influence product appearance by affecting surface finish and visible marks.
-
Understand why direct sprue is beneficial for large, robust products. ↩
-
Explore how direct sprue differs from side gating in terms of application and appearance. ↩
-
Learn why submerged gates might be preferred for products needing high aesthetic quality. ↩
-
Discover how spot gates excel in maintaining product appearance compared to direct sprue. ↩
-
Learn how side gating optimizes the molding process for plastic pipes by enhancing their surface quality and structural integrity. ↩
-
Discover why direct sprue methods may not be ideal for products with high aesthetic demands due to their tendency to leave visible marks. ↩
-
Explore how side gating helps maintain the visual integrity of high-end optical products by minimizing visible defects. ↩
-
Understand the impact of melt flow issues on product surface quality and how proper design can mitigate these effects. ↩
-
Find out how smartphone manufacturers use side gating to ensure a sleek and appealing finish on their products. ↩
-
Explore why spot gates are preferred for precision plastic toys due to their minimal surface marks and structural integrity. ↩
-
Discover how spot gates contribute to the aesthetic and functional requirements in cell phone button production. ↩
-
Learn about the role of spot gates in balancing appearance and functionality in consumer electronics. ↩
-
Understand scenarios where direct sprue is advantageous over spot gates for large products. ↩
-
Gain insights into how spot gates fit into the broader injection molding process. ↩
-
Explore how submerged gates enhance the appearance of cosmetic packaging by minimizing visible imperfections. ↩
-
Discover why submerged gates are favored for luxury cosmetic products, ensuring impeccable finishes. ↩
-
Understand potential issues with submerged gate design and their impact on maintaining high product standards. ↩
-
Learn strategies to achieve both aesthetic excellence and functionality in injection molding. ↩
-
Discover methods to minimize flow marks using scalloped gate designs. ↩
-
Explore techniques for concealing gate traces in mold design. ↩
-
Explore how spot gates enhance product aesthetics by reducing visible traces, beneficial for high-quality appearances. ↩
-
Discover comprehensive details about various gate types and their specific applications in injection molding processes. ↩