Precision injection molding is a critical player in advanced manufacturing, yet it presents unique challenges that can feel daunting.
The main challenges in precision injection molding include material selection and processing, mold design and manufacturing, precise control of injection molding parameters, ensuring dimensional accuracy, and maintaining product appearance quality.
Let’s dive deeper into these challenges and discover effective strategies that can help manufacturers navigate this complex landscape.
Material drying prevents defects in precision molding.True
Proper drying of materials like nylon prevents bubbles and hydrolysis.
How Does Material Selection Impact Precision Injection Molding?
In precision injection molding, the choice of material is crucial for ensuring product quality and dimensional accuracy.
Material selection in precision injection molding affects mechanical strength, dimensional stability, and creep resistance. Materials like engineering plastics require careful control over properties such as fluidity and shrinkage to maintain process stability and final product precision. Proper material drying is also essential to prevent defects like bubbles and hydrolysis.
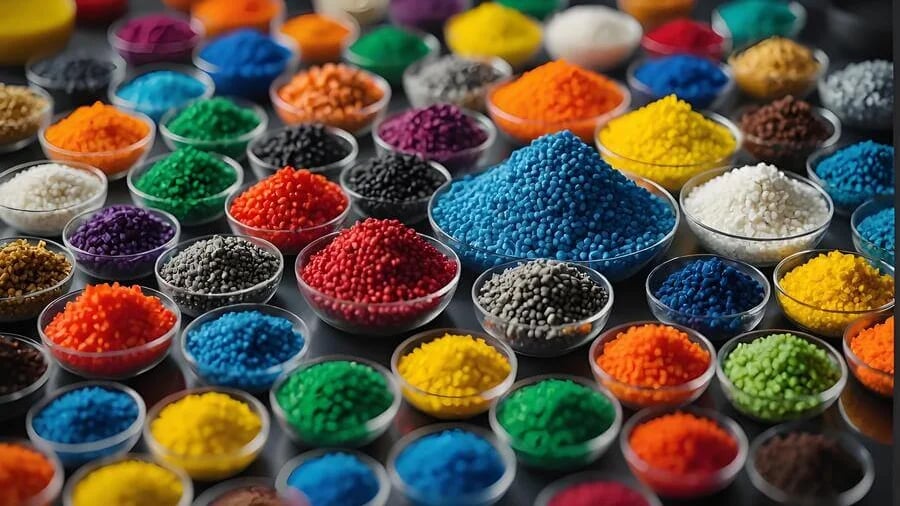
Material Performance Control
Precision injection molding demands materials with high mechanical strength and dimensional stability. Engineering plastics, for instance, can exhibit varying performances under different environmental conditions, such as changes in temperature and humidity. This variability can significantly impact the final product’s accuracy.
For example, nylon is known for its hygroscopic nature, which means it can absorb moisture from the environment. If not dried properly before the molding process, it can lead to hydrolysis or the formation of bubbles, severely affecting product integrity.
Material Characteristics | Effect on Molding |
---|---|
Fluidity | Influences fill consistency |
Shrinkage | Affects dimensional accuracy |
Mechanical Strength | Impacts durability |
Importance of Material Drying
Some plastics absorb moisture, and without adequate drying, this moisture can cause significant issues during molding. For instance, during the injection of hygroscopic materials like polyamides, any retained moisture can lead to defects that compromise the precision of the molded part.
Therefore, understanding the drying temperature and duration for each material is essential. High-precision processes often incorporate advanced drying systems to maintain optimal moisture levels.
Material Selection for Dimensional Accuracy
Selecting the right material not only involves considering its mechanical properties but also how it interacts with the mold and processing conditions. Factors such as shrinkage rates must be precisely calculated to ensure that the final product meets stringent accuracy requirements. Engineers often utilize computer simulations to predict these behaviors in advance.
By focusing on these aspects, manufacturers can mitigate issues related to dimensional inaccuracies and enhance the overall quality of their products. For more insights into material performance control1, explore industry case studies that highlight successful implementations.
Nylon must be dried before molding to prevent defects.True
Nylon absorbs moisture, causing defects like bubbles if not dried.
Material shrinkage is irrelevant in injection molding.False
Shrinkage affects dimensional accuracy, crucial for precision molding.
What Role Does Mold Design Play in Injection Molding Accuracy?
Mold design is pivotal in ensuring the precision and quality of injection molded products, directly affecting dimensional accuracy and product consistency.
Mold design significantly influences injection molding accuracy by determining the precision of the mold cavity, the rationality of mold structure, and the durability against wear. High-precision mold processing and optimal design ensure consistent product quality and dimensional stability.
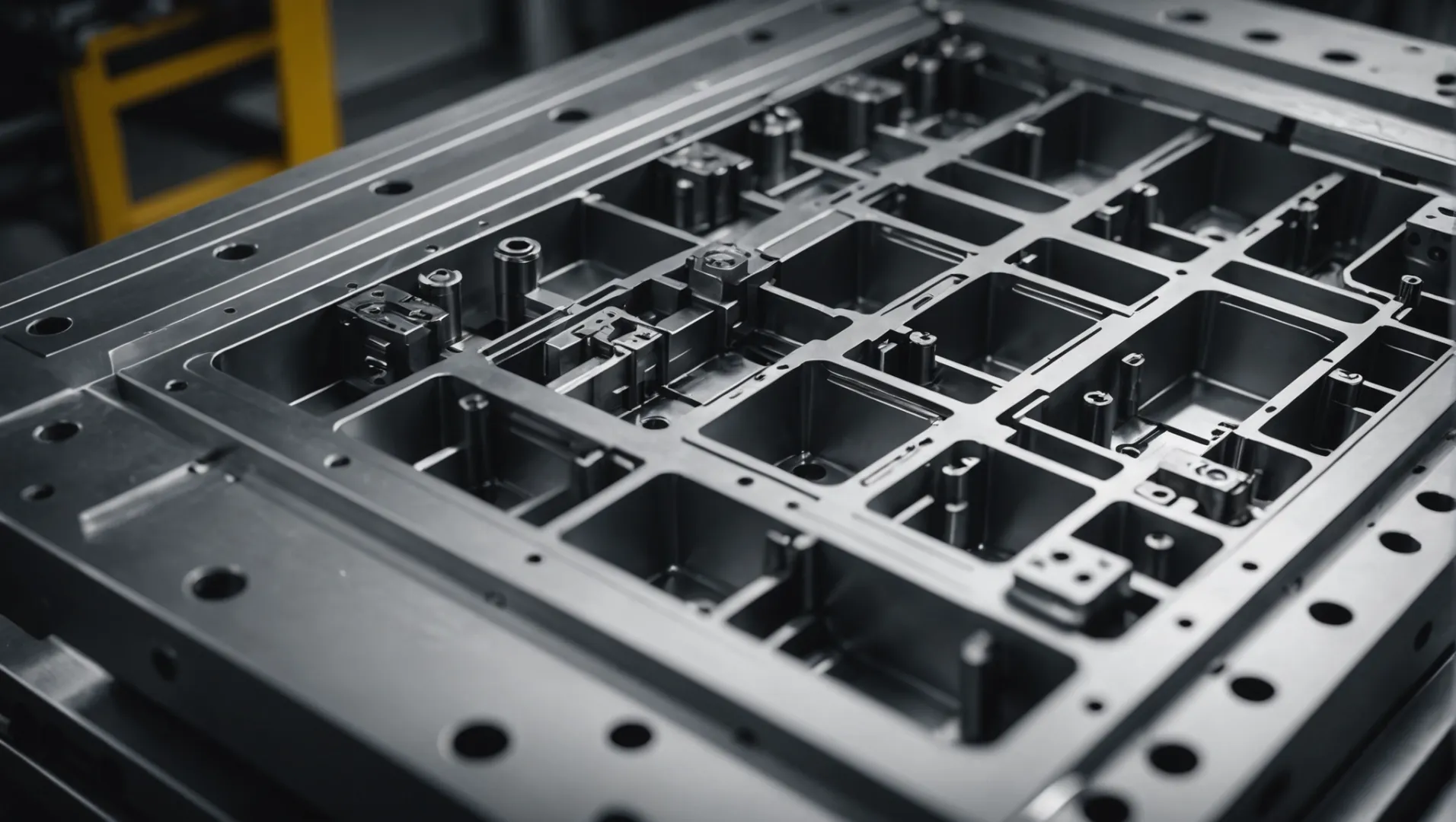
The Influence of Mold Cavity Precision
The dimensional accuracy of a mold cavity is crucial for producing precise injection molded parts. The cavity’s dimensions, surface finish, and parting line accuracy must meet stringent standards. Ideally, the dimensional tolerance of the mold should be controlled to less than one-third of the product’s tolerance to ensure high precision. This requires advanced techniques like CNC machining and EDM (Electrical Discharge Machining) to achieve necessary precision.
For instance, when manufacturing components for the aerospace industry, even minute deviations can lead to significant performance issues. Thus, employing high-precision equipment is not just beneficial but necessary. Learn more about CNC machining techniques2.
Importance of Mold Structure Rationality
The structural design of a mold must incorporate a well-thought-out cavity layout, efficient gate design, and an effective cooling system. An improperly designed cavity layout can lead to uneven product shrinkage, affecting dimensional accuracy. For example, in automotive parts where uniformity is critical, any imbalance can result in part rejection.
Similarly, an inappropriate gate design might cause defects such as weld marks or cavitation, negatively impacting both appearance and function. The cooling system’s design is also vital as it controls mold temperature and thus directly influences the product’s dimensional stability.
Combatting Mold Wear
During injection molding, molds are subjected to high pressure and friction, leading to wear over time. This wear can alter cavity dimensions, compromising product accuracy. To mitigate this, selecting mold materials with excellent wear resistance is crucial. Techniques like quenching or hard chrome plating can enhance durability.
For example, in the electronics industry where part precision is paramount, using high-quality materials and proper surface treatments ensures molds maintain their integrity over longer production runs. Explore options for mold material treatments3.
Advanced Mold Processing Techniques
Employing state-of-the-art processing technologies is essential for creating molds that meet precision requirements. Techniques such as wire cutting and laser sintering can significantly improve mold precision and longevity. Each method has its advantages depending on the specific requirements of the part being produced.
For example, laser sintering allows for complex geometries without additional machining, beneficial for intricate medical device components. Discover more about advanced mold processing technologies4.
Mold design affects injection molding accuracy.True
Mold design directly impacts the precision and quality of molded products.
Improper gate design causes uniform shrinkage.False
Improper gate design can lead to uneven shrinkage, not uniform.
Why Is Process Parameter Control Crucial in Injection Molding?
In the world of injection molding, controlling process parameters is key to achieving high-quality, precise products.
Controlling process parameters in injection molding is essential for ensuring product precision and quality. Key parameters like injection pressure, speed, holding time, and mold temperature must be meticulously managed to minimize defects, enhance dimensional accuracy, and maintain consistency in production.
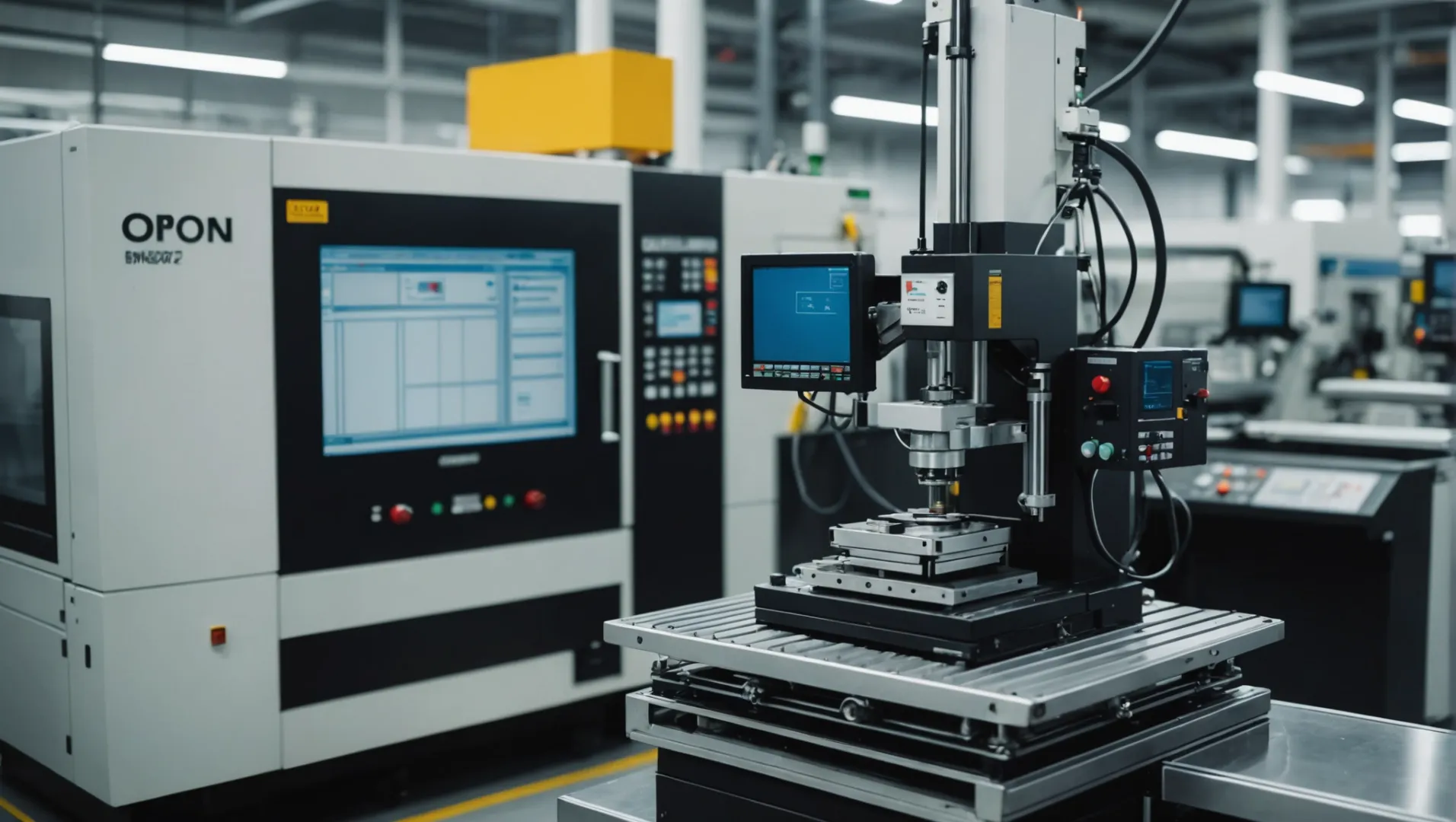
The Role of Injection Pressure
Injection pressure is pivotal in ensuring that the plastic melt fills the mold cavity completely. A higher pressure can improve part density and reduce shrinkage but may also cause excessive stress or damage to the mold. For instance, achieving the right balance in pressure control can prevent defects such as flash or part warping.
Importance of Injection Speed
Injection speed affects the flow of plastic melt within the cavity. Too fast a speed might lead to defects like weld lines or cavitation, while a slower speed can cause incomplete fills or uneven part sizes. Fine-tuning this parameter ensures uniform flow and minimizes surface defects. Adjusting the speed requires understanding the material’s viscosity and the part’s geometry.
Balancing Holding Time and Pressure
Holding pressure compensates for material shrinkage during cooling, directly impacting the final part’s precision. This parameter must be adjusted based on part size and material properties. The holding time ensures that the parts are adequately formed before ejection. For example, increasing holding pressure can reduce voids and sink marks, improving part integrity.
Controlling Mold Temperature
Mold temperature is critical for maintaining consistent cooling rates and dimensional accuracy. If temperatures fluctuate too much, it may lead to increased shrinkage or poor melt flow. Precision control within ±1℃ helps maintain uniformity in parts. Proper cooling system design is crucial in managing temperature effectively.
Impact of Molding Cycle
The molding cycle time affects production efficiency and part quality. A cycle that’s too short may result in incomplete fills or deformations, while a prolonged cycle can increase costs. Optimizing this parameter involves balancing time with quality requirements.
To master these parameters, manufacturers need to employ high-precision equipment and incorporate dimension measurement systems5 for real-time feedback.
Understanding and optimizing these process parameters not only enhances product quality but also maximizes operational efficiency, making it a cornerstone for success in injection molding.
Injection pressure affects part density.True
Higher injection pressure increases part density and reduces shrinkage.
Holding time does not impact part precision.False
Holding time ensures parts form correctly, affecting their precision.
How Can Product Appearance Be Optimized in Precision Molding?
In precision molding, optimizing product appearance is pivotal for achieving high-quality standards.
To optimize product appearance in precision molding, focus on mold surface finish, color uniformity, and defect prevention. These factors ensure aesthetic quality and enhance the final product’s appeal.
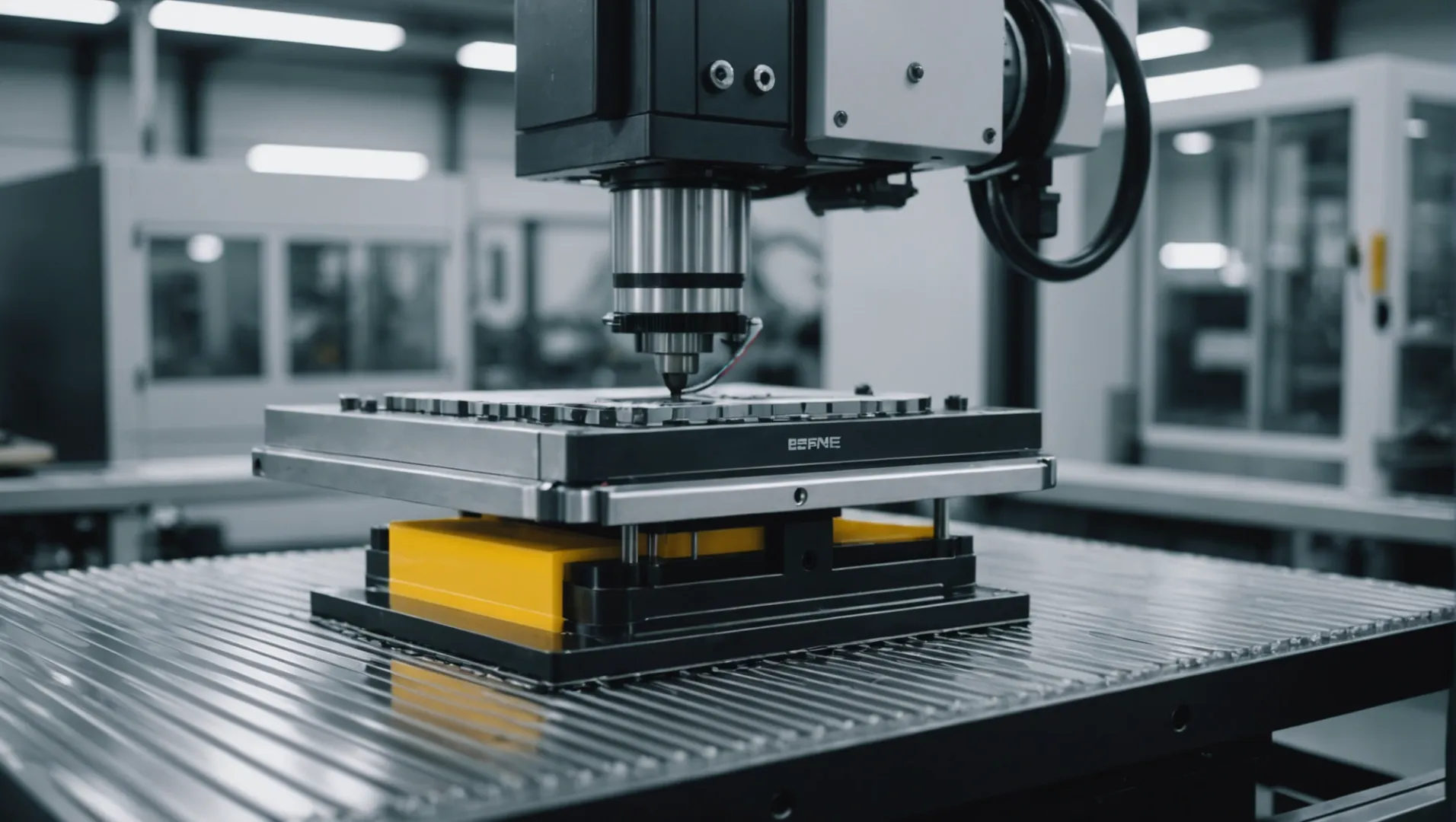
Enhancing Surface Finish
The surface finish of a molded product is directly influenced by the mold’s surface condition. Achieving a high-quality finish involves meticulous attention to detail during mold manufacturing and maintenance. The mold should be polished to a mirror-like surface to minimize imperfections and ensure that the final product has a smooth appearance. Additionally, maintaining this finish through regular cleaning and inspection helps avoid surface degradation over time.
Ensuring Color Uniformity
Color consistency is critical in products where aesthetics are a priority. Achieving uniform color distribution across the molded part requires careful control of several factors:
- Material Mixing: The initial blending of pigments must be thorough to avoid color discrepancies.
- Temperature Control: Maintaining consistent temperatures during molding prevents color variations caused by uneven heating.
- Cycle Time Regulation: Precise control of the molding cycle ensures that each batch receives the same processing time, contributing to consistent color output.
For further insights, you might explore more about color uniformity challenges6 faced in plastic molding industries.
Preventing Surface Defects
Surface defects such as weld lines, flow marks, and cavitation can severely affect the product’s appearance. To mitigate these issues:
- Gate Design Optimization: Proper gate placement minimizes the risk of weld lines and flow marks.
- Cooling System Efficiency: An effective cooling system ensures that temperature variations do not cause surface imperfections.
- Injection Speed Adjustment: Controlling the speed of injection can help avoid defects by allowing the molten plastic to flow smoothly into the mold without causing disturbances.
To delve deeper into defect prevention strategies7, reviewing industry best practices can provide valuable guidance.
Optimizing these aspects of precision molding not only enhances the aesthetic appeal of the final product but also increases its market competitiveness.
Mold surface finish affects product appearance.True
A high-quality mold surface ensures a smooth final product appearance.
Color uniformity is irrelevant in precision molding.False
Consistent color is crucial for aesthetic quality in precision molding.
Conclusion
By mastering these challenges, manufacturers can significantly boost product quality and efficiency, paving the way for success.
-
Provides detailed examples of controlling material performance for precision.: Injection molding process monitoring and process control can help you achieve several goals: improved process quality, higher-quality products and lower … ↩
-
Discover CNC machining methods to enhance mold precision.: This usually requires careful selection of tooling, careful creation of toolpaths, and very rigid work holding. You usually still need to follow … ↩
-
Learn about treatments that extend mold life and accuracy.: In this work, two different coatings were tested in order to increase the wear resistance of the surface of a mold used for glass fiber reinforced plastics. ↩
-
Explore cutting-edge technologies enhancing mold production.: Direct Metal Laser Sintering (DMLS) is a new technology in plastic injection molding that utilizes metal 3D printing to create molds. This … ↩
-
Discover tools for precise dimensional control during injection molding.: This measurement should be done in real time and close to the part’s production time to evaluate the quality of the produced parts for future … ↩
-
Discover common challenges and solutions for maintaining color uniformity in molding.: Color Consistency Challenges During Injection Molding Process … The volume of parts is the most important factor affecting the consistency of molding colors. ↩
-
Learn effective strategies to prevent common surface defects in injection molding.: Establishing quality control measures such as raw material inspection and in-process inspection can help to minimize injection molding defects … ↩