Imagine standing in the heart of a bustling factory, where injection molding machines are the unsung heroes.
A 6-cavity mold can perform efficiently with the right clamping force, adequate injection capacity, proper mold mounting, and optimized cycle time, ensuring high-quality output and peak production rates.
I remember the first time I encountered a 6-cavity mold in action—it was like watching a well-oiled machine, literally! The secret behind this efficiency lies in understanding and optimizing key factors. Let’s dive into how these elements work together to keep production smooth and seamless.
6-cavity molds increase production speed.True
Using multi-cavity molds like 6-cavity increases output per cycle, speeding up production.
Injection capacity is irrelevant for 6-cavity molds.False
Adequate injection capacity is crucial to fill all cavities uniformly for quality products.

How does clamping force impact 6-cavity molding?
Ever felt the thrill of watching a mold come to life in an injection molding machine?
In 6-cavity molding, clamping force ensures the mold stays closed during injection, preventing flash. It’s determined using the formula F = p × A, where ‘p’ is injection pressure and ‘A’ is the total projected area.
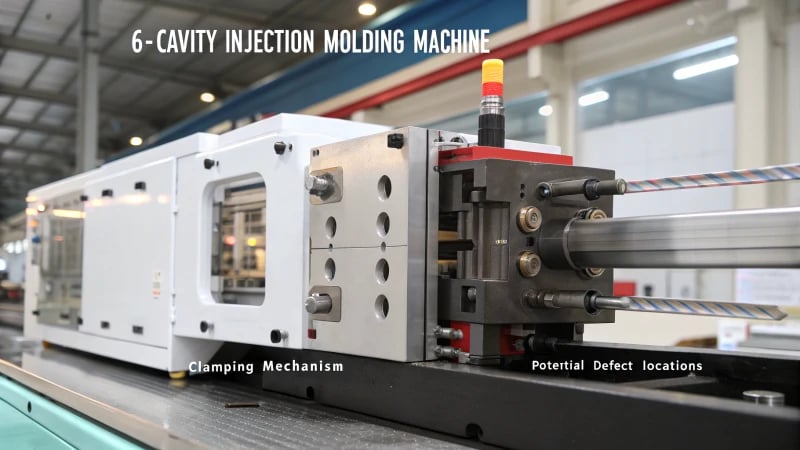
Understanding Clamping Force
I’ve often marveled at how something as seemingly straightforward as clamping force plays such a pivotal role in molding. Imagine you’re working with a 6-cavity mold, and each cavity needs to be just right. The clamping force is what keeps this mold intact under the intense pressure of molten plastic. Without enough force, you’re looking at the nightmare of flash1—unwanted material seeping out, turning your neat designs into messy mishaps.
-
Formula for Clamping Force
Remember the first time you calculated a clamping force? I do. It was like unlocking a secret:
F = p × A
- p: Injection Pressure
- A: Total Projected Area of Cavities
Parameter | Description |
---|---|
Injection Pressure | The force exerted by molten plastic |
Projected Area | Combined area of all cavities in the mold |
Factors Influencing Clamping Force
These days, I’ve learned to consider a few crucial factors when it comes to clamping force:
- Injection Pressure: The higher the pressure, the more clamping force you need. It’s like trying to keep a lid on a pressure cooker without letting any steam escape.
- Projected Area: Bigger molds mean larger areas, demanding more force. Think of it like holding back a tide with your hands.
Practical Implications
Every project has taught me something new about clamping force:
- Flash: I’ve battled this more times than I’d like to admit. Calculating the right force is my armor against this defect.
- Mold Compatibility: Ensuring that the injection machine matches the mold is like ensuring a snug fit between puzzle pieces.
- Cycle Time Adjustment: More cavities can tweak cycle times. It’s about finding that sweet spot where efficiency meets quality.
Diving deep into these principles has been invaluable in refining my design and operation skills in injection molding. By getting the clamping force spot on, not only do I enhance product quality, but I also significantly cut down on waste. Curious about injection capacity2 and how it fits into the bigger picture? There are plenty of resources out there to explore.
Clamping force prevents flash in 6-cavity molds.True
Clamping force keeps the mold closed, preventing material seepage.
Higher injection pressure reduces clamping force needed.False
Higher pressure increases the need for greater clamping force.
How Does Injection Capacity Affect Production Quality?
Ever wondered how something as technical as injection capacity could have such a big impact on production quality? Let’s dive into this fascinating world!
Injection capacity is vital for production quality, as it ensures adequate molten material fills all mold cavities. Insufficient capacity can cause defects like short shots, compromising the product’s integrity.
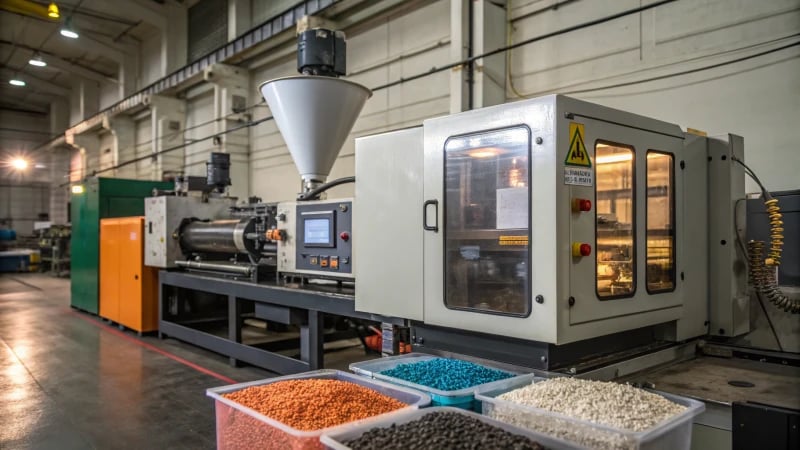
Understanding Injection Capacity
I’ve always been intrigued by how the small details in injection molding can make or break a product. Injection capacity is one of those critical details. It’s all about the volume of molten material that the machine can inject in one go. Imagine trying to fill multiple bottles with water using a small cup—it just doesn’t cut it. The injection unit’s3 ability to handle this efficiently is key to getting things right.
Role of Injection Capacity in Production Quality
I remember working on a project where we underestimated the material volume needed for a multi-cavity mold. It was a real wake-up call when we ended up with incomplete parts. The injection capacity must align with the total volume required for all cavities; otherwise, you end up with short shots.
- Material Volume: This is the biggie. The injection capacity has to meet the total demand for all cavities. Falling short means your mold won’t be completely filled, leading to those dreaded incomplete parts.
- Cycle Time Optimization: With the right injection capacity, you can breeze through cycles faster. It’s like hitting every green light on your commute—production times shrink, and efficiency skyrockets.
- Consistency and Uniformity: There’s nothing like the satisfaction of seeing each part come out exactly like the last. A properly matched injection capacity ensures a steady flow of material, maintaining uniformity across all your products.
Factor | Impact on Production Quality |
---|---|
Material Volume | Short shots, incomplete parts |
Cycle Time | Faster cycles, increased efficiency |
Consistency | Uniformity across products |
Practical Considerations
If you’ve ever tried running a 6-cavity mold4, you’ll know how crucial it is to get your shot volume calculations right. I learned early on that your machine’s injection capacity should slightly exceed what you think you need to allow for any variations.
- Calculation Example: Let’s say each cavity needs 150 cm³—you’re looking at needing over 900 cm³ per shot from your machine.
- Clamping Force Relation: It’s not just about filling cavities; you also need enough clamping force to keep everything closed tight during injection. Use the formula (F = p\times A) for calculations.
Challenges and Solutions
- Melt Uniformity: I’ve faced issues with varying shot sizes affecting melt uniformity more than once. Make sure your machine’s barrel matches your mold design requirements closely.
- Dimensional Accuracy: Keeping dimensional accuracy intact requires consistent injection capacity to provide uniform pressure and material distribution.
Addressing these factors ensures top-notch production quality, minimizes defects, and optimizes your manufacturing processes5. Regularly tweaking machine settings based on what you’re producing is key to getting the best results.
Injection capacity affects cycle time efficiency.True
Adequate injection capacity speeds up cycle times by efficiently filling cavities.
Higher injection capacity always improves product quality.False
Excess capacity may not improve quality and can lead to waste.
Why is Mold Mounting and Compatibility Crucial?
Ever wondered how a single misstep in mold mounting can lead to a domino effect of production headaches?
Mold mounting and compatibility ensure molds fit machines correctly, crucial for efficiency, safety, and quality in injection molding by preventing defects and optimizing performance.

The Basics of Mold Mounting
I remember the first time I watched a mold being mounted onto an injection molding machine. It was like watching a puzzle piece fall perfectly into place. But just like puzzles, if even one tiny piece is off, the whole picture gets skewed. This is why mold mounting is so essential. It’s about securely attaching the mold to the machine’s platens so it stays put during injection. Imagine baking a cake and not securing the oven door—chaos! Incorrect mounting leads to misalignment, causing defects like flash or short shots.
Here’s a simple table outlining key elements:
Aspect | Importance |
---|---|
Alignment | Prevents defects |
Stability | Ensures consistent production |
Compatibility | Matches mold with machine specifications |
Compatibility: The Key to Success
Back in my early days, I learned that compatibility isn’t just a buzzword; it’s the linchpin of success. It ensures that the mold’s dimensions and bolt-hole pattern align perfectly with the machine’s specifications. Picture trying to fit a square peg into a round hole—doesn’t work, right? This harmony is crucial for the ejection system too, ensuring parts pop out smoothly like cookies from a tray.
- Clamping Force: I always remind myself of the basic formula (F = p \times A) to calculate clamping force. It’s like ensuring your seatbelt fits snugly before a rollercoaster ride—essential for keeping everything secure.
- Injection Capacity: Your machine’s injection unit must be able to fill all cavities at once. Think of it like filling multiple cups from one jug; you want all cups filled evenly to avoid short shots or incomplete parts.
Coordinating Mold and Machine Systems
This part brings everything full circle. Imagine a dance where every step syncs flawlessly—that’s what coordinating the mold and machine systems should feel like. The ejection system needs to jive with the machine’s mechanisms to prevent damage during part removal. Just like adjusting your playlist for a longer run, you must tweak cycle time when running multiple cavities, balancing filling, packing, cooling, and ejection for peak productivity.
For more in-depth guidance, consider exploring injection molding best practices6. Aligning these elements optimizes production, enhancing both safety and quality outcomes.
Misalignment causes product defects like flash.True
Correct mold alignment prevents defects such as flash, ensuring quality.
Compatibility affects only the mold's size.False
Compatibility involves size, bolt pattern, and ejection system alignment.
How Does Cycle Time Influence Efficiency?
Have you ever wondered how tweaking just one factor can transform an entire manufacturing process?
Cycle time is crucial for production efficiency, with shorter cycles enhancing throughput, reducing costs, and accelerating delivery, thereby improving overall operational performance.
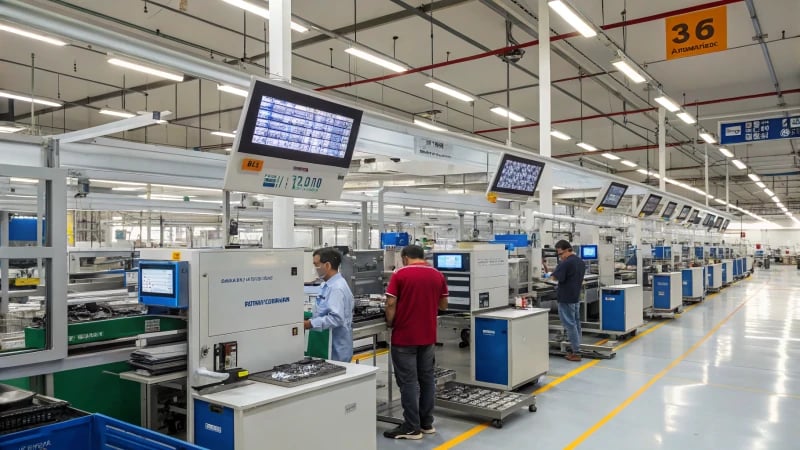
When I first delved into the world of manufacturing, the concept of cycle time was a revelation. Imagine orchestrating a symphony where every note needs to hit just right for a harmonious performance. In manufacturing, cycle time is that rhythm—each second shaved off can lead to a crescendo of benefits.
Cycle Time and Its Components
Cycle time in manufacturing comprises several stages: filling, packing, cooling, and ejection. Each stage affects the total time taken to produce a part. For example, in injection molding, running a 6-cavity mold7 can alter cycle time significantly. The filling stage must be optimized to ensure that all cavities receive enough material simultaneously.
Balancing Clamping Force
I remember working on a project where we used a 6-cavity mold in injection molding. It was an intricate dance of filling, packing, cooling, and ejection stages. Each stage’s duration had a ripple effect on the total cycle time. Optimizing the filling stage was critical, ensuring each cavity received its due share of material simultaneously.
The clamping force required for a mold is calculated using the formula (F = p \times A), where (p) is injection pressure and (A) is the total projected area of the cavities. For efficient production with a 6-cavity mold, getting this right is essential to keep everything tightly sealed and prevent defects like flash.
Factor | Importance in Cycle Time |
---|---|
Clamping Force | Prevents mold opening and defects |
Injection Capacity | Ensures complete filling of all cavities |
Injection Capacity Considerations
Matching the injection capacity to the total volume of the cavities is another puzzle piece. Once, we faced issues because our unit couldn’t provide enough material, leading to short shots. Ensuring the injection unit’s capacity matched the required shot volume became a non-negotiable part of my checklist.
Mold Mounting and Compatibility
Aligning the mold’s size and bolt-hole pattern with machine specifications is crucial—think of it as ensuring your smartphone charger fits perfectly into the socket; any mismatch can halt progress. Additionally, coordinating the ejection system with the machine’s mechanism guarantees that each part exits smoothly post-cycle.
Optimizing Cycle Time
Tinkering with each stage to fine-tune cycle times can significantly enhance efficiency. I recall a breakthrough moment when reducing cooling time without sacrificing part quality substantially boosted throughput.
These adjustments underscore how analyzing each component can illuminate improvement areas setting the stage for enhanced operational performance8.
Incorporating these insights into manufacturing doesn’t just improve efficiency; it also trims costs and elevates product quality, making it vital for competitive success in today’s market.
Clamping force directly affects cycle time efficiency.True
Clamping force prevents mold defects, ensuring efficient cycle completion.
Mismatched injection capacity leads to longer cycle times.True
Insufficient capacity causes incomplete fills, extending the production cycle.
How Do Multi-Cavity Molds Compare to Single-Cavity Molds?
Diving into the world of injection molding feels like opening a box of endless possibilities—each mold offering its unique path to perfection. Let’s unravel the mysteries of single and multi-cavity molds together.
Multi-cavity molds boost efficiency with multiple parts per cycle, ideal for high-volume production but require robust machinery. Single-cavity molds are simpler and cost-effective, suitable for small runs or complex designs.
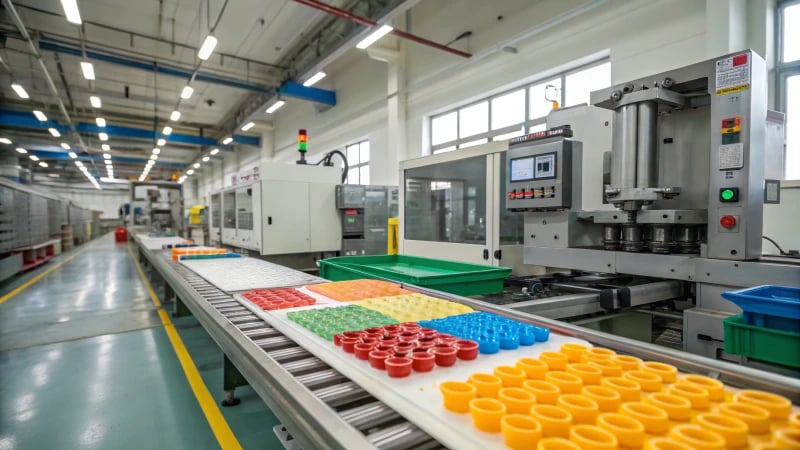
Efficiency and Production Rate
Imagine running a marathon but every step you take counts as two. That’s the magic of multi-cavity molds—they churn out multiple parts in one go. It’s like having a superpower in mass production, especially when you’re racing against the clock. But here’s the catch: your machine needs to be a beast, with enough clamping force and injection capacity to handle the load. I once had to use a 6-cavity mold and found myself knee-deep in calculations, ensuring every detail was precise, from the projected area to the injection pressure. For instance, using a 6-cavity mold9 involves calculating these factors meticulously.
Cost Considerations
Picture this: standing in front of a coffee shop menu, weighing the cost of a fancy latte against a simple brew. That’s how I feel about multi-cavity molds. They lower the cost per part, thanks to higher output. Yet, just like that fancy latte, they come with a higher price tag upfront due to their complexity. On the other hand, single-cavity molds are like that comforting simple brew—they’re easier on the wallet, making them great for smaller jobs or when I’m experimenting with new designs.
Design and Complexity
When it comes to design, it’s like choosing between crafting an intricate origami crane or a straightforward paper plane. Complex designs often call for the precision of a single-cavity mold to avoid defects. I’ve learned through trial and error that for simpler designs where volume is key, multi-cavity molds shine. Analyzing mold complexity became my go-to strategy when deciding which path to take; analyzing mold complexity10 helps in making informed decisions.
Material and Machine Requirements
I remember the first time I had to ensure a machine’s plasticizing capacity was up to snuff for a multi-cavity mold. It was like making sure my car’s engine could handle a cross-country road trip without a hitch. The right shot volume is crucial—it’s all about ensuring everything meshes well between the mold’s ejection system and the machine’s ejection mechanism for smooth sailing. Explore machine compatibility11 for an effective molding process.
Cycle Time Optimization
Optimizing cycle time feels like perfecting a recipe—tweaking filling, packing, cooling, and ejection times until you hit that sweet spot. With multi-cavity molds, it’s all about balancing speed and quality. I’ve spent countless hours fine-tuning these parameters to prevent hiccups in production; learning that every second counts when it comes to maintaining high standards is crucial.
Learn more about optimizing cycle time12 in injection molding processes.
Mold Type | Advantages | Challenges |
---|---|---|
Multi-Cavity | High production rate | Requires robust machine capability |
Single-Cavity | Lower initial cost | Lower output per cycle |
Better for complex part precision | More frequent changeovers |
Embracing these differences has helped me navigate the injection molding landscape more effectively. It’s not just about choosing a mold—it’s about understanding your needs and making informed decisions.
Multi-cavity molds increase production rates.True
They manufacture multiple parts in a single cycle, boosting efficiency.
Single-cavity molds are more cost-effective for large runs.False
They are better for small runs or complex parts due to lower initial costs.
Conclusion
A 6-cavity mold enhances production efficiency in injection molding, requiring optimal clamping force, sufficient injection capacity, proper mold mounting, and adjusted cycle times for quality output.
-
Learn about common causes of flash in molding and prevention techniques. ↩
-
Discover methods to calculate injection capacity for multi-cavity molds. ↩
-
Explores how the injection unit’s design impacts material delivery and quality. ↩
-
Guides on calculating shot volume, crucial for efficient molding processes. ↩
-
Learn strategies to improve efficiency and quality in molding operations. ↩
-
Discover comprehensive best practices to improve efficiency and quality in injection molding processes. ↩
-
Explore specific techniques to optimize cycle time when using a 6-cavity mold. ↩
-
Learn how adjusting cycle times can significantly enhance operational efficiency. ↩
-
Discover how to calculate clamping force and pressure needs for multi-cavity molds. ↩
-
Learn how part complexity influences mold design choice. ↩
-
Ensure your machine is equipped for multi-cavity mold operations. ↩
-
Find techniques to optimize cycle times in injection molding. ↩