Have you ever thought about why some injection molded items don’t last as expected?
Injection molded items often lack strength because of impurities, not drying materials well, wrong injection settings and bad mold designs. These problems cause defects such as cracks or incomplete fillings. This affects how long and how well the product works.
I recall my first experience with a product recall caused by a crack in a molded part. It felt like a nightmare. That experience taught me the value of good material quality. Dust or metal chips sometimes create stress points, which become weak spots. Not managing recycled materials carefully possibly leads to unstable parts.
In the beginning, I underestimated how critical it is to dry certain materials like nylon. Moisture becomes vapor during the molding, forming bubbles that make the product weak. Choosing correct injection parameters is crucial. I learned this importance the hard way. Pressure and temperature need control. Mold design is important too. A wrongly sized gate or poor exhaust often causes failures.
Focusing on these areas really strengthens products. It also saves time and stress. The key lies in understanding how materials, processes and design work together to keep products strong.
Impurities in materials weaken injection molded products.True
Impurities can cause structural defects, reducing product strength.
Proper drying of materials has no impact on product strength.False
Improper drying can lead to weak spots, affecting durability.
What Material Issues Contribute to Weakness in Injection Molded Products?
Ever thought about why some injection molded products just break? Many problems with the materials lead to weak and fragile items.
Problems in injection molded products often come from too many impurities, bad recycled materials and wrong material selections. Poor drying also causes trouble. Fixing these problems really improves product strength and life. Strength and life enhance.
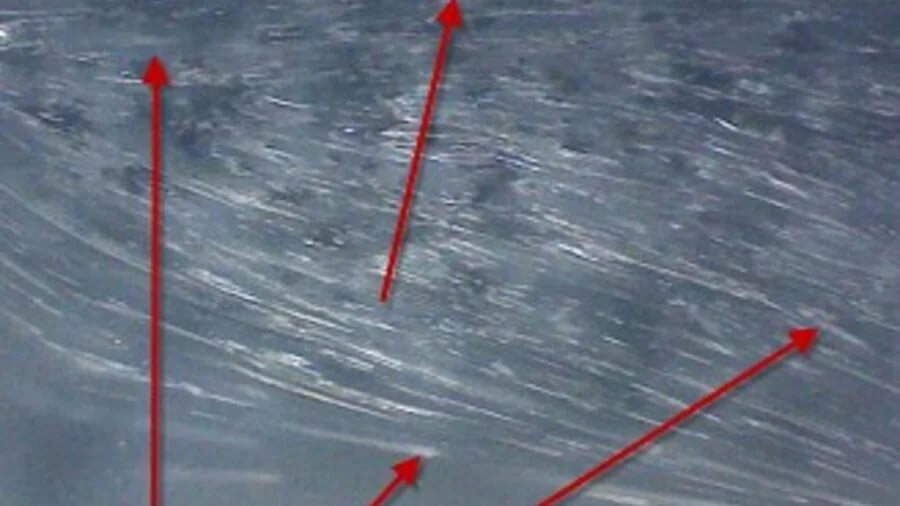
High Impurity Content
I remember a project where everything seemed perfect until the final tests. The product kept breaking easily, which was puzzling. The plastic we used contained many impurities like dust and tiny metal chips. These impurities created weak spots, causing cracks even with small impacts. It’s like a well-made cake hiding little rocks inside! Products prone to cracks1 can result from such impurities.
Recycled Material Quality
Using recycled materials sounds good for saving money and helping the environment. However, relying too much on low-quality recycled materials often causes problems. Repeated processing weakens the molecular chains, making the material unstable. Combining recycled materials with new ones often strikes a better balance. This very important mix usually keeps costs low and maintains product quality. A smart balance works wonders.
Improper Material Selection
I recall a story about using LDPE for a part needing to hold up under high stress. It turned out badly – the part failed dramatically. This mistake taught me that selecting the right material is very important, especially for parts needing strength. Picking the correct material makes a big difference.
Requirement | Recommended Material |
---|---|
High Strength | Polycarbonate (PC) |
Toughness | Acrylonitrile Butadiene Styrene (ABS) |
Stiffness | Polypropylene (PP) |
Using LDPE for automotive parts2 can lead to damage due to its low strength.
Insufficient Material Pretreatment
I once skipped drying a batch of nylon parts that absorbed moisture – a big mistake! Moisture turned into steam during molding, creating bubbles that weakened the product’s strength. Now, I always dry materials properly to stop these costly errors. Good drying is crucial.
Monitoring drying parameters can prevent bubble formation3.
Analyzing Impact on Product Design
Discovering these material issues really changed how I design products. Picking suitable materials and pretreatment methods greatly improves performance, which is very important for consumer electronics where durability really matters.
Evaluating material properties ensures we always meet mechanical strength needs effectively.
For more advice on handling these material challenges, check industry best practices4.
High impurity content leads to product cracks.True
Impurities create stress points, increasing crack susceptibility.
Recycled materials always enhance product strength.False
Low-quality recycled materials can weaken product integrity.
How Does the Injection Molding Process Affect Product Strength?
Do you ever think about how the smallest details in injection molding decide a product’s durability?
Injection molding influences how strong a product becomes. Material choice plays a very important role. Mold design significantly contributes to product integrity. Process parameters significantly affect results. Careful control of these elements results in strong products. Neglecting them may cause problems. Defects like cracks might appear. Weak joints may form.
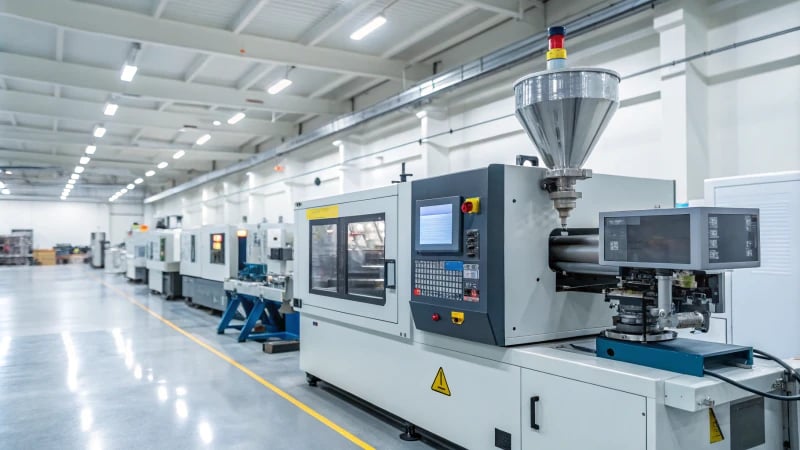
The Role of Material Selection
The material choice5 plays a pivotal role in product strength during injection molding. Imagine this: using a material with many impurities is like trying to build a house on shaky ground. Impurities lead to stress points. I once chose to use recycled materials to be more environmentally friendly, but they were not as stable as I hoped. They had been used many times and their molecular chains were broken, leading to lower strength.
Material Quality Issues
- High impurities harm molecular chain strength.
- Recycled materials often have broken chains, reducing stability.
Material | Issue | Impact on Strength |
---|---|---|
LDPE | Low strength | Easily damaged |
PC | Moisture-induced bubbles | Lower density |
Injection Parameters and Their Impact
Unreasonable injection parameters are detrimental to product strength. Insufficient injection pressure results in incomplete cavity filling, making parts prone to damage. Similarly, improper injection speed can cause surface defects and an uneven internal structure.
Key Parameters
- Injection Pressure: Low pressure means parts are not completely filled.
- Injection Speed: A balance is needed – too fast causes defects, too slow leads to early cooling.
Mold Design Influences
Designing a mold6 felt like solving a tough puzzle. Gate size and position are vital; small or poorly positioned gates can lead to insufficient filling. Additionally, a runner that is too long or thin increases pressure loss, affecting the melt flow.
Mold Feature | Potential Issue | Resulting Problem |
---|---|---|
Gate size | Too small | Poor filling |
Runner | Too long/thin | Pressure loss |
The injection molding process intertwines with every aspect of manufacturing, from material choice to mold design. Understanding these interactions is vital for ensuring product strength and durability in the final output.
Additional Considerations
It’s very important to manage mold temperature control7. Improper temperature affects the molecular structure, impacting strength. High temperatures may break down materials while low temperatures increase thickness, causing issues like poor filling and cold joints.
Temperature Control
- Too High: Longer cooling time, potential material degradation.
- Too Low: Thickness rises, making complete mold filling hard.
Proper management of each stage of the injection molding process ensures that the end product meets the desired mechanical performance requirements. Examining these factors closely can help optimize production and achieve superior product quality.
High impurity content weakens product strength in injection molding.True
Impurities disrupt molecular integrity, leading to weak points.
Low injection speed enhances product strength in molding.False
Low speed may cause premature cooling, leading to defects.
How Does Mold Design Ensure Product Durability?
Have you ever thought about how a product lasts for many years?
Mold design plays a crucial role in product durability. It manages how materials spread and reduces problems like stress points and empty spaces. Key parts are gate design, the runner system and exhaust features. These elements work together to strengthen the structure.
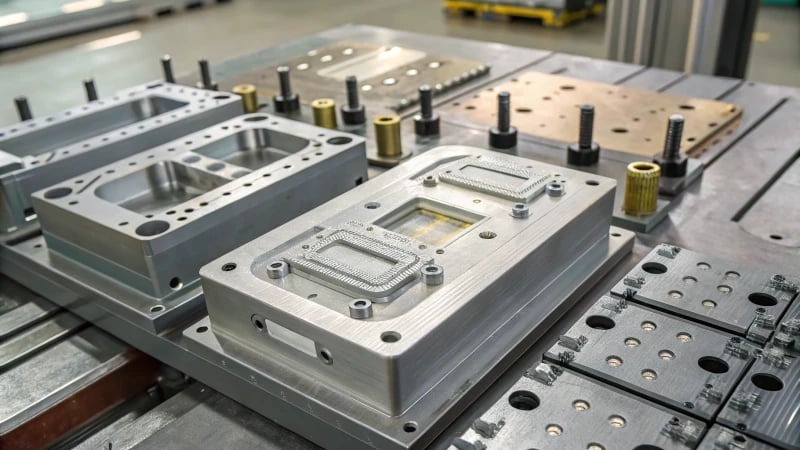
Importance of Gate Design in Mold Durability
I remember when I was a young designer, trying to understand gate design. An experienced mentor once told me that a gate too small restricts material flow, creating weak areas. I understood when I imagined filling a balloon with a straw – very slow and not effective. A well-sized gate, placed correctly, allows material to flow evenly, strengthening the product like a strong seam in fabric.
Consider the case of injection molding for automotive parts, where the use of improper gate positions8 can drastically affect durability. A strategically placed and appropriately sized gate ensures uniform material distribution, enhancing structural strength.
Runner System Design: A Path to Strength
At the start of my mold designing journey, I battled with the runner system. It’s like planning roads in a city – make a mistake and traffic (or pressure loss) can cause problems. I discovered that using complex CAD techniques can change a mess into a clear path, allowing the melt to fill every part of the mold cavity. This change was crucial for me in creating strong products.
Using advanced CAD techniques9, designers can create runner systems that minimize pressure loss, ensuring robust product formation.
Table: Runner System Considerations
Parameter | Impact on Durability |
---|---|
Runner Length | Pressure loss |
Runner Thickness | Flow resistance |
Surface Texture | Friction increase |
Exhaust Systems: Breathing Life into Products
One time, I crafted a mold with poor exhaust features. The product had flaws, similar to baking a cake without heating the oven – just not rising as it should. That experience showed me how important vent placement and size are for smooth gas escape. Done correctly, it’s like letting the product breathe, providing solid and dependable results.
Molds with poor exhaust designs10 often produce products with uneven internal composition, adversely affecting durability. Investing in accurate exhaust solutions is now essential in my design process as it guarantees a consistent internal structure and promises long-lasting durability.
Gate size affects product durability in mold design.True
A correctly sized gate ensures even material distribution, enhancing strength.
Runner thickness has no impact on product strength.False
Thicker runners reduce flow resistance, improving cavity filling and strength.
How Can Manufacturers Enhance the Strength of Injection Molded Products?
Curious about how to create stronger injection molded products? Let’s explore materials, designs and processes together to increase toughness.
Manufacturers should use high-quality materials to increase the strength of injection molded products. They should adjust injection settings very carefully and create accurate mold designs. Important steps include drying materials well, changing injection speeds and placing gates strategically.
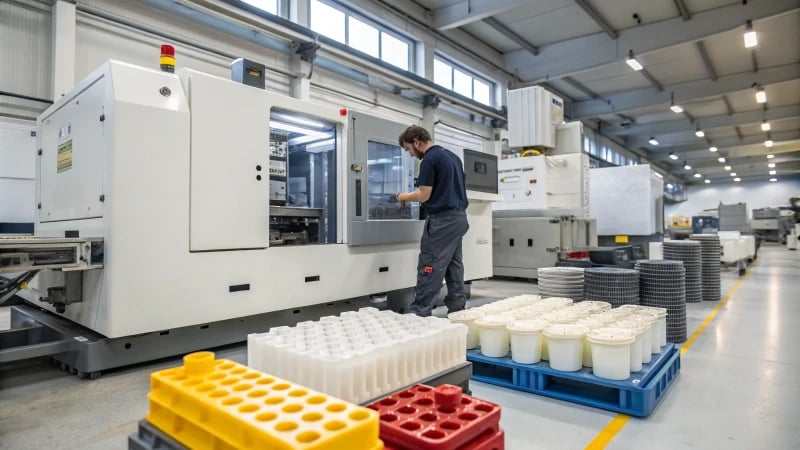
Choosing and Preparing Materials
Selecting the right material matters a lot. Imagine working late and seeing products crack because of not checking for impurities. Dust and metal bits? They cause big problems in the tiny parts of the material. Always choose materials with really low impurity levels.
Material Concerns | Solution |
---|---|
Impurity Content | Use cleaner materials |
Recycled Materials | Limit recycled content |
Finding cheap recycled materials was exciting. But these materials sometimes weaken the product. Balance is key – too much weakens important parts of the material.
Improving the Injection Molding Process
Getting the process correct is important. I spent many hours adjusting injection settings. Not enough pressure? The mold fills only halfway. The melt needs to compact properly for a product that is very strong.
- Injection Speed: This is hard. Too quick means defects; too slow leaves a half-filled mold. Balancing speed is crucial.
- Holding Parameters: I learned that low holding pressure or time creates shrinkage holes, which are a product’s enemy.
Designing Molds
Designing molds feels like shaping clay. Details matter a lot. Gate size and place are crucial. If too small or not in the right spot, cavities won’t fill and strength will be uneven.
Design Flaw | Effect on Strength |
---|---|
Small Gate Size | Insufficient flow |
Improper Gate Position | Uneven strength |
The runner system must not be too long or too thin as it risks losing pressure. A very smooth surface keeps the product strong.
Controlling Environment and Process
Temperature control is vital to prevent issues11. Too hot or cold causes problems with filling. Materials like nylon need correct drying; I once forgot this, and it was like a balloon deflating—bubbles messed up everything, reducing density and strength.
Proper preparation really improves quality.
High impurity content weakens injection molded products.True
Impurities create stress points in plastic, leading to cracks.
Excessive recycled material increases product strength.False
Recycled materials have damaged chains, reducing stability.
Conclusion
Injection molded products often lack strength due to impurities, improper drying, incorrect injection settings, and poor mold designs, leading to defects like cracks and reduced durability.
-
Explore how impurities cause stress points, leading to cracks and weakening products. ↩
-
Discover why LDPE lacks strength for use in high-stress applications like automotive parts. ↩
-
Understand why proper drying prevents bubble formation and improves product strength. ↩
-
Find strategies to enhance product performance by addressing common material issues. ↩
-
Explore how choosing different materials affects the final product’s durability and mechanical properties. ↩
-
Learn how various aspects of mold design can affect the structural integrity of molded products. ↩
-
Understand why controlling mold temperature is critical for ensuring product quality and strength. ↩
-
Explore how different gate positions affect stress distribution and durability in injection molded products. ↩
-
Discover how CAD tools optimize runner systems for better melt flow and product strength. ↩
-
Learn why proper exhaust systems are essential for maintaining product integrity and preventing defects. ↩
-
Understanding impurity effects helps in selecting cleaner materials, enhancing product strength. ↩