Ever thought about how your preferred plastic toys or automobile parts take shape? This happens through injection molding!
Injection molded plastic parts are made by heating and melting plastic, injecting it into a mold under high pressure, and then cooling it to form a specific shape. This method is efficient for producing large quantities of identical parts.
You understand the basics now, so explore each step of this amazing change. Every phase in the injection molding process holds its own special importance and details, which turn the final item into something not only useful but excellent.
Injection molding is ideal for mass production.True
Injection molding efficiently manufactures big numbers of the same parts.
What Are the Key Stages in the Injection Molding Process?
Injection molding changes raw plastic into exact, working parts. This process involves a detailed series of steps.
The key stages in the injection molding process include mold closing, injection, pressure holding, cooling, mold opening, and product removal. Each stage is crucial to ensure the accuracy and quality of the final product.
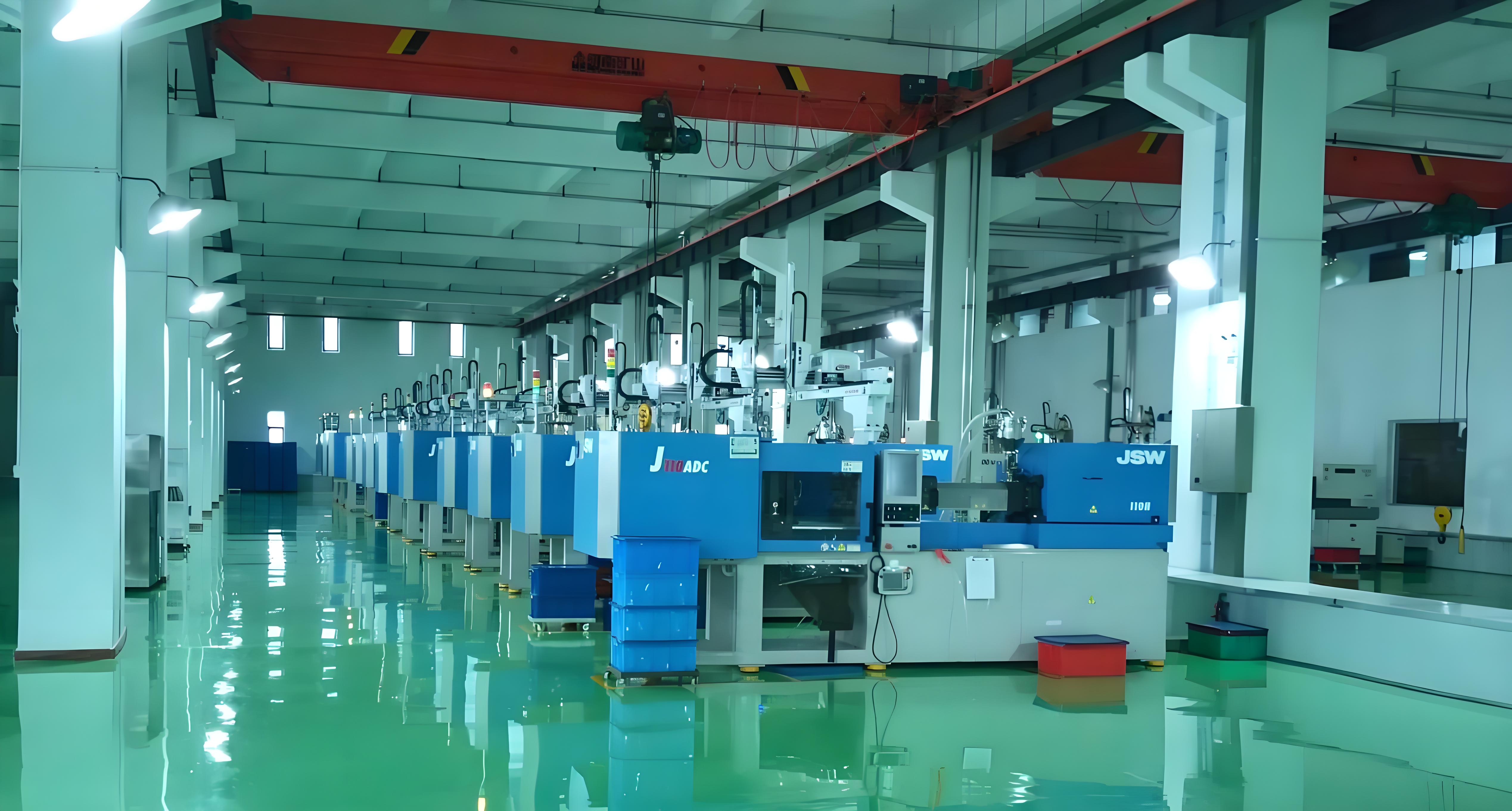
Injection Molding Process
Mold Closing
The injection molding process starts with mold closing. During this time, two mold halves, called "A" and "B" sides, get clamped tightly. This stops the hot plastic from leaking during injection.
Injection of Plastic
When the mold is shut well, molten plastic enters the mold cavity. The plastic warms and melts in a barrel, then forces through a nozzle using hydraulic or mechanical power. This is very important for the initial form of the part.
Holding Pressure
After the cavity fills, holding pressure helps to deal with material shrinkage as the plastic cools and hardens. This step keeps the part’s shape and size correct to stop flaws like sink marks or gaps.
Cooling
Cooling takes a lot of time in the process. Coolant runs through channels in the mold to speed up plastic cooling. Good cooling is crucial for the final product’s stability and surface look.
Mold Opening
When the plastic cools enough and hardens, the mold opens. This means reversing the clamping system to split the "A" and "B" mold sides.
Product Removal
In the end, an ejector system pushes the finished item out of the mold cavity. Often, this is automatic and might involve extra steps like trimming or other tasks to check quality.
By understanding these stages, manufacturers probably improve production efficiency1 and quality control measures. Each step truly influences the success of the injection molding process.
Mold closing prevents plastic leakage.True
High pressure clamping stops any plastic from escaping during injection.
Cooling is the quickest stage in molding.False
Durable cooling needs much time because of necessary dimensional steadiness.
Why Is Injection Molding Preferred for Mass Production?
Injection molding is a top choice for mass production because of its efficiency and accuracy. But why is it so beneficial for large-scale production?
Injection molding is preferred for mass production because it delivers high efficiency, consistent quality, and versatility in material and design, making it ideal for producing large quantities of identical parts.
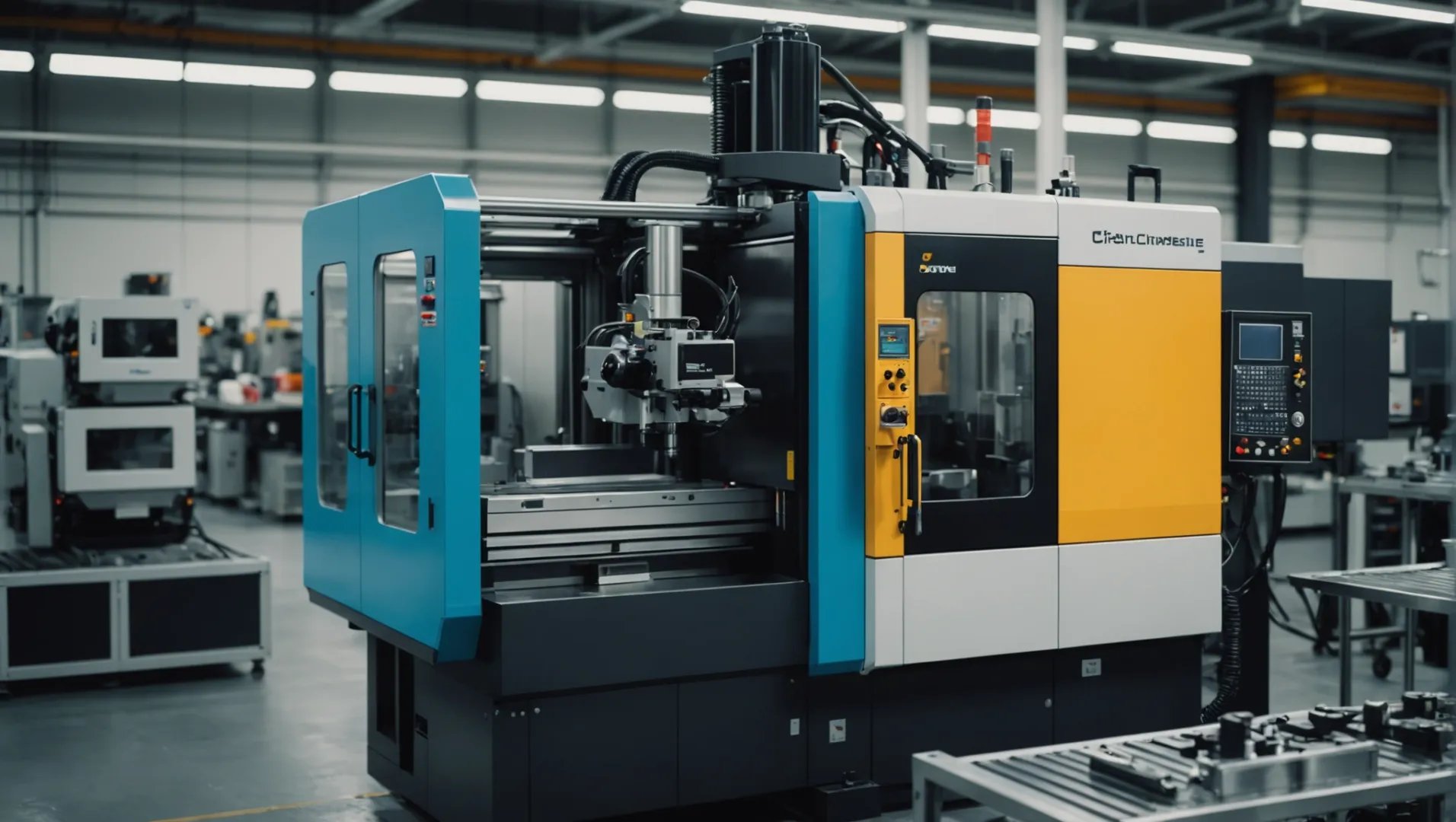
Injection Molding Machine in Operation
High Efficiency and Productivity
Injection molding is popular for mass production because it works very fast. Machines create many parts with little human help, offering an automated solution that reduces time.
An example is a car company producing parts for dashboards. The same mold continues to be used without wearing out, allowing non-stop production and high output. This means lower worker costs and faster product delivery.
Consistent Quality and Precision
All units in mass production need the same quality. Injection molding helps by ensuring each part is made to the correct size and shape as set by the mold. This uniformity is critical in fields like electronics and medical goods where small errors can cause problems.
For instance, making medical syringes requires that each one meets strict quality rules for safe use. This is achieved using accurate molds and advanced control systems that check each production step.
Versatility in Material Use
Injection molding works with many materials, including different thermoplastics and thermosetting plastics. This adaptability allows choosing materials matched to product needs, like strength or heat resistance.
Polypropylene (PP) is often chosen for household products because it is strong and can handle stress. In contrast, polycarbonate is used for products needing transparency and impact protection, like eyewear lenses.
Material | Properties | Common Uses |
---|---|---|
Polypropylene | Strong, stress-handling | Household goods, car parts |
Polycarbonate | Clear, impact-proof | Eyewear lenses, clear containers |
ABS | Strong mechanical features | Appliance cases, toy parts |
Design Flexibility
Injection molding permits great creativity in design. The process creates complex shapes with fine details hard to achieve through other methods. This adaptability comes from molds designed precisely to needs.
For example, cases for electronic gadgets often have complex forms with exact spots for buttons. Injection molding reproduces these complex designs accurately, making sure every part matches the intended design.
In summary, while setup costs for injection molding can be high, its advantages in efficiency, steady quality, material choice flexibility and design creativity make it the top choice for large-scale production.
Injection molding reduces labor costs in mass production.True
Automation in injection molding reduces the need for human effort and decreases worker expenses.
Polycarbonate is used for its high heat resistance in injection molding.False
Polycarbonate attracts attention for clearness and resistance to impact, not for tolerance to heat.
What Materials Are Suitable for Injection Molding?
Selecting the appropriate material for injection molding is important for your product’s success. Each material offers distinct properties, affecting strength, flexibility and cost.
Thermoplastics like polyethylene, polypropylene, polystyrene, polycarbonate, and ABS are suitable for injection molding due to their ability to be melted, molded, and cooled repeatedly without altering their fundamental properties.
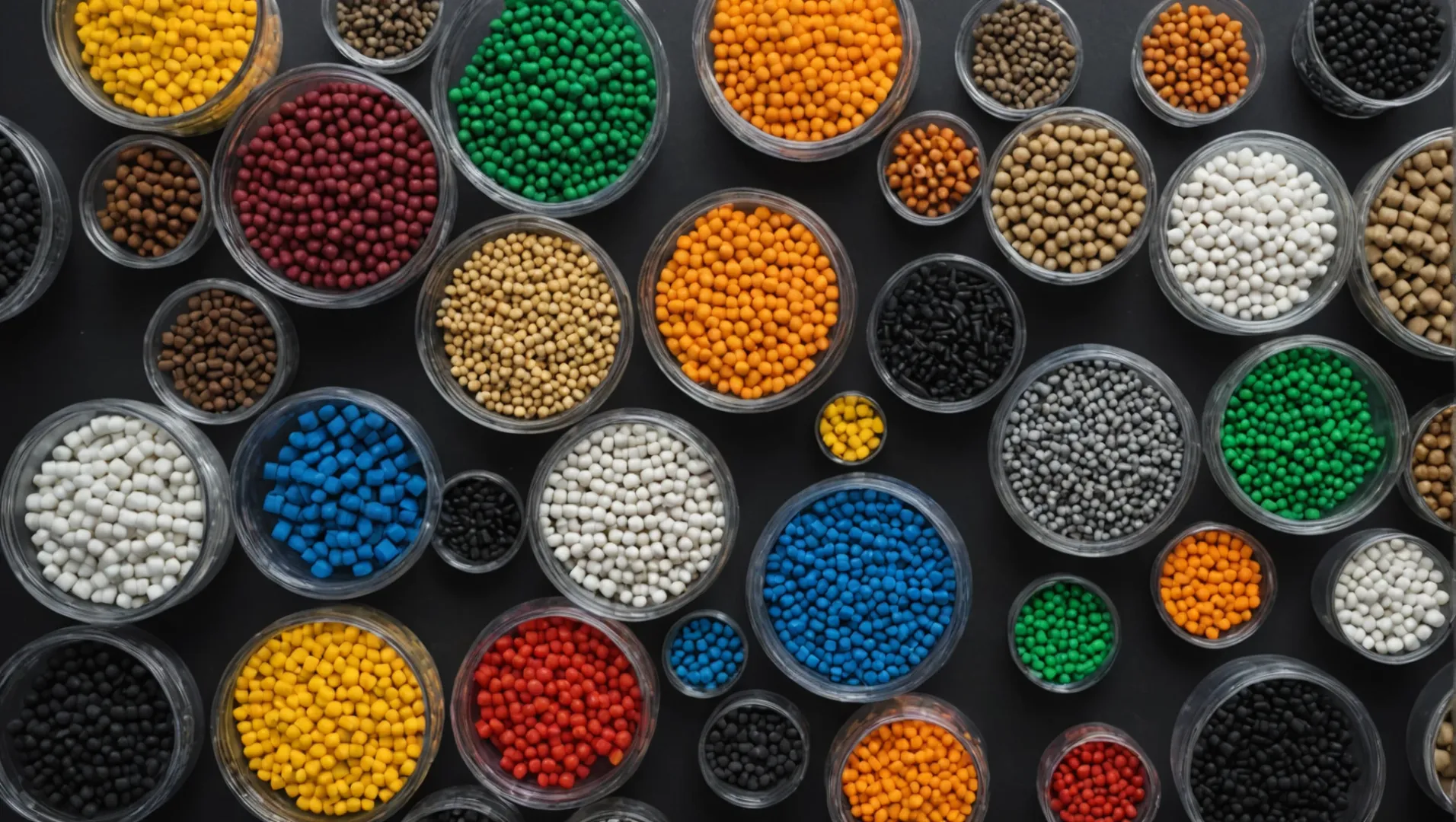
Using Thermoplastics: Popular Choices
Thermoplastics rule the injection molding process2 due to their ability to be reheated and shaped again. These materials adjust easily, suiting many different uses.
-
Polyethylene (PE): PE is robust and bends well, often seen in packaging, containers, and pipes. It comes in different strengths, each offering a mix of durability and flexibility.
-
Polypropylene (PP): PP fights chemicals well and lasts long without breaking. It is used for car parts, fabrics, and household items.
-
Polystyrene (PS): PS is clear and sturdy, great for throw-away cutlery and CD cases.
-
Polycarbonate (PC): PC withstands impacts and is clear, so it serves in glasses lenses, medical tools, and lights.
-
Acrylonitrile Butadiene Styrene (ABS): ABS is strong and resists impacts, often used in car parts, gadget cases, and toys like LEGO.
Material | Key Traits | Common Uses |
---|---|---|
PE | Bends, strong | Packing, pipes |
PP | Resists chemicals | Car parts, fabric |
PS | Clear, stiff | Cutlery |
PC | Impact strength | Glasses lenses |
ABS | Strong | Car parts |
Thermosetting Plastics: Smaller Role
Though thermoplastics are more flexible, some thermosetting plastics are useful in molding too. Once set, these materials stay fixed. Phenolic resins and epoxy resins help where heat is very important.
Picking the Right Material
Deciding which material fits best depends on product requirements. Here are important points to think about:
-
Mechanical Traits: Material must meet strength, stretch and durability needs of the use.
-
Thermal Traits: Must match temperature conditions and stay stable under heat.
-
Chemical Resistance: Important for items facing strong chemicals or tough settings.
-
Cost Balance: Finding cheaper options while keeping material quality is very crucial.
Knowing these helps in picking a material that performs well and fits the budget. For more help in choosing the best material, talking with a specialist or doing a material comparison3 might be useful.
Polyethylene is used in automotive parts.False
Polyethylene often appears in packaging and tubing, not in car parts.
Thermoplastics can be reshaped multiple times.True
Thermoplastics can be heated again and reshaped, which allows them to serve in various molding processes.
How Does Injection Molding Impact Product Design?
Injection molding greatly affects product design by determining forms, substances and production efficiencies.
Injection molding impacts product design by enabling complex shapes, ensuring high precision, and accommodating a wide range of materials. Designers must consider mold design, part functionality, and production efficiency during the design phase.
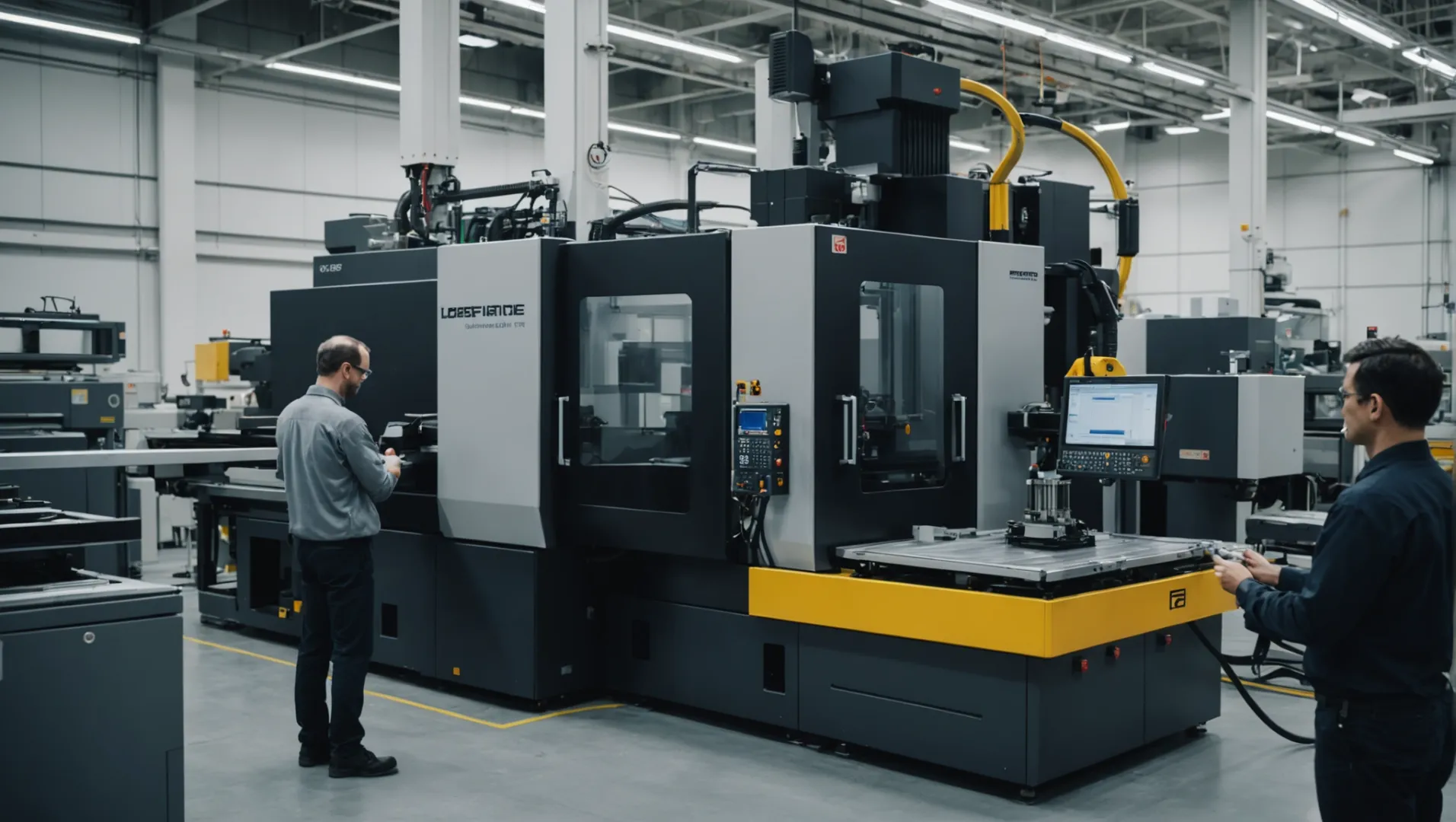
Design Flexibility and Complexity
Injection molding permits the creation of parts with detailed shapes. Designers create products with features like inside spaces, threads, and fine textures. For example, car parts like dashboards and center consoles come out as one piece, even with their complex shapes.
Precision and Consistency
Injection molding has high accuracy, which is key for products needing close fits and exact sizes. The precise mold production and controlled injection steps help every part turn out nearly the same. This is vital for industries like electronics, where parts like circuit casings need exact measurements.
Material Versatility
This method supports a wide range of materials, including some thermoplastics and thermosetting plastics. This range allows designers to pick materials based on needs like strength, clarity, or flexibility. For instance, polycarbonate gets picked for its very strong impact resistance in phone cases.
Impact on Cost and Efficiency
Initial mold expenses for injection molding are high, but the cost per part drops a lot when producing in large numbers. Designers balance upfront spending with possible savings in production and material usage. Recycling leftover materials also adds to cost efficiency and sustainability.
Design Considerations
Designers think about draft angles, wall thickness, and rib placement to improve moldability and cut down flaws like warping or sink spots. Knowing these factors during the design stage helps fully use injection molding advantages.
Injection molding enables intricate product geometries.True
Injection molding permits intricate forms and fine patterns.
Designers ignore mold design in injection molding.False
Mold design plays a key role for keeping things working and running smoothly.
Conclusion
Injection molding transforms manufacturing through its effectiveness and adaptability. Grasping its method enhances appreciation for its importance in producing top-quality items in various industries.
-
Discover strategies to enhance efficiency and reduce cycle times.: 1. Streamline Processes and Workflow · 2. Optimize Machine Utilization · 3. Invest in Advanced Technology · 4. Implement Effective Production … ↩
-
Explore why thermoplastics are preferred for their versatility.: Thermoplastic molding is a manufacturing process that works to create fully functional parts by injecting plastic resin into a pre-made mold. ↩
-
Learn how to evaluate material properties effectively.: Comparing Injection Molding Materials. Tough, stiff, hard, and strong. Good lubricity and resistance to hydrocarbons and organic solvents. ↩