Curious about how molds are made? You’re not alone!
The injection mold-making process involves a series of meticulous steps, starting with product design and analysis, followed by mold design, material preparation, mechanical processing, and assembly. It culminates in testing and optimizing the mold to ensure high-quality production.
While this snippet gives you a quick overview, the full process is complex and requires detailed understanding. Dive deeper into each stage to discover how precision and efficiency are achieved in this fascinating manufacturing technique.
Mold flow analysis identifies gate locations.True
Mold flow analysis optimizes gate placement for efficient mold filling.
What Are the Initial Steps in Mold Design?
Mold design begins with crucial steps that lay the foundation for successful manufacturing.
Initial steps in mold design include product design analysis and mold flow analysis, which help determine structural requirements and optimize efficiency.
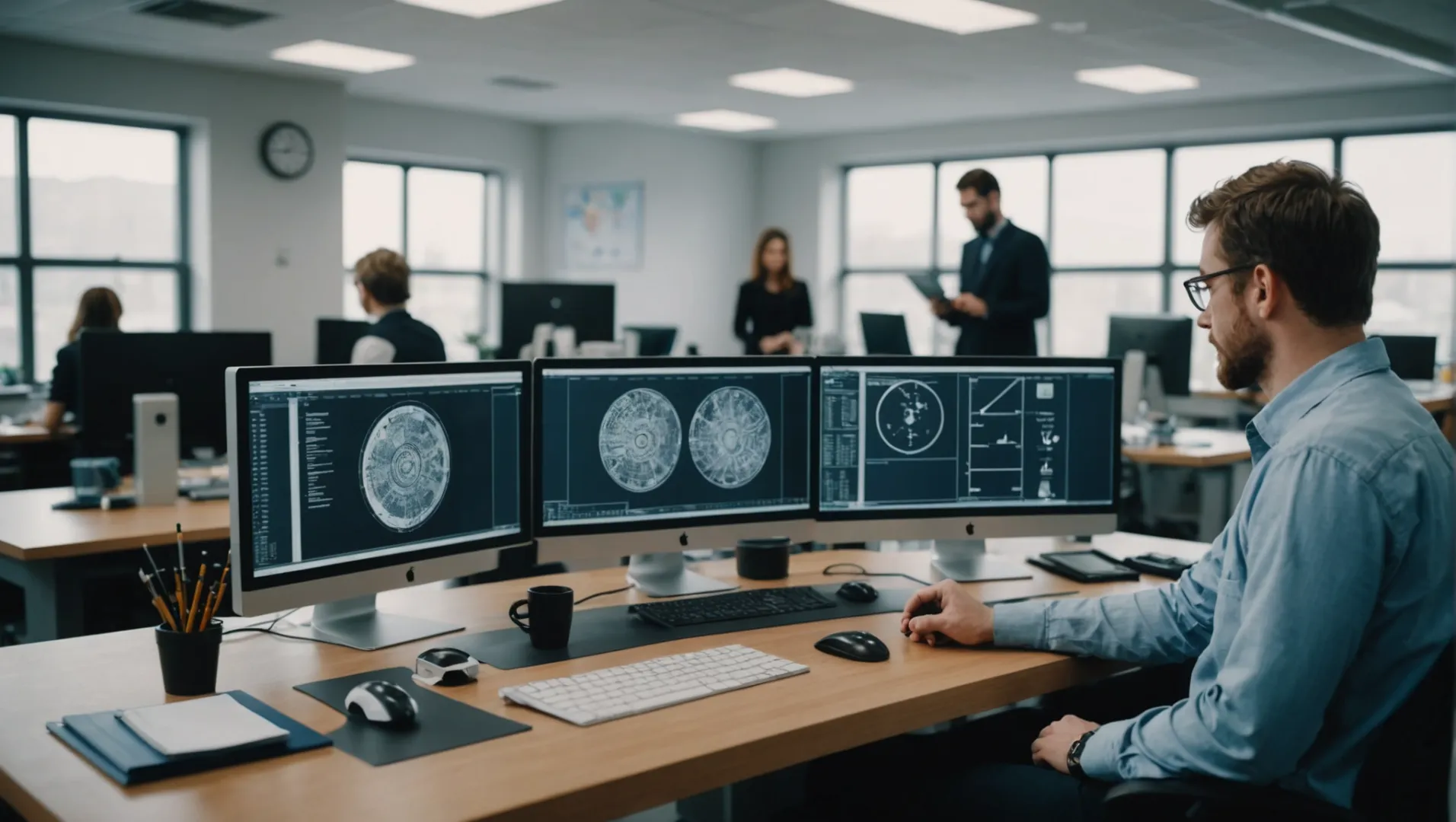
Product Design and Analysis
The initial phase in mold design involves a detailed analysis of the product intended for molding. Designers receive product design drawings or physical samples from clients, which they meticulously assess to understand the shape, size, precision needs, and structural attributes of the product. This analysis is crucial for determining essential mold specifications like cavity layout and parting surfaces.
Understanding the product’s structural features1 ensures that the mold can be designed to accommodate these features without compromising the product’s integrity or the production process’s efficiency.
Mold Flow Analysis
Mold flow analysis is an essential step that simulates how plastic will move through the mold during the injection process. This analysis helps identify optimal gate locations, runner layouts, and cooling systems, crucial for achieving high-quality products and efficient production cycles.
By conducting a mold flow simulation2, designers can preemptively address potential issues like uneven filling or warping, thus enhancing both product quality and manufacturing speed.
Determining Mold Structure
Once the product design and mold flow analyses are complete, the next step is to sketch out the mold’s overall structure. This involves designing the layout of cavities and cores, determining parting lines, and planning the ejection system. Each of these elements is vital for ensuring that the finished product can be easily released from the mold without damage.
The selection of appropriate mold frames3 and standard components, such as screws and guide bushings, is also part of this stage. Choosing the right materials and components contributes to mold durability and performance.
Design Verification
Before proceeding to the actual manufacturing of the mold, a thorough verification of the design is conducted. This step ensures that the proposed design is both feasible and safe. It also checks for rationality in terms of operation and cost-effectiveness. Adjustments may be made based on feedback from this verification process to optimize efficiency and functionality.
Completing these initial steps in mold design not only prepares the groundwork for subsequent stages like material selection and mechanical processing but also plays a pivotal role in achieving a balance between product quality and production efficiency.
Mold design starts with product design analysis.True
Product design analysis is the first step to determine mold specifications.
Mold flow analysis is optional in mold design.False
Mold flow analysis is essential for optimizing gate locations and efficiency.
How Does Mechanical Processing Impact Mold Quality?
Mechanical processing is a pivotal phase in the mold-making journey, directly influencing the mold’s precision and durability.
Mechanical processing impacts mold quality by ensuring precise dimensions and fit, critical for high-performance molds. It involves using various techniques like milling, grinding, and drilling to achieve the desired accuracy and surface finish, which are essential for optimal mold functionality and longevity.
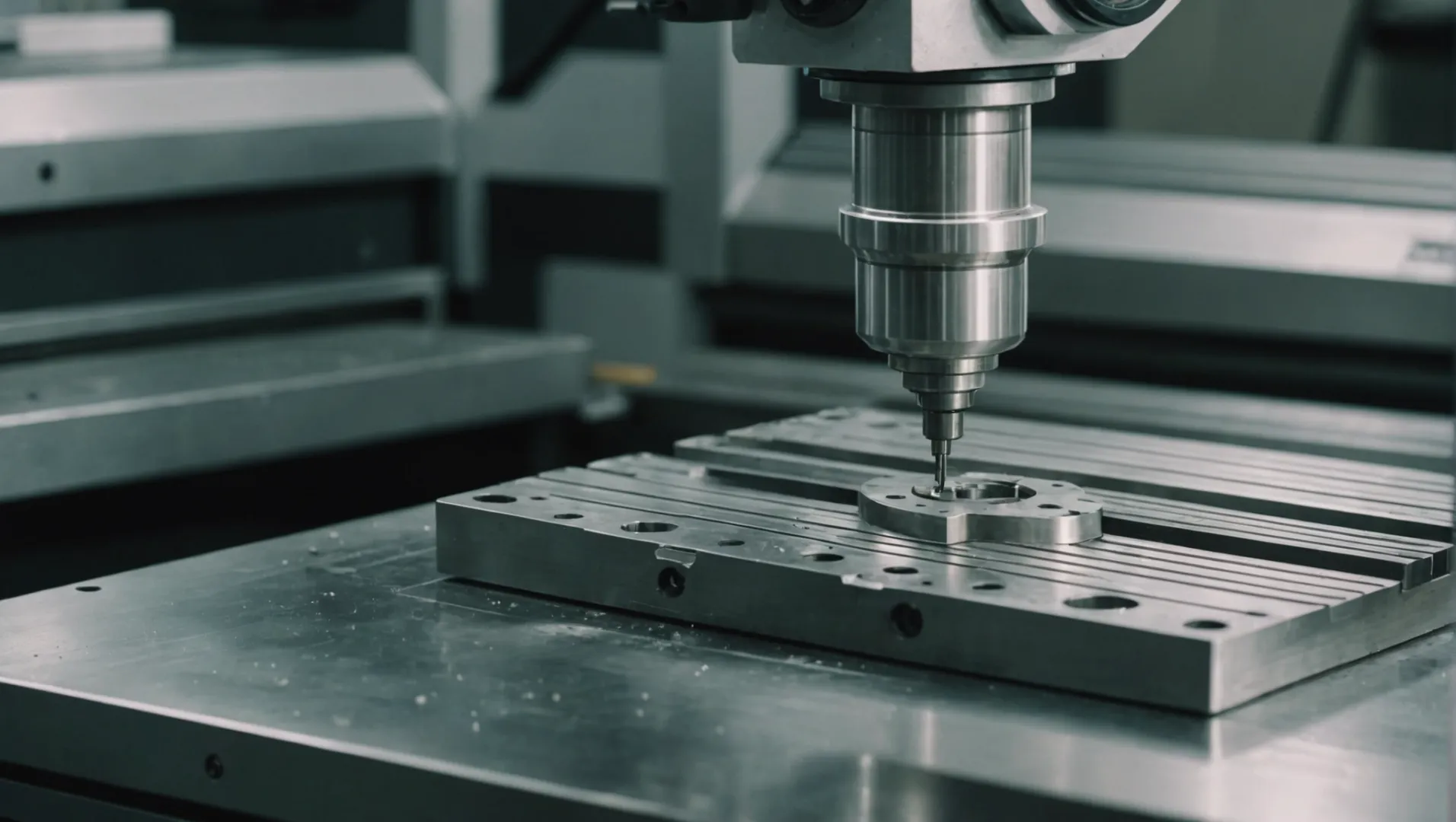
Importance of Precision in Mechanical Processing
Mechanical processing encompasses several techniques aimed at achieving high precision and accuracy. This stage focuses on crafting the mold core, cavity, and other critical components to exact specifications. Techniques such as milling, grinding, and drilling are employed to meet these stringent requirements. The precision achieved in this stage significantly impacts the overall quality of the mold, affecting both its performance and lifespan.
For example, milling operations4 are crucial for shaping the mold cavities. The choice of cutting tools and parameters can influence the surface finish, impacting the mold’s ability to release parts smoothly. Furthermore, precise milling ensures that the cavity dimensions adhere strictly to design specifications, reducing the risk of defects in the final product.
Role of Advanced Machinery and Techniques
The use of advanced machinery such as CNC machines allows for high-precision mechanical processing. These machines operate with computer-aided design (CAD) software, which guides the tool paths with remarkable accuracy. This automation minimizes human error and ensures consistency across multiple mold components.
Grinding is another critical process used to achieve fine surface finishes and tight tolerances. This technique helps enhance the wear resistance of the mold surfaces by creating smooth finishes that reduce friction during molding operations. By maintaining these tolerances, manufacturers can ensure molds have prolonged durability and reliable performance.
Challenges in Achieving Desired Accuracy
Despite the advancements in technology, mechanical processing presents challenges such as tool wear and thermal deformation. Tools used in milling or drilling can wear over time, affecting precision. Regular maintenance and tool replacement are essential to maintain consistent quality.
Thermal deformation occurs due to the heat generated during processing. This can lead to dimensional inaccuracies if not properly managed. Techniques such as cooling systems or choosing materials with suitable thermal properties are employed to counteract these effects.
Impact on Mold Performance and Efficiency
The meticulous attention to detail in mechanical processing directly correlates with the mold’s performance during production runs. High-quality mechanical processing ensures that molds can withstand the repeated stress of injection cycles without compromising on part quality.
Moreover, efficient mechanical processing can lead to reduced cycle times in production. By ensuring precise fit and smooth operation, molds can operate at higher speeds without risking damage or defects in produced parts. This boosts overall manufacturing efficiency, making it a critical aspect of the mold-making process.
Mechanical processing ensures mold precision and durability.True
Precision in mechanical processing is crucial for the mold's accuracy and lifespan.
Advanced machinery does not affect mold quality.False
CNC machines enhance precision, reducing human error and improving mold quality.
Why Is EDM Crucial for Complex Mold Parts?
Electrical Discharge Machining (EDM) plays a pivotal role in crafting intricate mold parts with unmatched precision and detail.
EDM is essential for creating complex mold parts due to its ability to machine intricate geometries with high precision, especially where traditional machining techniques fall short.
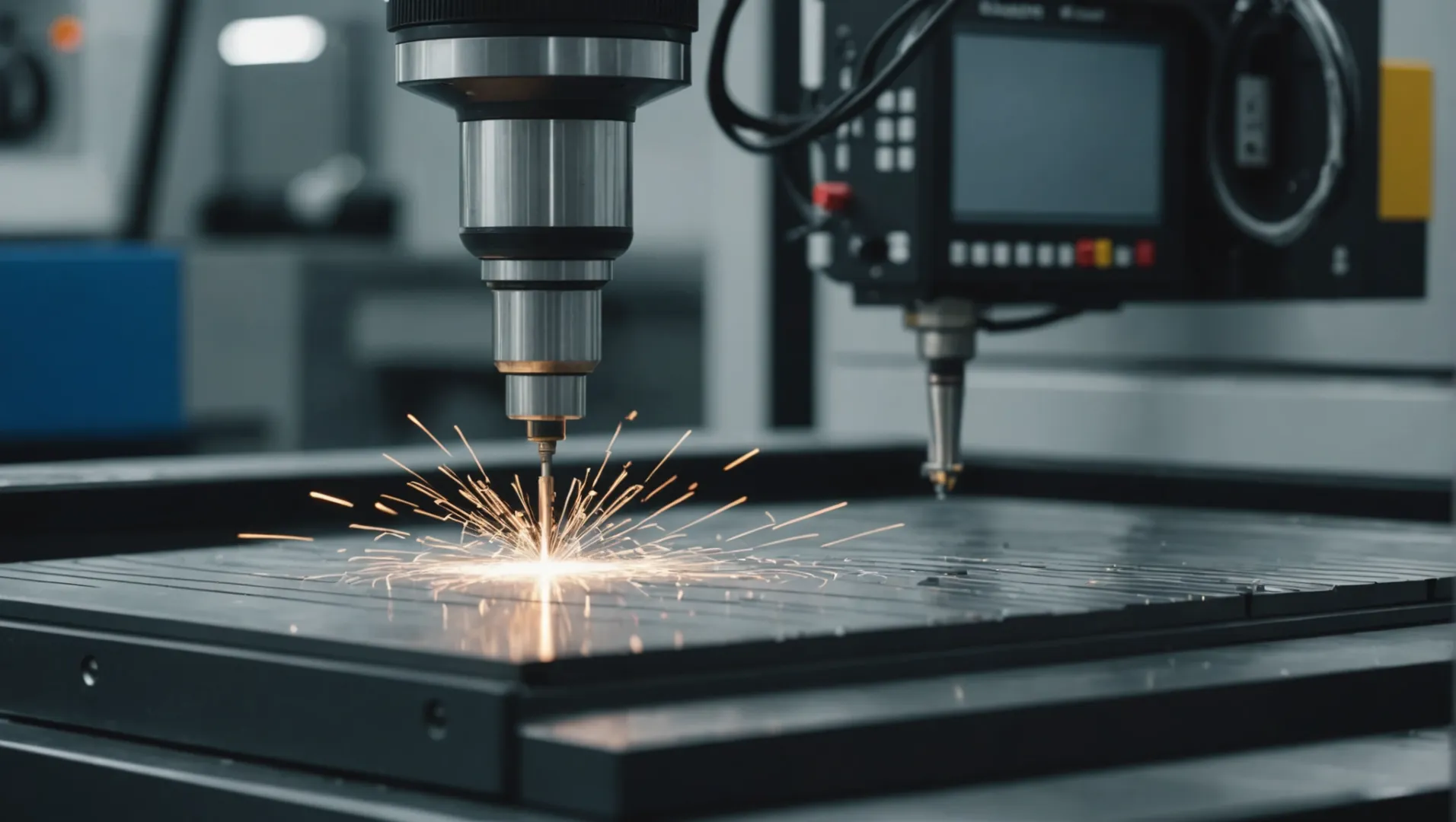
The Fundamentals of EDM
Electrical Discharge Machining (EDM) is a non-conventional machining process that removes material from a workpiece through a series of rapidly recurring electric discharges between an electrode and the workpiece. This technique is particularly useful for molds with complex shapes, intricate contours, or delicate materials that might be damaged by traditional methods.
EDM excels in producing parts with tight tolerances and fine surface finishes, making it indispensable for industries such as aerospace and automotive, where precision is paramount.
Why Complexity Demands EDM
-
Intricate Geometries: Traditional machining often struggles with complex shapes due to limitations in tool accessibility. EDM, however, can create precise internal corners and intricate cavities with ease. For example, when molding components that require detailed features like undercuts or narrow slots, EDM provides the necessary flexibility.
-
Hard Materials: Some mold parts are made from extremely hard materials, such as carbide or hardened steel. Conventional machining can be inefficient or even impossible in these scenarios. EDM can handle these materials effectively because it doesn’t rely on mechanical force, thus avoiding tool wear issues.
-
High Precision and Surface Finish: EDM is renowned for its ability to produce high-precision components with excellent surface finishes. This quality is critical for molds used in high-stakes industries where product performance is closely tied to the precision of each component.
EDM in Action: A Closer Look
Consider the example of a complex automotive mold part with a highly detailed surface texture that contributes to the aesthetic and functional qualities of the final product. Exploring advanced EDM techniques5 could reveal how manufacturers use this technology to achieve such intricate details without compromising structural integrity.
Feature | Traditional Machining | EDM |
---|---|---|
Complex Geometries | Limited | Excellent |
Hard Materials | Challenging | Efficient |
Surface Finish | Varies | Superior |
Ensuring Efficiency and Quality
To maximize the benefits of EDM, selecting the right electrode material and processing parameters is crucial. Additionally, post-processing steps like cleaning and inspection are vital to ensure that the final mold meets all design specifications and quality standards.
By integrating EDM into the mold-making process, manufacturers not only achieve the required complexity and precision but also enhance production efficiency. Exploring how EDM complements other manufacturing processes6 offers deeper insights into its strategic role in modern manufacturing.
EDM is ineffective for machining hard materials.False
EDM is effective for hard materials, avoiding tool wear issues.
EDM provides superior surface finishes in mold parts.True
EDM excels in producing high-precision components with excellent finishes.
What Role Does Surface Treatment Play in Mold Longevity?
Surface treatment is a critical step in ensuring the longevity and efficiency of molds in manufacturing.
Surface treatment enhances mold longevity by improving wear resistance, reducing corrosion, and optimizing mold release properties. Techniques like quenching, nitriding, and chromium plating are tailored based on the mold’s use and material characteristics.
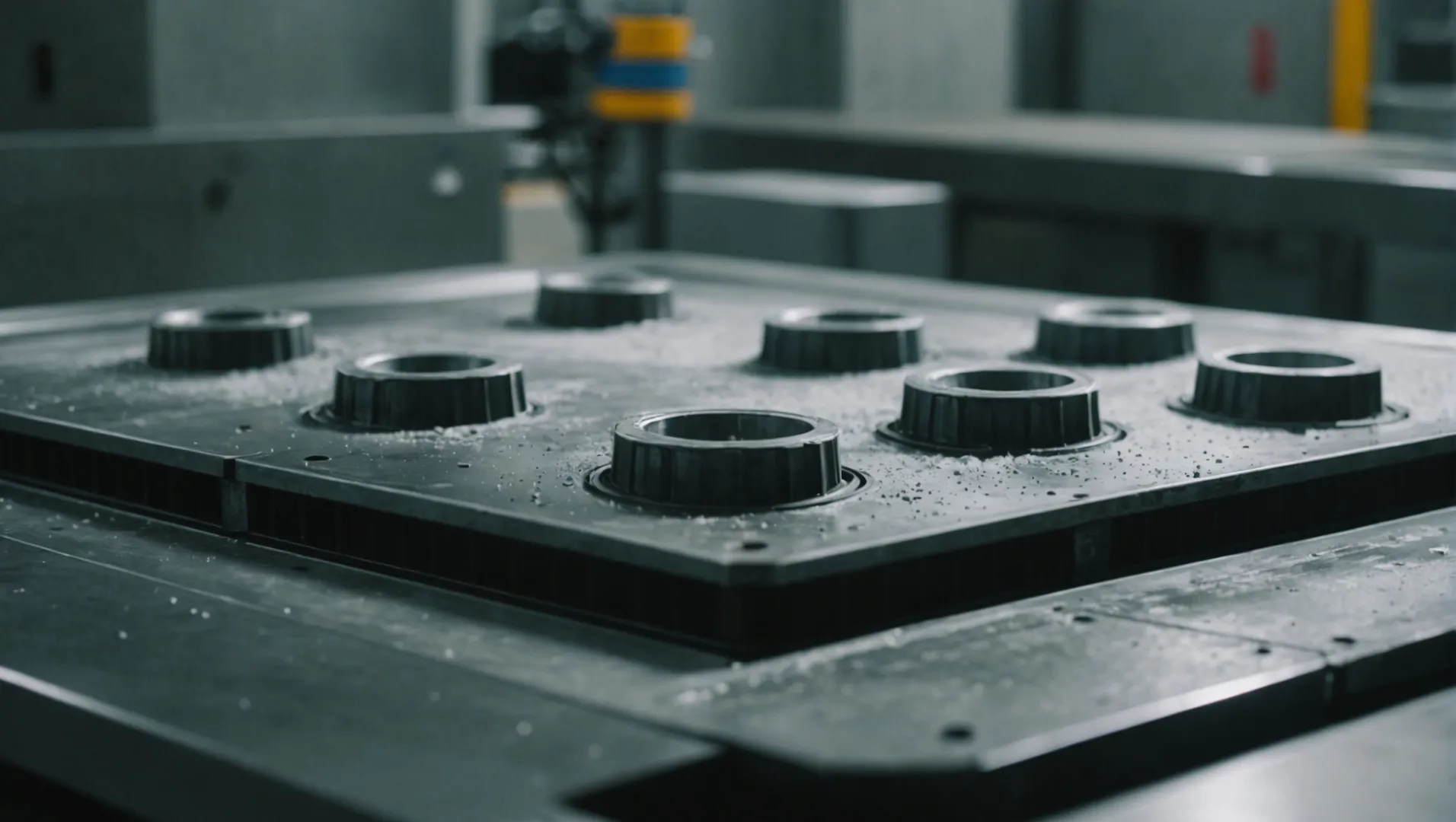
Enhancing Wear Resistance
Wear resistance is vital for molds that undergo repeated cycles under high pressure and temperature. Surface treatments such as quenching and nitriding enhance this resistance by hardening the surface, making it less susceptible to abrasion and deformation over time.
- Quenching: This process involves heating the mold material to a high temperature and then rapidly cooling it, which hardens the surface and enhances durability. It’s particularly effective for molds used in high-volume production settings.
- Nitriding: By diffusing nitrogen into the surface layer of the mold material, nitriding forms a hard nitride layer that significantly increases wear resistance without compromising the core strength of the mold.
Preventing Corrosion
Corrosion can severely impact mold longevity, especially when molds are exposed to corrosive materials or environments. Surface treatments aim to create a protective barrier that resists corrosion.
- Chromium Plating: Applying a thin layer of chromium provides excellent protection against oxidation and rust. This method is especially beneficial for molds used with corrosive plastics or in humid conditions.
Improving Mold Release Performance
Mold release performance is crucial for maintaining product quality and reducing cycle times. Surface treatments can help in achieving smoother ejection of molded parts.
- Polishing and Coating: Polishing reduces surface roughness, while specialized coatings can be applied to reduce friction between the mold and the part, facilitating easier release.
Tailoring Surface Treatment to Mold Needs
Choosing the right surface treatment depends on the mold’s operational environment and the material used. For example, a mold used in high-temperature applications7 may require different treatments compared to one used in corrosive settings.
Understanding the specific requirements of each mold ensures that the selected surface treatment not only enhances longevity but also optimizes performance, leading to higher efficiency and lower maintenance costs.
Quenching improves mold longevity by enhancing wear resistance.True
Quenching hardens the mold surface, increasing durability under stress.
Nitriding is ineffective for molds in corrosive environments.False
Nitriding enhances wear resistance but does not prevent corrosion.
Conclusion
Every step in the injection mold-making process is crucial for quality production. Reflect on these insights to enhance your skills or drive innovation in manufacturing.
-
Explore why understanding structural features is crucial in mold design.: The guide injection mold components are critical in ensuring that the mold core opens and closes accurately along the designed path. The guiding … ↩
-
Learn how mold flow analysis improves product quality and efficiency.: What are the benefits of mold flow analysis? · Optimize the runner system · Predict the pattern of the fill · Determine shrinkage rate · Reduce lead times. ↩
-
Discover tips on choosing the right mold frames for durability.: Ultimate Guide for Selecting the Right Injection Mold · Five Key Items to Consider Before Selecting a Mold · Speed to Build · Cost of the Initial Mold Build. ↩
-
Explains how milling ensures dimensional accuracy in mold cavities.: Diamond is known for producing very detailed, high-precision (±0.0001 inch/0.0025 millimeter) injection molds designed for very high-volume … ↩
-
Discover how EDM achieves intricate details without compromising integrity.: Proper cooling is crucial in molding, yet often overlooked. Discover proper cooling methods to prevent defects and improve efficiency. ↩
-
Learn how EDM enhances efficiency alongside other manufacturing methods.: This paper has as its focus the integration of Electrical Discharge Machining (EDM) within a Computer Integrated Manufacturing (CIM) environment. ↩
-
Discover specialized treatments for molds exposed to extreme heat conditions.: One of the earliest forms of mold treatment is chrome plating. This increases tool hardness to resist abrasion when using glass-filled resins. ↩