In the world of injection molding, the design of the parting surface can make or break the success of a project.
The key points in injection mold parting surface design include considerations of product shape, demolding direction, mold structure rationality, gate positioning, and exhaust system design. The main challenges involve complex product structures, high precision requirements, material selection, and the demand for innovative designs.
While understanding these essentials provides a foundational grasp of parting surface design, overcoming the associated challenges requires deeper insights. Read on to explore how these factors play out in real-world scenarios and discover strategies to optimize your mold designs.
Product shape dictates mold parting surface design.True
Product shape affects where molds split, ensuring minimal stress during demolding.
How Does Product Shape Influence Parting Surface Design?
The shape of a product significantly dictates the design of the parting surface in injection molds.
Product shape influences parting surface design by dictating where the mold splits, ensuring minimal stress during demolding, and facilitating mold processing. The parting surface should align with the product’s geometry to prevent deformation, ease demolding, and maintain product integrity.
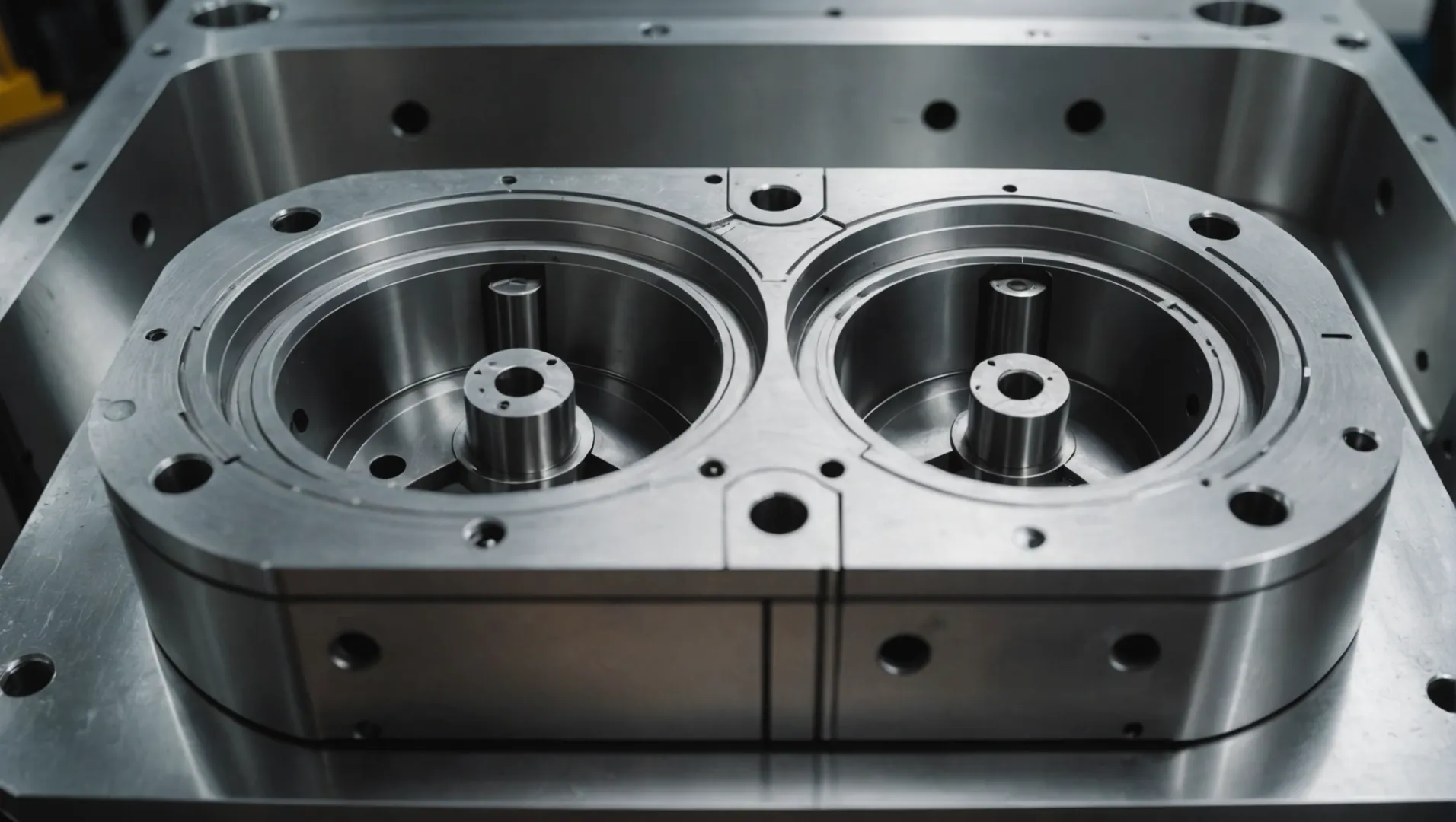
Aligning the Parting Surface with Product Geometry
The contour of the product is crucial when designing the parting surface. For example, in a cylindrical product, the parting surface is typically set along the diameter, allowing smooth separation of the mold halves. This approach minimizes tension during demolding, which is essential for maintaining the product’s shape and structural integrity.
In products with intricate shapes, designers must conduct a detailed analysis of geometric features to determine the most feasible parting position. This ensures that complex areas, like curves or angles, do not create unnecessary resistance or require excessive force during the mold separation process. Selecting an optimal parting line aids in achieving seamless processing1 and enhances the overall mold efficiency.
Considering Demolding Directions
The demolding direction is another key factor influenced by product shape. The parting surface must be designed to align with the natural demolding path of the product, which often requires a strategic approach. For instance, products with side holes or undercuts might need additional elements such as sliders or inclined ejectors to aid demolding without causing damage.
Designers must ensure that these components have adequate space within the mold for movement. The parting line should facilitate this arrangement, reducing any risk of deformation or cracking due to uneven forces during demolding. This alignment is pivotal for maintaining product quality and consistency across production batches.
Impact on Mold Structure and Efficiency
The shape of a product also affects how the mold is constructed. Regularly shaped products allow for simpler parting surfaces, often involving planes or regular curves that simplify mold processing and assembly. However, irregularly shaped products may necessitate complex molds with intricate parting lines.
Such designs must consider mold strength and rigidity; weak points can lead to premature wear or failure. By strategically placing reinforcing ribs or optimizing the mold structure, designers can enhance durability while maintaining ease of assembly2 and accuracy.
Balancing Design Complexity with Cost
Complex shapes can drive up mold design costs due to the need for advanced features and precision machining. Designers often face a trade-off between cost and performance, as intricate parting surfaces might require higher-grade materials or sophisticated manufacturing processes.
By leveraging innovative technologies like 3D printing or high-speed machining, designers can balance innovation with cost-effectiveness3, ensuring that the mold design aligns with both production goals and budgetary constraints.
Cylindrical products have simpler parting surfaces.True
Cylindrical shapes allow parting surfaces along the diameter, easing demolding.
Complex shapes require fewer mold design features.False
Complex shapes need advanced features to ensure efficient demolding.
What Role Does Demolding Direction Play in Mold Design?
Demolding direction is pivotal in mold design, influencing product integrity and manufacturing efficiency.
Demolding direction determines how a product is released from the mold, affecting product quality and mold longevity. It requires careful alignment with the product’s structure to avoid damage and ensure a smooth release, often necessitating additional features like sliders for complex designs.
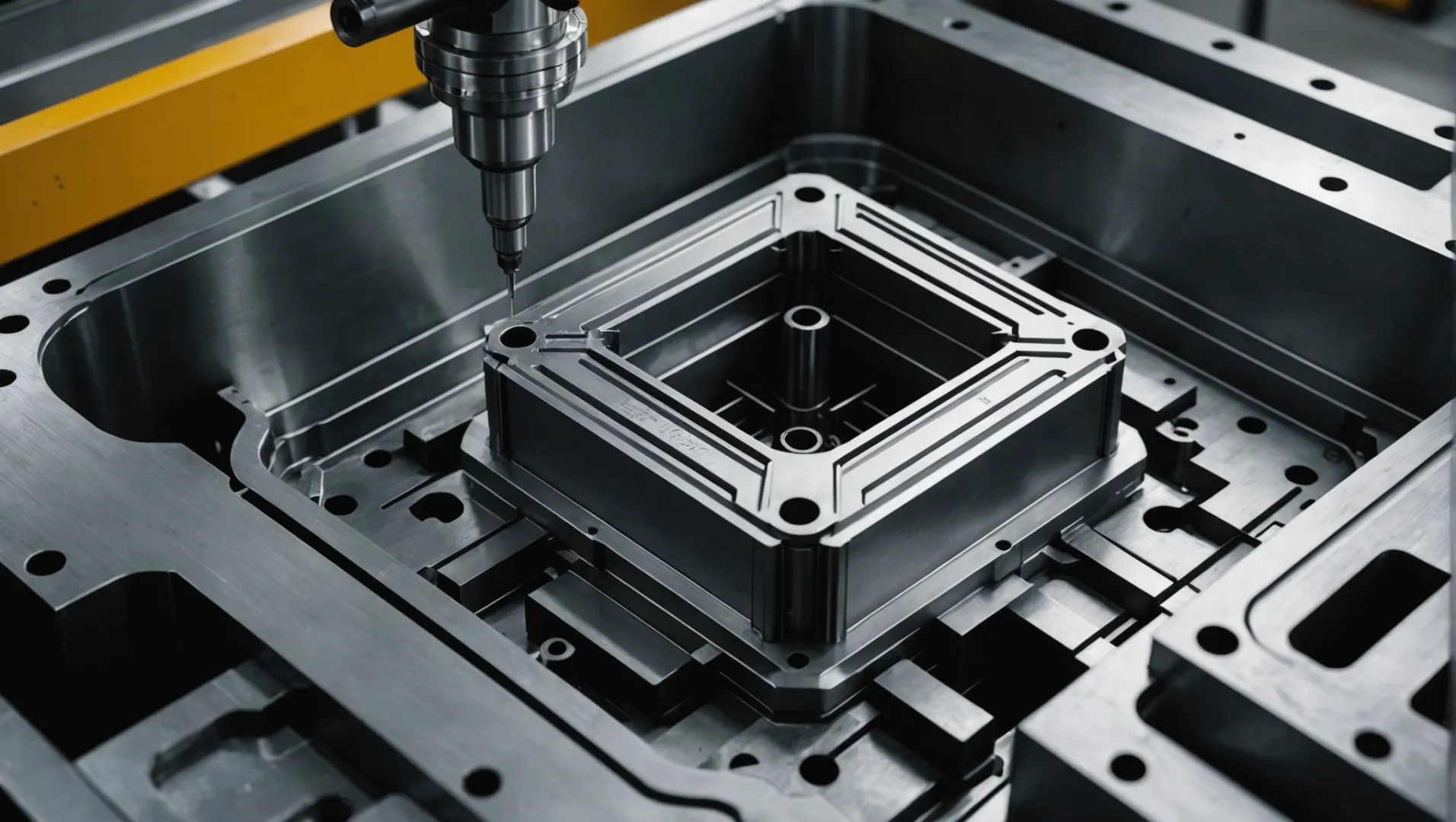
Understanding Demolding Direction
In the realm of mold design, demolding direction refers to the path along which a molded product is ejected from its mold. This direction is crucial as it dictates not only the ease of demolding but also the potential for defects in the finished product. For instance, aligning the demolding direction with the natural contours of a product minimizes stress and deformation during ejection.
Consider a simple cylindrical part. The optimal demolding direction is along the axis of the cylinder, allowing for smooth separation without exerting undue stress on the product. Conversely, a complex component with features such as side holes or undercuts demands innovative solutions like sliders or lifters to facilitate demolding without compromising product integrity.
Aligning Demolding Direction with Product Features
Properly aligning the demolding direction with a product’s structural features is integral to maintaining its quality. The design must account for potential obstacles that might hinder the release process. For example, products with intricate geometries often require customized mold designs to address these challenges effectively.
In such cases, additional components like sliders or lifters may be integrated into the mold design. These elements help in overcoming obstacles posed by complex features, ensuring that each part of the product releases cleanly and without damage. Such enhancements, while initially increasing mold complexity and cost, ultimately lead to higher quality products and reduced waste.
The Impact on Mold Longevity and Cost
The choice of demolding direction can significantly affect both mold longevity and overall production costs. A well-considered demolding direction can reduce wear and tear on the mold, prolonging its lifespan and reducing the need for frequent maintenance or replacement.
When designing molds for high-volume production, considering demolding direction becomes even more critical. Misalignment can lead to increased wear on specific parts of the mold, leading to higher maintenance costs and potential downtime. By ensuring that the demolding process is as smooth as possible, manufacturers can achieve greater efficiency and cost-effectiveness.
In conclusion, while demolding direction might seem like a minor detail, its impact on mold design and production efficiency cannot be overstated. Understanding these principles4 is essential for any manufacturer aiming to optimize their injection molding processes for both quality and cost-effectiveness.
Demolding direction affects mold longevity.True
Proper demolding direction reduces mold wear, extending its lifespan.
Sliders are unnecessary for complex mold designs.False
Sliders help release complex parts without damage, ensuring quality.
How Can Mold Structure Affect Production Efficiency?
The mold structure in injection molding plays a pivotal role in determining production efficiency and quality.
Mold structure affects production efficiency by influencing cycle times, material waste, and product quality. Efficient mold design reduces production time, ensures consistent quality, and minimizes material usage.
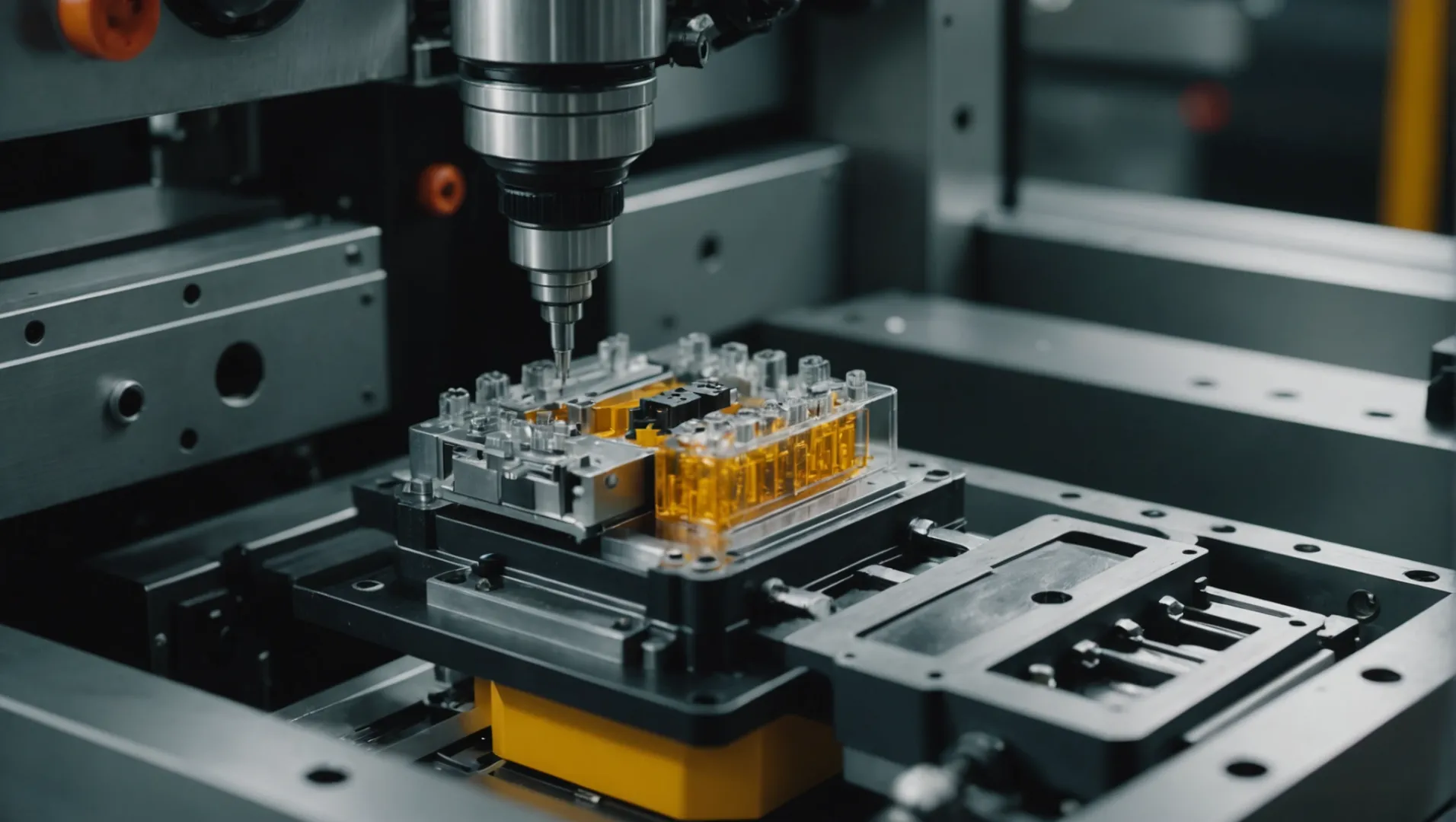
Understanding Mold Structure and Production Efficiency
The structure of an injection mold is a critical determinant of how efficiently a production line operates. A well-designed mold can significantly reduce cycle times — the duration from when material is injected until the finished part is ejected. This efficiency is primarily achieved through strategic design choices that optimize cooling channels, gate placement, and ejection systems.
Cooling Systems
One of the most critical aspects of mold structure impacting efficiency is the cooling system. Efficient cooling channels ensure rapid heat dissipation, reducing the overall cycle time. For example, conformal cooling channels, which are designed to follow the contours of the mold cavity, provide uniform cooling and reduce warping or shrinkage issues. This design innovation allows for faster production cycles without sacrificing product quality5.
Gate and Runner Systems
The design of gate and runner systems within the mold affects not only the material flow but also the ease of demolding. A well-planned runner system reduces material waste and ensures even distribution of the molten plastic. This means fewer defects and less need for post-processing, directly impacting production costs and efficiency.
Ejection Mechanisms
Efficient ejection mechanisms are essential for smooth operations. Poorly designed ejection systems can lead to product damage or require additional time to separate the finished product from the mold. By utilizing advanced ejection techniques such as hydraulic or pneumatic systems, manufacturers can improve cycle efficiency6 and maintain product integrity.
Structural Integrity and Maintenance
The robustness of a mold structure also plays into its efficiency. A strong, durable mold requires less frequent maintenance, ensuring consistent uptime in production. Materials such as hardened steel, though costly upfront, offer longer lifespans and resist wear and tear better than softer materials. By investing in high-quality materials and designs, companies can achieve greater long-term efficiency.
In conclusion, while mold structure might seem like a backend detail in production, its impact on efficiency and quality is profound. By focusing on cooling systems, gate design, ejection methods, and material choice, manufacturers can optimize their processes significantly.
Efficient mold design reduces production time.True
Strategic design choices optimize cooling and ejection, cutting cycle times.
Poorly designed molds increase material waste.True
Inefficient runner systems lead to uneven flow and excess waste.
Why Is Innovative Design Important in Modern Injection Molding?
In the fast-evolving field of injection molding, innovative design is not just a trend but a necessity for staying competitive and efficient.
Innovative design in modern injection molding is crucial for improving product quality, reducing costs, and accelerating production timelines. It enables the adoption of advanced technologies and addresses the complexities of intricate mold structures, ultimately driving industrial growth and competitiveness.
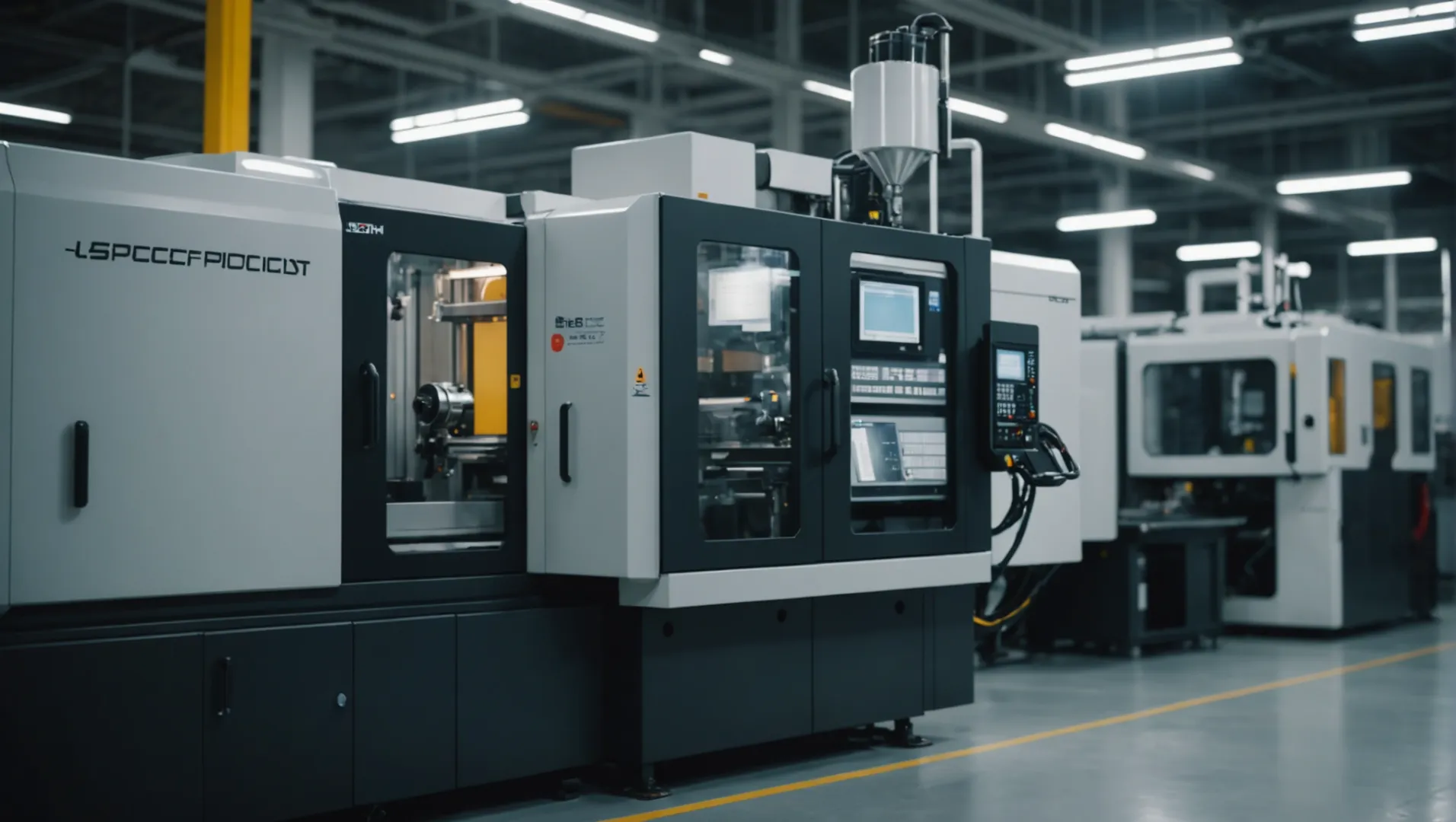
The Impact of Innovative Design on Product Quality
Innovative design in injection molding is essential to achieving superior product quality. By integrating advanced technologies such as simulation software and 3D printing, designers can create molds that yield highly precise components. For instance, using simulation allows for the analysis of potential defects before the physical mold is produced, ensuring smoother production processes.
Moreover, innovative designs cater to increasingly complex product geometries and functions. Exploring novel materials7 and mold features can lead to enhanced durability and performance, meeting stringent industry standards.
Cost Reduction Through Design Innovation
Cost management is a significant challenge in the manufacturing sector. Innovative design strategies can lead to substantial cost savings by optimizing material usage and reducing waste. For example, employing automated design techniques8 can minimize manual intervention, resulting in faster cycle times and lower labor costs.
Additionally, innovative designs often incorporate multi-functional components that reduce the number of parts required in an assembly, leading to lower material costs and simplified logistics.
Accelerating Production Timelines
With market demands escalating, the ability to quickly adapt to new trends and customer preferences is crucial. Innovative designs facilitate rapid prototyping and testing, significantly reducing the time from concept to production. The integration of advanced manufacturing technologies9 such as AI-driven design optimizes production schedules and enhances flexibility.
This acceleration is vital for maintaining a competitive edge, particularly in industries where product life cycles are continually shortening.
Addressing Complex Mold Structures
Modern products often feature intricate designs that require equally complex molds. Innovative design approaches, including the use of modular mold systems10, allow for easier customization and scalability. These systems enable manufacturers to respond swiftly to design changes without the need for complete retooling.
Furthermore, incorporating smart technologies such as sensors and IoT devices into mold designs can provide real-time data on mold conditions, enhancing predictive maintenance capabilities and minimizing downtime.
Innovative design in injection molding is not just about creating new products but about optimizing processes to meet future demands efficiently. As technology advances, the importance of staying at the forefront of design innovation becomes increasingly apparent.
Innovative design reduces injection molding costs.True
Design innovations optimize material use, cutting costs significantly.
Simulation software is irrelevant in mold design.False
Simulation software helps identify defects, improving mold accuracy.
Conclusion
Mastering the design of injection mold parting surfaces is crucial for achieving high-quality, cost-effective products. By addressing design complexities and precision challenges, engineers can significantly enhance production outcomes.
-
Explore strategies for optimizing mold designs to enhance processing efficiency.: 1. Determine the proper wall thickness. · 2. Keep wall thickness consistent. · 3. Pick the ideal location for the gate. · 4. Avoid sharp corners. ↩
-
Learn methods to improve accuracy and ease of mold assembly.: Machine calibration is a critical process in CNC machining, ensuring that machines maintain their ability to produce parts with high precision. ↩
-
Discover how innovation can balance cost in mold design.: Proper tooling design and optimization are crucial for cost-effective injection mold production. Minimize the number of cavities and use multi-cavity molds … ↩
-
Explore how demolding affects product quality and manufacturing efficiency.: Injection molded functional parts must have draft angles toward both sides of the cavity and core to reduce the risk of part damage and to ensure ejection. ↩
-
Learn how conformal cooling improves cycle time and product quality.: This is considered beneficial for rapidly cooling the mold between injection cycles, increasing productivity, and improving the quality of … ↩
-
Discover efficient ejection methods to boost production speed.: The molten polymer is injected into an injection mold and then cooled and hardened to obtain the desired shape. The injection molding method can be used to … ↩
-
Discover new materials that enhance durability and performance.: A great innovation for injection molding is structural foam molding. This process combines injection molding and gas-assisted injection molding … ↩
-
Learn how automation reduces costs and improves efficiency.: There is no “one size fits all” solution in automation. When considering what it would look like in your plant, hone in on the staff, products, … ↩
-
Explore cutting-edge technologies driving rapid production.: It is possible to master the whole life cycle of your parts by combining additive manufacturing and injection molding. Take a look at our 3-step-process. ↩
-
Understand how modular systems offer flexibility and efficiency.: A modular molding system produces small, high quality precise parts with low tooling investment and extremely competitive piece pricing. ↩