Ever wondered how those intricate plastic components you use daily are made? The answer lies in the precise art of injection mold manufacturing.
Injection mold manufacturing involves stages like design, preparation, processing, assembly, debugging, optimization, and acceptance, ensuring the final product meets quality and functionality standards.
It all starts with mold design, where I meticulously analyze product drawings to understand every nuance, from shape to material. Then comes manufacturing preparation, a phase where selecting the right steel feels like choosing the perfect ingredients for a recipe. Processing mold parts is akin to sculpting a masterpiece from raw metal. Assembly requires a touch of precision and creativity, ensuring every part fits just right, like a puzzle coming together.
Debugging is my favorite part—solving problems to ensure perfection. It’s like fine-tuning an instrument until it plays a flawless tune. Finally, acceptance and delivery wrap up the journey, where I get to see the tangible results of our hard work. This process isn’t just about manufacturing; it’s about crafting solutions that work seamlessly in the real world.
Injection mold manufacturing includes debugging and optimization.True
Debugging and optimization are crucial stages to ensure product quality.
Mold design is the final stage in injection mold manufacturing.False
Mold design is the initial stage, setting the foundation for production.
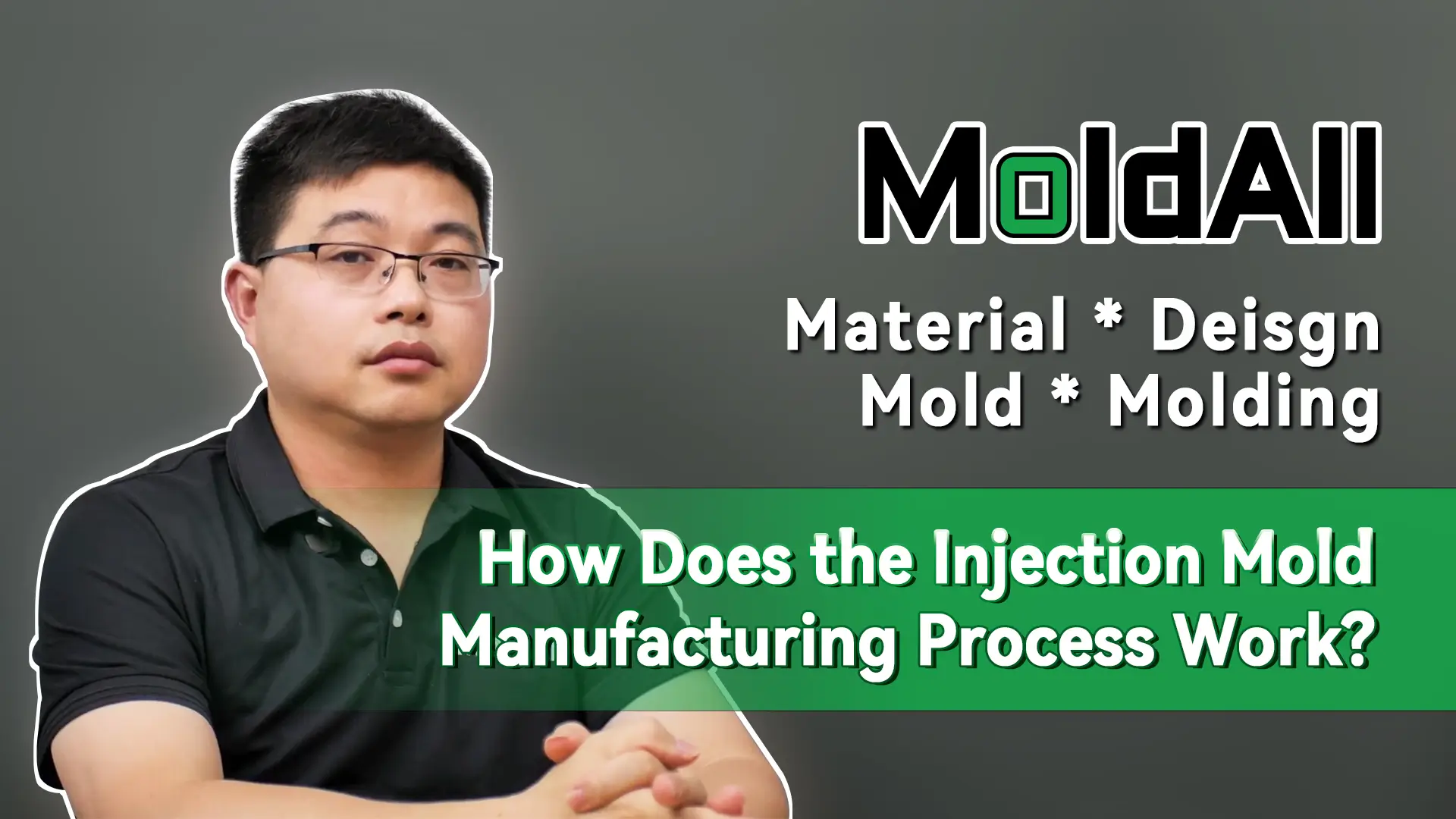
How Do You Design a Mold Successfully?
Diving into mold design feels like stepping into a world where creativity meets precision. Each step is a puzzle piece contributing to the perfect mold.
Successful mold design involves analyzing the product, selecting an appropriate mold structure, and creating detailed drawings to meet quality standards and production requirements effectively.
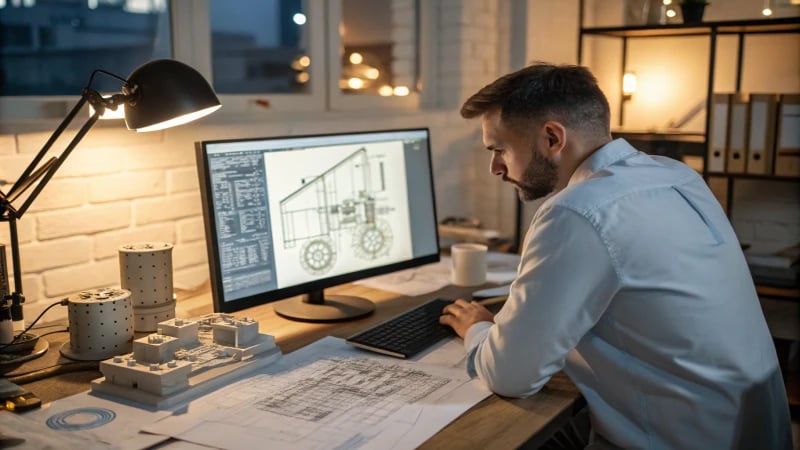
Product Analysis
When I first started in mold design, the excitement of transforming a concept into something tangible was overwhelming. It all begins with understanding the product’s requirements. Analyzing drawings or samples, I focus on the geometric shapes, dimensional tolerances, and materials. I remember working on automotive interior parts, realizing how crucial it was to get every curve and texture right. This stage ensures the mold meets the product’s functional and aesthetic demands.
Determining the Mold Structure
Choosing the right mold type feels like selecting the perfect tool for a task. Depending on the product’s characteristics and production needs, I might opt for large gate molds for bigger parts or hot runner molds for precision in electronic product shells. Hot runner molds are particularly fascinating, enhancing both quality and efficiency with their design intricacies—like molding devices and cooling systems—that fit together like a well-planned dance.
Mold Type | Usage Scenario |
---|---|
Large Gate | Large parts with lower precision needs |
Hot Runner | High-volume production with stringent quality |
Generating Drawings
Creating detailed drawings is where art meets technology. Using software like UG or Pro/E, I transform ideas into precise two-dimensional drawings and three-dimensional models. Every technical requirement—from size to surface roughness—is meticulously marked to ensure that during assembly1, each part fits seamlessly.
Mold Manufacturing Preparation
This stage is like preparing for a grand performance, ensuring everything is ready to meet the demands of precise mold processing. From selecting materials like P20 or H13 steel to preparing auxiliary materials, every choice impacts the final product. I’ve learned that equipment debugging is crucial; ensuring CNC machines are calibrated perfectly to maintain accuracy during processing makes all the difference.
Material | Application |
---|---|
P20 Steel | General purpose for mold bases |
H13 Steel | High-temperature applications |
These steps are more than just technical tasks; they’re a journey towards creating molds that are not only functional but also masterpieces of engineering.
Product analysis is the first step in mold design.True
Product analysis involves understanding requirements like shape and material.
Hot runner molds are used for low-volume production.False
Hot runner molds are used for high-volume production with quality needs.
Why is Material Procurement Vital in Mold Manufacturing?
Ever wondered what truly drives the success behind mold manufacturing? It all starts with material procurement.
Material procurement is essential in mold manufacturing to ensure the availability of suitable materials for each production phase, impacting cost, quality, and design feasibility. This includes selecting, purchasing, and managing materials for mold creation.
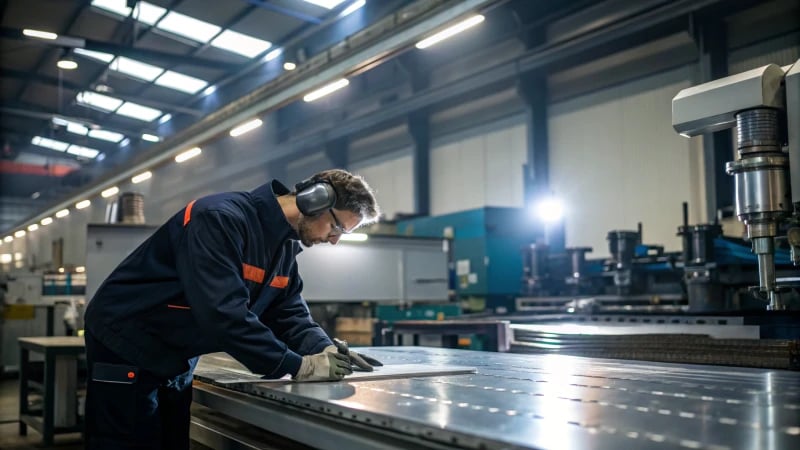
Importance of Material Selection
I remember the first time I had to choose between P20 and H13 steel for a project. It felt like deciding between two equally delicious desserts, each with its own unique benefits. The choice of materials in mold manufacturing isn’t just a technical decision; it’s an art form. Picking the right one can make all the difference in the durability and performance of a mold. For example, P20 steel is like that trusty old car that never breaks down—reliable and durable. Meanwhile, H13 steel stands tall against high temperatures, much like an old friend who’s weathered every storm with you. Understanding these materials’ properties can significantly enhance production efficiency and quality.
For more information on material properties, visit properties of different mold steels2.
Strategic Procurement Planning
Planning procurement is like orchestrating a symphony where every note matters. It’s about forecasting needs and timing purchases so that production never misses a beat. Effective planning considers lead times, supplier reliability, and costs—much like preparing for a big family dinner where timing is everything to ensure everyone leaves satisfied. A well-executed strategy can dramatically reduce downtime, ensuring everything runs smoothly.
Cost Implications
Negotiating with suppliers or opting for alternative materials without sacrificing quality reminds me of those times when you find an incredible deal on your favorite brand. It’s all about being savvy with expenses. Bulk purchasing can lead to significant savings, but it requires a delicate balance, much like keeping a well-stocked pantry without overloading it.
Supply Chain Management
When I think about supply chain management, I imagine it as building a circle of trust among friends. Establishing strong relationships with reliable suppliers ensures timely delivery and quality assurance. It’s like having a backup plan in place for when life’s little surprises hit you out of nowhere—like a diversified supplier network that minimizes risks in times of crisis.
For more insights on supply chain strategies, visit supply chain management techniques3.
Technological Integration in Procurement
Technology in procurement feels like having a personal assistant who knows everything about your schedule and preferences. Utilizing ERP systems can streamline the procurement process by integrating it with other business functions like finance and production. These systems provide real-time data on inventory levels, supplier performance, and order status—empowering informed decisions that enhance operational efficiency.
Learn about ERP systems for manufacturing4 for further details.
Material Type | Common Uses | Benefits |
---|---|---|
P20 Steel | General molds | High machinability |
H13 Steel | High-temperature applications | Thermal resistance |
Beryllium Copper | Injection mold components | Excellent thermal conductivity |
Each aspect of material procurement plays a pivotal role in shaping the efficiency and quality of mold manufacturing, weaving together practicality and creativity to form the backbone of successful production.
P20 steel is used for high-temperature applications.False
P20 steel is typically used for general molds, not high-temperature applications.
ERP systems enhance procurement efficiency in mold manufacturing.True
ERP systems integrate procurement with other functions, improving efficiency.
How Are Mold Parts Processed?
Ever wondered what really goes into creating those intricate mold parts? Let me take you through the journey of transforming raw materials into precision components.
Mold parts are processed using cutting, roughing, finishing, electrode processing, and drilling to ensure precise dimensional accuracy and surface quality.
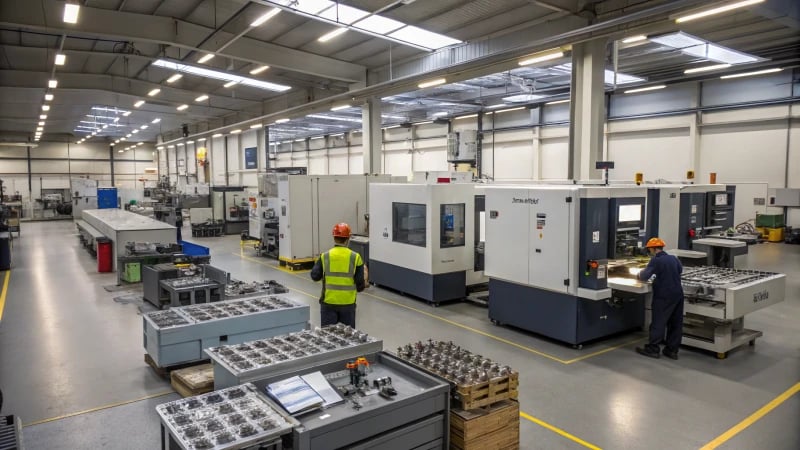
I remember my early days in mold design, where the process seemed like an intricate dance of precision and patience. Each step had its own rhythm and purpose, much like crafting a delicate piece of art.
Cutting Techniques
Cutting forms the foundational step in mold parts processing5. It involves transforming raw material into blanks suitable for further refinement. Materials are carefully selected based on design specifications, then cut to precise measurements.
Material | Application |
---|---|
Steel | General molds |
Copper | Electrodes |
Roughing and Finishing
Once the blanks are ready, roughing removes excess material using CNC machining centers. It leaves a small allowance for finishing, enhancing efficiency.
- Roughing: Quick removal with larger tools.
- Finishing: Precision work with smaller tools ensuring tight tolerances.
Explore more on CNC machining6 if you’re curious about how this all comes together.
Electrode Processing
Electrodes are vital for sections inaccessible by standard machining. High-precision CNC machines create electrodes used in electrical discharge machining (EDM). This technique is essential for intricate details like deep grooves or sharp corners, where conventional tools fall short.
Drilling and Reaming
Drilling creates necessary holes for mounting and cooling. Reaming follows to refine these holes, meeting specific design criteria.
- Drilling: Initial hole creation.
- Reaming: Fine-tuning for precision and surface finish.
Discover how reaming techniques7 enhance mold production.
Comprehensive Mold Design
Effective processing hinges on meticulous mold design8. Designers analyze product specifications, selecting appropriate mold structures like hot runner molds for enhanced quality. The design phase sets the stage for all subsequent processing steps.
Mastering these techniques means achieving superior quality in mold parts processing, meeting both aesthetic beauty and functional precision.
Cutting is the first step in mold parts processing.True
Cutting transforms raw materials into blanks for further processing.
Reaming is used before drilling in mold processing.False
Drilling creates initial holes, followed by reaming for precision.
How Does Mold Assembly Ensure Product Quality?
Have you ever wondered how the pieces of a puzzle come together so flawlessly? In manufacturing, mold assembly is that crucial puzzle piece.
Mold assembly ensures product quality through precise fitting, cleaning, assembling, and debugging of components, resulting in reliable and accurate products.
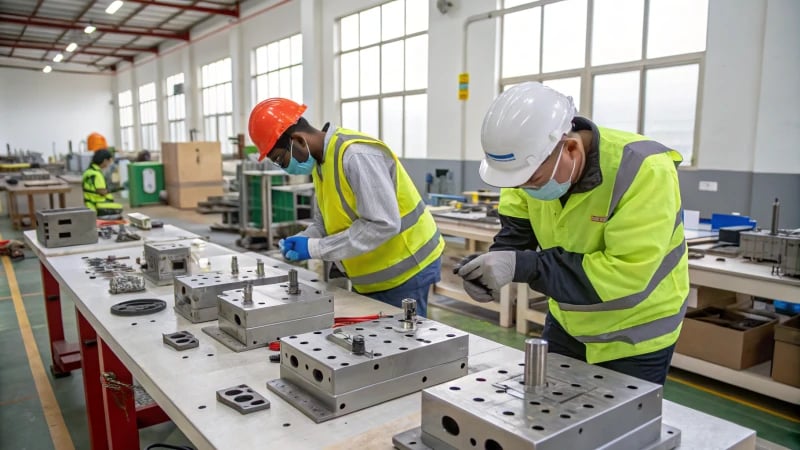
The Importance of Parts Cleaning
I remember the first time I saw a mold being assembled—it was a bit like watching a sculptor at work. Each piece was meticulously cleaned, as if they were preparing an heirloom for display. Removing every trace of oil or debris isn’t just about aesthetics; it’s about ensuring every component fits together perfectly. Just like cleaning up before guests arrive, this step sets the stage for everything that follows.
Component Assembly Techniques
Once everything is spick and span, the real magic begins. Picture a complex 3D puzzle where each piece must align perfectly. I recall working on molds for electronic devices, where precision isn’t just preferred—it’s mandatory. Every core, every cavity is assembled with the utmost care, guided by detailed drawings and precise measurements, ensuring that ejection and cooling systems function without a hitch.
For instance, when assembling molds9 for electronic devices, precision is paramount to ensure proper ejection and cooling systems are in place.
General Assembly Debugging
And then comes the moment of truth: debugging. It’s like rehearsing for a big play. The mold is tested for opening and closing, ejection systems are scrutinized, and cooling flows are verified. I learned early on that if the cooling system fails during this stage, it can lead to defective products—something we all strive to avoid.
Step | Description |
---|---|
Cleaning | Removes impurities to maintain part quality. |
Component Assembly | Parts are aligned according to design specifications. |
Debugging | Verifies functional integrity of the mold. |
Leveraging Technology in Assembly
In today’s world, technology is our ally. Advanced software like UG or Pro/E helps us create precise models, offering a clear blueprint that guides the entire assembly process. This technological advantage not only sharpens accuracy but also anticipates potential issues before they become real headaches.
Using advanced software like UG or Pro/E enhances accuracy and expedites debugging by predicting potential issues early on.
Optimizing with Trial Molds
Trial molds are my safety net—they let me catch mistakes before they spiral into larger problems. By simulating real-world conditions, I can tweak and refine the molds until they’re just right. It’s akin to test-driving a car before you buy it; these trials ensure everything meets the high standards we set for our products.
In conclusion, mold assembly is more than just putting pieces together; it’s an art that blends precision with creativity, ensuring that every product we produce meets the highest quality standards. From automotive parts to consumer electronics, understanding these processes allows manufacturers like us to enhance product reliability and performance across various applications.
For more insights on trial molding practices10, exploring further can reveal how these trials contribute to refining assembly processes.
Cleaning mold parts removes all impurities.True
Cleaning is essential to remove oils and debris, ensuring quality.
Debugging skips testing the cooling system.False
Debugging includes testing cooling systems to prevent defects.
Why Is Mold Debugging and Optimization Crucial?
Ever wondered why some products just seem to fit perfectly, while others feel a bit off?
Mold debugging and optimization are vital to fix defects, enhance production efficiency, and ensure quality in injection molding, saving time and resources by preventing costly errors.
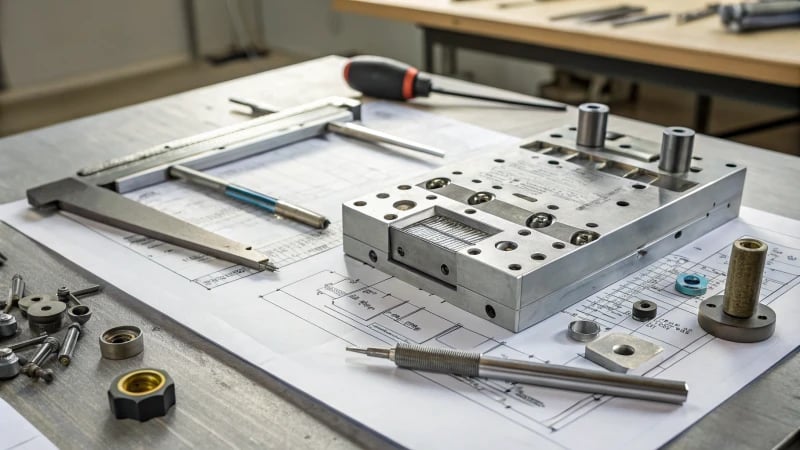
For me, the world of injection molding is like a complex dance where every step counts, and mold debugging is the critical rehearsal. Let me take you back to when I first realized this. It was during my early days in the industry; I was part of a project for a consumer electronics company. We faced unexpected defects in our product trial runs. I remember feeling a mix of frustration and determination as we scrutinized every detail of our mold setup. It was like solving a puzzle, where each piece needed careful examination to fit perfectly.
The Importance of Mold Debugging
Mold debugging became our lifeline. It’s the phase where we put molds to the test, simulating real-world conditions to catch flaws before they spiral into costly errors. During one particular trial mold production, I watched as our team carefully adjusted parameters, akin to fine-tuning a musical instrument. We sought precision in dimensional accuracy and surface quality, ensuring our products met the design blueprints.
- Trial Mold Production: We immersed ourselves in these trials, using the same materials and settings as actual production, aiming for perfection.
- Problem Analysis: I learned to dissect issues like flash and dimensional discrepancies, tweaking settings such as mold clamping force to bring our designs to life with precision.
Enhancing Efficiency Through Optimization
Optimization is the cherry on top of our debugging efforts. It’s where I discovered the true art of balancing performance indicators like appearance and cycle time with production costs. I’ll never forget the eureka moment when we successfully reduced waste and improved efficiency without compromising quality—an achievement that saved us significant resources.
- Mold Performance Indicators: Final debugging ensures every detail meets our high standards, turning our molds into reliable tools for consistent production.
- Production Cost Management: Fine-tuning mold operations became a game-changer, enhancing injection molding efficiency11 while cutting down on unnecessary expenses.
Techniques for Effective Mold Debugging
Over time, I honed my approach to mold debugging through these steps:
Step | Description |
---|---|
Trial Mold | Perform initial testing using production-like conditions to identify potential issues early. |
Problem Analysis | Analyze defects encountered during trials to inform necessary adjustments. |
Final Debugging | Conduct multiple trials to refine the mold for stable production. |
Through detailed analysis and iterative testing, we’ve optimized molds for peak performance, ensuring they align with the highest production standards. For those interested in diving deeper, techniques like mold flow analysis12 offer a predictive edge by simulating the injection process to catch issues before they arise.
Reflecting on my journey, I’ve come to appreciate how mold debugging and optimization are not just technical processes—they’re essential practices that breathe life into designs, turning concepts into reliable products that meet even the highest expectations.
Mold debugging identifies defects like flash and dimensional deviations.True
Mold debugging helps detect issues such as flash or dimensional errors during trials.
Optimization increases production costs by increasing waste and energy use.False
Optimization reduces waste and energy use, lowering production costs.
What does mold acceptance and delivery entail?
Navigating the world of mold acceptance and delivery is like embarking on a detailed adventure—every step matters.
Mold acceptance and delivery involve setting standards, thorough inspections, and ensuring quality criteria are met, ensuring mold reliability and efficiency before client delivery.
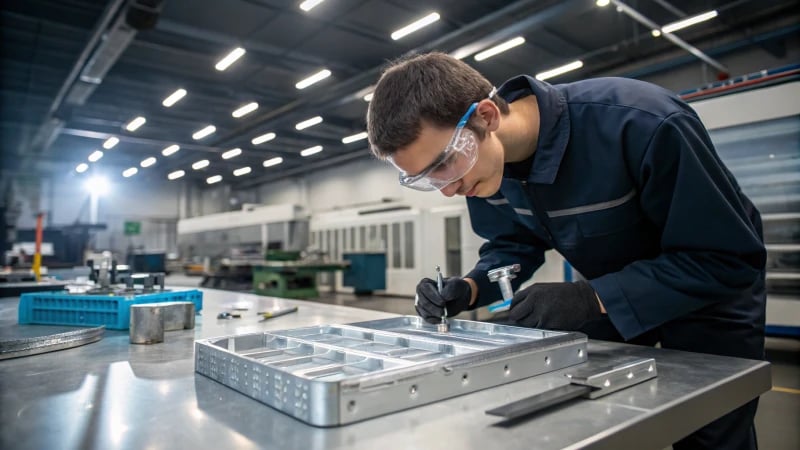
Establishing Acceptance Standards
I remember the first time I sat down with a client to hash out acceptance standards for their molds. It felt like setting the rules of a game where both sides wanted to win. Establishing these standards is crucial because they define what’s acceptable in terms of product accuracy, appearance, and longevity. Imagine designing molds for automotive parts; every little detail, like dimensional tolerances13, needs to be spot-on to ensure everything fits together like a dream.
Conducting Acceptance Inspections
The inspection phase reminds me of a detective at work, seeking out anything that doesn’t belong. These inspections include everything from scrutinizing surfaces for defects to measuring dimensions with precision tools. I’ve learned that even the smallest inconsistency can snowball into a major issue down the line. So, hardness inspections and non-destructive testing become my trusty sidekicks in ensuring no internal flaws slip through.
Example of Acceptance Inspection Components
Inspection Type | Description |
---|---|
Visual Inspection | Check for surface defects |
Dimensional Measurement | Verify all dimensions meet standards |
Hardness Inspection | Ensure material strength |
Flaw Detection | Identify internal defects |
Trial Production Verification
Conducting a trial run is like taking a new car for a spin before buying it. It’s my way of ensuring that the mold performs as expected under real-world conditions. These trial runs are essential because they help me spot potential issues that might not be apparent during initial checks.
Delivery and Usage Training
Once all inspections are cleared, delivering the mold feels like sending off a prized creation. But it’s not just about dropping it off—it’s about ensuring the clients know how to use and maintain it properly. I always emphasize comprehensive training sessions because they’re key to preventing any operational hiccups that could lead to premature wear or damage.
By meticulously following these processes, I can confidently deliver molds that not only meet but often exceed client expectations, ensuring smooth and efficient production cycles. Technical documents14 are my silent partners in this journey, guiding users through every aspect of mold operation and maintenance.
Dimensional accuracy is not part of acceptance standards.False
Dimensional accuracy is a key part of mold acceptance standards.
Trial production helps identify issues not seen in inspections.True
Trial runs reveal performance issues under real conditions.
Conclusion
The injection mold manufacturing process involves stages from design to delivery, ensuring high-quality plastic components through meticulous analysis, material selection, processing, assembly, debugging, and acceptance inspections.
-
Accurate assembly ensures efficient operation by aligning all components correctly, reducing errors in production. ↩
-
Explore how P20 and H13 steels enhance mold durability and machining efficiency. ↩
-
Discover strategies to strengthen supplier relationships and mitigate risks. ↩
-
Learn how ERP systems integrate procurement with business operations for efficiency. ↩
-
Learn how cutting techniques set the foundation for precise mold parts processing. ↩
-
CNC machining centers play a critical role in roughing and finishing processes. ↩
-
Reaming enhances the precision and quality of drilled holes in mold production. ↩
-
Understand why thorough mold design is crucial for successful parts processing. ↩
-
Explore detailed methods and technologies for precision assembly in electronic mold manufacturing. ↩
-
Discover how trial molding identifies and corrects defects before mass production. ↩
-
Learn techniques to boost efficiency in your molding process. ↩
-
Explore how mold flow analysis predicts and prevents production issues. ↩
-
Learn about specific dimensional tolerances required for automotive parts molds to ensure proper fit and function. ↩
-
Understand why technical documents are crucial for guiding users in mold operation and maintenance. ↩