Have you ever thought about how quickly your favorite gadgets get produced? In manufacturing, speed doesn’t just relate to time – it’s a real game-changer.
Injection mold filling speeds differ because of equipment, material traits and design. Small machines inject between 5 and 20 cm per second. High-speed machines inject as fast as 500 cm per second. Material thickness and product size are very important in finding the best speeds.
I recall standing next to a loud injection molding machine for the first time, amazed at how quickly it transformed raw materials into shiny electronic cases. The machine’s work depended on its screw size and stroke, affecting how fast it could produce items. It moved with accuracy and strength.
The kind of plastic used also mattered. I discovered that plastics like polypropylene allowed quicker injection speeds. In contrast, materials like polycarbonate needed careful handling to prevent any problems. This knowledge was crucial when we had to create thin-walled products, pushing speed while keeping quality.
As I explored more, I realized the product’s size and shape greatly influenced injection speeds. Creating thin-walled objects needed fast fills to avoid defects, whereas bigger items required a slower pace to stop cracks caused by stress. Each project rewarded me with a new lesson on balancing speed with quality. It is something I continue to improve.
High-speed machines reach 300-500 cm/sec injection speeds.True
High-speed injection molding machines for precision components achieve these speeds.
All plastics have the same injection speed range.False
Different plastics have varying viscosities, affecting their injection speeds.
- 1. What Factors Influence Injection Mold Filling Speed?
- 2. How Does Equipment Performance Affect Injection Speed?
- 3. Why Do Material Properties Matter in Injection Molding?
- 4. How Do Product Size and Shape Affect Molding Speed?
- 5. How Can You Optimize Injection Speed for Better Quality?
- 6. Conclusion
What Factors Influence Injection Mold Filling Speed?
Some injection molds fill faster than others. The reason is a mix of machine power, material selection and product design details. These factors play a vital role. Machine performance greatly influences how quickly the mold fills. Material choice also affects speed. Design intricacies can change filling time, too. Each part contributes to the final outcome.
The speed of filling an injection mold depends on how the equipment performs, the size of the screw, how thick or thin the material is and how the product is designed. Faster filling happens with top-quality machines, materials that flow easily and designs with very thin walls.
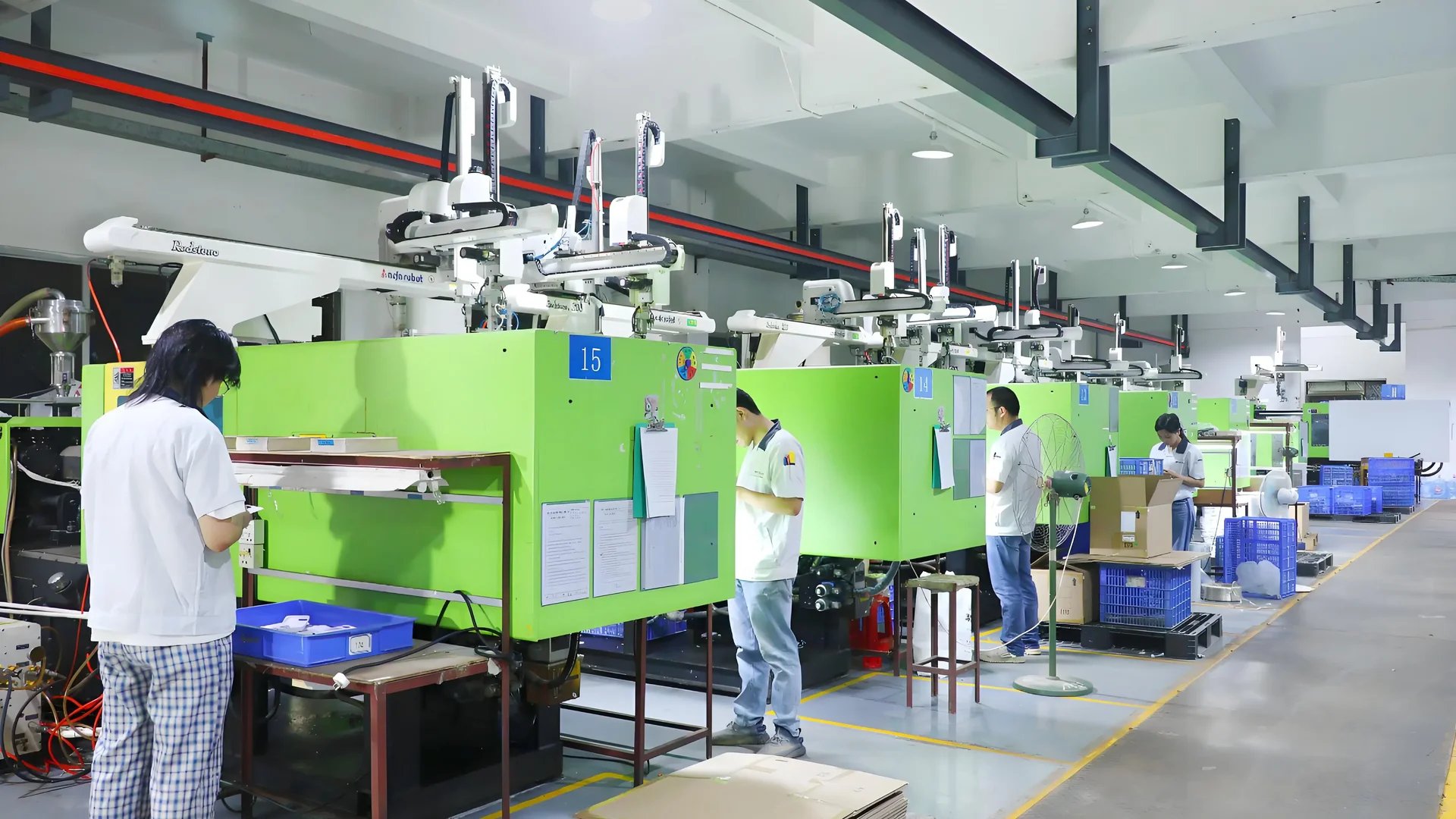
Equipment Factors
Performance of Injection Molding Machine
After years spent in manufacturing, I really value the mix of factors that set mold filling speed. It’s like conducting a symphony where each part is important. The capabilities of an injection molding machine significantly impact filling speed. I recall an old but dependable machine beside me. It could handle toy production at 20 cm/sec. Then I worked with a fast, advanced model moving at 500 cm/sec, creating parts for new electronics easily. This big difference taught me that machine ability greatly influences how efficiently we produce.
Machine Type | Speed Range (cm/sec) |
---|---|
Ordinary Small Machines | 5 – 20 |
High-end Industrial-grade | 300 – 500 |
Screw Diameter and Stroke
This is like Goldilocks searching for just right. Picking the perfect screw size and stroke really matters. A larger screw diameter increases injection volume but may require higher speeds to maintain consistent filling times. Adjusting injection speed1 involves finding balance to stop blockages.
Material Factors
Plastic Material Properties
I’ve fought with stubborn materials. Different materials exhibit varying viscosities. Plastics like polyethylene (PE) and polypropylene (PP) flow smoothly at higher injection speeds (10 – 100 cm/sec). High-viscosity plastics like polycarbonate (PC) need slower speeds to prevent overheating or air gaps – roughly 5 – 30 cm/sec.
Material Type | Viscosity Level | Speed Range (cm/sec) |
---|---|---|
PE/PP | Low | 10 – 100 |
PC | High | 5 – 30 |
Product Factors
Product Size and Shape
Creating thin products taught me to use high speeds – between 100 to 300 cm/sec2 – to avoid errors. However, larger designs with thick walls require slowing down to prevent stress and bending.
This table illustrates the relationship between product characteristics and speed:
Product Type | Wall Thickness (mm) | Speed Range (cm/sec) |
---|---|---|
Thin-walled | 0.5 – 1 | 100 – 300 |
Thick-walled | Varied | 10 – 50 |
Understanding these aspects is truly powerful in mold design3. It lets us decide wisely so production stays efficient and high in quality. Knowing each detail is important to mastering mold design.
High viscosity plastics require slower injection speeds.True
High viscosity materials like PC need slower speeds to avoid defects.
Thin-walled products need lower injection speeds.False
Thin-walled products require higher speeds to prevent short shots.
How Does Equipment Performance Affect Injection Speed?
Sometimes, people think about why some molded items look perfect and others don’t. Equipment performance really impacts the speed of the injection process.
The performance of injection molding machines is very important for determining speed. Important details such as the type of machine, the size of the screw and the characteristics of the plastic greatly influence both speed and the quality of the product.
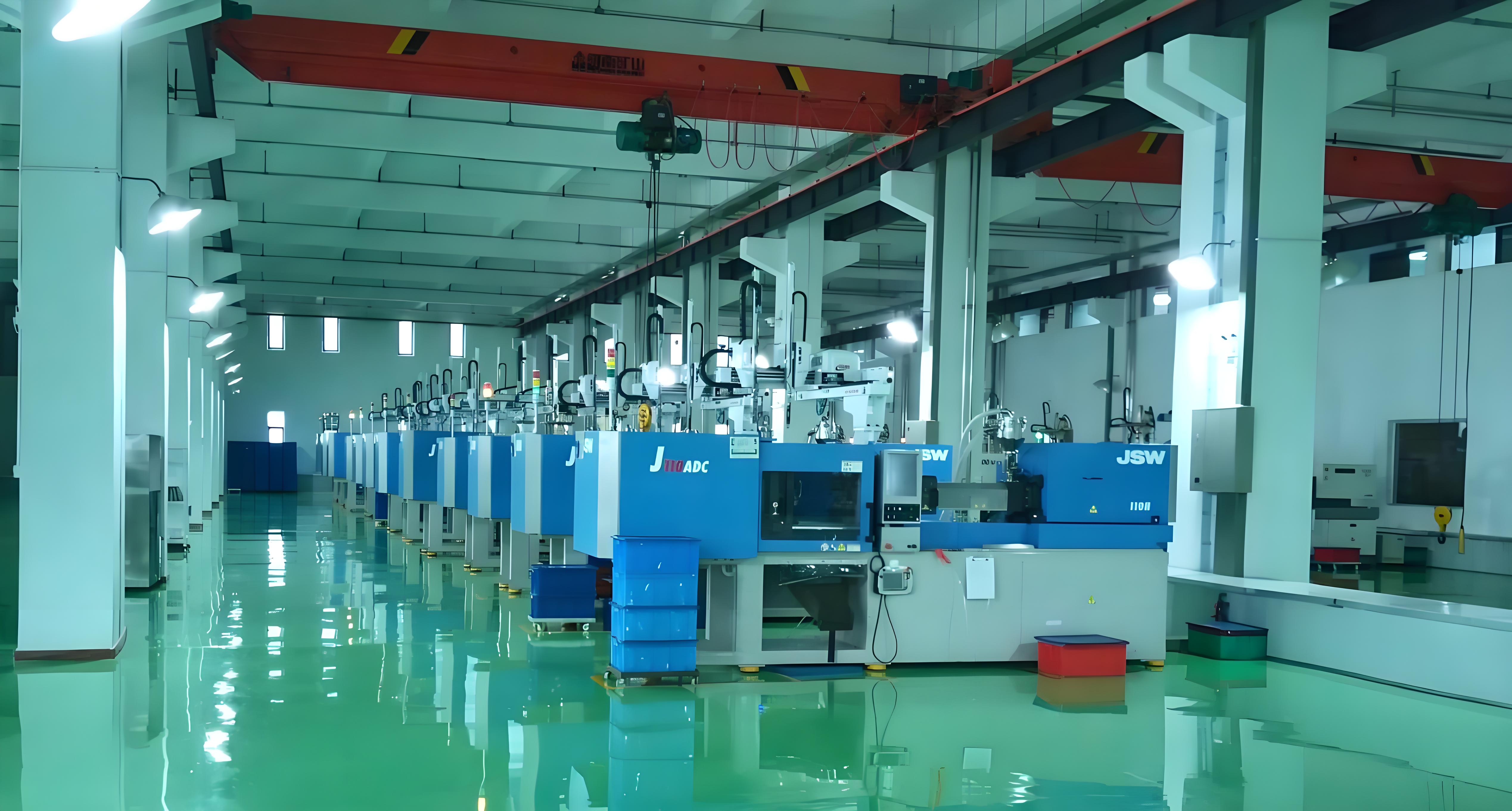
Impact of Injection Molding Machine Performance
I remember seeing a busy injection molding machine for the first time. Watching it create detailed parts with great accuracy was amazing. Its performance determines the pace of the injection process. Picture a small machine producing tiny plastic toys; its speed ranges from 5 to 20 cm/sec. But industrial machines race at speeds reaching 500 cm/sec, especially those designed for precision4. It’s like comparing a slow bicycle ride to a speedy race car.
Role of Screw Diameter and Stroke
Let’s talk about screw diameter. Imagine two machines together – one with a thick 50mm screw, the other with a slim 30mm screw. The bigger screw injects more plastic per shot due to its larger size. However, achieving similar speeds may require higher operational speeds5 due to the increased volume.
Screw Diameter | Injection Speed Range |
---|---|
30mm | Moderate |
50mm | Higher for same volume |
Influence of Material Properties
Material choice fascinates me. Low viscosity materials, such as polyethylene (PE) and polypropylene (PP), flow smoothly through molds, reaching speeds of up to 100 cm/sec. However, thicker materials like polycarbonate (PC) require slowing down to prevent overheating and bubbles, avoiding issues like material scorching6. It’s like using different kinds of oil when cooking, as each oil has a unique smoke point.
Importance of Product Size and Shape
Size plays a role too! Thin-walled objects need a quick injection burst – up to 300 cm/sec – to fill every part perfectly. Meanwhile, thick-walled products require a gentle approach to avoid warps or cracks.
Product Type | Recommended Speed |
---|---|
Thin-walled | 100 – 300 cm/sec |
Thick-walled | 10 – 50 cm/sec |
Knowing these factors not only helps improve quality but also turns the process into a well-orchestrated symphony – where every part contributes to harmony.
High-speed machines reach 300-500 cm/sec injection speed.True
High-end machines for precision components achieve these speeds.
Polycarbonate needs higher injection speeds than polypropylene.False
Polycarbonate requires lower speeds to avoid scorching.
Why Do Material Properties Matter in Injection Molding?
Have you ever asked yourself why picking the correct material in injection molding seems like a chess match?
In injection molding, material properties play a crucial role. They help decide which plastics suit the task best. They also decide flow, temperature and speed settings. The strength of the finished product depends on these properties. Durability and finish also rely on them. These factors are important for successful manufacturing.
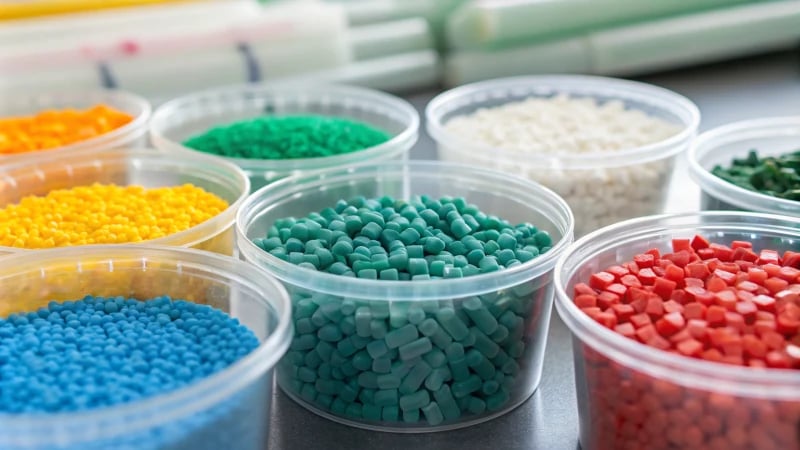
The Importance of Material Properties
Starting with injection molding felt like diving into a tough and technical world. Decisions rested on mysterious "material properties." Only after some errors did I fully grasp their critical role in perfecting the process.
Choosing the correct material isn’t just a simple step; it’s the key that opens the door to success or failure in manufacturing. Viscosity, melting point, and thermal conductivity are essential. They act like secret ingredients that influence how materials behave under injection molding conditions7. I learned this when some parts ended up warped due to my neglect of viscosity’s role.
For instance, working with materials like polyethylene (PE) allows high-speed injection, ideal for making many items quickly. However, with polycarbonate (PC), patience is necessary to avoid scorching.
Material | Viscosity | Injection Speed Range (cm/sec) |
---|---|---|
Polyethylene | Low | 10 – 100 |
Polycarbonate | High | 5 – 30 |
Equipment Factors Impacting Material Selection
Finding the right equipment feels akin to picking the perfect running shoes. In the beginning, my small machine struggled with anything beyond low-viscosity plastics due to its speed limits. Large industrial machines handle tougher materials more easily.
The screw diameter and stroke revealed a lot about material compatibility. Bigger screws inject more material but need higher speeds to match smaller screws. Balancing these factors was puzzling but vital for choosing the right material for my machine.
Product Design Considerations
Product size and shape need careful planning. Thin-walled products demand faster injection speeds to fill molds and avoid flaws, a lesson learned from defected containers.
Meanwhile, large, thick items need a softer approach with slower speeds to avoid stress.
Product Type | Injection Speed Range (cm/sec) |
---|---|
Thin-walled containers | 100 – 300 |
Thick-walled shells | 10 – 50 |
Understanding these dynamics helps me design for both beauty and function while fitting production scales8. This all-around strategy not only helps manufacturing but also improves product quality.
How material properties interact with machine abilities is always on my mind early in design. Matching the material with the machine’s strengths and product needs has prevented costly errors and improved my product’s performance.
High viscosity plastics require lower injection speeds.True
High viscosity plastics like PC need slower speeds to avoid defects.
Thin-walled products use lower injection speeds than thick-walled ones.False
Thin-walled products require higher speeds to fill mold quickly.
How Do Product Size and Shape Affect Molding Speed?
Do you ever think about how a product’s size and shape could really speed up or slow down the molding process?
Product size and shape greatly affect molding speed. Thin-walled designs need fast speeds to fill molds fully. Thick-walled structures need slow speeds to avoid stress and defects. This is very important.
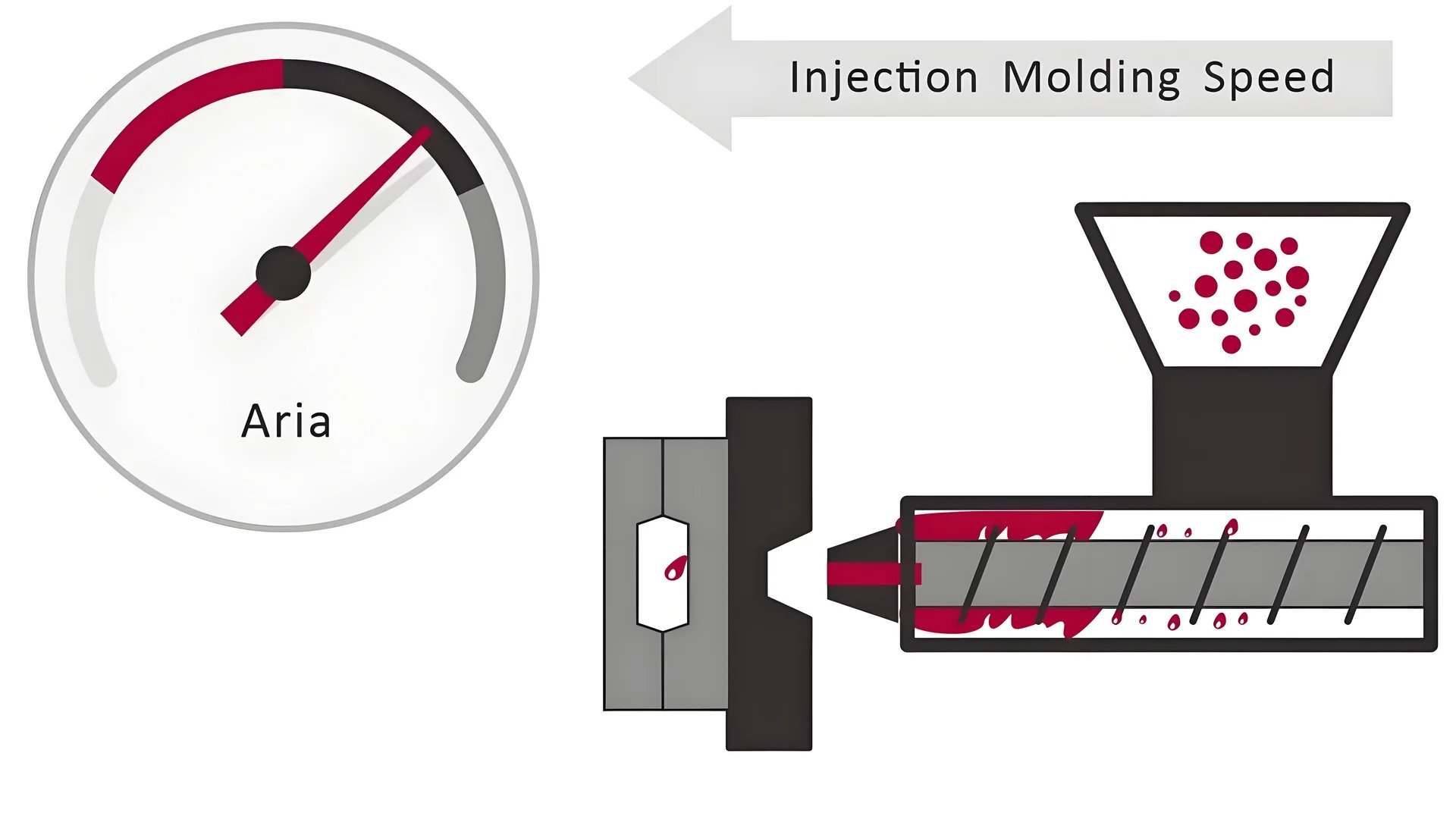
Understanding Product Size and Shape
The dimensions of a product9 play a crucial role in determining the injection molding speed. Thin-walled designs, which are typically found in plastic containers or electronic casings, demand higher speeds. This ensures the molten plastic fills the entire mold cavity quickly, avoiding defects like short shots.
Conversely, large and thick-walled products require lower injection speeds. If injected too quickly, the internal stress can lead to deformation or cracking, compromising the product’s integrity.
Equipment Influence on Molding Speed
The performance of injection machines10 directly affects how different sizes and shapes are molded. A high-speed injection molding machine can achieve speeds up to 500 cm/sec, particularly beneficial for thin-walled designs. Machines with larger screw diameters also influence speed, necessitating adjustments based on product size and shape.
Machine Type | Suitable for | Injection Speed Range |
---|---|---|
Ordinary Small Machine | Small Plastic Toys | 5 – 20 cm/sec |
High-speed Machine | Precision Components | 300 – 500 cm/sec |
Material Properties and Product Design
Different materials react uniquely under various molding speeds. For example, polyethylene (PE) and polypropylene (PP) allow for higher speeds due to their lower viscosity. However, materials like polycarbonate (PC) require slower speeds to prevent issues such as scorching.
The choice of material11 is essential when designing a product, as it dictates the optimal molding speed for ensuring quality and precision. For instance, PP materials might be molded at 10 – 100 cm/sec, while PC requires around 5 – 30 cm/sec.
Practical Examples
In practice, producing thin-walled plastic containers with a thickness of 0.5 – 1mm might need speeds of 100 – 300 cm/sec to ensure proper fill and quality. On the other hand, crafting large, thick-walled plastic shells might be executed at speeds closer to 10 – 50 cm/sec to mitigate potential defects.
By understanding these factors, manufacturers can optimize their processes, ensuring efficiency and maintaining high-quality standards throughout production.
High viscosity plastics require lower injection speeds.True
High viscosity materials like PC need lower speeds to prevent defects.
Thin-walled products need lower injection speeds.False
Higher speeds are required for thin-walled products to avoid defects.
How Can You Optimize Injection Speed for Better Quality?
Some injection-molded products have a perfect look. The secret is adjusting injection speed. Yes, speed matters.
Adjust injection speed for quality by concentrating on machine performance, screw diameter and material properties. Tweaking these elements reduces defects. Production efficiency increases with these changes.
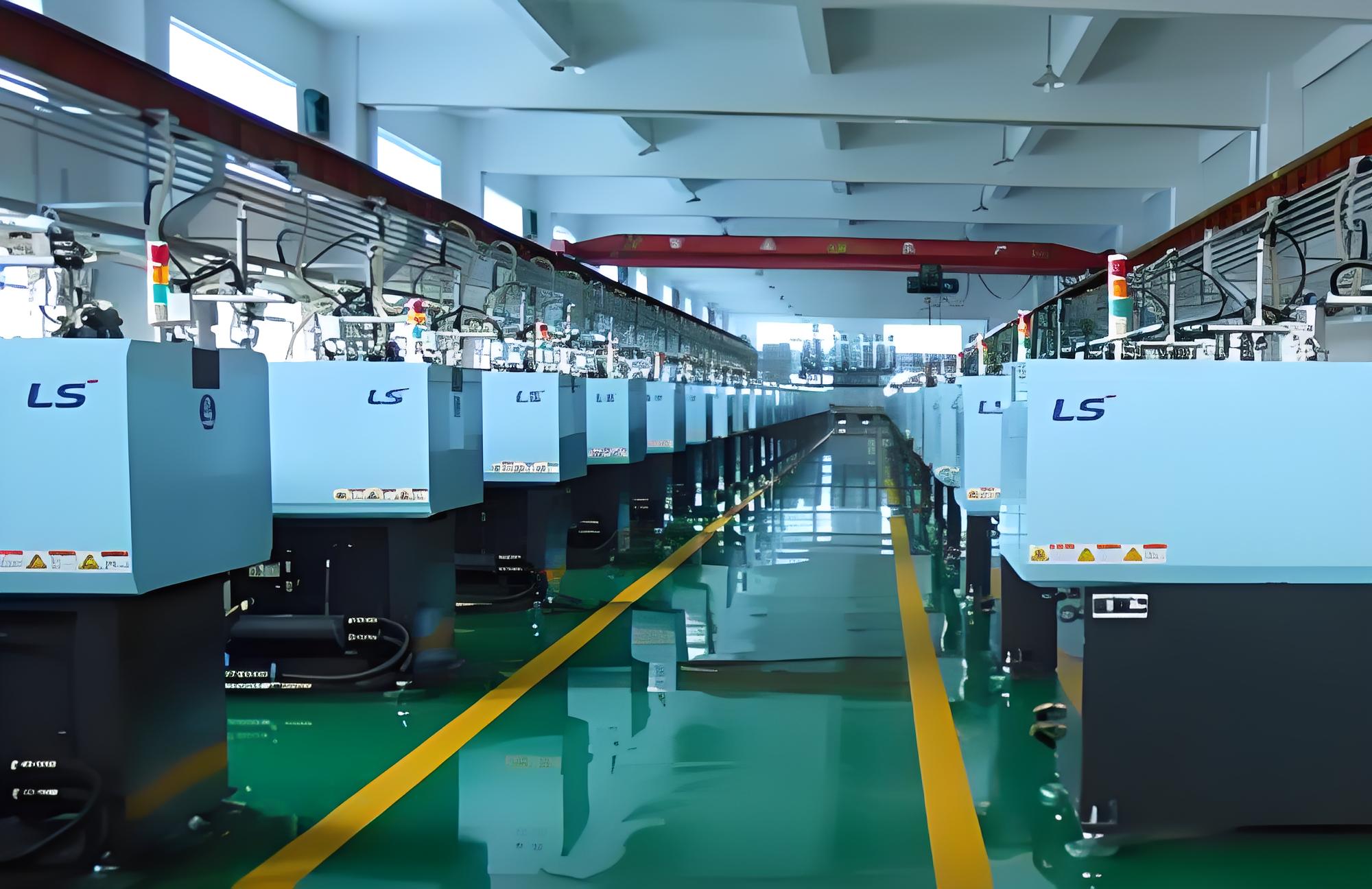
Understanding Equipment Factors
Performance of Injection Molding Machines
The machine type matters a lot for injection speed. Imagine changing your car from a simple sedan to a racing car. You notice the difference in speed. Basic machines are like sedans, running between 5 to 20 cm/sec. In contrast, high-speed machines are the Ferraris, going at 300 to 500 cm/sec. Picking the right one is very important for raising production efficiency12.
Screw Diameter and Stroke
Let’s talk about screws. It’s like choosing a thick or thin straw for your milkshake. A bigger screw size means more volume per turn. However, you must adjust the speed for smooth flow. A 50mm screw needs more speed than a 30mm screw to keep the same injection volumes. Adjusting these settings helps get the best output13.
Analyzing Material Factors
Plastic Material Properties
Materials act differently under pressure – like people! Low viscosity materials, like PE and PP, handle stress well and move fast (10-100 cm/sec). High viscosity materials, like PC, need slower speeds (5-30 cm/sec) to avoid overheating. Knowing these differences helps maintain quality control14.
Evaluating Product Factors
Product Size and Shape
Product size and shape affect speed too. Think about painting a big wall versus a small canvas; each needs a different method. Thin items require high speeds (100-300 cm/sec) for quick filling. Thicker products need lower speeds (10-50 cm/sec) to lessen stress and prevent bending. Adapting speed to these needs is very important for improving mold design15.
Practical Tips for Optimization
- Calibrate Machines Regularly: Like tuning a musical instrument, keeping equipment in good condition makes everything run smoothly.
- Test Different Materials: Try materials that work well with your machine.
- Analyze Product Design: Aligning design with machine and material capabilities is important for having the best results16.
Table: Common Injection Speeds by Material Type
Material Type | Speed Range (cm/sec) |
---|---|
Polyethylene (PE) | 10 – 100 |
Polypropylene (PP) | 10 – 100 |
Polycarbonate (PC) | 5 – 30 |
Glass-Fiber Plastics | Variable |
Optimizing injection speed isn’t simply about small changes; it’s about understanding how each part of your process connects. By sharing my thoughts and experiences, I hope you’ll discover new ways to improve your approach and get that perfect result every time.
High-speed machines can inject at 300-500 cm/sec.True
High-end industrial-grade injection molding machines achieve these speeds.
Thick-walled products require high injection speeds.False
Thick-walled products need lower speeds to avoid stress issues.
Conclusion
Injection mold filling speeds vary based on machine performance, material properties, and product design, ranging from 5 to 500 cm/sec for optimal quality and efficiency in production.
-
Explore how screw dimensions influence the speed and consistency of mold filling. ↩
-
Learn how machine capabilities can enhance production efficiency. ↩
-
Discover why mold design is crucial for efficient production processes. ↩
-
Explore how high-speed machines impact production quality and efficiency. ↩
-
Learn how screw diameter adjustments optimize injection speed. ↩
-
Discover methods to prevent defects like material scorching. ↩
-
Explore how material properties influence injection molding processes, affecting product quality and efficiency. ↩
-
Understand how selecting materials impacts large-scale production efficiency and output quality. ↩
-
Explore how different product dimensions influence the speed of the molding process, affecting efficiency and quality outcomes. ↩
-
Learn about the relationship between machine capabilities and their effect on molding speed for various product designs. ↩
-
Understand how selecting different materials can alter the required injection speed for optimal manufacturing results. ↩
-
Understanding machine types helps optimize injection speed for better production results. ↩
-
Exploring screw parameters can improve mold efficiency and product quality. ↩
-
Learn how viscosity affects speed to prevent defects like scorching. ↩
-
Tailoring speed to product dimensions avoids stress and enhances quality. ↩
-
Selecting the right material optimizes machine performance and product quality. ↩