Have you ever thought about how your favorite plastic items come into being? Everything begins with injection molds.
An injection mold begins its journey with product analysis, design, manufacturing and testing. Every stage plays a key role in crafting molds that meet quality and production standards. Each stage is very important.
I first jumped into the world of mold design and discovered endless possibilities. Each step in developing an injection mold leads to the creation of perfect plastic pieces. Picture a sleek smartphone case or a sturdy toy.
The journey kicks off with product analysis and design planning. I sit with a cup of coffee and learn about every detail of the product. Understanding each curve and corner helps me create detailed engineering drawings using 3D software. I imagine how the final product feels in someone’s hands.
Then, the mold structure design comes next. I feel like an architect designing the blueprint for a mold that shapes the future. Choices like the number of cavities and the cooling system are important because they affect the final product quality. A single detail can really change everything.
We proceed to drawing and review. I double-check everything carefully. It’s like proofreading a novel to ensure no errors exist before moving ahead.
In mold manufacturing and processing, excitement grows. It’s thrilling to watch designs turn into steel molds with precision machines. It’s an incredible transformation.
Finally, the trial mold and acceptance stage happens. It’s similar to a dress rehearsal. I tweak and adjust until it all fits perfectly.
I save everything in data organization and archiving because each project teaches valuable lessons. These records become important for future designs. Learning new skills and seeing ideas come to life really satisfies me. I love this process.
Mold kernel design affects product quality.True
The mold kernel's design directly impacts the product's molding quality.
Shrinkage rate is irrelevant in mold design.False
Shrinkage rate is crucial for accurate sizing in mold design.
- 1. How Do I Conduct Product Analysis for Injection Molding?
- 2. How Does Mold Structure Design Impact Production Efficiency?
- 3. Why is accurate engineering drawing transformation essential?
- 4. What Are the Best Practices for Mold Manufacturing and Processing?
- 5. What’s the Inside Scoop on Mold Trial and Acceptance?
- 6. Why is Data Organization Crucial After Mold Development?
- 7. Conclusion
How Do I Conduct Product Analysis for Injection Molding?
Have you ever thought about how injection molding turns ideas into real things? Let’s explore the crucial steps that help your creative vision change into perfect, working products.
To analyze a product for injection molding, focus on how the design works. Look at how materials behave. Plan how to build molds. Measure everything carefully. Check how much materials shrink. Understand any problems in production. This helps to improve the molding process.
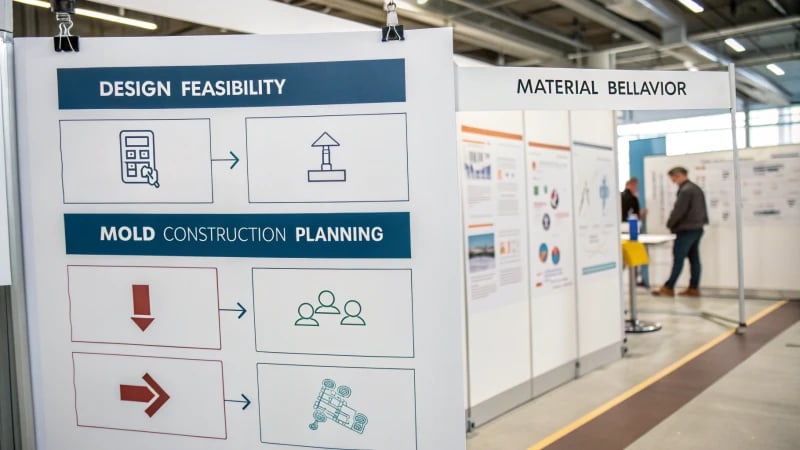
Product Analysis and Design Planning
When I entered the world of injection molding, a comprehensive product analysis1 seemed like solving a tricky puzzle. Understanding design details felt crucial. This meant knowing how mold pieces fit and where parting lines belong. Such analysis helps molding happen smoothly.
I spent hours turning designs into detailed 3D engineering drawings with software tools. Breathing life into these designs was thrilling. Every line and curve had to be just right. These blueprints served as the starting point for creating molds tough enough for the production process, capturing every minute detail necessary for successful production.
Understanding Shrinkage Rates
Material behavior stands out as a captivating part. My experience with shrinkage rates astonished me. Each material reacted differently after cooling, influencing how designs are scaled.
Material Type | Typical Shrinkage Rate |
---|---|
ABS | 0.4% – 0.8% |
Polyethylene | 1.5% – 3% |
Predicting the final product’s look became possible with this knowledge, ensuring dimensional accuracy and helping avoid costly post-production adjustments.
Mold Structure Considerations
Designing the mold structure resembled a strategic chess game. The arrangement of products within a mold should account for the number of cavities, mold orientation, and injection points. Every decision impacted quality and efficiency.
Choices like core extraction mechanisms, such as sliders or angled ejectors, enable smooth removal of complex parts post-molding.
The cooling system design held great importance; efficient cooling impacts both quality and speed of production. I once tried spiral cooling pathways—the quality and speed improvements delighted me.
Options include straight-through or stepped cooling pathways, each offering unique benefits depending on the mold design2.
Troubleshooting Potential Challenges
Troubleshooting might sound scary, yet it spurred creativity in addressing challenges such as air entrapment or uneven filling during injection molding.
An effective exhaust system design mitigates these issues by facilitating air release without compromising material integrity through strategically placed vents to optimize airflow during the injection phase.
My mentor demonstrated how a well-planned exhaust system uplifted product quality—important lessons linger with me today.
Tip: Regularly assess potential mold defects3 like sink marks or warping early in the design phase to preemptively address them through design adjustments or process parameter tweaks.
This proactive step saves precious time and resources.
Incorporating Feedback Loops
Feedback loops form a crucial part of my work in continuous improvement integral to successful injection molding.
Incorporate feedback from initial trials into subsequent design iterations to refine both product and mold designs—aligning with lean manufacturing principles brings optimal results.
Detailed records from each stage serve as valuable references for future projects and aid in troubleshooting during production scaling.
In conclusion, effective product analysis in injection molding requires meticulous attention to detail at each step—from understanding material behavior to perfecting mold design—to enhance production quality and efficiency while maintaining cost-effectiveness across diverse applications.
Product analysis includes determining mold parting line.True
Determining the mold parting line is a key part of product analysis.
Mold embryo supports and fixes the mold kernel.False
The mold embryo supports and fixes the mold nut, not the kernel.
How Does Mold Structure Design Impact Production Efficiency?
Picture adjusting your mold design perfectly, then seeing production times decrease and expenses fall sharply. Curious?
Mold structure design very significantly influences production efficiency. It allows for smooth material flow. It enables optimal cooling. Mold structure also supports efficient ejection processes. Carefully designed molds shorten cycle times. They really reduce defects. Manufacturing costs decrease as well. Lower costs contribute to higher productivity.
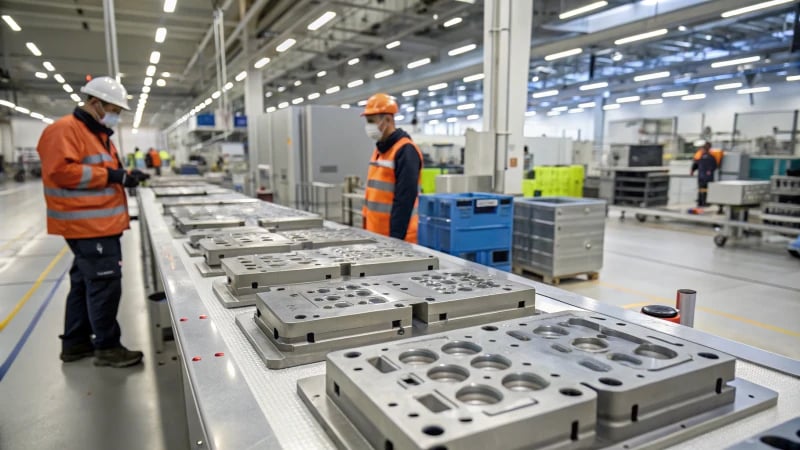
Key Parts of Mold Structure Design
Mold design has many details. Each one affects the whole production process. Let’s explore the key parts that may help or hurt your efficiency goals.
Product Layout
A few years ago, I worked on a project where changing the product layout in the mold had a huge impact on our cycle times4. Arrangement and number of cavities were like a tricky puzzle. Uniform material spread reduced waste and improved quality. It was a big change for us.
Mold Core Design
The mold core is like its heart. Heat dissipation and pressure spread greatly influence product uniformity. Crafting an efficient core design5 has always been crucial to ensure each batch meets quality standards. It’s very important.
Cooling Design System
In my experience, designing a good cooling system is essential. I tested a spiral cooling setup once, which greatly reduced our cycle times. Various waterway styles, like spiral or stepped, significantly improve cooling speed and product uniformity.
Cooling Style | Advantages |
---|---|
Straight-through | Simple design, easy maintenance |
Spiral | Even temperature distribution |
Stepped | Optimizes cooling for complex shapes |
Ejector Design System
Preventing product damage during ejection is crucial. Choosing the right method, such as air ejectors6 or push plates, protects product shape and maintains short cycle times. I’ve felt this challenge personally.
Exhaust Design System
Designing the exhaust system felt like solving a puzzle at first. Proper exhaust slot placement avoids defects like burn marks or incomplete fills. This knowledge has helped improve mold performance7 over time.
Influence on Production Efficiency
Each part of mold design contributes in its own way to production efficiency. Improving these parts can increase productivity and reduce costs. Advanced simulation tools probably provide insights into possible enhancements.
Using software like CAD8 has been very helpful for carefully planning and testing mold designs before production begins, ensuring all parts work together to achieve desired efficiency results.
Product analysis ensures mold design feasibility.True
Analyzing the product helps identify potential issues in mold design.
Cooling system design doesn't affect production efficiency.False
Proper cooling system design is crucial for efficient production.
Why is accurate engineering drawing transformation essential?
Ever looked at a blueprint and wondered how it turns into a real object? Accurate engineering drawing transforms ideas into reality. This process really brings imagination to life. Blueprints become products. Yes, real products.
Accurate engineering drawing transformation is vital. Design specifications turn into clear plans through this process. Errors decrease as a result. High-quality manufacturing outcomes follow. This exactness keeps things consistent. Specifications are met. Teams communicate well when precision is a priority.
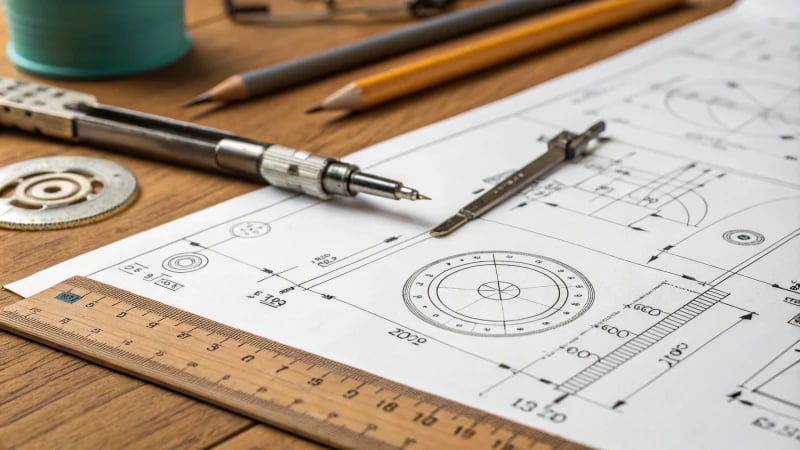
The Role of Engineering Drawings in Manufacturing
Engineering drawings serve as the blueprint for manufacturing processes. These documents translate complex designs9 into understandable guidelines for engineers and technicians. Precise transformation of these drawings ensures that each dimension, specification, and component is accurately represented.
Key Aspects of Accurate Transformation
-
Dimensional Accuracy: Imagine building a puzzle where pieces don’t fit—it’s really frustrating. Proper dimensional scaling works like ensuring each puzzle piece is the right shape. Accurate sizes help components fit together without errors or the need for costly fixes.
Aspect Importance Dimensional Accuracy Ensures component compatibility Material Specification Guides appropriate material selection -
Material Specifications: Selecting the right material is similar to choosing the best fabric for a custom suit. Knowing the material properties and correctly adding this information to drawings is vital. It helps pick materials, affecting how strong and reliable the final product is.
Impact on Injection Mold Development
Working on injection mold development feels like assembling a complex puzzle. Here, precise drawing transformation is key:
-
Product Analysis: Engineers analyze details such as mold parting lines and cavity arrangements, predicting manufacturing issues before they happen.
-
Design Planning: Designers use 3D software10 to turn product ideas into precise engineering drawings. This step captures every detail of the design, providing a useful reference for later stages.
-
Shrinkage Calculations: Engineers calculate shrinkage rates using material properties to make sure molds account for material contraction during cooling.
Enhancing Communication and Collaboration
Clear communication can really impact a project. Accurate drawing transformation makes sure everyone understands each other, aligning goals across teams and reducing misunderstandings.
-
Standardization: Standard formats and symbols create a common understanding across teams, streamlining teamwork and elevating efficiency.
-
Quality Assurance: Detailed drawings serve as checkpoints in manufacturing, enabling continuous checks against design specifications to ensure products meet quality standards.
Focusing on these aspects helps companies enhance their production processes11, ensuring that products match customer needs and industry standards—like organizing a production line where everything fits perfectly from design to final product.
Product analysis is the first step in mold development.True
The process begins with analyzing the product to ensure feasibility.
Cooling systems are optional in mold design.False
Cooling systems are crucial for temperature control and quality.
What Are the Best Practices for Mold Manufacturing and Processing?
Starting a journey in mold manufacturing resembles creating a work of art. Each detail really counts.
The best practices for mold manufacturing and processing involve careful study of the product, exact mold creation and effective work. Important steps include planning, designing the mold layout and testing to produce faultless work and excellent results.
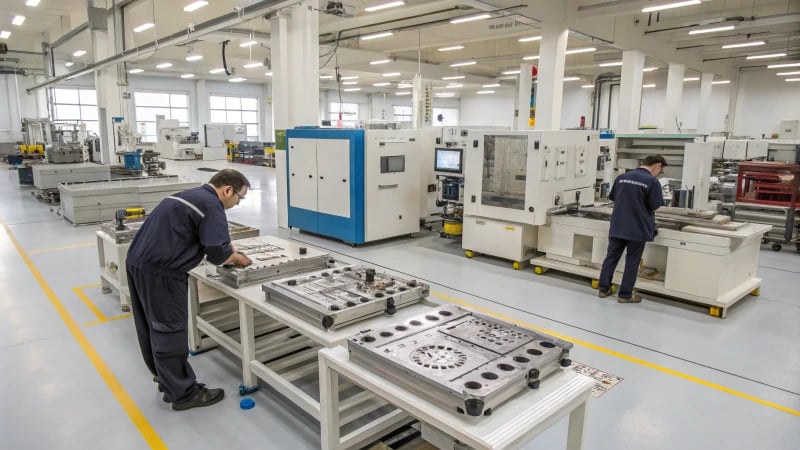
Product Analysis and Design Planning
When I first entered the mold manufacturing field, the adventure began well before any material reached the machine. It starts with careful product analysis12. This stage involves examining the product’s measurements, shrinkage rates, and material entry points. I recall my initial experience using 3D software to turn our ideas into engineering drawings – it was like breathing life into a concept. Precision in every tiny detail guarantees accuracy in the next steps. Precision is key.
Mold Structure Design
Designing the mold structure blends creativity with technical skill. I learned to study everything, including the number of cavities, cooling methods, and ejection systems. My mentor compared arranging products based on size and machine needs to solving a complex puzzle. A thoughtful mold structure13 design really impacts the final product’s quality.
Key Components of Mold Structure
Component | Functionality |
---|---|
Mold Kernel | Direct contact with product; affects molding quality |
Mold Embryo | Supports and fixes other mold parts |
Pouring System | Channels molten plastic into the mold cavity |
Core Extraction | Facilitates smooth removal of product post-molding |
Exhaust System | Discharges air to avoid defects |
Ejector System | Ejects product from mold cavity after formation |
Trial Mold and Acceptance
Then comes the exciting stage: mold testing14. Here, we see if our designs work in reality. It is crucial for identifying any defects or irregularities in the mold design. I vividly remember my first trial, holding my breath as the machine came to life. Often, adjustments are necessary based on these tests, leading to refinement until reaching perfection.
Trial testing involves:
- Setting up the mold on an injection machine.
- Adjusting elements like injection pressure and cooling time.
- Watching molding quality and fine-tuning as needed.
These steps are vital for a smooth production process and achieving top-notch output.
Data Organization and Archiving
Through all these processes, keeping detailed records proves invaluable. Organizing data from the start of the design to the end of trials greatly simplifies future mold repairs15 and new product designs. These archives turn into truly valuable resources for efficient production management.
Mold parting lines affect injection mold quality.True
Correct design of mold parting lines ensures product quality and feasibility.
Cooling systems are optional in mold design.False
Cooling systems are essential for temperature control and product quality.
What’s the Inside Scoop on Mold Trial and Acceptance?
In the beginning, I explored the world of injection molding. Mold trials seemed mysterious. Yet, discovering their secrets often results in perfect products. Avoiding expensive errors is really important. A small revelation changes everything.
Testing a mold requires using an injection molding machine. Pressure, temperature and other settings get adjusted during testing. Various trials help the product reach quality standards. Repairs happen if needed.
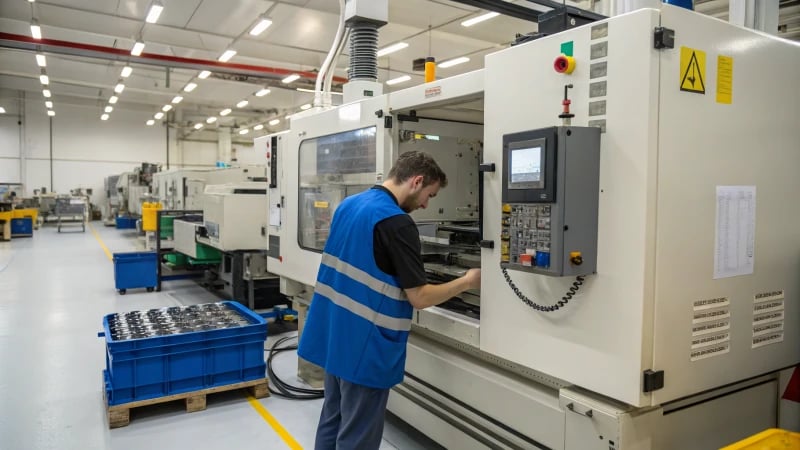
Grasping the Mold Trial Process
Starting a mold trial is like beginning a big experiment. Imagine setting up that shiny, new mold on the injection molding machine for the first time. The air buzzes with excitement as you adjust key settings – pressure, speed, temperature – hoping they will all work well together to create the perfect piece.
Testing and Adjusting Parameters
The first trial, known as T0, is like testing a car before a big race. The process begins with a dry run – no plastic yet – only to check if everything is working correctly. Once that checks out, you test how it performs under real conditions. It reminds me of my first major project where every measurement needed to be exact.
Parameter | Importance |
---|---|
Injection Pressure | Ensures material fills the mold properly |
Mold Temperature | Affects cooling rate and product quality |
Cooling Time | Impacts part strength and cycle time |
Detecting Problems and Fixing the Mold
Finding flaws like shrinkage or warping is like solving a detective case. I recall a time when strange warping led me down a path of adjusting gate locations and fine-tuning cooling systems. It was a big learning experience!
If defects such as shrinkage or warping are identified, solutions could involve adjusting the gate location or optimizing the cooling system]. Technicians may also adjust the mold structure16 for improved performance.
Final Acceptance Steps
Completing successful trials feels like crossing a finish line. This step needs detailed records of results, confirming each adjustment is fixed. When all looks good, that mold earns its special number and spot in the archives for future use.
Acceptance occurs after several successful trials where all specifications are met. The final acceptance involves documenting all test results and ensuring that any previously identified issues are resolved.
Once accepted, the mold is numbered and archived for future reference, maintaining quality standards in production.
Finishing this stage feels like solving a hard puzzle.
In the end, mold trials and their acceptance require precision, patience, and persistence – a real mix of art and science in injection molding. After each successful trial, there’s relief and joy, ready to face the next challenge.
Mold kernel design affects product quality.True
The mold kernel's design quality directly impacts the molding quality.
Trial molds are unnecessary in injection molding.False
Trial molds ensure the product meets dimensional and quality requirements.
Why is Data Organization Crucial After Mold Development?
Have you ever thought about why organizing your data after mold development becomes a crucial factor for your manufacturing? Structure brings order. Order reduces chaos. Data has value when it’s sorted. Patterns and trends become clear. Problems show up early. Early problems are easier to solve. Good decisions follow. Factories really need good choices. Efficiency gets a boost. Costs might drop. Output probably increases. Results could be surprising. Smart planning leads to success.
Data organization after mold development means arranging all technical details like drawings, specifications and test records in order. Quality control depends on this practice. Having organized data helps in solving problems. This probably makes future mold designs faster. Really fast.
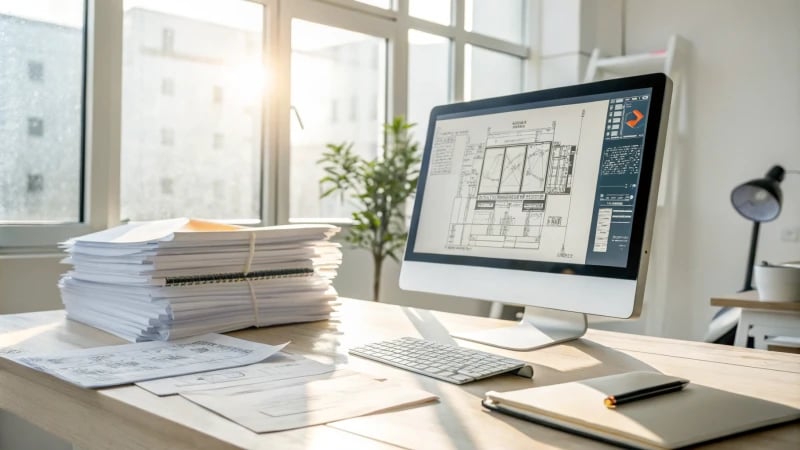
Understanding the Role of Data in Mold Development
When I started with mold development, the amount of data surprised me. Technical specs, engineering drawings, inspection records—all of it was overwhelming. Organizing this information is important for maintaining efficiency17 and keeping product quality high. Picture looking for a needle in a haystack; that’s what mold development feels like without good organization.
Key Steps in Data Organization
-
Systematic Archiving: I learned fast that sorting and storing data helps the most. From mission statements to part drawings and repair records, having everything in order makes life easier.
-
Binding and Numbering: There’s something very satisfying about a well-organized set of documents. It lets anyone involved solve problems quickly without endless searching. This is important.
-
Archiving and Preservation: Keeping data both on paper and digitally means I have backups for any problem. One time, when digital files were lost, my paper copies saved the day.
Data Type | Description |
---|---|
Parts Drawings | Detailed engineering illustrations |
Mold Assembly Diagrams | Visuals of mold structure |
Inspection Records | Quality assurance documentation |
Importance in Quality Control
Well-organized data really helps when fixing molds or dealing with defects. Engineers can quickly reference past records to identify issues, ensuring consistent quality control.
Enhancing Future Mold Designs
Data from old projects is probably a goldmine of information for new designs. Learning from well-documented mistakes helps me better new molds and avoid extra troubles, thus improving new mold efficiency18.
Implementing Efficient Data Systems
Using digital tools like Product Lifecycle Management (PLM) systems changed how I manage data. These platforms organize mold data and offer benefits like centralized access and better team collaboration while following industry rules.
- Benefits:
- Centralized data access
- Enhanced collaboration among teams
- Improved compliance with industry standards
Smart data organization drives innovation. If you want to improve your manufacturing operations, consider implementing a strategic data management system that aligns with your goals.
Product analysis determines mold parting line.True
Product analysis identifies key features like parting lines for mold design.
Cooling system design affects mold assembly.False
Cooling system design impacts temperature control, not mold assembly.
Conclusion
The standard development process for injection molds includes product analysis, design planning, mold structure design, manufacturing, trial testing, and data organization to ensure quality and efficiency.
-
Understanding this concept is crucial for assessing design feasibility and planning mold construction effectively. ↩
-
Explore different cooling system designs to enhance product quality and production efficiency. ↩
-
Learn about potential defects to proactively address them during design and production stages. ↩
-
Understanding product arrangement’s role in cycle efficiency helps enhance production timelines. ↩
-
Exploring kernel structure’s impact aids in optimizing mold performance. ↩
-
Air ejectors can improve ejection efficiency and product safety. ↩
-
Exhaust systems prevent defects and improve product quality. ↩
-
Choosing suitable CAD tools enhances precision in mold designing. ↩
-
Explore how engineering drawings facilitate accurate communication between design and production teams. ↩
-
Discover tools that optimize the conversion of product designs into detailed engineering plans. ↩
-
Learn how precise drawings improve manufacturing efficiency and product quality. ↩
-
Explore why thorough product analysis is crucial in ensuring successful mold manufacturing and defect-free production outcomes. ↩
-
Understand critical aspects of mold structure design that impact product quality and manufacturing efficiency. ↩
-
Learn the steps involved in trial mold testing to ensure the final product meets all specified requirements. ↩
-
Discover how systematic data organization can enhance future mold repair and new product design processes. ↩
-
Explore different techniques for modifying mold structures to enhance performance. ↩
-
Learn how structured data enhances operational efficiency by streamlining processes and reducing errors. ↩
-
Understand how past data provides insights that improve the efficiency and quality of new projects. ↩