Navigating the world of manufacturing can feel overwhelming, especially when it comes to injection mold design. But understanding standardization is key to unlocking efficiency and reliability in this complex process.
Injection mold design standardization involves setting guidelines for mold structure, size, material selection, processing methods, and assembly techniques. These standards ensure consistent quality, interchangeability, and cost-effectiveness in mold manufacturing.
Now that we’ve laid down the basics, let’s dive deeper into the components that make up injection mold design standardization and uncover how they contribute to manufacturing success.
Standard mold frames reduce manufacturing costs.True
Standard mold frames enhance versatility and interchangeability, lowering costs.
What Are the Key Elements of Mold Structure Standardization?
Mold structure standardization is pivotal in optimizing manufacturing efficiency and ensuring product quality. But what are its key components?
The key elements of mold structure standardization include mold frame standards, mold part standards, and adherence to size and material specifications. These elements ensure compatibility, reduce costs, and enhance the durability and functionality of molds.

Standardization of Mold Frame
The use of standard mold frames1 is a cornerstone of structural standardization. These frames typically consist of fixed and movable plates, guide pillars, and sleeves, among other components. By utilizing standard frames, manufacturers can enhance the versatility and interchangeability of molds. This approach not only reduces costs but also ensures that molds are adaptable to various product sizes by selecting appropriate frame specifications.
Component | Purpose |
---|---|
Fixed Mold Base Plate | Provides stability and alignment |
Movable Mold Plate | Allows for dynamic movement during molding |
Guide Pillars | Ensures precision and alignment |
Mold Part Standardization
The standardization extends to individual mold parts such as ejector pins, reset rods, and pull rods. By adhering to standardized size, shape, and material guidelines, manufacturers can ensure consistent performance and reliability across different molds. This standardization facilitates maintenance and replacement, significantly improving manufacturing efficiency and mold quality.
Importance of Size and Material Standards
Adhering to size tolerance standards is crucial for ensuring the quality and interchangeability of molds. The size accuracy of a mold should always exceed that of the product to maintain precision in manufacturing. Simultaneously, selecting materials such as P20 or NAK80 steel according to industry standards ensures the mold’s durability and performance.
In summary, understanding these key elements and their applications helps manufacturers achieve high efficiency, cost-effectiveness, and reliability in their production processes.
Standard mold frames reduce manufacturing costs.True
Standard frames enhance versatility and adaptability, lowering costs.
Mold part standardization decreases maintenance efficiency.False
Standardization improves maintenance and replacement, boosting efficiency.
How Do Size Tolerances Impact Mold Design Quality?
Precision in size tolerances is pivotal in mold design, directly affecting product quality and efficiency.
Size tolerances in mold design dictate the accuracy and stability of the final product. By adhering to national or industry standards, molds can produce consistently high-quality components that meet exact specifications, ensuring interchangeability and reducing manufacturing costs.
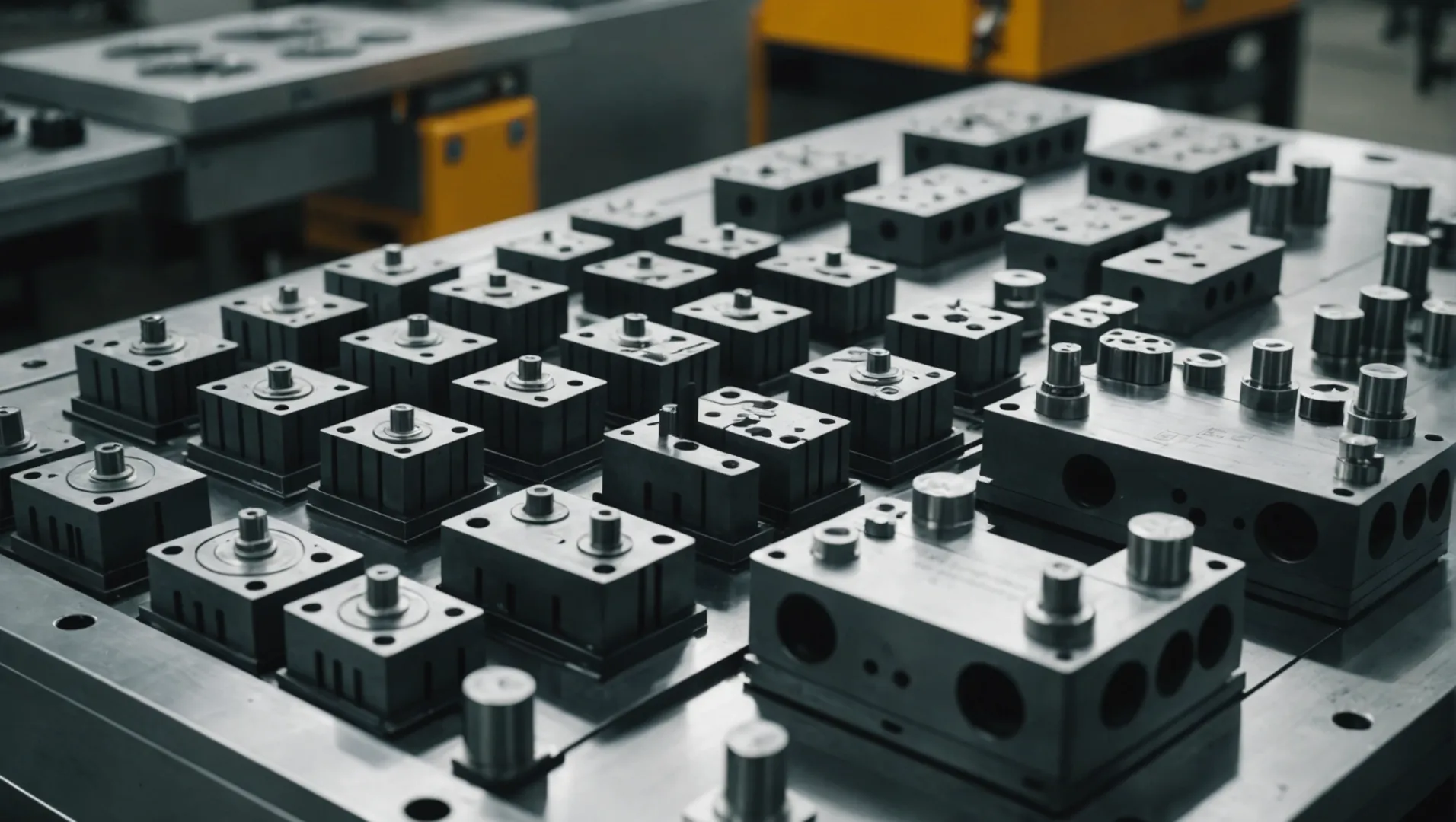
Understanding Size Tolerances in Mold Design
In the realm of injection molding2, size tolerances play a crucial role in determining the final quality of molded products. These tolerances refer to the permissible limits or variations in a physical dimension, which must be adhered to during the design and manufacturing processes. By ensuring these limits are met, manufacturers can produce parts that are consistent in size and shape, enhancing their interchangeability3 and reliability.
Product Size Tolerance
The product’s size tolerance defines the acceptable range within which a product’s dimensions can vary without affecting its functionality or assembly with other parts. In injection mold design, product size tolerances are guided by either national or industry standards, ensuring that each component fits perfectly with others in an assembly line.
For instance, a slight deviation from specified dimensions could result in parts that do not fit together as intended, leading to functional issues or increased waste due to rejected parts.
Mold Part Size Tolerance
Each mold component also has its own size tolerance, which is crucial for maintaining the precision of the mold as a whole. The size tolerance for mold parts, such as cavities and cores, should be more stringent than that of the final product to ensure that any minor deviations do not compromise the integrity of the final molded item.
This strict control over dimensions involves selecting appropriate materials and processing techniques to achieve the desired precision. For example, precise machining processes can help attain the necessary accuracy, while high-quality steel can withstand wear and maintain dimensional stability over multiple production cycles.
Component | Typical Tolerance | Importance |
---|---|---|
Cavity Size | ±0.005 mm | Ensures product shape fidelity |
Core Size | ±0.010 mm | Affects part thickness and fit |
Ejector Pins | ±0.020 mm | Influences part release |
The Role of Standardization
By standardizing size tolerances, manufacturers can streamline production processes, reduce costs, and minimize errors. This standardization leads to improved manufacturing efficiency and enhances the overall quality of molds.
Moreover, using standardized components like ejector pins and guide pillars ensures ease of maintenance and replacement, thus prolonging the life of molds and reducing downtime.
In summary, understanding and implementing precise size tolerances in mold design is not just about compliance but about achieving a balance between quality, cost-effectiveness, and production efficiency. This underscores the importance of adhering to established standards to meet consumer demands and industry requirements efficiently.
Size tolerances ensure product interchangeability.True
Adhering to size tolerances allows for consistent part fitting.
Mold part tolerances can be less strict than product tolerances.False
Mold parts require stricter tolerances to ensure final product precision.
Why Is Material Selection Crucial in Mold Standardization?
Material selection is the cornerstone of mold standardization, dictating the durability, functionality, and cost-effectiveness of the mold. But why is it so pivotal in ensuring the success of standardized molds?
Material selection in mold standardization ensures durability, performance, and cost-efficiency by choosing appropriate steels and heat treatments according to established standards.
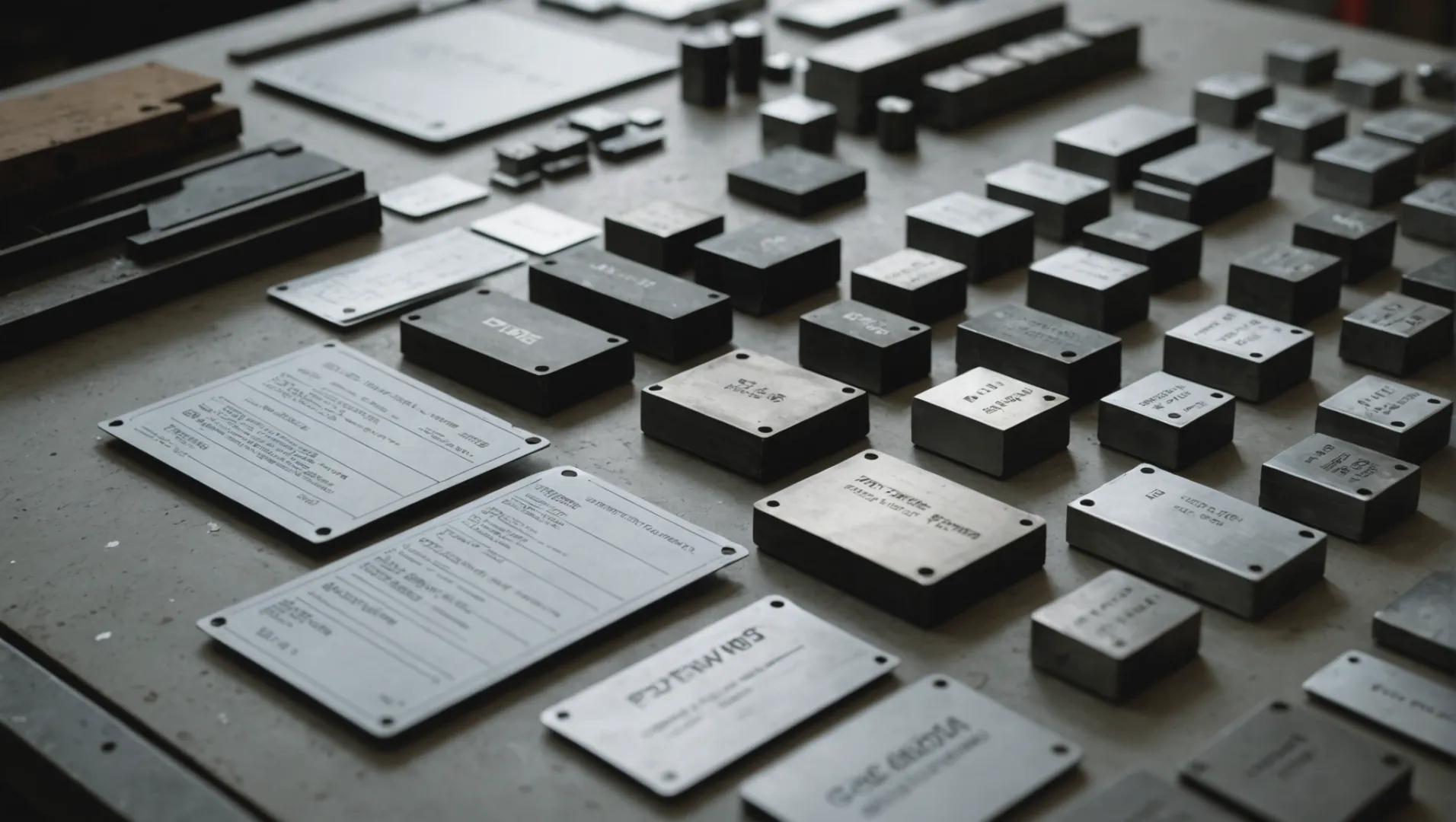
Understanding Material Properties
When selecting materials for mold standardization, it’s essential to consider the properties that different materials bring to the table. For instance, the commonly used steels like P20, 718, and NAK80 each offer unique benefits. P20 steel is known for its versatility and excellent polishability, making it suitable for various applications. On the other hand, 718 is highly favored for its robustness and ability to withstand high wear and tear, thus extending the lifespan of molds.
The importance of material properties4 cannot be overstated as these determine how well a mold will perform under specific conditions. By adhering to recognized standards for materials, manufacturers can ensure that the molds not only meet but exceed performance expectations.
The Role of Heat Treatment
Heat treatment is another critical factor in material selection that directly impacts the mold’s performance. Proper heat treatment enhances a material’s hardness and wear resistance, which are crucial for molds that undergo significant mechanical stress. For example, precise control over heat treatment parameters can significantly improve the quality and durability of critical components like cavities and cores.
Aligning with Standards
Adhering to national or industry standards for both materials and heat treatments ensures that molds are manufactured with predictable quality and performance. This alignment not only aids in maintaining consistency across production but also facilitates easier maintenance and replacement of mold parts. By selecting materials that conform to these standards, manufacturers can achieve a high level of quality control.
Cost Implications
Material selection has direct implications on the cost-efficiency of mold manufacturing. Choosing standardized materials can reduce costs through economies of scale and streamlined procurement processes. Moreover, standardized materials often come with established supplier networks, reducing lead times and enabling more efficient production schedules.
A cost analysis of materials5 demonstrates that while some high-performance materials may have a higher upfront cost, their extended lifecycle and reduced maintenance needs offer better long-term value.
Summary
In summary, material selection in mold standardization is not merely about choosing a type of steel; it’s about understanding how different materials interact with processing techniques and usage conditions to optimize performance. By focusing on key elements such as material properties, heat treatment processes, and adherence to standards, manufacturers can produce molds that are reliable, durable, and cost-effective.
P20 steel is known for its excellent polishability.True
P20 steel's polishability makes it versatile for various applications.
Heat treatment decreases a mold's wear resistance.False
Heat treatment increases hardness and wear resistance of molds.
How Does Standardized Processing Enhance Mold Durability?
Standardized processing is the cornerstone of enhancing mold durability, ensuring consistent performance and longevity. But how does this practice actually extend the lifespan of molds?
Standardized processing enhances mold durability by ensuring uniformity in manufacturing techniques, adhering to precise machining protocols, and implementing rigorous inspection standards. This approach minimizes wear and tear, reduces production errors, and extends the operational life of molds.
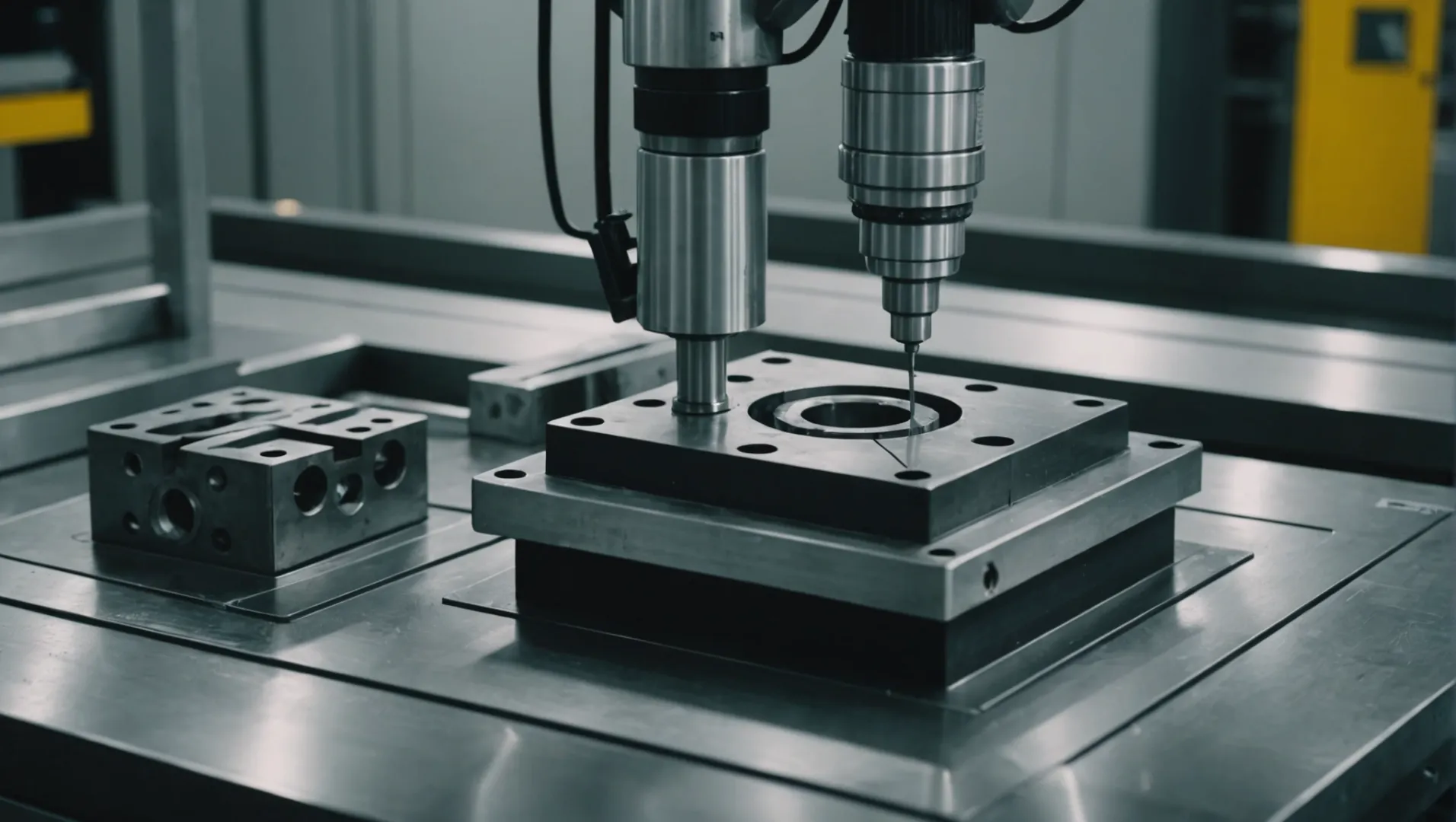
Ensuring Consistency Through Processing Technology Standards
Standardized processing ensures that every mold component is crafted with precision and consistency. This involves adhering to national or industry standards for cutting, EDM (electrical discharge machining), and wire cutting technologies. By following these standards, manufacturers can achieve the required processing accuracy and surface quality, which are crucial for the longevity of molds6.
For instance, using a standardized EDM process ensures that the intricate parts of a mold are accurately shaped without introducing structural weaknesses that could lead to premature failure. By maintaining a uniform approach across different manufacturing stages, variability is minimized, thus reducing the risk of defects and enhancing mold durability.
Rigorous Inspection Standards
The inspection phase is vital for detecting any deviations from the required specifications early in the production process. Standardized inspection standards demand high-precision equipment to evaluate critical dimensions and geometric tolerances. By employing these standards, potential issues can be addressed before they escalate into costly repairs or replacements.
For example, by utilizing advanced metrology tools to inspect key dimensions, such as cavity and core sizes, manufacturers can ensure that molds remain within acceptable tolerances throughout their lifecycle. This proactive approach helps in identifying wear patterns and potential points of failure, allowing for timely interventions.
Benefits of Controlled Assembly Processes
Standardization extends into the assembly phase, where precise cleaning, inspection, and assembly protocols are followed. This ensures that each component fits perfectly and functions as intended. The importance of controlled assembly processes7 cannot be overstated, as improper assembly can introduce stress points that compromise mold integrity.
Moreover, standardized debugging processes post-assembly help in fine-tuning the mold setup to optimize performance. By catching issues early in the assembly stage, manufacturers can prevent operational failures that could lead to decreased mold durability.
Heat Treatment and Material Longevity
Heat treatment is a critical factor in determining mold durability. Standardizing heat treatment processes ensures that mold components attain the desired hardness, strength, and wear resistance. This controlled approach prevents inconsistencies that could lead to material fatigue or premature wear.
By selecting appropriate steels like P20 or NAK80 based on standardized criteria, manufacturers can enhance the life expectancy of their molds. The role of standardized heat treatment8 in improving material properties cannot be overlooked as it directly influences the performance and lifespan of the mold components.
Standardized processing reduces mold wear and tear.True
It ensures uniformity in manufacturing, minimizing errors.
Controlled assembly processes can decrease mold durability.False
Controlled assembly enhances fit and function, improving durability.
Conclusion
In summary, embracing injection mold design standardization is essential for achieving efficiency and quality in production. By adhering to these guidelines, manufacturers can significantly enhance their processes and outcomes.
-
Explore how standard mold frames improve versatility and reduce manufacturing costs.: Dedicated mold bases offer a higher mold life than MUD inserts, allowing a molder to run more cycles or parts throughout the life of the mold … ↩
-
Discover why precise size tolerances are vital for mold quality.: Fine tolerances, also called precision tolerances, provide a tighter tolerance band which ultimately makes the mold and subsequent parts more expensive. ↩
-
Learn how interchangeable parts improve manufacturing efficiency.: Speed is a critical factor in manufacturing. Interchangeable inserts significantly reduce lead times by allowing for rapid mold changes and … ↩
-
Explore how material properties influence mold performance and longevity.: The material selected for the injection molding part directly impacts nearly every aspect of the final product, from its strength and durability to its … ↩
-
Understand the cost implications of different materials in mold production.: The cost of purchasing materials for molds differs according to the material chosen. Thermoplastic pellets cost approximately $1 to $5 per kg. Material cost is … ↩
-
Discover how standardization reduces wear and prolongs mold life.: Maintenance Needs: Regular maintenance is less stringent than higher-class molds but still crucial for maximizing their lifespan. Ideal … ↩
-
Learn how precise assembly enhances mold durability.: This process eliminates the need for post-molding assembly and reduces the number of parts being used in the product, hence improving the product quality. ↩
-
Explore how standardized heat treatment improves material longevity.: The choice of mold material plays a crucial role in heat treatment, as it can significantly impact the deformation of the treated parts. This … ↩