Have you ever faced a challenging decision in manufacturing that made you pause? I certainly have, especially when it comes to material compatibility.
Directly injecting PP plastic resin into an ABS mold is generally not recommended due to significant differences in shrinkage rates, processing temperatures, and material properties, which can lead to dimensional inaccuracies and product performance issues.
Yet, don’t be discouraged just yet! There are methods and considerations that could open doors to using PP in ABS molds under certain conditions. Let’s explore these possibilities together!
PP resin can be injected into ABS molds without issues.False
PP and ABS have different shrinkage rates and processing temperatures, causing compatibility issues.
What Are the Key Differences Between PP and ABS Materials?
Understanding the distinct characteristics of PP and ABS is essential for optimizing their use in manufacturing processes.
PP and ABS differ in shrinkage rates, processing temperatures, and material properties, affecting their suitability for different applications.
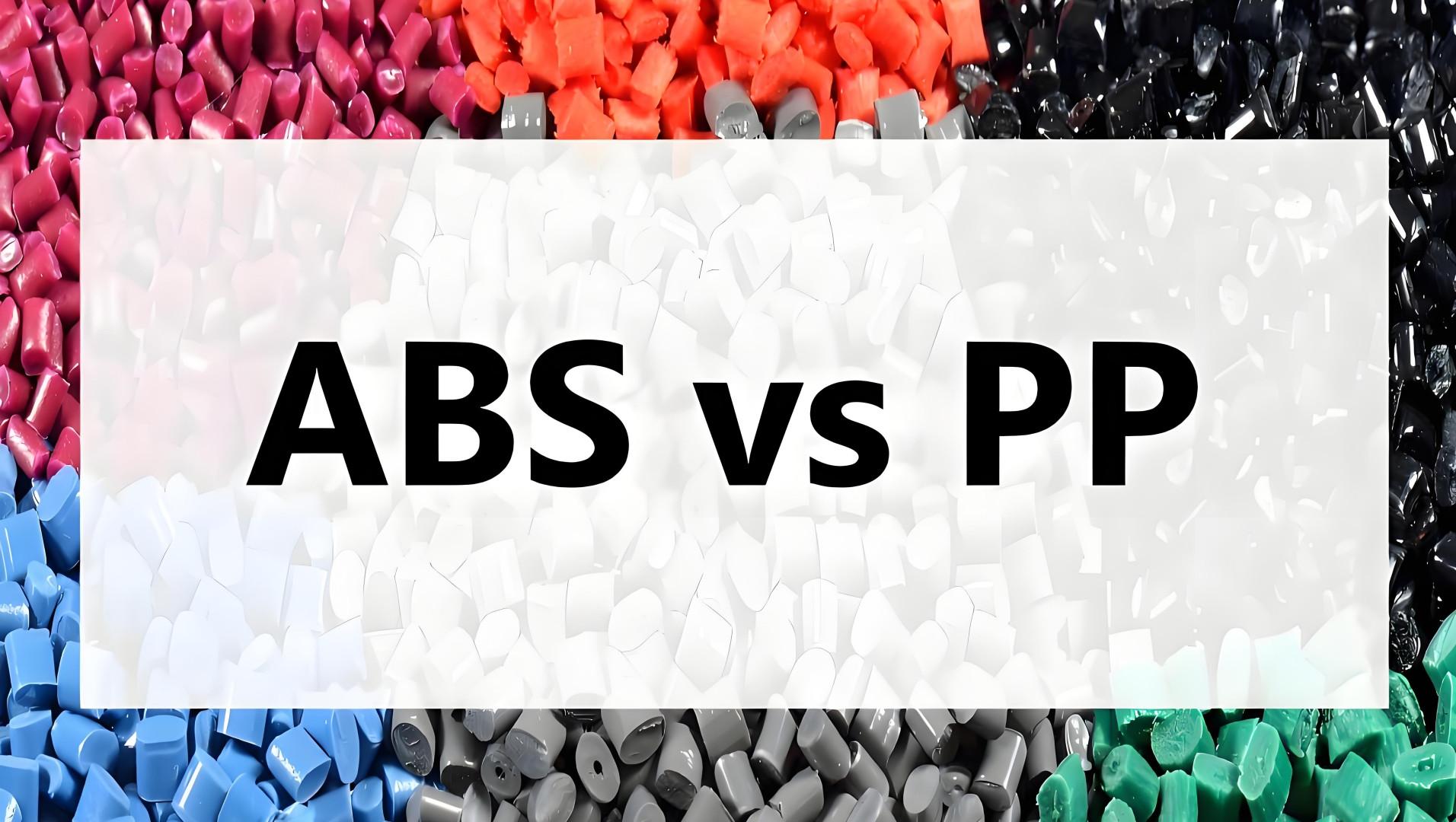
Shrinkage Rates: Why They Matter
One of the most critical differences between PP (polypropylene) and ABS (acrylonitrile-butadiene-styrene) lies in their shrinkage rates. PP exhibits a higher shrinkage rate, which can lead to size discrepancies if injected into molds designed for ABS, which shrinks less. This variance can result in dimensional deviations and deformation during the manufacturing process.
Material | Typical Shrinkage Rate (%) |
---|---|
PP | 1.5 – 2.5 |
ABS | 0.5 – 0.7 |
The table above highlights the significant difference in shrinkage rates that manufacturers must consider.
Processing Temperatures: A Crucial Factor
Processing temperatures further differentiate these two materials. PP typically requires lower processing temperatures compared to ABS. If ABS molds are used with PP without adjusting for this discrepancy, it can lead to decomposition of PP and performance degradation.
- PP Processing Temperature: 160°C to 220°C
- ABS Processing Temperature: 210°C to 250°C
These differences necessitate careful adjustment in manufacturing processes1 to ensure optimal product quality.
Material Properties: Tailoring for Performance
From a material properties standpoint, ABS is renowned for its toughness and impact resistance, making it ideal for applications requiring durability. Conversely, PP boasts better heat resistance and chemical corrosion resistance, attributes that make it suitable for environments where such properties are paramount.
Mechanical and Chemical Properties Comparison
Property | PP | ABS |
---|---|---|
Toughness | Moderate | High |
Heat Resistance | Excellent | Moderate |
Chemical Resistance | Excellent | Moderate |
Impact Resistance | Low to Moderate | High |
Understanding these key differences helps manufacturers decide which material is best suited for specific applications, thereby optimizing both performance and cost-efficiency. For more insights on material selection, explore comprehensive guides2.
PP has a higher shrinkage rate than ABS.True
PP's shrinkage rate is 1.5-2.5%, while ABS is 0.5-0.7%.
ABS requires lower processing temperatures than PP.False
ABS needs 210°C-250°C, whereas PP requires 160°C-220°C.
How Do Shrinkage Rates Affect Injection Molding?
Shrinkage rates are crucial in injection molding, influencing the final product’s dimensional accuracy and structural integrity.
Shrinkage rates determine how much a material contracts during cooling in injection molding. Differences in shrinkage rates between materials like PP and ABS can lead to mismatched dimensions, warping, and defects if not properly managed.
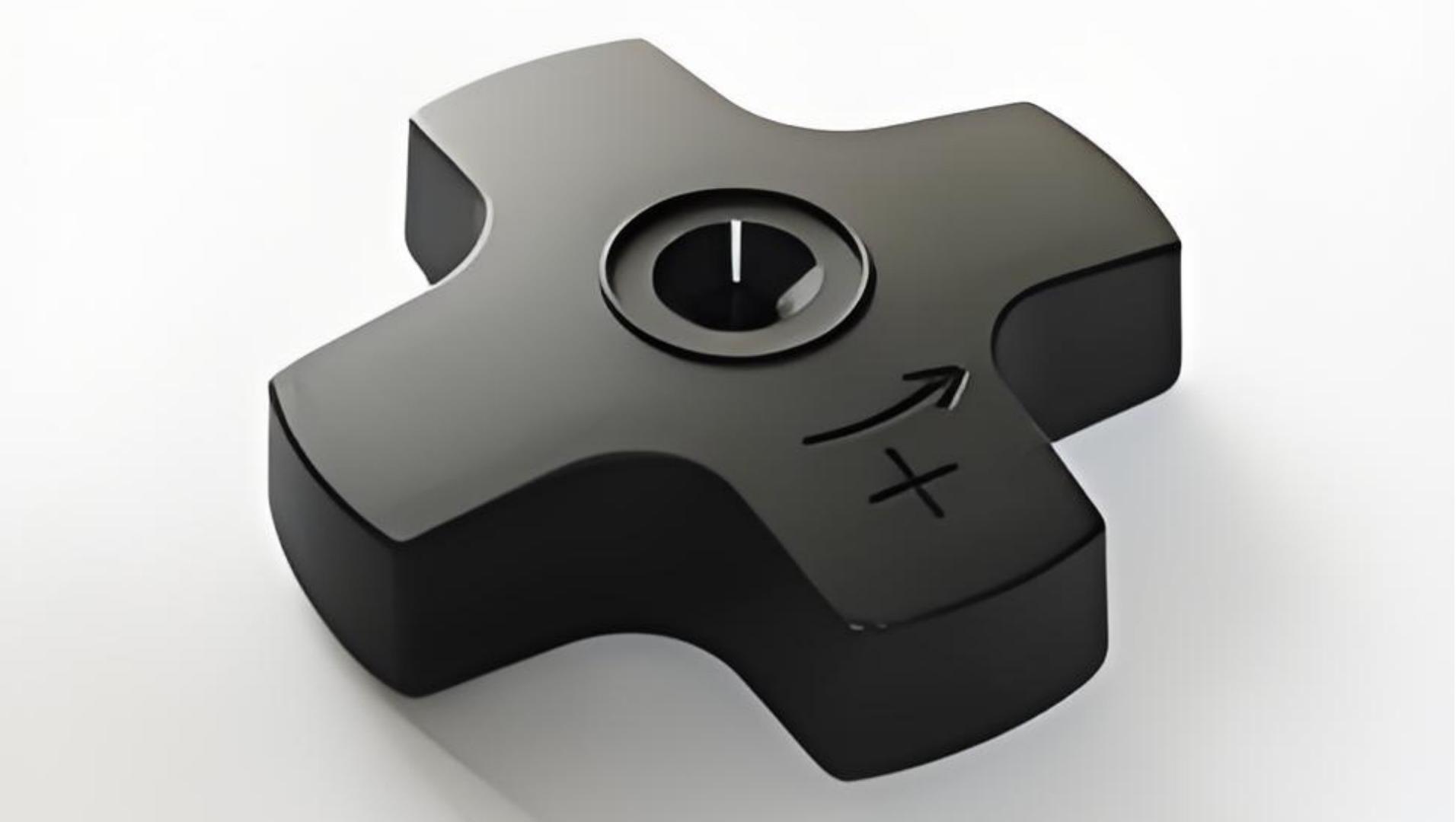
Understanding Shrinkage in Injection Molding
In the injection molding process3, materials undergo thermal expansion and contraction. When a molten polymer cools, it shrinks, impacting the final dimensions of the molded part. This phenomenon is known as shrinkage.
The shrinkage rate is the percentage by which a material reduces in size as it transitions from molten to solid state. It’s determined by factors such as material properties, mold design, and processing conditions.
Comparative Shrinkage Rates of PP and ABS
Polypropylene (PP) typically exhibits a higher shrinkage rate compared to acrylonitrile-butadiene-styrene (ABS). This difference arises due to the inherent molecular structure of these materials. PP can shrink by 1.5% to 2.5%, whereas ABS shrinks around 0.4% to 0.8%.
Material | Typical Shrinkage Rate |
---|---|
PP | 1.5% – 2.5% |
ABS | 0.4% – 0.8% |
This disparity can lead to issues such as dimensional deviation and structural warping when attempting to use PP in molds designed for ABS, making it essential to consider these rates during the design phase.
Implications of Incompatible Shrinkage Rates
Dimensional Accuracy
Molds are typically designed to accommodate specific shrinkage rates, ensuring the final product meets precise specifications. An incompatible material like PP in an ABS mold could result in a finished product that deviates significantly from intended dimensions, causing misalignment in assemblies or requiring additional post-processing.
Structural Integrity and Performance
Shrinkage affects not only the dimensions but also the performance of the molded parts. Excessive shrinkage can lead to internal stresses, which may compromise structural integrity, resulting in defects like warping or cracking.
Strategies for Managing Shrinkage Rate Differences
Mold Design Adjustments
Adapting mold designs to account for different shrinkage rates is one strategy. For instance, adding allowances in the mold can compensate for higher shrinkage rates of materials like PP.
Processing Parameter Optimization
Fine-tuning parameters such as injection speed, pressure, and cooling time can help mitigate shrinkage-related issues. By optimizing these settings, manufacturers can achieve better dimensional accuracy even when using non-standard material combinations.
Injection molding best practices4 often involve comprehensive testing and adjustments based on empirical data to ensure compatibility between materials with different shrinkage characteristics.
Conclusion: Considerations for Material Compatibility
Understanding and managing shrinkage rates is vital for successful injection molding5. Manufacturers should meticulously evaluate material compatibility and design molds accordingly to avoid production pitfalls.
PP has a higher shrinkage rate than ABS.True
PP shrinks 1.5%-2.5%, while ABS shrinks 0.4%-0.8%.
ABS molds can be used for PP without issues.False
Using PP in ABS molds can cause dimensional and structural issues.
Can Processing Techniques Bridge Material Differences?
Exploring how processing techniques can potentially bridge the gap between differing materials like PP and ABS in injection molding.
While processing techniques can mitigate some differences between PP and ABS, they cannot fully overcome inherent material disparities. Adjusting mold designs, optimizing processing parameters, and modifying materials are potential strategies, but these often involve increased costs and complexities.

Understanding Material Incompatibilities
In general, materials like polypropylene (PP)6 and acrylonitrile-butadiene-styrene (ABS)7 present distinct challenges in injection molding due to their inherent differences. The most pressing issues include varying shrinkage rates and processing temperatures, which significantly affect the outcome.
Shrinkage Rates and Dimensional Accuracy
Shrinkage is a critical factor that can lead to dimensional deviations. With PP exhibiting higher shrinkage rates than ABS, molds designed for ABS might not accommodate PP‘s characteristics, resulting in flawed products.
Material | Shrinkage Rate (%) |
---|---|
PP | 1.0 – 2.5 |
ABS | 0.4 – 0.9 |
Processing Temperatures and Material Stability
Another hurdle is the variation in processing temperatures. ABS typically requires higher temperatures compared to PP, which can lead to PP‘s decomposition if not handled correctly.
Bridging the Gap with Processing Techniques
Mold Design Adjustments
Adjusting the mold design to align with PP’s characteristics, such as altering dimensions to accommodate its higher shrinkage rate, is one strategy. This ensures that the final product meets the desired specifications.
Optimizing Processing Parameters
Processing parameters like injection temperature, pressure, and speed can be fine-tuned to cater to PP‘s requirements. This can minimize degradation risks and enhance compatibility.
Material Modification
Enhancing PP by modifying its properties to better mimic ABS could improve compatibility. Alternatively, surface treatments on ABS molds can be employed to improve interactions with PP.
Considerations and Limitations
While these techniques offer pathways to bridge material differences, they come with their own set of challenges. Increased costs, potential for errors during adjustments, and the need for extensive trials are some considerations manufacturers must weigh. Therefore, comprehensive analysis and experiments tailored to specific production conditions are essential to determine viable solutions.
Understanding these techniques allows manufacturers to make informed decisions about using different materials in their processes without compromising quality or efficiency.
PP has a higher shrinkage rate than ABS.True
PP's shrinkage rate ranges from 1.0% to 2.5%, while ABS is 0.4% to 0.9%.
ABS requires lower processing temperatures than PP.False
ABS typically requires higher processing temperatures compared to PP.
What Are the Alternatives to Modifying Existing Molds?
Exploring alternatives can lead to innovative solutions and cost-saving strategies in injection molding.
Alternatives to modifying existing molds include using inserts, adopting hybrid molds, or leveraging advanced technologies like 3D printing for prototyping, all of which can accommodate material differences without permanent mold alterations.
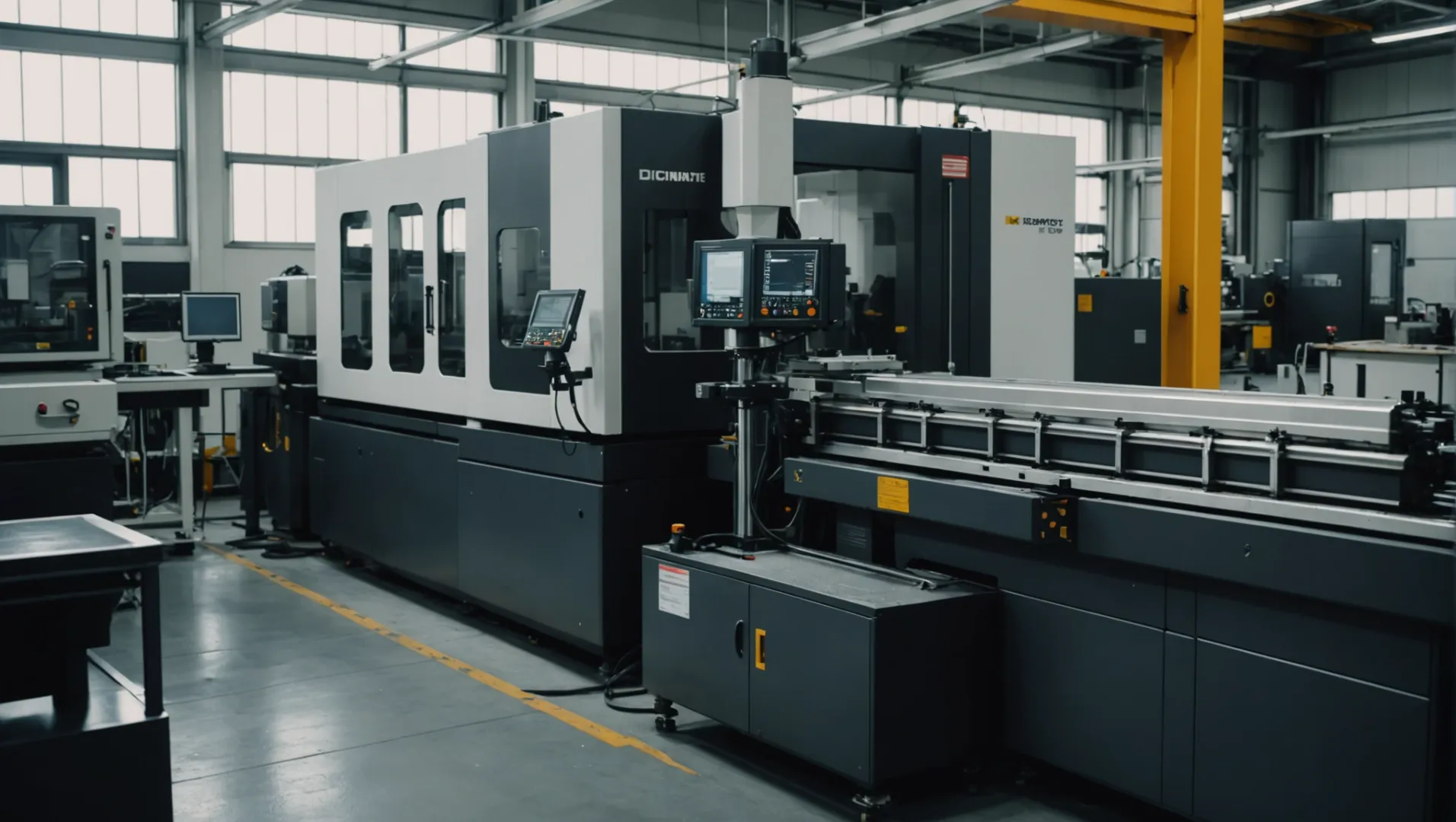
Exploring Insert Usage
One of the practical alternatives to altering molds is the use of inserts. Inserts are components that can be placed within the mold to change its characteristics temporarily. By using inserts crafted from compatible materials, manufacturers can adjust the mold cavity size or surface finish to better suit different plastics like PP (polypropylene) and ABS (acrylonitrile-butadiene-styrene copolymer).
Benefits of Inserts
- Cost-Effectiveness: Inserts are generally less expensive than fabricating a new mold.
- Flexibility: They allow for quick changes to adapt to different production requirements.
However, it’s crucial to ensure that the inserts fit precisely to avoid issues like mold flashing8, which can compromise product quality.
Utilizing Hybrid Mold Systems
Hybrid molds combine features of both standard and interchangeable mold components. These systems are designed to accommodate multiple materials without extensive modification.
Key Advantages
- Versatility: Easily adapt the mold for different materials.
- Longevity: Reduce wear and tear by customizing only parts that directly interact with the material.
When considering hybrid molds, it’s essential to evaluate their compatibility with both the material and production volume to ensure efficiency and cost-effectiveness9.
Advanced Technologies: 3D Printing and CNC Machining
Modern manufacturing technologies such as 3D printing and CNC machining offer innovative solutions for prototyping and short-run production without altering existing molds permanently.
3D Printing Benefits
- Rapid Prototyping: Allows for fast testing of mold designs and material compatibility.
- Customization: Easily create complex geometries without traditional mold limitations.
Using CNC machining10 allows for precise alterations to specific parts of a mold, maintaining overall mold integrity while accommodating new material specifications.
Conclusion
Exploring these alternatives can not only save costs but also enhance flexibility in production. By using inserts, hybrid molds, or leveraging advanced technologies like 3D printing and CNC machining, manufacturers can accommodate material differences effectively without altering existing molds permanently.
Inserts are a permanent mold modification.False
Inserts are temporary components that modify mold characteristics.
Hybrid molds reduce wear and tear.True
Hybrid molds customize only parts interacting with materials, reducing wear.
Conclusion
Understanding material compatibility is vital for successful injection molding. Explore the options, test thoroughly, and don’t hesitate to seek expert advice.
-
Discover techniques to optimize processes for different material properties.: In this article, you will learn how to select materials that are compatible with the manufacturing process, using some practical tools and methods. ↩
-
Gain insights into selecting the right materials for your projects.: By understanding your product’s requirements, evaluating manufacturing processes, considering costs, and testing prototypes, you can make an … ↩
-
Explore a comprehensive overview of injection molding fundamentals.: Learn the basics to the injection molding process, including: how it works, design principles, materials, and quality systems. ↩
-
Discover strategies for optimizing injection molding processes.: Design Tips for Injection Molding · 2. Take Into Account the Part Tolerance · 3. Choose the Right Wall Thickness · 4. Add Draft Angles to Your Design · 5. Add Ribs … ↩
-
Learn about evaluating and ensuring material compatibility.: In this blog post, we will discuss the factors that need to be considered when selecting multiple materials for double-shot injection molding. ↩
-
Discover the fundamental differences between PP and ABS materials.: ABS will show less shrinkage than PP during molding because of PP’s semi-crystalline nature, so tolerances generally can be slightly tighter … ↩
-
Explore how ABS’s properties contrast with those of PP.: Also, ABS is less prone to warp than PP. On the other hand, PP has better heat resistance and is less expensive when compared to ABS. As a … ↩
-
Learn about mold flashing and its impact on product quality.: Injection molding flash is a defect that occurs when molten plastic flows out of the mold during injection and solidifies. ↩
-
Discover how hybrid molds enhance production efficiency.: Linear AMS’ hybrid approach to producing mold inserts takes advantage of the best of additive and subtractive manufacturing to provide real-world solutions. ↩
-
Explore the precision and adaptability of CNC machining.: CNC Machining, a process characterized by its precision and flexibility, stands out in its ability to cater to complex and detailed designs. The … ↩