Injection molding is not just a process; it’s the heartbeat of modern manufacturing. However, I’ve seen firsthand how material waste can drain resources and inflate costs. Let’s dive into how we can turn that around.
To improve material utilization in injection molding, focus on optimizing mold design, controlling process parameters, strengthening material management, and enhancing production management. These strategies help reduce waste and improve efficiency.
While these initial strategies provide a solid foundation, let’s explore deeper methods to truly maximize your production capabilities.
Hot runner systems reduce material waste in injection molding.True
Hot runners keep plastic molten, eliminating runner waste.
What Role Does Mold Design Play in Material Utilization?
Mold design is pivotal in optimizing material usage in injection molding, directly affecting waste and efficiency.
Mold design is crucial in maximizing material utilization by optimizing runner systems and cavity designs. By ensuring balanced flow and efficient layouts, waste is minimized, and efficiency is increased.
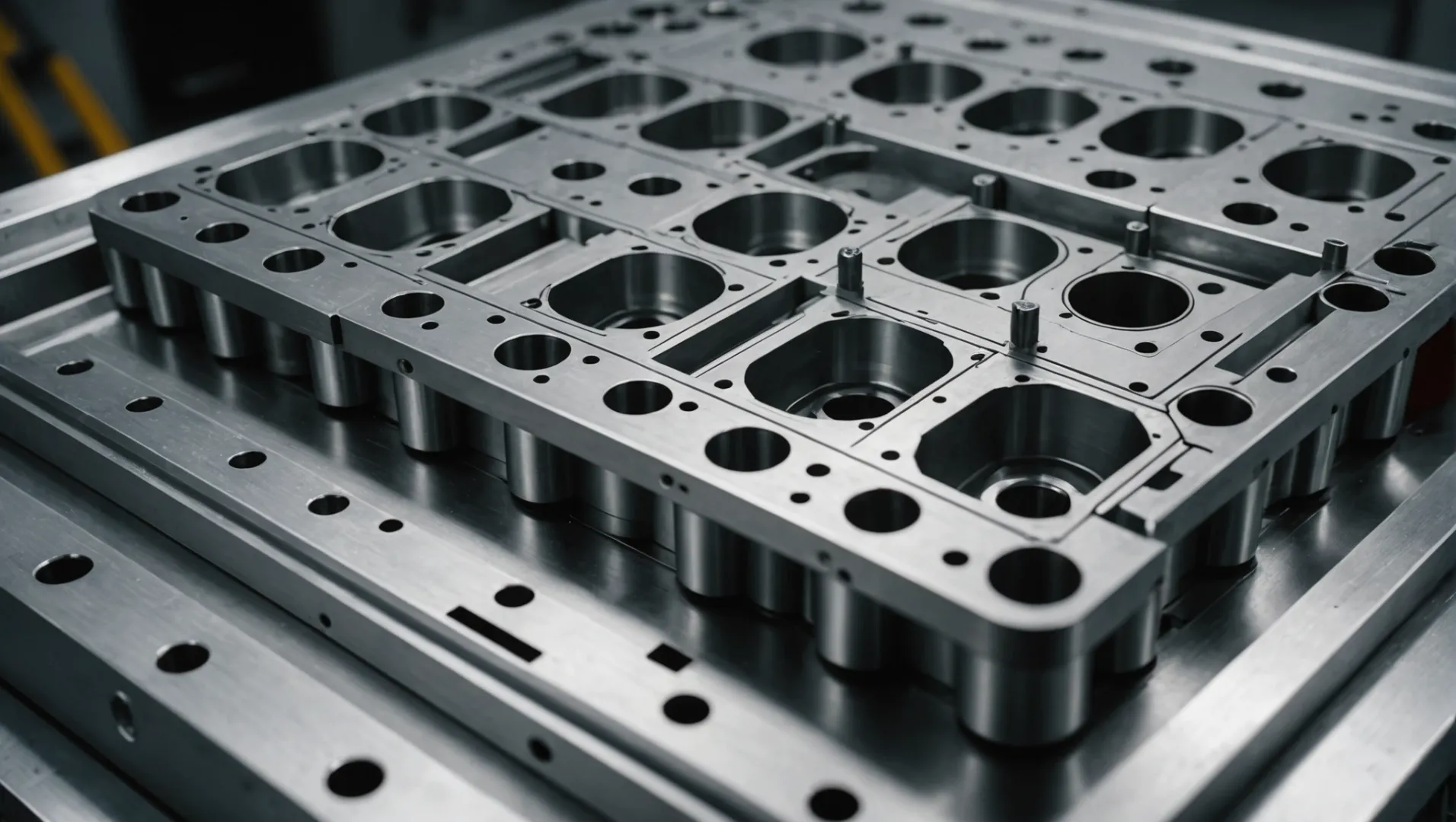
The Importance of a Balanced Runner System
A well-designed runner system is essential for efficient material usage. The objective is to create a balanced runner layout that ensures the melt fills each cavity evenly, reducing the waste typically associated with unbalanced flow. The implementation of a hot runner system1 can significantly enhance material utilization. Unlike traditional cold runners, a hot runner keeps the plastic in a molten state, eliminating runner waste that usually requires removal after molding.
Table 1: Comparison of Cold Runner vs. Hot Runner Systems
Feature | Cold Runner | Hot Runner |
---|---|---|
Material Waste | High | Low |
Initial Cost | Low | High |
Maintenance | Simple | Complex |
Cycle Time | Longer | Shorter |
Optimizing the runner size is another critical aspect. The runner diameter should be appropriate for the part size and shape. A larger diameter increases material use, whereas a smaller one may raise the filling pressure, affecting quality. Similarly, controlling runner length helps reduce material residence time and pressure loss.
Accurate Cavity Design for Enhanced Utilization
Cavity design impacts how efficiently material is used during injection molding. The number and layout of cavities must be optimized based on production needs and machine specifications. Excessive cavities can overwhelm the machine’s clamping force, compromising quality, while too few cavities decrease production efficiency.
A simplified cavity structure reduces manufacturing complexity and material usage. For parts not requiring high precision, avoiding over-design can help. For instance, eliminating unnecessary features like rounded corners or chamfers can significantly reduce material consumption without sacrificing part functionality.
By focusing on these aspects of mold design, manufacturers can effectively improve material utilization rates, leading to cost savings and enhanced production efficiency. Understanding and implementing these strategies is crucial for staying competitive in the field of injection molding.
Hot runner systems reduce material waste in molding.True
Hot runners keep plastic molten, eliminating runner waste.
Larger runner diameters decrease material usage.False
Larger diameters increase material use, not decrease it.
How Can Process Parameters Influence Material Efficiency?
In injection molding, process parameters are crucial in determining how efficiently materials are used, impacting both costs and environmental footprint.
Process parameters such as injection pressure, speed, and temperature directly affect material efficiency in injection molding by influencing the quality of parts and minimizing waste.
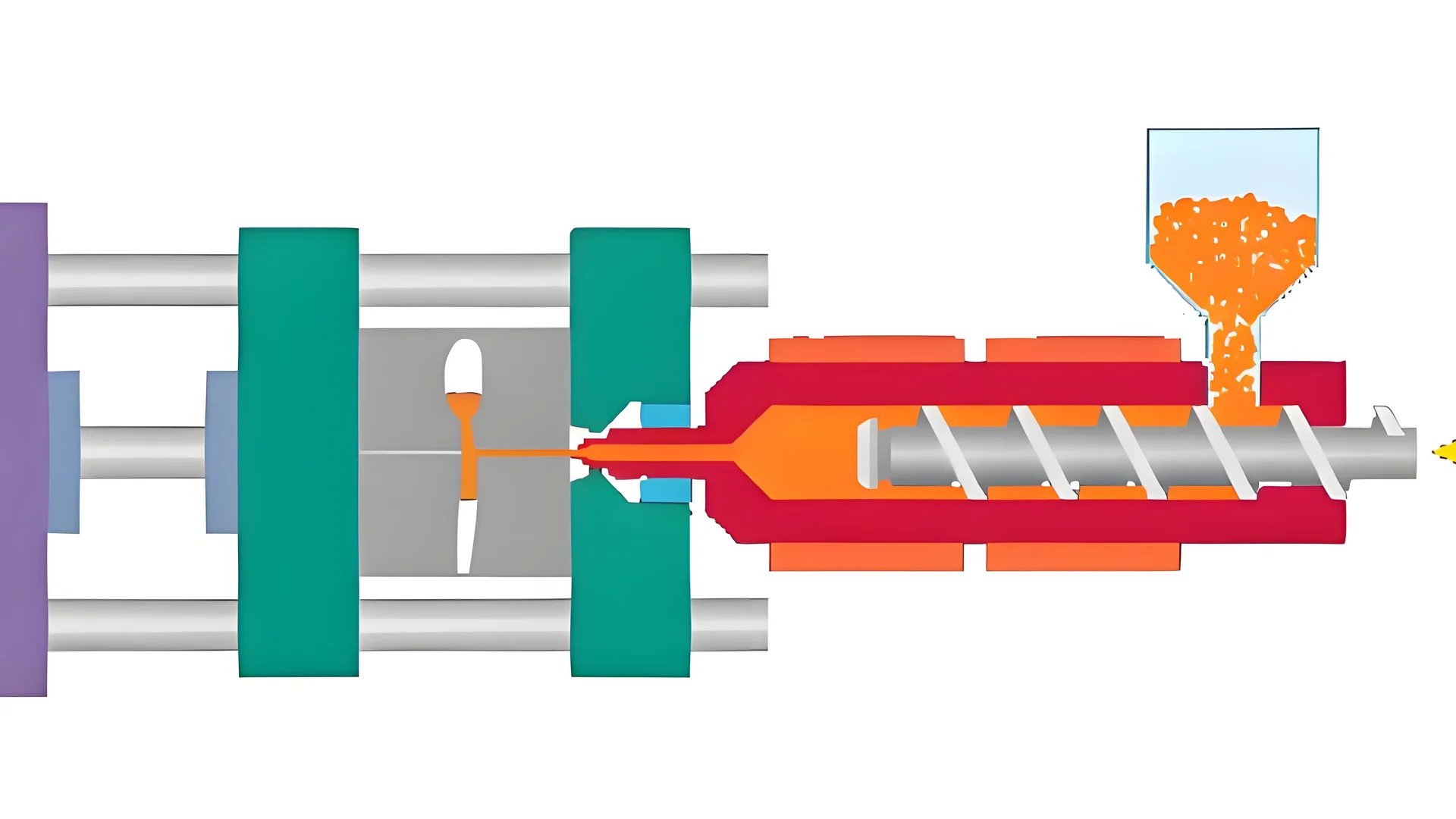
Understanding Injection Pressure and Speed
In injection molding, selecting appropriate injection pressure and speed2 is vital to ensure the melt fills the mold cavity effectively without causing excess material waste. The pressure must be calibrated to avoid overpacking the mold, which can lead to flash, a common defect that necessitates additional trimming and material loss.
For example, higher speeds and pressures are typically needed for thin-walled parts to ensure complete filling. Conversely, lower speeds and pressures can be used for thicker parts to prevent defects like internal stress or shrinkage. This balance not only preserves material but also maintains the integrity of the molded part.
Importance of Temperature Control
Temperature control within the injection molding machine, including barrel, nozzle, and mold temperatures, is another critical parameter. Each type of plastic has its own optimal temperature range that ensures proper flow and filling. If the temperature is too high, plastics may degrade, leading to compromised part quality and wasted material. If too low, increased viscosity can impede flow, requiring more pressure and potentially causing incomplete fills.
Precise temperature adjustments tailored to specific plastics can significantly enhance material efficiency. For instance, crystalline plastics3 benefit from higher mold temperatures to improve crystallinity and part strength, whereas non-crystalline plastics perform better with lower temperatures to speed up cycle times.
Utilizing Automation for Parameter Optimization
With advancements in technology, automated systems can now adjust these parameters in real-time based on feedback from sensors embedded in the molds. This not only optimizes material usage by reducing variability but also enhances overall production efficiency.
An automated system continuously monitors factors like mold temperature and pressure within the cavity, adjusting parameters on-the-fly to maintain optimal conditions. This results in reduced cycle times and less material waste due to defects, demonstrating the significant role of technology in modern manufacturing processes.
Higher injection pressure reduces material waste.False
Higher pressure can cause defects like flash, increasing waste.
Automated systems optimize injection molding efficiency.True
Automation adjusts parameters in real-time, reducing waste and cycle time.
Why Is Material Management Crucial in Injection Molding?
In injection molding, effective material management is essential for minimizing waste and maximizing efficiency.
Material management in injection molding is crucial because it ensures optimal use of materials, reduces costs, and enhances environmental sustainability. Proper material selection, handling, and processing prevent defects and waste, leading to higher-quality products and improved profitability.
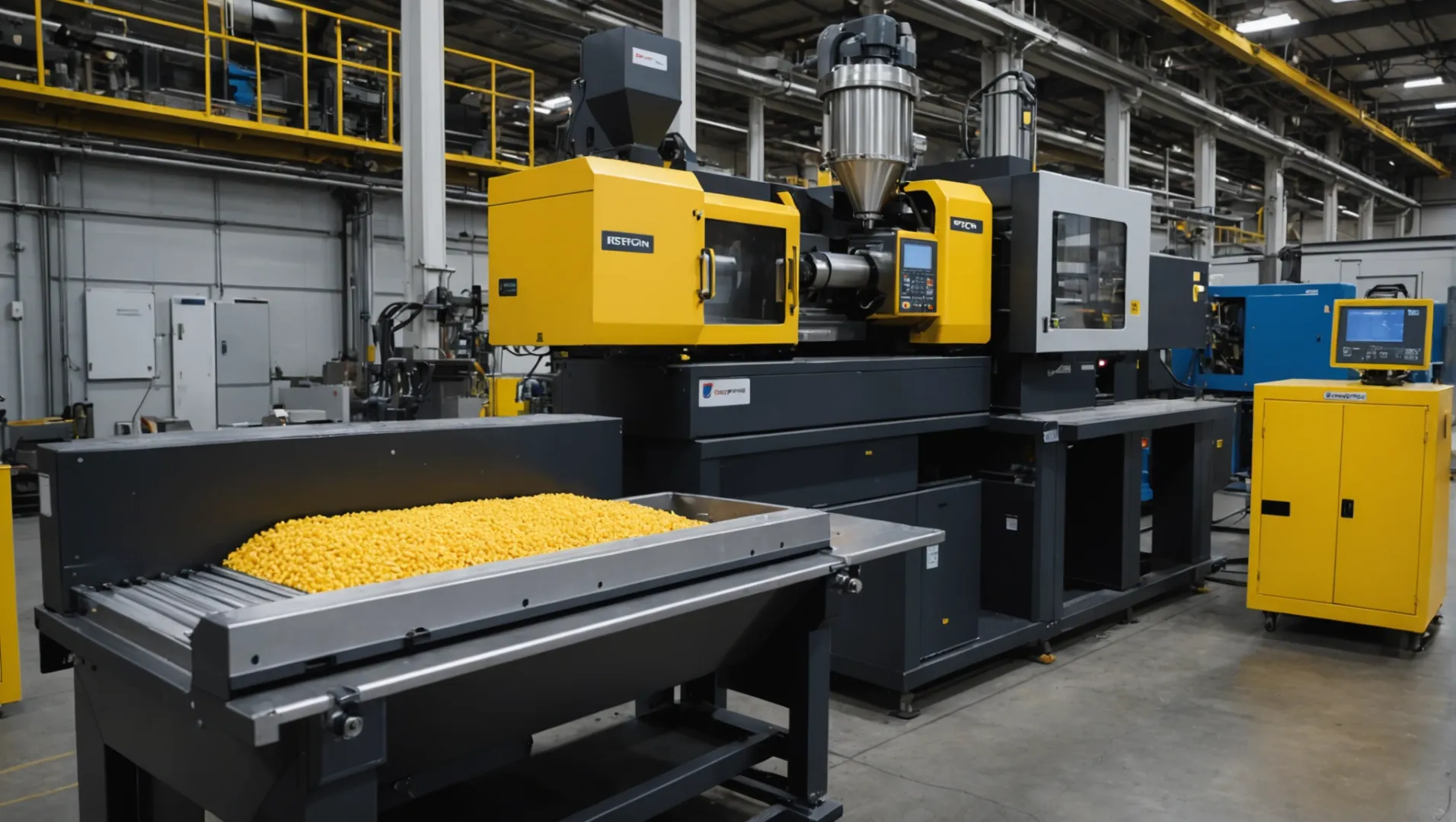
Choosing the Right Plastic Material
Selecting the appropriate plastic material is a fundamental step in material management4 for injection molding. Different materials come with unique properties that impact the final product’s performance. For instance, opting for materials that offer the necessary strength and durability can reduce the need for excess material to achieve the desired quality.
Moreover, choosing environmentally friendly and recyclable materials not only minimizes environmental impact but also enhances a company’s reputation. This approach aligns with the increasing demand for sustainable practices in manufacturing.
Optimizing Material Drying and Processing
Proper drying and processing of materials are essential to maintain their quality. Moisture in plastic pellets can lead to defects such as bubbles or voids in the final product. Therefore, ensuring that materials are adequately dried before use is crucial.
Specialized drying techniques may be required for high-performance or engineering plastics to maintain their properties. This step is critical for preventing waste due to substandard products.
Material Type | Drying Technique | Benefits |
---|---|---|
Standard Plastics | Conventional Oven Drying | Cost-effective, simple |
Engineering Plastics | Dehumidifying Dryers | Maintains material integrity |
High-Performance Plastics | Vacuum Drying | Preserves material properties |
Implementing Efficient Handling Practices
Improving how materials are handled within the production environment can significantly impact material utilization. Training employees on correct material handling methods reduces the risk of contamination and waste. Encouraging conservation awareness among staff ensures that every step of the process is optimized for efficiency.
Utilizing a Quality Management System
A robust quality management system helps in monitoring the injection molding process closely. By implementing strict quality controls and regular inspections, any potential issues can be identified early, preventing large-scale material waste.
Additionally, classifying and recycling waste effectively contributes to better material management. Repairable waste can be reused, while non-repairable waste should be recycled responsibly.
By focusing on these aspects of material management, companies can not only improve their production efficiency but also reduce costs and contribute positively to environmental sustainability.
Proper drying prevents defects in injection molding.True
Moisture in plastic pellets causes bubbles or voids, affecting quality.
Using any plastic material ensures product durability.False
Material properties affect performance; wrong choices lead to poor quality.
How Can Production Management Elevate Material Utilization?
In the world of injection molding, production management holds the key to unlocking optimal material utilization and minimizing waste.
Production management can elevate material utilization by focusing on employee training, implementing quality systems, and optimizing production schedules. These measures ensure efficient use of materials, enhance operational skills, and improve product quality.
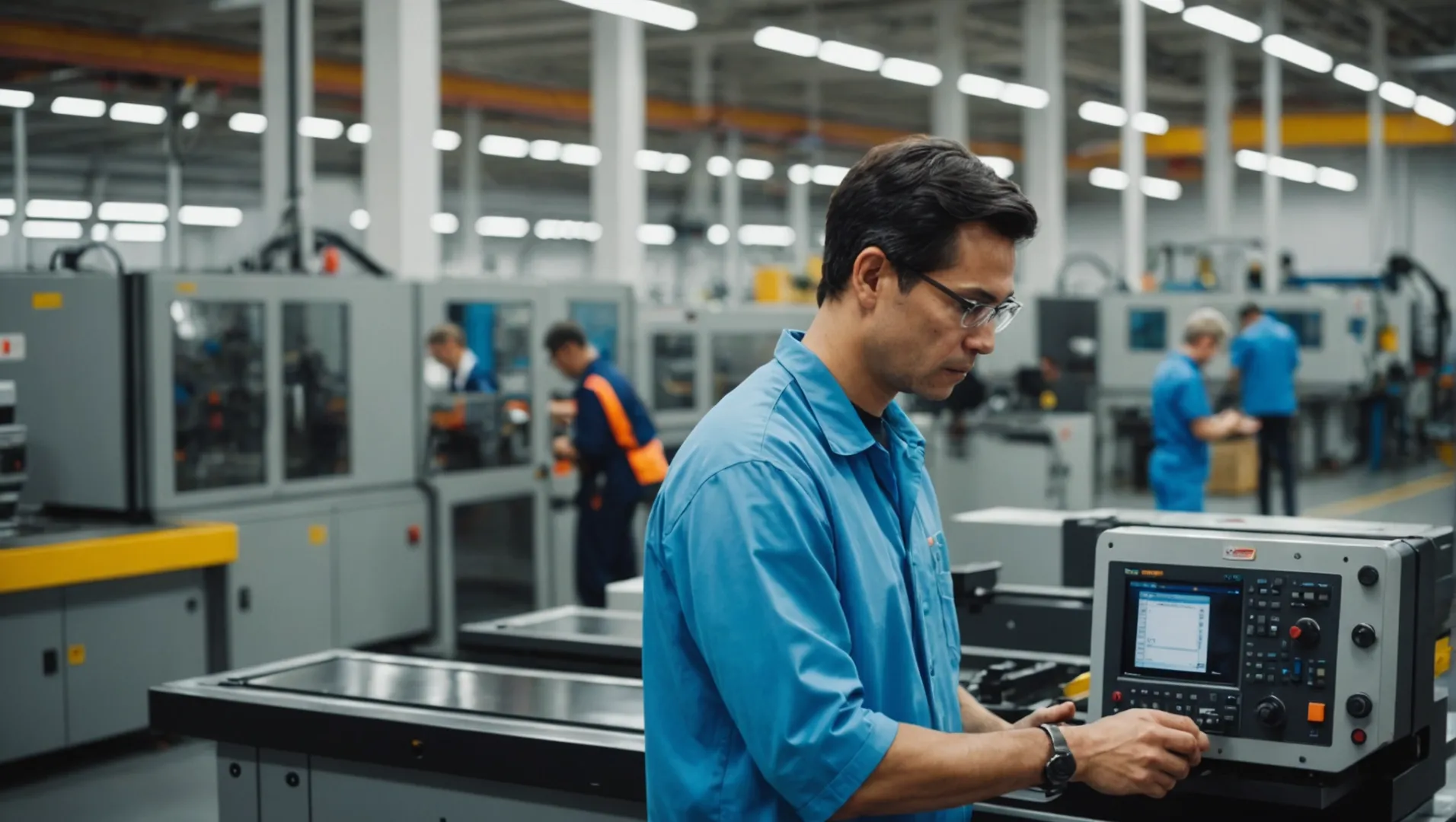
Employee Training: The Foundation of Efficient Production
One crucial aspect of production management is the comprehensive training of employees involved in the injection molding process. Skilled operators who understand the nuances of mold adjustments, parameter settings, and material handling can significantly reduce material waste. By fostering a culture of continuous learning and improvement, companies can ensure that their workforce is well-equipped to minimize errors and enhance material utilization. Training programs that emphasize quality control techniques5 and efficient operation practices can be pivotal in achieving these goals.
Implementing a Robust Quality Management System
A thorough quality management system (QMS) is another powerful tool in optimizing material utilization. By implementing rigorous quality checks and monitoring protocols throughout the injection molding process, companies can swiftly identify defects and reduce scrap rates. A QMS not only helps in maintaining high product standards but also plays a role in recycling efforts. By classifying waste into repairable and recyclable categories, firms can further minimize material wastage. Explore how effective quality management6 systems can transform your production outcomes.
Strategic Production Planning and Scheduling
Strategic planning and scheduling are vital components of effective production management. By aligning production plans with order requirements and capacity, businesses can avoid unnecessary mold changes and process adjustments that lead to material waste. Additionally, optimizing equipment utilization through well-coordinated scheduling enhances production efficiency. It’s essential to consider production flow and avoid bottlenecks that can lead to idle material, thus maximizing resource use. Learn more about smart scheduling techniques7 to boost your manufacturing efficacy.
Table: Key Areas of Focus for Material Utilization
Area | Focus | Benefit |
---|---|---|
Employee Training | Skill development | Reduced errors & waste |
Quality Management | Rigorous inspections | Lower scrap rate |
Production Scheduling | Efficient planning | Maximized equipment utilization |
By concentrating efforts on these key areas, production management not only enhances material utilization but also drives the overall efficiency of the manufacturing process. As companies continue to evolve their strategies in response to changing market dynamics, these practices remain central to achieving sustainable production goals.
Employee training reduces material waste.True
Skilled operators minimize errors, leading to less waste.
Quality management systems increase scrap rates.False
Quality systems reduce defects and scrap, enhancing utilization.
Conclusion
Improving material utilization in injection molding not only cuts waste but also boosts efficiency. Implement these strategies to enhance your operations and embrace sustainability.
-
Hot runners reduce waste, enhance efficiency by keeping plastics molten.: Also, with hot runner systems, lower injection pressures can generally be used, which will reduce mold and platen deflection and keep flash … ↩
-
Learn how pressure and speed settings impact material usage.: The injection pressure determines the amount of material that comes out of the nozzle and the velocity. Impact of Injection Pressure in … ↩
-
Explore optimal temperature settings for crystalline plastics.: Crystallization proceeds very rapidly at a temperature midway between the melting point and glass-transition temperature of the polymer. As the … ↩
-
Explore how material choices impact injection molding efficiency.: Learn how to select the right material for your injection molding design with this technical overview of thermoplastic resins. ↩
-
Discover techniques that enhance quality control and minimize waste.: The first stage is the design stage, followed by Mold and Pre-Production Inspection and In Process Quality Control and Final Inspection. ↩
-
Explore how a robust QMS can improve efficiency and reduce defects.: 1. Improved Customer Satisfaction · 2. Enhanced Efficiency · 3. Better Decision-Making · 4. Increased Employee Engagement · 5. Compliance with … ↩
-
Learn about methods to optimize production schedules for efficiency.: Production planning and scheduling involve setting targets and creating a detailed plan to meet customer demand in a timely and cost-effective manner. ↩