Have you ever thought about what it takes to create perfect plastic parts? Let me take you on a journey through the world of injection molding precision!
To improve the precision of injection molds, focus on optimizing design structures, using advanced processing equipment, and implementing strict quality control measures. Proper maintenance and regular calibration are also key to maintaining mold accuracy over time.
But wait! There’s so much more to this process. Stick around as we uncover deeper insights and advanced methods that can truly transform your molding experience.
Temperature control affects mold precision.True
Temperature influences material flow and cooling, impacting mold accuracy.
What Role Does Temperature Control Play in Mold Precision?
Temperature control is vital in achieving precision in injection molding, affecting every stage from design to final product.
Temperature control impacts mold precision by influencing material flow, cooling rates, and dimensional stability, directly affecting the quality and consistency of molded products.
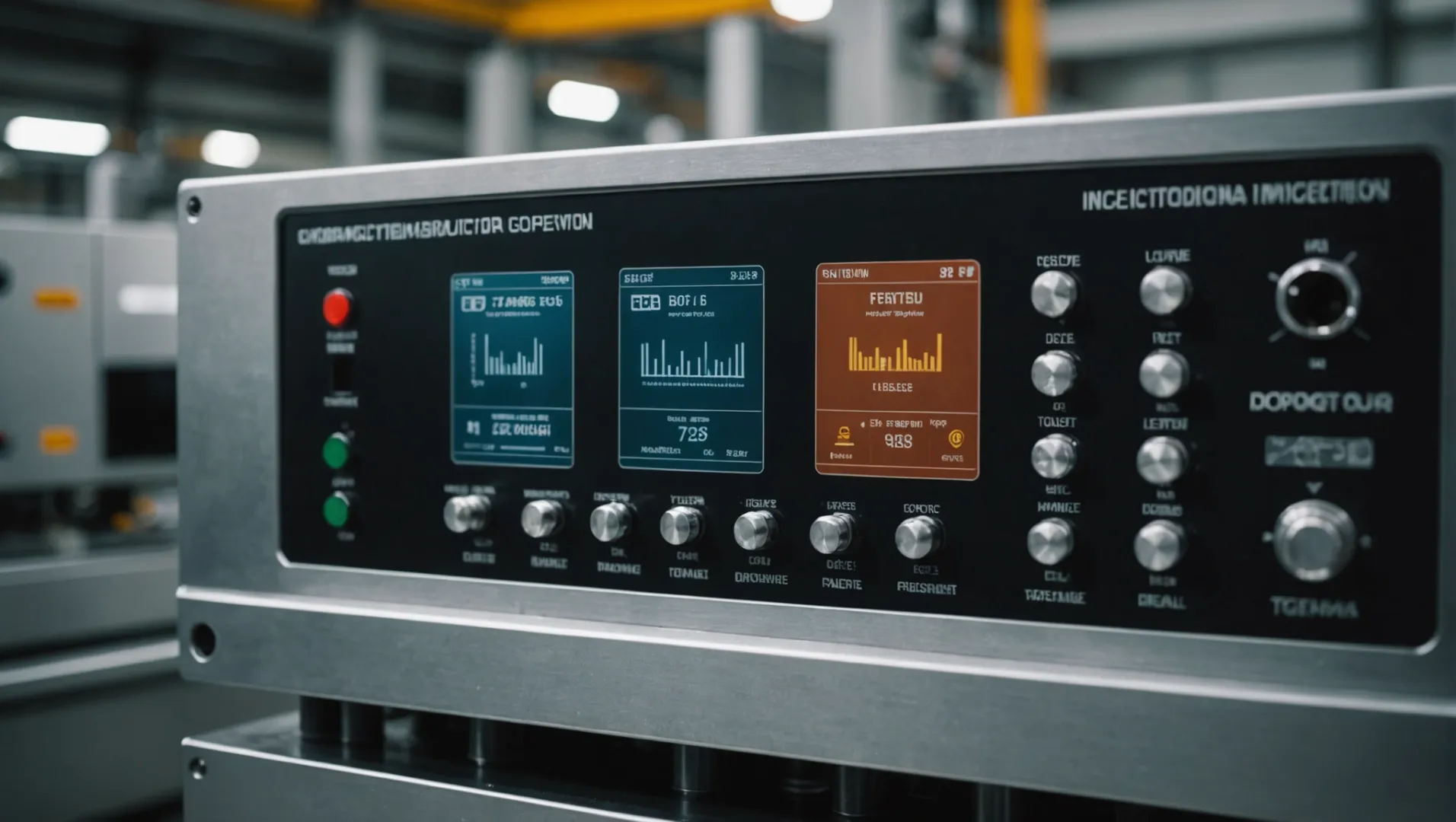
The Science Behind Temperature Control
Temperature control in injection molding is crucial because it directly affects the flow characteristics of the plastic material. The viscosity of the plastic decreases with increased temperature, allowing for easier flow through the mold. This uniform flow minimizes pressure variations and ensures that the material fills all cavities evenly.
Moreover, maintaining the correct mold temperature prevents premature cooling and solidification of the plastic, reducing defects such as warping or incomplete filling. This is especially important for complex molds with thin walls or intricate designs where uneven cooling can lead to dimensional inaccuracies.
Optimizing Mold Temperature for Precision
- Selecting Optimal Mold Temperature: The optimal temperature depends on the type of plastic used. For instance, amorphous plastics like ABS require different temperature settings compared to crystalline plastics like polypropylene. Adjusting the temperature settings based on material properties ensures optimal flow and cooling rates.
- Using Advanced Temperature Control Systems: Modern molds often incorporate advanced temperature control systems such as heaters and cooling channels. These systems allow for precise regulation of temperature across different zones of the mold, accommodating complex designs.
Impact on Different Stages of Molding
- Design Stage: During the design phase1, temperature considerations are integrated into CAD simulations to predict potential issues such as shrinkage or warping.
- Manufacturing Stage: Temperature variations are minimized through high-precision equipment that maintains consistent thermal conditions, improving component accuracy.
- Use and Maintenance Stage: Regular monitoring and maintenance of temperature control systems prevent wear and tear, ensuring long-term precision in mold operation.
Case Studies and Real-World Applications
A study on automotive parts production demonstrated that maintaining consistent mold temperatures reduced dimensional deviations by 15%, significantly improving product quality. Similarly, in medical device manufacturing, precise temperature control minimized material stress, enhancing reliability and performance.
Incorporating temperature control strategies not only boosts precision but also enhances efficiency and reduces waste, contributing to sustainable manufacturing practices.
Temperature control affects mold precision.True
Temperature control impacts material flow, cooling, and stability.
All plastics require the same mold temperature.False
Different plastics like ABS and polypropylene need specific temperatures.
How Do Tolerances Affect Injection Molding Accuracy?
Understanding tolerances is key to enhancing the accuracy of injection molding processes.
Tolerances impact injection molding accuracy by defining permissible limits for dimensional variations, ensuring components fit and function correctly. Accurate tolerances minimize defects and improve product reliability.
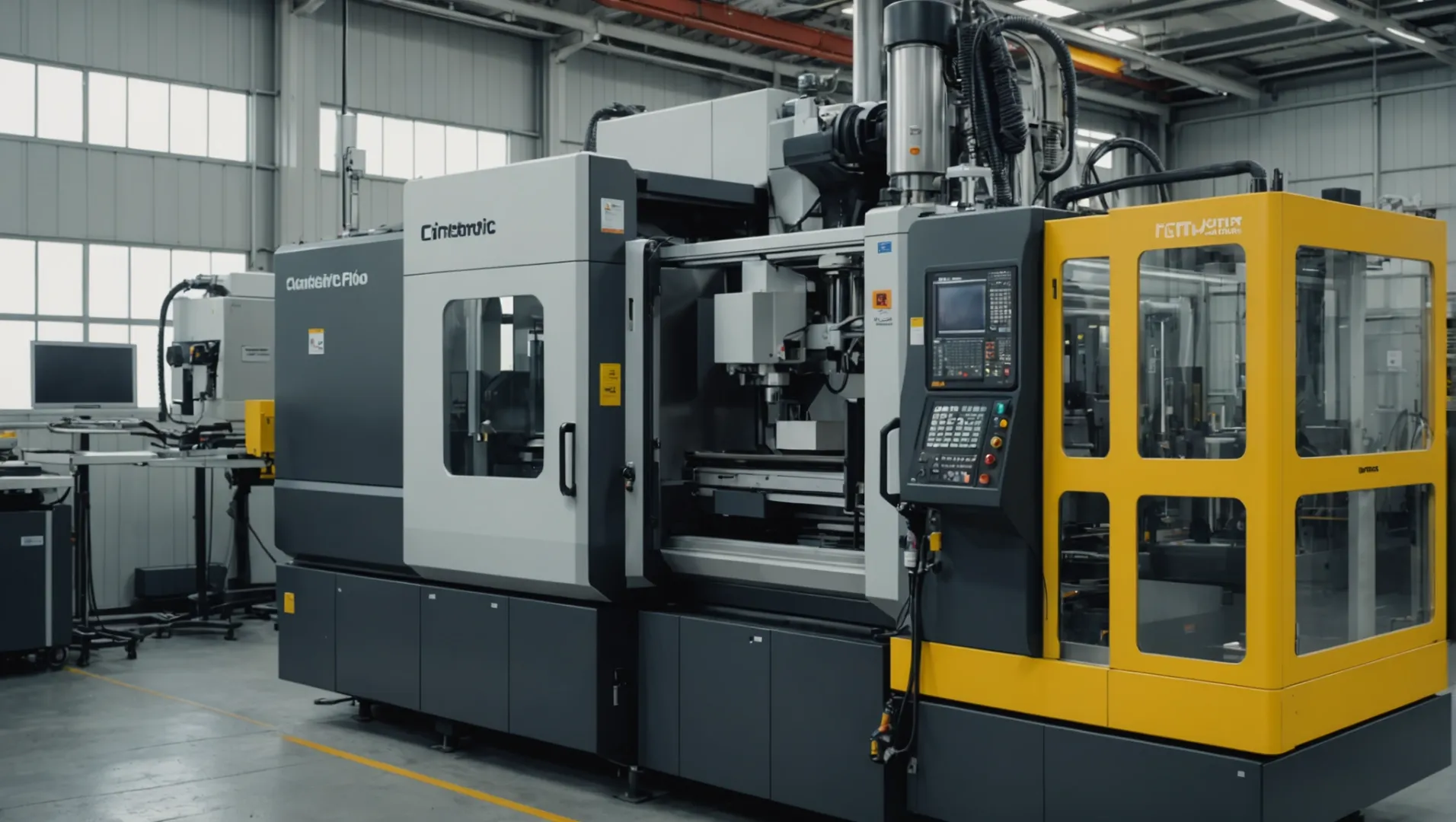
The Importance of Tolerances in Injection Molding
In injection molding, tolerances determine the allowable limits of variation in dimensions. They are crucial because even minor deviations can lead to significant product defects2 or malfunctions. Properly set tolerances ensure that each component fits seamlessly with others, maintaining the overall functionality and quality of the final product.
Factors Influencing Tolerances
- Material Properties: Different plastics have varying shrinkage rates, affecting dimensional accuracy. Understanding these properties is essential when setting tolerances.
- Mold Design: A well-designed mold can accommodate material expansion and contraction, reducing the risk of errors.
- Processing Conditions: Factors such as temperature, pressure, and cooling rate can influence the final dimensions of molded parts.
Designing with Tolerances in Mind
During the design stage, engineers must calculate tolerances considering the mold’s structural stability and symmetry. Advanced software tools like CAD/CAM allow for precise modeling and simulation, helping identify potential design flaws3 early on.
Manufacturing Precision
Using high-precision equipment is vital to maintaining tight tolerances. CNC machining centers and EDM machines are often employed to achieve the necessary accuracy. Regular maintenance and calibration of these machines further ensure their effectiveness.
Quality Control and Inspection
Implementing a rigorous quality inspection system is critical. Using equipment like coordinate measuring machines can verify that all dimensions are within specified tolerances, ensuring consistent production quality.
Understanding how tolerances affect injection molding accuracy is essential for producing reliable, high-quality components. By focusing on design precision, selecting appropriate materials, and maintaining stringent quality controls, manufacturers can greatly enhance their product’s performance.
Tolerances ensure fit and function in injection molding.True
Tolerances define limits for variations, ensuring components fit correctly.
CAD/CAM tools are unnecessary for tolerance design.False
CAD/CAM tools help in precise modeling, crucial for setting tolerances.
What Are the Latest Technologies in Mold Manufacturing?
Mold manufacturing has rapidly evolved, integrating cutting-edge technologies to enhance efficiency and precision.
The latest technologies in mold manufacturing include advanced CAD/CAM software, high-precision CNC machining, and additive manufacturing techniques. These innovations ensure higher accuracy, speed, and customization in mold production, meeting modern industrial demands.
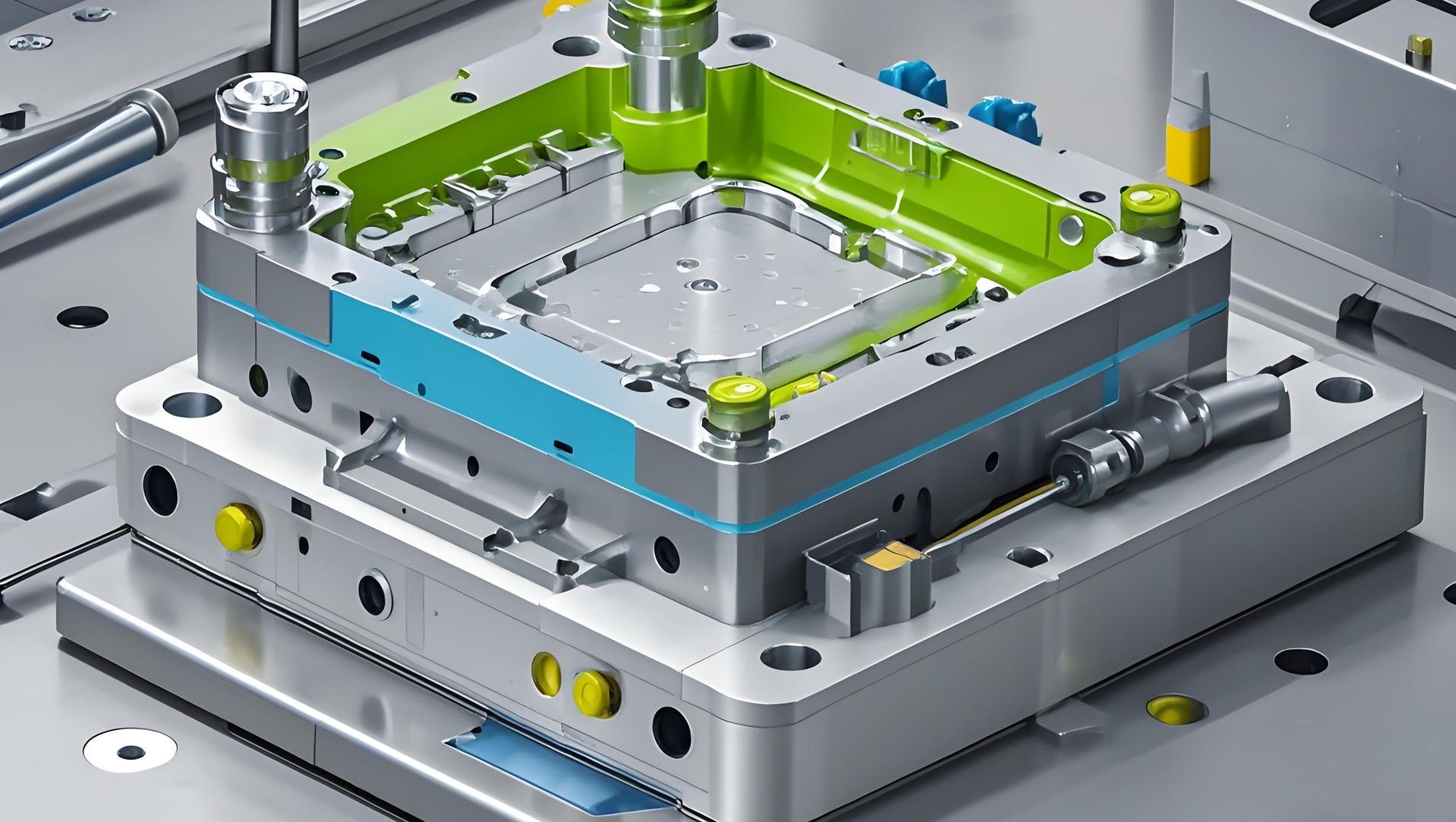
Advanced CAD/CAM Software Integration
The integration of state-of-the-art CAD/CAM software4 in mold manufacturing has revolutionized design accuracy. This software allows engineers to create precise 3D models and simulate potential issues before the actual manufacturing process begins. With simulation analysis, designers can optimize mold features such as the runner system, enhancing the flow balance of the plastic melt.
High-Precision CNC Machining
High-precision CNC (Computer Numerical Control) machining is pivotal in improving mold quality. Modern CNC machines offer unparalleled precision and repeatability, crucial for creating complex mold components. The ability to automate the machining process reduces human error and increases production speed. Regular maintenance and calibration of these machines are essential to ensure they operate at peak performance.
Additive Manufacturing Techniques
Additive manufacturing, or 3D printing, is gaining traction in mold manufacturing due to its ability to produce intricate designs that traditional methods cannot achieve. It allows for rapid prototyping, reducing the lead time from design to production. Moreover, it enables manufacturers to test and refine mold designs quickly, facilitating innovation.
Enhanced Quality Control Measures
Incorporating enhanced quality control technologies, such as laser scanning and three-coordinate measuring machines, ensures the dimensional accuracy of mold parts. These technologies provide comprehensive inspection capabilities, detecting deviations early in the process. Implementing a strict quality inspection system helps maintain the high standards required in modern manufacturing environments.
Industry 4.0 and IoT Integration
The integration of Industry 4.0 principles and IoT (Internet of Things) in mold manufacturing processes offers real-time monitoring and data analytics. These technologies enable predictive maintenance and process optimization by collecting and analyzing data from various stages of production. As a result, manufacturers can achieve higher efficiency and reduce downtime significantly.
Advanced CAD/CAM software enhances mold design accuracy.True
CAD/CAM software allows precise 3D modeling and simulation.
Additive manufacturing slows down the mold production process.False
Additive manufacturing speeds up prototyping and design refinement.
How Can Advanced Software Aid in Mold Design and Simulation?
Harnessing the power of advanced software is revolutionizing mold design and simulation, enhancing precision and efficiency.
Advanced software enhances mold design and simulation by enabling precise 3D modeling, predictive analysis, and optimization of mold structures and processes, leading to higher accuracy and efficiency in manufacturing.
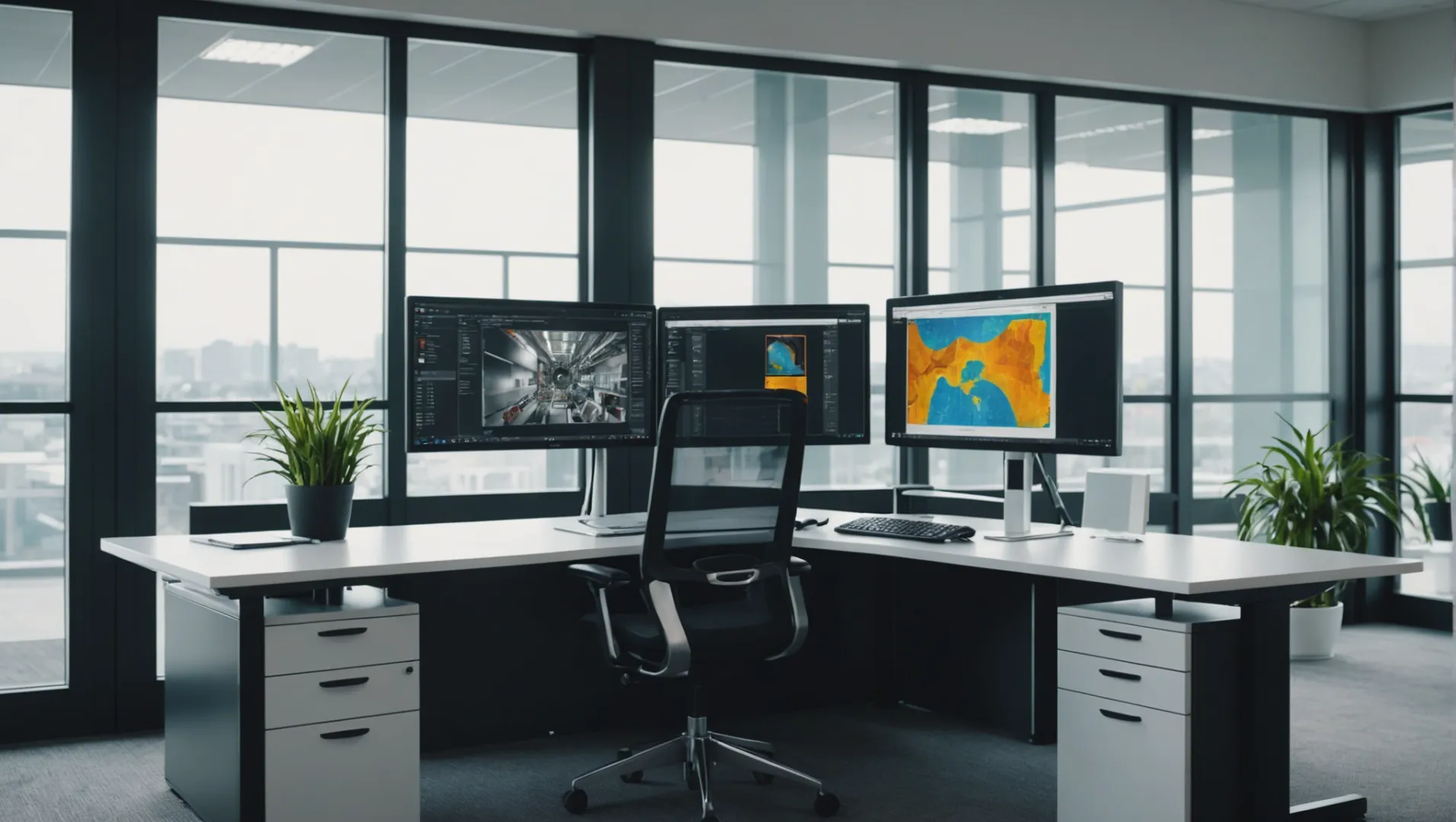
Enhancing Design Precision with 3D Modeling
Advanced CAD/CAM software is pivotal in creating accurate 3D models5 of molds, which are essential for precision engineering. These models allow designers to visualize the final product and make necessary adjustments before physical production, minimizing errors and material wastage.
Using sophisticated features like parametric modeling, designers can create complex geometries and make iterative changes swiftly. This flexibility not only saves time but also ensures that the final design meets stringent specifications without compromising structural integrity.
Predictive Analysis for Improved Outcomes
Simulation tools integrated within advanced software packages offer powerful predictive capabilities. These tools perform finite element analysis6 (FEA) and mold flow analysis, predicting how materials will behave under various conditions. This predictive analysis helps identify potential issues such as warping or uneven flow before they occur in the actual production process.
For example, by simulating the runner system, designers can ensure even distribution of material within the mold, which is crucial for maintaining uniform thickness and reducing defects.
Optimization of Mold Structures and Processes
Software-driven simulations provide insights into optimizing the structure of molds. For instance, through reinforcement of areas susceptible to deformation, software aids in creating stable, symmetrical molds that resist uneven forces during the injection process. Implementing reinforcing ribs, as suggested by experts, is one such technique that can be validated using simulation results.
Moreover, advanced software allows for continuous improvement through real-time feedback7 loops. By analyzing production data and integrating it back into the design process, manufacturers can tweak designs for better performance and longevity.
Automating Quality Control Measures
Incorporating automated quality control features within mold design software significantly enhances precision. The software can automatically check designs against predefined parameters, ensuring that each component meets the necessary criteria for quality and compliance.
By reducing reliance on manual inspections, these systems increase efficiency and reduce human error, ensuring that only top-quality molds reach the manufacturing floor.
3D modeling in mold design reduces material wastage.True
3D models allow adjustments before production, minimizing errors.
Finite Element Analysis predicts material behavior under stress.True
FEA simulates conditions to foresee potential issues like warping.
Conclusion
Embracing these strategies will empower you to enhance injection mold precision, ensuring top-notch product quality. Let’s embark on this journey toward excellence together!
- Explore how temperature affects mold design and simulation outcomes.: Temperature significantly impacts each step of the entire plastic injection molding process. This is why temperature control is crucial and … ↩
- Learn how proper tolerances reduce defects in molded products.: If an injection molding material has a higher shrink rate, tolerances are harder to control. ↩
- Discover how simulations prevent design flaws early in development.: The simulation allows manufacturers to predict potential issues such as air traps, sink marks, and weld lines before creating physical molds, … ↩
- Explore how modern CAD/CAM software enhances mold design accuracy.: Cimatron Mold is a single, integrated CAD/CAM software solution dedicated to mold making—from quoting, to design, to manufacturing. ↩
- Explore the transformative impact of 3D modeling on mold design.: well i personally felt that it would be much more better to have mold design in 3D.This is because in 3d, more complex product can be done. ↩
- Learn how FEA predicts material behavior under stress.: The Finite Element Analysis (FEA) is a specialized simulation of a physical entity using the numerical algorithm known as Finite Element … ↩
- Discover how real-time feedback improves design and production quality.: Efficiency is in everyone’s interest. However, achieving it is heavily dependent on the quality and timeliness of crucial performance data. ↩