Let’s face it—every minute counts in manufacturing. Improving injection mold change efficiency can drastically enhance productivity and minimize downtime, ensuring a seamless operation.
To improve injection mold change efficiency, focus on thorough preparation, streamlined processes, and continual optimization. This includes pre-change inspections, using quick-connect devices, and fostering team collaboration.
But wait, there’s more! If you think those initial steps are game-changers, you’ll be amazed by the deeper insights and expert tips we have to explore together.
Quick-connect devices reduce mold change time.True
Quick-connect devices streamline connections, minimizing setup time.
What Are the Key Steps in Mold Preparation?
Proper mold preparation is vital for efficient injection mold changes, minimizing downtime and ensuring quality output.
Key steps in mold preparation include thorough inspection, cleaning, maintenance, and gathering necessary tools. This ensures a smooth transition during the mold change process, preventing delays and defects.
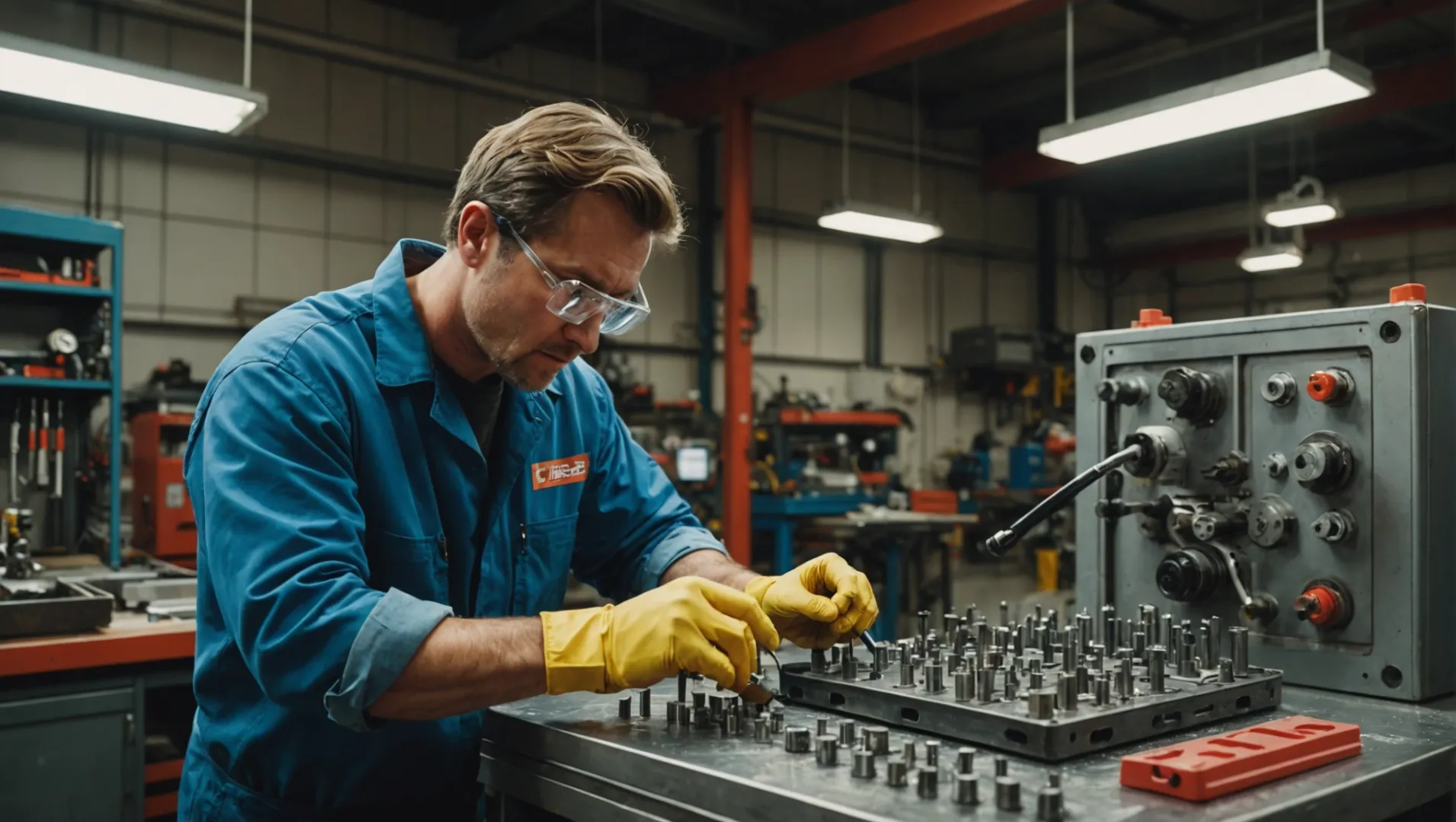
Conducting a Comprehensive Inspection
Before initiating any mold change, it’s crucial to conduct a thorough inspection of the mold. This involves checking for any visible deformities such as cracks or wear and tear. Addressing these issues beforehand can prevent significant disruptions during production. Mold inspection should also include verifying the integrity of components such as ejectors and cooling channels.
Cleaning and Maintenance
Maintaining a clean mold is essential for ensuring the quality of the products manufactured. Cleaning involves removing any oil, dust, or debris from the mold’s surface. Applying a rust inhibitor can further extend the mold’s lifespan by protecting it against environmental damage. Regular maintenance practices help in retaining the mold’s functionality and effectiveness over time.
Gathering Necessary Accessories and Tools
To avoid unnecessary delays during the mold change process, it is essential to prepare all necessary accessories and tools in advance. This includes bolts, nuts, wrenches, and any specific components required for the particular mold in use. By ensuring everything is in place before starting, the team can focus on executing the mold change efficiently without interruptions.
Tools and Accessories Needed |
---|
Bolts |
Nuts |
Wrenches |
Rings |
Equipment Preparation
Alongside preparing the mold itself, it’s imperative to ensure that the injection molding machine is ready for the new mold installation. This involves checking parameters such as temperature, pressure, and speed settings to confirm that they are within normal operating ranges. Clean the machine’s template and tie rod to facilitate smooth installation of the new mold.
Additionally, ensure that lifting equipment like cranes or forklifts are operational and ready to handle the mold safely and quickly. Checking lifting equipment safety1 regularly can prevent accidents and enhance efficiency.
Importance of Documentation
Documenting every step of the mold preparation process provides a valuable reference for future operations. Keeping records helps identify recurring issues and areas where efficiency can be improved. It also serves as a training resource for new team members, allowing them to learn from past experiences.
By following these detailed steps, you ensure that your injection molding operations are not only efficient but also consistent in delivering high-quality products.
Mold inspection checks for deformities.True
Inspecting for deformities prevents disruptions during production.
Documentation is unnecessary in mold preparation.False
Documentation helps identify issues and improve efficiency.
How Can Process Optimization Boost Efficiency?
Efficiency in operations often hinges on the meticulous optimization of processes, which can dramatically enhance productivity and minimize waste.
Process optimization boosts efficiency by eliminating redundancies, streamlining workflows, and utilizing resources effectively. It focuses on refining each step to achieve maximum output with minimal input, ultimately enhancing overall productivity.

Identifying Bottlenecks and Redundancies
One of the first steps in process optimization is to identify any bottlenecks2 or redundant steps within a workflow. By mapping out each stage of the process, you can highlight areas where delays or unnecessary repetitions occur. For example, during an injection mold change, evaluating the time spent on each task can reveal potential for time savings.
Streamlining Workflows
Once bottlenecks are identified, the next step is to streamline workflows. This involves analyzing current procedures to determine if any steps can be combined or eliminated. An effective method is to develop a standard operating procedure (SOP) that outlines each task clearly and sets a benchmark for performance. SOPs ensure that every team member understands their role, leading to smoother transitions and reduced errors.
Leveraging Technology
Integrating technology into processes can significantly boost efficiency. For instance, using automated systems3 to handle repetitive tasks reduces human error and frees up personnel for more strategic activities. In the context of mold changes, employing quick-connect devices and hydraulic connectors can drastically cut down on installation times.
Emphasizing Data-Driven Decisions
Data plays a crucial role in process optimization. By collecting data on various aspects of the operation—such as time spent, resources used, and error rates—managers can make informed decisions about where improvements are needed. Analyzing this data regularly can help in spotting trends and predicting potential issues before they escalate.
Continuous Feedback Loop
Implementing a continuous feedback loop is vital for sustaining improvements in efficiency. Encouraging team members to provide feedback on the process allows for real-time adjustments and fosters a culture of continuous improvement. Regular meetings to discuss progress and challenges ensure that the team remains aligned with organizational goals.
By focusing on these key areas, process optimization can transform inefficient operations into streamlined, productive workflows. Emphasizing these strategies not only enhances efficiency but also contributes to a more agile and responsive business environment.
Process optimization reduces operational waste.True
By eliminating redundancies and refining workflows, waste is minimized.
Data is irrelevant in process optimization.False
Data helps identify inefficiencies and informs decision-making for improvements.
Why Is Multi-Person Collaboration Essential During Mold Changes?
Multi-person collaboration in mold changes ensures efficiency, safety, and reduced downtime in manufacturing processes.
Collaboration is crucial during mold changes to ensure precision, safety, and minimized downtime. By clearly defining roles and fostering effective communication, teams can swiftly address challenges, optimize workflows, and enhance overall production efficiency.

The Importance of Role Clarity
In the context of mold changes, role clarity is paramount. Each team member should know their specific tasks, from inspecting the mold to positioning it correctly on the machine. This clarity eliminates confusion and reduces errors, ensuring that each step of the process is executed precisely.
Assigning clear responsibilities also helps in problem-solving. For instance, if a part doesn’t fit correctly or if there’s an issue with alignment, knowing who is responsible for which component can speed up troubleshooting significantly.
Enhancing Communication and Problem-Solving
Effective team communication4 is the backbone of successful multi-person collaboration. Regular briefings before and after mold changes can be used to discuss potential issues and solutions, ensuring that everyone is on the same page.
When problems arise during the mold change, a collaborative approach facilitates quick solutions. Team members can pool their knowledge and experience to address issues promptly, minimizing downtime and preventing costly delays.
Streamlining Workflows through Collaboration
Collaborative workflows are designed to be efficient. By working together, teams can streamline the mold change process by ensuring that each step is prepared in advance and that tools and equipment are ready to go.
For example, while one person may focus on cleaning and inspecting the mold, another can prepare the machine parameters for the new mold. This parallel processing saves valuable time and ensures a smoother transition from one mold to another.
Safety Considerations in Collaborative Settings
Safety is a critical concern during mold changes, especially when heavy equipment is involved. Multi-person collaboration ensures that all safety protocols are followed, such as proper lifting techniques and the use of protective gear.
By working together, team members can watch out for each other’s safety, making sure that everyone adheres to best practices and that any potential hazards are identified and mitigated quickly.
Training and Continuous Improvement
Finally, collaboration fosters an environment of continuous learning. Training sessions5 where team members share their experiences can lead to improvements in mold change efficiency. By learning from each other’s successes and challenges, teams can continuously refine their processes.
Role clarity reduces errors in mold changes.True
Clear roles prevent confusion, ensuring precise execution of tasks.
Safety protocols are less important in collaborative settings.False
Safety is crucial; collaboration ensures adherence to safety protocols.
What Role Does Continuous Improvement Play in Mold Change Efficiency?
Continuous improvement is the backbone of enhancing mold change efficiency, offering a pathway to sustained productivity gains.
Continuous improvement in mold change efficiency involves analyzing past processes, identifying bottlenecks, and implementing iterative enhancements. By recording mold change activities, training personnel, and fostering a culture of learning, businesses can streamline operations and reduce downtime.
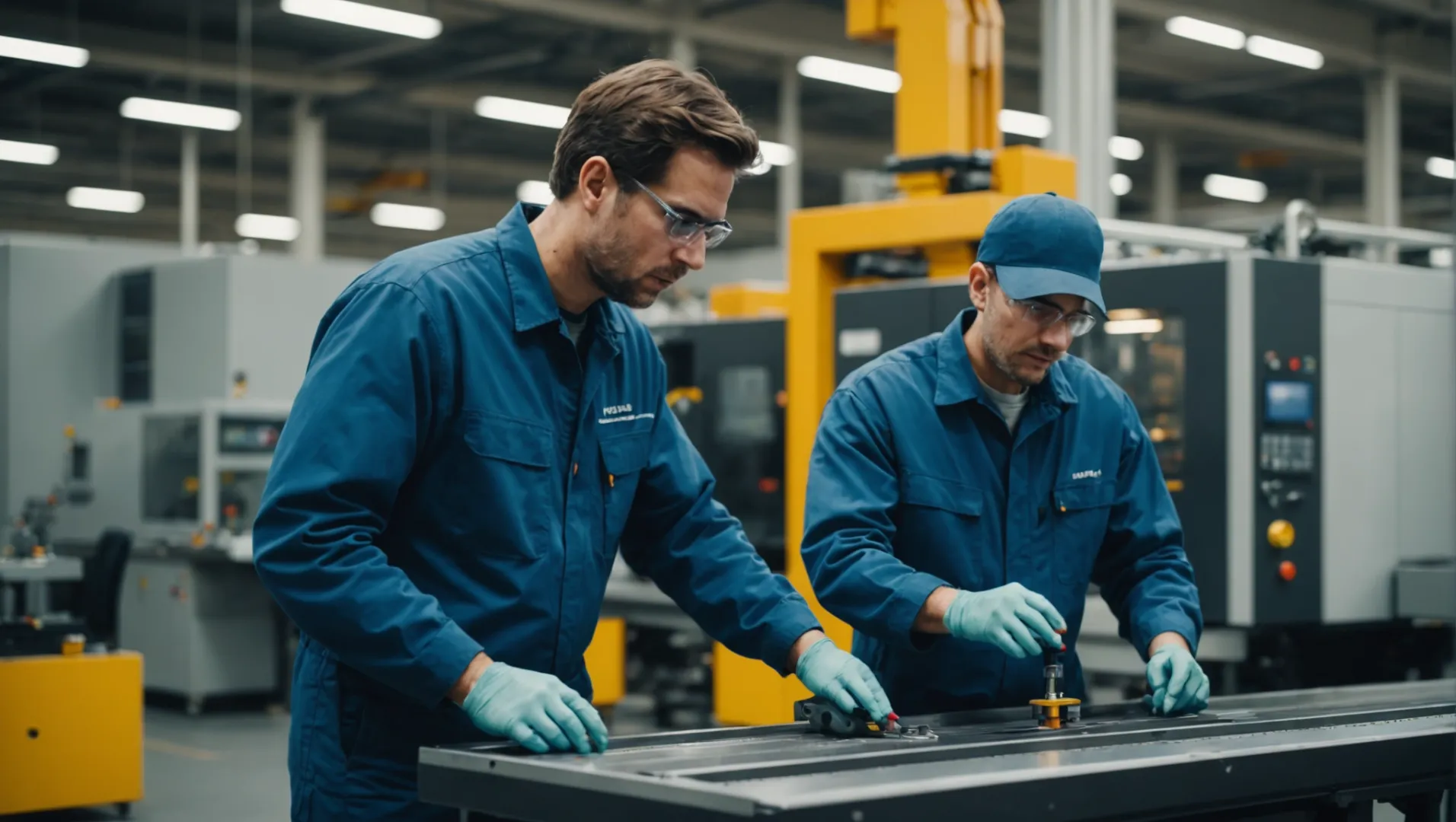
Recording and Analyzing Mold Change Processes
A critical component of continuous improvement6 in mold change efficiency is the systematic recording and analysis of each mold change process. By maintaining detailed records of time taken, encountered problems, and solutions implemented, companies can pinpoint inefficiencies and areas for improvement. Regular analysis helps identify patterns that could lead to innovative solutions and streamlined processes.
Aspect | What to Record | Purpose |
---|---|---|
Time Taken | Duration of each mold change | To identify time-consuming steps |
Encountered Issues | Problems faced during the process | To understand recurring challenges |
Solutions | Effective solutions applied | To replicate successful strategies in future changes |
Training and Education for Enhanced Efficiency
The role of training7 cannot be overstated when aiming for continuous improvement. Training programs should focus on enhancing operators’ technical skills and their awareness of mold change efficiency. By investing in education, companies empower their teams to execute mold changes more proficiently, leading to less downtime and higher productivity.
Training sessions should include:
- Hands-on Workshops: Allow operators to practice under supervision.
- Feedback Mechanisms: Encourage sharing of experiences to learn collectively.
- Regular Updates: Keep the team informed about new technologies or methods.
Fostering a Culture of Learning and Communication
Creating an environment that promotes open communication and collaborative learning8 is essential for continuous improvement. Encouraging team members to share their experiences and insights can lead to collective problem-solving and innovation. Regular meetings or forums where ideas are exchanged can accelerate the improvement process.
- Team Meetings: Schedule regular check-ins to discuss mold change processes.
- Suggestion Box: Implement a system where team members can propose new ideas.
- Cross-Training: Encourage learning across different roles to build versatile teams.
Conclusion
While continuous improvement is a journey rather than a destination, the benefits it brings to mold change efficiency are substantial. By embedding a mindset of constant enhancement in your operations, you can achieve not only greater efficiency but also a competitive edge in the manufacturing industry.
Recording mold changes helps identify inefficiencies.True
Systematic recording reveals patterns and bottlenecks in processes.
Training reduces downtime in mold change operations.True
Training enhances skills, leading to more efficient mold changes.
Conclusion
By embracing these strategies, you’ll not only enhance your injection mold change efficiency but also create a thriving environment where productivity soars.
-
Ensures safety and prevents accidents during mold changes.: Inspecting lifting equipment will help you to identify any damage or wear and tear before putting them into use. This will help to avert accidents at … ↩
-
Discover techniques for identifying and resolving workflow bottlenecks.: A bottleneck analysis, also known as a root cause analysis, is the best approach to identifying bottlenecks and finding ways to solve them. ↩
-
Learn how automation can enhance efficiency in manufacturing.: The benefits of automation in production result in better-quality products, boosted productivity, higher sales and an improved bottom line. It can even drive … ↩
-
Learn how improved communication can optimize manufacturing efficiency.: Manufacturing Employees Are Demanding More Flexibility Than Ever Before. Better production floor communication for employees is often about better listening. ↩
-
Discover why training enhances team performance in manufacturing.: The fact that a person has more tools to be successful strengthens their confidence and motivation at work. ↩
-
Discover methods to implement continuous improvement effectively.: The primary goals of continuous improvement in manufacturing include increasing productivity and efficiency, eradicating waste and improving both employee … ↩
-
Understand why training is crucial for operational efficiency.: Another significant advantage of training is the effect it has on the retention of talent. We could say that this derives from the other points … ↩
-
Learn how collaborative learning enhances team performance.: 11 benefits of collaborative learning · 1. Improves problem-solving skills · 2. Encourages social interaction · 3. Promotes diversity · 4. Improves … ↩