Are you grappling with inconsistent part sizes in your injection molding process? Trust me, you’re not alone!
To improve dimensional stability in injection molding, focus on selecting the right plastic resin, designing accurate molds, optimizing injection process parameters, and implementing thorough quality control. These steps help ensure consistent product dimensions and reduce defects.
While these basic steps provide a solid foundation, diving deeper into each aspect reveals specific strategies that can significantly enhance dimensional stability. Let’s explore these techniques together!
Choosing the right resin minimizes shrinkage in injection molding.True
Proper resin selection reduces shrinkage, enhancing dimensional stability.
How Does Raw Material Selection Affect Dimensional Stability?
Raw material selection is crucial in determining the dimensional stability of injection-molded products. Choosing the right resin and ensuring material quality can minimize shrinkage and deviations.
Selecting appropriate raw materials significantly impacts dimensional stability by influencing shrinkage, stability, and the uniformity of the final product. The choice of resin and control over impurities and moisture are key factors.
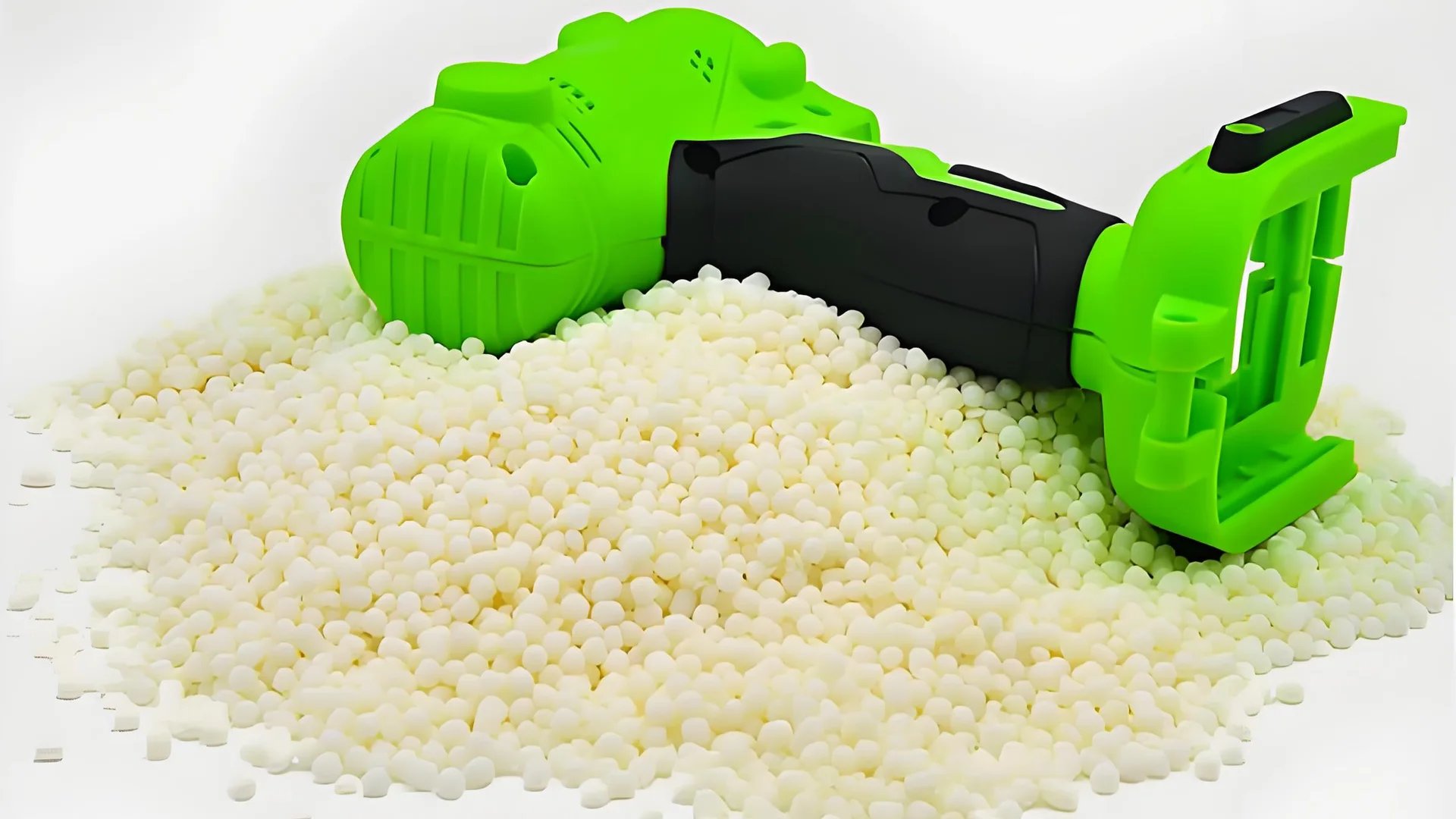
Choosing the Right Plastic Resin
The selection of plastic resin1 plays a pivotal role in ensuring dimensional stability. Different resins exhibit varying degrees of shrinkage and thermal expansion. For instance, resins with low crystallinity, such as amorphous polymers, tend to offer better dimensional stability due to their consistent molecular structure.
- Resin Characteristics: The molecular weight distribution and crystallinity of the resin are critical. Resins with narrow molecular weight distribution are less prone to variations in shrinkage and warping.
- Fluidity Considerations: High fluidity resins fill molds more uniformly, reducing the likelihood of dimensional discrepancies due to incomplete filling.
Controlling Raw Material Quality
Consistency and purity of raw materials are equally important. Impurities and uneven compositions can lead to defects such as warping or surface irregularities.
- Supplier Reliability: Opting for reliable suppliers ensures that the raw material’s quality remains consistent across batches.
- Moisture Management: Moisture content in raw materials can significantly affect the dimensional stability, leading to problems such as silver streaks or voids. Ensuring proper drying protocols based on resin type can mitigate these issues.
Table: Impact of Material Properties on Dimensional Stability
Material Property | Effect on Dimensional Stability |
---|---|
Molecular Weight Distribution | Affects shrinkage consistency |
Crystallinity | Influences thermal expansion and accuracy |
Fluidity | Enhances mold filling and reduces deviations |
Moisture Content | Can cause surface defects if not properly managed |
Conclusion
Incorporating a strategic approach to raw material selection2 can greatly enhance the dimensional stability of injection-molded products. By focusing on resin characteristics and stringent quality controls, manufacturers can achieve high precision in their molded parts.
Resins with low crystallinity have better dimensional stability.True
Low crystallinity resins offer consistent molecular structure, reducing shrinkage.
Moisture content in raw materials does not affect stability.False
Moisture can cause defects like silver streaks, affecting stability.
What Role Does Mold Design Play in Achieving Precision?
Mold design is a critical factor in ensuring the precision of injection-molded parts.
Mold design significantly influences precision in injection molding by determining the dimensional accuracy, surface quality, and stability of parts. Key aspects include the mold structure, cooling system, and manufacturing processes that collectively reduce defects and improve product quality.
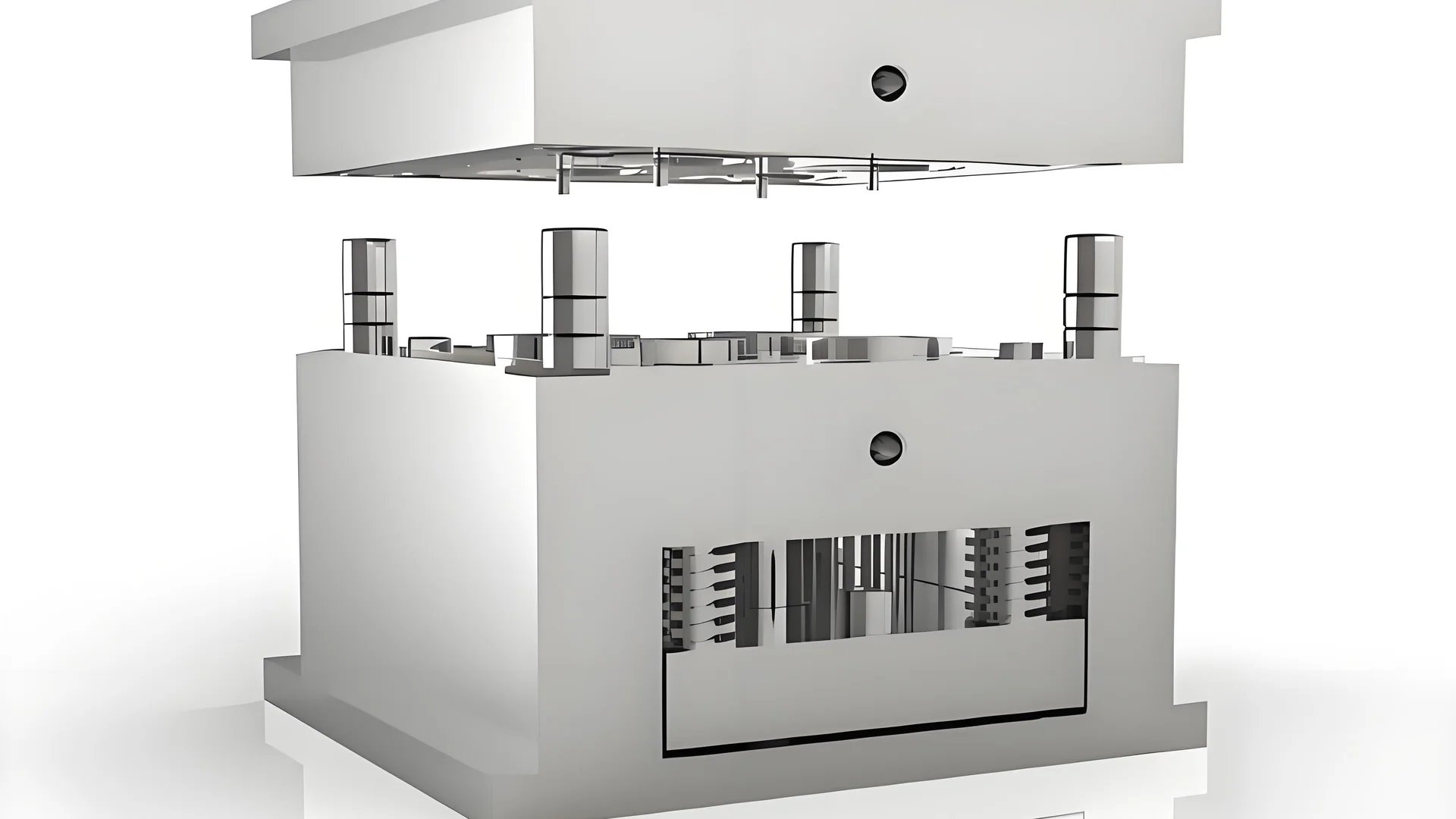
Understanding Mold Structure
The mold structure forms the foundation of precision in injection molding3. A well-designed mold structure accounts for parting lines and gate positions, which are pivotal in ensuring even filling of the mold cavity. This reduces the likelihood of warping and dimensional deviations.
Parting Surface and Gate Design
The positioning of the parting surface should minimize disruptions at critical dimensions. By carefully selecting gate locations, manufacturers can ensure uniform flow and pressure distribution, reducing inconsistencies.
Simulation Software
Utilizing simulation software for mold design can preemptively identify potential issues such as air traps or weld lines. By rectifying these issues early, manufacturers can enhance the precision and reliability of the molding process.
Cooling System Design
Effective cooling system design is another cornerstone of achieving high precision in molded parts. Uniform cooling helps mitigate differential shrinkage, which is a common cause of dimensional inaccuracies.
-
Cooling Channels Layout: The layout should be optimized to ensure consistent temperature across the mold. This requires precise calculations and sometimes innovative designs to cater to complex part geometries.
-
Thermal Analysis: Conducting a thorough thermal analysis can highlight hot spots or areas with uneven cooling, allowing for adjustments that enhance dimensional stability.
High-Precision Mold Manufacturing
Once the design phase is optimized, translating it into a physical mold with high precision is crucial.
-
Advanced Processing Equipment: Utilizing state-of-the-art CNC machines and high-precision tools ensures that each mold component adheres to exact specifications, minimizing errors in final parts.
-
Surface Treatments: Polishing and surface treatments reduce friction during demolding, which not only facilitates easier part removal but also preserves the integrity and dimensions of the molded components.
The Impact of High-Precision Molds on Production
High-precision molds deliver multiple benefits:
Benefit | Description |
---|---|
Improved Part Quality | Higher dimensional accuracy and surface finish |
Increased Efficiency | Reduced cycle times due to efficient demolding |
Cost Savings | Fewer defects lead to less material waste |
Overall, the intricacies of mold design directly affect production outcomes. By focusing on precision in each design aspect—from structural layout to cooling system efficiency—manufacturers can consistently achieve high-quality, precise parts. Explore more about advanced mold technologies4 to see how they can be applied to your processes.
Simulation software identifies mold design issues early.True
Simulation software helps predict and rectify mold design flaws before production.
Cooling system design does not affect mold precision.False
Effective cooling systems ensure uniform temperature, reducing dimensional inaccuracies.
Which Process Parameters Are Crucial for Dimensional Accuracy?
Understanding key process parameters is essential to achieving precise dimensions in injection molded parts.
Crucial process parameters for dimensional accuracy include temperature, pressure, speed, and time control. These parameters impact how materials fill and solidify within molds, directly influencing the final dimensions. Properly adjusting and monitoring these factors ensures minimal shrinkage and warping, enhancing overall precision.
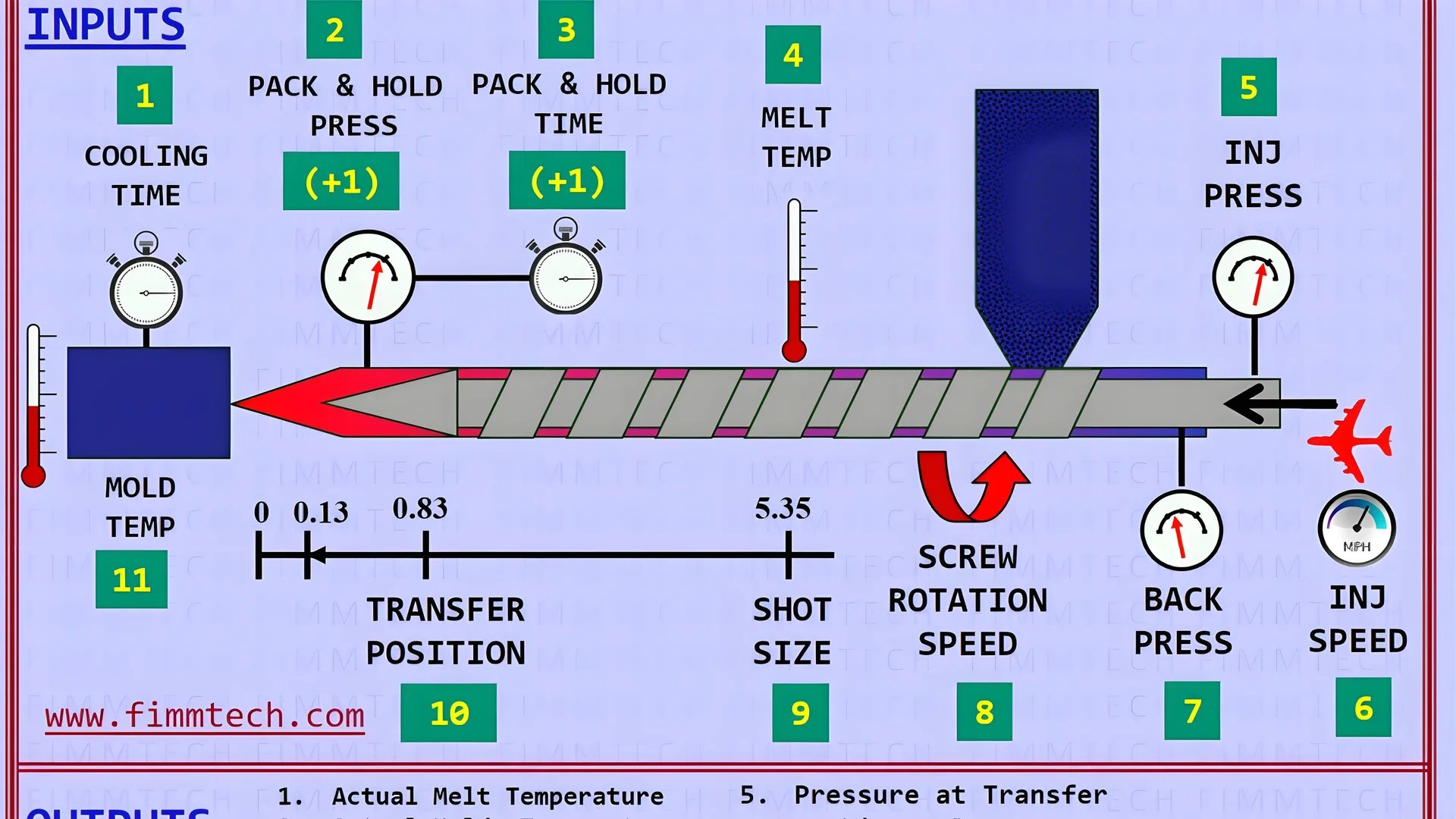
Temperature Control
Temperature significantly influences the fluidity of the plastic resin and its ability to fill the mold completely. The three main temperature zones to manage are:
- Barrel Temperature: It affects the melting of the resin. Too high a temperature can degrade the material, while too low may result in incomplete filling.
- Nozzle Temperature: Ensures the material remains molten as it enters the mold.
- Mold Temperature: Affects the cooling rate of the resin, impacting shrinkage and crystallinity.
Implementing stable temperature control systems is crucial. For instance, maintaining consistent barrel temperatures5 can prevent fluctuations that lead to inconsistent part dimensions.
Pressure Control
Injection pressure, holding pressure, and back pressure are pivotal for ensuring complete mold filling and reducing defects like sink marks:
- Injection Pressure: Determines how effectively the resin is injected into the mold cavity. Insufficient pressure can lead to incomplete parts.
- Holding Pressure: Maintains pressure on the resin during cooling to counteract shrinkage.
- Back Pressure: Impacts the melt quality by ensuring proper homogenization of the material.
Fine-tuning these pressures based on material type and mold design can lead to significant improvements in dimensional accuracy. Explore strategies to optimize injection pressure settings6 for better results.
Speed Control
Adjusting speeds during different phases of injection molding—such as injection, holding, and cooling—can minimize dimensional deviations:
- Injection Speed: Affects how quickly the mold fills. High speeds might lead to turbulence and air entrapment.
- Holding Speed: Influences how uniformly pressure is applied during solidification.
- Cooling Speed: Impacts how evenly the part cools, affecting internal stresses and shrinkage.
Conduct experiments to establish the ideal speed settings that balance flow with material properties. Consider exploring how cooling speed adjustments7 can enhance dimensional precision.
Time Control
Properly timed cycles ensure materials are neither under nor overprocessed, which can affect size consistency:
- Injection Time: Dictates how quickly material is injected into the mold.
- Holding Time: Ensures pressure is maintained until the gate freezes.
- Cooling Time: Allows sufficient solidification before ejection to minimize post-molding shrinkage.
Experimentation with these timings based on product specifications can help achieve better accuracy. Discover effective cooling time strategies8 that optimize dimensional outcomes.
Together, these process parameters form the backbone of achieving dimensional accuracy in injection molding. By carefully adjusting and monitoring these factors, manufacturers can reduce waste and improve product quality.
Barrel temperature affects resin melting.True
Correct barrel temperature ensures resin melts evenly, preventing defects.
High injection speed reduces air entrapment.False
High speeds can cause turbulence, increasing air entrapment risk.
How Can Post-Processing Enhance Dimensional Stability?
Post-processing can be the unsung hero in achieving dimensional stability for injection molded parts.
Post-processing techniques such as annealing and humidity adjustment can significantly enhance dimensional stability by relieving internal stresses and balancing moisture content in plastics.
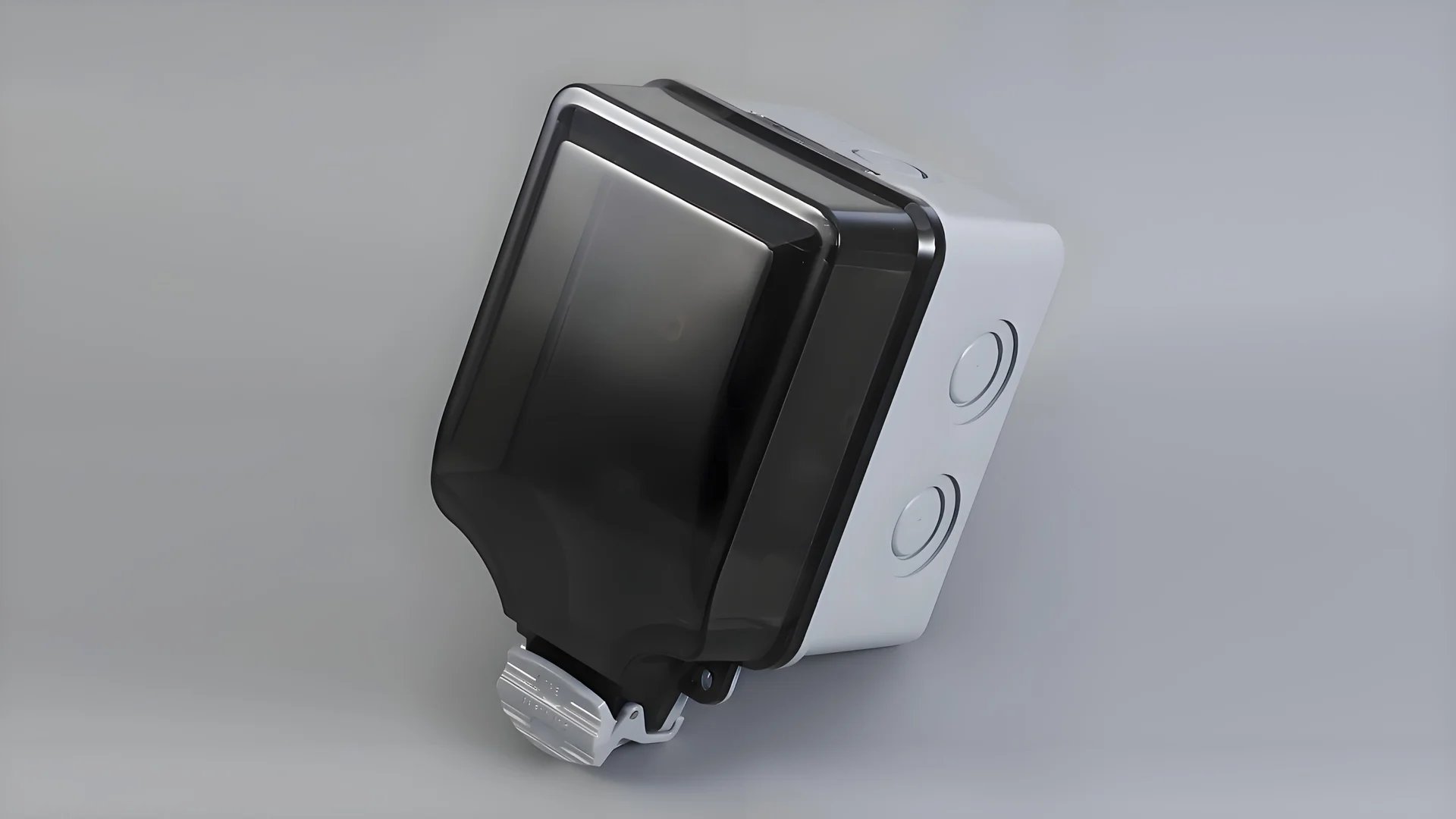
Understanding Annealing in Injection Molding
Annealing is a heat treatment process that involves heating the plastic parts to a specific temperature, maintaining that temperature for a period, and then slowly cooling them down. This process helps in relieving internal stresses that can lead to warping and distortion. For instance, annealing temperature9 and time vary depending on the plastic resin type, and precise control is crucial to achieving optimal results. Polycarbonate parts, for example, may require different annealing conditions than polyamide parts.
The annealing process reduces internal stresses formed during the molding process, particularly in high-precision products. As these stresses are relieved, the material becomes more dimensionally stable, reducing post-mold shrinkage and improving the consistency of part dimensions.
The Role of Humidity Adjustment
Some plastics, like nylon, are hygroscopic, meaning they absorb moisture from the environment. This can lead to changes in dimensions after molding. Implementing a humidity adjustment treatment involves exposing the molded part to controlled humidity conditions so it can absorb a stable amount of moisture before it goes into use. The goal is to reach an equilibrium state where further moisture absorption during product use is minimized.
Choosing the right conditions for humidity adjustment10 is essential. This involves determining the specific humidity level and exposure time based on the plastic type and intended product application. By ensuring consistent moisture content throughout the material, dimensional changes caused by environmental humidity fluctuations can be mitigated.
Combining Techniques for Maximum Effect
While annealing and humidity adjustment are effective separately, combining these methods can lead to even greater improvements in dimensional stability. For example, a product subjected to both annealing and humidity control might exhibit enhanced performance in environments with varying temperatures and humidity levels.
Post-Processing Technique | Benefits |
---|---|
Annealing | Reduces internal stresses and distortion |
Humidity Adjustment | Balances moisture content in hygroscopic plastics |
Combined Approach | Maximizes dimensional stability across varied conditions |
By integrating these post-processing techniques into your manufacturing process, you can ensure that your injection-molded products meet stringent dimensional requirements while reducing defects.
Annealing reduces internal stresses in molded parts.True
Annealing involves heating and slowly cooling plastics to relieve stresses.
Humidity adjustment is unnecessary for nylon parts.False
Nylon absorbs moisture; humidity control stabilizes its dimensions.
Conclusion
By implementing these techniques, you can significantly improve the dimensional stability of molded parts. Consider these strategies to optimize your processes and enhance overall production efficiency.
-
Explore how resin crystallinity influences shrinkage and stability.: The degree to which molded parts shrink as they cool is largely dependent upon the composition of the material being processed. ↩
-
Learn strategies for maintaining consistency in raw materials.: To ensure this, use top-notch materials, maintain machines meticulously, optimize mold designs, and control process parameters. Implement robust … ↩
-
Discover how mold structure intricacies influence dimensional precision.: When the mold is not compliant or exactly constrained, deflections and misalignment of platens may cause high levels of stress, leading to increased wear over … ↩
-
Learn about cutting-edge mold technologies enhancing precision.: Owned and managed by engineers, we specialize in technical applications of fluid path, critical shutoffs, and disciplined manufacturing. ↩
-
Consistent barrel temperatures ensure even melting, reducing defects.: Certainly, barrel-zone temperatures influence melt temperature. Most agree that about 20% of the energy to melt the plastic comes from the … ↩
-
Optimizing pressure reduces defects like sink marks and voids.: Injection Molding Machine Calibration: Regular calibration of the injection molding machine is crucial for maintaining accuracy in the process. ↩
-
Adjusting cooling speed minimizes internal stresses and shrinkage.: This paper investigates experimentally and analytically the influence of cooling method and cutting parameters on two major dimensional accuracy characteristics ↩
-
Proper cooling times prevent warping and dimensional changes.: A good rule of thumb is adding 20% to the cooling timer to account for variation on incoming material and slight shifts in machine performance. ↩
-
Find specific annealing temperatures for polycarbonate parts.: Heat oven to 250°F at a maximum heating rate of 20°F per hour. 3. Hold oven temperature at 250°F for 30 minutes plus 15 minutes for every 1/8” of cross-section. ↩
-
Learn about optimal humidity conditions for nylon products.: … nylon with 0.20% actually contains 0.40% moisture in the polymer fraction. … control over moisture content. The polymer responds to a … ↩